Wyłączniki i czujniki bezpieczeństwa
dr inż. Marcin Bieńkowski drukuj
Szeroko rozumiane bezpieczeństwo pracy, zarówno ludzi, jak i maszyn, to kluczowy warunek, jaki nakładają na przedsiębiorstwo regulacje prawne, czynniki ekonomiczne i po prostu zdrowy rozsądek. Wymogi te ciągle się zaostrzają, a poprawie bezpieczeństwa sprzyjają coraz lepsze technologie i systemy zabezpieczeń. Równie ważne jest doskonalenie procedur związanych z bezpieczeństwem pracy i zarządzaniem produkcją. Niemniej jednak jednym z najpopularniejszych i skutecznych rozwiązań wpływających na wzrost bezpieczeństwa są tzw. wyłączniki bezpieczeństwa, określane również wyłącznikami awaryjnymi. Ich dobór podyktowany jest najczęściej przeznaczeniem, a działanie określają wykorzystane w nich technologie.
Eliminacja potencjalnych zagrożeń i zapobieganie wypadkom związanym z działaniem maszyn i urządzeń wpływa bezpośrednio na efektywne funkcjonowanie zakładu. Ograniczone zostają wydatki związane z odszkodowaniami i opieką medyczną dla ofiar wypadków oraz koszty związane z nieplanowanymi przestojami. Bezpośrednie przełożenie na wydajność produkcji i ekonomikę funkcjonowania przedsiębiorstwa ma również większa odporność maszyn i urządzeń na błędy ludzkie, co z kolei odpowiada bezpośrednio za skrócenie sumarycznego czasu nieplanowanych przestojów. Wydłuża się również czas bezawaryjnej pracy całego systemu i poszczególnych linii produkcyjnych.
Z bezpieczeństwem systemów przemysłowych związane jest również pojęcie bezpieczeństwa funkcjonalnego. Pojęcie to odnosi się do systemu sterowania, którego jakość działania zależy od prawidłowego funkcjonowania elementów realizujących poszczególne, założone przez projektantów funkcje bezpieczeństwa, a także od zewnętrznych urządzeń i czujników zmniejszających ryzyko wystąpienia zagrożeń. Do tego typu zewnętrznych systemów bezpieczeństwa zalicza się wyłączniki bezpieczeństwa, czujniki elektromechaniczne, wyłączniki linkowe, optyczne kurtyny świetlne, a także maty bezpieczeństwa oraz urządzenia nazywane sterownikami bezpieczeństwa.
Klasyfikacja zagrożeń
Zagrożenia występujące w przemyśle klasyfikuje się ze względu na stopień ich uciążliwości i ze względu na ich charakter. Warto zauważyć, że praca w warunkach uciążliwych nie stwarza sama w sobie bezpośredniego ryzyka doznania urazu, ale w istotny sposób utrudnia wykonywanie obowiązków i powoduje znacznie szybsze zmęczenie pracownika. Jeśli zaś chodzi o czynniki szkodliwe, to mogą one wywoływać choroby zawodowe lub osłabiać reakcję na niebezpieczne bodźce, co z kolei może doprowadzić do wypadku.
Największym zagrożeniem dla bezpieczeństwa, jak nietrudno się domyślić, są różnego rodzaju czynniki i warunki niebezpieczne. Ich oddziaływanie pojawia się zazwyczaj nagle i mogą one być przyczyną poważnych urazów, zatruć, a w skrajnym przypadku mogą nawet doprowadzić do śmierci pracownika. To właśnie takie niespodziewanie pojawiające się warunki niebezpieczne, przed którymi trzeba koniecznie zabezpieczyć pracownika, są z punktu widzenia wdrażania systemów bezpieczeństwa najistotniejszym elementem.
Jeśli chodzi o klasyfikację, zagrożenia szkodliwe oraz uciążliwe dzieli się na cztery główne grupy. Pierwszą z nich są czynniki fizyczne, np. mechaniczne, związane z odpryskami czy opiłkami metalu powstającymi podczas obróbki skrawaniem. Do drugiej grupy zalicza się warunki psychofizyczne, które bezpośrednio są związane z kondycją i koncentracją człowieka, np. zmęczeniem czy hałasem. Dwie kolejne grupy to zagrożenia chemiczne oraz biologiczne. Do zagrożeń chemicznych zalicza się kontakt pracownika z niebezpiecznymi materiałami chemicznymi, które mogą być zarówno surowcem, produktem, jak i odpadem bądź produktem ubocznym prowadzonego procesu technologicznego. Jeśli chodzi o zagrożenia biologiczne, możemy mieć do czynienia z mikroorganizmami, takimi jak grzyby, wirusy czy bakterie.
