Jak rozdzielacze wytwarzane metodami przyrostowymi zmniejszają zużycie energii i emisję CO2
Materiał prasowy (Bosch Rexroth Sp. z o.o. ) drukuj
Rozdzielacze wytwarzane techniką druku 3D z rdzeniem piaskowym zapewniają lepszą ochronę środowiska w hydraulice przemysłowej. Korzyści z optymalnie zaprojektowanej geometrii wewnętrznej i zewnętrznej są widoczne w całym cyklu życia produktu: od oszczędności zasobów poprzez uproszczenie montażu i serwisu po mniejsze zużycie energii i ograniczenie emisji CO2 dzięki lepszej jakości procesów.
Zmiany klimatyczne należą do największych wyzwań naszych czasów. Przedsiębiorstwa przemysłowe muszą dziś tworzyć rozwiązania, które trwale zmniejszają emisje CO2. Hydraulika nowej generacji oferuje trzy główne czynniki zapewniające lepszą ochronę środowiska: zmniejszenie zużycia energii, płynu i materiału.
Jeśli chodzi o rozdzielacze, to kluczem do zwiększenia sprawności energetycznej i oszczędności zasobów jest stosowanie przyrostowych technologii produkcji. Za pomocą tych technologii geometrię wewnętrzną i zewnętrzną można projektować z większą swobodą niż dotychczas. Pozwala to na tworzenie systemów ze zoptymalizowanym przepływem i zintegrowanymi funkcjami, doskonale dopasowanych do konstrukcji maszyny. W hydraulice przemysłowej stosowane są głównie dwa typy produkcji przyrostowej: selektywne przetapianie laserowe (SLM) i drukowanie pośrednie techniką opartą na rdzeniu piaskowym. Najczęściej stosowaną metodą produkcji rozdzielaczy jest druk 3D z rdzeniem piaskowym. Więcej informacji na ten temat zamieszczamy poniżej.
Optymalizacja komputerowa
Przed rozpoczęciem drukowania rozdzielacza techniką 3D z rdzeniem piaskowym producent oblicza optymalną geometrię wewnętrzną, wykorzystując symulację przepływu. Dzięki symulacji CFD (ang. Computational Fluid Dynamics - obliczeniowa mechanika płynów) można lepiej przeanalizować poszczególne przepływy i dowiedzieć się, jak uniknąć kawitacji i strat ciśnienia przy ograniczeniu do minimum zużycia materiałów, tak aby osiągnąć optymalną sprawność energetyczną i przedłużyć okres eksploatacji urządzenia. Równocześnie w symulacji tej brane są pod uwagę zintegrowane funkcje i umiejscowienie połączeń.
Aby jeszcze bardziej zmniejszyć wagę urządzenia i ilość materiału potrzebną do jego wytworzenia, a także ułatwić instalację systemu w maszynie, przeprowadza się również optymalizację geometrii zewnętrznej. W rezultacie oszczędność zasobów obejmuje cały cykl eksploatacji życia produktu: od wytwarzania poprzez użytkowanie po recykling.
W kolejnej fazie drukarka 3D tworzy negatyw rozdzielacza w cienkich warstwach o grubości 280 mikrometrów. Ten model rdzeniowy służy do odlania surowego bloku, w którym są maszynowo umieszczane gwinty i powierzchnie uszczelniające.
Zalety technologii druku 3D z rdzeniem piaskowym
W przypadku wytwarzania pojedynczych bloków kontrolnych zaletą drukowania 3D z rdzeniem piaskowym jest z jednej strony, zwiększenie sprawności energetycznej, z drugiej - zmniejszenie zużycia zasobów. Ponadto technika ta oferuje użytkownikom inne atrakcyjne korzyści, takie jak większa funkcjonalność i prostota montażu. Jest to możliwe dzięki większej swobodzie projektowania, jaką zapewnia wytwarzanie przyrostowe. W porównaniu z tradycyjnymi procesami, można odlewać o wiele bardziej złożone formy, np. kanały o zmiennej średnicy.
1. Większa wydajność podczas montażu, eksploatacji i serwisowania
Dzięki swobodzie projektowania oferowanej przez technikę druku 3D ze rdzeniem piaskowym można utworzyć geometrię zewnętrzną, która umożliwi lepsze dopasowanie rozdzielacza do małych przestrzeni w instalacjach. Ułatwia ona również montaż i serwis. W fazie konstrukcji wszystkie połączenia są precyzyjnie pozycjonowane z myślą o ich optymalnej dostępności.
Projekt wewnętrzny skupia się na optymalizacji przepływu. W wyniku symulacji CFD optymalizowana jest geometria wewnętrzna. Straty ciśnienia i kawitacja są ograniczone do minimum, podczas gdy mniej martwych przestrzeni oznacza lepszą jakość sterowania. Dzięki tej większej swobodzie projektowania można uniknąć przekierowywania kanałów pod kątem prostym. Wszystko to ostatecznie polepsza jakość procesów.
2. Zintegrowane funkcje
Dzięki swobodzie projektowania geometrii wewnętrznej i zewnętrznej takie komponenty, jak filtry lub akumulatory, które zwykle były instalowane odrębnie, można podłączyć bezpośrednio do bloku nawet w bardzo wymagających lub ciasnych przestrzeniach instalacyjnych. W przypadku orurowania pozwala to nie tylko zaoszczędzić czas i materiały, lecz również zmniejsza ryzyko wycieku, ponieważ otwory pomocnicze i zaślepki gwintowe nie są już potrzebne.
