Profesjonalna kontrola jakości wyrobów. Usługi skanowania 3D w PIAP
Maciej Cader drukuj
Proces pozyskiwania chmury punktów geometrycznych w przestrzeni trójwymiarowej (skanowane 3D) to w dzisiejszych czasach nic nadzwyczajnego. Na rynku dostępne są przeróżne skanery 3D, których cena rozpoczyna się już od 2000 zł. To czym tak naprawdę firmy zajmujące się skanowaniem 3D ze sobą konkurują, to oprogramowanie realizujące postprocessing, czyli operacje na pozyskanej chmurze punktów.
Nie jest tajemnicą ani wielkim odkryciem, że na rynku bezwzględny prym w dziedzinie skanowania 3D wiedzie niemiecka firma GOM, której produkty zakupił Przemysłowy Instytut Automatyki i Pomiarów PIAP, m.in. do prowadzenia profesjonalnej kontroli jakości swoich wyrobów. Duże doświadczenie zespołu PIAP pozwala także na oferowanie wysokiej jakości usług komercyjnych dla innych podmiotów gospo-
darczych.
Analiza odchyłek geometrycznych
Laboratorium Szybkiego Prototypowania i Obliczeń Numerycznych PIAP realizuje usługi precyzyjnego skanowania 3D, czyli pozyskiwania geometrii rzeczywistego obiektu, która może być wykorzystana do kontroli jakości, jak również do druku 3D lub obróbki skrawaniem. Jedną z usług realizowanych w laboratorium jest m.in. analiza odchyłek geometrycznych. Upraszczając, analizę przeprowadza się przez nałożenie punktów pomiarowych (chmury punktów) zeskanowanego modelu na geometrię modelu w programie CAD. To tak, jakby za pomocą współrzędnościowej maszyny pomiarowej zrealizować pomiary w kilkudziesięciu milionach punktów badanego modelu. W efekcie, po automatycznym oszacowaniu dokładności samego procesu skanowania, operator może wygenerować wizualizację odchylenia geometrycznego w zadanej postaci, np. w postaci ogólnej mapy odchyłek (rys. 1) lub uzyskując odpowiedzi „TAK/NIE” na pytanie, w których miejscach geometria mieści się w zadanym polu tolerancji, a w których nie.
Oprogramowaniu ma wbudowanych wiele opcji pośrednich, tj. ułatwiających wizualizację odchyłek. Jedną z bardziej przydatnych jest wizualizacja odchylenia geometrycznego powierzchni zewnętrznych części we wskazanej płaszczyźnie przekroju. Równie przydatną opcją jest możliwość dopasowania chmury punktów do modelu CAD skanowanej części, względem jej wybranego detalu geometrycznego – np. wybranej płaszczyzny, powierzchni, otworu itp. Wówczas odchyłka dla detalu wynosi 0 jednostek, a pozostałe odchyłki są odniesione do położenia chmury punktów dopasowanej do wspomnianego detalu części.
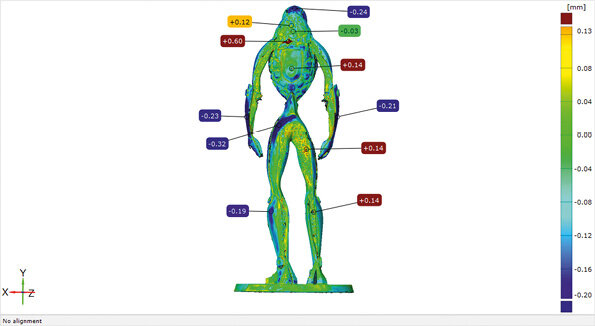
Rys. 1. Analiza odchyłek geometrycznych dla modelu figurki, mapa odchyłek geometrycznych rzeczywistego zeskanowanego obiektu modelu względem modelu CAD (po prawej)
Uśrednianie pomiarów
Uśrednianie chmur punktów może być wykorzystywane w trzech odrębnych zagadnieniach: uśrednianie wartości z n pomiarów, analizę trendu oraz analizę odkształceń części w stanach statycznych dla n prób. Dzięki tej opcji możliwe jest porównywanie n skanów wykonanych na n obiektach geometrycznie podobnych. Jest to opcja, która może być wykorzystywana np. do badania jakości wybranej losowo partii części z danej serii produkcyjnej. Zbuforowane skany nakłada się na siebie używając odpowiednich referencji geometrycznych. Po ich nałożeniu oprogramowanie może wyznaczyć geometrię uśrednioną przez najlepsze dopasowanie chmur punktów i automatycznie wykonać analizę np. odchylenia standardowego. Ta opcja umożliwia także badanie trendu. Po nałożeniu na siebie n skanów wybranej partii części, możliwe jest zbadanie trendów wymiarowych, np. wymiarów wybranych detali geometrycznych badanej części (wałków, otworów, powierzchni itp.). Punkty krzywej (rys. 2) to kolejne wartości zmierzonej średnicy nominalnej otworu w 10 kolejnych skanach (stąd 10 punktów). W tabeli na rys. 2 znajdują się: wartość nominalna (Nominal), wartość średnia (Avg), odchyłkę (Sigma), wartość minimalna (Min) oraz maksymalna (Max). W prezentowanym przypadku wartości te zostały określone dla skanu (dla części) nr 8 z serii 10 zeskanowanych punktów, co jest zobrazowane prostą pionową przecinającą punkt nr 8 na wykresie. Analiza trendu zmian średnicy otworu, odbywa się w odniesieniu do geometrii referencyjnej, którą w prezentowanym przypadku jest geometria CAD badanego (zeskanowanego) modelu części.
