Bezpieczeństwo w Ethernecie przemysłowym
Redakcja serwisu print
Osoby odpowiedzialne za utrzymanie ruchu w zakładach przemysłowych dobrze sobie zdają sprawę z tego, jak ważne jest zapewnienie wysokiego poziomu bezpieczeństwa. Gdy na terenie hali fabrycznej pojawia się Ethernet przemysłowy, zadanie to bardzo się komplikuje, szczególnie jeśli zakładowa sieć zostaje podłączona do Internetu.
Bezpieczeństwo w kontekście sieci przemysłowych nie jest tym samym zagadnieniem, co w przypadku sieci komputerowych, w których sprowadza się do zapewnienia spójności i poufności danych. Znacznie większe znaczenie nabiera dostępność komunikacji, która nierzadko bezpośrednio decyduje o bezpieczeństwie fizycznym pracowników hal fabrycznych.
Wyjątkowo ważne jest też utrzymanie opóźnień w komunikacji na założonym poziomie, gdyż zależy od nich poprawność wykonywania procesów przemysłowych, w których ewentualne przestoje wiążą się najczęściej z ogromnymi kosztami.
Redundancja w przemyśle
Podstawowym sposobem zapewniania ciągłości prowadzenia procesów przemysłowych jest stosowanie redundancji. Polega ona na zwielokrotnianiu instalowanych urządzeń, które w przypadku sieci zaliczane są do elementów aktywnych, a także na prowadzeniu redundantnych połączeń pomiędzy nimi.
W przypadku sieci bazujących na magistralach, nierzadko możliwe jest połączenie ze sobą krańcowych elementów aktywnych sieci i stworzenie pierścienia. Ponieważ klasyczny Ethernet bazuje jednak raczej na topologii gwiazdy, redundancję można zapewnić prowadząc równolegle więcej niż jeden przewód łączący ze sobą dwa urządzenia oraz odpowiednio konfigurując złącza, do których przewody te są podłączone.
W rozległych sieciach ethernetowych redundantne połączenia tworzy się jednak inaczej – poprzez wprowadzanie tzw. oczek sieci – małych lub nawet dużych pierścieni, w ramach których komunikacja może odbywać się kilkoma drogami, a marszruta – czyli trasa którą pokonują pakiety – dobierana jest automatycznie w zależności od warunków panujących na łączach.
Zarządzanie skomplikowaną siecią przemysłową
Okazuje się, że efektywne nadzorowanie procesu routingu jest znacznie trudniejsze niż w klasycznym Ethernecie. W zwykłych sieciach komputerowych, w razie wystąpienia usterki, próby transmisji są powtarzane, aż po pewnym czasie urządzenia biorące udział w nieudanej komunikacji zaznaczają w swojej pamięci, że dana trasa jest aktualnie niedostępna i szukają innej. Preferowane trasy dobierane są poprzez obliczanie liczby przeskoków, czyli w gruncie rzeczy urządzeń pośredniczących w transmisji do docelowej końcówki sieciowej, ale proces optymalizacji marszruty przebiega stopniowo i dosyć wolno.
Takie postępowanie nie sprawdziłoby się w przemyśle, gdzie konieczne jest nie tylko błyskawiczne reagowanie na usterki ale też utrzymanie minimalnych opóźnień w trakcie normalnej pracy. Dlatego stosuje się różnorodne protokoły do nadzorowania sieci i, które pozwalają na tworzenie wirtualnej mapy połączeń i optymalne przekierowanie ruchu w przypadku wystąpienia usterek.
Poszczególni producenci opracowują własne odmiany protokołów tego typu, bazując najczęściej na znanych z klasycznego Ethernetu: SNMP (Simple Network Management Protocol) i STP (Spanning Tree Protocol). Ten pierwszy obsługiwany jest przez bardzo wiele – w tym również zwykłych – urządzeń ethernetowych i umożliwia zdalną konfigurację sieci oraz zarządzanie jej połączeniami. Drugi służy szybkiemu tworzeniu tras alternatywnych w przypadku wystąpienia usterki. Jego przemysłowe implementacje pozwalają ograniczyć czas reakcji na awarię do ułamków sekundy, a dokładne opóźnienie przełączenia zależy od konkretnej implementacji i liczby urządzeń oraz złożoności topologii sieci.
