Czas na cztery zero. Raport specjalny 2018
Materiał prasowy print
Czwarta rewolucja przemysłowa to już zdecydowanie nie wizja przyszłości. To rzeczywistość. Jej istotą nie jest już relatywnie proste wykorzystanie możliwości komputera i oprogramowania w planowaniu czy zarządzaniu produkcją, lecz integrowanie automatyzacji i robotyzacji procesów produkcyjnych z systemami i stworzonymi sieciami oraz ludźmi.
Przemysł 4.0 (Industrie 4.0) – termin ukuty w środowiskach promujących niemiecką myśl techniczną (premiera na targach elektroniki w 2011 r.) – jest młody, a zrobił dynamiczną karierę. I nie przeszkadza fakt, że obejmuje on zbyt szeroki zestaw technologii, zjawisk, procesów, by poddać się ścisłej definicji. Nie wchodząc w zawiłości interpretacyjne, pod terminem tym rozumiemy zarówno zbiór technik (Internet Rzeczy, Cloud Computing, Big Data, sztuczną inteligencją, rozszerzoną rzeczywistość, druk 3D, Digital Twin, współpracujące z człowiekiem automaty i roboty), jak i sposób myślenia o biznesie, zarządzaniu czy budowaniu łańcucha wartości.
Z punktu widzenia biznesowego celu mianem Przemysłu 4.0 określamy wszechobecny w rozwiniętych gospodarkach trend przynoszący firmom konkretne korzyści ekonomiczne – przede wszystkim poprzez obniżenie kosztów wytwarzania, standaryzację i stabilizację jakości, podwyższenie produktywności, możliwość szybkiej reakcji na zmiany w procesie produkcyjnym czy – korzystniej – przewidywanie awarii.
Raport firmy analitycznej International Data Corporation potwierdza to, co wynika z obserwacji rynku i wiodących technologiczne branż przemysłu (m.in. motoryzacja).
Otóż cyfrowa transformacja jest najistotniejszym trendem w globalnej gospodarce. Za trzy lata ponad 90%. przedsiębiorstw będzie korzystać z technologii IT, co specjalnie nie dziwi; ważne, że trzy czwarte aplikacji biznesowych wykorzystywać będzie sztuczną inteligencję. Codziennością stanie się rozszerzona rzeczywistość (AR).
Teraz albo nigdy
Firmy, które nie wejdą na biznesową cyfrową platformę – ostrzegają analitycy – są zagrożone zniknięciem z rynku. Jeśli dodać do tego permanentny brak rąk do pracy, z którym obecnie boryka się polska gospodarka, konieczna staje się decyzja o wprowadzaniu automatów, robotów i technologii cyfrowych. Wysokie koszty wprowadzania nowoczesnych rozwiązań zwracają się szybko, a alternatywa w praktyce nie istnieje. Przemysł 4.0 nie jest opcją rozwoju tradycyjnego przedsiębiorstwa, z której można skorzystać bądź nie.
To imperatyw zmiany, której kierunek już znamy, podobnie jak cel – chodzi o efektywność i redukcję kosztów, ale także szybkość reakcji na wciąż zmieniające się potrzeby konsumenta i inne dynamiczne zjawiska na niestabilnych rynkach.
Firmy, które szybciej wchodzą w nurt tych przeobrażeń, oferują wyższą jakość przy niższych cenach, przejmują rynek i klientów, ale także przyciągają najlepszych pracowników, pogłębiając swoją przewagę. Zdaniem ekspertów Deloitte inwestorzy coraz częściej zwracają uwagę nie na zasoby materialne (fabryki, maszyny), lecz wysoko wyceniają te spółki, które inwestują w innowacyjność, technologie i wiedzę. Przedsiębiorstwa tworzące nowe modele biznesowe oparte na nowych technologiach, które dają nadzieję na duże zyski w przyszłości, mogą osiągać zdecydowanie wyższą wartość niż spółki działające w oparciu o tradycyjne modele.
W kontekście tych trendów oraz ambicji szybko rozwijającej się polskiej gospodarki jedno z najważniejszych pytań o jej przyszłość brzmi – w jaki sposób firmy (wiodące w branżach lub typowe co do skali i struktur) realizują ideę nowoczesnego przemysłu opartego na technologiach, wiedzy i komunikacji? Tak postawione pytanie wymaga, by próbą znalezienia odpowiedzi objąć szersze spektrum zjawisk niż Przemysł 4.0. Hasło „nowego polskiego przemysłu” obejmuje także modernizacje, innowacje organizacyjne, działania na rzecz redukcji kosztów czy efektywności energetycznej, współpracę z nauką, podnoszenie kompetencji kadry.
Jakie znaczenie nadaje się w firmach poszczególnym trendom i zjawiskom współtworzącym polski krajobraz Przemysłu 4.0 (Big Data, Internet rzeczy, robotyzacja i automatyzacja, technologie informatyczne i komunikacyjne, sztuczna inteligencja, innowacyjność i działalność badawczo-rozwojowa). Z jakimi inwestycjami to się wiąże? Jakie były ich motywy i jakie są biznesowe cele, które firma chce w ten sposób osiągnąć?
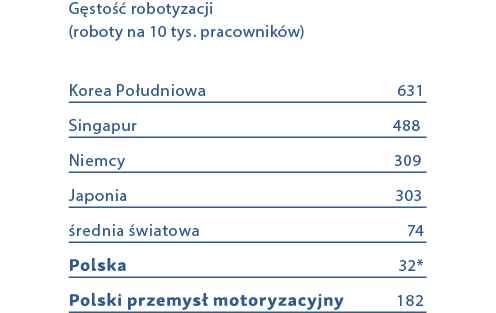
Gęstość robotyzacji. *Na nasz wynik składało się 9,7 tys. robotów obecnych w naszej gospodarce (wzrost o 19 proc. w stosunku do poprzedniego roku).
Ostrożnie, robot
O stanie zaawansowania procesu przemian wiele mówią (choć nie wyczerpują obszaru Przemysł 4.0) dane dotyczące robotyzacji gospodarki. Polska, z gospodarką w pierwszej trzydziestce globalnego rankingu, wciąż nie potrafi przestawić się na automatyzację produkcji. Tak zwana „gęstość robotyzacji” jest nadal niska.
Według danych z raportu IFR (International Federation of Robotics) „World Robotics 2017” Polska odbiega poziomem robotyzacji od średniej światowej. Średnia gęstość na świecie to 74 roboty na 10 tysięcy pracowników w przemyśle – w Polsce mamy ich zaledwie 32.
Odstajemy pod tym względem także od innych krajów naszego regionu. W Czechach wskaźnik ten wynosi 101, a na Słowacji aż 135. Węgry, ze wskaźnikiem robotyzacji 57, także są lepsze od Polski. Z drugiej strony dynamika postępów robotyzacji w Polsce jest bardzo wysoka. Według wcześniejszego raportu IFR między 2016 r. a 2019 r. w regionie CEE średni przyrost liczby robotów wyniesie aż 14 proc. rok do roku. To optymistyczna prognoza i spory potencjał.
