Czujniki optyczne i zbliżeniowe
Marcin Bieńkowski drukuj
W wielu układach sterowania i systemach automatyki niejednokrotnie zachodzi konieczność bezkontaktowego wykrywania obecności lub pozycji obiektu. Dzięki temu możliwe jest odpowiednie zaprogramowanie układów automatyki, tak aby dany proces technologiczny przebiegał prawidłowo, zgodnie z założeniami. Czujniki zbliżeniowe i optyczne idealnie nadają się też do wykrywania zagrożeń i nietypowych sytuacji produkcyjnych, zwiększając w ten sposób bezpieczeństwo pracy i eliminują sytuacje, w których uszkodzeniu mogłaby ulec np. linia produkcyjna.
W zależności od konstrukcji i zasady działania, czujniki zbliżeniowe mogą w sposób bezkontaktowy wykrywać wszelkiego rodzaju obiekty czy obecność ludzi. Również w zależności od swojej konstrukcji, czujniki zbliżeniowe charakteryzują się funkcjonalnością, możliwościami aplikacyjnymi czy ograniczeniami dotyczącymi ich działania i wykrywalności obiektów. To dlatego ich użytkownicy muszą być świadomi cech konstrukcyjnych, wykorzystanych technologii, możliwości, ograniczeń i sposobu ich wykorzystania. Wśród nich znajdziemy też, zarówno proste sensory, których podstawową funkcją jest sygnalizowanie obecności lub braku obiektu w sposób bezdotykowy, jak i dużo bardziej zaawansowane czujniki optyczne z możliwością przetwarzania dwu- lub trójwymiarowego obrazu. Przyjrzyjmy się zatem typom i rodzajom stosowanych w przemyśle czujników zbliżeniowych.
Rodzaje czujników stosowanych w systemach automatyki
Bezkontaktowe czujniki zbliżeniowe wykorzystuje się najczęściej do kontroli przemieszczenia, położenia i poziomu. Wśród nich wyróżnić można pięć głównych grup, a mianowicie: czujniki indukcyjne, sensory magnetyczne, pojemnościowe, laserowe, optyczne i ultradźwiękowe.
Najstarszą grupą czujników zbliżeniowych są czujniki indukcyjne. Pojawiły się one na rynku już w latach 60. XX wieku i do dziś należą do grupy najchętniej stosowanych sensorów zbliżeniowych w przemyśle. Wykrywają one różnego rodzaju metalowe obiekty, a zasięg detekcji uzależniony jest od rodzaju metalu, z jakiego wykonano obiekt i siły wytwarzanego przez nie pola magnetycznego. Czujniki te do swojego działania wykorzystują pole elektromagnetyczne o wysokiej częstotliwości. Pole to wytwarzane jest przez cewkę, która stanowi część obwodu rezonansowego, a w każdym czujniku indukcyjnym, niezależnie od producenta, wyróżnić można następujące części: cewkę, oscylator, obwody detekcji, obwody wyjściowe.
W czujnikach tych prąd zmienny wytworzony w oscylatorze przepływając przez cewkę generuje pole magnetyczne, a od umiejscowienia tej cewki zależy, gdzie usytuowana jest powierzchnia aktywna czujnika – np. w osi pionowej czy poziomej sensora. Gdy w zasięgu czujnika, ściślej wytworzonego przez cewkę pola elektromagnetycznego pojawi się przewodzący prąd elektryczny obiekt, wówczas na jego powierzchni wyindukują się prądy wirowe, które tworzą pole przeciwnie skierowane do pola czujnika, które to pole skutecznie zmniejsza indukcyjność cewki obwodu rezonansowego znajdującego się w czujniku. Zmiany te wykrywane są przez obwód detekcji i na tej podstawie zostają aktywowane obwody wyjściowe.
