Sprzęgła indukcyjne w fabryce Forda. Nowy wymiar przesyłu informacji
Materiał prasowy (Balluff Sp. z o.o.) drukuj
Wycofywanie produktów stymuluje wdrażanie innowacji. Świadczą o tym zmiany, które zaszły w fabryce Forda w Kolonii, w której 17 mobilnych palet GEO obsługuje linię spawalniczą. Do tej pory zasilanie i przesył danych odbywały się za pośrednictwem podatnych na usterki połączeń wtykowych, natomiast obecnie proces ten jest realizowany przy użyciu sprzęgieł indukcyjnych, które umożliwiają bezprzewodowe realizowanie wspomnianej funkcji.
Testy z użyciem pustej palety dowiodły, że zastosowanie bezprzewodowej technologii pozwala całkowicie wyeliminować problemy mechaniczne i poprawić efektywność produkcji. Dla firmy Ford jest to wystarczający powód, aby w przyszłości wyposażać linie produkcyjne w nieulegające zużyciu sprzęgła indukcyjne wyposażone w interfejs IO-Link. Gwarantuje to stabilność procesorów i wydłuża czas gotowości urządzeń do pracy. Ponadto zastosowanie interfejsu IO-Link wpisuje się w założenia Przemysłu 4.0 i znacząco ułatwia kontrolę linii produkcyjnych.
W przemyśle motoryzacyjnym mamy do czynienia z dużą złożonością procesów, jak i samych linii produkcyjnych. Wychodząc naprzeciw oczekiwaniom klientów, firma Balluff oferuje innowacyjne, „szyte na miarę” rozwiązania, które często pozwalają zrewolucjonizować cały proces. Tak właśnie stało się w przypadku fabryki Forda.
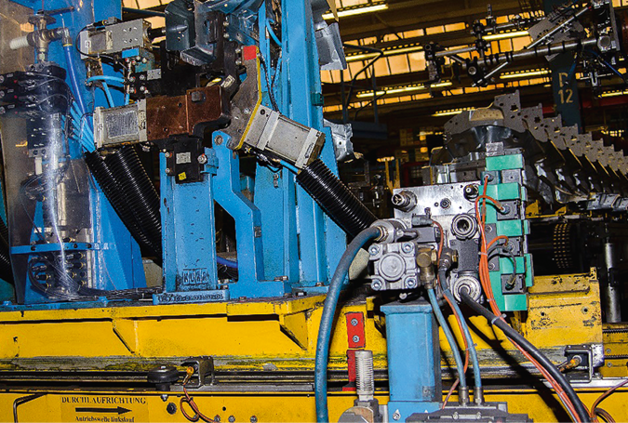
Mobilna paleta GEO na chwilę przed dokowaniem: z prawej strony (między elementami zielonej pokrywy ochronnej) trzy moduły sprzęgła firmy Balluff, z szybkozłączami hydraulicznymi z lewej strony
Efektywna zmiana złączy na sprzęgła indukcyjne Balluff
Jeszcze niedawno do realizacji procesu w obrębie zautomatyzowanych linii spawalniczych w fabryce Forda, wymagane było zastosowanie mechanicznych połączeń, które pozwalały 17 paletom GEO wykonywać ruch obrotowy. Każda z nich oprócz wyspy zaworowej zawierała szereg urządzeń, które gwarantowały podłączenie do nadrzędnego systemu sterowania ze sterownikiem PLC. Sworznie pozycjonujące gwarantowały, że położenia układów pneumatycznych i elektrycznych przenośnej palety i stacji bazowej pokrywają się ze sobą. Doprowadzane sprężone powietrze zaciska obrabiany element. Okrągłe złącze dostarcza zasilanie i dane.
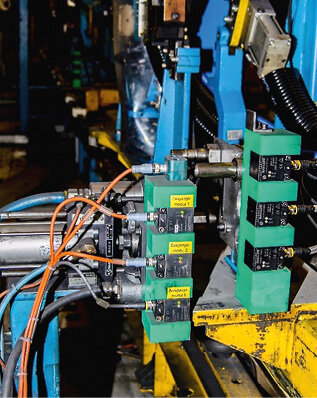
Paleta GEO (po prawej) na chwilę przed opuszczeniem i dokowaniem: trzy pary sprzęgieł do przesyłu zasilania i wymiany danych są ustawione naprzeciw siebie
W 2014 r. producent dotychczas stosowanych złączy wycofał z oferty elektryczny moduł stykowy i rozpoczęto poszukiwania odpowiedniego produktu zastępczego. Wymiana na porównywalny produkt konkurencji była niemożliwa, ale firma Ford była otwarta na innowacyjne rozwiązania niemechaniczne. – Firmy Ford i Balluff od lat utrzymują bliskie relacje partnerskie. Gdy dowiedzieliśmy się o problemie, natychmiast zaproponowaliśmy nasze rozwiązanie: sprzęgła indukcyjne z interfejsem IO-Link. Ich zalety to przede wszystkim bezstykowe zasilanie i przesył danych przez szczelinę powietrzną. Koniec ze zużyciem mechanicznym lub uszkodzeniami przewodów; sprzęgła indukcyjne umożliwiają łatwy i szybki montaż oraz są całkowicie bezserwisowe – podkreśla Ulrich Balwanz, kierownik ds. kluczowych klientów z branży motoryzacyjnej w firmie Balluff.
