Systemy sterowania – falowniki i serwonapędy
Marcin Bieńkowski print
Zagadnienia związane z rozruchem i sterowaniem prędkością obrotową asynchronicznych silników elektrycznych to jedna z najważniejszych kwestii dotyczących sterowania napędami w systemach automatyki przemysłowej. W praktyce, bezpośredni rozruch silnika za pomocą napięcia znamionowego stosuje się wyłącznie w wypadku silników małej mocy. W przypadku silników o większych mocach najczęściej wykorzystywanymi metodami rozruchu są: rozruch przez zmianę napięcia zasilania stojana, rozruch przez włączenie dodatkowej rezystancji w obwód stojana lub wirnika oraz rozruch przez zmianę częstotliwości napięcia zasilającego. Ta ostatnia metoda pozwala również na płynną regulację prędkości obrotowej podczas pracy, dlatego jest tak chętnie wykorzystywana.
Urządzeniem stosowanym do sterowania silnikiem, które umożliwia zmianę częstotliwości napięcia zasilającego jest falownik. I w tym miejscu należy od razu wyjaśnić kilka nieporozumień dotyczących nazewnictwa. Falownik czyli inwerter (od ang. power inverter) lub przetwornik mocy DC/AC służy do zamiany zasilającego go prądu stałego na prąd przemienny o regulowanej częstotliwości napięcia wyjściowego. Jeśli w falowniku dodatkowo zaimplementuje się mechanizm modulacji szerokości impulsów PWM (Pulse Width Modulation), to jednocześnie ze zmianą częstotliwości można swobodnie regulować również wartość skuteczną napięcia wyjściowego, co jest istotne w wielu systemach sterowania.
Używane zamiennie z falownikiem, nawet przez bardzo doświadczonych inżynierów, pojęcie konwertera lub przemiennika częstotliwości dotyczy zaś zespołu układów, których współpraca zamienia prąd zmienny o stałej częstotliwości, np. z sieci energetycznej, na prąd zmienny, którego częstotliwość i, jeśli zachodzi taka potrzeba, napięcie skuteczne możemy swobodnie regulować. Na przemiennik częstotliwości składają się zatem takie elementy jak:
- Prostownik, który podłączony jest do źródła prądu zmiennego zasilającego przemiennik częstotliwości. Odpowiada on za dostarczanie napięcia stałego niezbędnego do dalszej pracy całego urządzenia. Prostownik zasilany jest z jednej lub trzech faz napięcia przemiennego, a na wyjściu prostownika generowane jest stałe napięcie pulsacyjne. Prostowniki znajdujące się w przetwornikach częstotliwości mogą być niesterowalne (4, 6, 12, 18 i 24-pulsowe) oraz sterowalne, zbudowane w oparciu o układ tyrystorów lub połowicznie sterowalne, tyrystorowo-diodowe;
- Układ pośredni, którego zadaniem jest wygładzenie wyprostowanego napięcia i dostarczenie go do falownika – rozróżniamy trzy rodzaje stopni pośrednich: zamieniający napięcie wyprostowane na prąd stały, stabilizujący i wygładzający pulsujące napięcie stałe (odfiltrowuje składową przemienną z napięcia wyprostowanego), zamieniający stałe napięcie na napięcie stałe o regulowanej wartości. W stopniu pośrednim znajdują się także kondensatory lub bloki kondensatorów elektrolitycznych, w których magazynowana jest energia prądu stałego;
- Falownik, który – zgodnie z tym co napisano wcześniej – zamienia napięcie stałe w napięcie zmienne o regulowanej częstotliwości i wartości skutecznej. Warto wspomnieć, że właśnie wprost do modułu falownikowego podłączony jest silnik;
- Układ sterowania, umożliwiający regulowanie i ustawienie przez użytkownika żądanej wartości napięcia i częstotliwości. W zależności od sposobu sterowania, niektóre przemienniki mogą obsługiwać kilka zewnętrznych urządzeń jednocześnie;
- Układ zabezpieczeń, chroniący zarówno przemiennik częstotliwości, jak urządzenia podłączone do niego przed przeciążeniami, skokami napięcia, przebiciami itp.
