Efektywna automatyzacja i utrzymanie ruchu – z wizytą w fabryce Danfoss Poland
Urszula Chojnacka, Jolanta Górska-Szkaradek print
Zakład produkcyjny Danfoss w Grodzisku Mazowieckim specjalizuje się w produkcji kabli i mat grzejnych oraz komponentów do automatycznej kontroli, wykorzystywanych m.in. w układach chłodniczych i zabezpieczających. Grodziski „kampus” jest najmocniejszym, obok lokalizacji w Danii, punktem na mapie europejskich działań Grupy Danfoss, a poczynione ostatnio inwestycje jeszcze zwiększyły jego potencjał produkcyjny.
Fabryka Danfoss w Grodzisku Mazowieckim, która powstała w 1998 r., składa się z dwóch hal. W jednej z nich produkowane są kable i maty grzejne. – Wykonujemy kilkadziesiąt, w zależności od potrzeb odbiorców, grup produktowych, między innymi maty grzejne, kable grzejne do położenia bezpośrednio w posadzce, kable zewnętrzne do podgrzewania chodników, podjazdów i dachów, jak również kable inteligentne, czyli samoregulujące, które na różnych odcinkach mają różną oporność i tam, gdzie jest wymagana określona temperatura, kabel sam rozgrzewa się odcinkowo, a tam, gdzie temperatura jest wyższa od zadanej – pozostaje w swojej temperaturze – opowiada Jacek Stępiński, starszy kierownik do spraw projektów utrzymania ruchu w Danfoss Poland.
Kable zewnętrzne, chociaż nie należą do najtańszych rozwiązań, cieszą się coraz większym zainteresowaniem na rynku. – Układy naszych kabli zewnętrznych są zamontowane między innymi na dachu lotniska w Gdańsku. Są też stosowane na przykład do podgrzewania przystanków autobusowych czy wiaduktów, które w ten sposób są odszraniane – mówi Jarosław Strzelczyk,
starszy dyrektor operacyjny w Danfoss Poland. Z dobrodziejstw tego rozwiązania korzysta również sama fabryka – kable zostały zamontowane do podgrzewania niektórych wejść do budynków.
Możliwości zastosowań wspomnianych kabli są jednak znacznie szersze. – Od niespełna roku kable grzejne Danfoss są wykorzystywane nawet do ogrzewania powierzchni okien okrętowych – zaznacza Krzysztof Powała, kierownik ds. kluczowych klientów w Dziale Komponentów Automatyki Przemysłowej spółki Danfoss Poland.
Produkcja kabli grzejnych w grodziskiej fabryce odbywa się na linii, na której pracuje osiem wytłaczarek ślimakowych. Ciąg produkcyjny rozpoczyna się od zasypu oraz od wytłaczarki i podawania drutu oporowego i drutu do oplotu. Następnie przez układ chłodzenia i sprawdzania przebiciowego markowane są odcinki kabla, by były łatwo identyfikowalne w zakresie rodzaju, typu, oporności. Dopiero wtedy następuje etap połączenia kabla z matą.
W drugiej części fabryki produkowane są komponenty do automatycznej kontroli, wykorzystywane np. w układach chłodniczych i zabezpieczających. Najważniejszymi są tzw. przełączniki – presostaty itermostaty – oraz zawory używane do kontroli przepływu czynnika chłodniczego. – Jednym z nich chciałbym się szczególnie pochwalić: presostat RT w tym lub podobnym wariancie jest obecny na rynku od 70 lat, a sprzedaży mógłby mu pozazdrościć niejeden oparty na nowoczesnej elektronice – podkreśla Jacek Stępiński.
