Systemy fotowoltaiczne. Jak wybrać optymalne rozwiązanie?
Marcin Bieńkowski print
Instalacje fotowoltaiczne już na dobre zadomowiły się w naszym krajobrazie. Najczęściej spotkać je można na dachach jednorodzinnych domów, gdzie, dzięki różnym dostępnym od wielu lat programom dofinansowania, montaż paneli stał się wyjątkowo opłacalny. Teraz po zieloną, słoneczną energię coraz częściej zaczynają sięgać firmy i przedsiębiorstwa, które chcą obniżyć koszty swojej działalności.
Zanim zaczniemy omawiać poszczególne rodzaje instalacji fotowoltaicznych, warto przyjrzeć się budowie i zasadzie działania paneli fotowoltaicznych, określanych też często mianem paneli PV (photovoltaic). Podstawowym i najmniejszym elementem paneli fotowoltaicznych, czyli modułów, które montowane są np. na dachu, jest półprzewodnikowe, najczęściej krzemowe, nieco rzadziej germanowe lub selenowe ogniwo fotowoltaiczne, nazywane też ogniwem fotoelektrycznym lub fotoogniwem.
Początki fotowoltaiki sięgają 1839 r., kiedy to Antoine César Becquerel po raz pierwszy zaobserwował zjawisko zamiany promieniowania słonecznego na energię elektryczną. Pierwsze ogniwo fotowoltaiczne wykonane z krzemu powstało w 1954 r., a jego sprawność wynosiła wówczas zaledwie 6 %. Obecnie produkowane, pojedyncze ogniwa charakteryzują się sprawnością wynoszącą 14–19 %.
Ogniwa fotowoltaiczne
Fotoogniwo to, najprościej rzecz ujmując, element półprzewodnikowy, w którym na skutek występowania efektu fotoelektrycznego następuje przemiana energii świetlnej w energię elektryczną. Zasadniczo fotoogniwo zbudowane jest z dwóch warstw półprzewodnika. Pierwsza, znajdująca się na górze, to cienka i przezroczysta dla światła warstwa typu n. To nad nią umieszczona jest elektroda ujemna i powłoka antyrefleksyjna panelu. Na samym spodzie znajduje się zaś elektroda dodatnia. Druga umiejscowiona na dole, wprost na elektrodzie dodatniej, półprzewodnikowa, grubsza warstwa, to półprzewodnik typu p. Obie warstwy oddzielone są barierą potencjału, którą tworzy złącze p-n, o czym za chwilę. W tym miejscu trzeba podkreślić, że elementem czynnym fotoogniwa jest właśnie to półprzewodnikowe złącze p-n, choć generacja nośników odbywa się, tak naprawdę w całej objętości fotoogniwa.
W obecnie produkowanych ogniwach krzemowych warstwa półprzewodnika typu n, czyli ta, która skierowana jest w stronę światła słonecznego, domieszkowana jest ujemnie fosforem, co skutkuje wytworzeniem w niej nadmiaru elektronów (przewodnictwo elektronowe). Dolna warstwa krzemu tworzącego fotoogniwo domieszkowana jest dodatnio przez dodanie atomów boru (niedobór elektronów, przewodnictwo dziurowe). Po zetknięciu ze sobą obu typów półprzewodnika, na granicy tych dwóch warstw, atomy z warstwy typu n „oddają” swoje nadmiarowe elektrony atomom z warstwy typu p „zapełniając” ich dziury. W ten sposób powstaje złącze p-n, które składa się z atomów o obojętnym ładunku elektrycznym. Na skutek odpłynięcia nośników ładunku z półprzewodników typu n i p do złącza p-n, na jego granicy wytwarzana jest bariera potencjału blokująca dalszy napływ nadmiarowych ładunków z głębi półprzewodnika, a w obszarze granicznym tworzy się pole elektryczne.
Teraz, kiedy na obszar półprzewodnika, w tym na obszar złącza p-n, pada najmniejsza jednostka światła, czyli foton, który ma wyższą energię od szerokości przerwy energetycznej półprzewodnika, to jest on w stanie „wybić” elektrony walencyjne z atomów o obojętnym ładunku do pasma przewodzenia. W ten sposób powstają pary elektron-dziura. Wspomniane przed chwilą, związane z obecnością złącza p-n, pole elektryczne przesuwa, o ile wcześniej nie dojdzie do procesu rekombinacji, wytworzone nośniki dziurowe i elektronowe w różne strony, odseparowując je od siebie. Elektrony trafiają do obszaru n, zaś dziury do obszaru p.
Rozdzielenie nośników ładunku sprawia, że w półprzewodniku pojawia się różnica potencjałów, a więc powstaje na nim zewnętrzne napięcie elektryczne. Ponieważ rozdzielone nośniki są nośnikami nadmiarowymi, czyli charakteryzują się nieskończonym czasem życia, a napięcie na złączu p-n jest stałe, oświetlone światłem słonecznym ogniwo fotowoltaiczne działa jak typowe ogniwo elektryczne, które scharakteryzować można standardową siłą elektromotoryczną. Opisane zjawisko nosi nazwę efektu fotowoltaicznego.