Zastosowanie interfejsu IO-Link stwarza nowe możliwości w diagnostyce i parametryzacji współpracujących urządzeń. Elementy wykonawcze i czujniki są podłączone do mastera IO-Link za pomocą standardowego przewodu ze złączami M12. „Empowered by IO-Link” oznacza, że sprzęgło indukcyjne jest gotowe do komunikowania się dosłownie w chwili wyjęcia z opakowania.

System gotowy do wymiany danych: dwa moduły wejściowe dostarczają palecie GEO zasilanie i dane, moduł wyjściowy przesyła dane z modułu przenośnego do sterownika PLC
Pomyślny rezultat testów
Testy sprzęgła indukcyjnego Balluff BIC przebiegły pomyślnie. – Testowaliśmy alternatywne systemy i dostawców, jednak końcowa analiza wskazała na sprzęgła z interfejsem IO-Link firmy Balluff ze względu na dużą niezawodność i wytrzymałość – mówi Michel Dang, inżynier technologii produkcji w firmie Ford. W celu sprawdzenia możliwości przetwarzania danych nowych systemów firma Ford najpierw wyposażyła jedną paletę i stację dokującą w sprzęgła indukcyjne, moduł rozszerzeń oraz master IO-Link w odpowiedniej stacji dokującej. – Po trwającym miesiąc okresie testowym oraz nawet 3 tys. cykli dokowania dziennie system nie wykrył ani jednego błędu sygnału diagnostycznego. Był to bardzo mocny argument za podjęciem decyzji o dalszej rozbudowie systemu – dodaje Michel Dang.
W międzyczasie linia spawalnicza została w pełni wyposażona w system sprzęgieł indukcyjnych firmy Balluff, obejmujący wszystkie 17 mobilnych palet GEO. Dopiero po nawiązaniu połączenia ze stacją dokującą i wykryciu prawidłowego osadzenia i bezpiecznego zaciśnięcia obrabianego elementu, robot spawalniczy otrzymuje zezwolenie na rozpoczęcie pracy. Procedura ta jest powtarzana tysiące razy w każdej stacji, a bezprzewodowe sprzęgła indukcyjne zapewniają jej bezproblemową realizację. Wprowadzenie systemu spowodowało, że w 2017 r. nowy Ford Fiesta zjeżdżał z linii produkcyjnej w zakładzie w Kolonii z częstotliwością dwóch samochodów co 68 sekund. – Sprzęgła indukcyjne firmy Balluff wykazały odporność na trudne warunki przemysłowe. Obecnie planujemy zastosować system w dodatkowej linii spawalniczej wyposażonej w 21 palet GEO – twierdzi Michel Dang.
Bezstykowe, szybkie i niezawodne: sprzęgła indukcyjne BIC
Wiele powodów i liczne obszary zastosowań przemawiają za stosowaniem bezstykowego przesyłu danych i zasilania. Zasada funkcjonowania jest zadziwiająco prosta: kiedy aktywne powierzchnie obu elementów (bazowego – element stały i zdalnego – element przenośny) sprzęgła indukcyjnego są ustawione naprzeciwko siebie, element stały generuje zasilanie (12 V/500 mA) dla modułu przenośnego (zasilona cewka wytwarza pole elektromagnetyczne). W efekcie następuje przesył danych.
Dwukierunkowy system BIC firmy Balluff wykorzystuje interfejs IO-Link, umożliwiając równoczesne sterowanie elementami wykonawczymi i zbieranie sygnałów z czujników za pośrednictwem koncentratora sygnałów I/O. Warto zauważyć, że z punktu widzenia infrastruktury systemu sprzęgło indukcyjne jest elementem niewidocznym i traktowane jest jako połączenie przewodowe, a instalacja oparta jest na zasadzie plug&play. Uruchomienie systemu BIC nie wymaga konfiguracji ani integracji.
BALLUFF Sp. z o.o.
ul. Graniczna 21A, 54-516 Wrocław
tel. 71 382 09 00, fax 71 338 49 30
e-mail: balluff@balluff.pl
www.balluff.pl
źródło: Automatyka 5/2018
Komentarze
blog comments powered by Disqus