Skanery do śledzenia spoiny on-line
Marek Pachuta, Zbigniew Pilat drukuj
O jakości połączeń spawanych decydują: przygotowanie łączonych detali, ustawienie procesu i prowadzenie palnika. W stanowiskach zrobotyzowanych trajektoria ruchu palnika jest ustalana na etapie programowania robota. W wielu przypadkach, szczególnie przy łączeniu elementów konstrukcji o znacznych gabarytach, trajektoria ta musi być modyfikowana przy kolejnej zmianie detali spawanych, jak też w trakcie procesu. Dostępne rozwiązania, bazujące na różnych typach systemów sensorycznych, umożliwiają zmianę trajektorii robota w trakcie spawania, czyli w trybie on-line, w zależności od zmian położenia i geometrii detali i palnika.
Według ostatniego raportu międzynarodowej organizacji robotowej IFR (International Federation of Robotics) około 29 proc. wszystkich robotów zainstalowanych w przemyśle pracuje dzisiaj przy procesach spawalniczych. Nic nie wskazuje na to, aby sytuacja miała się zmienić w najbliższym czasie. Spośród robotów wprowadzonych w 2013 r. na rynek, 28 proc. znalazło zastosowanie również w spawalnictwie. Są to przede wszystkim stanowiska i linie spawania łukowego oraz zgrzewania punktowego, pracujące głównie w przemyśle motoryzacyjnym.
W przypadku spawania łukowego, czynniki decydujące o jakości połączeń spawanych można podzielić na trzy grupy:
- przygotowanie detali przeznaczonych do spawania (dokładność wymiarów, stan powierzchni, dla grubszych elementów jakość ukosowania),
- odpowiednie ustawienie procesu (właściwy wybór technologii i jej parametrów, dobór materiałów, gazów osłonowych),
- odpowiednie położenie spoiny.
Położenie spoiny wynika przede wszystkim ze sposobu prowadzenia palnika spawalniczego. Na stanowiskach zrobotyzowanego spawania palnikiem operuje robot, dla którego jest to narzędzie robocze. Robot realizuje trajektorię ruchu narzędzia-palnika, zgodnie z tym, jak został nauczony na etapie programowania. Na pewno więc na dokładność położenia spoiny wpływa dokładność pracy robota, w tym wykonywanie tzw. ruchów interpolowanych. Najczęściej jest to prowadzenie narzędzia po prostej lub po okręgu. Współczesne roboty osiągają tu bardzo dobrą precyzję, wystarczającą do zastosowań w spawaniu łukowym. Dlatego w wielu aplikacjach, głównie realizujących łączenie niewielkich elementów, radzą sobie znakomicie, uzyskując dobrą wydajność przy bardzo wysokiej i stabilnej jakości. Jednak przy łączeniu elementów konstrukcji o znacznych gabarytach okazuje się, że raz wyuczona trajektoria musi być modyfikowana przy kolejnej zmianie detali spawanych, jak też w trakcie procesu. Po prostu rzeczywiste położenie złącza spawanego jest inne niż podczas uczenia robota. Wynika to z następujących przyczyn:
- Ustawienie detali spawanych może być inne niż podczas programowania, np. na skutek błędów pozycjonowania, niedokładności przyrządów mocujących, zmienności gabarytów detali (w ramach tolerancji wymiarowej) itp.
- Geometria narzędzia-palnika, tzn. jego pozycja i orientacja względem ramienia robota, może być inna niż podczas programowania, np. na skutek kolizji palnika z elementami stanowiska, zużycia elementów eksploatacyjnych itp.
- Detale spawane mogą zmieniać swoje położenie i/lub orientację podczas samego procesu, np. na skutek odkształceń termicznych materiału. Dodatkowo elementy o dużych gabarytach, które są wykonywane w procesach cięcia, tłoczenia i gięcia, nie zawsze będą „trzymać wymiar”, np. prostoliniowość lub kształt krawędzi mogą się zmieniać w zależności od egzemplarza.