Dyrektywa maszynowa
Z punktu widzenia wdrażania systemów bezpieczeństwa i stosowania w nich odpowiednich czujników, istotnym zagadnieniem, o którym trzeba koniecznie wspomnieć są przepisy zawarte w tzw. dyrektywie maszynowej. Zgodnie z obowiązującym w UE prawem, wszystkie maszyny wprowadzane do sprzedaży na rynku europejskim muszą być bezpieczne, niezależnie od tego, czy są to urządzenia stare czy nowe. Podstawowe wymagania dla wytwórców maszyn i użytkowników systemów, którzy sami budują i modyfikują maszyny, zostały zdefiniowane i opisane w odpowiednich dyrektywach, w tym we wspomnianej dyrektywie maszynowej 2006/42/WE oraz we wprowadzających je przepisach krajowych. W przypadku Polski podstawowym aktem prawnym jest Rozporządzenie Ministra Gospodarki w sprawie zasadniczych wymagań dla maszyn, opublikowane w Dz. U. Nr 199 Poz. 1228 z dnia 21 października 2008 r.
Wspomniane przepisy określają zasadnicze wymagania w zakresie bezpieczeństwa i ochrony zdrowia, dotyczące projektowania i wykonywania wprowadzanych do obrotu lub oddawanych do użytku maszyn, wyposażenia wymiennego, elementów bezpieczeństwa, osprzętu do podnoszenia, łańcuchów, lin, pasów, odłączalnych urządzeń do mechanicznego przenoszenia napędu, a także maszyn nieukończonych. W przepisach określono też procedury oceny zgodności oraz sposoby oznakowania maszyn, a także wzór znaku CE.
Z Rozporządzenia Ministra Gospodarki z 2008 r. wynika, że producent lub jego upoważniony przedstawiciel, działający na terenie Unii Europejskiej, ma obowiązek przeprowadzenia oceny ryzyk mających zastosowanie do danego urządzenia lub maszyny w celu określenia zasadniczych wymagań związanych z bezpieczeństwem i ochroną zdrowia. Maszyny i urządzenia powinny być zaprojektowane i wykonane z uwzględnieniem wyników tej oceny. Układy sterowania należy zaprojektować i wykonać tak, aby zapewniały bezpieczeństwo oraz zapobiegały powstawaniu sytuacji zagrożenia, a defekty sprzętu komputerowego i oprogramowania układu sterowania nie prowadziły do powstawania sytuacji niebezpiecznych.
Sterowanie musi być też odporne na obciążenia wynikające z zamierzonego zastosowania i wpływy czynników zewnętrznych, a błędy w układach logicznych nie mogą powodować sytuacji niebezpiecznych. Istotne jest też to, aby uwzględniać wszelkie możliwe do przewidzenia błędy ludzkie, które mogą się pojawić w trakcie pracy urządzenia. Konstrukcja maszyny, systemu automatyki, linii technologicznej, infrastruktury i gniazd technologicznych musi zagwarantować, by maszyna czy urządzenie nie mogły się w sposób nieoczekiwany uruchomić, a parametry – zwłaszcza te wpływające bezpośrednio na bezpieczeństwo – nie zmieniały się w sposób niekontrolowany.
Po wydaniu polecenia zatrzymania maszyna, urządzenie lub linia muszą się zatrzymać, a żadna ruchoma część ani zamocowany element nie mogą odpaść lub zostać wyrzucone, ponieważ stwarzałoby to zagrożenie zranienia czy pozbawienia życia pracownika. Automatyczne lub ręczne zatrzymywanie części ruchomych nie może zostać zakłócone. Istotne jest też to, aby elementy systemu bezpieczeństwa zapewniały skuteczną ochronę lub wysyłały polecenie zatrzymania, a elementy układu sterowania związane z bezpieczeństwem działały w sposób spójny w całym zespole maszyn, linii technologicznych, gniazd lub maszyn nieukończonych.
Maszyna spełniająca wymienione kryteria musi legitymować się specjalnym oświadczeniem producenta, tzw. Deklaracją zgodności, stwierdzającą na jego wyłączną odpowiedzialność, że wyrób, proces wytwórczy lub usługa są zgodne z określoną normą lub innym dokumentem normatywnym.
Układy sterowania
Elementem nadrzędnym dla systemu bezpieczeństwa jest układ sterowania, którego zadaniem jest połączenie poszczególnych elementów systemu bezpieczeństwa w funkcjonalną całość. Wyróżnia się cztery podstawowe grupy systemów:
- maszyny i urządzenia z lokalnym systemem sterowania, który realizuje funkcje bezpieczeństwa w oparciu o przekaźniki bezpieczeństwa,
- maszyny lub urządzenia z lokalnym albo globalnym systemem sterowania wykorzystującym programowalne przekaźniki bezpieczeństwa,
- maszyny oraz systemy z rozproszonymi czujnikami bezpieczeństwa i elementami wykonawczymi wykorzystującymi przemysłowe systemy transmisji danych,
- maszyny, urządzenia lub linie sterowane globalnie z rozbudowanymi funkcjami bezpieczeństwa.