Dzięki powstałemu na skutek działania promieni słonecznych napięciu elektrycznemu, po zamknięciu obwodu odbiornikiem energii, między górną a dolną elektrodą w obwodzie popłynie prąd. Wytworzony w ten sposób prąd to prąd stały, który nie jest standardowo wykorzystywany w energetyce. Aby móc z niego korzystać, konieczne jest zastosowanie falownika (inwertera), który zmieni prąd stały w prąd zmienny. Dla typowych paneli fotowoltaicznych, moc wytwarzana przez pojedyncze ogniwo wynosi ok. 1,5–2,5 W, przy napięciu ok. 0,5 V. Żeby wartość mocy była jak największa, należy ją dostarczyć w tzw. punkcie mocy maksymalnej MPP (Maximum Power Point), czyli w punkcie charakterystyki prądowo-napięciowej ogniwa fotowoltaicznego, dla którego wartość prądu i napięcia jest maksymalna.
Od ogniwa do panelu
Jak wspomniano, moc pojedynczego ogniwa fotowoltaicznego jest bardzo mała rzędu 1,5–2,6 W dla ogniwa o wymiarach 12,5 cm × 12,5 cm, dlatego w rzeczywistych instalacjach fotowoltaicznych pojedyncze fotoogniwa łączy się w moduły (panele), a te z kolei w łańcuchy (panele połączone ze sobą w szereg). Łańcuchy usytuowane względem siebie równolegle tworzą macierz fotowoltaiczną. Elektrycznie ogniwa modułu łączy się ze sobą równolegle, szeregowo lub szeregowo-równolegle, jednak już same moduły zawsze łączone są szeregowo. W konsekwencji, żeby uzyskać największą wydajność instalacji, każdy moduł musi pracować z maksymalną wydajnością. Obniżenie uzysku z jednego modułu wpływa na obniżenie wydajności całej instalacji.
Przy połączeniu szeregowym przednia elektroda pierwszego ogniwa jest połączona z tylną elektrodą ogniwa następnego, a napięcia w takim połączeniu poszczególnych ogniw sumują się. Przy połączeniu równoległym, przednia elektroda ogniwa poprzedniego łączona jest z przednią elektrodą ogniwa następnego. W tym przypadku prądy połączonych w ten sposób ogniw są sumowane. Łączenie szeregowo-równoległe polega na jednoczesnym łączeniu ogniw szeregowo i równolegle. Przy takim połączeniu sumują się zarówno napięcia, jak i natężenia prądów. Napięcia sumuje się w zależności od liczby modułów w łańcuchu jednego szeregu, natężenia prądów sumuję się w zależności do liczby połączonych równolegle łańcuchów.
Zacienienie ogniw fotowoltaicznych
W tym miejscu trzeba wspomnieć o bardzo częstym problemie eksploatacyjnym – chwilowym zacienieniu spowodowanym np. cieniem rzucanym przez drzewa, leżący śnieg, czy liście, które mogły przykleić się do pojedynczego modułu. Spadek mocy paneli zależy w tym przypadku od sposobu wykonanego połączenia, czy jest to połączenie szeregowe, czy równoległe. Warto wiedzieć, że 3 % cienia na module potrafi zmniejszyć wydajność łańcucha modułów aż o 25 %. Cień obejmujący już od 6 % do 10 % jednego modułu potrafi zmniejszyć wydajność całego łańcucha nawet o połowę.
Klasyczne instalacje fotowoltaiczne charakteryzują się szeregowym połączeniem modułów. Przy połączeniu szeregowym zacienienie tylko jednego ogniwa w całym panelu powoduje, że prąd płynący przez panel dostosowuje się do prądu płynącego przez najsłabsze ogniwo, w wyniku czego wartość prądu spada niemal do zera. Tak oświetlony panel szybko ulega przegrzaniu, co grozi jego uszkodzeniem.
Aby zapobiec spaleniu panelu, stosuje się bocznikowanie ogniw za pomocą diod. Diody są włączone równolegle w układ szeregowy ogniw i przy normalnej ich pracy są spolaryzowane w kierunku zaporowym, odwrotnie do ogniw fotowoltaicznych. Przy normalnym nasłonecznieniu i braku zacienienia prąd płynie przez ogniwa z pominięciem diod. Jeśli jedno z fotoogniw jest zacienione, dioda polaryzuje się w kierunku przewodzenia i prąd może płynąć w obwodzie z pominięciem zasłoniętego ogniwa.
Z kolei w instalacjach równoległych każde ogniwo pracuje niezależnie i zapewnia większe uzyski energii, pod warunkiem, że zastosowano cyfrowe optymalizatory mocy i inwertery dla każdego z modułów. Takie połączenie umożliwia śledzenie maksymalnego punktu mocy osobno dla pojedynczego modułu. Optymalizatory mocy sprawiają, że każde ogniwo redukuje straty związane z częściowym efektem zacienienia, zabrudzenia czy uszkodzenia pojedynczych modułów instalacji. Zastosowanie takiego rozwiązania powoduje spadek produkcji energii wyłącznie dla określonego panelu, a reszta będzie pracowała wykorzystując maksymalnie swoje możliwości.
Niestety, ze względu na konieczność stosowania bardziej rozbudowanych systemów sterowniczych, tego typu instalacje są droższe. Ogniwa połączone równoległe z wykorzystaniem optymalizatorów są doskonałym rozwiązaniem dla dachów o nieregularnych kształtach lub w instalacjach, gdzie poszczególne panele zorientowane są na różne strony świata.
