Maszyna na miarę Przemysłu 4.0 – inteligencja i modułowość
Proces produkcyjny może być realizowany przez różnego typu maszyny i systemy. Klasyczne podejście traktuje maszynę produkcyjną jako jedną całość, której przebudowa jest bardzo trudna i często sprawia, że rozwiązanie po modyfikacji nie jest optymalne. Dziś maszyny modułowe i rozproszona logika pozwalają zmienić ten system działania.
Tradycyjna koncepcja okablowania bazuje na dużych szafach sterowniczych, w których sygnały z obiektu prowadzone są do jednego sterownika. Problemy pojawiają się w przypadku dużych odległości, gdzie dochodzi do spadków napięcia lub występowania zakłóceń, które mają znaczenie np. dla pomiarów.
Część producentów maszyn do lokalnego zbierania sygnałów wykorzystuje szafki z terminalami zaciskowymi, które umieszcza w punktach występowania większej liczby sygnałów, gdzie wprowadzane są połączenia z pojedynczych urządzeń, a następnie za pomocą jednego przewodu wielożyłowego przechodzą w kierunku głównej szafy sterującej. Wymaga to jednak projektowania oraz pracy nad kolejnymi szafkami. Prostszym rozwiązaniem byłoby zamontowanie (najlepiej bez szafki) urządzenia lokalnie zbierającego sygnały. Jakie zatem są aktualnie techniczne możliwości zoptymalizowania okablowania na maszynie?
Koncentratory pasywne
W miarę rozwoju technologii rynek wzbogacał się o kolejne rozwiązania. Najprostszym z nich jest tzw. koncentrator pasywny. Dzięki zastosowaniu tego urządzenia możliwe jest pominięcie montażu mniejszych szafek w miejscu zagęszczenia sygnałów. Koncentratory serii TB o stopniu ochrony IP67 pozwalają na doprowadzenie sygnałów bezpośrednio do urządzenia i przesłanie ich jednym przewodem do szafy. Zapewnia to oszczędność miejsca na obiekcie i skrócenie czasu niezbędnego do wykonania połączeń. Pozostaje jednak nadal kwestia ułożenia lub wymiany grubego, wielożyłowego przewodu, co często stanowi wyzwanie. Czy istnieje rozwiązanie pozwalające na redukcję okablowania i umożliwiające sprawną wymianę danych między sterownikiem a lokalnym modułem koncentrującym sygnały?
Koncentratory sieciowe
Jeżeli przewody z koncentratorów pasywnych stanowią przeszkodę, z pomocą przychodzą urządzenia umożliwiające komunikację. W zależności od stosowanej na maszynie sieci zbierają one sygnały z innych urządzeń na obiekcie i przekazują informacje o stanie do sterownika. Pozwala to na wyeliminowanie wielożyłowego przewodu. W zamian potrzebny jest przewód doprowadzający zasilanie i sieć. W przypadku niektórych przewodów sieciowych możliwe jest przesyłanie zasilania za ich pośrednictwem (należy jednak mieć na uwadze maksymalne natężenie prądu, który można nimi poprowadzić). Takie rozwiązanie pozwala na szybkie reagowanie w razie wystąpienia awarii, spowodowanej np. uszkodzeniem przewodu.
Cienkie przewody można wymienić dużo szybciej, a dodatkowo ten sam typ przewodu może zostać użyty w wielu miejscach w zakładzie, co procentuje większą dostępnością części zamiennych w magazynach wewnętrznych klientów. Prostsze jest również układanie mniejszych przewodów w łańcuchach, co pozwala na zastosowanie rozwiązania np. na ramieniu robota przemysłowego.
Koncentratory sieciowe występują w różnych wersjach. Oprócz rozwiązań o stopniu ochrony IP67, nadających się do montażu bezpośrednio na obiekcie, występują także wersje IP20 do montażu na szynie w szafie sterowniczej. Sygnały obsługiwane przez koncentratory sieciowe to m.in. cyfrowe, analogowe, IO-Link, RFID, Safety oraz RS-232/485. Doskonałym rozwiązaniem do montażu w szafie są koncentratory serii FEN20, a w przypadku montażu bezpośrednio na maszynie – serii TBEN oraz BLcompact. Dzięki tym urządzeniom możliwe jest dzielenie maszyny na mniejsze części, w których koncentrowane są sygnały. Może więc warto zastanowić się nad podzieleniem maszyny na mniejsze części?