Tharsus, brytyjski producent robotów, prognozuje, że czeka nas prawdziwa inwazja maszyn zaprojektowanych do współpracy z ludźmi w wykonywaniu powtarzalnych zadań. Coboty, coraz tańsze, m.in. dzięki malejącym cenom czujników i sztucznej inteligencji, wskazują jeden z kierunków zmian, które wskutek synergii m.in. chmury obliczeniowej i AI – dadzą także mniejszym przedsiębiorstwom szanse, dotychczas rezerwowane dlapotentatów.
Czy z nowych możliwości związanych z upowszechnieniem technologii Przemysłu 4.0 będą umiały skorzystać także polskie firmy?
Wielcy są ostrożni
Przemysł 4.0 daje firmom przewagę konkurencyjną, wzrost rentowności, podnosi jakość i bezpieczeństwo produktów i co za tym idzie – prestiż. Nic dziwnego, że to hasło nęci największe firmy polskiej gospodarki.
Mając relatywnie duże możliwości inwestycyjne, zaplecze kadrowe i naukowo-badawcze mogłyby pełnić rolę pionierów przecierających szlak. Jednak wśród potentatów trudno o przykład kompleksowego podejścia do przemysłowej rewolucji, tj. o wprowadzanie rozwiązań Industry 4.0 jednocześnie na wszystkich poziomach biznesowej struktury.
Ryzyko związane z taką wewnętrzną rewolucją skłania do ostrożności, ale z drugiej strony wdrażanie cząstkowych rozwiązań grozi „silosowatością”. Izolowane, niezintegrowane rozwiązania nie są wystarczająco efektywne, zrażają do kolejnych prób – koło się zamyka.
– W szczególności interesują nas projekty związane z: robotyzacją, automatyzacją, cyfryzacją procesów, z technologiami IT (w zarządzaniu produkcją i firmą), przemysłowym Internetem Rzeczy (IIoT), sztuczną inteligencją, wirtualną czy rozszerzoną rzeczywistością (VR/AR) – deklarują szeroko przedstawiciele PKN Orlen.
Naftowy potentat zwraca też uwagę na „przedsięwzięcia zorientowane na pozyskanie kompetencji związanych z nowymi technologiami (szkolenia, rekrutacja)” oraz na wykorzystanie innowacyjnych rozwiązań. Chodzi tu o współpracę z instytucjami nauki, rozwój bazy laboratoryjnej czy – szerzej – sektora badawczo-rozwojowego.
Naturalnym obszarem implementacji rozwiązań przemysłowego Internetu Rzeczy (IIoT) w firmach, gdzie o wyniku ekonomicznym decyduje masowość produkcji i stabilna praca rozbudowanych i złożonych instalacji wytwórczych, jest utrzymanie ruchu.
„Dzięki czujnikom, algorytmom, zaawansowanej analityce i umiejętności wyciągania wniosków z informacji firmy produkcyjne mogą w sposób bardziej efektywny eliminować wąskie gardła, np. w przypadku PKN Orlen zmniejszać postoje remontowe poprzez zastosowanie utrzymania zapobiegawczego, tzw. predictive maintenance” – czytamy w opracowaniu płockiego potentata naftowego.
Dla Lotosu pojęcie Przemysłu 4.0 nie uosabia kolejnej rewolucji przemysłowej, lecz jest „naturalnym krokiem na drodze ewolucji cyfrowej”. Technologie IIoT są stosowane w rafineriach od kilkunastu lat. W Lotosie stabilność i niezawodność procesów wytwórczych wspierana jest przez tzw. autopiloty kluczowych instalacji produkcyjnych, które eliminują zmienność i zakłócenia procesu wytwórczego, jednocześnie lokując go bliżej ekonomicznego optimum. Technologia ta analizuje bieżące ograniczenia techniczne i eliminuje kluczowe przyczyny utraty stabilności, jednocześnie redukując liczbę interwencji operatora. Analizy wskazały jednoznacznie, że instalacje z dobrym autopilotem wykazują się większą wydajnością i dostępnością, mniejsza jest również liczba występujących na nich awarii i nieplanowanych postojów.
Innym przykładem z obszaru bezpieczeństwa procesowego są treningowe symulatory procesowe – identyczne co do zasady działania z tymi wykorzystywanymi w lotnictwie, na tyle doskonałe, że trudno odróżnić „wirtualną rzeczywistość rafinerii” od rzeczywistego procesu. Przykładem konkretnych rozwiązań wykorzystujących technologie komunikacyjne, czujniki i automatykę może być projekt Smart Helmet, który Lotos zamierza realizować wspólnie ze start-upem 3dplab. „Sprytny Hełm” to de facto system monitoringu w czasie rzeczywistym pracowników przebywających na terenie instalacji, który ma za zadanie zapewnić bezpieczeństwo poprzez dwustronną komunikację oraz identyfikację ewentualnych skażeń. Lotos rozwija kompetencje w obszarze zaawansowanej analizy danych, weryfikuje możliwości implementacji rozwiązań opartych na wykorzystaniu sztucznej inteligencji oraz zastosowaniu praktycznym modelowania predykcyjnego. W gdańskiej spółce pod obserwacją są też obszary robotyzacji, głębszej automatyzacji i autonomizacji, integracji infrastruktury i danych.
Tradycyjnie, ale inteligentnie
W ArcelorMittal Poland innowacje mają charakter bardziej tradycyjny, co nie zmienia faktu, że przynoszą znaczące korzyści środowiskowe i ekonomiczne zgodnie ze strategicznym hasłem „zero marnotrawstwa”. Modernizacja wielkiego pieca w Krakowie, remont nagrzewnic, nowy system chłodzenia wielkiego pieca to rozwiązania niewchodzące wprawdzie w obszar Przemysłu 4.0, za to znacznie zmniejszające wpływ na środowisko (mniejsze zużycia wody i koksu, ograniczenie emisji). Filtry hybrydowe w systemie odpylania taśm spiekalniczych w Dąbrowie Górniczej to pierwsze tego typu instalacje w Polsce. Na skłonność do inwestowania w nowe technologie w przypadku hutniczego potentata wpływ ma przyszłość polityki ochrony klimatu, z którą związane regulacje silnie ograniczają konkurencyjność europejskiego sektora stalowego.
Ograniczony zakres remontu wielkiego pieca nr 2 w hucie ArcelorMittal w Dąbrowie Górniczej pozwoli wydłużyć zdolność pieca do pracy o 3–5, a nie o kilkanaście lat. W tym czasie firma będzie obserwować zmiany na rynku i zastanawiać się, czy w warunkach nowej polityki klimatycznej wydawanie na generalny remont pieca ok. 300 mln złotych będzie miało szanse się zwrócić. Obecny remont kosztuje ok. 85 mln złotych.
Tomasz Ślęzak, członek zarządu, dyrektor energii i ochrony środowiska ArcelorMittal Poland, nie wyklucza, że remontowany piec zastąpiony zostanie piecem elektrycznym, ale i tę decyzję warunkują ceny uprawnień do emisji CO2 rzutujące na ceny energii powstającej przecież w Polsce głównie ze spalania paliw kopalnych.