W pierwszych dwóch przypadkach wymagana jest odpowiednia korekcja wyuczonej trajektorii przed spawaniem, czyli w trybie off-line. W ostatniej sytuacji korekcja musi być wykonywana podczas samego procesu spawania, czyli w trybie on-line. Aby możliwa była realizacja takich korekt trajektorii, producenci oferują w swoich robotach specjalne funkcje i mechanizmy. Do ich prawidłowego i skutecznego działania konieczne jest wyposażenie robota w odpowiednie systemy sensoryczne, które dostarczą układowi sterowania niezbędne informacje.
W artykule przedstawiono różne typy systemów sensorycznych używanych w stanowiskach zrobotyzowanych do obserwowania rzeczywistego położenia złącza spawanego (pot. szwu) i odpowiedniej korekty trajektorii narzędzia-palnika w czasie spawania, a więc w trybie on-line. Rozwiązanie to nazywane jest „śledzeniem szwu/ścieżki” (z ang. Seam/Path Tracking) i jest dzisiaj oferowane przez wszystkich liczących się producentów robotów przemysłowych przeznaczonych do spawania łukowego. Autorzy wykorzystali dostępne materiały firm produkujących roboty i systemy sensoryczne, a także własne doświadczenia z wdrożeń zrobotyzowanych instalacji spawania łukowego, realizowanych w ostatnich latach dla odbiorców przemysłowych oraz prowadzonych prac badawczo-rozwojowych.
Różne konfiguracje zrobotyzowanych stanowisk spawania
Generalnie można przyjąć, że każde zrobotyzowane stanowisko spawalnicze składa się z następujących grup podzespołów i urządzeń:
- system robota przemysłowego przystosowany do współpracy z zestawem spawalniczym,
- zestaw spawalniczy przystosowany do współpracy z robotem,
- układ sterowania stanowiska – najczęściej PLC w odpowiedniej konfiguracji, na ogół z panelem operatorskim realizującym funkcje HMI,
- system pozycjonowania i mocowania detali spawanych,
- system zabezpieczenia stanowiska, np. ogrodzenia, osłony, bariery dostępu, sygnalizacja,
- system dostarczania detali do spawania i odbioru gotowych, pospawanych zespołów, np. magazyny/pola odkładcze, żurawiki, transportery,
- wyposażenie dodatkowe, np. czyszczarka palnika, obcinaczka drutu, urządzenia filtrowentylacyjne.
Na rysunku 1 przedstawiono przykładowe rozmieszczenie elementów typowego stanowiska.
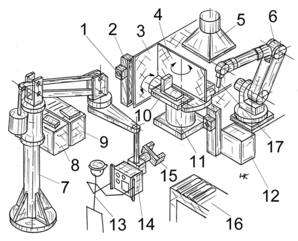
Rys. 1. Przykładowe rozmieszczenie elementów zrobotyzowanego stanowiska spawalniczego 1 – stop awaryjny, 2 – kurtyna świetlna, 3 – ściana osłonowa, 4 – ekran ochronny, 5 – wyciąg dymu, 6 – robot, 7 – manipulator, 8, 9 – podajniki wejściowe, 10 – narzędzie spawalnicze, 11 – pozycjoner spawalniczy, 12 – układ sterowania, 13 – operator, 14 – panel operatora, 15 – chwytak, 16 – podajnik wyjściowy, 17 – głowica-palnik spawalniczy
W praktyce konfiguracja zrobotyzowanego stanowiska spawania jest zawsze dostosowana do warunków aplikacji i zależy od wielu czynników. Stanowisko to musi być dopasowane do zadania produkcyjnego oraz spełniać szczegółowe wymagania odbiorcy. Wybór konkretnych rozwiązań jest dokonywany na etapie opracowania projektu robotyzacji określonego procesu produkcyjnego. Na początku, wspólnie z przyszłym użytkownikiem, opracowywane są szczegółowe wymagania techniczne, które zawierają m.in.:
- ogólne rozplanowanie dostosowane do warunków lokalizacji,
- parametry detali i podzespołów przewidzianych do spawania (gabaryty i ciężar),
- wymagania dla procesu spawania,
- typ manipulatora robota (konfiguracja kinematyczna) oraz jego zasięg i udźwig,
- wymagane parametry ruchu robota – prędkość i dynamika ruchów, dokładność i powtarzalność,
- komunikację robota z otoczeniem – rodzaj, liczba i parametry kanałów wejść/wyjść,
- warunki włączenia stanowiska w strukturę zakładu (drogi komunikacyjne, trasy zasilania, sposób dostarczania detali i odbioru wyrobów itp.),
- wyposażenie dodatkowe, np. pokrowiec ochronny, sprzęgło antykolizyjne.