W większości maszyn i systemów przemysłowych wystarczają podstawowe, lokalnie zaimplementowane funkcje bezpieczeństwa, które odnoszą się do takich zdarzeń, jak stop awaryjny, kontrola osłony barier i kurtyn świetlnych, sterowanie dwuręczne, kontrola mat naciskowych, prędkości, stanu zatrzymania. Początkowo, do końca lat 80. ubiegłego wieku, w tym celu stosowano kombinację przekaźników i styczników. W przypadku wystąpienia niebezpiecznej sytuacji, element wykonawczy był po prostu izolowany od źródła energii. Niestety tego rodzaju układ mógł być łatwo odłączony, ulec awarii lub zostać przypadkowo ominięty (np. skleiły się styki stycznika), co sprawiało, że maszyna pozbawiona była funkcji bezpieczeństwa, ale jej praca wciąż była możliwa.
Rozwiązaniami, które miały ograniczyć sytuacje, gdy maszyna czy linia produkcyjna pozbawiona byłaby przypadkowo lub celowo (sic!) funkcji ochrony, stały się specjalne obwody przekaźników. Wykorzystywano tu m.in. kombinacje trójstykowe czy kaskadowe, gdzie do istniejącego stycznika równolegle dołączano drugi, a napięcia sterujące elementami wykonawczymi doprowadzano szeregowo przez styki obydwu styczników.
Rozwój tego typu systemów doprowadził do skonstruowania na początku lat 90. pierwszego przekaźnika bezpieczeństwa, za który uznaje się przekaźnik PNOZ niemieckiej firmy Pilz. Warto zwrócić w tym miejscu uwagę na fakt, że przekaźniki bezpieczeństwa muszą być zaprojektowane w taki sposób, aby zarówno błąd urządzenia, jak i usterka spowodowana przyczyną zewnętrzną, np. czujnikiem lub elementem wykonawczym nie powodowały ograniczenia funkcji bezpieczeństwa, oczywiście pod warunkiem prawidłowego ich podłączenia.
Obecnie do prostej implementacji funkcji bezpieczeństwa w maszynach czy na liniach produkcyjnych stosuje się dość proste przekaźniki bezpieczeństwa, takie jak urządzenia wspomnianej firmy Pilz: PNOZcompact, PNOZpower, PNOZelog czy bardzo popularne przekaźniki Siemens SIRIUS 3SK1 lub SIRIUS 3RM1. Co ciekawe, ten ostatni to układ hybrydowy pełniący jednocześnie funkcję sterowania i przekaźnika bezpieczeństwa. Przekaźniki tego typu umożliwiają szybką i prostą realizację podstawowych, wymienionych wcześniej funkcji bezpieczeństwa i nie wymagają od użytkownika umiejętności programistycznych.
Programowalne przekaźniki bezpieczeństwa
Obecnie do nieco bardziej skomplikowanych zadań wykorzystuje się programowalne przekaźniki bezpieczeństwa. Dobrym przykładem mogą być urządzenia SIRIUS 3SK2 i PNOZmulti. Pozwalają one użytkownikom na swobodne definiowanie zadań i samodzielne zaprogramowanie sterujących nimi algorytmów. Innymi słowy, przekaźniki programowalne pozwalają na znaczne uproszczenie projektowanej aplikacji i zmniejszenie liczby przekaźników bezpieczeństwa w systemie, które realizują tylko pojedyncze zadania, a co za tym idzie, na obniżenie całkowitych kosztów instalacji systemu bezpieczeństwa. Warto zwrócić uwagę, że do standardowych funkcji monitoringu realizowanych przez przekaźniki programowalne należą: kontrola zatrzymania awaryjnego, kontrola przesunięcia/wychylenia/obrotu, kontrola mat czujnikowych, kontrola kurtyn świetlnych czy kontrola łączników lub rygli.
Bardziej zaawansowane przekaźniki bezpieczeństwa, np. Schneider Electric XPS MC32ZP czy Omron NX, oferują rozbudowaną diagnostykę, sporą liczbę wejść (zwykle od 8 do 32, niekiedy nawet do 256) oraz parametryzację. W większości przypadków istnieje możliwość przyłączenia ich do nadrzędnego systemu automatyki (np. przez Profibus lub Profinet), w tym do systemów wizualizacji czy interfejsów HMI. Dzięki temu możliwa jest realizacja rozbudowanych aplikacji wykorzystujących wiele funkcji bezpieczeństwa – np. muting dla kurtyn świetlnych, monitorowanie osłon, z i bez funkcji ryglowania, jak również realizacja funkcji stop awaryjny. Dzięki modułowej i rozszerzalnej konstrukcji tego typu przekaźnika można stopniowo rozbudowywać system w celu elastycznego dostosowania go do wykonywanych zadań, aż do osiągnięcia najwyższego poziomu bezpieczeństwa.