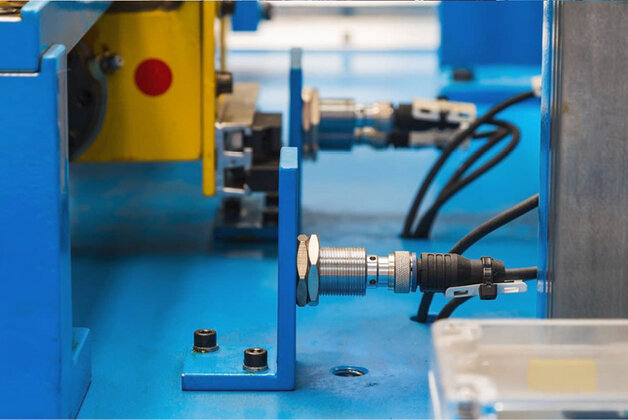
Przykładowa aplikacja z wykorzystaniem indukcyjnych czujników zbliżeniowych (inductive proximity sensor)
Detekcja
W czujnikach indukcyjnych detekcja zmian pola elektromagnetycznego może odbywać się w dwojaki sposób. W pierwszym przypadku, gdy obiekt zbliża się do czujnika, wartość indukowanych prądów wirowych rośnie, co prowadzi do tłumienia amplitudy drgań w obwodzie oscylacyjnym. Czujnik wykrywa tę zmianę za pomocą detektora amplitudy. Drugą z metod jest wykrywanie zmiany częstotliwości drgań, a nie zmian amplitudy oscylacji. Wielkość tych zmian, zarówno amplitudowych, jak i oscylacyjnych zależy od odległości obiektu od czoła czujnika. W praktyce obwody wyjściowe aktywowane są po zbliżeniu się obiektu na odpowiednią, założoną przez producenta czujnika odległość.
Warto podkreślić, że obiekty wykonane z metalu niemagnetycznego, np. z aluminium lub miedzi, zbliżając się do czujnika powodują wzrost częstotliwości oscylacji. Z kolei przedmioty z metali magnetycznych, jak stal czy nikiel, powodują zmniejszenie częstotliwości oscylacji generatora. Zmiany ta w stosunku do częstotliwości odniesienia w odpowiedni sposób zmieniają stan wyjść czujnika.
W zależności od tego, jaki mamy zasięg czujnika, rodzaj materiału, z którego wykonany jest wykrywany przedmiot, gabarytów obiektu, rodzaju zabudowy czujnika (z czołem zabudowanym czy niezabudowanym), częstotliwość przełączania i innych parametrów, zależy jakie elementy i pod jakimi warunkami możemy wykryć. W katalogowych opisach czujników indukcyjnych spotkać się można z różnymi opisami zasięgu ich działania. Najczęściej podaje się maksymalny, nominalny zasięg czujnika oznaczany symbolem Sn. Jest on skalowany dla typowej stali konstrukcyjnej St3.
Często podawany jest też zasięg zalecany, określany też jako zasięg roboczy lub pewny i oznaczany jako Sa. Mierzony jest on dla tego samego gatunku stali i najczęściej określany jako 0,81 zasięgu maksymalnego Sn. Wartość ta wynika m.in. z wartości tolerancji zasilania, różnicy temperatury, oraz tolerancji elementów elektronicznych użytych do budowy czujnika. Co ważne, w zależności od zabudowy czoła czujnika (czoło zabudowane lub niezabudowane) ten sam sensor może charakteryzować się mniejszym lub większym zasięgiem. W przypadku czujników o korpusie gwintowanym zabudowę rozpoznać można po tym, jak daleko gwint sięga czoła czujnika – czy korpus jest nagwintowany prawie do końca czoła czy jakaś część czoła wystaje ponad metalowy korpus. Czujniki z czołem zabudowanych mają zazwyczaj mniejszy zasięg, ale są dużo bardziej odporne na przypadkowe uszkodzenia mechaniczne i charakteryzują się też dużo bardziej precyzyjny punkt przełączania. Czujniki z czołem niezabudowanym potocznie nazywane też z czołem „wystającym” charakteryzują się większym zasięgiem ale też mniej precyzyjnym punktem przełączania.
Istotnym parametrem czujników indukcyjnych jest też histereza. Wyrażona jest ona najczęściej jako wartość procentowa, ujęta w funkcji zasięgu czujnika. Jest to różnica odległości, na którą reaguje czujnik indukcyjny przy zbliżaniu i oddalaniu metalu od czoła czujnika. Wartość histerezy głównie zależna jest od rodzaju i wielkości czujnika i zazwyczaj nie przekracza 20 % zakresu pomiarowego. Co ważne, zjawisko to występuje również w sytuacjach, gdy przesuwamy obiekt z boku do czoła czujnika. W tym miejscu należy też wspomnieć o parametrze określanym jako częstotliwość przełączania, który określa maksymalna częstotliwość, z jaką czujnik może wykrywać pojawiające się obiekty, a więc sygnalizować ich obecność na wyjściu. W przypadku szybko pojawiających się obiektów warunek maksymalnej częstotliwości przełączania jest zwykle spełniany w około połowie zasięgu nominalnego Sn.