Oprócz kontroli jakości partii produkcyjnej tą metodą w laboratorium PIAP wykonywane są precyzyjne pomiary odkształceń części maszyn w wyniku statycznego obciążenia. Wykonując skan nieobciążonej części zbierane są szczegółowe informacje geometryczne o jej stanie – część referencyjna. Następnie tę część poddaje się obciążeniom statycznym zgodnym z obciążeniem występującym podczas jej pracy. W ostatnim kroku skany części nieobciążonej (referencyjnej) oraz skany części obciążonej (odkształconej) nakładane są na siebie. Różnica geometryczna wskazuje synoptyki odkształceń części w wyniku poddania jej obciążeniom. Badanie to umożliwia analizę zużycia (lub powypadkową) części. Dzięki tej metodzie można badać stopień degradacji maszyny. Na rys. 3 pokazano wynik testu przeprowadzonego na modelu szczęki chwytaka robota mobilnego. Przeprowadzone ww. metodą badanie dostarczyło szczegółowych informacji o odkształceniach części w wyniku działania siły pochodzącej od masy ładunku podnoszonego przez robota.
Jak to działa?
Skanery dostępne w Instytucie PIAP służą do prowadzenia precyzyjnych pomiarów bezdotykowych i niezależnych od właściwości materiału, w stanie statycznym. Pomiar (skanowanie 3D) geometrii odbywa się na podstawie automatycznej analizy efektu zniekształcenia linii niebieskiego światła (światła strukturalnego) oświetlającego powierzchnię skanowanego obiektu podczas procesu skanowania. Prążki światła niebieskiego o różnych grubościach są generowane przez projektor zintegrowany w obudowie skanera.
Powierzchnie poszczególnych części są naświetlane światłem o określonych parametrach, a linie proste ulegają zniekształceniu w zależności od jej ugięć. Obraz oświetlonego przedmiotu odczytywany jest przez dwie kamery i przesyłany do jednostki monitorująco-obliczeniowej. Uproszczony schemat stanowiska przedstawiono na rys. 4. Aby jednostka monitorująco – skanująca mogła złożyć kilka obrazów skanowanych, np. podczas skanowania części o znacznie większych wymiarach niż dostępne przestrzenie pomiarowe, wymagane jest oklejenie skanowanego obiektu punktami referencyjnymi (markerami). Są one niezbędne do łączenia geometrii pozyskanej w kilku procesach skanowania lub do określania odchyłek geometrii skanowanej (obciążonej zdeformowanej) względem geometrii wzorcowej (nieobciążonej niezdeformowanej). Wielkość punktów pomiarowych zależy od wielkości obszaru pomiarowego, ten z kolei zależy od zastosowanej optyki (obiektywów kamer i projektora). Skanowane części znajdują się w punkcie centralnym (rys. 4) obszaru pomiarowego.
