Termowizja skuteczną metodą kontroli obiektów przemysłowych
Marcin Bieńkowski print
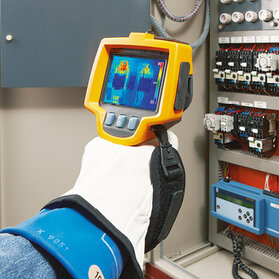
Na ekranie kamery termowizyjnej bez problemu można zobaczyć, które przekaźniki są przeciążone (fot. Fluke)
W dzisiejszych czasach trudno wyobrazić sobie funkcjonowanie służb utrzymania ruchu bez tak pomocnych narzędzi, jak kamery termowizyjne. Pozwalają one nie tylko rejestrować obrazy termograficzne przydatne w kontroli procesu produkcyjnego, ale również szybko zlokalizować miejsce awarii, zanim jeszcze ona nastąpi.
Termowizja, nazywana niekiedy termografią, jest jedną z metod termicznej diagnostyki obiektów. Wykorzystywane jest tutaj zjawisko bezkontaktowej detekcji promieniowania elektromagnetycznego w paśmie średniej podczerwieni, czyli dla długości fal od ok. 0,9 μm do 14 μm. Dzięki temu kamera termowizyjna może rejestrować promieniowanie cieplne o temperaturze z zakresu od około –50 °C do około +2000 °C, które jest emitowane przez ciała fizyczne.
Oczywiście, nie każda kamera może mierzyć temperaturę w tak szerokim przedziale. Zazwyczaj jest to zakres od –20 °C do +250 °C. Rzadziej zdarzają się modele pozwalające na pomiary temperatury w przedziale od –20 °C do +650 °C czy bardziej „szerokopasmowe” modele mierzące w zakresie od –40/–50 °C do +1600/1700 °C, a nawet dochodzące do górnej granicy +2000 °C. W pomiarach termowizyjnych istotne jest to, że obserwowane obiekty nie muszą być oświetlane zewnętrznym źródłem promieniowania podczerwonego.
Temperaturowe zdjęcie
Kamera termowizyjna nie mierzy jednak pojedynczej, uśrednionej temperatury obiektu (patrz: ramka „Pirometr a kamera termowizyjna”) – w wyniku pomiaru uzyskiwany jest rozkład temperatury na powierzchni mierzonego obiektu. Kamera cyfrowo rejestruje tak powstałą „mapę temperaturową” obiektu, która w odpowiedni sposób na wyświetlaczu urządzenia jest graficznie interpretowana. Każdej temperaturze przypisywane są inne barwy, dzięki czemu na ekranie LCD kamery można zobaczyć termalny obraz obiektu, który nazywany jest termogramem lub termografem.
Możliwa jest też – w zależności od zaimplementowanego w kamerze oprogramowania – analiza termogramów bezpośrednio na ekranie, polegająca np. na wykreślaniu izoterm, określaniu rozkładu temperatury wzdłuż dowolnego profilu lub obiektu, tworzenie i wyświetlanie histogramów czy też podawanie uśrednionej wartości temperatury itp. Dodatkowo można dokonać bardzo precyzyjnego pomiaru temperatury fotografowanych lub filmowanych przez kamerę termowizyjną obiektów.
Najważniejszą zaletą termografii jest brak inwazyjności. Dzięki temu możliwe jest wykonywanie pomiarów temperatury bez ingerencji w proces technologiczny czy pomiary temperatury w medycynie bez konieczności bezpośredniej interakcji z pacjentem. Co więcej, możliwe jest też prowadzenie pomiarów temperatury w miejscach trudno dostępnych, w których wykorzystanie klasycznych, stykowych metod pomiaru temperatury byłoby bardzo trudne lub niemożliwe. Kamery termowizyjne bez problemu można zainstalować na dronach, co ułatwia szybką temperaturową inspekcję kluczowych elementów infrastruktury technologicznej – np. trudno dostępnych sieci ener-
Zdjęcia termograficzne pozwalają też szybko zdiagnozować, czy elementy maszyny lub urządzeń energetycznych nagrzewają się nierównomiernie lub znaleźć uszkodzoną izolację różnego rodzaju pieców czy ciepłowodów. Termografię stosuje się w diagnostyce układów energetycznych i elektronicznych, w budownictwie, górnictwie, przemyśle samochodowym i lotniczym, automatyce, a także w szeroko rozumianym utrzymaniu ruchu.
