Nowoczesna produkcja – szanse i wyzwania
Sylwia Batorska, Urszula Chojnacka (AutomatykaOnline.pl) drukuj
Kondycja i tempo rozwoju polskiej gospodarki w znacznej mierze zależą od produkcji przemysłowej i jej konkurencyjności. W tym zakresie przed polskimi przedsiębiorcami i decydentami stoi wiele wyzwań. Ich temat podjęli organizatorzy, prelegenci i uczestnicy II edycji Forum Nowoczesnej Produkcji, która – wraz z XXIV Konferencją Energetyczną EuroPOWER – odbyła się 9 i 10 listopada 2016 r. w warszawskim hotelu Radisson Blu. O tym, jak tworzyć innowacyjną gospodarkę XXI w. dyskutowali zarówno przedstawiciele rządu, jak i praktycy rynku. Wśród poruszanych tematów dominowała problematyka związana z Przemysłem 4.0.
Podczas uroczystego otwarcia tegorocznej konferencji dr Leszek Juchniewicz, przewodniczący Rady Programowej EuroPOWER, podkreślał, że do skutecznego rozwiązywania dylematów gospodarczych, przed którymi stoi nasz kraj, konieczna jest wizja rozwoju oraz sformułowanie strategii i dalekosiężnych celów gospodarczych z poszanowaniem zasad gospodarki rynkowej i stabilności priorytetów. Gośćmi honorowymi wydarzenia byli Jadwiga Emilewicz, podsekretarz stanu w Ministerstwie Rozwoju oraz Grzegorz Tobiszowski, sekretarz stanu w Ministerstwie Energii. Polityka energetyczna powinna wspierać politykę rozwoju przemysłu – to często przywoływane stwierdzenie na tegorocznych konferencjach FNP i EuroPOWER. Do tego jednak konieczne są innowacje, a co za tym idzie – inwestycje, przede wszystkim w nowe moce wytwórcze i przesyłowe, rozwiązania typu smart grid itp. Takie działania są tym ważniejsze, że uwarunkowania, w których dziś działa przemysł i przedsiębiorcy, zmieniają się bardzo dynamicznie, a nowe trendy wymuszają zmianę funkcjonujących modeli biznesowych. Nowoczesna gospodarka nie byłaby jednak możliwa bez spojrzenia perspektywicznego i na to kładli nacisk wszyscy prelegenci bez wyjątku. Bez wątpienia wśród kluczowych obszarów, na które powinien być położony nacisk w kolejnych latach jest rozwijanie nowoczesnych technologii, w tym magazynów energii i rozwiązań z zakresu e-mobilności.
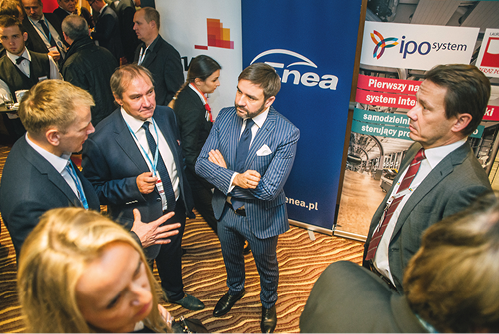
Rozmowy w kuluarach – Piotr Rutkowski, Orange Polska, Piotr Zesiuk, MMC Polska i Dariusz Piotrowski, Microsoft w Polsce
W erze Przemysłu 4.0
Wielokrotnie podkreślano na tegorocznym FNP, że żyjemy w erze cyfryzacji i automatyzacji, a ich nieodzownym elementem są działania spod znaku Industry 4.0. – Przemysł 4.0 rodzi się w głowie. Niekiedy spotykam się z niezrozumieniem tematu przez klienta, który przychodzi i prosi o produkt 4.0. Nie ma takich produktów – 4.0 to nowoczesne zarządzanie – stwierdził Thomas Ilkow, dyrektor generalny Bosch Rexroth. Skąd w ogóle wzięła się koncepcja Przemysłu 4.0? W dużej mierze z nowych potrzeb klientów oraz z konieczności dostosowania się do zmieniających się uwarunkowań rynkowych i szybkiego reagowania na nie. – Przedstawiciele przemysłu europejskiego zdali sobie sprawę, że dotychczasowe metody produkcji nie są w stanie sprostać konkurencji azjatyckiej i musieli znaleźć rozwiązanie tego problemu – mówił Tomasz Haiduk,
Digital Factory, Process Industries and Drives Director w Siemens Polska. Przedstawiciel firmy Siemiens dodał też, że aby można było mówić o faktycznym działaniu w sferze 4.0, konieczne są zmiany w podejściu do tworzenia i produkowania. – Dziś często poszczególne ich etapy są od siebie niezależne – najpierw mamy etap projektowania, potem fizyczny model, następnie jego testy, potem dociera on do fabryki, a na koniec, gdy jest już na rynku, niekiedy okazuje się, że nie spełnia oczekiwań klientów. Ideą Przemysłu 4.0 jest przeniesienie wszystkich tych prac do sfery cyfrowej, dzięki temu jeszcze przed fizycznym wykonaniem produktu będzie wiadomo, czy sprosta on wymaganiom odbiorców. To wymaga drastycznej zmiany w myśleniu – zaznaczył Tomasz Haiduk.
