Efektywność energetyczna przemysłu i przedsiębiorstw
Piotr Gocłowski (ELMARK Automatyka) print
Ze względu na coraz wyższe koszty energii, ryzyko blackoutu czy chęć redukcji emisji CO2 wiele przedsiębiorstw staje przed wyzwaniem zmniejszenia i optymalizacji zużycia energii. Nie jest to proste zadanie i nie ma uniwersalnej receptury, jak je zrealizować, jednak ten artykuł przybliża nieco tę tematykę i opisuje przykłady optymalizacji kosztów energii oraz powody, dla których warto to robić.
Zazwyczaj proces produkcyjny jest złożony i bierze w nim udział wiele urządzeń. Ta złożoność sprawia, że w przypadku każdej instalacji czy procesu istnieje wiele dróg prowadzących do poprawy efektywności energetycznej. Czasami przesunięcie konsumpcji energii w czasie lub równomierne rozłożenie obciążenia skutkuje zmniejszeniem kosztów energii. Przekroczenie zadeklarowanej mocy umownej przez zakład jest kosztowne i przekłada się na wyższy rachunek za prąd.
Optymalizacja zużycia energii w przemyśle
Bywa, że w ciągu dnia w zakładzie produkcyjnym przekraczana jest moc umowna, ale w nocy pobór energii jest znacznie mniejszy. W takim przypadku należy zastanowić się, które obciążenia można przesunąć na mniej energochłonny okres. Przykładem może być praca sprężarki, odpowiadającej za dostarczenie odpowiedniego ciśnienia w sieci pneumatycznej. Jeśli jej praca zostałaby przesunięta na noc, a dodatkowo zwiększona zostałaby objętość zbiorników sprężonego powietrza, to udałoby się zredukować pracę sprężarki w najbardziej energochłonnym czasie pracy zakładu.
W przetwórstwie tworzyw sztucznych, hutach szkła, produkcji papieru i w zakładach o podobnym charakterze działalności zużycie energii elektrycznej bywa bardzo wysokie. Maszyny typu autoklawy albo piece czy silniki elektryczne pochłaniają czasem ogromną ilość energii, liczonej w setkach kilowatów. Warto przyjrzeć się harmonogramowi pracy takich urządzeń, ponieważ tkwi w nich duży potencjał oszczędności. Może okazać się, że urządzenie często ma przestoje, np. w oczekiwaniu na nowy wsad materiału. To oznacza, że obiekt jest w tym czasie nieproduktywny, a jednocześnie zużywa dużo energii. Modyfikacja planu pracy lub eliminacja przestojów może przynieść wymierne oszczędności.
W starszych zakładach produkcyjnych często funkcjonuje sporo wiekowych urządzeń, których pracę można dość łatwo zoptymalizować. Pierwszym krokiem do takiej optymalizacji, jaki nasuwa się na myśl, jest wymiana silników elektrycznych na urządzenia o większej sprawności. Innym sposobem jest zastosowanie urządzeń kontrolujących pracę silników elektrycznych, np. falowników. W sytuacji, gdy obciążenie silnika jest zmienne, a pracuje on na zasadzie włącz/wyłącz, wdrożenie takiego systemu obniży zużycie energii, ponieważ silnik będzie pobierał jej dokładnie tyle, ile potrzebuje w danym momencie. Jeśli takie sterowanie zostanie wdrożone we wszystkich silnikach ze zmiennym obciążeniem, oszczędności mogą okazać się na tyle wysokie, że stosunkowo duży koszt początkowy inwestycji szybko się zwróci. Im większa kontrola nad danym procesem, tym łatwiej zarządzać jego poszczególnymi elementami, a więc i optymalizować zużycie energii.
