Robot – pracownik przyszłości
Jakub Kwiatkowski (MITSUBISHI ELECTRIC EUROPE B. V.) print
Współczesny przemysł stawia niesamowicie wysokie wymagania wszystkim dostawcom. Szczególnie wyśrubowane są oczekiwania wobec firm, które dostarczają rozwiązania z zakresu robotyki. Jednym z częstych rozwiązań stosowanych na liniach produkcyjnych są roboty przemysłowe, które zdobywają coraz większą popularność w polskich fabrykach. Jednocześnie z roku na rok rosną wymagania wobec nich, ponieważ każdy chce produkować więcej, mniejszym kosztem i w krótszym czasie. Dlatego nieodłącznym elementem robotów stają się dodatki, które mają im zastępować ludzkie zmysły, pozwalając w ten sposób na wykorzystanie 100 proc. ich możliwości.
Współczesny przemysł oczekuje od robotów przede wszystkim zastąpienia człowieka w trudnym środowisku, np. podczas prac w warunkach trudnych, powtarzalnych, monotonnych i takich, gdzie łatwo o ludzki błąd. Oznacza to, że taki robot musi być wystarczająco inteligentny i zdolny do przystosowania się do zmiennych warunków pracy. Tak jak człowiek. Przyjrzyjmy się zatem, w jaki sposób możemy doposażyć robota, by spełniał on najbardziej wyśrubowane wymagania.
Integracja to podstawa
Pierwszą i najważniejszą rzeczą, jakiej potrzebuje robot, jest jeden, centralny system sterowania – porównując tę sytuację do człowieka, stanowi on niejako mózg całego systemu. Linia produkcyjna to nie tylko robot przemysłowy. Często składają się na nią taśmociągi, maszyny wieloosiowe, maszyny CNC, system nadrzędny itp. Jeśli jednostki te pracują oddzielnie, możemy spodziewać się problemów związanych z integracją systemu już na etapie projektowania. Mitsubishi Electric znalazło rozwiązanie, zapewniając jedną, wspólną platformę sterowania dla wszystkich aktywów składających się na linię produkcyjną – platformę iQ-R.
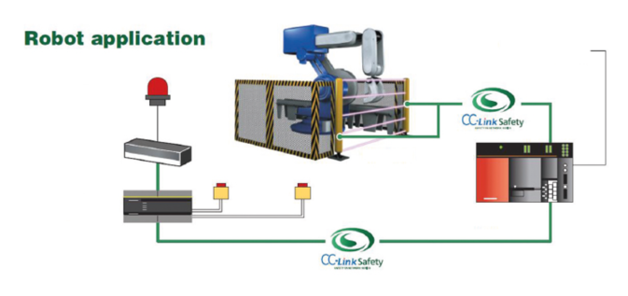
Dzięki światłowodowej sieci CC-link możemy do platformy sterowania podłączyć takie elementy, jak kurtyny laserowe, przyciski awaryjne oraz wyłączniki bezpieczeństwa
Platforma iQ-R jest niezwykle elastycznym, multifunkcyjnym systemem sterowania. Na płycie bazowej możemy umieścić nawet do czterech procesorów i 64 różnych modułów. Mogą to być jednostki PLC i robotów, wieloosiowe kontrolery Motion czy kontroler procesowy. Każdy z tych procesorów ma własny program i pracuje niezależne od innych. Jednak przy pomocy wspólnej szyny pamięci są w stanie wymieniać między sobą dane błyskawicznie. Dzięki temu, łącząc dwie cele zrobotyzowane z wieloosiową maszyną, mamy pewność, że obiekty te mogą bezkolizyjnie pracować nad jednym przedmiotem, wykorzystując tylko jeden sterownik. Zyskujemy w ten sposób maksymalizację bezpieczeństwa i minimalizację miejsca potrzebnego dla takiej aplikacji. Innym popularnym rozwiązaniem jest zastosowanie dwóch maszyn CNC sterowanych modułem C70 i sprzężonego z nimi robota, który odpowiada za dostarczenie i odebranie gotowego elementu z maszyny. Często spotykane jest również zastosowanie procesora C z modułem MES-IT. Dzięki nim jesteśmy w stanie kontrolować do 32 osi serwo oraz zbierać i wysyłać dane produkcyjne z całej fabryki. Wszystko dzięki użyciu jednej platformy iQ-R!