Wyjścia
Warto zaznaczyć, że czujniki indukcyjne w większości przypadków nie mają możliwości wykrywania różnych metalowych obiektów z tej samej lub zbliżonej odległości. Oznacza to, że zasięg dla różnych metali jest po prostu różny. Dla materiałów takich jak miedź, mosiądz, aluminium stosuje się specjalne współczynniki, które mnoży się przez zasięg czujnika. W ten sposób z pewnym przybliżeniem jesteśmy w stanie określić zasięg czujnika dla obiektów wykonanych z innych materiałów niż stal.
W sprzedaży dostępne są czujniki z różnymi rodzajami wyjść. Typowo czujniki wykonuje się z wyjściami przełączającymi PNP lub NPN. Występują również wersje umożliwiające podłączenie czujnika w obydwu polaryzacjach. Do pomiarów stosuje się najczęściej wersje z wyjściami analogowymi 4–20 mA lub 0–10 V. Jeżeli czujnik indukcyjny za pomocą swojego wyjścia ma bezpośrednio sterować urządzeniem podając mu zasilanie, używa się wówczas tzw. czujników dwuprzewodowych. Jeden z przewodów łączy się wówczas z cewką przekaźnika, która przerzuca zworę przekaźnika.
Na rynku dostępne są również czujniki umożliwiające wymianę danych np. wykorzystujące protokół IO-Link lub Ethernet. Te ostatnie znajdują zastosowanie w systemach Inteligentnej Fabryki i Przemysłowego Internetu Rzeczy. Warto zauważyć, że w sprzedaży dostępne są modele zarówno z komunikacją przewodową, jak i bezprzewodową, co pozwala dostosować je do zadań w konkretnej aplikacji.
Zastosowania
Elektromagnetyczne czujniki bezpieczeństwa zapewniają bezkontaktową, bezpieczną rejestrację zarówno pozycji, jak i położenia krańcowego monitorowanych obiektów, co ma istotne znaczenie z punktu widzenia bezpieczeństwa pracującej maszyny czy systemu automatyki. Czujniki te charakteryzują się odległością przełączania wynoszącą, w zależności od modelu zwykle 2–10 mm. Wiele modeli charakteryzuje się też wysokim stopniem ochrony IP65, IP67 a nawet IP69K i dużą wytrzymałością na ekstremalnie wysoką i niską temperaturę. Czujniki te są też wyjątkowo trwałe pod względem mechanicznym dzięki swoje sporej odporności na wibracje i uderzenia.
Większość powszechnie wykorzystywanych czujników indukcyjnych przeznaczona jest do pracy w typowych aplikacjach przemysłowych, gdzie nie występują zbyt ciężkie warunki pracy. Najpopularniejsze rodzaje czujników to te montowane w korpusach typu M12, M18 oraz nieco rzadziej M8 i M30, które charakteryzują się największym zasięgiem. Korpusy wykonane są z mosiądzu niklowanego, a czoła z tworzyw sztucznych. W przypadku, gdy potrzebny jest duży zasięg, często korzysta się z czujników indukcyjnych w obudowie prostopadłościennej. Istnieją również czujniki w postaci małych prostopadłościanów, które w wygodny sposób można umieszczać w profilach lub mocować do korpusów urządzeń.
W handlu dostępne są również czujniki dostosowane do pracy w konkretnych aplikacjach, czy środowiskach. Mogą to być czujniki do pracy w branży spożywczej, farmaceutycznej czy kosmetycznej. Ich korpusy wykonuje się ze stali nierdzewnej, a czoła czujników produkuje się tu w specjalnych atestowanych tworzyw sztucznych pozwalających na kontakt z żywnością. Produkowane są również sensory o zwiększonej odporności na oleje maszynowe, przekładniowe i chłodziwo, a także temperaturę – zarówno wysoką, jak i ujemną. Innym przykładem tego typu czujników specjalnych są sensory przystosowane do aplikacji, gdzie występują wysokie ciśnienia. Osobną grupą czujników indukcyjnych są czujniki przeznaczone do pracy w strefach zagrożonych wybuchem ATEX. Najczęściej spotyka się tu czujniki w wykonaniu iskrobezpiecznym, gdzie czujnik do pracy wykorzystuje rozwiązania niskoprądowe i jest podłączony do specjalnego modułu bezpieczeństwa.