Sterowniki bezpieczeństwa
Oddzielną grupą urządzeń bezpieczeństwa są sterowniki. Sterownik bezpieczeństwa to, najprościej rzecz ujmując, specjalizowany sterownik PLC, nazywany też sterownikiem safety PLC, w którym zaimplementowane są specjalne certyfikowane bloki programowania służące do obsługi podstawowych urządzeń stosowanych w technice bezpieczeństwa. Podstawową różnicą między sterownikami bezpieczeństwa a standardowymi sterownikami PLC jest ich konstrukcja. Urządzenia bezpieczeństwa bazują na redundantnej architekturze, w której sygnały wejściowe i wyjściowe analizowane są w dwóch oddzielnych torach. Taka konstrukcja pozwala na zachowanie bezpieczeństwa w przypadku, gdy jeden z kanałów funkcjonuje niepoprawnie lub mamy do czynienia z różnicą sygnałów wejściowych na obu kanałach.
Sterowniki bezpieczeństwa wyposażone są w co najmniej dwa procesory analizujące i porównujące sygnały. Inną cechą takiego sterownika jest wzajemne monitorowanie stanu pracy przez procesory. Tego typu architekturę stosuje się po to, aby zapewnić jak największą niezawodność działania maszyny czy linii produkcyjnej, a w przypadku awarii – aby je zatrzymać lub zapewnić bezpieczny stan urządzenia. Analiza sygnałów nie jest skomplikowana i jest znacznie prostsza niż w przypadku standardowych sterowników PLC. Z wyjątkiem najnowszych, eksperymentalnych rozwiązań, gdzie wprowadza się algorytmy sztucznej inteligencji i uczenia maszynowego, nie ma tutaj mowy o skomplikowanych algorytmach. Realizacja programu ogranicza się zazwyczaj do porównania faktycznych stanów z urządzeń wejściowych (różnych czujników bezpieczeństwa, kurtyn świetlnych, wyłączników E-stop) do stanów, które zostały zapisane w pamięci urządzenia i ewentualnej analizy odchyleń w sytuacjach niestandardowych.
Cechą, która odróżnia sterownik bezpieczeństwa od sterownika PLC jest dostęp do funkcji programowania i kontrola wprowadzanych zmian. Podobnie jak w przypadku systemów IT, dostęp do funkcji programowania zabezpieczony jest hasłem, a oprogramowanie sterujące korzysta z sum kontrolnych, które zmieniają się w chwili wprowadzenia jakiejkolwiek modyfikacji w ustawieniach urządzenia. Co więcej, zmiany te zawsze rejestrowane są w logach, które można w dowolnej chwili przejrzeć. Tego typu mechanizmy mają za zadanie zabezpieczyć system przed nieautoryzowanymi zmianami programu realizowanego przez sterownik, a tym samym zwiększyć bezpieczeństwo maszyny. Ciekawą opcją w nowoczesnych sterownikach bezpieczeństwa jest możliwość nie tyle samego przeglądania logów, ale generowania na ich podstawie raportów dotyczących zdarzeń i zmian w projekcie bezpieczeństwa.
Sterowniki bezpieczeństwa stosowane są wszędzie tam, gdzie wymagany jest wyższy poziom niezawodności aplikacji i monitorowana jest większa liczba funkcji bezpieczeństwa, czyli tam, gdzie stosowanie jednofunkcyjnych przekaźników bezpieczeństwa, w tym przekaźników programowalnych, staje się nieopłacalne. Wpływ na stosowanie sterowników bezpieczeństwa ma też konieczność komunikacji z innymi elementami układu sterowania, w tym ze standardowymi sterownikami PLC, panelami HMI czy globalnym systemem sterowania całą linią produkcyjną lub przemysłową infrastrukturą IT. Nawet najprostsze programowalne sterowniki bezpieczeństwa oferują dziś wymianę danych, korzystając z najpopularniejszych przemysłowych standardów komunikacyjnych, jak EtherNet/IP, Profibus, Profinet, Modbus/TCP, EtherCAT, CC-Link i innych.
Co ważne, większość dostępnych na rynku sterowników bezpieczeństwa to urządzenia, które można rozbudować. Modułowa konstrukcja z podziałem na jednostkę główną oraz moduły rozszerzeń pozwala na elastyczne budowanie systemu bezpieczeństwa dla całych linii technologicznych, które mogą być zarządzane z jednego centralnego punktu, z opcją rozproszenia funkcji bezpieczeństwa. Dodanie nowych modułów pozwala uzyskać nie tylko dodatkowe bezpieczne wejścia i wyjścia, ale także umożliwia na dołożenie specyficznych dla danej aplikacji funkcji. Zostawmy jednak sterowanie na boku i przejdźmy do urządzeń wykonawczych, czyli wyłączników i czujników bezpieczeństwa.
