Urządzenia transportu wewnętrznego w magazynach
Krzysztof Jaroszewski drukuj
W dzisiejszych czasach zagadnienie magazynowania nabiera znaczenia, ze względu na występujące w wielu branżach zjawisko większej podaży niż chwilowego popytu na wytwarzane dobra. Nakłada się na to również czynnik ekonomiczny związany z transportem dóbr w większych ilościach.
Często gotowe wyroby muszą zostać odtransportowane do magazynu do czasu skompletowania całego zamówienia odbiorcy, bądź zamówień różnych odbiorców, po to aby mogły być przewiezione jednym transportem. Z drugiej strony prowadzenie produkcji, w oparciu o bieżące dostawy surowców mogłoby okazać się dość ryzykowne w niektórych branżach, z uwagi na mogące pojawiać się przestoje produkcyjne spowodowane losowymi sytuacjami w opóźnieniach transportu.
Magazyny są również wykorzystywane jako środek umożliwiający lepsze rozdysponowanie dostaw. Często bardziej ekonomicznym okazuje się transport dóbr z wielokrotnym ich przeładunkiem w magazynach, niż transportowanie danego dobra jednym środkiem transportu od początku do końca. Dobrym przykładem są tutaj firmy spedycyjne, czy kurierskie, które mają wiele magazynów zlokalizowanych w różnych, strategicznych z punktu widzenia geograficznego położenia miejscach. Taka sieć magazynów pozwala optymalnie wykorzystać dostępne zasoby transportowe.
Powszechnym jest wykorzystywanie magazynów jako składowiska części zamiennych, bez których właściwie żaden zakład produkcyjny nie ma szansy sprawnie funkcjonować.
Według potrzeb
Magazyny mogą być duże i małe. Działać na zasadzie papierowego dokumentowania zawartości lub w oparciu o nowoczesny skomputeryzowany system zarządzania klasy WMS (Warehouse Management System – magazynowy system informatyczny). Funcjonować głównie z udziałem zasobów ludzkich w strefie transportu, lub z dominującym wykorzystaniem różnych środków technicznych.
W przypadku małych zakładów produkcyjnych czy warsztatów sprawdzać się może magazyn w formie minimalistycznej. Najczęściej jest to jedno pomieszczenie, w którym zarówno surowce, wytworzone dobra, jak i części zamienne są składowane razem, a zarządza tym jeden pracownik, niekoniecznie na cały etat. Zastosowanie takiego podejścia z pewnością nie będzie możliwe w przypadku dużego zakładu produkcyjnego, czy firmy spedycyjnej. Tu z uwagi na duży wolumen składowanych surowców, produktów, czy też magazynowanych części zamiennych i ich bogaty asortyment minimalistyczne podejście nie jest możliwe. W tym wypadku potrzebne są przestrzenie do magazynowania części zamiennych, surowców, być może półproduktów, jak i dóbr czekających na dalszy transport do innego miejsca składowania bądź bezpośrednio do odbiorcy końcowego. W takim przypadku efektywne zarządzanie wszystkimi zasobami magazynu efektywne będzie tylko przy zastosowaniu odpowiednich systemów wspomagających.
Optymalizacja czasu i powierzchni
Nowoczesne rozwiązania z obszaru magazynowania ukierunkowane są na optymalizację czasu dostępu do zasobów magazynowanych. Kluczowym zagadnieniem staje się odpowiednie znakowanie, zarówno powierzchni magazynowej, jak i magazynowanych towarów, co wiąże się z kolei z eliminowaniem zasobów ludzkich w obszarze transportowania towarów.
Inną kwestią jest optymalizacja wielkości powierzchni wykorzystywanej do magazynowania. Do tego celu służą odpowiednie konstrukcje półek magazynowych, często wraz z systemami przesuwania towarów między poziomami. Tym samym niepotrzebne stają się wózki transportujące, odbierające towar z półek. Często stosowanym rozwiązaniem są także regały grawitacyjne, czy inne podobne rozwiązania ułatwiające pobranie towaru.