Polski miks energii oparty na własnych zasobach węgla (zapewne jeszcze przez kilka najbliższych dekad) określa skłonność do inwestowania w nowe technologie w branży węglowej, co ma kluczowe znaczenie dla dostawców nowoczesnych urządzeń.
Zdaniem Mirosława Bendzery, prezesa Famuru, innowacyjność cechuje branżę wydobywczą już od dłuższego czasu, a „skok technologiczny” rozciąga się w tej specjalności na ostatnie 30 lat, kiedy to wzrósł poziom automatyzacji służący efektywności wydobycia oraz bezpieczeństwu pracy. Trend ten wiąże się w niektórych warunkach również z robotyzacją (czyli eliminowaniem siły ludzkiej) procesu wydobywczego i transportu urobku. Inny wskazany przez Bendzerę trend obejmuje wdrażanie rozwiązań informatycznych i komunikacyjnych, które pomagają monitorować proces produkcji, ale także pracę maszyn i ludzi. Trzecia grupa działań łączy oba systemy, sięgając tym samym faktycznie w obszar Przemysłu 4.0, pozwalając uzyskiwać dane, które są podstawą bieżącej kontroli, umożliwiającej reakcję on-line, czyli pozwalają analizować funkcjonowanie kopalni w czasie rzeczywistym. Famur opiera swoją działalność innowacyjną głównie na własnych biurach badawczo-rozwojowych oraz pracy około 400 inżynierów. W Jastrzębskiej Spółce Węglowej proces cyfryzacji i informatyzacji jest zapisany w strategii do 2030 r. w programach Jakość i Efektywność. Obecnie prowadzi się kilka projektów w dziedzinach „chętnie poddających się” cyfryzacji. Chodzi m.in. o modelowanie złoża 3D i harmonogramowanie produkcji. Wymagają one zaangażowania kopalnianych działów mierniczo-geologicznych i co oczywiste, zakupu nowoczesnego sprzętu. Po wcześniejszych zakupach nowoczesnych tachimetrów (optyczny instrument geodezyjny przeznaczony do pomiarów), mierniczy z JSW otrzymali skanery ręczne. To cyfrowy sprzęt oparty na powszechnie znanej technologii, który usprawnia i przyspiesza sporządzanie dokumentacji mierniczo-geologicznej. Ponadto jest wykorzystywany w miejscach z ograniczonym dostępem, co przyczynia się do poprawy bezpieczeństwa pracy geodetów górniczych.
– Musimy pamiętać, że w warunkach kopalni i zarządzania procesem wydobycia faza przygotowania produkcji ma kluczowe znaczenie dla jej racjonalności i trafności.
Oznacza ona zebranie niezbędnych informacji o charakterze wybieranego złoża, zwłaszcza czynnikach ograniczających prowadzenie eksploatacji – zaznacza Artur Dyczko, zastępca prezesa zarządu JSW ds. strategii i rozwoju.
Inwestycje w JSW to odpowiedzi na konkretne potrzeby wynikające ze specyfiki procesu wydobywczego. Przy tak dużej koncentracji robót górniczych i przygotowawczych oraz robót eksploatacyjnych stosowanie nowoczesnych urządzeń i przyrządów pomiarowych zapewnia wysoką dokładność przy stosunkowo krótkim czasie pomiaru, nie powodując przerw w ruchu zakładu górniczego.
Teraz kompleksowo
Branża automotive to zdecydowanie awangarda Przemysłu 4.0 w Polsce. Tu wdrażanie rozwiązań ma charakter kompleksowy i postępuje praktycznie u wszystkich liczących się producentów. Decyduje o tym nie tylko prosty dostęp do najnowszego know-how światowych potentatów, ale także ich presja na dostawców, specyfika branży (produkcja seryjna, złożony charakter produktu finalnego, doświadczenia w robotyzacji), jak również wymagania rynku (kastomizacja, krótkoseryjność i wahania popytu, restrykcyjne normy jakościowe, ostra konkurencja). Nie bez znaczenia są cenione przez inwestorów kwalifikacje polskiej kadry. Wśród funkcjonujących już rozwiązań wykorzystujących technologie Internetu Rzeczy, które wymienia Andrzej Korpak, dyrektor gliwickiej fabryki Opla, jest system „weld wizzard”, który zbiera i analizuje dane z systemów zgrzewania.
Algorytm przekazuje przetworzoną i spersonalizowaną informację na temat stanu urządzeń oraz samego procesu. Informacje te są wykorzystywane na poszczególnych poziomach zarządzania oraz przez służby utrzymania ruchu. System wyposażony jest w moduł przewidywania, który na podstawie analizy danych i zdarzeń historycznych informuje o potencjalnych awariach oraz anomaliach. Dzięki temu można im przeciwdziałać lub minimalizować ich skutki.
Przy montażu elementów pojazdu Opel stosuje system Big Data z wbudowanymi elementami „poka-yoke”, czyli metody eliminacji pomyłek. Bazuje na elektronicznych kluczach i sterownikach spiętych w system komputerowy z elementami wizualizacji. Informacje o poprawności wykonania danej operacji są przekazywane w czasie rzeczywistym do operatora oraz archiwizowane w bazie, dzięki czemu możemy odtworzyć historię budowy dla każdego pojazdu. Upraszczając – oczujnikowane narzędzia kontrolują poprawność wykonywanych przez człowieka operacji. Taka dokumentacja procesowa to kwestia bezpieczeństwa, a w niektórych krajach norma warunkująca dopuszczenie pojazdu do ruchu. Wśród korzyści Korpak wymienia mniejszą pracochłonność i liczbę analiz potrzebną do skutecznego utrzymania ruchu w zakładzie. Zmiany 4.0 w toczących się wfabryce procesach podniosły produktywność, pozwalają eliminować błędy, a tym samym zapewniają wysoki poziom jakości przy zmniejszeniu nakładu pracy.
Alstom Konstal, znany producent nowoczesnych środków transportu publicznego, może być kolejnym przykładem, wciąż rzadkiego na polskim rynku, kompleksowego podejścia do wdrażania rozwiązań Przemysłu 4.0. Alstom opracował spójny ekosystem cyfrowy w całym procesie przemysłowym, od etapu inżynieryjnego do usług. Dzieje się to w ramach programu „Smart Operations”. Został zainicjowany na początku 2017 r., a jego zakres obejmował 90 zakładów i magazynów firmy. Nazwy filarów programu wiele mówią o ich specyfice: Fabryka Przyszłości, Magazyn Przyszłości, Druk 3D, Cyfrowy Łańcuch.
– Wspomniany już program „Smart Operations” wykorzystuje nasze obecne, podstawowe systemy IT, a także rozwiązania cyfrowe właściwe dla naszego sektora, zapewniające wsparcie w związku z wyzwaniami, którym stawiamy czoła – deklaruje Radosław Banach, prezes spółki Alstom Konstal.
Technologie cyfrowe łączą maszyny, produkty oraz zespoły, stwarzając nowe możliwości, m.in. symulacje wirtualne, zaawansowane analizy, drukowanie przestrzenne, ekspertyzy zdalne i współpracę w czasie rzeczywistym.