3. Mniej materiałów, mniejsza waga
Podczas wytwarzania rozdzielaczy techniką drukowania 3D z rdzeniem piaskowym zużywa się co najmniej o 1/3 mniej materiałów w porównaniu z techniką tradycyjną. Oznacza to nie tylko oszczędność zasobów, lecz również mniejszą wagę urządzenia, która ułatwia jego transport i montaż.
Ile energii można zaoszczędzić? O ile zmniejszyć emisję CO2?
Następujący przykład pokazuje, o ile można zmniejszyć zużycie materiału i energii oraz emisję CO2 w wyniku drukowania 3D z rdzeniem piaskowym:
Rozdzielacz wytworzony techniką druku 3D z rdzeniem piaskowym wymaga o ok. 50 kg mniej materiału niż wyprodukowany w sposób tradycyjny. Mniejsza ilość materiału wykorzystana w odlewie oraz wynikająca z niej redukcja zużycia energii powoduje zmniejszenie emisji CO2 podczas produkcji o ok. 130 kg, tj. w przybliżeniu o jedną trzecią. Wielkość ta jest porównywalna z emisją samochodu zasilanego paliwem kopalnym, który przejechał 1000 km.
W fazie operacyjnej rozdzielacz wymaga mniej energii elektrycznej dzięki geometrii wewnętrznej ze zoptymalizowanym przepływem, minimalną różnicą ciśnień (wskaźnikiem ∆p) i niską emisją hałasu. Po 3000 godzin pracy łączna oszczędność energii kumuluje się do 740 kWh, co oznacza zmniejszenie emisji CO2 o około 450 kg. Odpowiada to emisji samochodu, który przejechał około 3000 km.
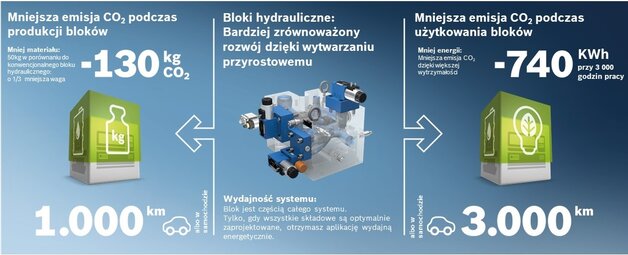
Przy 3000 godzin pracy w ciągu roku łączna oszczędność energii wynosi 740 kWh, a emisja CO2 zmniejsza się o około 450 kg na rok, co odpowiada przejechaniu przez samochód około 3000 km.
Czy ta inwestycja jest opłacalna?
Dzięki zmniejszeniu zużycia energii w fazie operacyjnej rozdzielacze produkowane techniką druku 3D z rdzeniem piaskowym zwykle przynoszą zwrot z inwestycji po ok. 3,5 roku. Później użytkownik osiąga bieżące oszczędności. Jeśli korzyści z systemu uzasadniają inwestycję, można skorzystać z atrakcyjnej opcji, jaką jest modernizacja istniejących już urządzeń poprzez instalację rozdzielaczy wykonanych techniką przyrostową. Pozwala to nie tylko zmniejszyć zużycie mocy i emisję CO2, lecz również znacznie usprawnić procesy.
Zawsze jednak zaleca się ocenę poszczególnych elementów, takich jak rozdzielacze, z perspektywy całego układu. Generalnie możliwości zaoszczędzenia energii i obniżenia emisji CO2 są największe wtedy, gdy układ jest modernizowany w całości. Dotyczy to zarówno nowych projektów, jak i modernizacji systemów już istniejących. Równie ważnym komponentem są w tym przypadku napędy o zmiennej prędkości obrotowej, które umożliwiają generowanie mocy na żądanie.
Podsumowanie: pełne wykorzystanie potencjału
Wraz z innymi innowacyjnymi rozwiązaniami, rozdzielacze produkowane techniką druku 3D z rdzeniem piaskowym stanowią ważną część nowoczesnych przemysłowych systemów hydraulicznych. Potraktowane jako inwestycja w technologię i ochronę środowiska, przynoszą one korzyści na wszystkich etapach cyklu życia. Podczas gdy geometria wewnętrzna zoptymalizowana za pomocą symulacji CFD zmniejsza zużycie energii, geometria zewnętrzna zaprojektowana z myślą o zaoszczędzeniu miejsca pozwala zmniejszyć ilość potrzebnego materiału. Obie geometrie prowadzą do zmniejszenia emisji CO2, ułatwiają manipulowanie urządzeniem i polepszają jakość procesów.
W ramach koncepcji Connected Hydraulics firma Bosch Rexroth oferuje pełną gamę rozwiązań umożliwiających zaoszczędzenie zasobów i zwiększenie sprawności energetycznej. Każdy, kto chce osiągnąć najlepsze rezultaty i najszybszy zwrot z inwestycji, może się zapoznać z kluczowymi czynnikami, które mu to ułatwią, i przekonać się o ich skuteczności.
źródło: Bosch Rexroth
Komentarze
blog comments powered by Disqus