Wszechstronność w branży browarniczej — skuteczna kontrola jakości dzięki czujnikom wizyjnym
Praktycznie w każdej branży producenci potrzebują uniwersalnych czujników, których wszechstronność umożliwiłaby łatwą i efektywną realizację zróżnicowanych zadań kontrolnych. Czujniki wizyjne BVS-E firmy Balluff, wyposażone w zintegrowane oświetlenie oraz w trzy wyjścia cyfrowe, wychodzą naprzeciw takim wymaganiom.
Czujniki BVS-E mogą w trakcie jednej inspekcji nie tylko weryfikować wiele charakterystycznych cech, ale jednocześnie wykonywać różne zadania, takie jak odczytywanie kodów, zliczanie krawędzi, porównywanie kontrastu, wzorców i położenia. Wszechstronność tych podzespołów przekonała osoby odpowiadające za sprawy techniczne w browarze Warsteiner. Czujniki były w browarze potrzebne po procesie napełniania, kiedy w ramach kompleksowej kontroli jakości weryfikowano obecność etykiet na beczkach, poprawność tekstu na etykietach butelek oraz jakość opakowań sześciopaków.
O browarze
Grupa Warsteiner zatrudnia 2,3 tys. pracowników. W 2012 r. osiągnięto wolumen sprzedaży równy 4,56 mln hektolitrów i dochód rzędu 530 mln euro, dzięki czemu firma stała się jednym z czołowych, prywatnych browarów w Niemczech. Zarządzane rodzinnie przedsiębiorstwo składa się obecnie ze 120 spółek, zlokalizowanych na całym świecie, a w jego portfolio jest kilka znanych marek, takich jak Herforder i Paderborner. Głównym podmiotem grupy jest firma Warsteiner Brauerei Haus Cramer, założona w 1753 r. w miejscowości Warstein w pobliżu Soest i produkująca piwo Warsteiner Premium Verum. Zakład zajmuje imponujący obszar, odpowiadający powierzchni około 66 boisk do piłki nożnej. To w tym miejscu każdego dnia organizuje się wysyłkę towarów do klientów. Realizacja zamówień wymaga użycia 4 tys. palet, które po załadunku transportuje się 200 ciężarówkami.
Sprawdzanie oznaczeń w szybkim procesie produkcyjnym
Na linii napełniającej butelki o pojemności 0,5 l stosuje się szybki laser do wypalania daty przydatności, godziny w danym dniu i kodu maszyny na etykietach, przymocowanych do tylnej strony butelek. Czujnik wizyjny służy do kontrolowania tych oznaczeń na każdej butelce. Inspekcja jest realizowana za pomocą tzw. funkcji zliczania krawędzi. W razie braku daty przydatności produkt nie może być przekazany do sprzedaży. Kamerę wyzwala czujnik fotoelektryczny. Wykrywa on pręty elementów centrujących, które prowadzą butelki przez system.
– Butelki przemieszczają się bardzo szybko. W ciągu godziny przez system przechodzi nawet 55 tysięcy butelek. Z tego wynika, że czujnik ma 25 milisekund na sprawdzenie butelki, przy prędkości 16 butelek na sekundę. Czujnik wizyjny BVS bez problemu radzi sobie z tym zadaniem. Zastosowaliśmy w tej aplikacji dodatkowy oświetlacz pierścieniowy, w niedużej obudowie serii VA, z soczewkami Fresnela. Dzięki temu moc zintegrowanego oświetlenia jest większa i bardziej skoncentrowana – wyjaśnia szczególne wyzwania, jakie występują w procesie produkcji, Andreas Zydek, który jako konsultant zarządzający firmy BHV Automation doradzał producentowi napojów w zakresie projektowania systemu.
Jeśli wykryty zostanie brak oznaczenia na etykiecie, czujnik generuje sygnał błędu. Zostaje on przekazany przez sterownik do rejestru przesuwnego. Gdy wadliwa butelka dotrze do popychacza, zostanie oddzielona od pozostałych butelek, przez zmianę kierunku i odrzucenie.
Aby spełnić specjalne wymagania browaru, czujnik i oświetlenie zostały dodatkowo zintegrowane w szczelnym korpusie instalacji V2A, ze szklanym panelem, który ułatwia czyszczenie systemu przy użyciu dużej ilości wody i detergentów.
Łatwa konfiguracja
Konfiguracja czujnika nie wymaga żadnej wiedzy z zakresu programowania ani skomplikowanego szkolenia. Wytrzymały, zaawansowany technicznie czujnik jest łatwy w obsłudze dzięki dołączonemu oprogramowaniu
ConVIS, o intuicyjnym interfejsie użytkownika.
