Aparatura kontrolno-pomiarowa w systemach automatyki
dr inż. Marcin Bieńkowski print
Aparatura kontrolno-pomiarowa to ogólne pojęcie określające przyrządy pomiarowe i różnego rodzaju mierniki wykorzystywane w najróżniejszych dziedzinach nauki i techniki, a także w różnorodnych branżach związanych z przemysłem, produkcją, wydobyciem, a nawet transportem. W systemach automatyki wykorzystuje się aparaturę kontrolno-pomiarową po to, aby możliwe było nadzorowanie przez człowieka realizowanego automatycznie procesu technologicznego bądź sprawdzenie aktualnego stanu maszyny czy urządzenia.
Praktycznie nie ma dzisiaj dziedziny przemysłu, w której nie byłyby potrzebne różnego rodzaju pomiary wielkości fizycznych, począwszy od temperatury, przez pomiary wielkości mechanicznych, w tym siły, masy, grubości, długości i kąta, objętości, poziomu, wysokości, naprężeń, ciśnienia, natężenia i barwy światła, wilgotności, radiacji, natężenia dźwięku, właściwości materiałów (np. koloru, chropowatości czy gęstości), a na pomiarach wielkości elektrycznych i magnetycznych skończywszy. Trudno też wymienić wszystkie branże, w których aparatura ta nie byłaby niezbędna.
Bez urządzeń kontrolno-pomiarowych nie funkcjonowałyby elektrownie, wodociągi, przemysł spożywczy, transport, motoryzacja, a nawet najmniejszy zakład mechaniczny, nie mówiąc już o dowolnej fabryce czy kopalni. Z różnych urządzeń kontrolno-pomiarowych korzystają również pracownicy związani z budownictwem czy gastronomią, laboratoria badawcze, a także – coraz częściej – gospodarstwa domowe. Nie chodzi tu tylko o termometry do pomiaru temperatury, ale także higrometry, barometry, manometry, czujniki dymu i/lub gazu.
Rodzaje przyrządów pomiarowych
Najogólniej rzecz ujmując, przyrządy pomiarowe podzielić można na mierniki, rejestratory, charakterografy i detektory, a ze względu na funkcję metrologiczną na przyrządy pomiarowe kontrolne i użytkowe. Jak można się domyślić, mierniki to po prostu przyrządy pomiarowe pozwalające określić wartość mierzonej wielkości. Wielkość ta przedstawiona jest za pomocą podziałki w przyrządach analogowych lub – w przyrządach cyfrowych – za pomocą liczby przedstawiającej bezpośrednio jej wartość. Przykładem typowego miernika może być woltomierz, amperomierz, galwanometr czy uniwersalny multimetr. Miernikiem jest też zwyczajna suwmiarka czy śruba mikrometryczna. Szerszym pojęciem tego słowa jest „przyrząd pomiarowy” – obejmuje również urządzenia do rejestracji wartości, generatory pomiarowe, wzorce, analizatory itp. Z kolei rejestrator to urządzenie służące do zapisu, a więc archiwizacji i prezentacji zebranych informacji o przebiegu mierzonych parametrów w czasie, np. temperatury czy ciśnienia oraz ewentualnie warunków, w których pomiary były prowadzone – np. temperatury otoczenia lub wilgotności. Rejestratory można sklasyfikować według metody zapisu danych procesowych na:
- rejestratory z zapisem danych na taśmie papierowej,
- rejestratory z cyfrowym zapisem danych.
Pierwszego typu rejestratorów w systemach automatyki praktycznie już się nie spotyka. Używane są natomiast dość często w medycynie (EKG, EEG) czy transporcie (tachografy). Jeśli chodzi o rejestratory z cyfrowym zapisem, to nośnikiem danych najczęściej jest wbudowana pamięć flash, dysk twardy lub zewnętrzny napęd USB. Coraz częściej stosowany jest też zdalny zapis danych na firmowych serwerach NAS lub bezpośrednio w chmurze. Dlatego rejestratory cyfrowe wyposażane są standardowo w interfejsy komunikacyjne pozwalające na przesyłanie danych w czasie rzeczywistym.
Warto zauważyć, że spotykane w przemyśle rejestratory oferują zwykle proste funkcje skalowania sygnału mierzonego i jego rejestrację w jednostkach fizycznych. Ponadto często są wyposażane w wyjścia alarmowe pozwalające sygnalizować przekroczenia dopuszczalnych dla danego procesu wartości granicznych oraz interfejsy komunikacyjne umożliwiające przesyłanie wartości chwilowych do systemów bezpośrednio sterujących procesem technologicznym, takich jak sterowniki PLC czy systemy SCADA.
Już na etapie produkcji rozstrzyga się, czy rejestrator będzie przystosowany do pomiaru określonych parametrów (np. temperatura, prąd, napięcie) i w jakim zakresie, czy też będzie wyposażony w wejścia prądowe uniwersalne (0/4…20 mA DC), pozwalające na odbiór sygnałów pomiarowych z czujników różnego typu, w szerokim zakresie wartości.