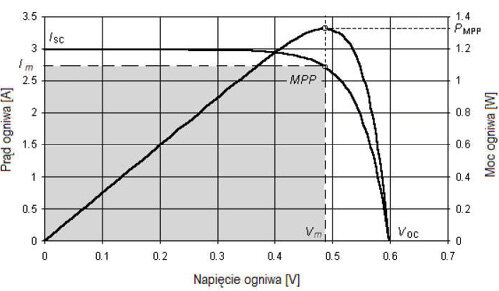
Rys. 3. Charakterystyka prądowo-napięciowej ogniwa fotowoltaicznego i krzywa sprawności. Moc w maksymalnym punkcie pracy jest równa polu zacienionego prostokąta, a punkt na przecięciu z krzywą MPP (Maximum Power Point) nosi nazwę maksymalnego punktu pracy. Źródło: instsani.pl
Rodzaje ogniw fotowoltaicznych
Ilość generowanego przez panel prądu zależy od jego sprawności. Sprawność ogniwa fotowoltaicznego to nic innego jak stosunek generowanej mocy do padającego na nie promieniowania słonecznego. W praktyce efektywność zależy od wielu czynników. Na część z nich mamy wpływ, na inne, takie jak warunki atmosferyczne nie. Sama skuteczność efektu fotowoltaicznego, jaką udaje się uzyskać, zależy od dwóch głównych czynników – od struktury materiału i właściwości zastosowanych warstw antyrefleksyjnych, zapobiegających rozpraszaniu i odbiciom padającego na panel PV światła. Powłoki te mają też za zadanie ograniczyć niekorzystne zjawisko nagrzewania się panelu. W krzemowych panelach słonecznych spadek sprawności sięga nawet 0,5 % na każdy dodatkowy stopień Celsjusza. Najmniej podatne na wysoką temperaturę, ale jednocześnie najdroższe są ogniwa z tellurku kadmu (CdTe).
W standardowych zastosowaniach konsumencko-przemysłowych najczęściej wykorzystuje się najłatwiejsze w produkcji i najtańsze, przede wszystkim pod względem kosztów materiałowych, panele krzemowe. Ze względu na stopień uporządkowania struktury krystalicznej krzemu, na rynku spotkać się można trzy odmiany paneli:
- z krzemu monokrystalicznego,
- z krzemu polikrystalicznego,
- z krzemu amorficznego.
Krzem monokrystaliczny charakteryzuje się silnie uporządkowaną strukturą pozbawioną większej liczby defektów. Rozpoznamy je po czarnym, ciemnogranatowym kolorze. Ogniwa zbudowane z tego rodzaju krzemu charakteryzują się najwyższą efektywnością przetwarzania energii słonecznej w energię elektryczną. Sprawność tego typu rozwiązań jest na poziomie 15–19 %.
W praktyce oznacza to, że energia promieniowania słonecznego padająca na 1 m2 ogniwa zostaje w 15 % przekształcona na energię elektryczną.
Na rynku najczęściej można spotkać nieco tańsze panele z krzemu polikrystalicznego, które rozpoznać można po niebieskim lub ciemnoniebieskim kolorze. Krzem taki charakteryzuje się mniej uporządkowaną strukturą oraz większą liczbą skaz. Z tego względu sprawność modułów zbudowanych z polikryształów krzemu osiąga wartość 14–16 %.
Z kolei najtańszy krzem amorficzny to krzem niemający uporządkowanej struktury krystalograficznej (jego struktura jest mocno chaotyczna) i charakteryzuje się stosunkowo dużą liczbą wad. Ma to bezpośredni wpływ na niską sprawność modułów, która wynosi obecnie zaledwie od 9 % do 14 %. Panele z krzemu amorficznego charakteryzują się nieco inną strukturą. Tutaj bardzo cienka warstwa krzemu osadzana jest na powierzchni innego materiału, np. szkła.
W panelach amorficznych nie jest zatem możliwe wyróżnienie pojedynczych ogniw, tak jak w panelach mono- i polikrystalicznych. Po tej charakterystycznej cesze można je rozróżnić od dwóch wyżej wymienionych typów. Panele tego typu najczęściej wykorzystuje się w urządzeniach elektronicznych i najtańszych instalacjach fotowoltaicznych. Zdecydowanie najpopularniejsze na rynku są obecnie moduły polikrystaliczne, około 70 % światowego rynku, i monokrystaliczne – około 25 %.
Wymienione typy paneli należą do urządzeń tzw. I generacji, opartych na opisanym krzemowym złączu p-n. Z paneli I generacji składa się 80 % systemów działających w Polsce. Oprócz nich dostępne są mniej popularne panele, do których należą:
- ogniwa II generacji, które produkowane są ze wspomnianego, odpornego na efekty termiczne tellurku kadmu (CdTe), panele wykonane z mieszaniny miedzi, indu, galu, selenu (CIGS), a także cienkowarstwowe (0,001–0,08 mm) panele z krzemu amorficznego nowej generacji. Półprzewodniki w tych ogniwach nakłada się za pomocą naparowywania, napylania oraz epitaksji. Dzięki technologii naparowywania, ogniwa II generacji można wykorzystywać jako elementy budowlane, np. nanieść je bezpośrednio na dachówki lub elementy wykończenia ścian.
- ogniwa III generacji bazują na różnych technologiach i nie są oparte na złączach półprzewodnikowych p-n. Tego typu ogniwa są obecnie w fazie rozwoju (dostępne są jedynie instalacje demonstracyjne) i charakteryzują się jeszcze dość niską sprawnością oraz żywotnością. Spośród stosowanych tu technologii wymienić można ogniwa barwnikowe, polimerowe oraz organiczne, wykorzystujące zjawisko fotosyntezy.