Gdy istnieje możliwość wysokiego składowania towarów dobrym rozwiązaniem mogą okazać się magazyny samonośne. Ich cechą jest to, że regały są jednocześnie elementem konstrukcyjnym budynku. Zwiększenie powierzchni magazynowej można osiągnąć na przykład przez zastosowanie regałów magazynowych o podwójnej głębokości składowania, które pozwolą na składowanie dwóch palet lub innych jednostek SKU (ang. stock keeping unit) z każdej strony korytarza. Innym sposobem jest zastosowanie układnic z pomostami przeładunkowymi, które oprócz wzrostu przepustowości magazynu pozwolą na zwiększenie zagęszczenia składowanych towarów.
Z kolei stosując system przesuwania regałów można zagospodarować miejsca, które w klasycznych konstrukcjach byłyby zarezerwowane dla korytarzy. Przykładem takiego rozwiązania jest system Movirack (oferowany na polskim rynku przez firmę Mecalux), zapewniający dostęp do różnych regałów z jednego korytarza roboczego. Zastosowanie regałów przepływowych umożliwia z kolei pracę w systemie FIFO (First In First Out), co pozwala na sprawne pozbywanie się z magazynu produktów o najkrótszej dacie przydatności. Innym sposobem na sprawne magazynowanie produktów może być zastosowanie regałów paletowych wjezdnych typu Drive-In lub Drive-Through. Jest to zespół regałów tworzących wewnętrzne korytarze towarowe z poziomami wyposażonymi w szyny podtrzymujące palety. Gwarantuje on kontrolę wejść i wyjść ładunków, zgodnie z zasadą LIFO (Last In First Out) w przypadku regałów typu drive-in lub FIFO dla regałów typu drive-through. Nadają się one do składowania produktów jednorodnych, np. gdy występuje duża liczba palet na jednostkę magazynową. Do magazynowania produktów zastosowane mogą być także regały typu push-back zapewniające składowanie i manipulację paletami zgodnie z zasadą LIFO.
Windy towarowe oraz spiralne
Sposobem na wykorzystanie rozwiązań automatyki w obszarze magazynowania są m.in. windy towarowe oraz spiralne. Do klasycznych rozwiązań należą taśmociągi oraz przenośniki różnych typów. Zastosowanie windy towarowej pozwala na szybką i bezpieczną dystrybucję ładunków między poziomami. Na każdym z poziomów towar jest ułożony w miejscach załadunku lub rozładunku, zależnie od wykonywanego zadania. Z kolei pionowe windy spiralne pozwalają na oszczędność powierzchni. Innym sposobem usprawnienia przepływu towarów w magazynie jest zastosowanie systemu układnic magazynowych, które obsługują ruch palet. Pozwalają one obniżyć liczbę używanych przy transporcie wózków widłowych.
Zintegrowane w systemie informatycznym układnice bezbłędnie realizują swoje zadania, a zautomatyzowanie procesów zmniejsza ryzyko pomyłek, typowych dla ludzi. Jednocześnie skraca się czas obsługi towarów, w tym poszukiwania konkretnej palety. Dlatego też zindywidualizowane urządzenia pobierające, rozwiązania samojezdne czy systemy satelitarne przez ograniczenie kontaktu personelu z towarem pozwalają na wyeliminowanie pomyłek oraz zwiększenie zdolności przemieszczania produktów czy szybkości ich wydawania. Równocześnie obserwuje się minimalizowanie ryzyka uszkodzeń mechanicznych towaru.