Dwie ostatnie grupy przyrządów, czyli charakterografy i detektory mają znacznie mniejsze znaczenie z punktu widzenia systemów automatyki. Pierwsze z nich to urządzenia służące do przeprowadzenia szybkich pomiarów, które pozwalają na niemal natychmiastową możliwość wykreślania charakterystyk mierzonego elementu. Zazwyczaj charakterografów używa się wyznaczania charakterystyk prądowo-napięciowych elementów półprzewodnikowych. Z kolei detektor to urządzenie służące do wykrywania i ewentualnie rejestracji zjawisk oraz parametrów fizycznych sygnałów, których nie można bezpośrednio obserwować. Innymi słowy, detektor stosowany jest wówczas, gdy badany sygnał nie możne być zarejestrowany bezpośrednio i musi być zamieniony na inną formę umożliwiającą obserwację bądź rejestrację. Detektory podzielić można na detektory cząstek, np. detektory cząstek elementarnych; detektory promieniowania elektromagnetycznego, np. fototranzystory; detektory zmiany składu chemicznego, np. spektrometry, tlenomierze, jonometry czy katarometry (detektory stężeniowe) oraz na detektory zmian parametrów fizycznych.
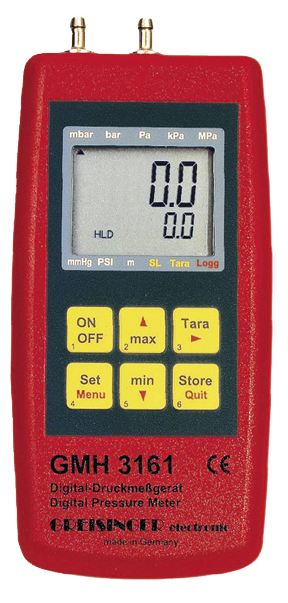
Greisinger GMH 3161 to przenośny manometr dla służb utrzymania ruchu z króćcami podłączeniowymi pozwalający mierzyć ciśnienie do 0.350 bar
Aparatura kontrolno-pomiarowa a przyrząd pomiarowy
Zastanówmy się teraz, jaka jest różnica między aparaturą kontrolno-pomiarową a przyrządem pomiarowym. Oba pojęcia używane są zazwyczaj zamiennie, niemniej jednak przyrząd to pojedynczy miernik, do którego może być podłączonych jeden lub kilka czujników pomiarowych. Aparatura zaś to jeden miernik o znacznie większych możliwościach technicznych albo zespół mierników połączonych w system pomiarowy sterujący procesem technologicznym. I tak prosty woltomierz czy multimetr trudno nazwać aparaturą kontrolno-pomiarową, jednak cyfrowy oscyloskop, na którym też można przeprowadzić proste pomiary, a jednocześnie sprawdzić charakterystyki sygnałów, jest już typową aparaturą kontrolno-pomiarową. Podobnie cęgowy miernik pola magnetycznego to typowy przyrząd pomiarowy, ale już spektrometr rezonansu pola magnetycznego to aparatura pomiarowa.
Aparatura przenośna
W tym miejscu warto też wspomnieć o mającej coraz większe znaczenie przenośnej aparaturze pomiarowej. Aparaturę przenośną, a więc taką, którą można zabrać ze sobą w miejsce dokonywania pomiarów, można podzielić na dwie grupy, przede wszystkim ze względu na cel ich zakupu i zastosowanie w firmie.
Pierwszą grupę stanowi sprzęt pozwalający na kompleksową diagnostykę urządzeń elektrycznych oraz mechanicznych, w tym linii produkcyjnej. W jej skład wchodzą szeroko rozumiane pomiary elektryczne, urządzenia do pomiaru wibracji, akcelerometry, analizatory ultradźwiękowe i rentgenowskie, przenośne wagi, a także kamery termowizyjne lub czujniki do kontaktowych pomiarów temperatury. Drugą grupę stanowi sprzęt kontrolny, pozwalający sprawdzić i ewentualnie wywzorcować czujniki oraz aparaturę na stałe zamontowaną w maszynach czy na linii produkcyjnej. Do tej grupy zaliczyć można m.in. obiektowe kalibratory pozwalające na weryfikację, czy urządzenia pomiarowe nadal zapewniają pomiar w odpowiedniej klasie dokładności, a także przenośne czujniki niebezpiecznych gazów lub kamery termowizyjne sprawdzające poprawność działania zamontowanych na linii pirometrów. W obu grupach urządzeń przenośnych widać wyraźny trend maksymalnego uproszczenia ich obsługi, nacisk na integrację urządzeń z oprogramowaniem i interfejsami komunikacyjnymi, w tym łącznością bezprzewodową oraz na konstruowanie urządzeń łączących w sobie kilka funkcji pomiarowych.
Urządzenia przenośne mogą bez problemu gromadzić dane pomiarowe w pamięci i przesyłać je np. do chmury. Montuje się też w nich duże wyświetlacze graficzne pozwalające na łatwe zobrazowanie kilku parametrów pomiarowych jednocześnie oraz na tworzenie w czasie rzeczywistym czytelnych wykresów. Sprzęt ten jest dużo mniejszy i wygodniejszy w użyciu niż jeszcze kilka lat temu. Mierniki z górnej półki, o największych możliwościach pomiarowych, charakteryzują się coraz większą dokładnością i rozdzielczością, zbliżoną do sprzętu typowo laboratoryjnego wykorzystywanego do wzorcowania.