Magnetyczne czujniki zbliżeniowe
Magnetyczne czujniki zbliżeniowe wykorzystywane są do pomiaru położenia i prędkości poruszających się metalowych elementów. Są to jedne z najprostszych sensorów zbliżeniowych. Ich zasada działania polega na sterowaniu stykami pod wpływem pola magnetycznego, którego źródłem może być elektromagnes lub magnes stały. Magnesy mogą być montowane w różnych ruchomych elementach, a ich położenie wykrywane właśnie za pomocą czujników magnetycznych. Najczęstsze zastosowanie tego typu czujników to wykrywanie położenia tłoczyska w siłownikach pneumatycznych i hydraulicznych oraz krańcówki zamknięcia osłon na liniach produkcyjnych.
W przeciwieństwie do innych czujników zbliżeniowych sensory magnetyczne charakteryzują się wyjątkowo prostą budową – nie ma tam elektroniki, która mogłaby się zepsuć. Co więcej, najprostsze czujniki nie wymagają w ogóle zasilania. W zależności od modelu czujnika styki mogą być przystosowane do przewodzenia małych prądów lub do dużych obciążeń indukcyjnych. Ze względu na to, że czujniki zbliżeniowe magnetyczne charakteryzują się wysoką odpornością na zapylenie, wysoką temperaturę i drgania, można wykorzystywać je wszędzie tam, gdzie panują trudne warunki eksploatacyjne. Magnetyczne czujniki zbliżeniowe charakteryzują się też dużą wytrzymałością na przeciążenia i przepięcia, dzięki czemu można je stosować w różnych układach automatyki, w tym w siłownikach pneumatycznych. Ich wadą jest mała czułość oraz konieczność stosowania magnesów lub elektromagnesów.
Jak działa czujnik magnetyczny
W zależności od budowy czujnika magnetycznego, czujniki te podzielić można na czujniki aktywne, wyposażone np. w czujnik Halla (tzw. hallotrony), bądź też pasywne np. korzystające z elementów zmiennej reluktancji, tzw. czujniki VR, które mierzą zmianę oporności magnetycznej, analogicznie do rezystancji elektrycznej lub kontaktrony
Czujnik VR składa się z magnesu trwałego, nabiegunnika oraz cewki czujnikowej zamkniętej w cylindrycznej obudowie. Źródłem pola magnetycznego jest tu magnes stały. Wykrywany obiekt z materiału magnetycznego, przechodząc blisko nabiegunnika powoduje zmiany pola magnetycznego. Zmiany ta generują napięcie w cewce sygnałowej, a wielkość tego napięcia zależy od wielkości obiektu docelowego, jego prędkości i wielkości szczeliny między biegunem a obiektem. Co ważne wykrywany obiekt musi znajdować się w ruchu, aby mógł być wykrytym.
Sensory o zmiennej reluktancji są elementami pasywnymi, nie potrzebują więc źródła zasilania. Tego typu czujniki wykorzystuje się najczęściej do pomiarów urządzeń wirujących, na przykład do wykrywania ruchu zębów na kołach zębatych lub klinów na paskach rozrządu. Mogą być również stosowane do wykrywania łbów śrub, rowków wpustowych lub innych szybko poruszających się metalowych elementów. Wykorzystywane są też jako obrotomierze do pomiaru prędkości obrotowej, a także parami do pomiaru mimośrodowości obracającego się wału.
Hallotrony
Czujniki Halla, jak można się domyślić, swoją nazwę zawdzięczają wykorzystaniu w mechanizmie ich działania efektu Halla. W uproszczeniu zjawisko to polega na pojawieniu się różnicy potencjałów w przewodniku, w którym płynie prąd elektryczny, gdy przewodnik ten znajduje się w poprzecznym do płynącego prądu polu magnetycznym. Pojawiające się tu napięcie jest proporcjonalne do gęstości strumienia pola magnetycznego. Czujnik Halla wymaga, aby wykrywany obiekt był namagnesowany lub miał wbudowany magnes.
Najczęściej jako element czynny stosuje się specjalną, bardzo cienką półprzewodnikową płytkę magneto-rezystywną. Czujniki te wykorzystuje się najczęściej do określania położenia tłoczyska w siłownikach. Cechują się krótszym czasem odpowiedzi od kontaktronów i precyzyjniejszym punktem przełączania. Czujniki Halla charakteryzują się zdolnością wykrywania statycznych pól magnetycznych i mogą być używane do wykrywania przesunięcia obiektów znajdujących się normalnie w stałej, określonej pozycji.