– Po podłączeniu czujnika do laptopa z systemem Windows, poprzez zintegrowane złącze Ethernet, można zobaczyć bieżący obraz obszaru detekcji na monitorze. Musimy tylko wybrać potrzebne narzędzia i sekcje obrazu. Po wykonaniu tych prostych czynności czujnik jest gotowy do pracy – wyjaśnia Rainer Ifland, lider zespołu inżynierii elektrycznej w dziale konserwacji browaru Warsteiner.
Określenie prawidłowych wartości progowych dla każdego narzędzia jest łatwe: czerwone i zielone wskaźniki sygnalizują prawidłowe ustawienie jeszcze przed przełączeniem do trybu roboczego. Od tego momentu czujniki będą pracować w pełni autonomicznie — jako niezależne urządzenia. Szczególnie przydatną właściwością jest możliwość zapisania przez użytkownika, bezpośrednio w czujniku, do 20 konfiguracji.
Dotyczy to także drugiego modelu czujnika, BVS-E Ident, który został zaprojektowany specjalnie do odczytywania i detekcji kodów 1D (kody kreskowe) lub 2D (kody DataMatrix). Ten czujnik można stosować do detekcji standardowych kodów, a także jako niezawodne narzędzie do weryfikacji tekstów i sekwencji numerów.
Monitorowanie obecności za pomocą kodu DataMatrix
To rozwiązanie jest stosowane w browarze Warsteiner w systemach etykietowania 30- i 50-litrowych beczek wielokrotnego użytku, wykonanych ze stali nierdzewnej. W trakcie kompleksowej inspekcji następuje kontrola obecności etykiety na korku zamykającym, w górnej części beczki. Etykieta zawiera informacje w formie zwykłego tekstu na temat typu piwa, daty napełnienia i daty przydatności, a dodatkowo może też zawierać uzupełniające dane, takie jak numer serii i jej wielkość.
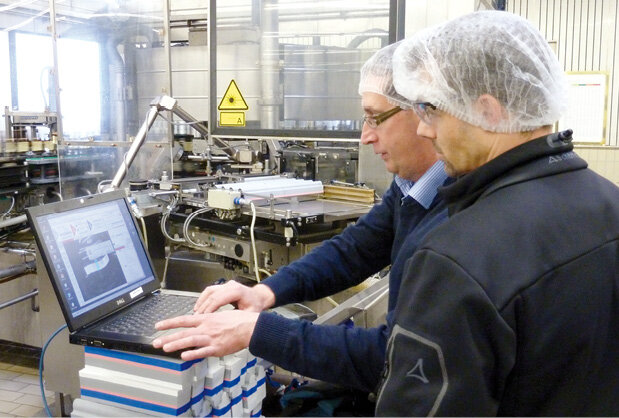
Konfiguracja czujnika za pomocą oprogramowania ConVIS trwa bardzo krótko, o czym przekonali się już Andreas Zydek z firmy BHV (z prawej) oraz Rainer Ifland z browaru Warsteiner
Warto mieć na uwadze, że to nie tekst jest odczytywany, a raczej dodatkowy kod 2D, wydrukowany na etykiecie. Dzięki temu możliwe jest uzyskanie szybkiego i dokładnego procesu detekcji. To bardzo ważne, ponieważ linia napełnia tysiąc beczek w ciągu godziny, w dwuzmianowym systemie pracy. Jeśli dane z odczytanego kodu są potrzebne w dalszym etapie produkcji (nie dotyczy to przedstawionego procesu), można je przesłać za pomocą interfejsu RS-232 lub Ethernet.
Proces detekcji w linii etykietującej można wyjaśnić w prosty sposób: przenośnik taśmowy transportuje beczki tak, aby były umieszczone na środku taśmy. Dlatego zabezpieczające korki na uszczelniającym zamknięciu beczki znajdują się zawsze w tej samej pozycji pod drukarką. Gdy czujnik wykryje obecność beczki, podajnik drukujący etykiety w odpowiednim czasie drukuje nową etykietę, która następnie jest mocowana do korka zabezpieczającego na beczce przez moduł pneumatyczny. Czujnik wizyjny zamontowany na ramie drukującej automatycznie dokonuje aktualizacji, jeśli wystąpi zmiana typu. Gdy moduł pneumatyczny powróci do położenia początkowego, następuje emisja sygnału. W odpowiedzi na sygnał czujnik najpierw informuje o swojej gotowości do pracy za pomocą sygnału „OK”, zapewniając w ten sposób efektywność kontroli linii produkcyjnej. Jeśli stwierdzono obecność etykiety, czujnik potwierdza ten fakt za pomocą drugiego sygnału „OK” na drugim wyjściu cyfrowym, po odczytaniu kodu DataMatrix. Beczki bez etykiet są bezzwłocznie odrzucane. Po inspekcji wizualnej są ponownie dostarczane do linii etykietującej.