Mimo to w systemach automatyki oraz w cennikach i dokumentacji technicznej wielu firm, przemienniki częstotliwości potocznie, cały czas nazywane są falownikami. Dlatego też, mimo że falownik formalnie jest elementem składowym konwertera częstotliwości, w niniejszym artykule będziemy posługiwali się tymi nazwami zamiennie. W tym miejscu warto też wspomnieć, że skutkiem stawiania znaku równości między falownikiem oraz przemiennikiem częstotliwości jest powstanie określenia „falownik do silnika”. Wzięło się to stąd, że falowniki wykorzystywane są w wielu systemach automatyki przemysłowej, wszędzie tam gdzie trzeba zamienić prąd stały na zmienny, zaś konwertery częstotliwości w praktyce wykorzystywane są niemal wyłącznie do sterowania prędkością obrotową i rozruchem silników asynchronicznych.
Jak działa falownik
Wyjaśniając różnicę w terminologii między falownikiem a przetwornikiem częstotliwości, omówiliśmy we wstępie już schemat blokowy i sposób działania konwertera częstotliwości – jest on taki sam (rys. 1.) dla każdego urządzenia dostępnego na rynku, niezależnie od nazwy serii, typu czy producenta. Zajmijmy się teraz samym falownikiem. Głównym elementem każdego falownika jest tranzystorowy układ mostkowy, tzw. mostek kluczy. To tu dokonuje się zamiana prądu stałego na sinusoidalny.
Generowanie prądu sinusoidalnego realizowane jest za pomocą odpowiedniego, sekwencyjnego przełączania tranzystorów mocy sterowanych przez obwód kontroli i regulacji. Początkowo do generowania napięcia sinusoidalnego stosowano przekaźniki, później były to tyrystory, obecnie ze względu na szybszy czas przełączania, zastąpiono je tranzystorami IGBT czyli tranzystorami bipolarnymi z izolowaną bramką.
Praca elementów półprzewodnikowa jest dwustanowa, stąd określenie „klucz tranzystorowy”, a częstotliwość ich przełączania może dochodzić nawet do wartości 100‒200 kHz. Tranzystory IGBT przełączane są za pomocą wspomnianych sygnałów sterowania, które generowane mogą być przy wykorzystaniu różnych algorytmów i metod. Współcześnie stosuje się trzy sprawdzone w warunkach przemysłowych i proste w implementacji metody sterowania – metodę bezpośrednią przez wejściowy, referencyjny sygnał sterujący, metodę wykorzystująca regulowane napięcie stałe obwodu pośredniego, które jest proporcjonalne do wejściowego sygnału sterującego oraz najczęściej obecnie stosowaną metodę modulacji szerokości impulsów PWM.
Ta ostatnia metoda polega na określeniu przez obwód sterowania czasu trwania okresów załączania i wyłączania odpowiednich par tranzystorów znajdujących się w poszczególnych gałęziach mostka. W metodzie PWM stałe napięcie pochodzące z obwodu pośredniego przetwornicy przełączane jest przez dwustanowe elementy mocy falownika, czyli tranzystory IGBT. Trzy gałęzie falownika, z dwoma tranzystorami przypadającymi na gałąź, generują łącznie osiem możliwych kombinacji otwarcia/zamknięcia zaworów (wyjść) półprzewodnikowych. W ten sposób powstaje osiem różnych wektorów napięcia na wyjściach falownika, co odpowiada krótkim impulsom napięcia na wyjściu o różnej szerokości (czasie trwania), dają w ten sposób żądany sygnał wyjściowy uśredniany w czasie. Jak widać, impulsowe napięcie może posłużyć do modulacji dowolnego kształtu sygnału, w tym wypadku krzywej sinusoidalnej.
