Zrobotyzowane stanowiska spajania i cięcia. Przekrój wdrożeń PIAP
Marek Petz (Łukasiewicz – PIAP) print
Procesy spajania – spawanie, zgrzewanie, również związane z nimi cięcie – są jednymi z najczęściej automatyzowanych i robotyzowanych procesów technologicznych. Według danych IFR około 30% robotów w przemyśle pracuje przy spawaniu. Przemysłowy Instytut Automatyki i Pomiarów PIAP ma długoletnie doświadczenie we wdrażaniu tego typu rozwiązań, opracowanych zgodnie z indywidualnymi potrzebami klienta.
Przemysłowy Instytut Automatyki i Pomiarów PIAP rozpoczął prace nad robotyzacją procesów produkcyjnych pod koniec lat 70., kupując licencję na roboty IRb-6 i IRb-60
od szwedzkiej firmy ASEA, która w 1975 r. wprowadziła na rynek jeden z pierwszych robotów o napędzie elektrycznym. Licencja ta była w PIAP rozwijana, powstawały nowe wersje robotów, a także pierwsze w Polsce zrobotyzowane stanowiska. Były to stanowiska przenoszenia materiałów i obsługi maszyn, ale dość szybko zbudowano również stanowiska spawania i zgrzewania.
Spawanie
Duże zaangażowanie robotów w procesy spawania wynika przede wszystkim z dwóch powodów:
- możliwości uzyskania lepszej i powtarzalnej jakości procesu,
- poprawy warunków pracy (powstające przy spawaniu czy cięciu gazy są szkodliwe dla człowieka).
Dodatkowo dochodzą jeszcze czynniki takie jak oszczędność materiałów produkcyjnych, wyższa wydajność czy poprawa wizerunku firmy na rynku.
Dość szybko po kupnie licencji na roboty przemysłowe IRb PIAP podjął działania mające na celu budowę zrobotyzowanego stanowiska spawania. Począwszy od 1986 r. powstały stanowiska spawania bardzo różne pod względem stopnia skomplikowania – zarówno bardzo proste (robot, ręczna spawarka, jeden przyrząd), jak i bardzo złożone (dwa roboty ze sprzężonym z nimi pozycjonerem, spawarki połączone siecią Ethernet, przyrządy umożliwiające kompensację naprężeń spawalniczych). Niektóre z tych stanowisk zostaną omówione w dalszej części artykułu.
Pierwsza robotyzacja spawania
Pierwszym stanowiskiem spawania w Polsce, zbudowanym przez PIAP w 1985 r., było stanowisko spawania płyty wahacza do samochodu Fiat 126p w FSM Tychy. Zespół wahacza został wybrany ze względu na to, że wszystkie spoiny były ułożone właściwie na płaszczyźnie. Był to warunek zastosowania istniejących wówczas robotów tylko pięcioosiowych, z ograniczonymi możliwościami złożonych ruchów. Stanowisko było oparte na obrotowym, trójpozycyjnym obrotniku, na którym znajdowały się trzy podwójne przyrządy mocujące. Spawanie było wykonywane przez dwa pięcioosiowe roboty IRb-6 (zbudowane w PIAP na licencji), współpracujące ze spawarkami OZAS (Opolskie Zakłady Aparatury Spawalniczej), dostosowanymi do współpracy z robotami. Na dwóch pozycjach obrotnika pracowały roboty, na trzeciej pozycji operator zdejmował zespawane wahacze i zakładał elementy nowych. W normalnym trybie pracy jeden robot spawał lewy wahacz, drugi robot prawy wahacz. W sytuacji awaryjnej (awaria robota, spawarki) każdy z robotów mógł spawać lewy i prawy wahacz, oczywiście z mniejszą wydajnością. Każda spawarka była połączona z robotem przez specjalnie zaprojektowany programator, umożliwiający dobór pięciu zestawów parametrów spawania. Robot, wyposażony tylko w wyjścia i wejścia cyfrowe, wybierał odpowiedni zestaw parametrów i włączał spawarkę. Taka możliwość wyboru całkowicie wystarczała dla potrzeb tego stanowiska.