Fabryka w Grodzisku wykorzystuje system pick-by-light. To rozwiązanie jest przydatne zwłaszcza tam, gdzie mamy do czynienia z ręczną kompletacją i sortowaniem komponentów. – Gdy pojawia się zlecenie, dzięki zapalonym lampkom pracownik wie, które komponenty ma pobrać. Jeśli lampka gdzieś się pali, wiadomo, że ten komponent nie został jeszcze pobrany. To rozwiązanie znacznie ułatwiło nam pracę. Jednocześnie jednak doszło wiele nowych produktów i to jest problem, ponieważ trzeba ten – bądź co bądź bardzo drogi – system modyfikować, by wprowadzić do niego kolejne elementy i by reagował on na ich pobieranie – opowiada Jacek Stępiński.
Zakład w Grodzisku zatrudnia około 800 osób. Pełna automatyzacja procesów nie jest planowana i, jak podkreślają przedstawiciele spółki, nie miałaby sensu. – Produkujemy tutaj około pięciu tysięcy wyrobów gotowych/kodów, na które składa się około 40 rodzin produktów, a w przypadku linii w pełni zautomatyzowanych jednym z największych kłopotów jest przezbrajanie. W grę wchodzą też inne czynniki – niektóre linie pracują na trzy zmiany, inne na jedną, są też takie, które nie pracują codziennie, w związku z tym pełna automatyzacja byłaby droga i nieefektywna, bo nie w pełni wykorzystana. Mielibyśmy przestoje i mniejszą elastyczność produkcji – tłumaczy Jarosław Strzelczyk. W planach jest natomiast częściowa automatyzacja procesów, w których praca człowieka nie jest potrzebna lub wskazana.
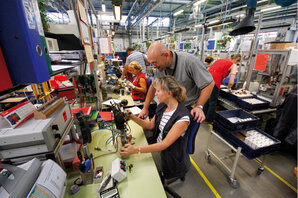
Poprawność deklarowanych parametrów wyrobów finalnie sprawdzana jest na stanowiskach kontroli jakości
Grodziska fabryka stawia na autonomiczne utrzymanie ruchu – gdy konieczne są drobne przestrojenia, mogą ich dokonać pracownicy produkcji. Zakład świadczy też na zasadzie outsourcingu utrzymanie ruchu dla innych firm, w tym dla spółki joint venture – Danfoss Saginomiya. Wielu pracowników produkcji ma kompetencje pozwalające im na pracę w obu halach i na różnych stanowiskach. – Pracownicy mają matrycę kompetencji i na jej podstawie osoby z kompetencjami z różnych działów są wymieniane. Dzięki temu sezonowa fluktuacja zamówień nie wiąże się z koniecznością przyuczania pracowników do nowych prac, odchodzenia jednych, przychodzenia innych itp. Temu między innymi zawdzięczamy 25-procentowe zwiększenie wydajności i produkcji po przeniesieniu produkcji z Danii do Polski. Możliwości naszej fabryki były jedną z kluczowych kwestii, które zdecydowały o przeniesieniu produkcji z Danii do nas – mówi Jacek Stępiński.
Na początku działalności w Polsce Danfoss stawiał gównie na produkcję zaworów i termostatów grzejnikowych. Później produkcja była systematycznie poszerzana: najpierw o styczniki, presostaty czy zawory, a od 2007 r. – także o pompy ciepła, których produkcję pięć lat później przeniesiono do Szwecji. Dziś Grodzisk produkuje znaczną część na potrzeby dywizji Refrigeration & A/C Controls. – Nasza produkcja to około 20 procent światowej produkcji Danfoss w tej dywizji, a wyroby trafiają na cały świat, przy czym blisko 60 procent odbiorców stanowią odbiorcy z Europy, w tym Rosji, a ponadto także zBliskiego Wschodu, ponad 20 procent – z Azji, 10 procent z Ameryki Północnej, a poniżej 10 procent – z Ameryki Południowej i reszty świata – mówi Jarosław Strzelczyk.