Pozostałe wektory pośrednie, potrzebne do wygładzenia sygnału tak, aby charakteryzował się na wyjściu jak najmniejszą liczbą „dziur” w paśmie, oraz wektory potrzebne do szybkich zmian modulacji sygnału wyjściowego, otrzymuje się sumując, przez ściśle określony czas, wybrane wektory główne. Szerokość impulsów napięcia między kolejnymi załączeniami i wyłączeniami zaworów półprzewodnikowych falownika określa amplitudę generowanego napięcia przemiennego, a w zależności od częstotliwości kluczowania (załączania) zaworów półprzewodnikowych, na wyjściu falownika pojawia się sinusoida o mniej lub bardziej łagodnym kształcie. Zastosowanie na wyjściu falowników cewki indukcyjnej pozwala na wygładzenie sygnału wyjściowego w formie uzyskanych, w opisany wyżej sposób krótkich impulsów tworzących quasi sinusoidę, do postaci czystego, sinusoidalnego przebiegu napięcia prądu przemiennego.
Odmianą metody sterowania z wykorzystaniem modulacji PWM, jest modulacja PWM z sinusoidalnym przebiegiem nośnym. W metodzie tej używa się sinusoidalnego napięcia odniesienia, tzw. napięcia modulującego dla każdego wyjścia mocy falownika. Okres sinusoidalnego napięcia odniesienia odpowiada za okres podstawowej harmonicznej sinusoidalnego napięcia wyjściowego falownika. Czasy przełączania elementów półprzewodnikowych (zaworów) falownika są określane względem punktów przecięcia przebiegów sinusoid napięć odniesienia i przebiegu trójkątnego napięcia modulowanego (rys. 2).
Oczywiście użytkownik ma możliwość ustawienia odpowiedniej częstotliwości nośnej, dostosowanej do parametrów zasilanego silnika. Należy jednak pamiętać, że ustawianie za wysokiej częstotliwości nośnej na tranzystorach IGBT może spowodować zbyt duże ilości ciepła, co wiąże się nie tylko z problemami związanymi z jego odprowadzaniem, ale również stratami mocy na przetwornicy częstotliwości, a gdy częstotliwość nośna jest zbyt niska, silnik zaczyna hałasować. Dlatego tak istotny jest dobór konwertora częstotliwości do używanego w danej aplikacji silnika.
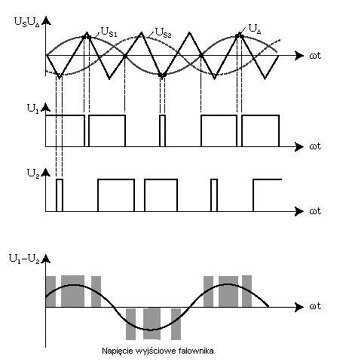
Rys. 2. Sposób kształtowania napięcia wyjściowego trójfazowego falownika PWM z sinusoidalnym przebiegiem nośnym (dwa napięcia odniesienia – jedno napięcie międzyfazowe) źródło: www.falowniki24.info.pl
Metody sterowania – falownik skalarny i wektorowy
Sterowanie skalarne, nazywane też sterowaniem U/f, co należy wymawiać jako U do f, jest najprostszym trybem sterowania silnikiem elektrycznym za pomocą falownika. Metoda ta wykorzystywana jest od lat siedemdziesiątych ubiegłego wieku, a falowniki skalarne są stosunkowo tanie. Tryb skalarny bazuje na stałym stosunku napięcia do częstotliwości. Nie zagłębiając się w teorię, stały stosunek napięcia do częstotliwości zapewnia wytworzenie znamionowego strumienia magnetycznego w silniku, a co za tym idzie, pozwala uzyskać maksymalny moment obrotowy pracy silnika elektrycznego.