Obrotnik i programator spawania zostały zaprojektowane i wykonane przez toruńską firmę Apator.
Prostymi (według obecnej oceny) stanowiskami pochodzącymi z lat 80. były również:
- Stanowisko z robotem IRb-6 (produkcji PIAP) zbudowane dla Pafawagu Wrocław. Było to stanowisko spawania obudowy łożyska z elementami podwozia wagonu kolejowego. Ponieważ spoina była okrągła, a robot nie miał możliwości zaprogramowania trajektorii kołowej, programowano kształt okręgu wieloma odcinkami liniowymi. Spawane elementy były dość grube (ścianka około 10 mm) i taki sposób programowania spełniał oczekiwania jakości i wytrzymałości spoin.
- Stanowisko z robotem IRb-6 (produkcji PIAP) spawania zespołów koparki dla Nowej Dęby. Spawany detal był umieszczony w przyrządzie na obrotniku o ukośnej osi obrotu, robot współpracujący z prostą spawarką doprowadzał palnik do odpowiedniej pozycji nad detal i inicjował obrót detalu. Prędkość obrotu była wstępnie dobierana ręcznie potencjometrem. Po wykonaniu pełnego obrotu robot otrzymywał sygnał z czujnika, wyłączał spawarkę i obrotnik się zatrzymywał.
Proste stanowiska spawalnicze były budowane przez PIAP także w latach późniejszych. Zbudowane w 2000 r. stanowisko składało się z używanego robota IRB 2000 (już sześcioosiowego) firmy ABB, kupionego przez użytkownika, który zwrócił się do PIAP z prośbą o uruchomienie. Trochę czasu zabrało samo uruchomienie i skonfigurowanie robota, potem została podłączona do robota zwykła ręczna spawarka. Ręczny przycisk na palniku (używany przez spawacza) został zastąpiony przekaźnikiem uruchamianym przez robota. Oczywiście robot mógł pracować tylko z jednym zestawem parametrów, wcześniej ustawionym w spawarce. Do mocowania detalu (zbiornik gazowy do samochodu) służył wykonany przez użytkownika prosty, ale skuteczny przyrząd umożliwiający spawanie kilku typów zbiorników. Ponieważ zbiorniki musiały być spawane według wymagań Urzędu Dozoru Technicznego (nie ręcznie), proste zrobotyzowane stanowisko było rozwiązaniem problemu. Stanowisko to zresztą początkowo zostało zbudowane w garażu i dopiero po kilku miesiącach przeniesiono je do nowo zbudowanej hali.
Wspólną cechą tych stanowisk był całkowity brak jakichkolwiek ogrodzeń. Ówczesne przepisy bezpieczeństwa nie regulowały tych kwestii ze względu na to, że stosowanie robotów było nowością. Dlatego też budując te stanowiska, staraliśmy się ograniczać zbyt łatwy dostęp do nich i duży nacisk kładliśmy na kwestię bezpieczeństwa przy szkoleniu obsługi. Na szczęście przy żadnym z nich nie zdarzył się wypadek groźny dla zdrowia lub życia człowieka.
Stanowiska standardowe
Stanowiska budowane w następnych latach były standardowymi stanowiskami spawania, wyposażanymi już w systemy bezpieczeństwa.
Spawanie zespołów maszyn rolniczych i drogowych
Każde z dwóch stanowisk zostało wyposażone w robot KR16L6 firmy KUKA, pozycjoner KUKA współpracujący z robotem jako tzw. siódma oś sterowana z układu sterowania robota, spawarkę firmy Kemppi oraz, oczywiście, przyrządy mocujące. Na jednym ze stanowisk pracuje dwuosiowy pozycjoner DKP 400, na drugim jednoosiowy pozycjoner o poziomej osi obrotu KPF1.
Spawanie stelażu łóżka do masażu
Robot KR6 współpracuje z trójosiowym pozycjonerem o pionowej osi obrotu KPF 3 (stoły robocze są siódmą i ósmą osią robota) i spawarką CMT firmy Fronius, połączoną z robotem przez DeviceNet. Było to pierwsze w Polsce zastosowanie w zrobotyzowanym stanowisku nowej technologii Fronius CMT (Cold Metal Transfer).
