Optymalizacja procesu produkcji – zastosowanie technologii RFID
Materiał prasowy (Balluff Sp. z o.o.) print
Technologia RFID (identyfikacja za pomocą fal radiowych) coraz powszechniej wykorzystywana jest w przemyśle. Swoją popularność zawdzięcza szerokim możliwością zastosowania oraz eliminacji ograniczeń, jakie niesie za sobą zastosowanie kodów kreskowych. Ciekawym przykładem jej wykorzystania jest aplikacja zrealizowana przez firmę Ferag AG na jednej z linii produkcyjnych.
System Skyfall jest innowacyjnym rozwiązaniem przenośników w obszarze logistyki wewnątrzzakładowej, o wydajności 12 000 wkładów na godzinę. Sercem podwieszanego rozwiązania jest system wytrzymałych szyn o trójwymiarowej kinematyce oraz korpusów rolkowych zwanych kapsułami. Służą one do przenoszenia wkładów z silikonem. Niezawodne oznaczenie każdej kapsuły ma kluczowe znaczenie dla procesu i właśnie z tego powodu firma Ferag podjęła decyzję o zastosowaniu metody identyfikacji w oparciu o technologię RFID. – System działa niezawodnie nawet w przypadku zanieczyszczenia nośników danych silikonem – podkreśla Rolf Werner, inżynier ds. sprzedaży w firmie Balluff.
Niezawodna identyfikacja przy dużej częstotliwości cyklu roboczego
Przemysłowy system RFID BIS M dostarczany przez specjalistę w dziedzinie czujników i technologii RFID, firmę Balluff, pracuje z częstotliwością 13,56 MHz. – System nie tylko spełnia trudne wymagania dotyczące częstotliwości cyklu roboczego i wytrzymałości, lecz jest również niezawodny w trudnym otoczeniu elementów metalowych – wyjaśnia Rolf Werner, omawiając funkcje systemu. W połączeniu z pasywnymi nośnikami danych to rozwiązanie HF zapewnia średni zasięg wynoszący 20 mm. Tym samym możliwe jest niezakłócone dokumentowanie całego procesu oraz automatyzacja przepływu materiału w czasie rzeczywistym.
Samoprzylepne, płaskie tagi RFID, przyklejone do powierzchni metalowych pozwalają na pełną identyfikację kapsuł. Spełniają one wymogi międzynarodowej normy ISO 15693 i zapewniają pewność odczytu z odległości 10 mm, nawet w otoczeniu metalowych elementów co było jednym z kluczowych wymogów firmy Ferag.
Tagi odczytywane są przez głowice RFID, które rozmieszczono wzdłuż całej ścieżki przesyłowej. Nośniki danych działają w sposób pasywny, pobierając niezbędne zasilanie z głowic do odczytu/zapisu. Eliminuje to konieczność stosowania dodatkowego źródła zasilania. Nośnik RFID wyposażony jest w antenę i mikrochip.
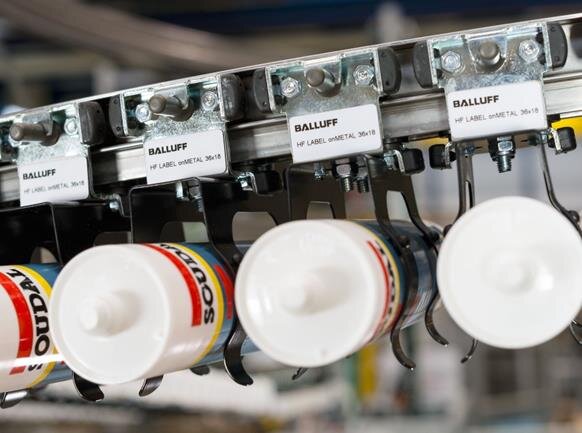
Płaskie, samoprzylepne znaczniki RFID, przyklejone do powierzchni metalowych umożliwiają identyfikację kapsuł
Znalezienie odpowiedniego rozwiązania
Cała sztuka polega na wybraniu odpowiedniego systemu i optymalnego połączenia nośnika RFID, głowicy do odczytu i procesora. W procesie wyboru rozwiązania uzyskaliśmy wsparcie eksperckie ze szwajcarskiego oddziału firmy Balluff.
– Rozmiar nośnika danych i geometria głowicy do odczytu/zapisu odgrywają istotną rolę – wyjaśnia Willi Brändli. – Pole HF generowane przez rozwiązanie musi być odpowiednio duże, aby znacznik przebywał w nim wystarczająco długo, umożliwiając odczytanie danych identyfikacyjnych nawet przy dużej prędkości”. Jednak jednocześnie musi być odpowiednio małe, aby nie nachodziło na pole kolejnej etykiety w procesie wykrywania. Wymaga to dużego doświadczenia.
Roberto Fenile kontynuuje – Początkowo sprawdzaliśmy rozwiązanie innego dostawcy systemów opartych na technologii RFID, jednak nie sprawdziło się ono przy tak złożonych wymaganiach. Następnie porównaliśmy systemy od różnych producentów i ostatecznie zdecydowaliśmy się na rozwiązanie Balluff, ponieważ jako twórca i producent firma ta doskonale zna możliwości swoich produktów, a jednocześnie nie cofa się przed tworzeniem niestandardowych wariantów dostosowanych do potrzeb klientów.
BIS V - nowe możliwości
Sercem układu jest procesor BIS V, który umożliwia podłączenie nawet czterech głowic do odczytu/zapisu, niezależnie od technologii, w której pracują (LF, HF i UHF). W połączeniu z głowicami RFID zapewnia on wymaganą przez użytkownika wysoką prędkość odczytu. Dzięki zastosowaniu czterech portów zmniejszono liczbę wymaganych procesorów, co zapewniło firmie Ferag znaczne oszczędności.
Uruchomienie systemu RFID i obsługa procesora jest dziecinnie prosta dzięki funkcji Plug-and-Play, a urządzenia peryferyjne podłączane są za pomocą standardowego złącza M12. Pełna diagnostyka, dostępność różnych systemów magistrali sieciowej (Profibus, EtherCAT, CC-Link, Ethernet/IP i Profinet) oraz różne częstotliwości pracy gwarantują możliwość wykorzystania procesora w każdym przypadku, niezależnie od lokalizacji.
Wielofunkcyjny, „inteligentny” procesor oferuje jednak jeszcze więcej. Do procesora RFID można podłączyć dodatkowe czujniki lub urządzenia wykonawcze dzięki wbudowanemu Masterowi IO-Link. Terminal USB, w który wyposażony jest procesor pełni funkcję interfejsu serwisowego przeznaczonego do aktualizowania oprogramowania i szybkiego uruchamiania bez konieczności korzystania ze sterownika PLC.
source: Balluff