Algorytmy sterowania skalarnego dobiera się bazując na zależnościach dotyczących stanu ustalonego. Najbardziej rozpowszechnione są układy sterowania skalarnego, w których stabilizacja strumienia uzyskiwana jest na podstawie charakterystyk liniowych u/f = const lub kwadratowych U/f² = const. Nastawiane są tylko amplitudy i prędkości kątowe (częstotliwości) wektorów przestrzennych napięć, prądów i strumieni skojarzonych silnika.
Falowniki ze sterowaniem skalarnym stosowane są w prostych aplikacjach, gdzie nie jest wymagana dokładna regulacja prędkości obrotowej oraz nie ma tzw. „ciężkiego rozruchu”, czyli tam gdzie obciążenie charakteryzuje się niewielką bezwładnością. Tego typu falowniki wykorzystuje się głównie w urządzeniach takich, jak wentylatory, pompy (charakterystyka kwadratowa) lub taśmociągach bądź też przenośnikach (charakterystyka liniowa), a więc wszędzie tam gdzie mamy do czynienia z obciążeniem zmiennomomentowym.
Istotny dla tych zastosowań jest fakt, że sterowanie skalarne idealnie nadają się do aplikacji wielosilnikowych, a więc wszędzie tam, gdzie do jednego przemiennika podłącza się kilka silników elektrycznych. Niestety sterowanie skalarne ma też swoje wady. Przy niskich częstotliwościach moment jest bardzo niski, a przez to jest zbyt mały, aby poruszyć wał silnika, który obciążony jest elementem, o wspomnianej dużej bezwładności.
Gdy występuje potrzeba operowania obciążeniami stałomomentowymi lub mamy do czynienia z dużymi siłami inercyjnymi, które wymagają dużego momentu rozruchowego, korzysta się z przemienników częstotliwości ze sterowaniem wektorowym, czyli modulacją PWM ze sterowaniem wektora napięcia. Sterowanie wektorowe jest bardziej skomplikowane i oddzielnie steruje się tu momentem i strumieniem uzwojenia. Przemiennik ze sterowaniem wektorowym jest w stanie bez problemu utrzymywać stałą wartość momentu obrotowego silnika w całym zakresie regulacji prędkości obrotowej, już od częstotliwości zasilania 0,5 Hz. Niestety w tym przypadku przemiennik może sterować tylko jednym silnikiem naraz.
Sterowanie wektorowe charakteryzuje się tym, że na podstawie zależności obowiązujących dla stanów nieustalonych i przejściowych nastawiane są nie tylko amplitudy i prędkości kątowe (częstotliwości), ale również fazy wektorów przestrzennych napięć, prądów i strumieni skojarzonych silnika. Układ sterowania oddziałuje więc na wzajemne położenie wektorów, zapewniając ich prawidłową orientację. W sterowaniu wektorowym moment i strumień określone są przez prąd stojana i nie mogą być nastawiane w sposób niezależny. Zależnie od sposobu wyznaczania kąta położenia wektora pola rozróżniamy dwa sposoby sterowania – bezpośredni oraz pośredni.
Falowniki wektorowe dzielą się dodatkowo na bezczujnikowe i ze sprzężeniem zwrotnym. Różnica występuje w metodzie wyznaczania prędkości obrotowej wirnika silnika. Dla falowników bezczujnikowych, prędkość obrotowa obliczana jest na podstawie modelu matematycznego silnika. W przypadku falowników ze sprzężeniem zwrotnym, pomiar aktualnej wartości prędkości odbywa się za pomocą enkodera inkrementalnego, który zamontowany jest na wale silnika.
Niezależnie od sposobu pracy, każdy przemiennik pracujący w trybie wektorowym wymaga dokładnego wprowadzenia parametrów silnika oraz wykonania autokonfiguracji. Dzięki temu falownik wykona pomiary pozostałych wartości elektrycznych, których nie ma na tabliczce znamionowej silnika, co z kolei pozwoli podczas pracy utrzymać stałą wartość momentu obrotowego. Co ważne, każdy przemiennik ze sterowaniem wektorowym może pracować również w trybie skalarnym i to zazwyczaj jest domyślnie ustawiony tryb sterowania.