W przypadku magazynowania dokumentów lub innych mniejszych przedmiotów, szczególnie takich, do których dostęp powinien być ściśle sankcjonowany skuteczne okażą się automatyczne szafy magazynowe RFID. Chronią one cenne przedmioty odpowiednio otagowane etykietami RFID, takie jak narzędzia, przyrządy pomiarowe, dokumentację czy sprzęt IT. Dostęp do ich zawartości mają jedynie osoby wyposażone w autoryzowaną kartę zbliżeniową RFID, dzięki czemu w systemie rejestrowana jest każda operacja pobierania i zwrotu. Szafy takie zapewniają całodobową możliwość dostępu do potrzebnych artykułów, bez konieczności korzystania z usług magazyniera. Dzięki technologii RFID wykorzystanej do identyfikacji zarówno zasobów magazynu, jak i osób wszelkie pobrania i zwroty do szafy magazynowej są rejestrowane w postaci operacji magazynowych generujących na bieżąco odpowiednie dokumenty.
Zdalnie sterowane systemy transportu
W nowoczesnych magazynach dąży się do osiągnięcia jak największego stopnia automatyzacji transportu. Środek transportu powinien być wykorzystywany w tych momentach i w tych miejscach (w odniesieniu do wózków), w których jest on niezbędny. Oznacza to, że taśmociągi i/lub podajniki powinny się włączać w chwilach, kiedy trafiają na nie towary i wyłączać od razu po ich dostarczeniu. W celu sterowania pracą takich urządzeń transportujących wartą rozważenia jest implementacja systemu identyfikacji towarów. Wyjątkiem są procesy transportu ciągłego.
Niezależnie od wybranego rozwiązania urządzenie transportujące musi pracować pod kontrolą systemu sterowania. W prostych przypadkach, gdy maszyna nie musi współpracować z innymi urządzeniami, można zastosować sterowanie lokalne. Jeśli maszyna jest tylko elementem większego systemu transportu należy zastosować sterowanie centralne. W tym drugim przypadku często sprawdza się sterowanie bezprzewodowe, którego zaletą jest brak przewodów sieciowych dedykowanych do przesyłania danych, co w przypadku rekonfiguracji ustawienia współpracujących maszyn może być nieocenioną zaletą. Bezprzewodowe sterowanie jest nieodzowne w przypadku samojezdnych wózków transportujących towary na duże odległości, szczególnie jeśli droga po jakiej się przemieszczają nie jest zawsze taka sama. Mamy tu do czynienia z optymalizacją wielokryterialną, a do tego ze standardowym sterowaniem urządzeniami wykonawczymi.
Dla przykładu trasa dla wózków automatycznych jest na bieżąco określana, a wszystkie parametry ruchu wyliczane bardzo często w oparciu o wiele parametrów. Z jednej strony do systemu trafiają żądania z obszaru przyjęć i wydań, z drugiej bieżące informacje o przemieszczaniu się wózka. Ponadto do zadań systemu sterowania należy koordynowanie współdziałania w jednej przestrzeni roboczej wielu wózków. W związku z koniecznością pozyskania rzetelnych informacji, niezbędnych do sterowania pojazdem, często wykorzystuje się jednocześnie kilka technologii, takich jak: laserowa, indukcyjna, czy też bazująca na kamerach video. System taki, należy pamiętać, musi także obsługiwać diagnostykę zasobów transportowych, gdyż od ich stanu technicznego zależy powodzenie zadania transportowego. Odpowiednie algorytmy FTC (Fault Tollerant Control – sterowanie tolerujące uszkodzenie) pozwalają kontynuować proces dostaw, nawet w sytuacji uszkodzenia elementów urządzeń transportowych.
Przykładem zdalnych systemów sterowania mogą być rozwiązania firmy SATEL, oferowane przez dystrybutora – firmę ASTOR. Radiomodemy SATEL mogą stanowić bazę dla systemu bezprzewodowej komunikacji między wózkami, czy innymi automatycznymi środkami transportu, a „centrum dowodzenia”. System bezprzewodowej komunikacji można zintegrować z innymi produktami z portfolio firmy. Z kolei dostawcą przemysłowych systemów bezprzewodowej komunikacji bazującej na standardzie Wi-Fi jest firma Ruckus Wireless, Inc., dostarczająca wszystkie niezbędne komponenty takiego systemu – rys. 1.