Termowizja wykorzystywana jest również w wielu dziedzinach nauki i życia codziennego. Stosowana jest przez wojsko, policję, straż leśną, służby ratownicze, a coraz częściej również w diagnostyce medycznej. Stosowana zapobiegawczo, umożliwia uniknięcie nieprzewidzianych przestojów produkcyjnych.
Utrzymanie ruchu
Służby utrzymania ruchu najczęściej wykorzystują kamery termowizyjne w dwóch obszarach: w konserwacji i kontroli urządzeń mechanicznych oraz przy sprawdzaniu poprawności pracy elementów elektrycznych. W przypadku urządzeń mechanicznych kamera termowizyjna pozwala bowiem bardzo szybko zdiagnozować stan techniczny obrabiarek oraz różnego rodzaju maszyn i urządzeń znajdujących się w halach produkcyjnych i na liniach technologicznych. Techniki termograficzne można wykorzystać do kontroli stanu silników elektrycznych, przekładni, prowadnic i innych elementów ruchomych maszyn.
Wszelkie urządzenia mechaniczne, silniki elektryczne czy przekładnie podczas pracy zawsze wydzielają pewną ilość ciepła związanego z tarciem lub przepływem prądu elektrycznego. Ciepło wydzielane podczas normalnej pracy powinno być oczywiście zawsze uwzględnione w założeniach konstrukcyjnych, jednak jeżeli urządzenie lub jego podzespół pracują nieprawidłowo, wówczas z maszyny, przekładni czy obrabiarki wydziela się znacznie większa ilość ciepła. Sytuacja ta może być związana z zacieraniem się lub blokowaniem elementów ruchomych, ich zużyciem, niewłaściwym smarowaniem bądź uszkodzeniem systemu chłodzącego. Za zwiększone wydzielanie ciepła odpowiadać też mogą przeciążone obwody elektryczne maszyn, urządzeń lub linii technologicznej.
W przypadku przegrzewania się silników i przekładni najczęstszą przyczyną kłopotów są problemy z łożyskami. Pomiar termowizyjny od razu pozwala jednoznacznie wskazać przyczynę awarii, ponieważ przegrzane łożysko jest bardzo dobrze widoczne na rejestrowanym termogramie. Na ekranie kamery termowizyjnej zobaczymy wówczas uszkodzone łożysko w postaci mocno czerwonego lub białego punktowego obszaru. Co więcej, w ten sposób można zdiagnozować nie tylko uszkodzenie łożyska, ale również jego nierównomierne obciążenie. Na termogramie uwidoczni się ono w ten sposób, że jeden z fragmentów obudowy łożyska będzie znacznie bardziej gorący, a co za tym idzie, odwzorowany jaśniejszym kolorem.
Dla łożysk ślizgowych, w których panewka pracuje poprawnie oraz zapewnione jest odpowiednie smarowanie i nie przekroczono nominalnego obciążenia, na termogramie obserwować będziemy równomierny rozkład temperatury. Ciepło wytwarzane podczas ruchu obrotowego będzie równomiernie odbierane przez korpus maszyny. Jeżeli łożysko ślizgowe jest w którymś miejscu cieplejsze, wówczas można się spodziewać, że w tym miejscu występuje większe tarcie. Istnieje więc ryzyko zatarcia się panewki.
Dzięki technologii termowizyjnej można również stosunkowo łatwo wykryć niedrożne kanały smarownicze czy przekroczone obciążenia oraz zużycie panewki w łożysku ślizgowym. Zaobserwowanie podwyższonej temperatury na termogramie powinno skutkować przeglądem zespołów smarowniczych i pomiarem luzów w układzie
Współosiowość wałów
Kolejnym typem usterki, którą można bardzo łatwo wykryć za pomocą termowizji, jest niewspółosiowość wałów. W tym przypadku elementy przekładni, które przenoszą moment obrotowy, a więc koła zębate lub pasy, nagrzewają się znacznie bardziej niż reszta podzespołów. Na rejestrowanym obrazie termowizyjnym uwidoczni się to w postaci nagrzanych brzegów współpracujących ze sobą kół zębatych bądź nagrzanej linii styku koła pasowego z pasem.