Mierniki i systemy monitoringu, pomiary ciągłe
Aparatura pomiarowa wykorzystywana w systemach automatyki i na liniach produkcyjnych to przede wszystkim systemy pomiarów wielkości elektrycznych, termometry, ultradźwiękowe czujniki napełnienia zbiorników, wagi tensometryczne i różnego rodzaju manometry oraz przepływomierze mierzące w sposób ciągły ciśnienie i przepływ medium procesowego w fazie ciekłej lub gazowej.
Jeśli chodzi o mierniki elektryczne, to są one zazwyczaj dostosowane do montażu na szynie DIN. Przykładem tego typu urządzenia może być trójfazowy, cyfrowy wskaźnik napięcia DMV-3, firmy F&F. Jest to po prostu trójfazowy woltomierz z ledowym wyświetlaczem wartości napięcia dla każdej o dokładności wskazań 1%, który monitoruje w sposób ciągły dostarczane na linie napięcie i w razie przekroczenia wartości krytycznych jest w stanie wszcząć alarm. Podobnym przyrządem, ale tym razem analogowym jest amperomierz ABB AMT 1/10, również przystosowany do montażu na szynie DIN. Jest to typowy, tani miernik kontrolny przystosowany do pracy ciągłej, który pozwala na pomiar prądów do 10 A.
Trochę bardziej zaawansowanym miernikiem elektrycznym dostosowanym do montażu na szynie DIN jest analizator sieci jedno- i trójfazowej M2M MODBUS firmy ABB. Umożliwia on ciągłe pomiary w czasie rzeczywistym głównych parametrów elektrycznych sieci jednofazowych lub trójfazowych, takich jak: napięcia, prąd, częstotliwości, współczynnik mocy, moc czynną i bierną, a także energię aktywną i bierną. Sprawdza on również jakość energii dzięki pomiarowi THD.
Kolejną grupą urządzeń stosowanych standardowo w systemach automatyki, które dostosowane są do montażu w szafkach sterowniczych są różnego rodzaju urządzenia do monitoringu i regulacji temperatury. Przykładem może być cyfrowy sterownik temperatury Omron E5CC. Wyposażony jest w szeroki zakres wejść czujników, w tym wejście uniwersalne, termoelementy, Pt oraz analogowe wejścia prądowe/napięciowe, co pozwala nie tylko na pomiary temperatury, ale również na sterowanie procesem technologicznym.
Urządzenia Przemysłowego Internetu Rzeczy
Skoro jesteśmy przy sterownikach, to trzeba zauważyć, że coraz częściej standardowe sterowniki PLC łączy się z czujnikami pomiarowymi będącymi elementami Przemysłowego Internetu Rzeczy. Sensory wyposażone w moduły komunikacyjne, najczęściej zgodne z przewodowym standardem Ethernet lub bezprzewodowym Wi-Fi, rzadziej Bluetooth, mogą aktywnie wysyłać rejestrowane wartości do urządzeń nadrzędnych, specjalizowanych sterowników lub sterowników PL, pełniących tu funkcję miernika. Dzięki możliwości dwustronnej komunikacji czujnik może dokonywać pomiaru tylko na wyraźne żądanie odczytu, co zmniejsza obciążenie sieci, a dodatkowo wydłuża czas pracy urządzenia.
Jak widać, podstawowym celem wdrożenia systemu pomiarowego wpisującego się w koncepcję Internetu Rzeczy, jest uzyskanie wszechstronnych informacji na temat procesów, operacji i produkcji. Zebrane dane pozwalają usprawnić działania i dostawy, a także lepiej wykorzystywać zasoby i poprawić jakość obsługi. Co więcej, system IoT pozwala zminimalizować ryzyko wystąpienia awarii, co przyczynia się do zwiększenia kontroli nad procesem technologicznym.
Jeśli chodzi o urządzenia pomiarowe, to tak naprawdę budowa całego systemu sprowadza się do zastąpienia klasycznych czujników pomiarowych inteligentnymi czujnikami wyposażonymi w interfejs komunikacyjny. Inteligencja czujnika wiąże się ze wstępnym przetworzeniem mierzonej wartości na sygnał cyfrowy (bądź liczbę odpowiadającą jego wartości), który wstępnie przetwarzany jest w czujniku i wysyłany do urządzenia nadrzędnego za pomocą interfejsu komunikacyjnego.
Z punktu widzenia tworzenia systemu pomiarowego są to dokładnie te same czujniki, które wykorzystuje się w tradycyjnych systemach automatyki, z tym, że mają dodany interfejs komunikacyjny pozwalający oddalić czujnik od miernika nawet o setki metrów. Miernikiem, o czym wspomniano, może być dowolny sterownik PLC, który odbiera sygnały i wysterowuje urządzenia wykonawcze, a także przesyła informacje o wykonanych przez inteligentne sensory pomiarach do systemu nadzorującego pracę linii produkcyjnej czy maszyny lub systemu SCADA odpowiedzialnego za realizację i monitoring całego procesu technologicznego.