Te dane są wykorzystywane przy opracowaniu projektu technicznego stanowiska. Pierwszym, bardzo ważnym krokiem jest ustalenie szczegółowej konfiguracji i rozmieszczenia elementów stanowiska. Stosowane konfiguracje zrobotyzowanych stanowisk spawalniczych można podzielić na pięć typów:
- Robot spawalniczy współpracuje z jednym systemem pozycjonująco-mocującym. Najczęściej jest to obrotowy stół (pozycjoner) spawalniczy. Jest to rozwiązanie najprostsze, jednak zapewnia pełną funkcjonalność. Stoły pojedyncze spotyka się najczęściej w wykonaniu jedno- lub dwustanowiskowym.
- Dla produktów o dużych gabarytach stosuje się konfigurację, w której robot obsługuje dwa pozycjonery jednostanowiskowe. Każdy pozycjoner ma co najmniej jedną oś sterowaną. Na ogół jest to oś pionowa lub pozioma. Jest to rozwiązanie dedykowane do łączenia elementów, które wymagają zmiany orientacji przestrzennej w trakcie procesu spawania. Każdy typ pozycjonera może być rozbudowywany przez dodanie kolejnych osi, które mogą być sterowane z układu robota, jako tzw. osie zewnętrzne.
- Zastosowanie dwóch współpracujących ze sobą robotów przemysłowych, z których jeden pełni rolę pozycjonera, manipulując detalem, a drugi prowadzi palnik spawalniczy. Robot pełniący rolę pozycjonera charakteryzuje się zazwyczaj udźwigiem od kilkudziesięciu do kilkuset kilogramów.
- W przypadku, gdy elementy spawane są produkowane na liniach, ze względu na koszty, jak również problemy organizacyjne, stanowiska zrobotyzowane są instalowane wprost na ciągach transportowych. W obszarze gniazda spawania montuje się odpowiednie stopery, zatrzymujące detale oraz układy, które te detale pozycjonują. Następnie robot przystępuje do wykonania operacji spawalniczych.
- Przy spawaniu dużych konstrukcji stosuje się standardowe roboty spawalnicze, instalowane na specjalnych konstrukcjach wsporczych, jednoosiowych torach jezdnych (naziemnych lub podwieszonych) lub wieloosiowych portalach.
Do spawania elementów o dużych gabarytach, gdzie problem śledzenia spoiny on-line jest szczególnie istotny, stosuje się najczęściej konfigurację 2, 4 lub 5.