Elektromagnetyczne czujniki bezpieczeństwa
Czujniki bezpieczeństwa są stosowane w najróżniejszych obszarach związanych z bezpieczeństwem maszyn i produkcji. Dobrym przykładem jest otwarcie osłon maszyny, które powinno skutkować zatrzymaniem niebezpiecznych ruchów podzespołów maszyny, a jednocześnie uniemożliwić jej ponowne uruchomienie. Oczywiście nie wolno dopuszczać do omijania ani nieuprawnionego manipulowania osłonami. Niektóre aplikacje wymagają również zablokowania drzwi ochronnych aż do zakończenia niebezpiecznego procesu produkcyjnego. Podobnie ma się sytuacja z wtargnięciem człowieka w obszar działania robota przemysłowego. Robot musi być wówczas natychmiast zatrzymany.
Najczęściej stosowanymi w przemyśle czujnikami bezpieczeństwa są czujniki elektromagnetyczne, bezdotykowe. Działanie tego rodzaju czujników polega na wykorzystaniu zjawiska magnetyzmu i indukcji magnetycznej. Służą one przede wszystkim do monitorowania położenia osłon stosowanych w maszynach, bramek w ogrodzeniach bezpieczeństwa, drzwi oraz pokryw rolowanych – wszystko zgodnie z wymaganiami normy PN-EN 60947-5-3. Co ważne, czujniki tego typu z powodzeniem mogą być używane również do monitorowania pozycji przesuwnych, uchylnych i zdejmowanych osłon ochronnych dowolnych urządzeń szafek sterujących. Można je także wykorzystać do standardowego monitorowania położenia elementów ruchomych. Bardzo często są to te same czujniki, które wykorzystuje się w systemach sterowania automatyki, ale charakteryzują się nieco inną, bardziej odporną na czynniki zewnętrzne budową, ze względu na zadania, jakie wykonują.
Oprócz kontroli zamknięcia osłon czy innych elementów stref bezpieczeństwa, elektromagnetyczne czujniki bezpieczeństwa mogą być stosowane tam, gdzie wymaga się wysokich standardów dotyczących higieny – np. w przemyśle spożywczym, opakowaniowym lub farmaceutycznym. Wiele modeli, zwłaszcza wykorzystujących obudowy ze stali nierdzewnej, jest dopuszczonych do użytku w obszarach zagrożonych wybuchem, zgodnie z dyrektywą ATEX.
Elektromagnetyczne czujniki bezpieczeństwa zapewniają bezkontaktową, bezpieczną rejestrację zarówno pozycji, jak i położenia krańcowego monitorowanych obiektów istotnych ze względu na bezpieczeństwo pracującej maszyny. Charakteryzują się odległością przełączania wynoszącą, w zależności od modelu, 2–10 mm. Najczęściej urządzenia tego typu pochwalić się mogą również stopniem ochrony IP65 lub IP67 i dużą wytrzymałością w przypadku ekstremalnie wysokiej lub niskiej temperatury. Są też trwałe pod względem mechanicznym, dzięki sporej odporności na wibracje i uderzenia. Warto zauważyć, że w sprzedaży dostępne są modele zarówno z komunikacją przewodową, jak i bezprzewodową, co pozwala dostosować je do zadań w konkretnej aplikacji.
Bariery i kurtyny świetlne
Drugim z najczęściej stosowanych w przemyśle rozwiązań bezpieczeństwa są kurtyny oraz bariery świetlne. Pozwalają one zabezpieczyć potencjalnie niebezpieczną strefę, np. wspomniane wcześniej zrobotyzowane gniazdo obróbcze czy obszar roboczy prasy hydraulicznej przed wtargnięciem człowieka lub włożeniem przez niego rąk czy palców w przestrzeń, w której wykonywane są operacje produkcyjno-technologiczne.
Podstawową różnicą między kurtynami świetlnymi i barierami jest to, że bariery świetlne emitują tylko kilka do kilkunastu promieni, zaś kurtyny od kilkunastu do kilkudziesięciu, a nawet kilkuset wiązek światła, tworząc większą przestrzeń ochronną. Zasada działania obu typów urządzeń jest praktycznie taka sama. Szczegółowe wymagania dotyczące barier i kurtyn świetlnych określa norma PN-EN 61496-1:2014-02 – Bezpieczeństwo maszyn – Elektroczułe wyposażenie ochronne – Część 2: Wymagania szczegółowe dotyczące wyposażenia wykorzystującego aktywne optoelektroniczne urządzenia ochronne (AOPD).
Bariery świetlne jako proste czujniki bezpieczeństwa stosuje się przede wszystkim do nadzorowania niebezpiecznych stref w otoczeniu maszyn, gniazd oraz linii produkcyjnych. Tworzą one niewidoczną barierę, po przekroczeniu której włączany jest alarm, a maszyna zostaje zatrzymana. Wykorzystuje się je też jako zabezpieczenie wejścia do zautomatyzowanych przestrzeni magazynowych czy stref zagrożonych wybuchem. Bariery świetlne chroniące daną strefę mogą mieć od jednego do kilku promieni, w zależności od potrzeb określonych w ramach analizy ryzyka.