W tym miejscu należy dodać, że tradycyjne ogniwa fotowoltaiczne wyprodukowane w określonych warunkach z jednej partii materiału, prawie nigdy nie mają identycznych parametrów pracy. Różnice między poszczególnymi modułami lub partiami produkcyjnymi mogą dochodzić nawet do 5 %. Tę różnicę określa sie jako tolerancję mocy i podaje w procentach mocy modułu, np. dla modułu o mocy nominalnej P = 250 Wp, Power Tolerance ΔPmax = 0/+3 określa, że moc modułu w warunkach testowych może się wahać od 250 Wp do 253 Wp. Tolerancja ±2 dla tego samego modułu oznacza zakres rozpiętości mocy od 248 Wp do 252 Wp. Co ważne, moduły z tzw. dodatnią tolerancją są zawsze korzystniejszą opcją zakupu dla klienta.
Inwertery fotowoltaiczne
Jak wspomniano, panele fotowoltaiczne wytwarzają prąd stały, który nie jest używany w standardowych instalacjach energetycznych. Aby móc zatem skorzystać z wytworzonej energii konieczna jest instalacja falownika (inwertera), który zmieni prąd stały wytwarzany przez panele fotowoltaiczne na prąd przemienny.
Oprócz przetwarzania prądu stałego na prąd przemienny, inwerter fotowoltaiczny realizuje też takie funkcje jak:
- synchronizowanie instalacji PV z siecią elektroenergetyczną,
- monitorowanie i zarządzanie systemem fotowoltaiki,
- rejestrowanie danych eksploatacyjnych,
- śledzenie parametrów MMPT (maksymalny punkt mocy modułów fotowoltaicznych),
- automatyczne rozłączanie w razie awarii.
Inwertery fotowoltaiczne podzielić można na:
- Inwertery wyspowe (off-grid). Falownik nie nawiązuje połączenia z siecią, a więc nie może oddawać do niej nadwyżek energii. Ma natomiast możliwość ładowania akumulatorów. Inwerter tego typu często dostosowuje napięcie do potrzeb podłączonych urządzeń i baterii, na przykład maszyn i urządzeń wykorzystywanych na budowie w terenie. W praktyce przemysłowej tego typu falowniki są rzadko stosowane.
- Inwertery sieciowe (on-grid). Tutaj falownik nawiązuje bezpośrednie połączenie z siecią energetyczną, oddając do niej nadwyżki nagromadzonej energii. Co ważne, dostosowuje napięcie do jego poziomu w sieci. Ten typ urządzenia nie pozwala na ładowanie akumulatorów, niemniej jest najczęściej stosowanym obecnie rodzajem falownika.
Inwertery hybrydowe, to połączenie funkcji obu wymienionych wyżej systemów. Pozwala wytwarzać prąd z paneli fotowoltaicznych, oddawać go w razie potrzeby do sieci energetycznej, albo ładować akumulatory. Falownik taki charakteryzuje się większą liczbą wejść i wyjść.
Inny podział inwerterów fotowoltaicznych, to podział na inwertery jedno- i trójfazowe. Te pierwsze stosowane są wszędzie tam, gdzie nie ma potrzeby korzystania z sieci trójfazowej. Tego typu falowniki spotkać można najczęściej w mniejszych, domowych instalacjach fotowoltaiki o mocy do kilku kW. Z kolei inwertery trójfazowe, stosowane są w instalacjach przemysłowych i systemach fotowoltaiki o większej niż kilka kW mocy. Kolejnym podziałem, jest podział ze względu na wielkość instalacji: mikroinwertery (np. domki letniskowe), inwertery stringowe (instalacje fotowoltaiczne o mocy do 30 kW) i inwertery centralne (duże instalacje, np. farmy fotowoltaiczne).
W najbardziej nowoczesnych i zaawansowanych instalacjach wykorzystuje się tzw. mikroinwertery. Falowniki te wpinane są bezpośrednio w każde ogniwo. W ten sposób zwiększa się wydajność działania systemu fotowoltaiki. W przeciwieństwie do falowników centralnych, moduły fotowoltaiczne wykorzystujące mikrofalowniki działają równolegle. Każdy moduł pracuje zawsze z największą możliwą do osiągnięcia w danym momencie mocą, a mniejsza wydajność pojedynczego ogniwa nie wpłynie znacząco na pracę całej instalacji. Co więcej, mikrofalownik może automatycznie poinformować, który panel został przykryty np. liśćmi czy śniegiem.
Jak można się domyślić, inwerter fotowoltaiczny jest zbudowany z następujących elementów: falownika – generującego prąd przemienny, stopnia pośredniego i końcowego – odpowiedzialnych za stabilizację i wygładzanie przebiegu napięcia oraz układu zabezpieczeń – chroniącego przed awariami przez odłączenie zasilania w przypadku wykrycia niepożądanych parametrów pracy. Do tego dochodzi mikroprocesorowy moduł elektroniki sterującej, która odpowiada za dobieranie w czasie rzeczywistym optymalnych parametrów pracy systemu fotowoltaicznego i wyświetla użytkownikowi oraz archiwizuje wszystkie informacje o bieżącym działaniu fotowoltaiki.