Czasami w niewspółosiowej przekładni pasowej nagrzany będzie jedynie sam pas. Jego nagrzewanie świadczy zazwyczaj o ześlizgiwaniu się z koła pasowego. W przekładniach łańcuchowych o nieprawidłowości ich pracy świadczą przede wszystkim nagrzane końce zębów koła łańcuchowego oraz sworznie łańcucha. W trakcie pracy przekładni mogą też przegrzewać się inne elementy układu przeniesienia napędu. Takie usterki również bardzo dobrze widać na termogramach. Najczęściej zbyt gorące będą takie elementy jak: tuleje, sprzęgła lub przeguby.
Termowizja posłużyć może również do kontroli stanów zazębienia zębów w przekładniach otwartych. Na termogramie zębów zębnika oraz wieńca zębatego napędu widoczne będą miejsca, w których występują podwyższone naciski lub zwiększone poślizgi. Dzięki temu zapobiec można sytuacji przyspieszonego zużycia zębów, wynikającego z występowania nadmiernych naprężeń kontaktowych. „Wychwycić” można również miejsca nadmiernego ścierania się powierzchni elementów, które ze sobą współpracują.
W przypadku silników elektrycznych, oprócz możliwości wykrywania uszkodzeń łożysk mogących skutkować zablokowaniem się wału, kamery termowizyjne pozwalają również odszukać miejsca, w których nastąpiło przebicie izolacji wirnika i stojana, a także przerwanie połączeń elektrycznych. W tej ostatniej sytuacji na termogramie zaobserwujemy miejsca o niższej niż właściwa temperaturze. Chłodniejsze i cieplejsze obszary obudowy pozwalają z kolei wykryć problemy z odprowadzaniem ciepła z obudowy silnika.
Podobną analizę można przeprowadzić również dla urządzeń hydraulicznych i pneumatycznych. Wyższa temperatura elementów wskazuje m.in. na możliwość „zacierania” się elementów ruchomych, np. siłowników. Z kolei nierównomierny rozkład temperatury świadczyć może o problemach z odprowadzaniem ciepła. W instalacjach pneumatycznych i hydraulicznych wyraźnie chłodniejsze miejsca mogą świadczyć o nieszczelności instalacji i wydostawaniu się z niej medium roboczego. Dzięki termowizji szybko można też znaleźć miejsca, w których urządzenia hydrauliczne i pneumatyczne są przeciążone.
Urządzenia elektryczne
Kolejnym obszarem, w którym służby utrzymania ruchu bardzo chętnie posługują się termowizją, jest sprawdzanie poprawności pracy elementów elektrycznych i elektronicznych, w tym systemów automatyki przemysłowej.
Dzięki termogramom można bardzo łatwo wykryć nieprawidłowe działanie transformatorów. W trakcie prawidłowej pracy transformator zawsze nagrzewa się do określonej w dokumentacji technicznej temperatury. Jeżeli zobaczymy na ekranie kamery termowizyjnej zbyt zimne elementy, np. rury w transformatorach olejowych, wówczas wiadomo, że transformator nie działa prawidłowo.
Z drugiej strony zaciski doprowadzające prąd czy zaciski izolatorów przepustowych zawsze powinny być chłodne. Jeżeli temperatura tych elementów nie jest zbliżona do temperatury obudowy urządzenia, wówczas oznacza to, że pracują one nieprawidłowo. Może być to spowodowane występowaniem wyładowań niezupełnych lub mikroiskrzenia.
Najczęściej przyczyną pojawienia się nieprawidłowych rozkładów temperatury w instalacjach elektrycznych jest okablowanie. Przewody mogą być niedokładnie zamocowane, obluzowały się w trakcie eksploatacji urządzenia lub są nadmiernie napięte. Łatwo też „wychwycić” przerwane kable lub przewody ze skorodowanymi złączami. Przerwanie obwodu uwidoczni się niższą temperaturą.
Podobnie zachowają się niedokładnie zamocowanie czy obluzowane na zaciskach kable. Jeżeli natomiast na zaciskach wystąpiło mikroiskrzenie (np. na źle zamocowanym przewodzie), będzie to bardzo dobrze widoczne na termogramie w postaci miejsc o podwyższonej temperaturze. Na obrazie termowizyjnym instalacji elektrycznej można też zlokalizować bezpieczniki bliskie przepalenia (są cieplejsze) lub już przepalone (mają znacznie niższą temperaturę).
