Pomiary procesowe i transmisja danych
Damian Żabicki print
Liczne pomiary wielkości elektrycznych i nieelektrycznych są powszechnie wykonywane na potrzeby realizowania procesów produkcyjnych. Od ich dokładności w dużej mierze zależy jakość wytwarzanych wyrobów. Z kolei transmisja danych jest niezbędna do wymiany danych między poszczególnymi urządzeniami systemów automatyki i sterowania.
Pomiary, jakie są stosowane w przemyśle, stanowią bardzo obszerne zagadnienie. Odpowiednie rozwiązanie jest dobierane w zależności od specyfiki procesów technologicznych zakładu produkcyjnego. Warto przyjrzeć się nieco bliżej pomiarom temperatury, przepływu i poziomu.
W systemach transmisji danych kluczową rolę odgrywa odpowiednie dopasowanie sygnałów w ramach pracujących urządzeń z uwzględnieniem właściwych standardów komunikacyjnych i protokołów transmisji. Coraz większą uwagę przywiązuje się do bezpieczeństwa danych przesyłanych w ramach urządzeń automatyki i sterowania. Warto podkreślić, że pierwsze cyberataki na systemy SCADA miały miejsce już
w latach 80.
Sieci Ethernet, które są nieodzownym elementem systemów sterowania, bardzo często mają styk z Internetem, w którym nie brakuje szkodliwego oprogramowania powstałego z myślą o atakach na systemy sterowania.
Pomiar temperatury
W praktyce przemysłowej pomiar temperatury może być wykonywany na wiele sposobów z wykorzystaniem różnych metod. Uwzględniając interakcje zachodzące między badanym obiektem pomiarowym a czujnikiem pomiarowym trzeba przede wszystkim mieć na uwadze pomiar dotykowy (pomiar kontaktowy). W takim rozwiązaniu czujnik (termometr) ma styk z obiektem, którego temperatura jest mierzona. Natomiast pomiar bezdotykowy (pomiar bezkontaktowy) bazuje na pomiarze parametrów promieniowania elektromagnetycznego emitowanego przez rozgrzane ciało. Mierzona jest m.in. długość fal lub ilość energii, jaką emituje obiekt.
W kontekście właściwości fizycznych czujnika pomiarowego wykorzystuje się zjawisko odkształcenia bimetali oraz wytwarzania napięcia elektrycznego na styku dwóch metali (termoelement) w różnych temperaturach. Oprócz tego wykorzystywane jest zjawisko zmiany rezystancji elementu (termistor), zmiany parametrów złącza półprzewodnikowego (termometr diodowy), zmiany objętości cieczy, gazu lub długości ciała stałego (termometr, termometr cieczowy) oraz parametrów promieniowania cieplnego ciała
(np. pirometr).
Najprostsze czujniki temperatury najczęściej wykonywane są z platyny lub niklu. Zazwyczaj są to urządzenia rezystancyjne. W zależności od potrzeb dobiera się czujniki przewodowe, płaszczowe (rezystancyjne i termoelektryczne) oraz głowicowe.
Niejednokrotnie zastosowanie znajdują termometry rezystancyjne. Typowe urządzenie tego typu składa się z czujnika pomiarowego z osłoną oraz głowicy przeznaczonej do instalacji przetwornika. Dzięki stożkowej lub zwężonej końcówce z taśmą termoprzewodzącą zapewniona jest szybka odpowiedź pomiarowa. Głowicę najczęściej wytwarza się ze stali, aluminium lub tworzywa sztucznego. Warto również wspomnieć o wymiennym wkładzie z izolacją mineralną instalowaną wewnątrz osłony. W efekcie można wymieniać i walidować czujnik bez przerywania procesu.
Termoelementy (termoogniwa, termopary, ogniwa termoelektryczne) są elementami obwodu elektrycznego, których budowa bazuje na zastosowaniu dwóch różnych materiałów. Zasada działania termoelementu opiera się na zjawisku Seebecka, zachodzącego na styku materiałów. Jako najważniejsze zalety termoelementów należy wymienić przede wszystkim brak zewnętrznego zasilania, niewielkie wymiary, małą bezwładność czasową, niską pojemność cieplną, wysoki poziom niezawodności oraz dobrą liniowość. Z kolei wśród wad wymienia się nietrwałość złącza pomiarowego. Szkodliwym zjawiskiem może być przepływ prądu poza obwodem termopary, gdzie złącze nie ma izolacji. Izolacja w dużej mierze przyczynia się do wyeliminowania tego zjawiska, ale wydłużany jest czas reakcji termoelementu na zmianę temperatury.