Kurtyny świetlne, jako urządzenia dysponujące szeregiem wiązek światła, które mogą być umieszczone na listwie nawet co kilka milimetrów, stosowane są najczęściej do nadzorowania strefy, która bezpośrednio przylega do obszaru roboczego maszyny. Monitorują przekroczenie tej strefy w niewielkim obszarze, chroniąc w ten sposób pracownika np. przed przypadkowym włożeniem rąk w obszar roboczy prasy lub dłoń operatora przed sięgnięciem w strefę działania ostrzy struga stolarskiego.
Kurtyny świetlne mają przeważnie postać listew, jednej z diodami laserowymi, drugiej z czujnikami. Można je montować zarówno w pionie, jak i poziomie. Montowane pionowo wykrywają m.in. czy wspomniana ręka operatora została wsunięta w strefę zagrożenia. Taki układ kurtyn jest powszechnie stosowany w maszynach obsługiwanych ręcznie. Montaż kurtyny w poziomie zapewnia detekcję powierzchni przed niebezpiecznym ruchem maszyny.
Jak wspomniano, bariery składają się z dwóch głównych elementów – nadajnika i odbiornika światła. Najczęściej stosowane są równoległe wiązki promieniowania podczerwonego. Wiązki te modulowane są ze ściśle określoną częstotliwością, a odbiornik jest czuły tylko na wiązki wysyłane przez nadajnik, który ma ściśle określone parametry. Dzięki temu inne źródła światła nie zakłócają prawidłowego działania bariery. Dostępne na rynku bariery i kurtyny świetlne różnią się zestawem dostępnych funkcji i zastosowanej w nich technologii. Najważniejsze z nich to blanking, czyli funkcja umożliwiająca wyłączenie żądanych wiązek promieni. Opcja multiscanning umożliwia wielokrotną detekcję wiązki w ściśle określonej jednostce czasu. Jest to kolejny mechanizm pozwalający wyeliminować wpływ zewnętrznych źródeł światła.
Najważniejszym parametrem, zarówno barier, jak i kurtyn świetlnych jest czas reakcji. Określa on czas od chwili przerwania wiązki, aż do momentu reakcji, tj. zatrzymania maszyny. W standardowych rozwiązaniach zwykle wynosi on około 2 ms, co jest wystarczające, aby zapobiec nieszczęściu.
Warto też wspomnieć o funkcji muting. Pozwala ona na przejście obiektu o zdefiniowanych znanych wymiarach przez chronioną strefę bez uruchomienia alarmu. Dzięki temu można na przykład automatycznie dostarczać komponenty czy surowce do produkcji bez wszczynania alarmu, a maszyna zatrzymana zostanie dopiero w chwili wtargnięcia do chronionej strefy człowieka.
W wielu zastosowaniach istotna może być też funkcja pracy cyklicznej, pozwalająca uruchamiać kurtynę tylko na określony czas, skorelowany z działaniami maszyny – na technologiczny czas zatrzymania robota w chronionym obszarze zrobotyzowanego gniazda. W przypadku kurtyn oraz barier wielowiązkowych istotna może być też rozdzielczość, czyli odległość między promieniami świetlnymi – najczęściej jest to 14 mm, choć (jak już wspomniano) niektóre modele charakteryzują się rozdzielczością rzędu 2–5 mm.
Laserowe skanery bezpieczeństwa
Innym coraz częściej stosowanym zabezpieczeniem są laserowe skanery bezpieczeństwa. To urządzenia, które przypominają pod względem działania kurtyny świetlne, ale nie wymagają oddzielnej listwy z odbiornikami, gdyż ta jest zintegrowana z nadajnikiem. Wiązka laserowa wysłana z emitera poprzez system lusterek trafia na wirujące zwierciadło, które rozprowadza ją w określonej strefie. Promienie laserowe odbite od obiektu wracają do odbiornika. Lokalizacja wykrywanego obiektu odbywa się na zasadzie pomiaru czasu powrotu promieni oraz kąta padania wiązki względem odbiornika – jest to dokładnie ta sama zasada działania, jak w przypadku lidarów stosowanych w samochodach autonomicznych.
Laserowe skanery bezpieczeństwa wykorzystuje się jako kontrolę wejścia w strefę niebezpieczną, przede wszystkim w strefę działania robota przemysłowego. Wzorem samochodów autonomicznych służą też do kontroli przestrzeni wokół automatycznych wózków transportowych. Dlaczego są coraz chętniej stosowane? Otóż laserowe skanery bezpieczeństwa wykrywają obecność osoby zbliżającej się do obszaru nawet ze znacznej odległości. W ten sposób jeden skaner bezpieczeństwa może obejmować zasięgiem sporą część zrobotyzowanej hali fabrycznej. Co więcej, w przypadku wejścia do obszaru ostrzegawczego następuje kontrolowane wyhamowanie niebezpiecznych ruchów maszyny, a w przypadku wejścia pracownika już bezpośrednio do obszaru chronionego następuje jej zatrzymanie.