Rozwiązaniem bardziej ukierunkowanym na obsługę magazynów jest np. bezprzewodowa komunikacja ze skanerami kodów kreskowych, lub etykiet RFID. Rozwiązania tego typu proponowane są przez wielu integratorów (np. DDI Systems) oraz producentów (np.: Cisco, Motorola, Honneywell). Honeywell w swoim portfolio produktowym ma nie tylko skanery kodów kreskowych, ale także mobilne komputery z serii Dolphin – modele 70e i 75e, które w połączeniu ze skanerami, zakładanymi na palec (fot. 2), sprawdzą się w każdym magazynie.
W przypadku, gdy praca odbywa się w hałasie lub, gdy obie ręce pracownika magazynu są zajęte przekazywaniu informacji o identyfikowanym produkcie może się okazać pomocne urządzenie Vocollect Voice Solutions, firmy Honeywell – fot. 3.
Nie mając doświadczenia w projektowaniu i budowie bezprzewodowego systemu komunikacyjnego na potrzeby zarządzania magazynem, zawsze można zwrócić się o pomoc do specjalistów. Doradzą oni, w jakich obszarach zastosować komunikację bezprzewodową, pomogą dobrać niezbędne urządzenia z szerokiego portfolia oferentów, a także pomogą przy wdrożeniu. Jedną z takich specjalistycznych firm jest np. LEVER Technology Group, oferująca aplikacje z użyciem bezprzewodowego skaneru kodów kreskowych, kontroli zapasów, transmisji dźwięku, czy też identyfikacji RFID.
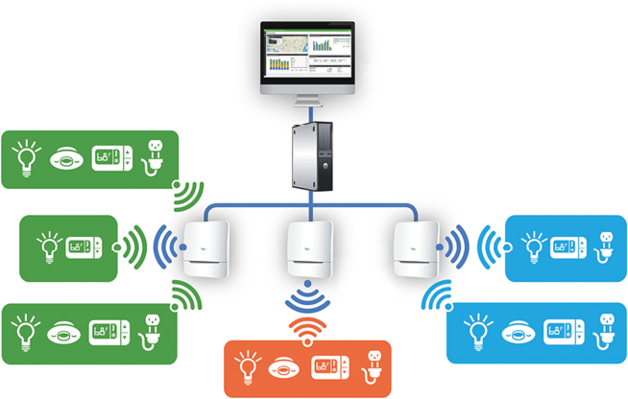
Rys. 2. Daintree Networks – idea bezprzewodowego sterowania oświetleniem, temperaturą i innymi urządzeniami
Autonomiczne pojazdy AGV
Zapewnienie efektywnego przepływu towarów między oddalonymi od siebie punktami magazynu, takimi jak: strefa przyjęć, miejsce magazynowania i strefa załadunku, może zostać osiągnięte przez zastosowanie zrobotyzowanych środków transportu. Należą do nich wózki typu AGV (Automated Guided Vehicles), czyli automatycznie sterowane pojazdy. AGV sprawdzają się wszędzie tam, gdzie najważniejsza jest wysoka skuteczność, dokładność oraz bezpieczeństwo wykonywanych prac. Oferentem tego typu środków transportu jest np. firma Cassioli. Zastosowanie w wózku platformy transportowej zwiększa jego przydatność do transportu na duże odległości w małych przestrzeniach. Platforma transportowa umożliwia, w zależności od potrzeb, podnoszenie, opuszczanie, obracanie oraz pełną kontrolę transportowanego przedmiotu. Rozwiązania w zakresie AVG ma również firma Rb-Poland Sp. z o.o. Logistic & Industrial Automation.