Sterowanie nowoczesnym inwerterem jest wyjątkowo proste. Wszystkie parametry pracy są na bieżąco wyświetlane na panelu LCD i jednocześnie archiwizowane i wysyłane do firmowego systemu IT lub systemu automatyki. Do podstawowych parametrów zaliczyć można wskazania mocy, napięcia, prąd DC i AC, a także dzienną, miesięczną i roczną produkcję energii. Dostępne są też falowniki wyposażone w zewnętrzne układy pomiarowe. Dzięki temu mogą one mierzyć zużycie energii przez podłączone urządzenia, co może być istotne w warunkach przemysłowych.
Jedną z funkcji inwertera jest śledzenie parametru MPPT (maksymalny punkt mocy modułów fotowoltaicznych), który zależy od natężenia światła słonecznego. Jest to o tyle istotne, że dzięki systemowi śledzenia maksymalnego punktu mocy paneli fotowoltaicznych, instalacja fotowoltaiczna pozwala wykorzystywać nawet o 20 % więcej energii w porównaniu z falownikami starszego typu, które są pozbawione tego układu.
Oczywiście – inwerter zsynchronizowany z siecią (sieciowy lub hybrydowy) zlicza energię produkowaną przez panele słoneczne, a jednocześnie odczytuje prąd pobrany z sieci energetycznej. W ten sposób można monitorować rzeczywiste oszczędności uzyskane dzięki panelom słonecznym. Dane takie można porównać w różnych cyklach – chwilowe, godzina, doba, tydzień, miesiąc, rok itp.
Moc inwertera fotowoltaicznego powinna wynosić od 80 % do 95 % mocy znamionowej instalacji fotowoltaicznej. Co ważne, inwertery fotowoltaiczne dość dobrze znoszą lekkie przeciążenia, nie ma więc obawy, że instalacja ulegnie uszkodzeniu. Dodatkowo, w polskich warunkach klimatycznych panele nigdy nie osiągają swoich nominalnych wartości mocy podawanej przez producenta.
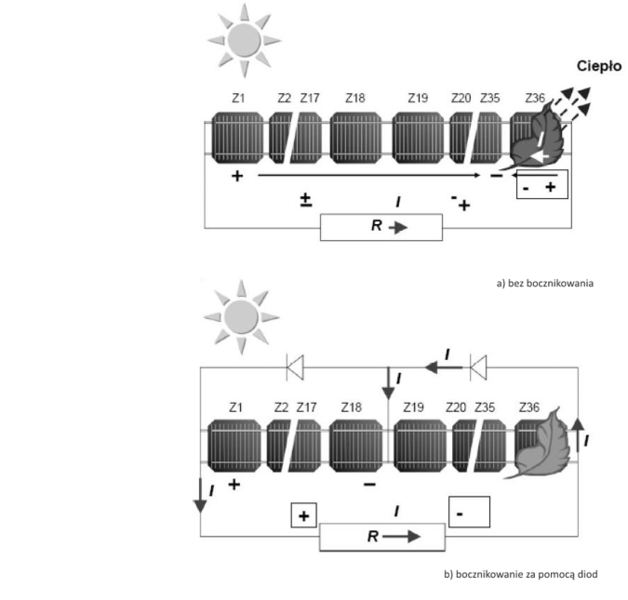
Rys. 5. Bocznikowanie diodami ogniw fotowoltaicznych, zapobiegające ich spaleniu w wypadku zacienienia.
Rodzaje instalacji fotowoltaicznych
Przejdźmy teraz do instalacji fotowoltaicznej traktowanej jako cały system. Niezależnie od jej rodzaju w skład wchodzą omówione już panele fotowoltaiczne, inwerter a także niezależne zabezpieczenia chroniące przed zbyt wysokim napięciem oraz system montażowy. Rodzaj samej instalacji skorelowany jest z rodzajem zamontowanego w systemie falownika. I tak instalacja sieciowa on-grid, nazywana też instalacją sieciową, to po prostu instalacja fotowoltaiczna podłączona do sieci dystrybucyjnej. Instalacje on-grid stanowią zdecydowaną większość systemów fotowoltaicznych montowanych na świecie. Tutaj energia elektryczna z modułów fotowoltaicznych wykorzystywana jest na potrzeby pracy podłączonych urządzeń, a w przypadku wygenerowania nadwyżek energii, sprzedawana do sieci energetycznej.
Podobnie jak w przypadku inwertera, instalacją off-grid lub instalacją autonomiczną nazywamy instalację działająca poza publiczną siecią elektroenergetyczną. Tutaj, podobnie jak w sieciowej, energia elektryczna z modułów fotowoltaicznych wykorzystywana jest na potrzeby pracy podłączonych urządzeń domowych, a w przypadku wystąpienia nadwyżek energii, wykorzystuje się ją do ładowania akumulatorów.
Z kolei w przypadku instalacji hybrydowej nie ma już prostej analogii do rodzaju użytego falownika. Fotowoltaiczna instalacja hybrydowa to instalacja, w której oprócz paneli fotowoltaicznych korzysta się z innego, własnego źródła energii elektrycznej. Są to najczęściej turbiny wiatrowe lub generatory spalinowe. Instalacja ta może również współpracować z siecią energetyczną. Energia pozyskiwana z paneli może być zużywana od razu, a jeśli do tego nie dojdzie jest magazynowana i może być spożytkowana później. Tego typu instalacje wykorzystywane są przez firmy energetyczne, a także korzysta się z nich w wypadku zasilania dużych fabryk lub całych kompleksów przemysłowych.