Spawanie szafek sterowniczych
Robot KR16L6 współpracuje z trójosiowym pozycjonerem o pionowej osi obrotu. Stoły robocze nie są tutaj zewnętrznymi osiami robota, a ustawiają się w kilku pozycjach roboczych na sygnał z robota. Ten pozycjoner został zaprojektowany i wykonany w Zakładach Automatyki Przemysłowej w Ostrowie Wielkopolskim. Również na tym stanowisku zastosowano spawarkę Fronius. Stanowisko to zostało zbudowane również z myślą o szlifowaniu produkowanych szafek. Po wykonaniu serii szafek i wymianie palnika na chwytak podciśnieniowy robot pobiera szafki układane w pozycjonerze przez operatora i szlifuje zarówno spoiny, jak i płaskie ścianki szafek na szlifierkach taśmowych.
Stanowiska specjalistyczne
W miarę rozwoju techniki spawalniczej i robotowej możliwe stało się budowanie stanowisk spełniających coraz wyższe wymagania użytkowników.
Spawanie zespołów pras do ubijania betonu
PIAP zbudował dwa bliźniacze stanowiska. W każdym z nich zastosowano dwa roboty ArcMate120 firmy Fanuc i współpracującą z robotem spawarkę Lincoln Electric, podłączoną przez DeviceNet. Jeden z robotów jest wyposażony w mechaniczny chwytak pobierający elementy do spawania. Pierwszy spawany element jest układany na stole spawalniczym, drugi element pobrany przez robota jest dostawiany do pierwszego i robot trzyma go, gdy drugi robot spawa te elementy. Elementy są pobierane z magazynków, a po zespawaniu – odkładane do pojemnika. Rola obsługi sprowadza się do uzupełniania co pewien czas magazynków i wymiany pojemnika. Wszystkie parametry spawania są programowane w robocie, a spawarka jest przez obsługę tylko włączana i wyłączana.
Stanowisko spawania pierścieni
Jednym z etapów produkcji pierścieni stalowych do rur, w gnieździe zbudowanym przez PIAP, jest spawanie w taki sposób, że płaskownik zwinięty do postaci dużej podkładki sprężystej jest podkładany pod prasę i ściskany, a boki są spawane. Jednak wykonanie tego płaskownika jest niezbyt dokładne i przed spawaniem konieczne jest znalezienie pozycji spoiny. Robot KR5arc HW KUKA jest wyposażony w czujnik laserowy, którym znajduje położenie powierzchni w poziomie, a drutem spawalniczym znajduje położenie powierzchni w pionie. Dopiero po takim określeniu położenia płaskownika, robot rozpoczyna spawanie.
Spawanie elementów wiatraków energetycznych
Sam proces spawania jest dość prosty (trzy spoiny liniowe). Natomiast ze względu na kształt spawanego zespołu („drabinka” w stałych odstępach stopni) wykorzystano istniejący w robocie schemat paletyzacji, tzn. zaprogramowano spawanie tylko pierwszego stopnia „drabinki”, a po zadeklarowaniu wartości przesunięć w kierunkach osi układu współrzędnych robot sam odtwarza trajektorie spawania dla kolejnych stopni. Znacznie ułatwiło to programowanie robota dla kilku typów „drabinek”.
Stanowisko spawania chłodnic aluminiowych
Chłodnice samochodowe muszą być oczywiście szczelne. Powtarzalność jakościową zapewnia spawanie robotem. Pierwsze stanowisko spawania chłodnic zostało zbudowane z użyciem robota IRB 1600 firmy ABB współpracującego z trójosiowym pozycjonerem IRBP o pionowej osi obrotu. Z robotem współpracuje spawarka CMT firmy Fronius połączona początkowo przez DeviceNet, a potem przez Ethernet. Pozycjoner pracuje jako zewnętrzna oś robota i spawanie odbywa się również w czasie obrotu pozycjonera, zapewniając ciągłość i szczelność spoiny.