Sterowanie w zrobotyzowanych stanowiskach spawania
Większość urządzeń wchodzących w skład instalacji zrobotyzowanego spawania wyposażanych jest dzisiaj w inteligentne sterowanie, programowalne i zapewniające komunikację za pośrednictwem sygnałów cyfrowych lub przemysłowych sieci komputerowych. Umożliwia to dostosowanie właściwości funkcjonalnych urządzenia do warunków aplikacji (wybór trybu pracy, ustawienie parametrów) na drodze programowej. Dzięki temu możliwa jest też wymiana bogatych w treść informacji, np. diagnostycznych, dotyczących stanu samych urządzeń, jak też przebiegu procesu. Rozwiązania te pozwalają także włączyć sterowniki urządzeń stanowiska zrobotyzowanego – wprost lub poprzez sieć zakładową – do sieci globalnej Internet. Wtedy nadzór, monitoring, a czasem i serwis takiej instalacji w trybie zdalnym może być realizowany z dowolnego miejsca na świecie, przez integratora, konsultantów dostawców lub producentów nadzorowanych urządzeń. Na rysunku 2 przedstawiono schemat ogólny przepływu informacji w takim typowym zrobotyzowanym gnieździe spawalniczym. Czujniki systemów sensorycznych stosowane w zrobotyzowanym spawaniu są montowane na ramieniu robota lub na elementach stałych stanowiska. Są one dołączane wprost do układów sterowania robotów lub do sterowników gniazd zrobotyzowanych. Proste czujniki komunikują się za pomocą sygnałów dwustanowych lub analogowych. Bardziej zaawansowane współpracują często ze specjalizowanymi sterownikami (kontrolerami) przetwarzającymi wstępnie uzyskane sygnały. Dopiero z tych sterowników informacja jest przesyłana do sterownika robota lub gniazda. Do tego zadania wykorzystuje się komunikację sieciową.
Systemy sensoryczne stosowane w zrobotyzowanym spawaniu
Systemy sensoryczne stosowane w zrobotyzownym spawaniu do korekcji trajektorii ruchu narzędzia-palnika można podzielić w zależności od przyczyny błędów, a nastepnie zastosowanych rozwiązań technicznych (rys. 3).
Korekcja trajektorii off-line (Seam/Path Finding)
Pomiary w celu wykonania korekcji off-line trajektorii ruchu robota dokonywane są przy użyciu systemu sensorycznego przed wykonaniem operacji spawania. Mają one na celu odpowiednie zmodyfikowanie wyuczonej trajektorii, a przez to wyeliminowanie niepoprawnego spawania, wynikającego z niedokładnego ułożenia detali względem robota, już w fazie wstępnej. W praktyce stosowane są cztery rozwiązania:
- Określanie położenia spoiny przez dotykanie charakterystycznych punktów na spawanych detalach nosi nazwę Touch Sense. Firmy produkujące roboty przemysłowe oferują pakiety technologiczne, które umożliwiają obsługę dwustanowego czujnika wykrycia elementu. Czujnik ten przyłączany jest na jedno z wejść robota. Jako czujnik dotykowy wykorzystany jest przeważnie drut spawalniczy. Producenci spawarek przeznaczonych do pracy z robotem wyposażają je w funkcje umożliwiające takie działania.
- Pomiar typu Touch Sense może być wykonany także bez fizycznego dotykania detalu. Zwykle do tego celu używane są czujniki do pomiaru odległości, mierzące położenie charakterystycznych części detalu (ostre krawędzie, zagięcia itp.). Przeważnie są to programowalne układy pomiaru odległości od detalu, z dwustanowym wyjściem informującym, że odległość jest większa lub mniejsza od wartości zaprogramowanej. Czujnik taki montuje się na ramieniu robota, najczęściej wiążąc go mechanicznie z mocowaniem palnika, a jego wyjście sygnałowe przyłączane jest na jedno z wejść szybkich robota.
- Specjalizowane skanery laserowe do określania położenia samej spoiny na podstawie pomiarów jej charakterystycznych parametrów. Skanery te, często zwane w literaturze czujnikami profilu, wykorzystują w swym działaniu zasadę pomiaru triangulacyjnego w celu uzyskania dwuwymiarowego profilu powierzchni wykonanych z dowolnych materiałów. Obraz profilu przetwarzany jest w kontrolerze czujnika, który określa odległość powierzchni spoiny od czujnika, jak i jej położenie w polu widzenia czujnika.
