Przemysł 4.0 w polskich realiach
Marcin Karbowniczek drukuj
Nie da się ukryć, że na naszych oczach odbywa się czwarta rewolucja przemysłowa. W odróżnieniu od poprzednich, rewolucyjnych zmian w przemyśle, tym razem implementowane nowatorskie rozwiązania cechują się ogromną różnorodnością. Łączy je tylko wspólna idea – maksymalne wykorzystanie sensorów i zbiorczego przetwarzania danych, by jak najbardziej zwiększyć wydajność produkcji, obniżyć jej koszty i usprawnić logistykę. Jak to wszystko wygląda w praktyce? Z przeprowadzonych analiz wynika, że sytuacja rysuje się dosyć ciekawie.
Przemysł 4.0 to główny temat wielu targów i konferencji przemysłowych na całym świecie. Choć czwarta rewolucja przemysłowa jest nazywana w ten sposób głównie w Europie, a w USA częściej można spotkać się zterminem „Industrial Internet of Things” lub po prostu „Industrial Internet”, pojęcia te są na tyle ogólne, że w praktyce obejmują ten sam zakres. Być może nawet to amerykańskie określenie jest bliższe temu, z czym Przemysł 4.0 się wiąże. W końcu hasło IoT zostało spopularyzowane z inicjatywy firmy Intel. Ten producent półprzewodników poszukiwał sposobu na promocję nowoczesnych rozwiązań M2M i sięgnął po niewiele mówiące określenie z końca ubiegłego wieku, które spodobało się odpowiednio dużej grupie pracowników. I trzeba przyznać, że czwarta rewolucja przemysłowa bazuje na komunikacji Machine-to-Machine na ogromną skalę, korzystając ze wszelkich możliwości z niej płynących.
Różne wizje rewolucji
Nadal – bo od pierwszych inicjatyw niemieckiego rządu, opatrzonych nazwą „Industrie 4.0” minęło już 6 lat – wiele osób pracujących w przemyśle, ale niewczytujących się w prasę, ani nieuczestniczących w szkoleniach branżowych, deklaruje, że nie wie co oznaczają hasła Przemysł 4.0 czy Industrial IoT. Z dokładniejszych rozmów z przedstawicielami polskich firm produkcyjnych wynika, że o ile w każdym większym zakładzie temat Przemysłu 4.0 jest znany, to zagadnienie to jest albo różnie rozumiane, albo tylko wybrani pracownicy „czują” o co chodzi w tym temacie. Wynika to w dużej mierze z faktu, że mało kto jest w stanie całościowo spojrzeć na zakład produkcyjny, a jak wiadomo koncepcja Przemysłu 4.0 przynosi największe efekty, jeśli jest wdrażana na każdym poziomie działania firmy. Dla obeznanych w temacie inżynierów utrzymania ruchu Przemysł 4.0 kojarzy się z monitorowaniem kondycji pomp, podczas gdy w przypadku kadry zarządzającej częściej pojawiają się skojarzenia z monitorowaniem łańcucha dostaw. Wszyscy mają rację, rzecz w tym, że najczęściej znają tylko wycinek całej koncepcji.
Realizacji koncepcji Przemysłu 4.0 oznacza działania Na wielu płaszczyznach Internet rzeczy, Industrie 4.0, Smart Production – nawet jeśli użyjemy innej nazwy, zawsze będzie chodziło o idealne połączenie cyfrowego i realnego świata. Firma KUKA jako wizjoner i prekursor inicjatywy Przemysł 4.0, w dużym stopniu napędza zmiany, których celem jest stworzenie sieciowej i inteligentnej produkcji. Wizja, kryjąca się za kolejną rewolucją przemysłową, łączy człowieka i maszynę w sieć produkcyjną i wymaga maksymalnej elastyczności systemów. Już dziś istnieją inteligentne maszyny, takie jak koboty i platformy, które odzwierciedlają nasze wyobrażenia o robocie przemysłowym. Współpracują one bezpośrednio z człowiekiem, są mobilne, czerpią wiedzę z „chmury”. Kolejna generacja inteligentnych maszyn, obok normalnych robotów przemysłowych posiada wszystkie umiejętności wyróżniające cyber-fizyczne systemy w Internecie rzeczy. Poza tym zwiększona została inteligencja, w celu np. bardziej precyzyjnego sterowania swoimi ruchami. Rozwój koncepcji Industry 4.0 niesie za sobą wielowymiarowość działań przedsiębiorstwa. Zwiększa zapotrzebowania na automatyzację procesów produkcji, czy metod i technologii wytwarzania. W efekcie pojawiają się nowe zagrożenia, dlatego niezbędne jest stosowanie rozwiązań zapewniających bezpieczeństwo zarówno pracowników, jak i maszyn. Tym wymogom całkowicie odpowiada zaprojektowany na wzór ludzkiej ręki robot LBR iiwa, który ze swoją otwartością systemu, funkcjami bezpieczeństwa oraz czucia jest całkowicie gotowy na erę Industry 4.0. |
Trzy szczeble zmian
Przemysł 4.0 odnosi się do niemal każdego aspektu działania zakładu przemysłowego. Na najniższym szczeblu koncentruje się na technologiach. To dzięki nim możliwe jest usprawnienie, przyspieszenie, lub zwiększenie wydajności działania poszczególnych komponentów automatyki. Dzięki licznym sensorom nowoczesne urządzenia i maszyny mają wbudowane zaawansowane funkcje diagnostyczne, których wyniki działania mogą być przekazywane do serwerów. Fakt dotarcia z komunikacją cyfrową nawet do najmniejszych elementów całego systemu sprawia, że z łatwością można pobrać szczegółowe dane pochodzące z dowolnie wybranego elementu prowadzonego procesu. Dzięki temu można też precyzyjnie, a jednocześnie zdalnie wpływać na parametry tych procesów. Osoba kontrolująca przebieg procesów nie musi już poruszać się po zakładzie, by dokonywać odczytów wskazań, ani by za pomocą różnych pokręteł i przycisków zmieniać nastawy. Technologia sprawia, że wszystko to można zrobić zdalnie, choćby za pomocą tabletu.