Metoda DTC – bezpośrednie sterowanie momentem
Metoda bezpośredniego sterowania momentem DTC (Direct Torque Control) jest niezwykle zaawansowaną metodą sterowania silnikiem indukcyjnym. Metoda DTC zakłada sterowanie momentem oraz strumieniem skojarzonym stojana silnika w sposób bezpośredni, a nie za pomocą kontroli prądu stojana. Pozwala ona uzyskać bardzo precyzyjną kontrole nad układem napędowym. W wypadku sterowania DTC wyznacza się odpowiedni sposób generacji sygnałów sterujących przełączaniem poszczególnych tranzystorów w falowniku w zależności od aktualnego stanu elektromagnetycznego silnika. W procesie sterowania nie jest też niezbędny pomiar położenia wału silnika, co jest jedną z podstawowych zalet tej metody.
Aby skorzystać z tej metody sterowania, należy w pierwszej kolejności podać wszelkie dane znamionowe silnika, takie jak: prąd, napięcie, moc, liczba obrotów, liczba biegunów, poślizg, współczynnik mocy. Następnie przetwornik częstotliwości wykonuje operacje tzw. autotuningu silnika, czyli estymuje, wylicza pozostałe dane silnika, w tym rezystancję i induktację uzwojeń, stałą czasową rotora itp. w sposób automatyczny w stanach z i bez rotacji silnika. Przy sterowaniu wektorowym, przetwornik częstotliwości korzysta z modelu matematycznego silnika, zaimplementowanego w procesorze sygnałowym. Dlatego tak ważne jest, aby zapisywać w falowniku wszelkie dane silnika, im ich więcej i są dokładniejsze tym lepsza kontrola nad silnikiem, a także i okresowo przeprowadzać operację autotuningu, gdyż parametry silnika zmieniają się wraz z upływem czasu.
Falowniki zasilane jedno- i trójfazowo
Oprócz wymienionego wyżej podziału, ze względu na sterowanie, wyróżnia się przemienniki częstotliwości zasilane jednofazowo i trójfazowo. Falownik zasilany jednofazowy zasilany jest na wejściu z jednej fazy napięcia przemiennego 230 V AC, natomiast na wyjściu, w zależności od potrzeb, o czym za chwilę, może mieć zarówno jedną, jak i trzy fazy o napięciu międzyfazowym 230 V. Tego typu przemienniki stosowane są w aplikacjach wykorzystujących małe silniki do 2,2 kW, o napięciu znamionowym 230 V. Bardzo ważne jest rozróżnienie przemienników do silników jednofazowych od przemienników zasilanych jednofazowo. Przemienniki do silników jednofazowych na wyjściu mają jedną fazę, natomiast przemienniki zasilane jednofazowo, trzy fazy.
Z kolei falowniki zasilane trójfazowo zasilane są z trzech faz 3 × 400 V AC, a na wyjściu falownika mają trzy fazy o napięciu międzyfazowym 400 V. Przemienniki częstotliwości do silników trójfazowych mają możliwość pracy w większych aplikacjach, gdzie wymagany zakres mocy wyjściowej może dochodzić nawet do 500 kW. Falowniki do silników trójfazowych są znacznie częściej wykorzystywane, co wynika z większego rozpowszechnienia silników trójfazowych w zastosowaniach przemysłowych.