Jako przykład można wymienić technologię Holo-maintenance, która polega na wyświetlaniu środowiska rozszerzonej rzeczywistości za pomocą okularów, co pozwala przekazywać pracownikom wskazówki dotyczące realizacji ich zadań lub skany 3D, uwzględniające geometrię rzeczywistych obiektów oraz ułatwiające porównywanie obrazów z trójwymiarowymi makietami, w celu wykrycia ewentualnych niedociągnięć.
Cyfrowy ekosystem w Alstomie przyspiesza współpracę oraz zwiększa tempo działania, pokonując barierę przestrzenną. Narzędzie zwane Delmia pozwala zespołom przemysłowym pozyskiwać informacje konsolidowane w czasie rzeczywistym przez Dział Inżynierii. Ułatwia to organizację pracy na liniach produkcyjnych, dzięki zamontowaniu ekranów i tabletów, które pozwalają na przekazywanie wskazówek pracownikom.
Stopniowo wprowadzane są elementy wirtualnej rzeczywistości i druku 3D. Zastosowanie sprzętu do wirtualnego malowania symuluje tę czynność z wykorzystaniem okularów 3D, co pozwala zaoszczędzić czas i farbę. Przy symulowaniu gestów stosuje się algorytmy odpowiadające za pomiar jakości pracy oraz ilości wykorzystanej farby.
– Przejście od wirtualnego elementu do rzeczywistej części jeszcze nigdy nie było tak szybkie. W ciągu kilku godzin jesteśmy w stanie wyprodukować części, aby przetestować je w rzeczywistych warunkach – podkreśla Banach. Możliwości druku 3D wykorzystuje także inny obecny w Polsce potentat – producent oświetlenia Signify (dawniej Philips Lighting), wskazując wśród motywów (skrócenie czasu dostaw i większa elastyczność prototypowania) także na kwestie zrównoważonego rozwoju – redukcja odpadów i emisji zanieczyszczeń środowiska zarówno po stronie użytkownika, jak i producenta.
Rozwijany w Signify program Telecaster umożliwia zamówienia online oprawy oświetleniowej w oparciu o dostępne predefiniowane modele 3D oraz w oparciu o model opracowany wyłącznie pod wymagania klienta. Powstał specjalny interfejs do składania zamówień, a po stronie produkcyjnej podjęto działania przekształcające jedną z fabryk w park profesjonalnych przemysłowych drukarek 3D, dzięki czemu możliwa jest produkcja opraw o nieograniczonym kształcie, szerokiej palecie kolorów oraz z różnych materiałów.
Zastosowanie druku 3D w procesach prototypowania oraz przygotowania narzędzi rozwija także Nowy Styl, polski potentat eksportowy, dla którego dizajn i relacje z wymagającymi klientami to podstawowe biznesowe zasoby. – Technologią VR posługujemy się w zakresie symulowania dla naszych klientów ich przyszłego środowiska pracy – informuje Tomasz Bardzik, dyrektor operacyjny w Grupie Nowy Styl, zaznaczając też, że firma szuka zastosowań Internetu Rzeczy w swoich produktach.
Jakość, głupcze…
Branżą w szczególny sposób uwarunkowaną, jeśli chodzi o wdrażanie rozwiązań Przemysłu 4.0, jest spawalnictwo – sektor pełniący rolę „służebną” wobec ważnych branż przemysłu. Tradycyjnie są to branże, gdzie mamy do czynienia z wysokimi wymaganiami w zakresie jakości, jak na przykład przemysł offshore, czy też z wysoką wydajnością, jak to ma miejsce w przemyśle samochodowym. By sprostać tym potrzebom, konieczne jest inwestowanie w robotyzację i automatyzację procesów spawalniczych oraz systemów sterowania jakością w czasie rzeczywistym.
Wielu producentów urządzeń i materiałów spawalniczych ma swoje przedstawicielstwa w Polsce, a jednocześnie szereg polskich firm wykonuje na zlecenie firm zachodnich konstrukcje spawane (wieże wiatrowe, elementy mostów, części silników lotniczych czy podzespoły samochodów osobowych i ciężarowych).
Jednak coraz częściej, jak przekonuje prof. Andrzej Klimpel z Politechniki Śląskiej, zdarza się, że w nowe technologie inwestują branże, które są kojarzone raczej z mało skomplikowaną produkcją, jak na przykład konstrukcje stalowe, maszyny rolnicze itd.
– Bardzo często inwestycja w rozwój technologii wymuszana jest przez ich klienta, który oczekuje dzisiaj wysokiej jakości również w przypadku prostej produkcji – podkreśla prof. Kimpel. – Znamy przypadki kompleksowej robotyzacji spawania takich elementów jak na przykład ogrodzenia. Istotnym aspektem zagadnienia jest również ciągłe dążenie do zwiększania wydajności produkcji spawalniczej, co pozwala na podnoszenie konkurencyjności i zdobywanie nowych rynków.
Nowe tereny – budowlanka
Firmy budowlane, z racji specyfiki swojej podstawowej działalności, w powszechnej opinii nie kojarzą się z innowacyjnością i inwestycjami w nowoczesne technologie. Jednak zdaniem ekspertów Deloitte w najbliższych latach sytuacja się zmieni. Budowlanymi trendami 4.0 mają być: wykorzystanie dronów, druk 3D, Internet Rzeczy oraz inteligentne materiały.
Inwestycji na tym polu dokonują już najwięksi gracze – Skanska, ACS, Strabag czy Vinci. Ostatnia z wymienionych firm pozyskała (fuzje i przejęcia) kilka podmiotów specjalizujących się w cyfrowych technologiach. Firmy budowlane, widząc potrzebę technologicznej ucieczki do przodu, inwestują w start-upy lub szukają partnerstwa z instytucjami, by pozyskać nowe kompetencje. Z kolei firmy technologiczne (na globalnym rynku Tesla i Google) coraz częściej interesują się rynkiem inwestycji budowlanych.
Wśród najbardziej ofensywnych kierunków wdrożeń firmy wymieniają fotowoltaikę zintegrowaną z budynkami (BIPV) wykorzystującą panele jako elementy elewacji. Produkowane ogniwa słoneczne są instalowane nie tylko na dachach budynków, ale zastępują tradycyjne materiały budowlane. Technologie nadają też nowej dynamiki metodom prefabrykacji, skracając i standaryzując procesy budowlane. Także w budownictwie, podobnie jak w przemyśle, nowe przyczółki zdobywa druk 3D. Na wdrożenia za wcześnie, ale rzecz warta jest zauważenia, bo nad technologią pracują rodzimi naukowcy. Chodzi o drukarkę wykorzystującą mieszankę betonową i o międzywydziałowy zespół z Uniwersytetu Technologicznego w Szczecinie. – Skupiliśmy się na testach – informował w sierpniu 2018 r. dr inż. Adam Zieliński z wydziału budownictwa i architektury tej uczelni. – Zbudowaliśmy stosunkowo małą drukarkę, wykonujemy elementy testowe służące do badań, w tym modele struktur budowlanych, takich jak ściany i słupy. Drukujemy też elementy małej architektury. Przykładem zmagania się z konkretnymi, dość typowymi dla rodzimych firm problemami z obszaru integracji technologicznej jest krajowy producent materiałów budowlanych Ceramika Paradyż. Firma inwestuje też w informatyzację procesu produkcji. Świadomość konieczności zmian jest tu wysoka, etap zaawansowania – wstępny.