W jej ofercie znajdują się wózki o napędzie elektrycznym Smax z żelowymi akumulatorami, laserowymi czujnikami bezpieczeństwa i o ładowności sięgającej 4 tony, a także holownicze wózki z rodziny Typ T03 z magnetycznym obwodem naprowadzania dla trakcji. Ciekawą propozycję odnośnie pojazdów AVG przedstawiła firma SEW Eurodrive, która w swoich samojezdnych wózkach najnowszej generacji zastosowała lekkie superkondensatory do magazynowania energii. Ich zaletą jest krótki czas ładowania, bezkontaktowe (indukcyjne) i samoczynne doładowywanie podczas jazdy lub na stacjach docelowych, bezprzewodowa komunikacja i nawigowanie pojazdów przez Bluetooth, WLAN, czy też za pomocą lasera. W pojazdach zainstalowany jest system safety, bazujący na skanerach bezpieczeństwa, który gwarantuje bezpieczeństwo ludzi i otoczenia.
Podstawowym problemem w przypadku stosowania autonomicznego wózka jest zapewnienie jego bezkolizyjnego poruszania się po obszarze, po którym poruszają się także inne wózki. Rozwiązaniem tego problemu zajęła się m.in. firma SICK, która proponuje skaner NAV350 do precyzyjnej i bardzo dynamicznej nawigacji w magazynie. Czujnik potrafi rejestrować naturalne i sztuczne (folia odblaskowa) punkty nawigacyjne i na ich podstawie obliczać bezwzględną pozycję systemu transportu samojezdnego. Skaner rejestruje bieg promieni świetlnych. Do obliczenia pozycji wystarczą już trzy odbłyśniki. W ofercie firmy SICK znajdują się także laserowe skanery bezpieczeństwa S300 lub S3000. Umożliwiają one pomiar wolnej powierzchni składowania, co jest wykorzystywane w automatycznej paletyzacji – za pomocą danych pomiarowych wygenerowanych przez laserowy skaner bezpieczeństwa można określić geometrię palety, a następnie dokładnie i bezpiecznie umieścić paletę na wózku transportowym.
Ten sam skaner może zostać zastosowany do wydobywania nieprzetworzonych danych z pomiarów, które można wykorzystać do rozpoznawania geometrii i położenia palet. Zastosowanie laserowego skanera bezpieczeństwa S3000 Expert z funkcją CMS (Contour Measurement and Safety) firmy SICK umożliwia połączenie rozwiązań w zakresie bezpieczeństwa z funkcjami nawigacyjnymi. Nieprzetworzone dane konturów w otoczeniu i znaczniki odblaskowe (odległość, kąt, odbłyśnik) są dostarczane do sterownika pokładowego wózka w celu ułatwienia nawigacji przez wykonanie mapowania terenu. Ma to szczególną zaletę, gdyż pozwala ograniczyć liczbę kolejnych czujników nawigacyjnych do minimum. Z kolei mobilny, zamontowany na pojeździe skaner laserowy S100, cechujący się dwuwymiarowym polem odczytu przebiegającym ukośnie w dół i z dołu do góry, może monitorować duży obszar przed wózkiem samojezdnym. Pozwala to zapobiec kolizjom z wiszącymi lub wystającymi przedmiotami bądź końcówkami wideł innych wózków, które mogą stanowić niebezpieczeństwo również dla personelu.
Wielu producentów autonomicznych systemów transportowych integruje opisane systemy bezpieczeństwa i nawigacji w swoich produktach oferując gotowe rozwiązania.
W przypadku systemów poruszających się po z góry określonych trasach zastosować można nieco tańsze ale i mniej elastyczne rozwiązania, wykorzystujące w celu identyfikacji trasy magnetyczne paski przyklejane do podłogi. Przykładem takiego rozwiązania jest wózek samojezdny MOVE, bazujący na systemie LeanTek firmy Trilogiq. Zastosowanie pasków magnetycznych zapewnia elastyczność pod względem konfigurowania i zmian trasy. Na podobnej zasadzie działają systemy wykorzystujące pętle indukcyjne – przewód umieszczony w podłodze emituje pole elektromagnetyczne wychwytywane przez antenę wózka.