Mówiąc o czujnikach temperatury trzeba uwzględnić wyroby takich producentów, jak chociażby firmy Czaki, Balluff, Guenther, ifm Electronic, Limatherm Sensor, Titec, Wika.
W zakresie bardziej zaawansowanych urządzeń pomiarowych warto zwrócić uwagę na przetworniki temperatury, które przetwarzają sygnały pomiarowe zebrane przez czujniki na sygnał standardowy. Nowoczesne urządzenia tego typu wykorzystują technologie cyfrowe. Bogata funkcjonalność pozwala np. na linearyzowanie czujnika w stosunku do termometru, co przekłada się na zwiększenie dokładności pomiarowej. W zależności od wersji urządzenia dobierany jest odpowiedni sygnał wyjściowy przetwornika. Najczęściej są to sygnały analogowe (np. sygnał prądowy 4–20 mA) oraz sygnały cyfrowe bazujące na standardowych protokołach komunikacyjnych.
Jednym z przykładów programowalnych przetworników temperatury jest AR580 firmy APAR. Urządzenie charakteryzuje się liniowym przetwarzaniem mierzonej temperatury na sygnał prądowy lub napięciowy. Możliwe jest stosowanie wejść termorezystancyjnych (Pt 100) oraz termoelementowych (J, K, S, N, E) z automatyczną lub stałą kompensacją temperatury spoiny odniesienia. Wyjście stanowi sygnał prądowy (4–20 mA) oraz napięciowy 0–10 V bez separacji galwanicznej układów wejścia/wyjścia. Obudowa jest przystosowana do montażu na listwie TS35 (szyna DIN).
Pomiar poziomu
W praktyce pomiar poziomu medium bardzo często wykorzystuje pomiar odległości lub długości. Zależnie od aplikacji zakres pomiarowy wynosi od kilku centymetrów do kilkudziesięciu metrów. Pomiar poziomu wykonuje się m.in. na potrzeby pomiarów cieczy w silosach czy zasobnikach.
Zarówno w odniesieniu do cieczy, jak i materiałów sypkich wyróżnia się trzy metody polegające na pomiarze czasu przelotu: radarową, ultradźwiękową oraz tzw. radar prowadzący. W każdej z nich nadajnik wysyła impulsy elektromagnetyczne lub falę ultradźwiękową, które po odbiciu od powierzchni cieczy/materiałów sypkich docierają do odbiornika. Mierząc czas przelotu wiązki oraz mnożąc go przez prędkość propagacji fali, przetwornik określa odległość między nadajnikiem a powierzchnią medium. Po uwzględnieniu wysokości zbiornika, można łatwo obliczyć rzeczywisty poziom zgromadzonego w nim materiału.
W ekstremalnych warunkach procesowych (wysoka temperatura i/lub ciśnienie, środowisko agresywne chemicznie itd.) stosowane są przyrządy radiometryczne. W odniesieniu do cieczy zastosowanie znajduje metoda pojemnościowa oraz metoda hydrostatyczna. Stosowane są też przyrządy z serwosterowaniem. W przypadku materiałów sypkich uwzględnia się natomiast metody elektromechaniczne.
Z powyższych metod warto przyjrzeć się bliżej przyrządom z serwosterowaniem czyli przetwornikom ze sterowaniem nadążnym. Zasada pomiaru jest następująca. Podczas opuszczania czujnika pływakowego, wraz z zetknięciem czujnika z cieczą, zmniejsza się jego ciężar w efekcie działania siły wyporu. Tym samym zmienia się moment obrotowy mechanizmu ze sprzężeniem, co jest wykrywane np. przez czujnik Hall’a. Sygnał proporcjonalny do pozycji czujnika trafia do układu sterowania silnikiem. Wraz ze zmianą poziomu cieczy zmienia się pozycja pływaka regulowana przez silnik napędowy. W oparciu o dokładną analizę ruchu obrotowego bębna linkowego wyznaczany jest poziom cieczy. Taka metoda pomiaru cechuje się przede wszystkim wielofunkcyjnością oraz odpornością na zmiany gęstości i prężności par w zbiornikach wysokociśnieniowych. Jest to metoda bardzo dokładna.