Instalacje fotowoltaiczne podzielić można również ze względu na ich umiejscowienie. Najpopularniejsze są instalacje fotowoltaiczne montowane na dachu. W przypadku montażu systemu fotoogniw na dachu ważne jest ich usytuowanie, konstrukcja oraz otoczenie. Najlepszy do montażu paneli fotowoltaicznych jest dach zwrócony na południe, który umożliwia umieszczenie paneli pod kątem około 35°. Bardzo istotna jest przestrzeń dookoła instalacji. Nie powinna być ona zacieniona przez obiekty zewnętrzne, takie jak drzewa i słupy, ale również elementy samego budynku jak np. komin. Panele fotowoltaiczne na dachu montowane są na specjalnych konstrukcjach dostosowanych do materiału, którym pokryty jest dach i do kąta jego nachylenia. Podczas montażu należy też pamiętać o względach architektonicznych – estetyce i o tym, aby instalacja w miarę możliwości współgrała ze znajdującą się obok zabudową.
Drugim rodzajem instalacji fotowoltaicznych, ze względu na ich umiejscowienie, są instalacje fotowoltaiczne posadowione na gruncie. Panele fotowoltaiczne na gruncie montuje się w przypadku budowy farm fotowoltaicznych zasilających np. fabryki lub kompleksy przemysłowe lub, gdy montaż paneli na dachu jest zbyt skomplikowany lub niemożliwy, np. na dachu zabytkowego budynku. Powodem montażu na gruncie zamiast na dachu są zazwyczaj liczne zacienienia, skomplikowana, nietypowa konstrukcja dachu lub brak na nim miejsca na odpowiednią liczbę paneli.
Instalacja taka charakteryzuje się bardziej rozbudowaną konstrukcją i dłuższym czasem montażu. Przed jej wykonaniem trzeba wziąć pod uwagę szereg czynników. Najważniejszym z nich jest to, aby na działce znajdowało się odpowiednio dużo miejsca, ponieważ prawidłowe funkcjonowanie instalacji wymaga odpowiedniej przestrzeni między panelami. W inwestycji trzeba uwzględnić również obecne zacienienie i przyszły plan zagospodarowania terenu.
Wybór instalacji fotowoltaicznej
Obecnie po instalacje fotowoltaiczne sięgają już nie tylko indywidualni użytkownicy, ale również firmy, które chcą zoptymalizować koszty poprowadzenia działalności i produkcji. Często wybieranym rozwiązaniem są tzw. mikroinstalacje fotowoltaiczne. Systemy o mocy do 50 kWp nie podlegają bowiem obowiązkowi zgłoszenia, a ich tworzenie i montaż nie podlega dodatkowym uwarunkowaniom prawno-technicznym. Firma powinna jednak dokładnie przeanalizować, jaką moc ma mieć projektowana instalacja. Ewentualne nadwyżki wyprodukowanego prądu zawsze można odsprzedać do zakładu energetycznego z zyskiem dla przedsiębiorstwa.
Cenę i moc potrzebnej instalacji fotowoltaicznej najczęściej przelicza się posługując się jednostką o nazwie kilowatopik (kWp), czyli mocą maksymalną panelu osiąganą w warunkach laboratoryjnych (Watt-peak). Jak można wyczytać na stronach PGNiG, ceny instalacji w segmencie klientów indywidualnych obecnie wahają się w granicach 4–7 tys. zł netto za 1 kWp, natomiast w segmencie przedsiębiorców zaczynają się już od ok. 3 tys. zł za 1 kWp. Średnia cena dla instalacja 40–50 kWp to około 3,5 tys. zł netto za 1 kWp.
Na cenę wpływ ma przede wszystkim jakość wykorzystanych komponentów, tj. modułów, inwertera, konstrukcji wsporczych oraz okablowania. Na koszt wpływać będą też warunki instalacji, np. odległość do najbliższej stacji transformatorowej, czy konieczność wykonania dodatkowych badań, np. nośności dachu lub badań geologicznych (w przypadku instalacji gruntowych).
Jak już wspomniano, decydując na instalację fotowoltaiczną dla firmy, warto w pierwszym kroku przeanalizować profil energetyczny przedsiębiorstwa, czyli schemat korzystania z energii elektrycznej, który zawsze będzie się różnił od schematu energetycznego gospodarstwa domowego. W przeważającej mierze firmy rozpoczynają pracę rano i kończą po południu, więc zapotrzebowanie na prąd występuje w czasie jego produkcji przez fotoogniwa.
Montaż i podłączenie paneli fotowoltaicznych w przedsiębiorstwie charakteryzuje się mniejszym nakładem środków niż w przypadku instalacji systemu fotowoltaicznego w domu. Na niższe koszty wpływa między innymi wielkość instalacji, gdyż im większa moc całego systemu, tym niższe koszty zainstalowania 1 kW. Ponieważ firmy cechują się dość dużym zapotrzebowaniem na energię, moc instalacji fotowoltaicznej powinna wynosić przynajmniej 10 kW.