Oprócz pasków do określenia toru jazdy wózka stosuje się malowane, w szczególności fluorescencyjne tory jazdy. Taki tor jazdy wykrywać może np. czujnik luminescencyjny LUT firmy SICK, przekształcający odbierane światło z luminoforów w sygnał cyfrowy używany do sterowania pojazdem. Również odbiciowy sygnał ultradźwiękowy może być nośnikiem informacji o pozycji wózka. Inne metody określania położenia wózka to te, które działają na podstawie znajomości punktów odniesienia współrzędnych umieszczonych w podłodze obiektu, czy też wykorzystujące satelitarną technologię GPS lub etykiety RFID, czyli pasywne transpondery radiowe umieszczone w regularnych odstępach w podłodze.
Alternatywą dla autonomicznych środków transportu mogą być dla przykładu wózki wspomagające kompletującego zamówienie człowieka, jak wprowadzony na rynek w 2016 r. model iGo Neo CX 20 firmy Still. Operator takiego wózka może nim sterować manualnie, ale może także uruchomić go w trybie, w którym wózek będzie za nim podążał. Jest to możliwe dzięki aplikacji MotionTracking, która gwarantuje, że wózek będzie poruszał się w rytm pracy operatora, odciążając go od monotonnego uruchamiania, prowadzenia i zatrzymywania wózka. Do zbierania informacji o otoczeniu wózek został wyposażony w laserowy system rozpoznawania otoczenia – podobny do tych oferowanych przez firmę SICK. Przetworzone przez system informacje o otoczeniu pozwalają unikać przeszkód zarówno statycznych, jak i dynamicznych oraz optymalnie planować trasę. Co ważne wózek ten do sprawnego poruszania się za operatorem w przestrzeni magazynu nie potrzebuje żadnego zewnętrznego systemu sterowania. Firma Still dzięki swojemu innowacyjnemu produktowi pozwala na oszczędności czasu pracy operatora (nawet o 30%) i pozwala na lepsze skupienie się przy wykonywaniu głównych zadań związanych z obsługą towarów.
Zastosowanie automatycznego transportu z wyeliminowaniem czynnika ludzkiego może mieć jeszcze jedną ważną zaletę. Jest nią oszczędność energii związana z ograniczeniem oświetlenia. Ludzie do prawidłowego funkcjonowania (szybkiego i poprawnego rozpoznawania towarów oraz przemieszczania się) potrzebują odpowiedniego oświetlenia miejsca pracy. Maszyny mogą właściwie pracować w ciemności. Biorąc pod uwagę to, że najczęściej konstrukcja hal magazynowych ogranicza zastosowanie światła dziennego do ich oświetlenia oraz konieczność funkcjonowania magazynu 24 godziny na dobę (również w nocy) duże zasoby finansowe należy przeznaczać na zakup energii eklektycznej oraz infrastruktury oświetleniowej. Zastępując ludzi rozwiązaniami automatyki można znacząco ograniczyć ten niekorzystny czynnik. Gdyby jednak okazało się, że w przestrzeni zdominowanej przez rozwiązania automatyczne pojawia się człowiek, to oczywiście należy ją odpowiednio oświetlić. W takim wypadku sprawdzają się rozwiązania automatyczne, takie jak oferowane przez amerykańską firmę CIMCON Lighting, Inc., czy też
AUDACY Wireless Controls system by IDEAL, które to firmy oferują kompleksowe systemy w tym zakresie. Szerzej tematem zajęła się np. firma Daintree Networks, której system inteligentnego sterowania światłem umożliwia też kontrolę temperatury oraz innych urządzeń – rys. 2.
Niewątpliwie przyszłością magazynów są drony. Ich szybki rozwój zarówno od strony technicznej, jak i programowej pozwala wnioskować, że tego typu urządzenia będą wykorzystywane w logistyce dostaw i magazynów. Już w roku 2015 firma Amazon oficjalnie zapowiedziała realizację dostaw za pomocą dronów Amazon Prime Air – fot. 4.