Sondy radarowe Micropilot FMR52 z oferty firmy Endress+Hauser znajdują zastosowanie przy pomiarze poziomu w zbiornikach magazynowych, buforowych, a także procesowych z mieszadłami i nagrzewnicami. Zbiorniki te mogą mieć wzburzoną ciecz, zapylenie i wysoką temperaturę. Funkcja Heartbeat Technology pozwala weryfikować stan i rozszerzać diagnostykę bez demontażu ze zbiornika. Tym sposobem jest więc możliwe automatyczne czyszczenie, suszenie lub chłodzenie anteny oraz wykrywanie i gaszenie piany.
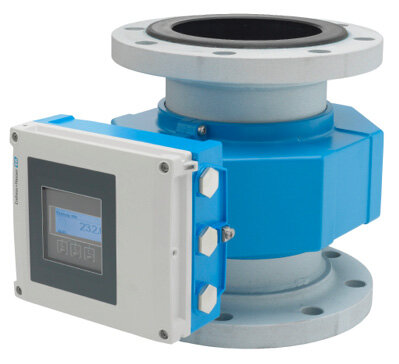
Promag W 400 Endress+Hauser – pierwszy przepływomierz elektromagnetyczny z pomiarem niezależnym od profilu przepływu oraz miejsca montażu
Pomiar przepływu
Pomiar przepływu jest realizowany przez przepływomierze mierzące strumień objętości lub masy. Przepływomierze, jakie znajdują zastosowanie w przemyśle, zazwyczaj mierzą przepływ cieczy, nieco rzadziej gazów. Przyrządy pomiarowe służące do pomiaru przepływu dzieli się na trzy grupy uwzględniając zjawiska fizyczne wykorzystywane podczas pomiaru. Mowa tu o oddziaływaniu mechanicznym, zjawisku falowym (przepływomierze ultradźwiękowe) oraz optycznym (efekt Dopplera). Zastosowanie znajdują również urządzenia, które wykorzystują pole elektromagnetyczne, bazujące na prawie indukcji elektromagnetycznej Faradaya.
Pomijając kwestię urządzeń mechanicznych warto wspomnieć o przepływomierzach masowych (Coriolisa). Ich cechą jest wykonywanie pomiaru z dużą dokładnością bez względu na profil przepływu medium. Mierzy się również lepkość, gęstość i strumień masy. Warto wspomnieć o uniwersalnej zasadzie pomiaru zarówno dla gazów jak i cieczy, bez względu na właściwości fizyczne produktu. Dla prawidłowej pracy przepływomierzy masowych nie jest wymagany prosty odcinek instalacji. Montaż przepływomierza Coriolisa jest tańszy w porównaniu z wdrożeniem systemu wagowego. Wadą takich urządzeń jest utrudniona kalibracja. Ponadto rura, na której zamontowany jest przepływomierz, musi być całkowicie wypełniona cieczą. Przepływomierze masowe niejednokrotnie mają problemy z pomiarami przepływu cieczy, w których obecne są pęcherzyki gazu. Charakteryzują się również ograniczoną odpowiedzią dynamiczną.
Niejednokrotnie zastosowanie znajdują termiczne przepływomierze masowe. Mierzą one prędkość przepływu medium wykorzystując zmianę w ogrzewaniu lub pobieraniu ciepła na skutek przepływu medium. W termicznych przepływomierzach masowych medium opływa czujniki. Między nimi znajduje się grzałka. Jeden z czujników ma za zadanie monitorowanie temperatury materiału. Drugi czujnik jest podgrzewany przez medium opływające grzałkę. Przepływ oblicza się w oparciu o różnicę temperatury czujników. Należy podkreślić, że moc grzałki jest wartością stałą. Inna metoda zakłada zmienną moc grzałki, która utrzymuje stałą różnicę temperatur. W takim rozwiązaniu prędkość przepływu jest określana z uwzględnieniem mocy grzałki. Termiczne przepływomierze masowe cechują się przede wszystkim wysokim poziomem czułości i dobrą dynamiką pomiarową. Ponadto urządzenia tego typu nie mają części ruchomych, a spadek ciśnienia jest niewielki. Wadą termicznych przepływomierzy masowych przede wszystkim jest bardzo częste zawyżanie wyników pomiarów w przypadku mediów o dużej wilgotności. Chodzi tutaj o sytuację, kiedy na czujniku pomiarowym skondensuje się woda. Istotną wadą takich urządzeń jest ograniczenie górnego zakresu przez limit energii ogrzewającej czujnik. Bardzo często zwraca się uwagę na niską odporność na działanie zanieczyszczeń, jakie pochodzą od mierzonego medium.