Warto też dodać, że inwestycję systemu fotowoltaicznego w firmie należy potraktować jako środek trwały i amortyzować pomniejszając kwotę odprowadzanego podatku. A niższe koszty inwestycji w system solarny to szybszy okres zwrotu z przedsięwzięcia. Zwrot z inwestycji w instalację fotowoltaiczną zajmuje obecnie od 6 do 10 lat. Jej żywotność jest dużo dłuższa, po tym okresie instalacja fotowoltaiczna przynosi zyski. Jednym z ciekawszych rozwiązań na sfinansowanie instalacji fotowoltaicznej dla firmy może być też leasing. Jest to relatywnie tanie rozwiązanie, gdyż jego koszt to zaledwie kilka procent w skali roku a w ten sposób nie trzeba angażować środków własnych. Atutem jest tu też fakt, że można go wpisać w koszty działalności firmy. Działanie to prowadzi do zmniejszenia obciążeń podatkowych z tytułu poniesionych kosztów finansowych.
Jak działa licznik dwukierunkowy? Niezbędnym elementem sieciowej instalacji fotowoltaicznej jest licznik dwukierunkowy. Jego zadaniem jest zliczanie energii elektrycznej, którą wytworzyła instalacja fotowoltaiczna oraz energii pobranej z sieci publicznej. Jest to więc urządzenie pomiarowe, które dokonuje pomiarów dwukierunkowego przepływu prądu – do sieci oraz z sieci. Na ich podstawie prosument (osoba będąca jednocześnie producentem i odbiorcą energii elektrycznej) rozlicza się z zakładem energetycznym. Funkcjonalność sieci elektrycznej jest zachowana. Jedyną różnicą jest dodatkowa mikroinstalacja do produkcji prądu. W zależności od inwertera (jednofazowy, trójfazowy) i od tego, czy zasilamy jedną bądź trzy fazy, firma energetyczna zamontuje odpowiedni licznik. Instalacja fotowoltaiczna może być również wyposażona w dodatkowy licznik, który umożliwi także analizowanie wykresów zużycia energii elektrycznej i energii, która dostarczana jest do sieci energetycznej. Źródło: Sunsol.pl |
Dobór mocy i montaż
Przed rozpoczęciem inwestycji, warto zastanowić się nad tym, jakiej wielkości instalacja jest tak naprawdę nam potrzebna i jak prawidłowo dobrać jej moc. Najlepszym rozwiązaniem jest instalacja o mocy, która pokryje całkowicie nasze zapotrzebowanie na energię elektryczną i pozwoli nadwyżki oddawać do sieci. Od 1 lipca 2016 r. w Polsce funkcjonuje system rozliczenia energii przez prosumentów w bilansach rocznych, który zakłada, że dla instalacji do 10 kWp za każdy 1 kWh energii wprowadzonej do sieci można odebrać 0,8 kWh energii, zaś dla instalacji 10–50 kWp, jest to 0,7 kWh energii.
W przypadku użytkowników indywidualnych obowiązuje system bezgotówkowego rozliczania wyprodukowanej i oddanej do sieci energii elektrycznej z zakładem energetycznym. Firma może natomiast podpisać stosowne umowy z dostawcą prądu. Należy jednak koniecznie sprawdzić, na jakich warunkach będziemy mogli odsprzedawać prąd i w jakich ilościach, zanim przystąpimy do kalkulacji. Zazwyczaj tę część energii, której przedsiębiorstwo nie wykorzysta na potrzeby własne, może odsprzedać do zakładu energetycznego po obowiązującej w danym kwartale cenie hurtowej.
Przyjmuje się, że instalacji fotowoltaicznej nie należy przewymiarować o więcej niż około 20 %. W polskich warunkach klimatycznych optymalnie usytuowana instalacja może wyprodukować rocznie nieco ponad 1000 kWh z 1 kWp zainstalowanej mocy. Wartość zużywanej mocy przez naszą firmę najlepiej poznamy analizując pobór prądu z kilku lat, najlepiej korzystając z ze zarchiwizowanych odczytów z liczników lub jeśli nie ma takiej możliwości, można też przeanalizować dotychczasowe faktury lub poprosić o pomoc dostawcę energii elektrycznej. Do takiego archiwalnego zużycia należy dodać planowane zwiększenie zużycie prądu, które może wynikać z zakupu nowych urządzeń, maszyn czy linii produkcyjnych.
Najlepiej, żeby instalacja fotowoltaiczna pokrywała zapotrzebowanie całej firmy lub danego budynku na energię elektryczną. Nie zawsze jednak będziemy dysponować odpowiednią ilością miejsca. Z tego powodu niezbędne jest dokonanie pomiarów dostępnej przestrzeni montażowej. Konieczne jest sprawdzenie wymiarów dachu bądź gruntu, a także określenie wymiarów i lokalizacji tych elementów, które mogą odpowiadać za zacienienie fotoogniw. Chodzi tu o takie elementy, jak kominy, anteny, drzewa, czy budynki sąsiadujące. Istotne znaczenie ma również skierowanie w stronę południa oraz nachylenie paneli fotowoltaicznych, które wpływa na dostępną przestrzeń montażową.
Panele fotowoltaiczne można zamontować wszędzie, gdzie będą wystawione na działanie promieni słonecznych. Optymalny jest dach, ale panele mogą być także instalowane na ogrodzeniach lub innych obiektach architektonicznych. W wypadku instalacji gruntowych, o ile warunki na to pozwalają, panele fotowoltaiczne powinny być usytuowane w kierunku południowym. Na południu Polski panele powinny być montowane pod kątem 20–30° licząc nachylenie od powierzchni gruntu, a na północy kraju pod kątem 25–35°. W ten sposób zapewnione są najlepsze warunki naświetleniowe. Przy montażu paneli na dachach płaskich często stosuje się niższy, bo wynoszący zaledwie 10–15° kąt nachylenia. Wynika to z faktu ograniczonej powierzchni montażowej i ze względów bezpieczeństwa ochrony instalacji przed silnymi wiatrami.