Pomiary elektryczne
W praktyce przemysłowej najczęściej dokonuje się pomiarów elektrycznych. Oprócz standardowych pomiarów napięcia, natężenia prądu, rezystancji czy mocy w kluczowych dla procesu sterowania punktach związanych z zasilaniem urządzeń, czy to prądem stałym, czy zmiennym, wykonuje się szereg pomiarów diagnostycznych mających na celu dostatecznie wczesne wykrycie usterek i zapobieżenie awarii.
Najważniejszą grupę urządzeń stanowią tu multimetry, czyli wielofunkcyjne, uniwersalne przyrządy, które pozwalają na pomiar kilku fizycznych wielkości elektrycznych, jak prąd, napięcie, rezystancja, a w droższych, bardziej uniwersalnych modelach także częstotliwości, pojemności, mocy czynnej, biernej, pozornej i innych często nieelektrycznych wielkości, takich jak temperatura czy wilgotność.
W nowoczesnych multimetrach możliwa jest automatyczna zmiana zakresów pomiarowych, co pozwala na pomiary parametrów zarówno dla urządzeń elektronicznych, jak i energetycznych. Sprzęt ten umożliwia wykonywanie pomiarów wartości rzeczywistych i skutecznych, a także na gromadzenie danych i tworzenie – jeśli jest wyposażony w graficzny wyświetlacz – różnego rodzaju wykresów w czasie rzeczywistym dla mierzonych wielkości. Co ważne, niektóre zaawansowane multimetry łączą w sobie również funkcję oscyloskopu. Tego typu sprzęt stosowany jest najczęściej przez techników odpowiedzialnych za uruchomienie linii produkcyjnej i służby utrzymania. Oczywiście w multimetry wyposażeni są też serwisanci dokonujący napraw maszyn i systemów automatyki.
Wybór multimetrów na rynku jest ogromy, od prostych urządzeń za kilkadziesiąt złotych, po bardzo precyzyjne urządzenia laboratoryjne czy sprzęt dopuszczony do pracy w atmosferze wybuchowej zgodny z wymaganiami ATEX. Innymi słowy są modele gorsze i lepsze, bardziej i mniej dokładne, bardzo funkcjonalne, rozbudowane, jak i wyjątkowo proste i tanie, trwałe i odporne na przeciążenia oraz takie, które zabezpieczone są w podstawowy sposób. Producenci dzielą je na kilka segmentów.
Pierwszy z nich to sprzęt o podstawowej funkcjonalności, niedrogi, a więc jednocześnie o umiarkowanej dokładności i rozdzielczości. Dla użytkownika najistotniejszy jest tutaj stosunek jakości do ceny, który zapewni odpowiednią trwałość urządzenia i odporność na typowe przeciążenia.
Drugą grupę aparatury stanowią bardziej zaawansowane, typowo przemysłowe mierniki o większej dokładności pomiarowej i realizujące więcej funkcji. Charakteryzują się zatem większą rozdzielczością pomiaru i z reguły mają „o jedną cyfrę na wyświetlaczu więcej” niż urządzenia poprzedniej grupy, zapewniając tym samym dokładny pomiar do 3–4 miejsc po przecinku. Charakteryzują się też szerszym zakresem pomiarowym, umożliwiającym mierzenie „elektronicznych” wielkości o niewielkich wartościach, jak i pozwalającym na prowadzenie pomiarów energetycznych związanych z napięciem zasilającym doprowadzonym do maszyn i urządzeń. Zwykle też spełniają wyższe normy w zakresie bezpieczeństwa użytkowania i mają odporne na uszkodzenia mechaniczne obudowy.
Trzecią kategorię stanowi sprzęt pomiarowy o największych możliwościach pomiarowych, wysokiej dokładności i rozdzielczości wynoszącej 6–8 cyfr, a nawet więcej. Jest to sprzęt, który może być używany w laboratoriach. Ma duże możliwości i rozbudowaną funkcjonalność, często wyposażony jest w wyświetlacz graficzny, moduł oscyloskopu oraz czujniki temperatury i wilgotności służące m.in. do kompensacji prowadzonych pomiarów.
Warto w tym miejscu wspomnieć o uniwersalnych miernikach cęgowych, które są swego rodzaju rozwinięciem grupy multimetrów, pozwalając na pomiary wartości prądów bez konieczności przerywania ciągłości obwodu elektrycznego. Nowoczesna aparatura tego typu umożliwia wykonywanie pomiarów nie tylko prądu mierzonego cęgami, ale też różnych wielkości elektrycznych, w tym częstotliwości, i magnetycznych. Nowoczesne mierniki mogą mierzyć m.in. bardzo dokładnie prądy nawet o niewielkiej wartości, zarówno dla prądu stałego, przemiennego, jak i przemiennego ze składową stałą. Bardziej zaawansowane modele poradzą sobie z pomiarami wirowania faz. Oczywiście wszystkie wymienione wyżej urządzenia, zarówno multimetry, jak i mierniki cęgowe, w bardziej zaawansowanych wersjach pozwalają na przechowywanie i transmisję danych do firmowej sieci Ethernet, najczęściej w sposób bezprzewodowy.