Produkcja kabli i mat grzejnych była przenoszona stopniowo. Pierwszy etap rozpoczął się w 2008 r., ostatni zakończył się w ubiegłym. Obecnie cała produkcja Grupy Danfoss wyrobów pod marką Devi – czyli mat grzejnych i kabli – odbywa się już w Grodzisku Mazowieckim. – Nasza produkcja zaopatruje obecnie wszystkie kraje, zarówno w Europie, jak i na całym świecie, przy czym na rynek europejski, uwzględniając Rosję, trafia ponad 80 procent – podkreśla Jarosław Strzelczyk. W przypadku elektrycznego ogrzewania podłogowego aż 70 proc. całego obrotu Grupy Danfoss pochodzi z wyrobów wyprodukowanych w Polsce.
Serwis dla większości zainstalowanych w grodziskiej fabryce maszyn Danfoss zapewnia we własnym zakresie, jednak są wyjątki. Należy do nich m.in. piec marki Mahler używany do lutowania – w tym przypadku firma korzysta z serwisu zewnętrznego, a przegląd odbywa się co dwa lata. Jak zauważa Jacek Stępiński, każde z tych rozwiązań ma swoje wady i zalety. – Korzystanie z usług zewnętrznych pozwala na optymalizowanie utrzymania ruchu, ale jednocześnie trzeba liczyć się z kosztami. Nierzadko własnymi siłami można zrobić więcej i lepiej. Tak więc w części obszarów zamawiamy serwisy zewnętrzne, w innych radzimy sobie sami – wyjaśnia starszy kierownik do spraw projektów utrzymania ruchu w Danfoss Poland.
Fabryka w Grodzisku Mazowieckim jest również wyposażona w nowoczesne stanowiska zrobotyzowane. Jednym z nich jest zakupione przez duński oddział firmy i przeniesione do Polski wtedy, gdy zapadła decyzja o przeniesieniu tu produkcji z Danii, zrobotyzowane urządzenie do produkcji zaworu KV, które jest w stanie zastąpić kilku pracowników – zamiast trzech osób na trzech stanowiskach pracuje jedna na jednym. Jego wielką zaletą jest niska awaryjność robotów, jednak samo stanowisko jest dużym wyzwaniem dla utrzymania ruchu.
– To zrobotyzowane rozwiązanie pozwala nam na o wiele większą wydajność – przyznaje Jacek Stępiński, dodając jednak, że z kolei na mniejszych, niezrobotyzowanych maszynach fabryka może szybko zacząć produkować inne niż jeszcze przed chwilą wyroby, co w przypadku stanowiska zrobotyzowanego nie jest ani łatwe, ani opłacalne. Wśród zalet zrobotyzowanego rozwiązania należy też wymienić kamerę wizyjną, która sprawdza m.in. kontur i cień elementów i dzięki temu wychwytuje produkt, który ma nie w pełni zgodny z wymaganiami wymiar. W razie wykrycia wady produkt bocznym torem wraca do operatora.
Kolejne miejsce w grodziskiej fabryce to lutowarka wielostanowiskowa. Najczęściej występujące na tym stanowisku problemy to przegrzanie i spadek poziomu mieszanki gazu. – To jedna z trzech maszyn, która ma cotygodniowy przegląd, podczas gdy inne mają przeglądy dwutygodniowe, miesięczne, kwartalne lub rzadsze – mówi Jacek Stępiński. Na stanowisku zainstalowany jest system monitorowania, a w miejscach, gdzie następuje proces lutowania – dwie kamery pokazujące rozkład ciepła.
W realizacji i w planach są również inwestycje związane z energooszczędnością. Wśród ostatnich była zmiana oświetlenia na jednej z hal, a ponadto modernizacja wentylacji. – Idziemy w kierunku, który promujemy w naszych produktach w całej Grupie Danfoss – energooszczędności. Przechodzimy na układy, które są sterowane automatycznie. To dość drogie modernizacje. Te inwestycje są już zaplanowane i chcemy je przeprowadzić w najbliższym roku lub dwóch latach. Obecnie modernizujemy instalację sprężonego powietrza – mówi Jarosław Strzelczyk. W najbliższych latach planowane jest też zainstalowanie klimatyzacji w starszej hali, która w przeciwieństwie do tej później powstałej, nie jest w nią wyposażona.