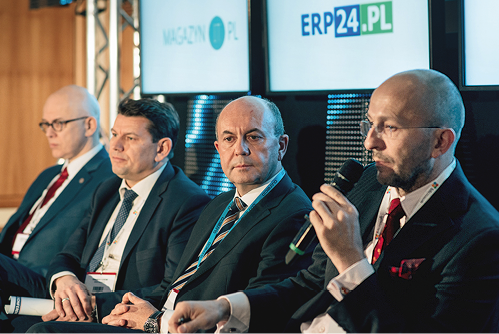
Andrzej Ziółkowski, Urząd Dozoru Technicznego, Thomas Ilkow, Bosch Rexroth, Tomasz Haiduk, Siemens Polska i Henryk Siodmok, Grupa Atlas
I nie tylko w myśleniu – wśród największych wyzwań związanych z Przemysłem 4.0 wymieniano m.in. zbyt małe wykorzystywanie dostępnych danych oraz rosnącą liczbę zamówień rozwiązań szytych na miarę. – Produkcja niestandardowa, która w naszym przypadku stanowiła jeszcze jakiś czas temu 20%, dziś osiąga poziom 50%. Tym ważniejsze jest więc przewidywanie, jak mogą zmieniać się oczekiwania rynku – podkreślił Tomasz Wypchło, dyrektor operacyjny ds. produkcji w firmie Wielton. Kolejna problematyczna kwestia to nastawienie samych przedsiębiorców. Jak podkreślił Stefan Życzkowski, prezes zarządu ASTOR, pod względem gotowości polskich firm do wdrożenia rozwiązań z zakresu Przemysłu 4.0 mamy w naszym kraju jeszcze wiele do zrobienia. – To jednak oznacza, że mamy perspektywę wzrostu – dodał prezes ASTOR. Wyzwaniem bez wątpienia jest również zapewnienie bezpieczeństwa – dziś można mówić o jego redefiniowaniu. – Do tej pory w przemyśle koncentrowano się na bezpieczeństwie poszczególnych urządzeń. Teraz, gdy te urządzenia komunikują się między sobą, mamy do czynienia z zupełnie nowym ryzykiem i moim zdaniem nie do końca jeszcze zdajemy sobie z tego sprawę. Świadomość bezpieczeństwa spada, a chęć do ryzyka jest coraz większa. Tymczasem trzeba pamiętać, jak dramatyczne mogą być konsekwencje, gdy w programie wystąpi błąd albo gdy zostaną wprowadzone niewłaściwe dane. Dlatego bardzo ważne są edukacja oraz wdrożenie odpowiednich zasad i procedur – ocenił Andrzej Ziółkowski, prezes Urzędu Dozoru Technicznego.
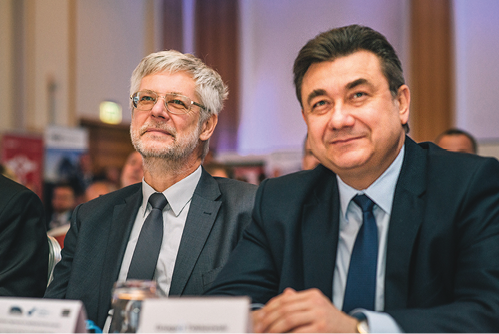
Andrzej Piotrowski, podsekretarz stanu w Ministerstwie Energii i Grzegorz Tobiszowski, sekretarz stanu w Ministerstwie Energii
W świecie innowacji i patentów
Na całym świecie nieodłącznym towarzyszem innowacji w przemyśle są patenty. Na tym polu Polska ma zarówno powody do zadowolenia, jak i obszary, które pozostawiają wiele do życzenia. Z danych Urzędu Patentowego RP wynika, że nasz kraj całkiem dobrze prezentuje się na mapie świata pod względem liczby zgłoszeń patentowych – 15. miejsce oraz udzielonych patentów – 17. miejsce na 200 krajów świata. Jednak gdy wziąć pod uwagę przełożenie tych liczb na populację, nasza sytuacja przedstawia się znacznie gorzej. – Negatywnym zjawiskiem jest to, że Polacy, pracując przy wielu projektach międzynarodowych, przekazują swoje prawa własności tym, którzy je finansują. Bywa więc, że kupujemy polskie wynalazki od obcych podmiotów – zauważyła Alicja Adamczak, prezes Urzędu Patentowego RP.