Pomiary rezystancji izolacji i uziemień
Oddzielną grupę urządzeń pomiarowych stanowią mierniki rezystancji izolacji i uziemienia. Nowoczesne mierniki izolacji pozwalają na pomiar rezystancji małym prądem, dzięki czemu możliwe jest uzyskanie zakresu pomiarowego przekraczającego 100 GΩ. Wartość napięcia pomiarowego można wybrać z zakresu 50 V, 100 V, 250vV, 500 V oraz 1000 V lub, w zależności od budowy miernika, w sposób płynny od 50 V do 1000 V, zwykle z dokładnością do 10 V. Pomiar przeprowadzić można metodą dwu- oraz trójprzewodową lub za pomocą specjalnego adaptera wpinanego do gniazda sieciowego, przy czym dokonywana jest automatyczna analiza kombinacji pomiarowych, ze wskazaniem prądu upływu. W niektórych modelach przewidziano możliwość pomiaru ciągłości połączeń ochronnych i wyrównawczych prądem ≥ 200 mA, zgodnie z normą PN-EN 61557-4 z jednoczesnym przeprowadzeniem autokalibracji przewodów pomiarowych.
Proste mierniki, dzięki którym możliwy jest pomiar uziemień, przystosowane są do prowadzenia pomiarów metodą techniczną, tzw. niskoczęstotliwościową. W tym przypadku możliwe jest również wykonanie pomiaru ciągłości połączeń ochronnych i wyrównawczych. Pomiar rezystancji jest przeprowadzany metodą 2p. W bardziej zawansowanych modelach przewidziano możliwość pomiaru ciągłości połączeń wyrównawczych i ochronnych prądem 200 mA z funkcją autozerowania. Napięcie pomiarowe wybiera się z zakresu 25–50 V.
Droższe, bardziej zaawansowane modele mierników uziemienia pozwalają na pomiar metodą techniczną (3p, 4p). W niektórych modelach pomiar jest przeprowadzany przy użyciu prądu o częstotliwości 125 Hz, dzięki czemu uzyskuje się wysoki poziom odporności na zakłócenia pochodzące z sieci energetycznej. Urządzenia te standardowo oferują funkcje pomiaru rezystywności gruntu i niskich rezystancji. Na rynku dostępne są przyrządy przeznaczone do pomiarów uziemień w energetyce, w których zakres pomiarowy, zgodnie z normą PN-EN 61557, zaczyna się od 0,30 Ω.
Kalibratory
Podsumowując temat aparatury kontrolno-pomiarowej służącej do pomiarów wielkości elektrycznych należy też wspomnieć o kalibratorach. To urządzenia, które służą do generowania odpowiednich sygnałów wzorcowych, pozwalających na skalibrowanie innej aparatury pomiarowej. Kalibratory umożliwiają wzorcowanie wielkości elektrycznych oraz nieelektrycznych. Najczęściej generują sygnały pozwalające skalibrować wartości prądu, napięcia, mocy, rezystancji, częstotliwości, energii, pojemności czy indukcyjności, a z wielkości nieelektrycznych symulacji temperatury czy siły. W dwóch ostatnich przypadkach podawany jest prąd lub napięcie o takich wartościach, jakie generują termopary czy czujniki tensometryczne.
Kalibrator pozwala na nastawianie wielkości wyjściowej oraz wybór źródła odniesienia, będącego źródłem wielkości elektrycznej przeznaczonej do porównywania. Wbudowany komparator porównuje wartości wielkości wyjściowej z wartością odniesienia. Dzięki temu na wyjściu kalibratora podawany jest sygnał wzorcowy
o bardzo dużej dokładności i stabilności w czasie. Kalibratory wykorzystywane są przede wszystkim tam, gdzie musimy dokonywać okresowej kalibracji aparatury pomiarowej, a zwłaszcza tam, gdzie obligują do tego obowiązujące przepisy.
Pomiar wielkości nieelektrycznych
Oprócz pomiarów elektrycznych, do prawidłowego działania systemów automatyki niezbędne jest kontrolowanie również różnego rodzaju wielkości fizycznych. Pomiary te mają na celu dostarczanie informacji na temat aktualnego stanu poszczególnych elementów systemu sterowania. Na tej podstawie można odpowiednio sterować elementami wykonawczymi. W tej grupie wielkości fizycznych najczęściej monitoruje się temperaturę, ciśnienie, wilgotność, szybkość przepływu i poziom napełnienia zbiorników lub silosów.
Pomiar temperatury w warunkach przemysłowych może być prowadzony na dwa sposoby – kontaktowo i bezkontaktowo. Pierwsza z metod jest prostsza i tańsza, Jej zaletą jest też duża dokładność pomiarów. Wykorzystuje się tu przede wszystkim czujniki rezystancyjne (termistory) oraz termoelementy, które podłączane są do miernika lub przetwornika, o czym piszę w dalszej części artykułu. Zaletą pierwszej grupy czujników jest ich szeroka oferta obejmująca różnego rodzaju obudowy, sposoby montażu i podłączenia – praktycznie dostosowane do każdej aplikacji. Z kolei termopary, czyli urządzenia wytwarzające napięcie, które zależy od mierzonej temperatury, sprawdzają się w miejscach trudno dostępnych lub tam, gdzie panuje wysokie ciśnienie, np. wewnątrz elementów wykonawczych maszyn hydraulicznych lub w aplikacjach związanych z przetwórstwem tworzyw sztucznych (pomiar temperatury wtrysku).