W przypadku instalacji dachowych, jeżeli kąt pochylenia dachu nie jest optymalny, stosuje się specjalne konstrukcje wsporcze. Na wybór konkretnego rozwiązania i jego cenę ma wpływ materiał, którym pokryty jest dach. Jeżeli kąt dachu mieści się w przedziale od 15° do 60° przy odchyleniu od południa ±45°, stosowanie konstrukcji wsporczej dopasowującej kąt montażu paneli nie jest uzasadnione pod względem ekonomicznym.
Jeśli chodzi o wymiary samych modułów PV, to typowy moduł fotowoltaiczny ma około 1,67 m długości i około 1 m szerokości. Wymagana powierzchnia montażowa potrzebna do uzyskania 1 kWp z instalacji fotowoltaicznej, wraz z uwzględnieniem koniecznych ze względów technicznych przestrzeni instalacyjnych między modułami, wynosi ok. 5,5 m2 dla standardowych, dostępnych na rynku modułów o mocy 330 Wp każdy.
Montaż instalacji fotowoltaicznej, to inwestycja, która może być również opłacona z dofinansowań promujących odnawialne źródła energii. Przede wszystkim należy sprawdzić dostępne Regionalne Programy Operacyjne, gdyż każde z województwo lub region oferuje własne zasady dofinansowania energetyki ekologicznej. Dodatkowo istnieje możliwość pozyskania środków z Funduszy Unijnych, a także z Narodowego Funduszu Ochrony Środowiska.
Jak poprawnie policzyć moc instalacji Dobierając moc instalacji można przyjąć, że w polskich warunkach nasłonecznienia na każde zużyte rocznie 1000 kWh energii dobiera się 1,25 kWp mocy instalacji fotowoltaicznej. Obliczając moc warto skorzystać z poniższego wzoru: Moc instalacji [kWp] gdzie: • Ek – ilość zużywanej rocznie energii [kWh] • a – procentowy udział bieżącej konsumpcji własnej [%] • b – procentowy udział ilości energii oddanej do sieci [%] • opust – 0,8 kWh za 1 kWh oddaną do sieci w przypadku instalacji do mocy 10 kW; 0,7 kWh, w przypadku instalacji o mocy 10–50 kW. • a + b = 100 % • uzysk – roczna produkcja energii z 1 kWp zainstalowanej mocy przez instalację PV [kWh] Źródło: columbusenergy.pl |
Zielona fabryka
Trend związany z montażem paneli fotowoltaicznych wpisuje się szerzej w proekologiczne działania związane z zielonymi budynkami lub zieloną fabryką. Wiele firm deklaruje chęć jak największego wyeliminowania negatywnego wpływu swojej produkcji na środowisko naturalne. Chodzi tutaj przede wszystkim o przedsiębiorstwa i zakłady, które realizując proekologiczną politykę poszczycić się mogą maksymalną efektywnością energetyczną, instalacjami odnawialnej energii OZE, w tym instalacją paneli fotowoltaicznych, zgodnością z przepisami ekologicznymi, zrównoważoną gospodarką dotyczącą odpadów, ograniczeniem do minimum strat, w tym strat energii w procesie produkcyjnym. Takie zielone przedsiębiorstwo produkcyjne powinno również uwzględniać wpływ swojej działalności na środowisko, a także gospodarować materiałami, odpadami i energią zgodnie z zasadami ekorozwoju.
Szeroko pojęta ekologia, stała się nie tylko modą, ale również wyzwaniem związanym z ograniczeniem emisji gazów cieplarnianych, w tym CO2. Dlatego coraz więcej firm zwraca się ku własnej zielonej energii. Idąc o krok dalej, panele fotowoltaiczne wpisujące się w koncepcję zielonej fabryki montowane są już nie tylko na dachach budynków fabrycznych ale tworzą coraz częściej tak zwane farmy fotowoltaiczne. Bardzo częstą praktyką jest wykorzystywanie do ich budowy nieużytków rolnych o minimalnej powierzchni 2 ha z gruntami klasy IV lub gorszej. Farma taka powinna powstać na płaskim terenie, ponadto powinna być zlokalizowana w pobliżu sieć niskiego lub średniego napięcia – od rodzaju sieci zależy wielkość instalacji, jaką można do niej wpiąć, dzięki czemu łatwiej będzie można zawrzeć umowę przyłączeniową.
Budowie farm fotowoltaicznych i wpisywanie się coraz większej liczby firm w proekologiczne trendy związane z zieloną fabryką, czy szerzej zielonym przemysłem podyktowane jest też względami praktycznymi. Polska sukcesywnie zamykać będzie kopalnie, drożeje też prąd pozyskiwany z węgla. Opłatę mocową w 2021 r. określono na 76,20 zł w przeliczeniu na każdą skonsumowaną megawatogodzinę energii w godzinach szczytowego jej poboru. W przypadku dużych fabryk, wzrost rocznych kosztów energii elektrycznej w związku z nową stawką opłaty mocowej może być nawet sześciocyfrowy. Jedynym rozwiązaniem może okazać się fotowoltaika.
source: Automatyka 4/2021