Dostępne w sprzedaży skanery laserowe pozwalają na obserwację obszaru w szerokim kącie widzenia dochodzącym do 190–275°. Skanery chronią strefę wokół siebie – zazwyczaj o promieniu 2–6 m, a w promieniu do 10–20 m definiują dodatkową strefę ostrzegawczą. W zależności od urządzenia możliwy jest jednoczesny monitoring od trzech do pięciu zdefiniowanych oddzielnych stref, a także możliwe jest łączenie kilku skanerów w system obejmujący całą halę.
Dywaniki i maty bezpieczeństwa
Ostatnim standardowo używanym typem czujników bezpieczeństwa są maty i dywaniki, które stosuje się bezpośrednio przy stanowiskach roboczych, miejscach kontrolnych i przejściach. Ich zaletą jest łatwość instalacji oraz wyraźne oznaczenie strefy ochronnej. Działanie mat bezpieczeństwa, w przeciwieństwie do zabezpieczeń optoelektronicznych, takich jak kurtyny i bariery świetlne, nie jest zakłócane przez dym lub opad drobnych ciał, np. wiórów w strefie ochrony. Urządzenia te charakteryzują się również brakiem reakcji na fałszywe sygnały wywoływane np. upadkiem drobnych przedmiotów. Mat i dywaników nie należy stosować tam, gdzie spadać mogą na nie przedmioty duże, ciężkie i ostre.
Zasada działania maty bezpieczeństwa jest wyjątkowo prosta. Mata składa się z dwóch przewodzących warstw, które oddzielone są od siebie separatorami. Wejście człowieka na matę sprawia, że pod jego ciężarem separatory zostają ściśnięte i dwie warstwy przewodzące stykają się ze sobą, powodując alarm i zatrzymanie maszyny. Maty i dywaniki różnią się od siebie wielkością obszaru detekcji. Dywaniki są znacznie mniejsze.
Każda mata musi charakteryzować się pełną zdolnością detekcji na całej przewidzianej do tego celu powierzchni – często jest to cala powierzchnia maty. Użyte do jej produkcji tworzywa muszą, co oczywiste, mieć wytrzymałą konstrukcję mechaniczną i być odporne na oleje, szczególnie, jeśli mata chroni obszar roboczy wokół maszyny do obróbki skrawaniem. Najważniejszymi parametrami maty są obszar detekcji oraz ciężar, jaki powoduje ściśnięcie separatorów, istotna też może być minimalna powierzchnia nacisku, wywołująca zadziałanie maty.
Maty stosuje się jako urządzenie lub dodatkowy system zabezpieczający służący do natychmiastowego zatrzymania maszyny. Kasowanie może odbyć się ręcznie lub automatycznie, w zależności od rodzaju aplikacji. Jeżeli istnieje jakiekolwiek ryzyko, że operator może przedostać się z maty w strefę zagrożenia, należy zawsze stosować kasowanie ręczne. W przypadku maty pełniącej rolę wtórnego zabezpieczenia, jej zadaniem jest uniemożliwienie ponownego uruchomienia maszyny, gdy ktoś znajduje się w strefie ochrony zasadniczej, czyli w strefie ryzyka. Bardzo często maty współpracują z kurtynami świetlnymi, które są głównym zabezpieczeniem, a mata chroni przed ponownym uruchomieniem maszyny, jeśli operator wciąż znajduje się w strefie ryzyka.
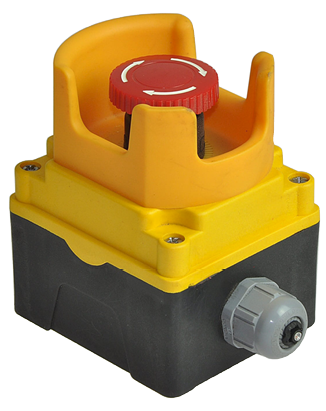
Wyłączniki bezpieczeństwa E-STOP mają charakterystyczną formę grzybka. Często montowane są w osłonach uniemożliwiajacych przypadkowe naciśnięcie
Awaryjne wyłączniki bezpieczeństwa
Najbardziej znanym typem awaryjnego wyłącznika bezpieczeństwa (wyłączników E-stop) są popularne grzybki. Wyłączniki te używane są jako ręcznie wyzwalane urządzenia stopu awaryjnego i charakteryzują się dużym czerwonym przyciskiem w kształcie grzybka, który jest dobrze widoczny na tle żółtej obudowy wyłącznika. Gdy wyłącznik zostanie naciśnięty, w określonym położeniu następuje jego zablokowanie, często nazywane „zatrzaśnięciem”. Zatrzaśnięcie to sprawia, że przycisk musi być ręcznie kasowany. Co ważne, czynność kasowania nie może się przyczynić do wywołania sytuacji niebezpiecznej, a reset przycisku może być wykonany przez jego obrót bądź wyciągnięcie. Tego typu wyłączniki awaryjne mogą występować w wersji z kluczykiem lub specjalnym kołnierzem zabezpieczającym, zapobiegającym przypadkowej ich aktywacji. Niektóre najnowsze modele wyłączników zatrzymania awaryjnego oferują funkcję samonadzorowania. Taki przycisk wyposażony jest w dodatkowy zestyk, którego zadaniem jest nadzorowanie, czy elementy z tyłu panelu wciąż znajdują się na swoich miejscach.