Trzeba jednak pamiętać, że takie awarie elektryczne jak przeciążenie, niezrównoważenie faz, nieprawidłowa biegunowość będą na zdjęciu termowizyjnym wyglądały bardzo podobnie. Wówczas do ich poprawnego zdiagnozowania niezbędne jest przeprowadzenie dodatkowych pomiarów elektrycznych, które umożliwią znalezienie przyczyny zarejestrowania nieprawidłowego termogramu. Sama kamera termowizyjna wskaże jednak służbom utrzymania ruchu miejsce, w którym wystąpiły nieprawidłowości.
Wysokotemperaturowe środowisko pracy
Służby utrzymania ruchu często odpowiedzialne są również za stan techniczny instalacji cieplnych i różnego rodzaju zbiorników. Tutaj również doskonale sprawdza się termowizja. Technika ta doskonale nadaje się do przeprowadzenia bezpiecznej kontroli kotłów grzewczych i pieców używanych w hutnictwie, odlewnictwie czy hartowaniu metali. Dzięki termowizji można bowiem sprawdzić stan techniczny urządzeń, które w normalnych warunkach pracują w wysokiej temperaturze.
Kontrolę stanu technicznego urządzenia, a nawet parametrów technologicznych znajdującego się w piecu wsadu, można przeprowadzić za pośrednictwem specjalnych okienek inspekcyjnych wykonanych w obudowie pieca. Szczególną uwagę zwraca się na diagnozowanie niewłaściwej pracy wymienników ciepła w piecach oraz na monitorowanie temperatury zewnętrznych powierzchni kadzi odlewniczych, w których transportowana jest roztopiona stal. W rejestrowanych przez kamery termowizyjne termogramach zwraca się uwagę na istnienie gorących punktów, świadczących o uszkodzeniach wewnętrznej ogniotrwałej powłoki kadzi lub nadmiernym zużyciu obudowy.
Warto zwrócić uwagę na fakt, że w tak ekstremalnie gorącym środowisku istnieje wiele czynników wpływających na możliwość błędnej interpretacji termogramu. Chodzi tu przede wszystkim o zakłócenia rejestrowanego obrazu, które powodują spaliny, płomienie, żużel i popiół. Z tego względu do pomiarów w gorącym środowisku pracy stosuje się kamery mające możliwość filtrowania określonych długości fal, dzięki czemu „odcina się” niepożądane oddziaływanie na rejestrowany obraz warunków otoczenia.
Jednak zastosowanie technik termowizji w hutnictwie i odlewnictwie jest znacznie szersze. Przede wszystkim, ze względu na wysoką temperaturę, kontrola maszyn i parametrów produkcji jest utrudniona. Kamery termowizyjne służą tutaj do wykrywania przegrzanych miejsc i dużych gradientów temperatury, a ponadto kontrolują stopień zużycia ogniotrwałych okładzin urządzeń i maszyn, szczelność wlewnic czy stan przewodów doprowadzających i odprowadzających gazy.
Pomiary termowizyjne wykorzystuje się również do kontroli chłodzenia. Przy obróbce gorącej stali wykorzystuje się m.in. piły i obcinarki używane do skracania stalowych prętów i blach. Muszą być one odpowiednio chłodzone, aby nie zużywały się i nie tępiły zbyt szybko. Przy ustalaniu temperatury pracy tych ostrzy wykorzystuje się kamery termowizyjne. Na podstawie termogramów można efektywnie sterować systemem chłodzącym ostrza. Pod wpływem wysokiej temperatury szybko zużywają się też rolki wykorzystywane do toczenia stalowych prętów i blach. Ich stan techniczny ocenia się również na podstawie pomiarów termowizyjnych.
Termowizja odgrywa też istotną rolę w diagnostyce w przemyśle chemicznym. Nie chodzi tylko o ocenę stanu izolacji termicznej kolumn rektyfikacyjnych czy reaktorów, ale również o kontrolę urządzeń pomocniczych, takich jak sprężarki, rurociągi, zbiorniki czy chłodnice. Termowizję wykorzystuje się też do monitorowania poziomu napełnienia zbiorników.