Maszyny modułowe
Dzięki koncentratorom sieciowym pojawiła się możliwość tworzenia maszyn w inny sposób niż dotychczas. Klasyczne podejście do budowy maszyn zakłada konstruowanie jednej zespolonej ze sobą całości. Ewentualne zmiany wiążą się z dużym nakładem pracy i czasu. Elementy są ściśle ze sobą powiązane, a dodatkowo niejednokrotnie maszyny wykonywane są w specjalnej konfiguracji, aby sprostać indywidualnym wymaganiom klienta.
Nowa koncepcja budowy maszyn ma na celu m.in. ułatwienie modernizacji, rozbudowy aplikacji, a także szybkiego skonfigurowania maszyny odpowiednio do potrzeb i dostępnej przestrzeni. Większość maszyn może zostać podzielona na kilka mniejszych, łatwiejszych do ustawienia, budowy czy wymiany modułów. To, jak powinna wyglądać całość zależy od indywidualnych wymagań użytkownika. Dzięki zastosowaniu koncepcji modułowej zyskuje się m.in. możliwość szybkiego reagowania na zmiany w procesie i zwiększenia stopnia automatyzacji. Koncentratory o stopniu ochrony IP67 pozwalają na sprawne dołączanie kolejnych układów, a wbudowane switche sprawiają, że rozbudowa jest łatwiejsza i wymaga mniejszych nakładów finansowych. Coraz częściej producenci maszyn decydują się na wykorzystanie komponentów sprzyjających rozwojowi koncepcji tworzenia maszyn składających się z modułów.
Kolejne korzyści wynikające z wykorzystania tego typu rozwiązania to ułatwienie prac serwisowych, a także przenoszenia maszyn do innych lokalizacji. Zmniejszenie wymiarów maszyn sprawia, że do ich przeniesienia potrzeba mniej specjalistycznego sprzętu, dzięki czemu czas takiej operacji ulega znacznemu skróceniu. Zastosowanie modułów budowanych w jednym standardzie sprawia także, że łatwiej zabezpieczyć stany magazynowe, co pozwala łatwiej usunąć nagłą awarię spowodowaną np. uszkodzeniem przewodu. Połączenia wykonywane są na mniejszych odległościach, dzięki czemu użyte przewody są krótsze niż w klasycznym rozwiązaniu, a tym samym ich wymiana jest o wiele łatwiejsza w realizacji. Czy można usprawnić coś jeszcze?
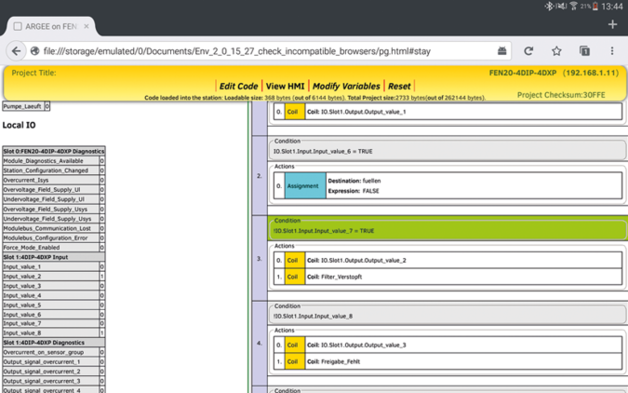
Dzięki wbudowanej funkcjonalności ARGEE – dostępnej w standardzie – koncentratory mogą być programowane przez przeglądarkę internetową
Sterowanie lokalne
Skoro maszyny można dzielić na moduły, to może logika też powinna zostać podzielona? Wszystko zależy od typu użytego sterownika, wymagań użytkownika oraz krytycznych parametrów procesu. Istnieją aplikacje, w których określone zadania powinny być realizowane w możliwie najkrótszym czasie – np. sygnał do zatrzymania napędu przy wydłużonym czasie cyklu może pojawiać się z opóźnieniem, które spowoduje mechaniczne uszkodzenie maszyny. Jeżeli część maszyny (moduł) odpowiedzialna za zatrzymanie będzie realizowała własną logikę, to moment zatrzymania nie będzie uzależniony od cyklu głównego sterownika. Taką możliwość stwarzają koncentratory sieciowe serii FEN20, TBEN oraz BLcompact.
Dzięki wbudowanej funkcjonalności ARGEE – dostępnej w standardzie – koncentratory mogą być programowane przez przeglądarkę internetową. Dostęp do bezpłatnych bibliotek usprawnia proces programowania urządzeń i otwiera nowe możliwości w zakresie tworzenia maszyn modułowych. Każda z części maszyny może mieć własny kontroler, dzięki czemu modernizacja lub przeniesienie modułu do innej maszyny wymaga minimalnych modyfikacji w programie głównego sterownika, z którym ARGEE może wymieniać dane. Zainteresowani użytkownicy mogą przetestować oprogramowanie ARGEE w bezpłatnym symulatorze zawierającym znaczną część modeli dostępnych w ofercie. Protokoły komunikacyjne, którymi może posługiwać się koncentrator programowalny to Profinet, EtherNet/IP oraz Modbus TCP. Wszystkie protokoły są dostępne w jednym urządzeniu pod nazwą Multiprotocol.