Wyłączniki grzybkowe dostępne są zarówno w wersjach panelowych, do montażu na panelach sterujących maszyn i urządzeń, jak i montowanych powierzchniowo. Oczywiście dostępne są specjalne wersje wyłączników umożliwiające ich użycie również w przypadku bardzo wymagających środowisk, w tym stref zagrożonych wybuchem, a więc w wersjach iskrobezpiecznych. Często wyłączniki grzybkowe są podświetlane, mogą być też wyposażone w widoczną z daleka diodę LED, co ma szczególne znaczenie w miejscach o dużym stopniu zapylenia. Dioda taka może dodatkowo pełnić funkcję informacyjną – gdy styki wyłącznika są zamknięte, dioda świeci na zielono, a w chwili zadziałania wyłącznika zaczyna migać na czerwono. Dodatkowym wzmocnieniem sygnału awaryjnego może być zastosowanie brzęczka z sygnałem dźwiękowym.
Do zatrzymywania awaryjnego maszyn służą również wyłączniki linkowe, które mogą być uruchamiane z dowolnego miejsca, przez które przebiega linka. W urządzeniach tego typu stosowana jest stalowa linka, którą przypina się do wyłącznika zatrzaskowego. W wyniku zerwania linki lub pociągnięcia jej w dowolnym kierunku przez operatora następuje uruchomienie wyłącznika i dochodzi do awaryjnego zatrzymania maszyny.
Co ważne, wyłączniki linkowe muszą wykrywać zarówno pociągnięcie linki, jak również jej poluzowanie. Oczywiście w wyniku chwycenia linki w dowolnym miejscu musi nastąpić aktywacja wyłącznika i odłączenie zasilania od maszyny, natomiast dzięki funkcji wykrywania luzu linki mamy pewność, że nie doszło do jej przerwania i że przełącznik zadziała. Linkowe wyłączniki bezpieczeństwa stosowane są w maszynach i przy ciągach produkcyjnych wtedy, gdy niemożliwe jest zamontowanie odpowiednich osłon. Są one z powodzeniem wykorzystywane do zabezpieczenia maszyn na długich odcinkach, np. taśmociągów, lub wzdłuż całej strefy zagrożenia linii produkcyjnej. Warto zauważyć, że jednym wyłącznikiem linkowym można zabezpieczyć strefę o długości ponad stu metrów.
Obudowa wyłącznika linkowego może być wykonana z różnego rodzaju materiałów. Na rynku dostępne są również wyłączniki wykonane ze stali nierdzewnej, które doskonale sprawdzają się w bardzo trudnych warunkach przemysłowych oraz tam, gdzie mamy do czynienia z podwyższonymi wymaganiami higienicznymi, np. w przemyśle spożywczym. Oczywiście dostępne są też wyłączniki w wykonaniu beziskrowym zgodne z dyrektywą ATEX.
Wyłączniki linkowe często są wyposażone w diodę LED, która sygnalizuje stan pracy wyłącznika, a także w wyłącznik E-Stop, dzięki czemu operator będzie mógł zatrzymać maszynę, gdy znajdzie się w pobliżu wyłącznika, a ma utrudniony dostęp do linki.
Podsumowanie
Ostatnio wiele firm zajmujących się produkcją urządzeń bezpieczeństwa pracuje nad implementacją w nich algorytmów sztucznej inteligencji i uczenia maszynowego. Sterowniki bezpieczeństwa korzystające z tego typu rozwiązań są obecnie w stadium testów i mogą być podłączone nie tylko bezpośrednio do czujników bezpieczeństwa, ale również do systemów automatyki przemysłowej oraz urządzeń Przemysłowego Internetu Rzeczy.
Sterowniki tego typu uczą się prawidłowych zachowań systemu, a także niewielkich odstępstw w sygnałach od normy, które nie świadczą jeszcze o awarii czy uszkodzeniu. Dzięki temu nie są wszczynane przypadkowe alarmy, a zatrzymanie maszyny nastąpi dopiero w chwili wykrycia nieprawidłowości, nawet w sytuacji, gdy standardowe systemy bezpieczeństwa nie zadziałają. Jak uważają analitycy, systemy bezpieczeństwa z zaimplementowanymi algorytmami sztucznej inteligencji wejdą do powszechnego użytku w najbliższych kilku latach.
*Tabele produktów znajdują się w wersji drukowanej i PDF miesięcznika Automatyka
źródło: Automatyka 1-2/2020
Słowa kluczowe
automatyka, bezpieczeństwo, czujnik, czujnik bezpieczeństwa, wyłącznik bezpieczeństwa, wyłączniki
Komentarze
blog comments powered by Disqus