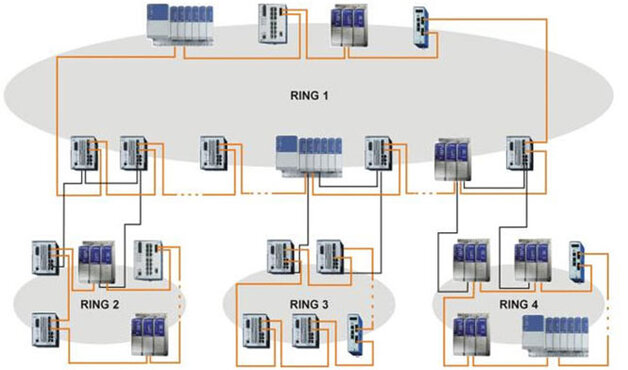
Rys. Liczne pierścienie w topologii jednej sieci przemysłowej. W tym przypadku zilustrowano sieć wykonaną w oparciu o urządzenia firmy Hirschmann, której protokoły Hiper Ring i Fast Hiper Ring pozwalają na uzyskanie czasu przełączania marszrut w wypadku usterki, nie większych niż 400 ms i 10 ms (odpowiednio)
Ethernet przemysłowy i zakłócenia
Usterki, jakie mogą wystąpić w Ethernecie przemysłowym obejmują nie tylko awarie wynikające z fizycznego przerwania łącza lub uszkodzenia urządzenia aktywnego. Trudne warunki środowiskowe panujące w halach fabrycznych mogą niekorzystnie wpływać na transmisję, tymczasowo lub trwale ją uniemożliwiając. Aby zmniejszyć ryzyko wystąpienia takiej sytuacji, dobrą praktyką jest stosowanie ekranowanych połączeń, które znacząco redukują wpływ zakłóceń elektromagnetycznych.
Alternatywną, choć istotnie droższą (i nie zawsze dostępną) jest wykorzystanie połączeń optycznych. Światłowody nie są bowiem wrażliwe na szum elektromagnetyczny panujący w otoczeniu. Ważne jest też zapewnienie odpowiedniej izolacji przed kurzem i wodą oraz wibracjami. Najczęściej wystarcza zastosowanie elementów sieciowych wyposażonych w złącza o dobrym stopniu ochronności IP, dostosowanym do przewidywanych warunków środowiskowych.
Wpływ Internetu
Większość dotąd opisanych kwestii związanych z bezpieczeństwem znajduje zastosowanie w przypadku niemal każdej sieci przemysłowej. Tymczasem Ethernet przemysłowy narażony jest na dodatkowe ryzyko, związane z dosyć bezpośrednim połączeniem infrastruktury fabrycznej do Ethernetu.
Ważną zaletą protokołu IP jest przecież możliwość prowadzenia wygodnej komunikacji z praktycznie każdym klasycznym urządzeniem ethernetowym. Pozwala to np. zarządzać pracą sieci, przeglądać dane historyczne z poziomu biur, a nie hal fabrycznych, a czasem i zdalnie – z dowolnego miejsca na świecie, poprzez Internet.
Nawet jeśli bezpośredni dostęp do sieci fabrycznej przez Internet nie zostanie zagwarantowany, warto pamiętać, że bardzo często komputery będące elementami ERP (Enterprise Resource Planning) czy MES (Manufacturing Execution Systems) są podłączone jednocześnie do sieci zakładowej oraz do biurowej, a poprzez tę drugą – do Internetu.
Istnieje więc ryzyko, że poprzez błędy w konfiguracji lub niepożądane działania pracowników, powstanie ścieżka umożliwiająca zdalny dostęp do urządzeń wykonawczych już z poziomu Internetu. A to sprawia, że zapewnienie kompleksowego bezpieczeństwa Ethernetu przemysłowego jest zagadnieniem naprawdę skomplikowanym.
Czytaj także:
>>>Ethernet Przemysłowy: Profinet i Ethernet/IP
Keywords
bezpieczeństwo, ethernet, Ethernet przemysłowy, sieci przemysłowe, snmp, stp