Z funkcjonalności ARGEE można skorzystać nawet wtedy, gdy całe sterowanie realizowane jest przez jeden sterownik PLC – jest to możliwe dzięki „Uśpionemu ARGEE”. Można to wykorzystać praktycznie wszędzie tam, gdzie w aplikacji może dojść do uszkodzenia części z powodu nagłej utraty komunikacji. Przykładem jest moduł ze sterowaniem bramą pieca oraz napędu. Do wykonania może poslużyć moduł TBEN-S1-8DXP ze stopniem ochrony IP67 oraz ośmioma konfigurowalnymi wejściami/wyjściami cyfrowymi. Podstawowym stanem będzie w tym przypadku przesyłanie sygnałów z czujników krańcowych do sterownika oraz realizacja komend otwarcia/zamknięcia bramy i startu/zatrzymania rolek (wyjazd z pieca). Jeżeli przedmioty zostaną w piecu zbyt długo, mogą ulec uszkodzeniu. W przypadku utraty komunikacji – np. z powodu przerwania przewodu komunikacyjnego – ARGEE może zacząć realizować własny program, który otworzy bramę i włączy rolki, aby przedmiot w bezpieczny sposób opuścił piec. Innym przykładem jest realizacja sterowania bramą pożarową. Moduł może realizować zadania za pomocą sterownika PLC. Jeżeli tylko pojawi się sygnał alarmowy, ARGEE może zacząć realizację własnej logiki, która będzie odpowiedzialna za sterowanie bramą. Opcji wykorzystania oprogramowania jest bardzo wiele – wszystko zależy od potrzeb użytkowników. Możliwości programowania dotyczą obecnie także modułów do obsługi sygnałów bezpieczeństwa, których na maszynie zwykle jest przynajmniej kilka.
W niektórych aplikacjach cały system oparty jest na technologii ARGEE, uzupełnionej o moduł z kanałami Safety TBPN-L1-FDIO1-2IOL (PROFIsafe) lub TBIP-L1-FDIO1-2IOL (CIP Safety) programowalne przez TURCK Safety Configurator. Progra-mowalne moduły bezpieczeństwa również doskonale wpisują się w koncepcję budowy maszyn modułowych. Oddalone sygnały z E-Stopów, rygli czy kurtyn bezpieczeństwa nie stanowią już problemu. Urządzenia te mogą być dodawane jako zdalne IO dla sterowników bezpieczeństwa lub realizować własne aplikacje.
Panele operatorskie
Dla zapewnienia przyjaznego środowiska komunikacji między człowiekiem a maszyną stosowane są panele operatorskie. Firma Turck oprócz standardowych paneli operatorskich oferuje także urządzenia z PLC. Dzięki temu jedno urządzenie zastępuje dwa. W topowej serii TX700 dostępne są warianty w pełni wykonane w stopniu ochrony IP67, specjalne wersje do zastosowania w branży spożywczej oraz modele do pracy w trudnych warunkach oświetleniowych. Atutem rozwiązań firmy Turck jest to, że niezależnie od tego, czy wybrany zostanie model w obudowie kompaktowej w postaci TBEN-Lx-PLC, czy któryś z paneli TX, klient może przez nie przesyłać dane bezpośrednio do chmury. Wszystkie te rozwiązania pozwalają tworzyć zakłady w duchu Przemysłu 4.0.
Podsumowanie
Maszyny modułowe i rozproszona logika pozwalają na szybszą reakcję i modernizację systemów automatyki. Jeżeli przedsiębiorstwo chce mieć możliwość ciągłego rozwoju wraz z zachowaniem optymalizacji procesów i kosztów, to opisywane podejście jest najlepszym dostępnym rozwiązaniem. Zmiany mogą następować niezależnie, ponieważ moduły z wbudowaną logiką mogą także pracować jako standardowe zdalne IO. Podzielenie logiki pozwala skracać czas cyklu oraz realizować dodatkowe zadania. Przyszłość należy do maszyn modułowych.
TURCK Sp. z o.o.
ul. Wrocławska 115
45-836 Opole
tel. 77 443 48 00, fax 77 443 48 01
e-mail: poland@turck.com
www.turck.pl
źródło: Autmatyka 12/2020
Komentarze
blog comments powered by Disqus