Zastąpić zmysły
Aby roboty były w stanie jak najlepiej wykonywać powierzone im prace, potrzebne jest im coś na kształt ludzkich zmysłów. Pierwszy z nich – wzrok – został znakomicie zastąpiony dzięki dedykowanym systemom wizyjnym.
Dwóch liderów w dziedzinie automatyzacji – Mitsubishi Electric i firma Cognex – połączyło siły i stworzyło wspólną platformę systemów wizyjnych dla robotów przemysłowych. Dzięki temu roboty MELFA mają wbudowane funkcje pozwalające w łatwy i szybki sposób… wyposażyć je w oczy. Dedykowany system wizyjny Cognex pozwala im znaleźć pożądany przedmiot w obszarze pracy i dostarczyć odpowiednie dane na temat jego położenia do platformy iQ-R, która jest „mózgiem” robota. Aby ułatwić pracę programistom, Mitsubishi Electric wyposażyło platformę iQ-R w specjalny system MELFA Vision, pozwalający sprzężyć robota z wizją w intuicyjny sposób.
System wizyjny można też wykorzystać podczas procesu kontroli jakości. Jest on w stanie całkowicie zastąpić człowieka i zapewnić wysoce efektywny i szybki sposób sprawdzania produktów. Przy wykorzystaniu High Speed Data Logger, jednego z modułów dostępnych dla platformy iQ-R, maszyna może zebrać i zapisać raporty z całego procesu wytwarzania i testowania. System taki w znacznym stopniu wspiera działania firm w zakresie filozofii Zero Defect, w której zakłada się wyeliminowanie wszystkich wadliwych produktów już na etapie produkcji i kontroli jakości. Dzięki High Speed Data Logger możliwe jest też wygenerowanie i wysłanie automatycznej informacji o produkcji np. do zarządu firmy, bez konieczności stawiania skomplikowanego systemu IT.
Krokiem milowym, jeśli chodzi o systemy wizyjne, było zastosowanie wizji 3D, która pozwala dostarczyć robotowi dużo więcej danych niż w przypadku obrazu obiektu na płaszczyźnie. Umożliwia to maszynie rozpoznanie i podniesienie obiektu leżącego np. w pudełku – nie ma już potrzeby budowania osobnej maszyny, która wyciągnie obiekt i zapewni jego poprawne ułożenie, tak by robot mógł nad nim pracować. Dzięki systemowi trójwymiarowej wizji może on sam rozpoznać m.in. pozycję i kąt nachylenia elementu. Warto podkreślić, że roboty Mitsubishi Electric mają wbudowane funkcje, pozwalające wykorzystać system wizyjny zarówno 2D, jak i 3D.
Kolejnym zmysłem, w jaki możemy wyposażyć robota, jest dotyk. W 2014 r. Mitsubishi Electric wprowadziło na rynek innowacyjny produkt, jakim jest czujnik siły 1F-FS001-W200 – laureat wielu prestiżowych nagród przyznawanych w konkursach na produkt roku w dziedzinie automatyki.
W przeszłości robot operujący nad przedmiotem musiał z góry znać wszystkie współrzędne położenia obiektu. To oznaczało, że nie był w stanie sam stwierdzić, czy obiekt został podniesiony lub odłożony w prawidłowy sposób. Dziś, dzięki zastosowaniu czujnika siły, roboty Mitsubishi Electric serii RV-F i RH-F mogą jeszcze delikatniej i z odpowiednią siłą operować elementami w otaczającej przestrzeni. Przykładowo w czasie pracy robota możemy wykrywać kontakt z elementami otoczenia, kontrolować i zmieniać siłę wywieraną przez robota oraz wpływać na to, jak pracuje. Jest to bardzo użyteczne w aplikacjach takich jak montaż, gdzie umieszczamy jeden element w drugim. Dzięki zastosowaniu czujnika na początku zadania kontrolujemy precyzyjnie siłę, aby nie uszkodzić powierzchni elementów, a gdy odpowiednia pozycja wkładania zostanie znaleziona, robot wykonuje zadanie do końca z właściwą sztywnością. Ponieważ robot może poruszać się w czasie dociskania narzędzia z kontrolowaną siłą, rozwiązanie to znajduje także idealne zastosowanie w aplikacjach takich jak szlifowanie i polerowanie. Ponadto dzięki czujnikowi można skrócić czas uczenia i programowania – robot sam znajdzie odpowiednią pozycję, która nie będzie niszczyć powierzchni obiektów. Dodatek ten znajduje także szerokie zastosowanie w aplikacjach kontroli jakości wykonania produktów, gdzie potrzebne są pomiary sił niezbędnych do wykonania ruchów.