Nie tylko prędkość obrotowa – regulacja PID, sterownik PLC
Oprócz podstawowej funkcjonalności związanej z regulacją prędkości obrotowej, dostępne w sprzedaży falowniki silnika falowniki dysponują możliwościami poprawy i automatyzacji pracy napędu. Przede wszystkim chodzi tu o możliwość płynnego rozbiegu i hamowania silnika. Z jednej strony ogranicza to związane z rozruchem udary prądowe, a z drugiej eliminuje hałas związany z wprawieniem w ruch napędzanego urządzenia. We współczesnych przemiennikach częstotliwości istotną rolę odgrywają również układy zabezpieczające pracę silnika. Dzięki nim można wyeliminować dodatkowe układy zabezpieczające. Z funkcji aplikacyjnych warto wspomnieć o wbudowanych w falownik regulatory PID. Tryb regulacji PID, to tryb regulacji ze sprzężeniem zwrotnym. Falownik dąży do zmniejszenia różnicy między wartością zadaną, nastawioną w falowniku, a wartością zwrotną otrzymywaną z czujników zainstalowanych na wysterowywanym urządzeniu. Może być to na przykład ciśnienie w układzie jego regulacji, czy poziom cieczy w zbiorniku wyrównawczym.
Jedną z charakterystycznych cech nowoczesnych falowników jest zintegrowanie ich z kontrolerem PLC. Dzięki temu możliwe jest zaprogramowanie sekwencji zadań realizowanych automatycznie przez falownik. Taki zaawansowany kontroler ruchu pozwala uruchomiać w dowolnej chwili silnik w zadanym kierunku, w zależności od realizowanego zadania, sterować jego działaniem lub czasem pracy w zależności od programu czy danych pochodzących z zewnętrznych czujników, bądź informacji spływających z elementów systemu automatyki. Oczywiście można też dowolnie zmieniać prędkość obrotową czy ustalać czas przyspieszania i hamowania itp.
Obecnie produkowane mikroprocesorowo sterowane falowniki wyposażone są w rozbudowane mechanizmy autodiagnostyki. Systemy diagnostyczne sprawdzają prawidłową pracę podzespołów falownika, nadzorują w czasie rzeczywistym parametry pracy linii zasilających, konwertera, inwertera, hamulca, obciążenia itp. po to, aby zapewnić bezpieczeństwo urządzeniom i przebywającym w obszarze ich pracy ludziom. W przypadku wadliwej pracy falownika bardzo często na panelu operatorskim przetwornika częstotliwości zgłaszany jest kod błędu, który informuje o możliwych przyczynach usterki.
Jaki falownik wybrać?
Poszukując właściwego falownika do aplikacji należy zwrócić uwagę na kilka zasadniczych kwestii, a przede wszystkim na typ wysterowywanego silnika. Spotykane w automatyce silniki prądu przemiennego mogą występować zarówno w wersji jednofazowej, są to głównie napędy małej mocy, np. w zainstalowanych na linii produkcyjnej elektronarzędziach, wentylatorach, pompach oraz w wersji trójfazowej. W sprzedaży dostępne są zarówno falowniki przeznaczone dla silników jednofazowych, jak i dla silników trójfazowych. W wypadku sterowania silnikami jednofazowymi warto zwrócić uwagę na wyprowadzenia połączeń silnika, gdyż falowniki takie można stosować wyłącznie do silników, które mają wyprowadzone w puszce montażowej końce obu uzwojeń i kondensator rozruchowy.
Oczywiście przetworniki częstotliwości występują zarówno w wersji zasilanej napięciem jedno-, jak i trójfazowym 400 V. Pierwsze z tych rozwiązań dostępne jest zazwyczaj tylko dla niewielkich mocy silnika do kilku kW, a na wyjściu takich falowników, o czym wspomniano wcześniej, pojawia się napięcie o wartości 3 × 230 V. W praktyce oznacza to konieczność zastosowania silnika o takim właśnie napięciu zasilania lub dla typowego silnika 230/400 V – przełączenie uzwojeń na układ typu „gwiazda”, o czym koniecznie należy pamiętać.
Istotne jest też to, aby oszacować moc, jaka będzie potrzebna do zasilania wysterowanego silnika. W tym celu najlepiej posłużyć się danymi technicznymi z tabliczki znamionowej i na tej podstawie dobrać falownik, który gwarantuje dostarczenie odpowiedniej wartości mocy i prądu. Warto zaznaczyć, że prąd jest jednym z istotniejszym z parametrów, na które należy zwrócić uwagę, zwłaszcza przy doborze falownika ze sterowaniem wektorowym. Jeśli silnik pracuje w trudnych warunkach, np. częste i ciężkie rozruchy, to warto rozważyć co najmniej 40% przewymiarowanie falownika, np. w miejsce falownika 4 kW zastosować falownik, który jest w stanie dostarczyć 5,5 kW mocy.