Dużym uznaniem w aplikacjach przemysłowych cieszą się przepływomierze wirowe. Bazują one na pomiarze ilości medium, jaka przepływa przez określoną powierzchnię. Powierzchnia ta jest prostopadła do kierunku przepływu medium. Wykorzystuje się tu ścieżkę wirową Karmana, która opisuje zjawisko powstawania wirów za ciałem nieopływowym.
Przepływomierze wirowe mają przegrodę umieszczoną w strudze przepływającego płynu. Przegroda generuje zawirowania odrywające się naprzemiennie od boków przegrody. Te z kolei są unoszone wraz ze strumieniem. Częstotliwość odrywania wirów jest wprost proporcjonalna do średniej prędkości przepływu będącej strumieniem objętości. Wraz z odrywaniem wirów obie strony przegrody powodują naprzemienne chwilowe pola niskiego ciśnienia. Pola te wykrywa czujnik znajdujący się za przegrodą. Zadaniem czujnika jest też zliczanie pola ciśnienia oraz generowanie liniowego sygnału cyfrowego, który ma wartość proporcjonalną do prędkości przepływającego płynu.
Zaletą przepływomierzy wirowych jest wysoki poziom dynamiki pomiaru. Istotna jest znaczna stabilność długoterminowa przy jednoczesnym wyeliminowaniu zjawiska płynięcia zera – na skutek dużej stabilności. Na system pomiarowy nie wpływają zmiany ciśnienia, temperatury i lepkości. Dzięki uniwersalności pomiarowej przepływomierze wirowe wykorzystywane są do pomiaru gazów pary i cieczy. Wadą przepływomierzy wirowych jest bardzo mała częstotliwość odrywania wirów w rurociągach o dużych przekrojach, a także niska odporność na deformacje prędkości.
Kolejną grupą urządzeń są przepływomierze turbinowe. Bazują one na zjawisku liniowej zależności prędkości obrotowej wirnika w stosunku do objętościowego natężenia przepływu. W przypadku niewielkiej wartości natężenia przepływu zastosowanie znajdują przepływomierze skrzydełkowe z wirnikiem prostopadłym do kierunku przepływu płynu. Jeżeli natężenia przepływu są większe, wykorzystuje się łopatki śrubowe obracane wokół osi przepływu.
Wiele aplikacji przemysłowych wykorzystuje przepływomierze ultradźwiękowe. Ich istotą jest pomiar prędkości przepływu medium przez powierzchnię prostopadłą do kierunku przepływu. Przepływomierze ultradźwiękowe bazują na pomiarze różnicy czasu przejścia fali ultradźwiękowej wywołanej efektem Dopplera. Fala emitowana jest na przemian między dwoma czujnikami znajdującymi się na rurociągu. W momencie zatrzymania przepływu czas przejścia fali w dwóch kierunkach będzie jednakowy. Z kolei wraz z rozejściem się fali przeciwnie w odniesieniu do płynącej cieczy, zmniejsza się prędkość propagacji zgodnie z ruchem cieczy. Różnica czasów przejścia mierzona przez przepływomierz jest proporcjonalna do prędkości cieczy w rurociągu. Uwzględniając profil i pole przekroju poprzecznego rury można wyznaczyć objętość strumienia.
Jako zaletę przepływomierzy ultradźwiękowych należy wymienić przede wszystkim pomiar bezkontaktowy. Takie rozwiązanie szczególnie dobrze sprawdzi się w przypadku pomiarów cieczy silnie agresywnych lub cieczy o dużym ciśnieniu. Ponadto urządzenia charakteryzują się znaczną trwałością. Można je też montować w instalacjach już istniejących. Przy montażu systemu pomiarowego nie ma potrzeby zatrzymywania procesu. Przepływomierze ultradźwiękowe nie powodują spadku ciśnienia w instalacji.
Następną grupą urządzeń są przepływomierze elektromagnetyczne. Mierzą one prędkość przepływu medium przez określoną powierzchnię, która jest prostopadła do kierunku pola magnetycznego. Wykorzystywane jest tu zjawisko indukcji elektromagnetycznej Faradaya. Lepkość, temperatura, gęstość i ciśnienie produktu nie wpływają na wynik pomiaru. Metodą elektromagnetyczną można mierzyć ciecze o wysokim poziomie koncentracji ciał stałych. Są to przede wszystkim szlamy kopalniane i masy celulozowe. Ze względu na to, że przepływomierze elektromagnetyczne nie mają części ruchomych, nie dochodzi do spadków ciśnienia w instalacji. Charakterystyczna jest duża dynamika pomiaru, stabilność w czasie i niezawodność.