Istotnym elementem procesu pomiaru temperatury jest przetwornik. Zadaniem przetwornika temperatury jest przetworzenie sygnału otrzymywanego z czujnika na zrozumiały dla reszty urządzeń systemu automatyki sygnał elektryczny. Przetworniki produkowane są w najróżniejszych formach, począwszy od modułu montowanego fabrycznie w sterowniku, przez niezależne moduły przystosowane do montażu na szynie DIN, na tzw. modelach głowicowych skończywszy.
Pomiarów bezkontaktowych dokonuje się za pomocą pirometrów lub kamer termowizyjnych. Ich zaletą, oprócz braku fizycznego kontaktu z mierzonym obiektem, jest możliwość kontroli temperatury w trudno dostępnych miejscach. Ponadto pozwalają one na bezproblemowy pomiar bardzo wysokiej temperatury panującej np. w wielkim piecu czy na walcowni, lub tam, gdzie temperatura może dochodzić do kilku tysięcy stopni. Zazwyczaj za pomocą pirometrów mierzy się temperaturę od –65 °C do 1250 °C. Obudowa czujnika zapewnić może wysoki stopień ochrony IP, nawet do IP68, i możliwość pracy w atmosferze wybuchowej ATEX. Dzięki tym cechom możliwe jest ich stosowanie w skrajnie trudnych warunkach środowiskowych. Niektóre czujniki dostosowane są do wykrywania gorących obiektów w ruchu. Pirometry mogą występować jako oddzielne czujniki montowane na stałe na linii produkcyjnej, jak i w postaci przenośnego miernika z ekranem graficznym, gdzie pomiaru dokonuje bezpośrednio człowiek. Z kolei z kamer termowizyjnych korzysta się do prowadzenia pomiarów temperatury obiektów w ruchu lub do kontroli temperatury obiektów – używane są najczęściej przez służby utrzymania ruchu. Zakres pomiarowy zależy od czujnika, ale również kamery pozwalają na pomiary od ujemnych wartości temperatur dochodzących nawet do –120 °C do temperatur sięgających tysięcy stopni. Większość nowoczesnych kamer zapewnia automatyczne wyszukiwanie zimnych i gorących przedmiotów, rejestruje datę i czas pomiaru oraz korzysta z oprogramowania do analizy zdjęć i tworzenia protokołów kontroli niezbędnych dla służb utrzymania ruchu. Wiele modeli wyposażonych jest również w łączność bezprzewodową umożliwiającą wysyłanie zdjęć wprost do firmowej sieci komputerowej lub do chmury.
Ciśnienie
Kolejną wielkością stosowaną do kontrolowania stanu systemów automatyki jest ciśnienie. Oprócz pomiarów dokonywanych z wykorzystaniem czujników mechanicznych, czyli różnego rodzaju manometrów, coraz częściej pomiary ciśnienia realizuje się za pomocą czujników elektronicznych, np. tensometrów. Ich zaletą jest możliwość bezpośredniego wykorzystywania sygnału pomiarowego w układach rejestrujących i regulacyjnych. W przypadku czujników mechanicznych należy wcześniej dokonać konwersji, np. przesunięcia na odpowiadający mu sygnał elektryczny, co czasem bywa kłopotliwe, choć oczywiście tego typu urządzenia również dostępne są w sprzedaży.
Jeśli chodzi o komponenty elektroniczne używane bezpośrednio do pomiaru ciśnienia, to można je podzielić na czujniki tensometryczne, piezorezystancyjne oraz pojemnościowe, a same przetworniki ciśnienia na standardowe i programowalne.
Zasada działania tensometrycznych czujników ciśnienia bazuje na wykorzystaniu zjawiska zmiany rezystancji drutu oporowego na skutek przyłożonej do niego siły. W przypadku manometrów czujniki tensometryczne najczęściej montowane są na membranie. Jej odkształcanie pod wpływem ciśnienia wywieranego przez mierzone medium sprawia, że zmienia się również siła nacisku na czujnik, a w konsekwencji także rezystancja drutu oporowego – im większa przyłożona siła, tym większa rezystancja tensometru. Największą wadą tensometrycznych sensorów ciśnienia jest duża zależność czułości i dokładności pomiaru od sposobu umieszczenia czujnika na powierzchni czynnej membrany, zaletą zaś wysoka odporność na wibracje i uderzenia.
Z kolei w przypadku czujników piezorezystancyjnych siła przykładana jest wprost do powierzchni krzemowej sensora. Dzięki temu uzyskano większą czułość oraz dokładność pomiaru ciśnienia. Ponadto właściwości fizykochemiczne krzemu pozwalają na pomiar bardzo małych ciśnień, rzędu pojedynczych milibarów. Wykonaną z krzemu membranę z naniesionymi na niej, metodami znanymi z produkcji układów półprzewodnikowych, zestawem sensorów piezorezystancyjnych umieszcza się w hermetycznej obudowie. Przestrzeń między czujnikiem a zewnętrzną membraną wypełnia się cieczą manometryczną, którą zazwyczaj stanowi olej syntetyczny. Zewnętrzna membrana, uginając się, napiera na olej, a ten na membranę czujnika. Wadą tego typu rozwiązań jest wpływ rozszerzalności temperaturowej cieczy na pomiary. Dlatego w tego typu manometrach minimalizuje się przestrzeń między zewnętrzną membraną a krzemową membraną czujnikami, a dodatkowo w cyfrowym mierniku stosuje się algorytmy kompensacji temperaturowej.