Aby to było możliwe, konieczne jest wdrożenie idei Przemysłu 4.0 na nieco wyższym poziomie. Dane z poszczególnych urządzeń przemysłowych powinny być zbierane w jednym miejscu i muszą nadawać się do wspólnego przetwarzania. Wynika to z dwóch powodów. Po pierwsze pozostawienie zebranych danych w oddzielnych zbiorach nie upraszcza korzystania z nich. Konieczność przełączania się między wieloma systemami komputerowymi nie przyspiesza pracy ani nie ułatwia wyszukiwania zależności między informacjami. Dopiero integracja systemów i wspólne przetwarzanie danych pozwalają operatorowi na przechodzenie od ogółu do szczegółu i szybkie znajdywanie przyczyn, np. obniżonej jakości produktu.
Drugim powodem jest ogromna ilość danych, jakie generują nowoczesne systemy automatyki przemysłowej. Oczujnikowanie każdego elementu zakładu i zbieranie, a następnie prezentowanie takich surowych danych operatorowi będzie przytłaczające. Jest to pierwszy problem z jakim spotykają się pracownicy utrzymania ruchu, czasem podawany jako argument przeciw wdrażaniu idei Przemysłu 4.0. Dlatego konieczne staje się przygotowanie algorytmów automatycznego, quasi-inteligentnego przetwarzania gromadzonych danych, tak by kierować uwagę operatora jedynie na istotne zdarzenia. Jednocześnie dobrą praktyką jest przygotowanie interfejsów, które pozwalają na poruszanie się od ogółu do szczegółu, a to właśnie wymaga dobrej, sensownej integracji wszystkich podsystemów. Dopiero wtedy zainstalowane sensory zaczynają faktycznie przynosić korzyści.
W jaki sposób przygotować kadrę techniczną do nadchodzącej czwartej rewolucji? Naszym zdaniem należy w pierwszej kolejności postawić na poprawę edukacji. To właśnie system kształcenia ma kluczowe znacznie na drodze do sukcesu przedsiębiorstw we współczesnej gospodarce opartej na wiedzy. Siemens ma własną wizję, jak taka edukacja techniczna powinna wyglądać. Naszym zdaniem najlepsze efekty daje tzw. kształcenie dualne. Zakłada ono udział przedsiębiorstw w przygotowaniu zawodowym przyszłych specjalistów, pozwalając przyszłym inżynierom zdobywać wiedzę i umiejętności praktyczne dostosowane do wymogów i potrzeb pracodawców. Odpowiedni profil kształcenia, dobrany pod kątem potrzeb pracodawcy, skraca również okres adaptacji pracownika w miejscu pracy. Siemens wypracował własne autorskie programy kształcenia dualnego od lat funkcjonujące w Niemczech pod nazwą Akademia Siemensa. Natomiast w Berlinie powołaliśmy Centrum Edukacji Mechatronicznej na prawach szkoły wyższej z certyfikacją międzynarodową. W Polsce wykorzystaliśmy także tę metodykę organizacji kształcenia dualnego wdrażając program mechatroniki wspólnie z Politechniką Lubelską. Oprócz dyplomu politechniki absolwent otrzymuje certyfikat Siemensa. Studenci biorą udział w rozwiązywaniu rzeczywistych problemów, z którymi spotykać się będą w zakładzie pracy. Ćwiczenia nie odbywają się wyłącznie w warunkach laboratoryjnych, ale oparte są na najnowocześniejszych systemach mechatronicznych, wykorzystywanych w przemyśle. Na tej współpracy zyskuje student, Siemens oraz uczelnia. A w końcowym rozrachunku przemysł polski uzyskuje dostęp do wykwalifikowanych inżynierów zdolnych obsłużyć współcześnie stosowane rozwiązania mechatroniczne. Po ukończeniu takich studiów absolwenci będą mogli podjąć pracę w dowolnej firmie i od razu efektywnie pracować na stanowisku inżynierskim. To takie poczwórne Win-Win-Win-Win. |
Dobre wdrożenie systemów Przemysłu 4.0 na dwóch powyższych poziomach może zwiększyć wydajność działania lub zmniejszyć koszty zakładu przemysłowego. Jak bardzo? To zależy przede wszystkim od tego, jak dawno zakład był modernizowany. Jeśli operuje na urządzeniach z przed kilku, a maksymalnie kilkunastu lat, przestrojenie fabryki pod kątem Przemysłu 4.0 na tych dwóch poziomach przyniesie – statystycznie – kilkuprocentową poprawę rentowności. W dużych placówkach będzie się to przekładało na duże kwoty, ale też koszt takich wdrożeń będzie znacznie większy. Dlatego aby faktycznie skorzystać z idei, z jaką wiąże się Przemysł 4.0, koncepcję tę należy wdrożyć również na trzecim poziomie, a więc w odniesieniu do zarządzania i logistyki.