Urządzenia serii CoriolisMaster FCB400 firmy ABB to kompaktowe przepływomierze masowe. Urządzenia te cechują się przede wszystkim niskim spadkiem ciśnienia, intuicyjnym wyświetlaczem oraz wymianą danych poprzez protokół HART. W przepływomierzu przewiduje się nawet pięć wejść/wyjść modułowych. Opcjonalnie może być zamontowana karta typu plug-in. Oprogramowanie jest automatycznie aktualizowane.
Zastosowany czujnik cechuje się rozbudowaną pamięcią a w razie potrzeby szybką wymianą elektroniki. Obsługę wykonuje się poprzez przezroczystą szybkę dzięki przyciskom pojemnościowym.
Termiczny przepływomierz masowy EE771 z oferty firmy Introl znajduje zastosowanie przede wszystkim przy pomiarze przepływu w rurociągach. Stosowany jest do pomiaru zużycia sprężonego powietrza, helu, azotu, argonu, CO2 i innych gazów niepalnych oraz niepowodujących korozji. Urządzenie mierzy przepływ objętościowy w warunkach normalnych zgodnie z normą DIN 1343. Mierzony jest nie tylko standardowy przepływ objętościowy ale i przepływ masowy oraz temperatura. Przyrząd ma wbudowany licznik zużycia gazu. Do dyspozycji są dwa wyjścia sygnału, które w zależności od aplikacji można konfigurować jako analogowe (prądowe lub napięciowe) albo jako wyjścia przełączające lub impulsowe do pomiaru zużycia.
Wieloparametrowe przepływomierze wirowe firmy HEINRICHS mierzą przepływ cieczy o niskich lepkościach, a także pary wodnej i gazów. Do wyboru jest wersja przeznaczona do montażu na istniejącym rurociągu (typ DVE) oraz jako wstawka rurowa (typ DVH). Czujnik pomiarowy może być wyposażony w elementy pomiarowe takie jak piezoelektryczny czujnik prędkości przepływu medium – czujnik podstawowy, czujnik temperatury Pt 100 oraz czujnik ciśnienia absolutnego medium. Inne przykłady przepływomierzy to Fluxus (firmy Flexim), ST100 (firmy FCI), Tricor TCM (firmy Tricor), M23 (firmy Vortek), FLONET FN10/FN20 (firmy Elis).
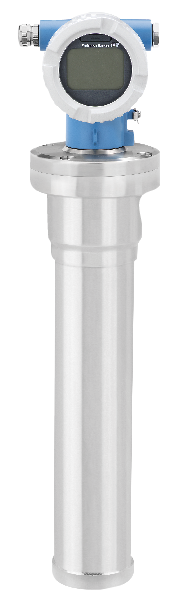
Gammapilot FMG50 – kompaktowy przetwornik do bezkontaktowego pomiaru rozdziału faz, gęstości, oraz sygnalizacji i ciągłego pomiaru poziomu cieczy, materiałów sypkich, zawiesin lub osadów, Endress+Hauser
Bezpieczeństwo przemysłowych systemów danych
Nie ma wątpliwości co do tego, że przemysłowe systemy sterowania znacznie odbiegają od sieci teleinformatycznych w wykonaniu standardowym. Pociąga to za sobą wdrożenie nieco innych założeń, zarówno w stosunku do zasobów informacji, jak i ich przesyłania. Bardzo często do przemysłowych systemów sterowania podchodzi się jak do łatwego celu w zakresie cyberataków. Wynika to stąd, że zastosowanie nietypowych, a do tego separowanych protokołów transmisji danych, jest trudne do rozszyfrowania. Stąd też sprzętu używanego w systemach sterowania nie wyposaża się w odpowiednie zabezpieczenia. Do tego bez problemu można znaleźć wirusa lub złośliwe oprogramowanie infekujące sterowniki PLC lub urządzenia przeznaczone do transmisji danych, które pracują w standardzie RTU.