Pole magnetyczne jest bardzo przenikliwe, co zapewnia hallotronom dużą odporność na zabrudzenia oraz odporność na zakłócenia. Za zasięg odpowiada odpowiednie dobranie zespołu czujnika i stałego magnes. W przypadku czujników magnetycznych ich zasięg wynosi od kilku do kilkudziesięciu mm. Dla czujników magnetycznych do siłowników zwykle podaje się ich czułość na natężenie pola magnetycznego wyrażone w militeslach [mT]. Czujniki Halla występują najczęściej jako czujniki magnetyczne w korpusach gwintowanych lub prostopadłościennych, a ich wygląd zbliżony jest do czujników indukcyjnych. Drugą grupą sensorów są czujniki Halla przystosowane do montażu na obudowie siłowników pneumatycznych.
Kontaktrony
Kontaktron to czujnik składający się z dwóch wykonanych z materiału ferromagnetycznego cienkich blaszek, które znajdują się w próżni albo w gazie obojętnym. Pod wpływem zewnętrznego pola magnetycznego jedna z blaszek staje się biegunem N, a druga biegunem S. Blaszki o przeciwnych biegunach przyciągają się i łączą zamykając obwód elektryczny. Innymi słowy w kontaktronie po przyłożeniu do niego magnesu, blaszki zwierają się i dzięki temu możliwy jest przepływ prądu, co traktuje się jako zadziałanie wyjścia czujnika. Po usunięciu magnesu blaszki rozwierają się dzięki ich własnej sprężystości.
Kontaktrony najczęściej stosuje się do sygnalizowania krańcowych położeń w osłonach maszyn i siłownikach. Jest to wyjątkowo proste i tanie rozwiązanie. Do wad zalicza się mała odporność na duże wibracje, gdzie może dochodzić do „sklejania” się blaszek mimo usunięcia ich z pola magnesu, czyli np. otwarcia osłony. Wówczas blaszki pozostaną zwarte, a obwód elektryczny jest dalej zamknięty.
Czujniki pojemnościowe
Czujniki pojemnościowe wykorzystuje się zarówno do wykrywania obiektów wykonanych z metalu, jak i innego rodzaju przeszkód niemetalicznych, np. wykonanych z drewna, szkła czy tworzywa sztucznego. Mogą być też stosowane do detekcji materiałów sypkich i cieczy, w tym wody i oleju. Możliwość wykrywania obiektów z tworzyw sztucznych sprawia, że czujniki pojemnościowe są chętnie montowane w systemach pakujących. Używa się ich też do detekcji napełnienia zbiornika cieczą.
Ten rodzaj sensorów działa na zasadzie pomiaru zmiany pojemności powstałej między obiektem a czujnikiem kondensatora. Kiedy do czujnika przybliżymy obiekt, kondensator zmienia swoją pojemność, która zależy wprost proporcjonalnie od odległości między wykrywanym obiektem a sensorem. W tym przypadku czoło sensora stanowi elektroda, która jest jedną z jego okładzin, drugą okładką kondensatora jest zaś sam badany obiekt. Gdy w polu detekcji pojawi się obiekt, wzrasta pojemność naszego kondensatora, co daje możliwość jego wykrycia.
Pojemność kondensatora zmienia się wraz ze zmianą odległości między jego dwiema okładzinami, a więc czujnikiem i badanym obiektem. Ustalona do zadziałania czujnika odległość między okładzinami powinna być wprost proporcjonalna do stałej dielektrycznej materiału, z którego wykonany jest wykrywany obiekt. Czujniki te są stosunkowo czułe. Należy więc uważać na obiekty sypkie lub lepkie, które obklejając czoło czujnika potrafią zafałszować wyniki jego działania. W większości przypadków czujniki pojemnościowe mają możliwość regulacji czułości za pomocą potencjometru lub przyciski do programowania.
Dużą zaletą czujników pojemnościowych jest możliwość łatwego ustawiania ich czułości czyli dystansu roboczego. Ta czułość zależy od wielkości czujnika, a także od tego, z jakiego materiału został wykonany wykrywany obiekt. Czujniki pojemnościowe dostępne są w wersjach pracujących przy napięciu stałym lub zmiennym.
Istotne jest też to, że czujniki pojemnościowe są wyjątkowo odporne na zakłócenia takie, jak: pył, aerozol w powietrzu, czy oddziaływanie elektromagnetyczne. Z tego też względu pojemnościowe czujniki zbliżeniowe stosuje się również tam, gdzie występują trudne lub bardzo trudne warunki pracy. Najczęściej wykorzystuje się je w przemyśle szklarskim, drzewnym, papierniczym, tworzyw sztucznych oraz w branży materiałów sypkich.