Takie systemy to jednak odległa przyszłość z uwagi na wiele czynników ograniczających, związanych z przebywaniem drona w środowisku zmiennych warunków pogodowych oraz lądowaniem i wyładunkiem towaru np. w środowisku miejskim. Jednakże rozwiązania wykorzystujące takiego typu środki transportu w zamkniętych magazynach oraz tam, gdzie dokładnie można określić miejsca startu i lądowania (pobierania i zdawania) powinny już niebawem pojawić się w ofercie. Jednym ze zwiastunów jest tu rozwiązanie zaprezentowane podczas ubiegłorocznych targów LogiMAT 2016 pod nazwą InventAIRy. Konstrukcja tego drona umożliwia mu poruszanie się w dowolnym kierunku, co uniezależnia go od przeszkód naziemnych. Co istotne, dzięki inteligentnemu systemowi sterowania oraz zainstalowanym czujnikom ultradźwiękowym, kamerom 3D i skanerom laserowym, poruszające się po magazynie drony same przygotowują i aktualizują jego mapy. Z pewnością z roku na rok będzie przybywało tego typu rozwiązań.
Automatyzacja zarządzania gospodarką magazynową
Nawet dobrze zaprojektowany magazyn, w którym zastosuje się najnowocześniejsze rozwiązania transportowe może okazać się wąskim gardłem, jeśli nie ma właściwego systemu zarządzania. W celu sprawnego prowadzenia ewidencji towarów znajdujących się w magazynie, przygotowywania raportów, czy zestawień surowców i gotowych produktów konieczne jest stosowanie odpowiednio wydajnych komputerowych narzędzi wspomagających. Szczególnie istotne jest wspomaganie procesu planowania dostaw surowców na potrzeby produkcji, jak i dostaw wyrobów gotowych do kontrahentów. Dobre narzędzia informatyczne pozwalają na lepsze wykorzystanie nie tylko zasobów magazynowych, ale także finansowych. Odpowiednie zestawienie informacji o aktualnych zasobach, przewidywanym wolumenie produkcji i mocach przerobowych (dostępności zasobów na linii produkcyjnej) może być bardzo pomocne przy optymalnym składaniu zamówień na surowce. Z kolei wiarygodna informacja o wolnej przestrzeni magazynowej, w połączniu z wiedzą o szybkości powstawiania nowych wyrobów, pozwoli na lepsze zaplanowanie transportu do odbiorców. Do takiego zarządzania zasobami magazynu nie wystarczą informacje z samego systemu klasy WMS. Informacje o zleceniach przyjętych do produkcji, czy terminie ich realizacji wykraczają poza tego typu system. Konieczne jest połączenie magazynu z systemem klasy ERP (Enterprise Resource Planning System). Zapewni to ścisłą kontrolę łańcucha dostaw od zamówień surowców po transport gotowych wyrobów dla odbiorców. W celu monitorowania i nadzorowania stanu maszyn i sprzętu na magazynie stosuje się systemy klasy MES (Manufacturing Execution System).
Rozwiązania informatyczne w sferze obsługi zagadnień związanych z funkcjonowaniem samego magazynu są dostarczane przez wiele firm. Należą do nich zarówno producenci krajowi, jak i zagraniczni. Rozwiązania IT w gospodarce magazynowej mogą być dedykowane konkretnym przedsiębiorstwom, personalizowane na bazie ogólnego szkieletu lub uniwersalne.
Jednym z dostawców systemu zarzadzania magazynem jest firma Exact Software Poland Sp. z o.o. oferująca produkt pod nazwą Globe Exact Warehouse Management System. Jest to jedno z narzędzi bardziej rozbudowanego systemu, jakim jest Globe Exact. Na rynku produktów klasy WMS wymienić należy także firmę Dexion, która oferuje dodatkowe narzędzie zarządzania magazynem sprzedawane pod nazwą Warehouse Intelligence System – C-WIS. Jest to zaawansowany system logistyczny opracowany w celach optymalizacji magazynowania towaru. Z kolei firma PSI oferuje system PSIwms, dedykowany różnym branżom i typom magazynów. System oparty jest na Smart Move Technology, czyli technologii wykorzystującej zaawansowane algorytmy matematyki wyższej do optymalizowania złożonych procesów logistycznych. Takie podejście pozwala na planowanie procesów przez automatyczne wybieranie i ustalanie kolejności realizowanych zadań, wyznaczanie optymalnego miejsca składowania i pobierania towaru. A to wszystko dzięki parametryzacji konfiguracji, umożliwiającej dopasowanie systemu do indywidualnych wymagań.