Głównym motywem wyboru wdrażanych i planowanych w Ceramice Paradyż rozwiązań jest potrzeba kompleksowego opomiarowania i zinformatyzowania procesu produkcyjnego płytek na wszystkich jego etapach. Zbieranie w czasie rzeczywistym danych o procesie produkcyjnym oraz o przetwarzanych półproduktach i produktach, a także elektroniczna archiwizacja tych danych i szybki do nich dostęp pozwolą na zarządzanie procesem produkcyjnym online. – Posiadamy pewne rozwiązania, ale nie obejmują one całości procesu produkcyjnego, tylko jego wybrane fragmenty – wyjaśnia Ferdynand Gacki, dyrektor rozwoju technologii wCeramice Paradyż. – Jest to związane z wykorzystaniem narzędzi informatycznych, które sterują poszczególnymi urządzeniami w naszych fabrykach. Problem polega na tym, że cały proces produkcyjny jest oparty na maszynach różnych producentów. Każdy z nich ma odmienne rozwiązania systemowe, związane ze sterowaniem tymi urządzeniami i niepracujące w jednym systemie.
Dlatego istnieje potrzeba kompatybilności wszystkich systemów obsługujących wszystkie urządzenia w procesie w jeden system.
Sztuka cyfrowego zarządzania
W Grupie Atlas inwestycje w zakresie cyfryzacji sprowadziły się w ostatnich latach do informatyki zarządczej – ściślej – do trzech dużych wdrożeń w trzech różnych obszarach. Chodzi o System SAS Visual Analytics w dziedzinie analizy i raportowania danych, w tym planowania budżetowania, IFS Applications w zakresie zarządzania procesami produkcyjnymi, ich harmonogramowania i monitorowania oraz Platformę IBM Connections – perspektywiczne narzędzie scalające podmioty Grupy w wirtualną firmę, w ramach której działają zespoły projektowe, niezależne od formalnych podziałów, struktury organizacyjnej i właścicielskiej.
Motywy tych wdrożeń? System analizy i raportowania danych wdrożony został celem ujednolicenia prezentacji danych z dotąd różnych funkcjonujących w poszczególnych podmiotach Grupy Atlas systemów i – tym samym – zapewnienia bieżącego dostępu do danych i podejmowania na tej podstawie decyzji. Inwestycja w cyfrowe rozwiązanie w obszarze systemów produkcyjnych związana była z potrzebą optymalizacji procesu wytwarzania wyrobów i poprawy jego płynności.
W przypadku Platformy IBM Connections celem była integracja, ale nie jak w Ceramice Paradyż na poziomie zakładu, lecz w obszarze zarządzania rozrośniętą i skomplikowaną strukturą biznesową. Atlas wymienia wśród celów „konkretne potrzeby w kwestii usprawnienia procesów zarządczych” i „optymalizację kosztów prowadzenia biznesu”.
– Wdrożenie platformy IBM Connections miało wpłynąć na usprawnienie i przyspieszenie procesu konsolidacji działających w ramach Grupy Atlas spółek o zróżnicowanych strukturach, stylach zarządzania i odmiennej kulturze, ale bez ryzyka związanego z „nieostrożną” centralizacją – wyjaśnia Henryk Siodmok, prezes Grupy Atlas. – Potrzeba była tu czytelna: przenoszenie dobrych praktyk, procesów oraz kreowanie relacji biznesowych, komunikacji dwukierunkowej i śledzenie postępów zmiany. Korzyści z wdrożenia rozwiązań informatycznych w zarządzaniu produkcją to przede wszystkim możliwość harmonogramowania i monitorowania produkcji, co pozwala np. na wydłużenie serii produkcyjnych, a tym samym obniżanie kosztów produkcji (szacunkowo rzędu 4 proc. w skali firmy). Bieżący monitoring zużycia surowców, w tym np. funkcja śledzenia zapasów online, daje możliwość szybszej i bardziej skutecznej reakcji na zagrożenia (np. braki). To przekłada się wprost na poprawę płynności procesów produkcyjnych i wyeliminowanie przestojów. Platforma IBM Connections zmienia profil i zestaw kompetencji w firmie. Dodatkowe elementy platformy pozwalają zbierać i systematyzować wiedzę. Tak pomyślana konsolidacja oznacza otwarcie kanałów komunikacji i wyrównywanie do najwyższego poziomu standardów i praktyk zarządzania.
Jeszcze bliżej odbiorcy
W niemal wszystkich rozmowach z przedstawicielami firm przemysłowych pojawia się w końcu rynek i klient jako ostateczny cel wprowadzania wszelkich innowacji technologicznych. Część z nich dotyczy odbiorców bezpośrednio, wkracza w obszar relacji producent–dystrybutor–użytkownik. Grupa Nowy Styl stosuje technologie i prowadzi prace rozwojowe w większości obszarów Przemysłu 4.0 – „w zależności od potrzeb wynikających z biznesu”. – Praktycznie wszystkie systemy wspomagające realizację procesów obsługi klienta, produkcji i dystrybucji są zintegrowane i zautomatyzowane – deklaruje Tomasz Bardzik, dyrektor operacyjny w Nowym Stylu. – Tego rodzaju projekty, na różną skalę, prowadzimy ciągle w całej Grupie nie tylko na poziomie produkcji, ale w całym łańcuchu wartości, jakie oferujemy swoim klientom. To naturalne – narzędzia 4.0 służące personalizacji i kastomizacji produktu wykraczają z fabrycznej hali w kierunku rynku. To istotny segment innowacji zależny jednak ściśle od specyfiki firmy i jej ekspozycji na masowego odbiorcę. Owszem, to masowość i efekt skali decydują o sile wielkich firm, ale to narzędzia Przemysłu 4.0 dają odpowiedź na wymaganą przez rynek indywidualizację popytu; pozwalają zrealizować paradoks – masowe dostosowywanie produktów do potrzeb klientów.
– Dla producentów takie podejście jest szansą na zwiększenie atrakcyjności ich oferty i budowanie w ten sposób przewagi konkurencyjnej – zauważają specjaliści Orlenu.
PKN Orlen personalizuje ofertę dla członków swojego programu lojalnościowego, a techniki Big Data stwarzają tu nowe możliwości. Rozwój programu lojalnościowego w oparciu o aplikację mobilną to według Orlenu „dźwignia pogłębionej wiedzy o kliencie”.
Konkurencja o klienta toczy się nie tylko wewnątrz branży paliwowej – coraz większa jest też rywalizacja między branżami. Użytkownicy oczekują, że będą mieć dostarczony taki standard i taką szybkość obsługi, do których przyzwyczaili się, korzystając ze smartfonów czy dokonując zakupów w Internecie (np. możliwość korzystania z automatycznych terminali płatniczych na stacjach paliw – przy dystrybutorach oraz w pawilonach handlowych).