Ultradźwiękowe czujniki zbliżeniowe
Gdy niezbędne są pomiary zbliżeniowe obiektów znajdujących się w większej odległości, z pomocą przychodzą czujniki ultradźwiękowe. Pozwalają one wykrywać wszelkiego rodzaju obiekty z odległości do kilku metrów. W sensorach ultradźwiękowych fala ultradźwięków emitowana jest w kierunku wykrywanych obiektów i gdy natrafi ona na obiekt, odbija się od niego i wraca do czujnika. Znając prędkość propagacji i ten czas, można obliczyć odległość.
Problem może być tu jednak fakt, że ultradźwięki mogą odbić się także od obiektów, które nie są przedmiotem pomiaru, na przykład obudowa maszyny czy znajdujący się w pobliżu operator. Aby uniknąć zafałszowania pomiaru, liczony jest czas, jaki mija od wysłania do odbioru fali. Gdy czas ten jest krótszy od wcześniej założonego, czujnik uzna, że wykrył obiekt. Jeżeli czas jest dłuższy uznaje się, że odbicie nastąpiło od maszyny lub ściany. Podstawową zaletą czujników ultradźwiękowych jest to, że są odporne nawet na duże zabrudzenia, mogą pracować zanurzone w cieczy i wykrywać różnego rodzaju obiekty, niezależnie od materiału, z którego są one wykonane.
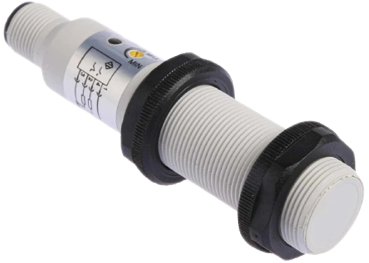
Pojemnościowy czujnik zbliżeniowy z serii RS PRO (RS Components) z wyjściem tranzystorowym PNP (zakres detekcji 5 mm, IP67, obudowa M18)
Czujniki optyczne
Typowe, zbliżeniowe czujniki optyczne, a w zasadzie czujniki fotoelektryczne, do detekcji obiektów wykorzystują promieniowanie podczerwone lub widzialne. Niemnie są też modele wykorzystujące do detekcji ultrafiolet lub nawet promieniowanie rentgenowskie. Czujniki tego typu podzielić można na dwie podstawowe grupy detektorów światła i emiterów wiązek świetlnych. Z kolei ze względu na szczegóły konstrukcyjne dzieli się je na kilka kategorii:
- czujniki odbiciowe (w tym z eliminacją wpływu tła),
- czujniki refleksyjne,
- bariery (czujniki obszaru),
- światłowodowe,
- luminescencyjne,
- szczelinowe,
- analogowe.
Niezależnie od rodzaju czujnika/fotoczujnika, jego parametry pracy obejmują:
- strefę działania (od milimetrów do metrów, określaną zakresem),
- częstotliwość pracy (od Hz, przez kHz do MHz),
-
napięcie zasilania, najczęściej
12–24 V DC lub 230 V AC, - stopień ochrony obudowy IP,
- rodzaj wyjścia,
- rodzaj gniazda zasilania,
- temperatury pracy.
Oprócz wymienionych parametrów, dla czujników analogowych i kurtyn świetlnych, określa się jeszcze dodatkowe cechy. W przypadku sensorów analogowych podawana jest rozdzielczość oraz dokładność. W przypadku kurtyn świetlnych określa się szerokość detekcji, odległość między wiązkami oraz minimalną wielkość wykrywanego obiektu.
Fotodetektory odbiciowe
Cecha charakterystyczną tego rodzaju czujników jest to, że emiter i detektor są umieszczone w jednej obudowie. Wykrywanie obiektów odbywa się przez emisję wiązki światła w ich stronę i oczekiwanie na powrót odbitego od obiektu światła. Obiekt wykryty jest natychmiast po odbiorze odbitego światła. Jeśli przed sensorem nie zostanie umieszczony żaden obiekt, wówczas światło nie będzie odbijane od powierzchni i nie wróci do odbiornika.
Zaletą tego typu sensorów jest prosta instalacja – nie ma potrzeby precyzyjnego ustawiania reflektorów, a montaż przebiega bardzo szybko. Wadą jest ograniczony zasięg – w praktyce maksymalna odległość detekcji to ok. 2 m. Czujniki tego typu wykorzystywane do detekcji początków i końców produktów na taśmach produkcyjnych. Fotodetektory odbiciowe najczęściej pracują w trybie, w którym wyjście jest aktywowane, gdy czujnik wykryje obiekt.