- Systemy wizyjne 2D (przy zastosowaniu jednej kamery) pozwalają określić położenie detalu i jego obrót na płaszczyźnie. Przy zastosowaniu dwóch kamer można realizować pomiar położenia typu 3D, czyli w przestrzeni trójwymiarowej. Sterowniki systemów wizyjnych to na ogół dość silne, specjalizowane komputery. Umożliwiają one przetwarzanie zgromadzonych obrazów w celu określenia położenia charakterystycznych fragmentów detalu (np. krawędzi, linii styku dwóch detali, punktów sczepienia).
Korekcja off-line opisu narzędzia (TCP)
W przypadku, gdy zmianie uległa geometria narzędzia-palnika, można ponownie dokonać jego opisu. Narzędzie, a właściwie jego punkt roboczy TCP (Tool Center Point), definiowane jest na końcu drutu wysuniętego z dyszy palnika na określoną długość. Pełny opis narzędzia zawiera – oprócz położenia TCP w układzie współrzędnych związanych z ostatnim członem robota – również jego orientację. Większość producentów robotów do spawania oferuje, jako opcje, funkcje automatycznej weryfikacji (sprawdzenia) poprawności opisu narzędzia, jak i jego kalibracji (definiowania), zarówno w zakresie samego TCP, jak też pełnego opisu (wraz z orientacją). Są to na ogół zestawy sprzętowo-programowe, współpracujące z układem sterowania robota.
Korekcja trajektorii on-line (Seam/Path Tracking)
Pomiary w celu wykonania korekcji on-line trajektorii ruchu robota dokonywane są za pomocą systemu sensorycznego w czasie realizacji operacji spawania. System taki musi być odporny na warunki środowiskowe towarzyszące procesowi oraz zapewniać odpowiednią szybkość, aby uzyskana informacja mogła być na bieżąco wykorzystana. Istnieją dwa podstawowe sposoby realizacji pomiarów i korekcji on-line trajektorii ruchu robota:
- Korekta trajektorii na podstawie pomiaru parametrów spawania. W tym przypadku robot, prowadząc palnik podczas spawania, musi wykonywać nim oscylacje. Powinny one być periodyczne (np. sinusoidalne, typu piła lub trapez), prostopadłe do ścieżki (szczeliny) spawania. System na bieżąco wykonuje pomiar parametrów łuku, m.in. prądu spawania. Na podstawie analizy wartości tych parametrów, z uwzględnieniem przebiegu ruchu oscylacyjnego, program robota oblicza odchyłki trajektorii palnika od szczeliny i wypracowuje korekty dla realizacji ruchu spawania, tak aby spoina została położona dokładnie na szczelinie. Producenci robotów oferują specjalne pakiety realizujące korekcje on-line na podstawie pomiaru parametrów łuku. Przykładem może być oprogramowanie KUKA.ArcSense firmy KUKA lub Weldguide III w robotach ABB.
- Korekta trajektorii przy użyciu skanerów laserowych. W przypadku tej metody (fot. 1) sterownik skanera rozpoznaje położenie spoiny na podstawie analizy charakterystycznych punktów na konturze, uzyskanym przez przecięcie się wiązki laserowej emitowanej z czujnika z fragmentem detalu zawierającym spoinę. Najczęściej stosuje się różne algorytmy identyfikacji dla różnych typów złącz spawanych. Dlatego operator musi zawsze wybrać, jaki typ złącza ma być śledzony. Należy zaznaczyć, że ta realizacja śledzenia należy do najdroższych metod. Jej praktyczne wykorzystanie wymaga też wykwalifikowanego personelu, zarówno programisty, jak i operatora stanowiska zrobotyzowanego. Firmy robotowe oferują oprogramowanie technologiczne, które umożliwia korektę trajektorii ruchu robota na bieżąco w trakcie procesu spawania na podstawie pomiaru położenia spoiny. Są to jednak pakiety dość skomplikowane w programowaniu i użyciu.