PIAP zbudował także cztery stanowiska spawania chłodnic, już bardziej rozbudowane. W każdym stanowisku pracują dwa roboty IRB 1600 przy jednym pozycjonerze IRBK, tym razem o pionowej osi obrotu. Podobnie jak poprzednio, zastosowano spawarki CMT z siecią Ethernet. Spawane są jednocześnie dwa jednakowe zespoły chłodnic, przy czym spawanie odbywa się również w czasie obrotu pozycjonera. Ze względu na wysokie wymagania w zakresie płaskości i równoległości niektórych powierzchni po spawaniu dużym problemem było wykonanie odpowiednich przyrządów pozwalających na kompensację odkształceń spawalniczych. Zastosowano w nich możliwość regulowanego wstępnego naprężenia detali przed spawaniem i w efekcie po próbach udało się spełnić wymagane warunki.
Zgrzewanie
Drugim z często robotyzowanych procesów spajania jest zgrzewanie. Jednym z pierwszych zrobotyzowanych stanowisk zgrzewania było zbudowane przez PIAP w 1987 r. stanowisko zgrzewania nadkoli Fiata 126p w FSM Tychy. Zastosowanym robotem był IRb-60Z, zbudowany w PIAP na podstawie licencji, ale rozbudowany do standardu sześcioosiowego i z układem sterowania dostosowanym do specyfiki procesu zgrzewania.
Innym, nowszym stanowiskiem, zbudowanym w 1998 r., było stanowisko zgrzewania blach ocynkowanych do kominków domowych. Wykorzystano w nim robota IRB 6000 firmy ABB. Ponieważ przy zgrzewaniu blach ocynkowanych następuje szybkie zużycie elektrod, zaprogramowano w robocie mechanizm sprawdzania stopnia zużycia elektrod. Przed każdym cyklem zgrzewania robot przesuwał kilkakrotnie kleszcze zgrzewalnicze przed czujnikiem optycznym aż do przesłonięcia tego czujnika. Określona w ten sposób długość kleszczy była automatycznie wprowadzana jako parametr ruchu do programu robota.
Cięcie
Dość odległym od spawania i zgrzewania, ale również związanym z termiczną obróbką materiału procesem jest cięcie. Często, jako tzw. ukosowanie, jest stosowane przed spawaniem grubych materiałów. Podczas cięcia stali powstają szkodliwe pyły i gazy, dlatego proces ten jest często robotyzowany.
Jedno z pierwszych stanowisk cięcia zbudowanych przez PIAP było wyposażone w robota IRp-6 (rozwojowa wersja licencyjnego IRb-6) z układem sterowania zaprojektowanym i wykonanym w PIAP. Robot ten poruszał się po torze jezdnym z programowaną prędkością i dzięki swojej większej przestrzeni roboczej mógł operować na dłuższych elementach. Stanowisko było wykorzystywane do ukosowania grubych elementów (do 20 mm) przed ich spawaniem.
Po kilku latach pracy robot ten został zastąpiony robotem KR5arc firmy KUKA, również w procesie ukosowania gazowego. Cięcie gazowe wymaga jednak pewnej obróbki elementów po cięciu (wygładzanie, szlifowanie), podczas gdy wady tej pozbawione jest cięcie plazmą.
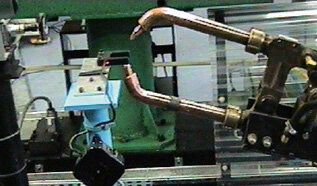
Badanie zużycia kleszczy czujnikiem optycznym – stanowisko zgrzewania z robotem IRB 6000 (prod. ABB)
Stanowisko do ukosowania plazmowego PIAP zbudował w tym samym zakładzie w 2009 r. Jakość powierzchni ukosowanych jest duża wyższa, większa jest również wydajność ukosowania. Nowoczesne stanowisko wytwarzania plazmy pozwala we współpracy z robotem na korygowanie trajektorii robota tak, aby utrzymywać stałą odległość głowicy plazmowej od ciętej blachy. W efekcie, mimo wyginania się blachy pod wpływem ciepła łuku plazmy, otrzymuje się jednakową szerokość ukosowanej fazy. Przy cięciu plazmowym problemem jest jednak większa ilość powstających pyłów i gazów. Wymagało to zbudowania specjalnej, mocno wentylowanej komory, w której odbywa się cięcie. Sam robot jest zabezpieczony dość szczelnym fartuchem, który zapobiega dostawaniu się pyłów do robota.