Czujniki refleksyjne
W czujnikach refleksyjnych, nadajnik i odbiornik również montowane są we wspólnej obudowie. Nadajnik emituje wiązkę światła w kierunku odbłyśnika. Jeśli nadajnik jest poprawnie wycelowany w odbłyśnik, światło po wyjściu z nadajnika przechodzi przez soczewkę, filtr polaryzacyjny, odbija się od odbłyśnika i trafia z powrotem do fotoprzekaźnika. Pojawienie się obiektu w obszarze pracy czujnika powoduje przerwanie wiązki, a więc wzbudzenie czujnika. Czujniki refleksyjne wykonuje się zwykle w układach dwusoczewkowych lub jednosoczewkowych z tzw. autokolimacją. Zaletą autokolimacji jest to, że światło jest wysyłane oraz wraca tą samą soczewką. Dzięki temu nie występuje tzw. martwa strefa, a sensor może wykrywać obiekty znajdujące się tuż przed swoją obudową.
Cechą charakterystyczną tych czujników jest nieco bardziej skomplikowany montaż, niż w przypadku sensorów odbiciowych wymagających zestrajania. Podstawową zaletą jest większy zasięg, który w praktyce może wynieść nawet do 12 m. Co więcej, czujniki te są znacznie bardziej uniwersalne i niewrażliwe na kolor wykrywanych obiektów. Mało tego, mogą wykrywać obiekty praktycznie przezroczyste, np. szklane.
Bariery świetlne
Fotoprzekaźniki występują też w wersjach z rozdzielonym nadajnikiem i odbiornikiem. Nadajnik oraz detektor umieszczone są w oddzielnych obudowach i są niezależnie zasilane. Wiązka światła emitowana jest bezpośrednio przez nadajnik w kierunku odbiornika, wzdłuż osi optycznej układu. Jak można się domyślić, odbiornik i nadajnik umieszcza się naprzeciwko siebie w skrajnych punktach zasięgu. Przesłonięcie wiązki promieni świetlnych przez obiekt powoduje przerwanie transmisji i przełączenie obwodu wyjściowego czujnika.
Ten typ czujników, nazywanych często barierami świetlnymi lub układami z wiązką przechodzącą, stosuje się w procesach identyfikacji obiektów nieprzezroczystych, także takich, które odbijają promienie świetlne. Konstrukcja ta sprawia, że bariery świetlne pozwalają na uzyskanie największych zasięgów działania, nawet do 50 metrów.
Warto też wspomnieć, że bariery świetlne dostępne na rynku wykonywane są w wersjach jedno- i wielowiązkowych. Te ostatnie sprzedawane są m.in. w postaci przygotowanych do montażu listew zawierających szereg nadajników lub odbiorników. Znajdują one zastosowanie przede wszystkim w instalacjach bezpieczeństwa, gdzie pozwalają na monitorowanie wtargnięcia pracownika w obszar roboczy maszyn.
Czujniki światłowodowe
Ograniczona przestrzeń potrzebna do montażu oraz potrzeba stosowania czujników optycznych w miejscach trudnodostępnych sprawiły, że powstała kategoria czujników nazywana sensorami światłowodowymi. Niezależnie od budowy, elementem wyróżniającym tę grupę produktów są światłowody doprowadzające sygnały świetlne z emitera do detektora przez obszar detekcji. Dzięki temu sensory mogą być montowane w miejscach oddalonych od punktu pomiaru i wykorzystywane w pomiarach w miejscach trudnodostępnych lub niekorzystnych środowiskowo, np. tam, gdzie panuje wysoka temperatura.
Sensory światłowodowe składają się z nadajnika ze źródłem światła, modulatora, odbiornika w postaci detektora światła wraz z demodulatorem oraz światłowodów doprowadzających impulsy świetlne do elementów modulatora i detektora. Czujniki tego typu dzieli się na sensory punktowe, pseudorozproszone oraz rozproszone. W wypadku sensorów punktowych wielkość mierzona wyznaczana jest w jednym punkcie, natomiast czujniki wielopunktowe noszą nazwę pseudorozproszonych. W sensorach rozproszonych głowicą pomiarową nie jest punktowy lub matrycowy fotodetektor, ale cała długość światłowodu.