W systemach produkcji ciepła termowizja jest również niezbędnym narzędziem wykorzystywanym przez pracujące tam służby utrzymania ruchu. Przydaje się ona do sprawdzania kotłów grzewczych i instalacji przesyłu pary wodnej. W ten sposób można również stwierdzić, czy osady nie zaburzyły swobodnego przepływu czynnika grzewczego, co w efekcie obniżyłoby współczynnik przenikania ciepła w wymienniku. Kamerę termowizyjną można też wykorzystać do określenia rozkładu temperatury obudowy skrzyni paleniskowej czy wykrycia pęknięć ogniotrwałej osłony paleniska.
Termowizja ma ponadto zastosowanie w kontroli oddzielaczy skroplin, które otwierają się, odprowadzając nagromadzone skropliny, po czym zamykają, pozwalając na swobodny przepływ pary. Usterki oddzielaczy skroplin powodują powstawanie dużych strat ciepła w instalacji parowej, stąd istotne jest szybkie wykrycie takiej awarii.
Utrzymanie produkcji
Warto zwrócić uwagę na zastosowanie kamer termowizyjnych w analizie produkcji. Technologia ta często służy do kontroli temperatury składników stosowanych w procesie produkcyjnym. Można tutaj wymienić kontrolę właściwego przebiegu procesów termicznych istotnych z punktu widzenia produkcji papieru, szkła czy żywności. Termowizję wykorzystuje się w tym przypadku do kontroli poprawnej pracy zaworów sterujących, odpowiedzialnych za dozowanie płynów i materiałów sypkich wykorzystywanych w procesie wytwarzania. Kluczową rolę odgrywa niedopuszczenie do powstania wycieków i niedokładności w porcjowaniu poszczególnych składników.
Termowizja jest też stosowana przez służby utrzymania ruchu do kontroli pracy pomp, wentylatorów i sprężarek, które muszą pracować w trybie 24/7, aby zachowana została ciągłość i bezpieczeństwo procesów technologicznych. Ponadto termografia jest istotnym elementem produkcji wyrobów szklanych – kontrola urządzeń wykorzystywanych podczas produkcji pozwala uzyskać założone parametry technologiczne otrzymywanego szkła.
Kamery termowizyjne dostępne na rynku
Światowy rynek kamer termowizyjnych jest zdominowany przez kilku dużych producentów, takich jak FLIR Systems, Fluke czy Testo. Oczywiście dostępne są też urządzenia mniejszych firm, a także znacznie tańsze wyroby chińskich producentów. W Polsce oprócz trzech wspomnianych marek sporym uznaniem cieszą się kamery rodzimej produkcji – firm Vigo System i Sonel.
Największym producentem kamer termowizyjnych na świecie jest amerykańska firma FLIR Systems. Co ciekawe, nazwa tej powstałej w 1978 r. firmy wywodzi się od słów Forward Looking InfraRed (FLIR), określających kamery termowizyjne stosowane w wojskowym i cywilnym lotnictwie. Do dziś firma produkuje różnego rodzaju cywilny i wojskowy sprzęt termowizyjny, w tym noktowizory i pracujące w podczerwieni systemy telewizji przemysłowej. Kamery firmy FLIR Systems podzielono na cztery serie: Ex, Exx, T4xx oraz T6xx, które charakteryzują się odpowiednio coraz wyższymi parametrami technicznymi, funkcjonalnością i ceną. Seria Ex to proste kamery termowizyjne ze stosunkowo niewielkimi czujnikami IR, pozwalające mierzyć temperaturę jednocześnie w wielu punktach – od 4800 do 76 800 (w zależności od modelu), zaś najbardziej zaawansowane modele z serii T6xx, wyposażone w sensor o rozdzielczości 640 × 480 px (307 200 punktów pomiaru temperatury), pozwalają mierzyć temperaturę z czułością <20 mK w zakresie od –40 °C do +2000 °C.