Innym stanowiskiem zrobotyzowanego cięcia gazowego było cięcie wspomnianych wcześniej pierścieni stalowych przed spawaniem. Ponieważ proces wyginania tych pierścieni nie był powtarzalny, konieczne było wyszukiwanie położenia materiału przed rozpoczęciem cięcia. Robot z czujnikiem laserowym przechodził nad zwojem pierścieni i określał położenie początków kolejnych zwojów. Następnie przechodził do procesu cięcia, nagrzewając początek każdego zwoju, włączając potem tzw. tlen tnący i przecinając materiał w ustalony sposób.
Nowe możliwości robotyzacji
W ostatnich kilku latach pojawiły się nowe możliwości robotyzacji spawania, zarówno od strony sprzętu spawalniczego, jak i robotów.
Firma Fronius wprowadziła na rynek wspomnianą już technologię CMT, w której proces spawania można bardzo precyzyjnie regulować. Dzięki dodatkowemu napędowi drutu, umieszczonemu blisko palnika, stopiony drut dozuje się praktycznie pojedynczymi kroplami. W ten sposób można dokładniej spawać cienkie blachy.
W PIAP prowadzone są obecnie prace nad tzw. spawaniem hybrydowym – MIG/MAG + plazma. W trakcie procesu spawania najpierw łuk plazmowy topi materiał, a potem spawarka MIG/MAG dodaje drut spawalniczy. Dzięki temu można z większą wydajnością spawać grube blachy. Niestety technologia ta jest dość droga i nie znalazła jeszcze zastosowania w Polsce, a w Europie – bardzo nieliczne.
Dobrze znane są dwie możliwości, jakie oferuje robot: wyszukiwanie położenia materiału przed spawaniem oraz nadążanie robota za zmiennym położeniem materiału w czasie spawania.
Wyszukiwanie położenia elementów spawanych (czy to drutem spawalniczym, czy czujnikiem zewnętrznym) dobrze sprawdza się w praktyce i jest obecnie standardem. Nadążanie robota za materiałem w trakcie spawania także może być realizowane za pomocą różnych czujników. Skaner laserowy umożliwia zastosowanie tego systemu właściwie dla każdego typu spoiny, ale jego cena jest porównywalna z ceną robota. Zastosowanie parametrów samego łuku spawalniczego jest oczywiście znacznie tańsze, ale ograniczone właściwie do spoin pachwinowych i spawania zakosowego.
Obie te możliwości odnoszą się do korekcji trajektorii robota, bez zmian parametrów spawania. Co pewien czas pojawiają się informacje o możliwości wpływania także na parametry spawania, np. zmniejszenia prędkości robota w razie wykrycia za pomocą czujnika szerszej szczeliny między spawanymi blachami. Wydaje się jednak, że na razie nie są one dostatecznie sprawdzone w praktyce. Na pewno jednak byłoby to bardzo przydatne rozwiązanie, pozwalające na zastosowanie robotyzacji spawania dla mniej dokładnie przygotowanych elementów.
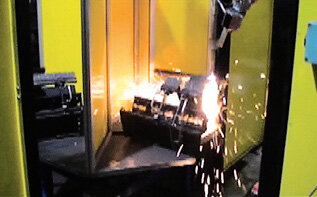
Stanowisko cięcia gazowego – robot KUKA KR5arc HW z czujnikiem laserowym wykrywającym położenie ciętych zwojów
Przygotowanie do robotyzacji spawania
Mimo coraz szerszego stosowania robotów przemysłowych do spawania, nie zawsze przyszły użytkownik zdaje sobie sprawę z konieczności przygotowania produkcji do właściwej pracy robota. Najważniejszymi elementami w tym przypadku są:
- powtarzalne wymiarowo przygotowanie detali,
- właściwe zaprojektowanie przyrządów,
- zapewnienie odpowiedniego dostarczania detali na stanowisko spawania,
- wykorzystanie robota co najmniej na dwie zmiany.
source: Automatyka 6/2016