Za szybkim rozwojem systemów przesyłu danych idzie szereg możliwości dla cyberprzestępców. Jeszcze całkiem niedawno dane w ramach infrastruktury przemysłowej były wymieniane w oparciu o porty szeregowe z krótkimi połączeniami. Wykorzystywano również sieci typu SDH/PDH. Do takich rozwiązań, w porównaniu z zaawansowanymi protokołami transmisyjnymi, trudno się włamać. Ponadto bardzo często nowoczesne systemy automatyki zazębiają się z różnego typu sieciami korporacyjnymi czy biurowymi. W efekcie coraz częściej zastosowanie znajduje ta sama infrastruktura sprzętowa – serwery i sieci. Na uwagę zasługuje dynamiczny rozwój systemów takich jak MES, ERP, CMMS czy SAP. Konieczne okazują się więc kolejne punkty pozwalające na styk takich systemów z przemysłowymi systemami sterowania. Niejednokrotnie systemy korporacyjne i przemysłowe systemy sterowania obejmuje taka sama polityka bezpieczeństwa. Jednak z racji różnych zagrożeń powinny być uwzględnione różne wymagania. Dodatkowo na ataki narażony jest przesył danych między urządzeniami rozproszonymi.
Należy uwzględnić szereg wymagań w zakresie bezpieczeństwa w odniesieniu do urządzeń RTU, które są łączone sieciami wewnętrznymi i zewnętrznymi. Mowa tu przede wszystkim o publicznych częściach infrastruktury sieciowej, a także modułach komunikacyjnych RTU. Rozbudowane urządzenia RTU niejednokrotnie cechują się zaawansowanymi możliwościami zbliżonymi do funkcjonalności komputerów. Do tego proces wymiany danych z innymi systemami bazuje na sieciach i protokołach IP. Są to kolejne elementy, które mogą być narażone na cyberataki.
Co prawda, redundancja przyczynia się do zwiększenia bezpieczeństwa aplikacji pod względem stabilności i ciągłości pracy, to jednak powstają dodatkowe obiekty (np. serwery), które mogą stać się celem cyberataków. Za punkty newralgiczne uznaje się wszelkie błędy, jakie niejednokrotnie powstają podczas wdrożenia systemu oraz błędy w konfiguracji. Na zmniejszenie odporności na zagrożenia wpływ mają usterki w pracy sprzętu i oprogramowania. Typowe cyberataki bardzo często przybierają formę DDoS oraz exploitów skutkujących przejęciem kontroli nad systemami.
Wszystko to przekłada się na implementowanie odpowiednich zabezpieczeń w urządzeniach automatyki przemysłowej. W protokołach komunikacyjnych implementuje się zabezpieczenia DNP3.0, SNMPv3, TLS, centralną autoryzację – RADIUS czy IPSec VPN (tryb tunelowy). Ponadto monitoruje się aktywność użytkowników za pomocą logowania zdarzeń – logowanie użytkownika (zdalne i lokalne), wylogowanie ręczne/po czasie, wymianę firmware itd. Należy też pamiętać o prostych, a jakże skutecznych narzędziach takich jak odpowiednia siła hasła.
Kluczowe miejsce zajmuje właściwa konfiguracja oprogramowania przez Bootstrap, czyli proste pierwsze uruchomienie. Warto zautomatyzować aktualizację oprogramowania. W przypadku zdalnego zarządzania konfiguracją urządzeń trzeba zadbać o zaufane źródło. Ważne jest aktualizowanie kluczy i certyfikatów bezpieczeństwa. Przydatnym rozwiązaniem jest funkcja pozwalająca na wycofanie zmian przez przywrócenie wcześniejszej wersji.
Kluczowe miejsce zajmuje tzw. hardening, będący zabezpieczeniem systemu przez redukowanie elementów do niezbędnego minimum. Chodzi tutaj o interfejsy oraz otwarte porty sieciowe. Warto zadbać o blokady dostępu w przypadku przekroczenia czasu trwania sesji, dezaktywację niepotrzebnych użytkowników czy usuwanie nieużywanych funkcji. Bardzo często usuwa się również moduły programów, które nie są używane.
Konwertery CRS-xxx z oferty firmy Mikronika umożliwiają komunikację w sieciach wykorzystujących protokół PPM2 w standardzie CAN-BUS/RS-485. Urządzenia konwertują protokoły szeregowe na standard magistrali CAN-BUS. Konwerter ma trzy porty komunikacyjne RSB (RS-485), CAN i RSA (RS-232). Port RSB i CAN służy do komunikacji z systemem nadrzędnym. W warstwie komunikacyjnej port wykorzystuje protokół CAN-BUS i PPM2. Port RSA służy jedynie do diagnozowania poprawności pracy urządzenia.