Do największych producentów kamer termowizyjnych na świecie zalicza się również firma Fluke. Ta działająca od 1948 r. amerykańska korporacja specjalizuje się w wytwarzaniu różnego rodzaju przyrządów pomiarowych dla przemysłu. Dostępne w ofercie kamery termowizyjne podzielono na trzy grupy – Performance, Professional i Expert. W ten sposób znacznie łatwiej dobrać kamerę do potrzeb przy uwzględnieniu współczynnika jakość/funkcjonalność w stosunku do ceny. Ciekawostką dotycząca kamer Fluke jest technologia Fluke Connect, pozwalająca na bezprzewodową komunikację ze smartfonami i tabletami pracującymi pod kontrolą systemów iOS i Android. Dzięki temu użytkownicy mogą analizować otrzymane wyniki na urządzeniu mobilnym, konsultować je z innymi członkami zespołu czy klientem oraz tworzyć i przesyłać raporty bezpośrednio z miejsca prowadzenia pomiarów. Pojemnościowe ekrany dotykowe ułatwiają natomiast bezpośrednią obsługę samych urządzeń. Cechą charakterystyczną modeli z serii Professional i Expert jest możliwość pomiarów wysokiej temperatury, dochodzącej do +1200 °C.
Z kolei Testo to niemiecki producent różnorodnych przyrządów kontrolno-pomiarowych. W jego ofercie znajdziemy kamery o wysokiej czułości termicznej. Przykładem takiej uniwersalnej kamery o czułości termicznej <50 mK jest model Testo 875-2i. Pozwala on m.in. na łatwe przeprowadzenie kompleksowych pomiarów termowizyjnych podzespołów mechanicznych i elektrycznych. Standardowo kamera pozwala na pomiar temperatury od –30 °C do +350 °C, jednak możliwe jest opcjonalne rozszerzenie jej zakresu pomiarowego do +550°C.
Mająca swoją siedzibę w Ożarowie Mazowieckim firma Vigo System zaliczana jest do światowej czołówki producentów niechłodzonych, fotonowych detektorów podczerwieni. Technologia ich produkcji została opracowana w latach 80. w Wojskowej Akademii Technicznej. Na tej bazie powstają obecnie detektory wykorzystywane w urządzeniach firmy Vigo System. O klasie i jakości produkowanego w Ożarowie sprzętu świadczy fakt, że opracowane i wyprodukowane przez Vigo System detektory podczerwieni pracują obecnie na pokładzie łazika Curiosity, w ramach misji Mars Science Laboratory. Firma ma też status oficjalnego dostawcy podzespołów dla NASA.
W seryjnej ofercie Vigo System znaleźć można kamery z serii VIGOcam oraz moduły termowizyjne IRMOD. W zastosowaniach związanych z utrzymaniem ruchu sprawdzą się modele VIGOcam v5 i VIGOcam v60. Pierwszy z nich to wielofunkcyjna kamera termowizyjna wyposażona w jeden z trzech obiektywów: standardowy – 15° × 11°, szerokokątny – 31° × 23° lub teleobiektyw – 9° × 7°. Obraz termiczny nagrywany jest z rozdzielczością 384 × 288 px. Pracę ułatwia wskaźnik laserowy oraz wbudowana kamera wideo (1600 × 1200 px) wraz z mikrofonem i głośnikiem. Z kolei kamera
VIGOcam v60 została wyposażona w detektor IR o rozdzielczości 640 × 480 px. Również w jej przypadku można wykorzystać trzy różne obiektywy: standardowy – 26° × 19°, szerokokątny –
W ofercie firmy Sonel, polskiego producenta aparatury pomiarowej z siedzibą w Świdnicy, znajdziemy łącznie 12 modeli kamer termowizyjnych. Ciekawymi urządzeniami z punktu widzenia służb utrzymania ruchu są dwie nowe kamery: KT-640 oraz KT-384. Pierwsza z nich to w pełni radiometryczna (rejestrująca temperaturę każdego punktu obrazu) kamera pracująca w rozdzielczości 640 × 480 px.
Pozwala ona na również na rejestrację rzeczywistego obrazu o rozdzielczości 5 Mpx. Technologia Infra Fusion, polegająca na podglądzie połączonych obrazów rzeczywistego i termicznego, pozwala na szybkie zlokalizowanie miejsca usterki.
Druga z kamer, KT-384, to kamera termowizyjna o rzeczywistej rozdzielczości termicznej 384 × 288 px, która pozwala na jednoczesny pomiar temperatury w 110 592 punktach. Jest prosta i intuicyjna w obsłudze. Może być wyposażona w jeden z czterech obiektywów – szerokokątny, standardowy, operacyjny lub teleobiektyw. Badania związane z rozwojem produktów...
Zapraszamy do lektury pełnej wersji artykułu w wydaniu 7-8/2015 miesięcznika "Automatyka"!
source: "Automatyka" 7-8/2015