Jeśli chodzi o czujniki pojemnościowe, to w tym przypadku cienka, krzemowa membrana umieszczana jest między okładzinami, tworząc w ten sposób kondensator. Ciśnienie medium, uginając membranę, wpływa na pojemność tak zbudowanego kondensatora, która to pojemność przetwarzana jest na sygnał wyjściowy. Czujniki pojemnościowe są umieszczane w szczelnej obudowie wypełnionej olejem i wyposażonej w membranę wykonaną najczęściej ze stali nierdzewnej. To właśnie ona bezpośrednio styka się z medium, którego ciśnienie mierzymy. Zaletą pojemnościowych czujników ciśnienia jest ich duża czułość.
W tym miejscu warto podkreślić fakt, że standardowe przetworniki ciśnienia na wyjściu podają analogowy sygnał prądowy lub napięciowy, zaś programowalne – sygnał cyfrowy. Jak można się domyślić, wyposażone są one w przetwornik analogowo-cyfrowy oraz mikroprocesor, który odpowiada za ewentualną kompensację pomiarową oraz wstępną obróbkę sygnału, tak aby bez problemu mógł być wysyłany do nadrzędnych elementów systemu automatyki.
Pomiary wilgotności
Następną, wymienioną wcześniej, istotną wielkością nieelektryczną, której pomiary są powszechnie realizowane w przemysłowych systemach automatyki, jest wilgotność. Zbyt wysoka lub zbyt niska wilgotność może nie tylko negatywnie wpłynąć na parametry fizyczne surowców i materiałów wykorzystywanych podczas procesu produkcji, ale również przyczynić się do uszkodzenia sprzętu elektronicznego wykorzystywanego na linii technologicznej.
Aparaturą wykorzystywaną do pomiarów wilgotności są higrometry, które można podzielić na trzy grupy. Pierwsza to higrometry korzystające z metod higroskopowych, wśród których wymienić można rezystancyjne i pojemnościowe czujniki wilgotności. Wykorzystuje się tutaj zjawisko zmiany właściwości elektrycznych materiału pod wpływem zmian wilgotności. Druga grupa mierników wykorzystuje zjawisko kondensacji, co oznacza, że wilgotność jest wyznaczana w sposób pośredni za pomocą pomiaru temperatury skraplania. Zasada działania czujnika polega na schładzaniu wewnętrznego lustra, do chwili skroplenia się na nim pary wodnej i wykrycia tego faktu za pomocą czujnika optycznego. Trzecią grupę stanowią optyczne czujniki podczerwone, w których wykorzystuje się zjawisko absorpcji promieniowania podczerwonego przez wilgoć zawartą w powietrzu. Czujnik wykorzystuje zjawisko pochłaniania fal podczerwonych mogą mierzyć wilgotność w zakresie 0–95% z dokładnością sięgającą 0,1%.
Przepływomierze
Pomiary przepływu dotyczą przepływu gazów, cieczy oraz materiałów sypkich, takich jak np. mąka, piasek, ziarno czy cement. Pomiary przepływu niezbędne są przede wszystkim we wszelkiego typu systemach dozujących oraz w gazociągach i rurociągach. Pozwalają one kontrolować prawidłowość przebiegu procesu technologicznego. Monitorowanie przepływu pozwala tez wykrywać nieszczelności instalacji.
Istnieje kilka rodzajów przepływomierzy, które podzielić można na mechaniczne i elektryczne. Te pierwsze dzieli się z kolei na objętościowe, manometryczne, zmiennoprzekrojowe oraz z otwartym kanałem. Te drugie to magnetyczne, impulsowe, ultradźwiękowe, Coriolisa i przepływomierze typu Vortex.
Objętościowe przepływomierze mechaniczne działają na zasadzie pomiaru szybkości napełniania i opróżniania określonej objętości. Najbardziej znanym rodzajem tego typu przepływomierzy są przepływomierze łopatkowe wykorzystywane do odmierzania gazów i paliw ciekłych. Ze względu na charakter pomiaru przepływomierze objętościowe najlepiej sprawdzają się przy odmierzaniu cieczy lepkich. Jeśli chodzi o przepływomierze manometryczne, to ich zasada działania sprowadza się do wyznaczenia różnicy ciśnień między wejściem i wyjściem układu pomiarowego. Ich zaletą jest stosunkowo niska cena. Z kolei przepływomierze zmiennoprzekrojowe, czyli tzw. rotametry charakteryzują się stożkową budową i obecnością pływaka, którego położenie wyznacza aktualny przepływ. Stosuje się je zarówno do pomiaru przepływu cieczy, jak i gazów. Ostatnią grupę przepływomierzy mechanicznych stanowią przepływomierze z otwartym kanałem, gdzie prędkość przepływu określa się na podstawie poziomu cieczy w pionowej rurce.