Oferowanie produktów dopasowanych do potrzeb klienta będzie, co podkreślają specjaliści z Orlenu, w dużym stopniu zależeć od sprawności systemu analityki danych, które są pozyskiwane z inteligentnych czujników, a także z innych źródeł, w tym z mediów społecznościowych.
Analizy takie jak bieżące badanie wzorców „współkupowania” to już codzienna praktyka. Stworzenie rekomendacji kolejnego produktu do zaproponowania klientowi stojącemu przy kasie jest łatwiejsze dzięki statystycznej analizie historii zakupów. Cyfryzacja relacji z klientem dotyczy wszystkich branż – także tych „ciężkich” i tradycyjnych. ArcelorMittal uruchomił platformę Steel Advisor for Industry. Ten internetowy przewodnik pomaga klientom znaleźć odpowiedni produkt w zależności od docelowego zastosowania.
W branży spożywczej zmienne trendy konsumpcyjne wymuszają na firmach ciągłą elastyczność i reakcje na nowe oczekiwania konsumentów.
– Klienci, kierując się modą, wpływem mediów społecznościowych, globalizacją przepisów oczekują nowych, ciekawych produktów. Zmieniają się też wymogi rynkowe związane z przestrzeganiem zasad higieny, świeżości produktów i bezpieczeństwa żywności, które stają się bardzo rygorystyczne. Produkty niespełniające określonych wymagań albo nie będą mogły trafić na rynek, albo nie przyciągną klientów – uważa Marcin Zalasa, dyrektor ds. kluczowych klientów (przemysł spożywczy) w firmie ABB. Dlatego Regionalne Centrum Aplikacji Zrobotyzowanych ABB w Warszawie projektuje swoje systemy w taki sposób, aby łatwo można było przeprogramować dane rozwiązanie i zastosować je dla szerokiego portfolio produktów, w ten sposób lepiej odpowiadając na trendy i oczekiwania rynku. Ceramika Paradyż widzi ścisły związek Przemysłu 4.0 zprocesem kastomizacji. – Dziś produkujemy płytki ceramiczne, jutro praktycznie błyskawicznie będziemy mogli rozpocząć produkcję np. wielkoformatowych stołów, blatów, parapetów czy siedzisk wykonanych zceramiki – uważa Ferdynand Gacki, dyrektor rozwoju technologii. – Przecież dzisiaj to potrzeby klienta rządzą rynkiem i jeżeli będą się one zmieniać, będziemy w stanie szybciej na te zmiany zareagować, oferując możliwość tworzenia własnej wizji wyrobu.
Przykład Grupy Powen-Wafapomp, dostawcy urządzeń dla przemysłu energetycznego, wydobywczego oraz petrochemicznego, pokazuje inne oblicze nowoczesnego polskiego przemysłu – to firma równie mocno jak liderzy technologicznej rewolucji zorientowana na rynek i niezwykle wymagającego klienta.
Powen-Wafapomp zdecydował się zainwestować 21,5 mln zł (projekt współfinansowany przez UE) we własne Centrum Badawczo-Rozwojowe. To przykład podmiotu z wielkimi tradycjami i renomą, stojącego dopiero uprogu rozwiązań Przemysłu 4.0, ale produkującego zaawansowane technicznie układy, z własnym zapleczem projektowym, nagradzanego za innowacyjność. – Chcemy wchodzić na rynek z nowymi rozwiązaniami, dedykowanymi pod indywidualne potrzeby klientów. Dzięki Centrum Badawczo-Rozwojowemu będziemy mogli rozwijać nowoczesne technologie, weryfikować parametry projektowanych urządzeń.
Dla Grupy Powen-Wafapomp innowacje to niekoniecznie „odkrywanie czegoś całkiem nowego”; raczej systematyczne usprawnianie istniejących rozwiązań. – Aby z powodzeniem funkcjonować na rynkach, szczególnie zagranicznych, musimy dysponować możliwie najlepszą bazą – argumentuje Piotr Kańtoch, prezes firmy. – Posiadanie nowoczesnego Centrum Badawczo-Rozwojowego pozwoli nam skupić się na optymalizowaniu efektywności energetycznej pomp i układów pompowych.
Uwaga, czynnik ludzki
Niezależnie od tego, czy Przemysł 4.0 uznamy za re-, czy za ewolucję, oczywisty staje się wpływ tych przeobrażeń na rynek pracy. Aktualny aspekt tej wzajemnej zależności to deficyt na rynku pracy dotyczący przede wszystkim zawodów inżynierskich, informatyków programistów, ale także specjalistów z kompetencjami do obsługi urządzeń, systemów, zaawansowanej automatyki i robotyki. Druga strona medalu – dotycząca nieco bardziej odległej perspektywy – to obawy o miejsca pracy, które zapewne znikną w wyniku rozwoju technologii. Zgodnie z raportem firmy doradczej PwC „Rynek pracy przyszłości. Czynniki kształtujące rynek pracy do 2030 roku”, 40 proc. istniejących zawodów może zostać „zredukowanych” przez sztuczną inteligencję, która użyta w maszynach, robotach i oprogramowaniu jest w stanie zastąpić człowieka. W ich miejsce narodzą się nowe, dla których obecnie nie ma nawet nazwy.
Kluczowe staje się w tym kontekście pytanie: co się nie daje zautomatyzować? Projektowanie, kreatywność, innowacyjność. Współczesny łańcuch wartości preferuje „twórców biznesu”. Ci, którzy dostarczają materiały, części zamienne i podzespoły, mogą zostać – i zapewne będą – wyeliminowani przez tańszych dostawców. Dotyczy to zarówno firm, jak i całych gospodarek, które swoje modele rozwoju oparły na przewagach związanych z niskimi kosztami pracy. Więcej – analogia da się zastosować do poziomu pracowników, wśród których zagrożeni „wyeliminowaniem” z przyszłego rynku pracy mogą czuć się ci, którzy wykonują czynności proste, powtarzalne, niewymagające wyższych kwalifikacji. W gliwickich zakładach Opla zmniejsza się zapotrzebowanie na pracowników wykonujących proste i powtarzalne prace, ale z drugiej zwiększa się popyt na wykwalifikowanych. Przy czym niekoniecznie chodzi o inżynierów, a raczej o wyspecjalizowanych pracowników produkcyjnych i utrzymania ruchu, którzy potrafią obsługiwać roboty, linie zautomatyzowane, rozwiązywać podstawowe problemy techniczne.
– Widzimy coraz większy udział inżynierów automatyków, IT oraz robotyków w naszym zespole – zaznacza Andrzej Korpak, dyrektor wytwórni. – Wiele rozwiązań o charakterze 4.0 wymyślamy i wdrażamy sami, dzięki temu, że siłą naszego zakładu są świetni inżynierowie.
Stocznia Crist z Gdyni kupiła w tym roku roboty spawalnicze i rozpoczęła szkolenie pracowników, którzy będą je obsługiwać. Spółka chce poprawić efektywność i ograniczyć zapotrzebowanie na trudnych do pozyskania na rynku pracowników produkcyjnych. Nieco odległy od przemysłu, ale potencjalnie uniwersalny model biznesowy pokazuje, jak może wyglądać odpowiedź na powyższe dylematy.