Oszczędzanie energii
Jednym ze sposobów zwiększenia energooszczędności napędów z silnikami prądu przemiennego jest stosowanie odpowiednio dobranych falowników, które dzięki wykorzystaniu ramp prędkości rozruchu i hamowania w znacznym stopniu zwiększają żywotność układów napędowych. Możliwe staje się wówczas uruchamianie napędów jedynie wtedy, kiedy jest to konieczne oraz dynamiczne dopasowanie prędkości do aktualnego zapotrzebowania.
Niektóre typy konwerterów częstotliwości, zwłaszcza te ze sterowaniem wektorowym, umożliwiają optymalizację pobieranej energii. Możliwe jest wówczas sterowanie momentowe dla zmiennego obciążenia podczas pracy napędu maszyny czy linii automatyki oraz praca, o czym wspomniano wcześniej, przy bardzo niskich prędkościach. Na rynku dostępne są modele przekształtników częstotliwości, które umożliwiają nie tylko oszczędne gospodarowanie energią, ale również jej odzysk – są to tzw. napędy regeneracyjne. Falowniki tego typu mają dodatkowy moduł odpowiedzialny za funkcję odzyskiwania energii. Podczas hamowania silnika odzyskana energia oddawana jest do sieci energetycznej, a nie, jak ma to miejsce w większości przypadków, zamieniana na ciepło przez rezystory hamujące. Warto też zwrócić uwagę, że zastosowanie przemiennika częstotliwości i regulacja pracy silnika wydłuża okres eksploatacji urządzeń, a także pozwala na modyfikację „w locie” parametrów układu napędowego, bez konieczności jego kosztownej rekonfiguracji mechanicznej.
Serwonapędy
Na koniec warto kilka słów poświęcić serwonapędom nazywanych też serwomechanizmami. Serwonapęd to zintegrowany układ napędowy, traktowany jako jedna całość, składający się z silnika, sterownika, falownika oraz zestawu czujników monitorujących jego pracę, będącego de facto modułem sprzężeń zwrotnych. Najczęściej mamy do czynienia z enkoderem, resolverem lub tachometrem, pracującym w układzie zamkniętej pętli sprzężenia zwrotnego.
Innymi słowy, serwomechanizm to układ wykonawczy pracujący w zamkniętym układzie sterowania, w którym sygnałem wyjściowym jest jakiś parametr, np. położenie, przyspieszenie czy przesunięcie, a na wejściu precyzyjnie regulujemy interesujące nas parametry ruchu, takie jak pozycjonowanie osi wału silnika, kontrolę prędkości obrotowej i kontrolę momentu.
Warto podkreślić, że serwonapędy służą przede wszystkim do realizowania ruchów obrotowych lub rzadziej liniowych, we wszystkich aplikacjach przemysłowych, w których wymagane jest precyzyjne pozycjonowanie oraz w tych zastosowaniach napędowych, od których wymaga się precyzyjnego przemieszczania między różnymi położeniami, sterowania przy bardzo małych prędkościach lub wszędzie tam, gdzie występuje duża dynamika ruchu. Przy czym ruch obrotowy osi może być też bez problemu zamieniony na ruch liniowy, np. przez zastosowanie śruby pociągowej. Dzięki tego typu przekładniom w istotny sposób zwiększyć można możliwości zastosowania serwonapędów.
Serwonapędy charakteryzują się wysoką sprawnością, która jest stała w dużym zakresie obciążeń, mogą też osiągać duże przyspieszenie kątowe wirnika. Cechują się również dobrymi właściwościami dynamicznymi i regulacyjnymi. Istotnym elementem serwonapędu jest sterownik serwo, nazywany też sterownikiem ruchu, który pozwala na uzyskanie wymaganego efektu, np. odpowiedniego pozycjonowania, liczby obrotów czy prędkości.