Jeśli chodzi o przepływomierze elektromagnetyczne, to mierzą one prędkość przepływu na podstawie szybkości przemieszczania się medium przez określoną powierzchnię, prostopadłą do kierunku pola magnetycznego. Przepływomierze ultradźwiękowe dokonują pomiaru prędkości przepływu na podstawie szybkości przemieszczania się medium przez określoną z góry powierzchnię prostopadłą do kierunku przepływu. Zaletą obu powyższych metod jest bezkontaktowy pomiar, brak spadku ciśnienia oraz możliwość ich wykorzystania do pomiaru przepływu materiałów sypkich. W tym ostatnim przypadku ultradźwięki można zastąpić promieniowaniem rentgenowskim.
Przepływomierze Coriolisa, zwane inaczej masowymi, wykorzystują siłę bezwładności nazywaną siłą Coriolisa. Zgodnie z prawami mechaniki, jednoczesnemu występowaniu ruchu obrotowego i postępowego ciała towarzyszy powstawanie siły bezwładności, której kierunek wyznaczony jest przez iloczyn wektorowy jego prędkości liniowej i obrotowej. Wartość siły jest proporcjonalna do masy poruszającego się ciała oraz iloczynu wektorowego wspomnianych prędkości. W przepływomierzu Coriolisa ruch obrotowy zastąpiono oscylacyjnym (drganiami) rury pomiarowej. Występujące w układzie bezwładności powodują opóźnienie fazy drgań rury w części dolotowej oraz jej przyspieszenie na odcinku wylotowym. Układ elektroniczny dokonuje pomiaru przesunięcia fazowego i na tej podstawie określa wartość strumienia masy. Ponadto pomiar częstotliwości rezonansowej drgań rur pomiarowych umożliwia bezpośrednie wyznaczenie gęstości produktu. Wadą tego typu przepływomierza jest skomplikowana kalibracja oraz konieczność napełniania całej rury przepływomierza medium. Do zalet należy możliwość pomiaru cieczy, gazów i materiałów, bezpośredni pomiar strumienia masy, gęstości, lepkości, temperatury, jak również wielkości pochodnych jak stężenia, zawartości innej substancji, objętości, a także bardzo wysoka dokładność pomiaru sięgająca ±0,05% i jego powtarzalność.
Kolejną grupę stanowią przepływomierze Vortex, zwane przepływomierzami wirowymi. Ich zasada działania wykorzystuje teorię ścieżki Karmana. Zgodnie z tą teorią po umieszczeniu w strudze płynu elementu o nieopływowym kształcie za tym elementem będą powstawały naprzemienne wiry. Wiry te są proporcjonalne do natężenia przepływu medium. Częstotliwość występowania wirów jest powiązana bezpośrednio z prędkością mierzonego medium i średnicą czujnika. Dzięki temu możliwe jest znalezienie wartości chwilowego przepływu na podstawie częstości występowania wirów. Piezoelektryczny element znajdujący się w czujniku wykrywa zmianę ciśnienia wywołaną przez wir i przesyła informację do przetwornika, gdzie częstotliwość występowania wirów przeliczana jest na prędkość przepływu mierzonego medium.
Pomiary poziomu
Ostatnią wymienioną wcześniej wielkością fizyczną jest poziom, którego pomiar jest wymagany w wielu systemach przemysłowych. Pomiary te pozwalają monitorować zarówno poziom cieczy, jak i materiałów sypkich w różnego rodzaju zbiornikach i silosach, jak również bezpośrednio w systemach podawczych i transportowych.
W pomiarach poziomu wykorzystuje się dwa typy czujników: kontaktowe i bezkontaktowe. Najprostszą metodą jest kontaktowa metoda mechaniczna realizowana za pomocą pływaka i ciężarka na lince. Jednak ze względu na dużą niedokładność metoda ta stosowana jest coraz rzadziej – zastępują ją metody hydrostatyczne, ultradźwiękowe i laserowe, a także elektryczne.
Hydrostatyczny pomiar poziomu bazuje na sprawdzaniu ciśnienia wytwarzanego przez słup cieczy, którą napełniany jest zbiornik. Dokładność pomiaru zależy wprost od dokładności wykorzystanego manometru. W przypadku pomiarów poziomu za pomocą lasera lub ultradźwięków czujniki umieszczane są nad mierzonym medium, a ich kontakt z medium jest możliwy tylko w przypadkach awaryjnych. Pomiar odległości odbywa się na zasadzie znalezienia różnicy fazy fali dźwiękowej lub świetlnej i na tej podstawie wyznaczana jest wysokość. Wadą obu metod pomiarowych jest możliwość błędnych wskazań w przypadku materiałów sypkich. Wynika to z tego, że granica między stanem gazowym a sypkim materiałem nie stanowi powierzchni płaskiej, a więc pomiar będzie uzależniony od umiejscowienia czujnika.
W przypadku elektrycznych metod pomiaru poziomu wykorzystuje się przede wszystkim metody rezystancyjną i pojemnościową. Pierwsza z nich bazuje na wskazaniach sondy w postaci metalowego pręta. Przez pręt ten płynie prąd, a jego wielkość zależy od miejsca, do którego odsłonięty jest pręt, czyli od wysokości, do jakiej dochodzi medium w zbiorniku. Druga metoda polega na badaniu zmiany pojemności między sondą pomiarową a ścianką zbiornika.
source: Automatyka 7-8/2020