Skanery laserowe do korekcji trajektorii on-line
Do współpracy ze skanerami laserowymi firmy robotowe oferują oprogramowanie technologiczne, które umożliwia korektę trajektorii ruchu robota na bieżąco w trakcie procesu spawania na podstawie pomiaru położenia spoiny (np. pakiet KUKA.SeamTech Tracking 2.0). Warunkiem prawidłowego działania tych funkcji jest sensor dokładny, niezawodny i szybki. Pomimo że sama idea, jak też zasada pracy takiego czujnika, są znane od kilkudziesięciu lat, dzisiaj tylko trzy firmy na świecie oferują rozwiązania, które spełniają wymagania pracy w pobliżu procesu spawania łukowego.
Najdłużej tematem zajmuje się angielska firma Meta Vision, założona w 1984 r. przez grupę badaczy z uniwersytetu Oxford. Była to jedna z pierwszych udanych prób powołania tzw. spin-off (choć wtedy tego pojęcia w zarządzaniu jeszcze nie używano), w celu komercjalizacji technologii opracowanej w jednostce naukowej. Firma ta swój pierwszy model systemu laserowego do śledzenia spoiny on-line zaprezentowała w 1985 r. Dzisiaj oferuje całą gamę inteligentnych systemów do monitorowania procesów spawalniczych oraz inspekcji wykonanych połączeń spawanych. Do śledzenia we współpracy z robotami przemysłowymi przeznaczony jest system Smart Laser Pilot (SLP), którego sercem jest czujnik SLS (Smart Laser Sensor). Firma ma przedstawicielstwa w Kanadzie i w Niemczech, przy czym przedstawicielstwo w Niemczech, będące w istocie firmą partnerską o nazwie Meta Scout, obsługuje także teren Polski.
Również w Niemczech ma swoją siedzibę firma Scansonic, która oferuje rodzinę systemów śledzących TH6D. Cała firma, tzn. część laboratoryjna, produkcyjna i dział aplikacji/sprzedaży mieści się w Berlinie. Jest to bardzo prężne przedsiębiorstwo. Powstało w 2000 r., a dzisiaj ma przedstawicielstwa/partnerów na całym świecie, od Ameryki Południowej aż po Daleki Wschód.
Kanadyjska firma Servo Robot formalnie powstała rok przed Meta Vision, jednak pierwszy laserowy system sensoryczny do spawania przedstawiła później, bo około roku 1990. Dzisiaj jednak to ta firma jest największym światowym dostawcą systemów śledzenia spoiny on-line. Jej flagowy system Power Track wykorzystuje czujnik laserowy POWER-CAM.
Wspólną cechą rozwiązań wszystkich trzech firm jest dwumodułowa budowa systemu sensorycznego. Głowica pomiarowa (używa się określenia czujnik, skaner lub kamera laserowa) jest montowana na ramieniu robota, w pobliżu palnika – tak aby „widzieć” trasę przed palnikiem. Sterownik, zabudowany w osobnej skrzynce, jest instalowany z dala od procesu spawania. Wszystkie one łączą się z układem sterowania robota przez szeregową magistralę Ethernet (TCP/IP).
Zasada działania czujników przeznaczonych do śledzenia spoiny (Seam Tracking) jest podobna do zasady działania czujników służących do określania jej położenia (Seam Finding). Sterowniki rozpoznają położenie spoiny na podstawie analizy położenia charakterystycznych punktów na konturze, uzyskanym przez przecięcie się wiązki laserowej emitowanej z czujnika z fragmentem detalu zawierającym spoinę. W celu zmniejszenia wpływu zakłóceń ze środowiska na wynik pomiarów niektóre czujniki wysyłają kilka równoległych wiązek laserowych (zwykle trzy lub pięć), przez co uzyskuje się redundancję pomiarów. Dodatkowo można uzyskać informację o zmianie kąta orientacji narzędzia względem spoiny. Punkty charakterystyczne spoiny używane do pomiarów zależą od typu spoiny. Zadaniem programisty jest wybranie tego typu spośród znajdujących się w banku danych sterownika czujnika, określenie punktu charakterystycznego, wzdłuż którego ma przesuwać się punkt TCP (koniec drutu spawalniczego) oraz wprowadzenie parametrów spoiny. Zadania te wykonuje programista za pomocą oprogramowania dostarczonego przez producenta czujnika.