Danfoss w Polsce realizuje również inwestycje zwiększające potencjał produkcyjny – kilka miesięcy temu spółka zakupiła w Grodzisku grunt obok już funkcjonującej fabryki z myślą o rozszerzeniu produkcji w przyszłości, na co nie byłoby miejsca w istniejących halach. – Polska ma w Grupie Danfoss bardzo wysoką ocenę, a Grodzisk – jako jedyny w Europie obok lokalizacji w Danii – jest określany mianem kampusu. Tak określane są miejsca, w których Danfoss chce intensywniej się rozwijać i planuje inwestycje z różnych obszarów. Na nowych terenach możemy zbudować hale większe niż te istniejące. Przy dwóch poziomach udałoby się nam uzyskać nawet 20 tysięcy metrów kwadratowych powierzchni – zaznacza Jarosław Strzelczyk.
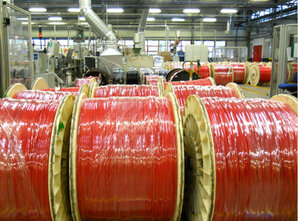
Największą bolączką w lean manufacturing są ogromne ilości kabla, które fabryka musi magazynować i ponosić związane z tym koszty
Polska spółka Danfoss, do której należą cztery fabryki w Polsce, zajmuje pod względem zatrudnienia 5. miejsce w całej Grupie Danfoss, a pod względem obrotów – 12. – Zawsze naszym kluczem do rynku była dostępność produktów. Zawdzięczamy to temu, że zbudowaliśmy szeroką sieć dystrybucji, co nie jest aż takie powszechne, bo wiele firm bazuje na sprzedaży bezpośredniej – podkreśla Krzysztof Powała.
Polska spółka Danfoss powstała w 1991 r., jednak jej produkty były w Polsce obecne już od lat 80. – Gdy więc po zmianach ustrojowych w centrali Danfoss w Danii zapadła decyzja o wejściu na rynek Europy Wschodniej, Polska była dość naturalnym wyborem. Jednocześnie nasz kraj był pierwszym rynkiem spoza Europy Zachodniej, w którym pojawiła się firma. Dopiero później Danfoss pojawił się wRosji, Chinach czy Indiach. Można powiedzieć, że globalizacja w Danfoss rozpoczęła się od Polski – stwierdza Jarosław Strzelczyk.
Dziś firma w zakresie ogrzewnictwa oferuje m.in. bardzo nowoczesne rozwiązanie do budynków inteligentnych, które pozwala sterować ogrzewaniem w całym budynku z panelu dotykowego, a system grzewczy jest skomunikowany drogą radiową. Najsilniejszym jednak segmentem Danfossa jest dziś chłodnictwo. Firma jest też znana m.in. z rozwiązań automatyki przemysłowej oraz przetwornic częstotliwości. W tym ostatnim segmencie chce stać się w najbliższych latach numerem 1 na świecie.
Obecnie trwa kampania marki Danfoss pod nazwą Engineering Tomorrow. – Koncepcja powstała w naszej duńskiej centrali, ale kampania jest globalna i obejmuje wszystkie filie firmy na całym świecie – wyjaśnia Krzysztof Powała. Nowa koncepcja marki Danfoss odwołuje się do dziedzictwa firmy i jest połączeniem potencjału inżynierii z określeniem głównych obszarów, w których Danfoss poszukuje innowacji. Są to: infrastruktura, przemysł spożywczy, energia i klimat.
Aspiracje Danfoss związane z koncepcją Engineering Tomorrow przedstawia poniższy film
Danfoss - Engineering Tomorrow
source: PAR 12/2014