Switch Itrusion Detection System/Intrusion Prevention System/DPI SCADA Firewall z oferty firmy Tekniska ma dwa porty Gigabit Ethernet do ochrony sieci OT. Urządzenie pracuje w dwóch trybach IDS/TAP – urządzenie monitoruje ruch w sieci i przekazuje informacje do urządzenia nadrzędnego przez port mgmt (management) oraz IPS / In Line – jako SCADA Firewall. Urządzenie wpięte szeregowo w linię komunikacyjną analizuje ruch sieciowy i aktywnie podejmuje działania wg zadanych reguł. Do dyspozycji są dwa porty RJ45 Gigabit Ethernet (1000BaseT) przeznaczone do pracy jako IDS 2 × TAP lub jako IPS 1 × In line pair z bypass’em zabezpieczającym. Oprócz tego przewidziano jeden port RJ45 mgmt oraz dwa porty USB.
Konwerter ADAM-4572 z oferty firmy Advantech obsługuje interfejs 10/100 Base-T (RJ45) i protokół TCP/RTU/ASCII. Interfejs szeregowy może pracować w standardzie RS-232 (Rx, Tx, Gnd), RS-422 (Rx+, Rx-, Tx+, Tx-) oraz RS-485 (Data+, Data-). Prędkość transmisji na łączu szeregowym wynosi do 921,6 kbps. Złącze portu szeregowego i zasilania bazuje na zaciskowym terminalu śrubowym. Konwerter jest zasilany napięciem 10–30 V DC. Konfiguracja urządzenia odbywa się za pomocą oprogramowania Advantech EKI Device Configuration Utility.
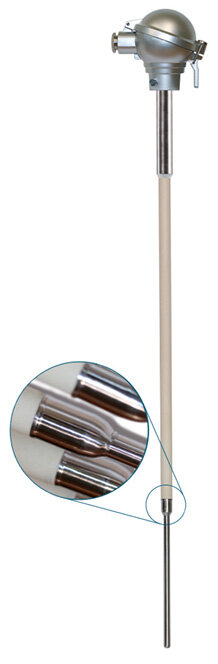
Czujniki temperatury oferowane przez Guenther to większa stabilność i dłuższa trwałość poparta patentem
Podsumowanie
W ramach podsumowania należy podkreślić, że w zakresie bardziej zaawansowanych urządzeń pomiarowych na uwagę zasługują przetworniki temperatury, które przetwarzają sygnały pomiarowe zebrane przez czujniki na sygnał standardowy. Nowoczesne urządzenia tego typu to urządzenia cyfrowe. Bogata funkcjonalność pozwala m.in. na linearyzowanie czujnika w stosunku do termometru, co przekłada się na zwiększenie dokładności pomiarowej.
W praktyce pomiar poziomu medium bardzo często przybiera postać pomiaru odległości lub długości. Zależnie od aplikacji zakres pomiarowy wynosi od kilku centymetrów do kilkudziesięciu metrów. Pomiar poziomu odbywa się m.in. na potrzeby pomiarów cieczy w silosach lub zasobnikach.
Do pomiaru przepływu wykorzystuje się przepływomierze mierzące strumień objętości lub masy. Przepływomierze, które znajdują zastosowanie w przemyśle, zazwyczaj mierzą przepływ cieczy a nieco rzadziej gazów. Przyrządy pomiarowe służące do pomiaru przepływu dzieli się na trzy grupy uwzględniając zjawisko fizyczne, jakie jest wykorzystywane przy pomiarze.
Nie ma wątpliwości co do tego, że przemysłowe systemy sterowania odbiegają od sieci teleinformatycznych w wykonaniu standardowym. Pociąga to za sobą wdrożenie nieco innych założeń, zarówno w stosunku do zasobów informacji jak i ich przesyłania. Bardzo często do przemysłowych systemów sterowania podchodzi się jak do łatwego celu cyberataków. Z reguły jest to skutkiem tego, że zastosowanie nietypowych, a do tego separowanych protokołów transmisji danych, jest trudne do rozszyfrowania. Stąd też sprzętu używanego w systemach sterowania nie wyposaża się w odpowiednie zabezpieczenia.
source: Automatyka 4/2020