Dla poprawnej współpracy czujnika z robotem należy także przeprowadzić tzw. kalibrację czujnika zainstalowanego na ramieniu robota. Kalibracja ma na celu powiązanie współrzędnych czujnika ze współrzędnymi robota i wykonywana jest przeważnie przy użyciu specjalnej płytki kalibracyjnej. Jej postać, jak i sposób kalibracji opracowywane są przez producenta czujnika we współpracy z producentem robota.
Pomiar położenia spoiny odbywa się w sposób ciągły z określonym taktem, a wynik analizy przekazywany jest do układu sterowania robota, w postaci uzgodnionej przez wytwórców czujników i robotów i stanowi tajemnicę firm. Program robota koryguje na tej podstawie, także w sposób ciągły, zaprogramowaną wcześniej na detalu wzorcowym trajektorię ruchu palnika spawalniczego.
Czujniki do Seam Tracking wyposażone są w instalację do jego chłodzenia w czasie pracy. Może to być chłodzenie powietrzem, jak również za pomocą cieczy chłodzącej. Mają one także dysze, za pomocą których do układu optycznego doprowadzone jest sprężone powietrze, chroniące go przed kurzem, dymem i oparami. Części optyczne szczególnie narażone na działanie środowiska, a w szczególności szybka osłaniająca wyjście/wejście wiązki laserowej, są łatwo demontowalne i wymienialne.
Wszystkie trzy wspomniane wyżej firmy oferują całą gamę systemów śledzenia spoiny. Do analizy wybrano konkretne modele. Kanadyjska firma Servo-Robot oferuje system Power Track, pracujące z czujnikami typu POWER-CAM (fot. 2). Wytwarzane są one w dwóch odmianach: POWER-CAM/HR (z rozdzielczością W × H = 0,016 × 0,025 mm) dla blach wykonanych z dużą dokładnością oraz POWER-CAM (z rozdzielczością W × H = 0,05 × 0,09 mm, ale większym zakresem pomiaru) dla blach wykonanych z mniejszą dokładnością.
Czujniki SLS (Smart Laser Sensor) z angielskiej firmy Meta Vision Systems również produkowane są w trzech wykonaniach: SLS-025 (pole widzenia 25 mm), SLS-050 (pole widzenia 50 mm, rozdzielczość W × H = 0,05 × 0,08 mm) i SLS-100 (pole widzenia 100 mm).
Czujniki systemu TH6D z niemieckiej firmy Scansonic (fot. 3) wykonywane są również w dwóch wersjach: TH6D-150-CFAA-AB (rozdzielczość W × H = 0,03 × 0,07 mm) i TH6D-150-KFAA-AB (rozdzielczość W × H = 0,08 × 0,12 mm).
Poniżej zebrano podstawowe parametry modeli systemów sensorycznych przeznaczonych do śledzenia on-line w zrobotyzowanych stanowiskach spawalniczych, oferowanych przez trzech liderów światowych w tym obszarze.
Podsumowanie
Wykorzystanie skanera laserowego do pomiaru on-line położenia złącza spawanego (seam tracking) nie jest metodą nową. Prace badawcze w tym obszarze były prowadzone już w latach 70. i 80. ubiegłego wieku. Od połowy lat 80. na rynku są oferowane rozwiązania przemysłowe. Wciąż nie są to jednak urządzenia tanie, głównie ze względu na trudne środowisko, w którym mają niezawodnie pracować. Właśnie cena jest obecnie największą barierą szerszego upowszechnienia tych systemów. Kompletny zestaw do wyposażenia robota to dzisiaj wydatek od kilkunastu do ponad czterdziestu tysięcy euro.
Wpływ warunków środowiskowych (światło, temperatura, zapylenie, zadymienie) jest również wciąż najpoważniejszym problemem technicznym, z którym tylko nieliczni sobie radzą. Niska skuteczność i niezadowalająca niezawodność systemów sensorycznych to kolejny powód ostrożności użytkowników przy podejmowaniu decyzji o ich zakupie.