Do sterowania silnikami elektrycznymi stosuje się sterowniki analogowe lub cyfrowe. Te ostatnie budowane są na bazie mikroprocesorów lub procesorów sygnałowych DSP i niemal całkowicie wyparły sterowniki analogowe ze względu nie tylko na łatwą kontrolę stanu pozwalającą na bezpośrednie zadawanie i zmianę parametrów układu czy łatwość zapamiętania nawet kilkuset położeń, ale również ze względu na możliwość globalnej komunikacji z pozostałymi elementami systemu automatyki i infrastruktury IT funkcjonującej na linii produkcyjnej. Systemy cyfrowe cechują się też znacznie większą uniwersalnością.
Silniki w serwonapędach
W serwonapędach stosuje się zwykle bezszczotkowe silniki synchroniczne prądu zmiennego z magnesami trwałymi na wirniku, z wbudowanym bezpośrednio w konstrukcję silnika enkoderem. Często stosuje się bezszczotkowe silniki prądu stałego, jednak we wszystkich aplikacjach wymagających precyzyjnego pozycjonowania, w serwonapędach wykorzystywane są silniki krokowe, gdzie impulsowe zasilanie sprawia, że wirnik nie obraca się ruchem ciągłym, lecz wykonuje za każdym razem ruch obrotowy o ściśle ustalonym kącie. Dzięki temu kąt obrotu wirnika jest ściśle zależny od liczby dostarczonych impulsów prądowych, a prędkość kątowa wirnika jest dokładnie równa częstotliwości impulsów pomnożonej przez wartość kąta obrotu wirnika w jednym cyklu pracy silnika.
Jak widać silnikiem takim jest bardzo łatwo sterować, korzystając ze standardowego sterownika PLC. Co ważne, w typowych rozwiązaniach, kąt obrotu wirnika pod wpływem przełożenia pojedynczego impulsu waha się kilku do kilkudziesięciu stopni.
Sterowanie
W typowym, współczesnym systemie automatyki przemysłowej wykorzystującym serwonapędy do realizacji procesu ruchu odpowiada moduł serwonapędu, który bezpośrednio zasili i wprawi w ruch serwomechanizm lub serwomotor, bez jakiegokolwiek pośrednictwa falownika. Sygnałem dla serwonapędów lub kontrolera silników krokowych jest podanie napięcia sterującego lub ciągu impulsów o zadanej częstotliwości. W ten sposób realizowane jest wysterowanie osi lub wirnika.
Obecnie, sygnały wyjściowe doprowadzane są do elementów wykonawczych w sposób całkowicie cyfrowy. Może się to odbywać za pośrednictwem umieszczonego na obudowie sterownika wieloosiowego wyjść cyfrowych, albo za pośrednictwem magistrali typu Ethernet, Powerline, CAN, Profibus czy Profinet. Coraz częściej serwonapędy wyposażane są jedynie w złącza magistrali danych i próżno na nich szukać tradycyjnych sterujących złączy analogowych bądź cyfrowych.
Warto też podkreślić, że kontroler serwonapędu ma też do dyspozycji kilka złączy analogowych i cyfrowych służących do zbierania danych z enkodera. Obecnie coraz częściej dane takie trafiają bezpośrednio do elementu wykonawczego, a ten przesyła je magistralą systemową do sterownika. W wielu rozwiązaniach stosowane są złącza pozwalające realizować funkcje obsługi robotów. Charakteryzują się wyższymi częstotliwościami pracy. Na zakończenie warto zaznaczyć, że wiele sterowników serwonapędów można bez problemu rozbudować o moduły rozszerzeń z dodatkowymi wyjściami i wejściami oraz złączami magistral systemowych.
source: Automatyka 9/2020