Ciekawym i innowacyjnym jest wspomagające narzędzie firmy HDF Polska. Wykorzystana tu technologia 3D daje operatorowi iluzję głębi i możliwość śledzenia ruchu w magazynie w formacie 3D. Oznacza to kontrolowanie rotacji towarów, a także wykonanie wielowymiarowej wizualizacji aktualnych stanów w czasie rzeczywistym, gdyż oprogramowanie jest w pełni zsynchronizowane z działającym magazynem. W ofercie tej firmy znajduje się system do zarządzania magazynem, wykorzystujący zaawansowane parametry optymalizacyjne, techniki automatycznej identyfikacji, globalne standardy identyfikacji GS1, współpracujący z aplikacją finansowo-księgową i kadrowo-płacową.
Podobnie system magazynowy ExpertWMS, oferowany przez firmę DATACONSULT, wspiera zarządzanie magazynem przez zdefiniowanie jedno- lub wieloetapowych procesów, które mogą bazować na dyspozycjach i uwzględniać zaawansowane systemy rezerwacji w wielu działach. System ten potrafi reagować na sygnały uruchamiając m.in. procedury kontroli jakości, inwentaryzacji towaru/lokalizacji czy automatycznych powiadomień. W efekcie program magazynowy WMS pomaga zarówno na poziomie operacyjnym, jak i zarządczym zwiększać wydajność magazynu i ograniczać jego koszty, szczególnie wraz z automatyką magazynową i systemami wizyjnymi. Wśród dużej liczby dostawców systemów klasy WMS na polskim rynku wymienić należy także firmę Logifact oferującą system pod nazwą LogifactWMS, czy też Asseco Business Solutions SA producenta systemu Asseco Softlab WMS.
Podsumowanie
Prowadzenie magazynu, nawet w rozmiarze „XXL”, nie musi w dzisiejszych czasach nastręczać problemu. Wiele firm, oferujących produkty specjalizowane na potrzeby branży magazynowej, jest w stanie dostarczyć rozwiązania, które rozwiążą niemal wszystkie problemy. Szczególnie wiele jest ofert pozwalających wyeliminować lub w znacznym stopniu ograniczyć udział człowieka na poziomie konfekcjonowania. A nawet, jeśli niektóre czynności zostaną powierzone ludziom, to dostępne rozwiązania pozwolą ograniczyć do minimum ryzyko pomyłek realizacji zamówień i występowania uszkodzeń transportowanych towarów.
Logistyczne aspekty działalności magazynu mogą ułatwić specjalizowane systemy komputerowe, bezbłędnie wskazujące miejsce składowania każdej sztuki towaru i zarządzające środkami transportu, dostarczającymi towar we wskazane miejsce w określonym czasie. Jeśli dodatkowo magazyn będzie obsługiwany przez samojezdne wózki, to gwarancja terminowości i trafności dostaw wzrasta do 100%. Zatem zamiast zastanawiać się, czy inwestować w zakrojoną na szeroką skalę automatyzację, warto spotkać się z firmami świadczącymi usługi w zakresie automatyzowania magazynów, poprosić o projekt „skrojony na miarę” i wycenę, a następnie wykonać studium opłacalności, które w zdecydowanej większości wykaże opłacalność inwestycji. Dzięki takiemu podejściu dotychczasowe środki i rozwiązania, które często zawodzą, mogą zostać zastąpione skuteczniejszymi.
źródło: Automatyka 4/2017
Komentarze
blog comments powered by Disqus