Rozważane alternatywy
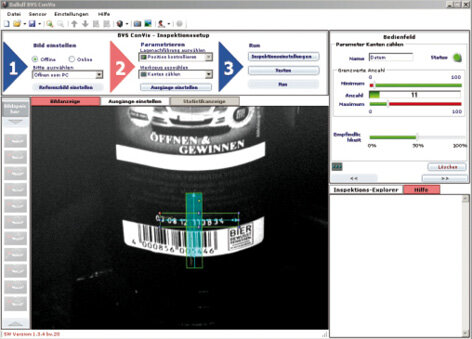
Aktualny obraz w obszarze detekcji, widziany na monitorze w interfejsie użytkownika oprogramowania ConVIS
– Oczywiście braliśmy pod uwagę inny proces, przykładowo z wykorzystaniem kodów kreskowych. Jednak wysoką jakość odczytu w tym środowisku można uzyskać tylko dzięki stosowaniu kodu DataMatrix, w połączeniu z procesem przetwarzania obrazu – mówi Andreas Zydek, omawiając proces poszukiwania optymalnego rozwiązania.
Jeśli kod kreskowy zostanie uszkodzony, zabrudzony lub zawilgocony, często jego odczytanie jest utrudnione lub nawet niemożliwe. Natomiast w przypadku korzystania z kodów DataMatrix, po uszkodzeniu 25 proc. lub nawet większej części informacji, prawidłowe odczytanie danych jest nadal możliwe.
Warto dodać, że pozycja etykiety na korku zabezpieczającym może się nieznacznie zmieniać, a informacja musi być możliwa do odczytania niezależnie od położenia. Dla czujnika wizyjnego firmy Balluff, z funkcją detekcji w zakresie 360°, to zadanie nie jest żadnym wyzwaniem. Andreas Zydek, w oparciu o swoje doświadczenia, twierdzi, że czytniki laserowe z obrotową głowicą odczytującą lub drogie czytniki laserowe krzyżowe nie są rozsądną alternatywą dla określonych warunków roboczych. –Przy ich pomocy nie uzyskalibyśmy wymaganej szybkości odczytu – podkreśla przedstawiciel firmy BHV.
Łatwa kontrola opakowań
Znaleziono także inteligentne rozwiązanie do trzeciego zadania, realizowanego w procesie produkcji w browarze Warsteiner: zestawy sześciu butelek, po napełnieniu, są grupowane w celu uformowania sześciopaku. Opatentowane opakowanie kartonowe nie wymaga użycia kleju i bazuje na specjalnym mechanizmie popychająco-ciągnącym, w którym karton jest automatycznie umieszczany wokół butelek z góry i od dołu. Trzy zakładki kartonowe są wzajemnie blokowane w taki sposób, że butelki można bezpiecznie transportować po podniesieniu. Także tutaj browar Warsteiner zastosował czujniki wizyjne firmy Balluff, w celu skontrolowania prawidłowości zamocowania blokad kartonowych w dolnej części opakowania. Zakładki o półksiężycowym kształcie zadrukowano czarnym kolorem, dzięki czemu zapewniają dobry kontrast w odniesieniu do pozostałej części opakowania. Ich szerokość jest kontrolowana w trzech pozycjach. Nawet jeśli tylko jedna zakładka blokująca jest wadliwa, następuje odrzucenie sześciopaku. Czujnik jest aktywowany przez krawędzie sześciopaku, natychmiast po ich wykryciu przez czujniki światłowodowe.
BALLUFF Sp. z o.o.
ul. Muchoborska 16, 54-424 Wrocław
tel. 71 338 49 29. fax 71 338 49 30
e-mail: balluff@balluff.pl
www.balluff.pl
www.warsteiner.de
www.bhv-automation.de
źródło: PAR 10/2014
Słowa kluczowe
balluff, browarnictwo, Czujniki wizyjne, oprogramowanie, systemy wizyjne
Komentarze
blog comments powered by Disqus