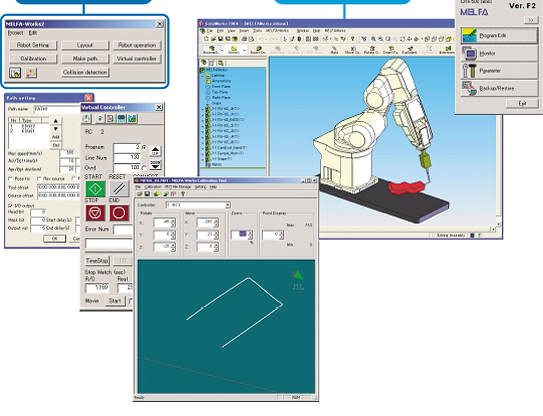
Oprogramowanie MELFA Works pozwala na zaimportowanie gotowych elementów, które umożliwią wykonanie potrzebnych testów i symulacji
Bezpieczeństwo przede wszystkim
Nowoczesna fabryka to przede wszystkim bezpieczna fabryka – nie tylko dla ludzi, ale także dla sprzętu i wytwarzanego produktu. Produkty Mitsubishi Electric są wyposażone w rozwiązania, które zapewniają odpowiedni poziom ochrony. Dzięki nim spełniają wyśrubowane normy, narzucane przez prawo, ale także dają pewność, że nikt nie ucierpi z powodu awarii czy błędu. Niezastąpiona jest w tym przypadku wspomniana już seria iQ-R, która jest w stanie zintegrować wszystkie podzespoły z linii produkcyjnej z systemem bezpieczeństwa. Dzięki światłowodowej sieci CC-link możemy do platformy sterowania podłączyć takie elementy, jak kurtyny laserowe, przyciski awaryjne oraz wyłączniki bezpieczeństwa. Dzięki nim w przypadku zagrożenia jesteśmy w stanie momentalnie zatrzymać urządzenia znajdujące się na drugim końcu fabryki – napędy, podzespoły elektryczne czy robota. Ponadto produkty Mitsubishi Electric, takie jak serwonapędy serii MR-J4 czy przetwornice częstotliwości FR-A800, są wyposażone w dodatkowe funkcje ochronne, np. SS1, SS2, SLS, SSM. Kompleksowe rozwiązania Mitsubishi Electric w zakresie bezpieczeństwa zapewniają bezpieczeństwo ludziom, maszynom i samemu produktowi.
Uczymy robota
Kolejną równie ważną cechą inteligentnego robota jest możliwość jego szybkiego i łatwego zaprogramowania. Kiedy robot na co dzień pracuje z różnymi elementami, bardzo istotne jest, aby proces uczenia go nowych zadań nie trwał długo. Obecnie bardzo dużo elementów jest projektowanych w programach CAD, np. Solid Works 3D. Dzięki oprogramowaniu MELFA Works możemy bez problemu przenieść projekt elementu wykonany w Solid Works do pamięci robota i dzięki temu znacznie skrócić czas potrzebny do jego zaprogramowania.
Kolejnym ciekawym ułatwieniem jest możliwość wykonywania symulacji w programach CAD. Oprogramowanie MELFA Works zawiera zestaw gotowych robotów, które można zaimportować do programu Solid Works i bez problemu dołączyć do projektu linii produkcyjnej. Dzięki temu mamy możliwość przetestowania wszystkich elementów takiej linii, zanim zostanie ona wykonana.
Pracownik na miarę XXI wieku
Dzisiaj już chyba nikogo nie trzeba specjalnie przekonywać, że automatyzacja produkcji jest koniecznością. Są dziedziny, w których roboty zadomowiły się na dobre już kilka dekad temu, są też takie, gdzie dopiero zaczynają być powszechne. Wynika to przede wszystkim z możliwości, jakie daje maszynom rozwój i zastosowanie różnych dodatków. A te, jak udowodniliśmy, z roku na rok są coraz lepsze. Miejmy nadzieję, że przełoży się to na coraz lepsze, tańsze, a w konsekwencji łatwiej dostępne produkty dla każdego z nas.
Mitsubishi Electric Europe B.V. Oddział w Polsce
ul. Krakowska 50
32-083 Balice
tel. 12 347 65 00
fax 12 347 65 01
source: Automatyka 6/2015