W czujnikach punktowych, światłowód używany jest tylko do transmisji sygnału świetlnego. Można tu mieć do czynienia zarówno z czujnikami odbiciowymi, jak i transmisyjnymi. Światłowodowe czujniki odbiciowe występują w dwóch wersjach – z dwoma światłowodami i reflektorem lub z jednym światłowodem i reflektorem. W pierwszym przyypadku jednym włóknem światło przesyłane jest w kierunku powierzchni odbijającej, natomiast drugim promień odbity dociera do detektora sygnału. W drugim modelu, sygnał odbity wraca do detektora tym samym światłowodem, ale wymagana jest obecność płytki światłodzielącej, która pozwala rozróżnić promień odbity od nadawanego.
W tym miejscu warto też wspomnieć, o czujnikach laserowych. Ze względu na charakterystykę laserowego źródła światła, które cechuje się małym kątem bryłowym generowanej wiązki, często sensory stosowane są do wykrywania, wykonywania pomiarów lub określania położenia małych obiektów z dużą dokładnością. Czujniki laserowe stosowane są również przy budowie barier świetlnych, a także w aplikacjach, w których podstawowym wymaganiem są duże, wynoszące do kilkudziesięciu, a niekiedy nawet ponad 100 m zakresy działania.
Czujniki szczelinowe
Czujniki szczelinowe to sensory, które pod względem zasady działania, są praktycznie identyczne z barierami świetlnymi, ale różnią się budową, gdyż detektor i odbiornik znajdują się w jednej obudowie. Sensory szczelinowe mają bardzo małe obszary detekcji – jedynie szczelinę, jaka znajduje się między emiterem. Wykorzystuje się je w systemach produkcyjnych, np. do wykrywania znaków na taśmie, kontroli ciągłości taśmy czy wykrywania niewielkich przedmiotów transportowanych zautomatyzowaną taśmą produkcyjną. Stosowane są też przy wykrywaniu otworów bądź zębów w kołach zębatych.
Czujniki szczelinowe wykorzystywane są przede wszystkim w szybkich procesach produkcyjnych, a ich widełkowy kształt obudowy – na jednym ramieniu widełek zamontowany jest nadajnik, na drugim odbiornik – eliminuje potrzebę ustawiania osi optycznych, co ułatwia ich montaż na linii produkcyjnej. Tego typu czujniki mają niewielki zakres działania – zwykle 10–30 mm, ale za to mogą wykrywać obiekty o niewielkich wymiarach ,nawet o wielkości ok. 0,3 mm.
Czujniki analogowe
Ostatnią grupą czujników są sensory analogowe. Te fotodetektory pozwalają nie tylko wykrywać obecność obiektów, ale też określać ich odległość od detektora. Na wyjściu otrzymywany jest sygnał analogowy prądowy lub napięciowy proporcjonalny do odległości między czujnikiem a wykrywanym obiektem. Często wykorzystuje się je do precyzyjnego pomiaru wielkości liniowych, parametrów elementów przemieszczających się lub wykonujących drgania.
Kamery CCD
Do wykrywania obecności obiektów coraz częściej stosuje się kamery CCD i systemy wizyjne. Pozwalają one na wykonywanie różnego rodzaju zadań związanych z przetwarzaniem obrazu. Systemy wizyjne standardowo mają zaimplementowane biblioteki podstawowych algorytmów przeznaczonych do przetwarzania różnego rodzaju obrazów w czasie rzeczywistym oraz do obróbki danych wideo. Można je wykorzystać do wykrywania obiektów pojawiających się w polu widzenia kamery. Pamiętać jednak należy, że z uwagi na specyficzny charakter zastosowań tego systemów wizyjnych możliwość ich programowania charakteryzują się w pewnym stopniu ograniczoną elastycznością.
Współczesne czujniki wizyjne mogą komunikować się z kontrolerem lub komputerem za pomocą standardowo wykorzystywanych w przemyśle magistral komunikacyjnych takich, jak sieci Ethernet. Siecią tą można wysyłać duże ilości danych rejestrowanych wewnątrz całego przedsiębiorstwa. Zastosowanie w systemach wizyjnych wyjść i wejść cyfrowych z rozszerzonymi możliwościami komunikacyjnymi, współpracujących np. z kontrolerami wieloosiowymi czy sterownikami PLC, pozwala użytkownikom bez problemu dostosować system wizyjny do kontroli produkcji czy sterowania dowolną linią produkcyjną.
źródło: Automatyka 10/2022
Słowa kluczowe
automatyka, czujniki, czujniki optyczne, czujniki zbliżeniowe, pomiary
Komentarze
blog comments powered by Disqus