Inteligentne Fabryki – automatyzacja, robotyzacja i informatyzacja
Idea tworzenia inteligentnych fabryk nie opiera się tylko na sposobach wytwarzania, liniach produkcyjnych, robotach, czy drukarkach 3D. Krzysztof Fiegler, członek zarządu IPOsystem, przekonywał, że Inteligentne Fabryki pracują już w Polsce, a ich bazą jest inteligentny system do samodzielnego zarządzania produkcją, optymalizujący pracę, zwiększający wydajność pracownika, a tym samym zakładu.
Prezentacja była wstępem do panelu dyskusyjnego na temat szans i wyzwań stojących przed polskimi przedsiębiorcami, którzy będą realizowali wdrożenia w zakresie automatyzacji i robotyzacji linii produkcyjnych oraz będą rozwijali systemy optymalizujące i zarządzające produkcją przemysłową.
Michał Kaczurba, dyrektor ds. rozwiązań dla sektora przemysłowego w Microsoft Polska wskazał na pilną potrzebę informatyzacji przedsiębiorstw. Transformacja cyfrowa, którą obecnie przechodzą firmy to strategiczny trend w obszarze produkcji przemysłowej. Fabryki wyposażone w systemy SCADA gromadzą ogromne ilości danych, ale nie czerpią nowej wiedzy, co wynika z braku efektywnej analizy tych danych. W jaki sposób zmienić w ramach cyfrowej transformacji taką fabrykę w fabrykę 4.0? Zdaniem Michała Kaczurby należałoby tego dokonać z zastosowaniem narzędzi wzbogacających środowisko użytkowników. Zaliczają się do nich analiza maszynowa, Internet Rzeczy oraz rozszerzona rzeczywistość, przy czym ta ostatnia jest szczególnie przydatna do celów szkoleniowych oraz dla służb utrzymania ruchu. W centrum wdrażanych rozwiązań powinien znajdować się konsument i jego potrzeby. Nowoczesne systemy komunikacji pozwalają na śledzenie cyklu życia produktu od jego projektowania i wytwarzania po utylizację. Dzięki temu możliwa jest bieżąca analiza potrzeb klienta, a także przewidywanie i zarządzanie usługami serwisowymi dla danego urządzenia.
Grzegorz Skowronek, dyrektor IPOsystem przyznał, że nazwa Konsument 4.0 już funkcjonuje i oznacza klienta, który wymaga określonych produktów indywidualnie skonstruowanych do jego potrzeb. Jako przykład podjęcia próby realizacji produkcji na indywidualne zamówienie konsumenta Krzysztof Fiegler podał projekt fabryki produkującej meble, w którym uczestniczy firma IPOsystem. Główną ideą tego projektu jest tworzenie zamówień przez klientów, którzy za pomocą specjalnego konfiguratora będą projektować swoje meble w internecie. Głównymi założeniami projektu są szybki termin realizacji (48 godzin od momentu złożenia zamówienia) oraz niska cena wyrobu. Taka fabryka ma powstać w ciągu dwóch lat.
Według Stefana Życzkowskiego jesteśmy na dobrej drodze do realizacji koncepcji Przemysłu 4.0, choć mamy jeszcze duży dystans do pokonania w stosunku do krajów Europy
Zachodniej. Przypominał, że koncepcja Przemysłu 4.0 pochodzi z rynku niemieckiego, który jest rynkiem dojrzałym. Firmy niemieckie mają wieloletnie doświadczenie, własne know-how i znaczny kapitał. Dla porównania polskie firmy nie mają więcej niż 20, maksymalnie 30 lat.
Tomasz Haiduk zwrócił uwagę na bariery finansowe, technologiczne i mentalne oraz związane z wykształceniem kadr. – Jedną z większych barier jest obecnie sprawa samej infrastruktury. Istniejąca automatyka z obwodem zamkniętym uniemożliwia pozyskiwanie danych. Szansą dla polskich przedsiębiorstw jest monitoring procesów, umożliwiający pozyskanie informacji, które mogą posłużyć do ulepszenia systemów – powiedział przedstawiciel firmy Siemens.