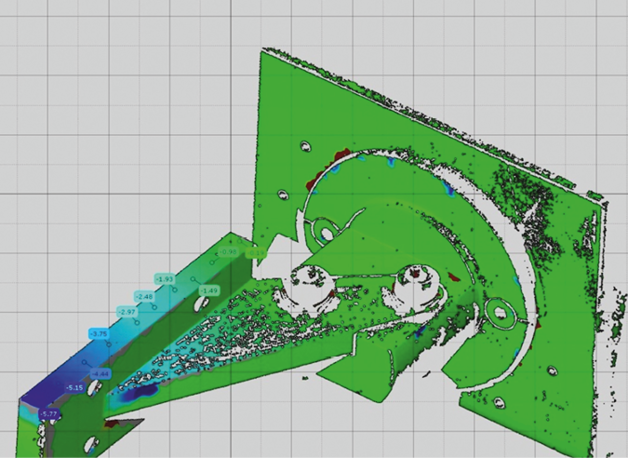
Rys. 3. Uśredniona wartość ugięcia szczęki chwytaka robota, pod wpływem obciążenia statycznego, podana w mm
Systemy ATOS dostępne w PIAP charakteryzują się następującymi parametrami, mającymi bezpośredni wpływ na proces skanowania:
- stereoskopowy układ kamer współpracujący z projektorem, które umożliwiają rejestrację trzech widoków skanowanego przedmiotu w ramach jednego pomiaru; rozdzielczość każdej z kamer wynosi 5 milionów pikseli,
- kąt triangulacyjny (kąt kamery) mieści się w przedziale 25–35°,
- czas wykonania jednego pomiaru (naświetlenia) nie przekracza 2 s (dla trzech widoków z kamer),
- I obszar pomiarowy o wymiarach 320×240 mm. Dopuszczalna rozbieżność wielkości obszaru pomiarowego wynosi ±5%, a min. dokładność 0,015 mm,
- II obszar pomiarowy o wymiarach 700×530 mm. Dopuszczalna rozbieżność wielkości obszaru pomiarowego wynosi ±5%, a min. dokładność 0,035 mm,
- III obszar pomiarowy (dla skanera ATOS CORE) o wymiarach 80×60 mm. Dopuszczalna rozbieżność wielkości obszaru pomiarowego wynosi ±5%, a min. dokładność 0,006 mm,
- projektor pracuje w technologii LED, z zastosowaniem źródła światła o fali w zakresie od 450 do 500 nm.
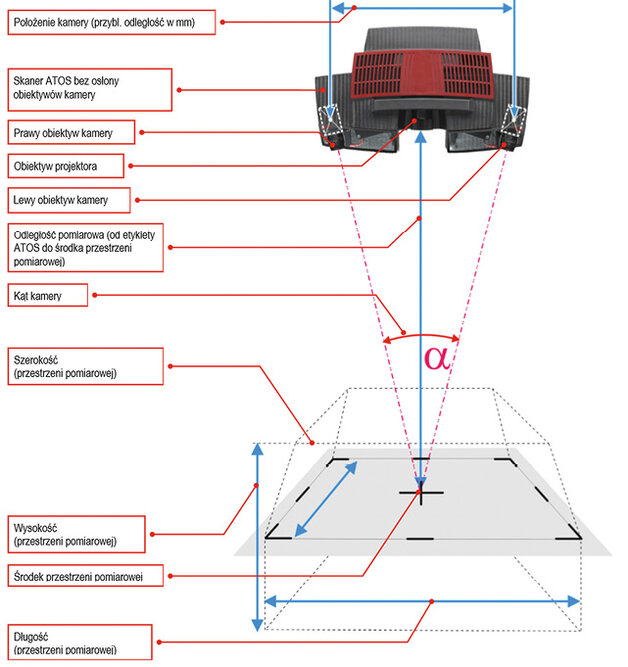
Rys. 4. Schemat stanowiska do skanowania przy wykorzystaniu systemu ATOS (na podstawie Instrukcji systemu ATOS opracowanej przez GOM GmbH)
Podsumowanie
Laboratorium Szybkiego Prototypowania i Obliczeń Numerycznych Przemysłowego Instytutu Automatyki i Pomiarów PIAP realizuje badania naukowe przy wykorzystaniu najnowocześniejszej aparatury i systemów numerycznych. Doświadczenia zdobyte w wyniku prowadzonych badań przełożyły się na ofertę komercyjną w zakresie:
- precyzyjnego skanowania 3D, w tym pozyskiwania i naprawy geometrii 3D części/obiektów,
- kontroli jakości i analizy trendów,
- bezkontaktowego badania powypadkowego zdeformowanych części,
- analiza stanów statycznych,
- druku 3D części maszyn z ultrawytrzymałych polimerów realizowanego na podstawie geometrii pozyskanej bezpośrednio (tj. z pominięciem inżynierii odwrotnej) z procesu skanowania 3D.
Instytut PIAP zaprasza do współpracy.
Przemysłowy Instytut Automatyki i Pomiarów PIAP
PIAP design
Al. Jerozolimskie 202, 02-486 Warszawa
e-mail: design@piap.pl
www.design.piap.pl
źródło: Automatyka 12/2016
Komentarze
blog comments powered by Disqus