Trzeba też pamiętać, że śledzenie spoiny w trybie on-line nie nadaje się do wszystkich aplikacji. Przede wszystkim spoiny nie mogą być zbyt krótkie. Musi też być do nich lepszy dostęp niż w przypadku spawania bez czujnika. Po prostu kamera laserowa zamontowana w pobliżu palnika znakomicie ogranicza jego możliwości penetracyjne. To powoduje, że systemy korekcji trajektorii z wykorzystaniem skanerów laserowych są wykorzystywane przede wszystkim przy produkcji elementów o dużych gabarytach.
Stosowanie skanerów laserowych jest mocno wspierane przez firmy produkujące roboty przemysłowe, przeznaczone w znacznej części do wykonywania aplikacji spawalniczych. Oferują one oprogramowanie technologiczne, obsługujące czujniki tego typu i realizujące korekcję trajektorii narzędzia robota. Rozwój możliwości robotów w zakresie wykorzystania informacji zbieranych przez zaawansowane systemy sensoryczne daje nadzieję na rozszerzenie obszaru ich zastosowania. To powinno doprowadzić do wzrostu zapotrzebowania, a w dalszej perspektywie do spadku cen tych czujników.
Szansą na obniżenie kosztów zakupu zaawansowanych systemów śledzenia spoin jest również wzrost konkurencji w tej branży. Do prac włączają się firmy, które do tej pory mają już znaczące dokonania w wykorzystaniu techniki laserowej w pomiarach, np. Keyence, Mikro-Epsilon, Sick. Pojawiają się również małe innowacyjne firmy, tworzone przez zespoły z udziałem naukowców i badaczy. Powtórzenie sukcesu Meta Vision wydaje się dziś łatwiejsze niż 20 lat temu. Wynika to przede wszystkim z ogromnego postępu w technologii laserowej, zarówno w samych urządzeniach wykonawczych, jak też w metodach i narzędziach do obróbki zebranych informacji. Oczywiście trzej liderzy rynku też wciąż pracują nad rozwojem już oferowanych urządzeń i opracowaniem nowych rozwiązań.
Przedstawione w artykule zaawansowane systemy sensoryczne stanowią pewien zestaw gotowych rozwiązań oferowanych na rynku. Projektant zrobotyzowanego stanowiska spawalniczego, wspólnie z technologiem, dobierają czujnik do warunków konkretnej aplikacji. Trzeba pamiętać, że czujniki zapewniające prawidłowe prowadzenie palnika nie są jedynymi elementami sensorycznymi w zrobotyzowanych stanowiskach spawania. W dzisiejszych instalacjach stosuje się różnorodne systemy zabezpieczenia, czujniki kontroli dostępu, ciśnienia gazu, końca drutu w zasobniku. W laboratoriach firm i ośrodkach badawczych prowadzone są prace nad integracją wielu różnych sensorów w jednym stanowisku. Zmierzają one do zaangażowania znacznie rozbudowanych komputerowych układów sterowania. Wiele zespołów pracuje również nad zastosowaniem najnowszych rozwiązań wizyjnych do korekcji trajektorii on-line podczas spawania. Niska odporność systemów wizyjnych na niekorzystne warunki panujące w pobliżu spawania jest głównym powodem, że prace te wciąż prowadzone są głównie w laboratoriach. W każdej chwili można jednak spodziewać się przełomu w tym temacie.
Niniejsza praca powstała w toku realizacji projektu E!IIPL-IL/05/02/2013 „RobWeld Super-MIG® Robotized Welding With Use of New Generation of Hybrid System Based on Super Heavy Duty Super MIG Concept”, w ramach Inicjatywy EUREKA przy dofinansowaniu przez Narodowe Centrum Badań i Rozwoju.
źródło: Automatyka 6/2015
Komentarze
blog comments powered by Disqus