– Nasz model współpracy wygląda tak, że przychodzimy do klienta i zadajemy kilka pytań o wykonywane czynności. Jeżeli rozpoznajemy miejsca, w których robot mógłby być zaprzęgnięty do pracy, przygotowujemy go, a miesięczną opłatę pobieramy dopiero, kiedy robot zacznie wykonywać realną pracę. Opłata za robota jest niższa niż wynagrodzenie pracownika. Dlatego robotyzacja jest szybka, prosta, nie wymaga nakładów z góry ani kompetencji IT po stronie klienta – wyjaśnia Konrad Jakubiec, członek zarządu Digital Teammates, dojrzałego start-upu współpracującego z sektorem usług finansowych.
Odpowiedzią PKN Orlen na trendy związane z gospodarką cyfrową jest uruchomienie programu szkoleniowego, którego celem jest przygotowanie specjalistów m.in. w zakresie wykorzystywania zaawansowanej analityki danych. – Mamy świadomość tego, że wejście w Przemysł 4.0 wymaga innych kompetencji niż te, które do tej pory stosowaliśmy w różnych obszarach funkcjonowania organizacji, jak np. te potrzebne do funkcjonowania zakładu produkcyjnego – twierdzą specjaliści z Orlenu.
Wnioski? Konkretne rozwiązania? Systemy motywacyjne w gospodarce 4.0 powinny zachęcać do poszukiwania i testowania nowych rozwiązań, podejmowania ryzyka, dzielenia się najlepszymi praktykami. Naftowy potentat wdrożył więc „Rynek Szans” – platformę ułatwiającą zaangażowanie pracownika w projekty multidyscyplinarne, wykraczające poza specjalizację działu, w którym pracownik jest zatrudniony. W ten sposób pracownicy mogą wykorzystywać swoją wiedzę, dzielić się doświadczeniami, poszerzać kompetencje.
Alstom Konstal ściśle współpracuje z polskimi uczelniami, m.in. Politechniką Śląską i Politechniką Krakowską. W ciągu ostatnich czterech lat firma zrekrutowała i wyszkoliła około stu inżynierów produkcyjnych, specjalizujących się w różnych dziedzinach projektowania pociągów.
To według Alstomu solidne fundamenty, aby co najmniej dwukrotnie zwiększyć tę liczbę w ciągu najbliższych dwóch-trzech lat. Wartością biznesową może być… odsunięcie pracownika od wykonywania pomiarów, niejednokrotnie obarczonych dużym błędem, i przekwalifikowanie go do monitorowania i nadzoru produkcji. System do zbierania danych i ich analizy on-line pozwala (to przykład z Ceramiki Paradyż) łatwiej uczyć się na popełnianych błędach. Można krok po kroku odtworzyć proces produkcji z danego dnia i sprawdzić, na jakim etapie powstało najwięcej błędów, by im w przyszłości zapobiegać. Wyzwanie stanowi natomiast zwykle zapewnienie wykwalifikowanej kadry do obsługi systemów, a także samych maszyn i urządzeń. Dotyczy to nie tylko pracowników wykonawczych, bezpośrednio obsługujących maszyny, ale także kadry zarządzającej średniego szczebla.
Progi, bariery, hamulce
Jedną z barier może być nadal wysoki koszt (np. stanowisk zrobotyzowanych), a więc i długi czas zwrotu z inwestycji w innowacyjne rozwiązania technologiczne. W praktyce decyzje zależą od tego, jakie cele stawia sobie dana organizacja. Jeżeli jest nastawiona, poza oszczędnościami czy zwiększeniem zysku, również na zrównoważony rozwój, to jest bardziej prawdopodobne, że zainwestuje w rozwiązania, których zwrot z inwestycji będzie dłuższy. W przypadku mniejszych podmiotów przyczyny mogą być bardziej prozaiczne. – Właściciele małych i średnich firm zwyczajnie nie mają czasu na refleksję dotyczącą korzyści z wdrożenia rozwiązań zdziedziny IV rewolucji przemysłowej – uważa Tomasz Haiduk, członek zarządu, dyrektor branż przemysłowych w firmie Siemens.
Jeśli dużą częścią małych i średnich firm zarządza jednoosobowo właściciel, to – zdaniem menedżera Siemensa – jest zazwyczaj tak pochłonięty bieżącą działalnością firmy i dbałością o utrzymanie jej na powierzchni, że po prostu nie ma czasu na refleksję dotyczącą innowacyjnych rozwiązań. – Dlatego wydaje się bardzo istotne, by nie bać się nowych technologii i zaufać trochę bardziej swej młodej kadrze; przekazać jej część decyzji, bo ona lepiej rozumie, jak można zarobić na innowacyjnych technologiach – radzi Haiduk.
W polskiej gospodarce tradycyjne modele biznesowe nadal radzą sobie całkiem dobrze. Mamy wysokie tempo wzrostu gospodarczego, wynikające z uruchamiania rezerw tradycyjnych czynników wzrostu (poprawa organizacji pracy). To podstawowa przyczyna niedoceniania potrzeby zmian, wynikających z presji konkurencyjnej, początkowo słabo widocznej i uważanej za mało groźną. Zmian nie ułatwia tradycyjna kultura organizacyjna objawiająca się m.in. w obawie przed „delegowaniem uprawnień” na roboty. Dotyczy to także niektórych regulacji, które często uniemożliwiają takie delegowanie (np. potrzeba wystawienia „po drodze” dokumentu rozliczeniowego). Wśród barier infrastrukturalnych przedsiębiorcy wskazują na niski poziom dostępu do stabilnego i szerokopasmowego internetu, który jest niezbędny przy planowanym zastosowaniu chmury obliczeniowej. W dużych aglomeracjach miejskich sytuacja wydaje się poprawna, natomiast w mniejszych miastach mamy już poważny problem. Innym ważnym dla producentów elementem są niesprzyjające i skomplikowane regulacje podatkowe oraz brak wiedzy o badaniach prowadzonych na wyższych uczelniach, a związanych ściśle – i bardzo użytecznych z punktu wdrażania rozwiązań – z Przemysłem 4.0 w firmie. Można to wiązać ze zbyt niskim poziomem (skutecznością) współpracy przemysłu z uczelniami wyższymi, co nadal ogranicza transfer tego typu technologii do sektora przemysłowego.
Czynnikiem limitującym efekty wdrożeń bywa człowiek lub struktura firmy. Implementując nowe technologie na nieprzygotowany organizacyjnie grunt, firma wystawia się na duże ryzyko, a przynajmniej na ograniczenie korzyści ekonomicznych, co fatalnie rokuje na przyszłość, zrażając do kolejnych projektów. Barierę stanowić może czasem brak zaufania przedsiębiorców do wdrażania cyfrowych technologii. Wynikać on może po części z braku kompetencji i otwartości na nowe rozwiązania, z problemów kadrowych lub z lęku przed utratą kontroli i z preferowania ręcznego sterowania firmą.