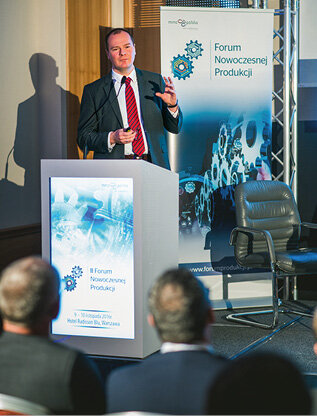
Łukasz Wojtczak, pełnomocnik dyrektora ds. aplikacji przemysłowych w Przemysłowym Instytucie Automatyki i Pomiarów PIAP
Panel dotyczący inteligentnych fabryk zakończyła prezentacja na temat robotyzacji w Polsce na tle sytuacji w krajowym przemyśle, którą przedstawił Łukasz Wojtczak, kierownik działu sprzedaży i marketingu, pełnomocnik dyrektora ds. aplikacji przemysłowych w Przemysłowym Instytucie Automatyki i Pomiarów PIAP. Wskazał on na ważną role robotyzacji i cobotyzacji w rozwoju krajowej produkcji. W krajowym przemyśle w 2015 r. zostało zainstalowanych 1800 nowych robotów. Wskaźnik gęstości robotyzacji (czyli liczba robotów przypadających na 10 tys. osób pracujących w przemyśle) wynosi 28 dla Polski i jest jednym z najniższych w Europie. Dla porównania w Niemczech jest on ponad dziesięciokrotnie wyższy.
Z obserwacji Łukasza Wojtczaka wynika, że polskie firmy wykazują gotowość do robotyzacji procesów. Szczególnie duży potencjał tkwi w sektorze MSP, do którego należy 99% podmiotów gospodarczych, generujących łącznie około 50% PKB. Do Instytutu PIAP, jako uznanego integratora robotów przemysłowych i współpracujących, wpływa dużo zapytań dotyczących wdrożeń stanowisk zrobotyzowanych. Bariery nie leżą w strefie mentalnej lecz w możliwościach technicznych i finansowych firm. Częściowym rozwiązaniem będącym odpowiedzią na potrzeby adaptacyjnej produkcji jest cobotyzacja, czyli współpraca człowieka ramię w ramię z robotem.
Internet Rzeczy w produkcji przemysłowej
Prezentację wprowadzającą do kolejnego panelu poświęconego Internetowi Rzeczy w produkcji przemysłowej wygłosił Michał Kaczurba. Zaprezentował on ideę utworzenia Microsoft IoT Insider Lab, czyli laboratoriów, w których wspólnie z klientami przeprowadza się projekty polegające na prototypowaniu urządzeń, wdrażaniu ich do produkcji małoseryjnej i opracowywaniu kompletnej aplikacji. Przykładem powstałego w ten sposób produktu jest robot wąż, który monitoruje wnętrza rurociągów rafineryjnych i gazowych.
W kolejnej dyskusji prelegenci podjęli próbę usystematyzowania znaczenia pojęcia Internet Rzeczy w kontekście produkcji przemysłowej. Przemysław Szuder, członek zarządu Microsoft w Polsce stwierdził, że IoT jest pomostem, który łączy świat fizyczny ze światem wirtualnym. Przekazywanie danych do systemu informatycznego w czasie rzeczywistym, połączone z zastosowaniem modeli analitycznych i predykcyjnych pozwala jeszcze lepiej podejmować różnego rodzaju decyzje. Firma Bosch opracowała koncept ekosystemu, który ma być otwarty na współpracę z innymi ekosystemami na świecie. System ma za zadanie służyć innowacyjności, pomagać biznesowi z różnych sektorów, definiować modele biznesowe.
Dyrektor Departamentu Innowacji i Rozwoju Urzędu Dozoru Technicznego, Janusz Samuła podkreślił, że Internet Rzeczy można wykorzystać do kontroli i do poprawy bezpieczeństwa procesów produkcyjnych na drodze zdalnej kontroli stanu urządzeń w czasie rzeczywistym. Monitoring on-line jest rozwiązaniem już stosowanym przez UDT we współpracy z firmami. Umożliwia on natychmiastową reakcję w razie wystąpienia problemu. Można zmienić sposób eksploatacji lub sposób sterowania maszyną, a tym samym wydłużyć okresy przeglądów i obniżyć koszty użytkowania.
Prawdziwa wartość Internetu Rzeczy płynie z wykorzystania modeli predykcyjnych do lepszego zarządzania produkcją. Rola chmury obliczeniowej w symulacji, modelowaniu, monitorowaniu i predykcji w czasie rzeczywistym jest szczególnie istotna dla osiągnięcia efektów ekonomicznych. Inspiracji do tworzenia nowych rozwiązań IoT należy szukać w przemyśle high-tech, w centrach badawczych. Często wynikają one z inicjatyw pracowniczych.
źródło: Automatyka 12/2016
Słowa kluczowe
Forum Nowoczesnej Produkcji, Nowoczesna produkcja, Przemysł 4.0
Komentarze
blog comments powered by Disqus