Optymalizacja produkcji łożysk dzięki RFID
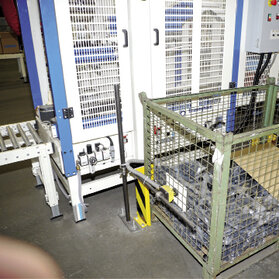
Głowica zapisująco-odczytująca HF niezawodnie odczytuje nośniki danych RFID zamontowane na siatce kontenera, niezależnie od dużej ilości metalu znajdującej się wokół (fot. Turck)
W trakcie 43 lat pracy Heinz Ehmann, menedżer firmy Alfred Thun GmbH & Co KG z siedzibą w Ennepetal, był świadkiem wielu prób wprowadzenia ręcznego systemu nadzoru produkcji. Ze względu na wysoki nakład pracy, jaki niosą ze sobą takie rozwiązania, nigdy nie były one brane pod uwagę jako realne opcje. Obecnie, wraz z rozwojem technologii RFID pojawiły się nowe możliwości realizacji zautomatyzowanych systemów kontroli i nadzoru produkcji materiałów. Dzięki temu rodzinna firma z Ennepetal mogła zwiększyć wydajność i utrzymać wiodącą na rynku pozycję we wszystkich swoich segmentach produktowych.
Thun zaopatruje przemysł rowerowy na całym świecie w łożyska wewnętrzne do rowerów miejskich, dziecięcych i górskich. Ponadto dostarcza kompletne komponenty do rowerów elektrycznych systemu Pedelec, których popularność w ostatnim czasie stale rośnie. Zatrudniająca 60 pracowników firma dostarcza każdego roku prawie milion sztuk łożysk, co przekłada się na około 60-procentowy udział w rynku i czyni tego niemieckiego producenta jednym z europejskich liderów sprzedaży łożysk rowerowych.
Wymagania
W 2009 r. firma zdecydowała się zmodernizować swoją produkcję. Celem modernizacji było wdrożenie systemu nadzoru partii materiału w całym łańcuchu produkcji z wykorzystaniem systemu RFID. W trakcie wdrażania należało rozwiązać kilka kwestii technicznych, takich jak sposób montażu nośnika, proces przyjęcia towaru do identyfikacji, a także etap oczyszczania i powlekania łożysk.
– Jeżeli chcemy, aby proces produkcji był niezawodny i wysoce powtarzalny, musimy wdrożyć zautomatyzowany system identyfikacji RFID, który wymaga jedynie niewielkiego wkładu pracy operatora – wyjaśnia Heinz Ehmann z firmy Thun.
Pierwszym rozwiązaniem, jakie wzięto pod uwagę, był system RFID wykorzystujący częstotliwość UHF. Zaletą tego zakresu częstotliwości jest niewątpliwie zasięg pracy oraz elastyczność całego systemu. Zastosowanie pasma UHF w środowisku produkcyjnym firmy Thun nie było jednak takie oczywiste ze względu na metalowe obudowy koszy transportowych, do których nośniki UHF miały być przymocowane. Ostatecznie postanowiono wykorzystać alternatywne rozwiązanie, zaproponowane przez integratora systemów, firmę Weingartner Automatisierung z Oberhausen. Rozwiązanie to bazowało na systemie BLident firmy Turck.
System BLident dostarcza bogaty pakiet rozwiązań identyfikacji RFID, które spełniały wszystkie wymagania projektu. Dzięki szerokiemu portfolio Turck mógł spełnić większość zadań stawianych przez projekt, nawet jeżeli niektóre z nich były rozwiązywane w trakcie jego realizacji.
System RFID firmy Turck pozwala na jednoczesne stosowanie zarówno komponentów HF, jak i UHF. W pierwszym etapie projektu wykorzystano technologię HF, która wykorzystuje częstotliwość 13,56 MHz. Częstotliwość ta zmniejsza wpływ potencjalnych zakłóceń, co było szczególnie istotne w otoczeniu urządzeń generujących silne pola. Decyzja o wyborze tego rozwiązania zapadła po udanym teście zanurzenia nośników RFID w kąpieli galwanicznej. Wysoka temperatura i kwaśne środowisko galwaniczne nie zaszkodziło nośnikom, które mają obudowę o stopniu ochrony IP67. Jednym z wyzwań było też dostrojenie komunikacji między elementami sieci, które miały być dostosowane do systemu ERP Navision.