W przypadku mniejszych firm, m.in. z silnego przecież sektora rolno-spożywczego, zwraca uwagę swoiste pęknięcie między zdecydowanie deklarowaną chęcią wprowadzania rozwiązań technicznych, otwartością na innowacje przynoszące wymierne korzyści a świadomością własnych ograniczeń – nie tylko finansowych, ale i kompetencyjnych.
„Chciałbym, ale nie stać mnie i nie wiem jak” – to formuła powtarzająca się w rozmowach z polskimi przedsiębiorcami.
Jutro, ale już dziś
Dynamika procesu wdrażania rozwiązań z obszaru technologii cyfrowych w Polsce jest ściśle powiązana z kondycją dużych podmiotów gospodarczych. Małe przedsiębiorstwa (a jest ich przecież 98 proc.) albo twierdzą, że nie potrzebują takich wdrożeń, albo po prostu korzystają z usług zewnętrznych – np. istniejących kanałów sprzedażowych typu e-commerce i innych rozwiązań webowych. „Dla nas za wcześnie, nie mamy nic do zaprezentowania” – tego typu szczere odpowiedzi (za które jako autorzy ankiety i raportu jesteśmy, bez żadnej ironii, wdzięczni) padały rzadko. Po pierwsze staraliśmy się celować z ankietami w firmy, które już wkroczyły na drogę 4.0. Po drugie ci, którzy tę podróż dopiero rozpoczęli, woleli taktownie zamilknąć niż pozostawić rubryki pustawe. Tak czy inaczej – brak odpowiedzi jest tu symptomatyczny.
Nie o rozliczanie z dokonań tu przecież chodzi. Zaprawiony w boju polski biznes potwierdza swój rozsądek, doświadczenie, a może także instynkt. Owszem, temat Industry 4.0 jest interesujący dla wszystkich – ciekawość, deklaracje zainteresowania są powszechne. To dobry prognostyk. Jednak ryzyko „wyrwania się przed szereg”, przeinwestowania, zbyt długiego oczekiwania na zwrot z inwestycji każe zaczekać z decyzją o wydaniu pieniędzy. Czysta zdrowa kalkulacja każe wykorzystywać dostępne już teraz przewagi – dostęp (to prawda – coraz trudniejszy) do nieźle wykwalifikowanej, a wciąż tańszej niż na Zachodzie siły roboczej czy importowane technologie, może nie z najwyższej półki, ale dające nadal szanse skutecznego konkurowania – także na międzynarodowych rynkach.
– Polskie firmy z branży spożywczej mają bardzo zróżnicowane podejście do zagadnień związanych z Przemysłem 4.0 – uważa Marcin Zalasa, dyrektor ds. kluczowych klientów (przemysł spożywczy) w firmie ABB. – Widoczna jest różnica pomiędzy dużymi koncernami, które, chociażby ze względu na skalę działalności, intensywnie inwestują w robotyzację, a niewielkimi firmami, dla których zastosowanie niektórych rozwiązań wciąż pozostaje wyzwaniem. W przypadku małych polskich przedsiębiorstw wciąż pojawiają się wątpliwości, czy inwestycja w automatyzację i inteligentne systemy się zwróci.
Dużych przedsiębiorstw, których inwestycje zdynamizowałyby rozwój technologii i wdrożeń cyfryzacyjnych, które mogłyby pełnić rolę „technologicznych lokomotyw”, jest w Polsce niewiele. Te, które realizują planowo i kompleksowo programy wdrożeń 4.0, to w dużej części zakłady międzynarodowych koncernów, z silnym zapleczem technologii, know-how i poważnymi budżetami wdrożeniowymi.
Dla tych, którzy myślą o Przemyśle 4.0 w swojej firmie, nie mając takiego handicapu, ważne są dwa czynniki mogące przyśpieszyć procesy wprowadzania w życie Przemysłu 4.0: spadające koszty rozwiązań (np. stanowisk zrobotyzowanych) oraz wzrost kosztów pracy.
Swoim rytmem?
Pewne procesy w polskiej gospodarce inicjowane są jednak w sposób naturalny – wymusza je rynek, odbiorca, partnerzy biznesowi. Z natury konserwatywna branża rolno-spożywcza, w której zmiany nie zachodzą rewolucyjnie, dokonała jednak w ostatnich latach potężnego postępu. Chodzi przede wszystkim o automatyzację procesów związanych z produkcją, wykorzystanie coraz nowocześniejszych maszyn, co nie wyczerpuje istoty Przemysłu 4.0, ale jest prostym korytarzem, który do niego prowadzi.
Postęp ten przyszedł do nas wraz z zastrzykiem unijnych funduszy, ale to właśnie dzięki nowoczesnym, technologicznym rozwiązaniom polska żywność ma dobrą opinię na świecie, a sektor rolno-spożywczy, jeden zfilarów polskiego eksportu, generalnie nadąża za globalnymi trendami rynkowymi, proponuje nowe produkty, inwestuje w konfekcjonowanie, konsekwentnie promuje się poprzez hasło „zdrowej żywności”.
Co ważne, technologia nie kłóci się z naturalnością. W produkcji ekologicznej, która jest bardziej pracochłonna, wprowadzenie rozwiązań zmniejszających nakłady ręcznej pracy jest jak najbardziej wskazane. Wśród deklaracji liderów zmian znaleźć można i taką konstatację, że Przemysł 4.0 wspiera udostępnianie pełnego potencjału wartości, jakimi dysponuje firma, poprzez ułatwiony dostęp do często ukrytych wewnątrz firmy zasobów wiedzy, doświadczenia i kompetencji. W tym kontekście głównym parametrem staje się czas. Poprzednie rewolucje przemysłowe rozciągały się na wieki i dekady; IV rewolucja to coraz to nowsze technologie wdrażane w rytmie miesięcy. Wiele polskich firm podchodzi do tych wyzwań, szukając złotego środka (nie za wcześnie i nie za późno), przygotowując grunt, próbując wykorzystać nowe kompetencje młodych ludzi, dostępne wsparcie finansowe i instytucjonalne. Trzeba jednak pamiętać, że wczesne zainicjowanie procesu zmian pod presją gospodarki 4.0 nie stanowi gwarancji, że transformacja zakończy się powodzeniem. W dużej mierze zależy to od samego przedsiębiorstwa: jego strategii, kultury organizacyjnej i kompetencji. To w skali firmy. W skali makro – od tego, w jakim czasie, rytmie i tempie polski przemysł wejdzie na nową drogę zależy natomiast, czy IV rewolucja przemysłowa będzie okresem, w którym polska gospodarka skróci swój dystans do najlepszych, czy też straci, osiadając na dobre na obecnie satysfakcjonujących, sprawdzonych pozycjach. Zapewne nie sięgniemy po pozycję liderów głównego nurtu technologicznych zmian, którzy już odskoczyli od pel tonu. Możemy jednak postawić na polskie specjalności (i wykorzystać ich potencjał, jednocześnie mądrze czerpiąc wiedzę, doświadczenie i zyski z kooperacji z największymi i najnowocześniejszymi).
source: Automatyka 10/2018 / wnp.pl