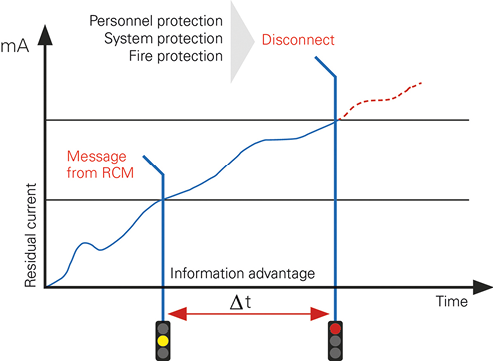
Wykres prezentujący, w jaki sposób z biegiem czasu może rosnąć prąd upływu. Jego stały pomiar umożliwia uprzedzenie zadziałania wyłącznika RCD
Aby móc ocenić realne zużycie energii przez zakład czy przedsiębiorstwo, warto rozważyć wdrożenie systemu zarządzania energią (EnMS), który umożliwia monitorowanie w czasie rzeczywistym aktualnego zużycia, zapisywanie pomiarów do bazy danych, tworzenie trendów historycznych, generowanie różnych raportów itp. Takie narzędzie pozwala łatwiej identyfikować miejsca, w których energia ucieka w największej ilości i zapobiegać temu, a tym samym generować oszczędności. Te ostatnie oznaczają niższe koszty produkcji, co automatycznie zwiększa konkurencyjność i rentowność przedsiębiorstwa optymalizującego zużycie energii. Inną zaletą systemu jest łatwiejsze kontrolowanie kosztów zakładu dzięki stałemu monitorowaniu energii, co umożliwia znacznie szybsze reagowanie w przypadku wystąpienia w trakcie produkcji niespodziewanej sytuacji lub następuje zmiana w trakcie eksploatacji. Przykładowo stały niewielki wzrost poboru energii silnika elektrycznego może przełożyć się na jego zużycie lub narastające obciążenie. W takim przypadku otrzymujemy sygnał, że coś się dzieje, więc należy to sprawdzić. Innym przykładem jest stały pomiar prądu upływu, który może kontrolować stan izolacji przewodów i z wyprzedzeniem zasygnalizować, że niebawem zadziała wyłącznik różnicowo-prądowy, co może wstrzymać produkcję. W wielu przypadkach taka prewencja umożliwia uniknięcie nieplanowanych przestojów, które potrafią generować poważne straty.
Z tych kilku przykładów wyłania się interesujący i dość oczywisty fakt, że całkowita efektywność energetyczna procesu/instalacji jest sumą cząstkowych efektywności energetycznych poszczególnych urządzeń i części. Zawsze należy przyjrzeć się poszczególnym elementom procesu i próbować poprawić jego efektywność. Ciekawą metodologią do usprawniania procesów jest filozofia Kaizen, która opiera się na ciągłym, nieprzerwanym ulepszaniu, prowadzonym małymi krokami. Kaizen wydaje się idealną filozofią działania do polepszania efektywności energetycznej przedsiębiorstwa.
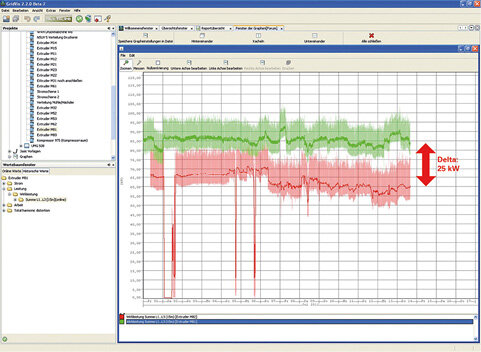
Porównanie mocy skutecznej zużywanej przez extruder przed i po wprowadzeniu systemu mierzącego efektywność energetyczną i optymalizacją
Dlaczego trzeba dążyć do zwiększania efektywności energetycznej?
Jeśli chodzi o interes przedsiębiorstw, głównym i racjonalnym powodem zwiększenia skuteczności produkcji jest oszczędność kosztów energii, co może przełożyć się na wyższy zysk. Jeśli chodzi o interes publiczny, kluczowym powodem, dla którego w każdej branży dąży się do redukcji zużycia energii, jest potrzeba zmniejszenia emisji CO₂. Zmniejszenie zużycia energii procesów, zakładów czy urządzeń ma jeszcze jedną zaletę: sprawia, że poprawia się krajowe bezpieczeństwo dostaw energii. W Polsce w ostatnich latach stanowi to dosyć poważny problem. Latem 2015 r. długie upały spowodowały, że duże zakłady przemysłowe miały ograniczony przydział energii. To jeden z powodów, dla których duże przedsiębiorstwa mają obowiązek przeprowadzenia audytów energetycznych do 31 października 2017 r.
Analizatory energii jako element systemu zarządzania energią
Firma Janitza produkuje nowoczesne analizatory jakości energii elektrycznej, które są przydatnym narzędziem i elementem systemów zarządzania energią, szczególnie w dużych i średnich przedsiębiorstwach. Umożliwiają precyzyjny pomiar nie tylko zużycia energii, ale także jej jakości, która często ma wpływ na urządzenia elektroniczne. Janitza może pochwalić się pełną ofertą dla systemów zarządzania energią, począwszy od liczników zgodnych z dyrektywą MID, prostych analizatorów energii, a także zaawansowanych analizatorów klasy „A”, aż po wyrafinowane oprogramowanie GridVis z szerokim wachlarzem funkcji upraszczających proces zbierania, przetwarzania, analizowania, raportowania i prezentowania danych.
ELMARK AUTOMATYKA Sp. z o.o.
ul. Niemcewicza 76,05-075 Warszawa-Wesoła
tel. 22 773 79 37, 22 778 99 25
fax 22 773 79 36
e-mail: elmark@elmark.com.pl
www.elmark.com.pl
source: Automatyka 9/2017