Rejestracja otrzymanych towarów
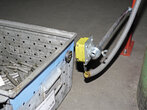
Nośniki danych RFID są pewnie zamontowane na metalowym kontenerze przy użyciu elementu dystansującego (fot. Turck)
Proces identyfikacji rozpoczyna się w momencie, gdy towar jest odbierany. Jeżeli dokument dostawy jest wyposażony w kod Data Matrix, komponenty od dostawców są skanowane. Dane docierają do systemu ERP i są łączone z polem UID nośnika RFID, przypisanego do odpowiedniego kosza transportowego. Wszystkie dane gromadzone w centralnej bazie danych SQL są odczytywane i zapisywane za pomocą systemu Middleware Visam. Thun zoptymalizował proces pozwalając, by dostawca mógł zachować minimalny poziom zapasów. Aktualnie dostępne i wymagane ilości mogą być pobierane z systemu ERP w dowolnym miejscu i o dowolnym czasie dzięki dostępowi on-line.
System identyfikacji sprawdził się szczególnie na etapie oczyszczania i montażu łożysk. Czystość łożyska musi być zagwarantowana na każdym etapie procesu. Dzięki głowicom RFID urządzenie „wie”, jaka partia produkcyjna jest w danym momencie przetwarzana. Światło lampki K50 sygnalizuje pracownikom, czy procedura jest wykonywana prawidłowo, czy też nie.
W trakcie wdrażania systemu pojawił się też inny problem, który został szybko rozwiązany: wykorzystywana w procesie oczyszczania śrutownia miała ładowność jedynie 80 kg, gdy kosze transportowe były dwukrotnie cięższe. W przeszłości używanie wag wymuszało ręczne kalibrowanie, obecnie proces ten udało się zautomatyzować. Dzięki technologii RFID wszystkie wałki z jednego kosza transportowego mogą być łatwo przypisane do właściwej serii. Podczas opróżniania kosza czujnik nachylenia mierzy kąt nachylenia, co pozwala automatycznie na jego ponowne napełnienie. Wykorzystanie czujnika znacznie usprawniło pracę systemu, ponieważ w przeszłości zdarzały się przypadki przestojów, spowodowane powtórnym skierowaniem do procesu pełnego kosza.
Jakość
Kolejnym etapem była automatyzacja montażu specjalnych uchwytów. Dawniej pracownik ręcznie wprowadzał specjalną konfigurację zawierającą typ uchwytu za pomocą panelu operatorskiego znajdującego się na maszynie montującej. Niestety, w sytuacji gdy stosowanych jest wiele typów uchwytów, pomyłki były nie do uniknięcia. Obecnie zamówienie jest wprowadzane centralnie za pomocą systemu ERP i przesyłane bezpośrednio do maszyny, przy której pracownik jedynie akceptuje zamówienie i uruchamia proces. Maszyna odczytuje wszystkie potrzebne informacje zawierające ustawienia i komponenty z bazy danych, a następnie ustawia poprawną konfigurację. Głowice RFID odczytują dane z umieszczonych na koszach nośników, sprawdzając, czy przy bieżącym zamówieniu zostaną użyte właściwe komponenty. Czujnik nachylenia firmy Turck dba o to, by kosz został całkowicie opróżniony. Informacja z czujnika oraz odczytane z nośnika dane są następnie przesyłane protokołem Modbus TCP do systemu Middleware Visam za pomocą interfejsu systemu BL67 i środowiska CoDeSys.
Perspektywy
Dzięki nadzorowi i możliwości śledzenia lokalizacji partii materiałów za pomocą RFID firma z Ennepetal stworzyła wartość, którą dodała do produktów oferowanych klientom. Lepsza przejrzystość procesów produkcyjnych umożliwia zwiększenie ich elastyczności bez ponoszenia dodatkowych kosztów. Firma Thun zyskała znaczącą przewagę nad konkurencją, która będzie się powiększać wraz z dalszymi optymalizacjami systemu. Kolejnym krokiem w tym kierunku będzie włączenie do systemu kontroli jakości i usług.
Patryk Zalewski
Specjalista ds. automatyki
TURCK Sp. z o.o.
tel. 774434809
kom. +48604097271
e-mail: patryk.zalewski@turck.com
źródło: TURCK
Komentarze
blog comments powered by Disqus