Ten trzeci poziom najmniej wiąże się z technologiami, a najbardziej ze stylem działania firmy, a nawet jej relacjami z kontrahentami. Dlatego w dużej mierze opiera się na ludziach i ich odpowiednim wyszkoleniu, gdzie systemy komputerowe stanowią tylko narzędzia, którymi można się posługiwać. Kluczem do sukcesu wydają się nowoczesne systemy ERP, pozwalające m.in. na automatyzację niektórych kontaktów z klientami idostawcami. Przydatne są też techniki modelowania 3D, a ostatnio nawet wirtualnej rzeczywistości, które dla klientów stanowią bardzo atrakcyjny sposób prezentacji oferowanych produktów. Co ciekawe, niektóre zinnowacyjnych funkcji takich systemów już od dawna są wykorzystywane w transakcjach konsumenckich. Przykładowo, klient zamawiający niemal dowolny towar w sklepie internetowym, w ogóle nie musi bezpośrednio kontaktować się z pracownikiem sklepu, a jednocześnie cały czas ma dostęp do kompletnych informacji na temat swojego zamówienia. Za pomocą kilku kliknięć jest może opłacić zamówienie, a następnie sprawdzić stan jego realizacji. Widzi, czy towar jest w magazynie, czy został zapakowany, a jeśli go wysłano, to jaki jest numer paczki. Ten natomiast pozwala ją śledzić, określając dosyć dokładnie, gdzie akurat się znajduje i przewidzieć czas dostawy. Choć dla konsumentów możliwości te wydają się oczywiste, w przemyśle wciąż stanowią nowość. Bardzo niewiele firm udostępnia swoim kontrahentom systemy elektroniczne, które pozwalają na jakąkolwiek samoobsługę. W zdecydowanej większości zakładów, zarówno od strony zakupów, jak i po stronie sprzedaży, znaczną część pracy wykonują ludzie, którzy na dodatek często nie są w stanie odpowiadać na nieco bardziej szczegółowe zapytania kontrahentów. Tymczasem przygotowanie odpowiednich systemów komputerowych, mających połączenie z serwerami obsługującymi maszyny produkcyjne pozwoliłoby znacznie podnieść jakość obsługi klienta (czy nawet dostawcy), przy jednoczesnym zmniejszeniu jej kosztów. I choć część osób wciąż będzie preferowało kontakt z człowiekiem, w rzeczywistości szybciej i sprawniej będzie można uzyskać wartościowe informacje za pomocą systemu komputerowego. A dzięki ich większej szczegółowości pozwoli to kontrahentom lepiej zaplanować własne operacje i w ten sposób podnieść wydajność.
Specjaliści zajmujący się Przemysłem 4.0 i wdrażaniem tej koncepcji są zgodni, że dopiero kompleksowe zaimplementowanie tych idei na wszystkich wymienionych poziomach prowadzi do realnych i to całkiem dużych korzyści. Niestety, optymalne przygotowanie takich aplikacji wcale nie jest łatwe. Wymaga zarówno spojrzenia z zewnątrz na prowadzone w zakładzie procesy, jak i znajomości specyfiki branży, w której firma operuje. Istotne jest nie tylko obeznanie z technologiami, ale po części nawet psychologii, która nierzadko stanowi trudną do pokonania przeszkodę na drodze do sukcesu.
Jakie są szanse i bariery w rozwoju technologii cyfrowych? Industry 4.0 zmienia sposób podejścia do produkcji. Cyfryzacja wytwarzania oznacza, że na etapie projektu możliwe będzie dostosowanie produktu ściśle do potrzeb klienta. Stanowi to przełom w porównaniu z dotychczasowymi metodami opartymi na produkcji masowej i dychotomii między niskim kosztem wytwarzania, a indywidualnym podejściem do produktu. Industry 4.0 zaciera ten podział. Produkt w Industry 4.0 będzie miał cechy zindywidualizowane, dopasowane do potrzeb klienta przy zachowaniu niskich kosztów produkcji. Dotyczy to dużych korporacji, ale także firm MŚP, bardziej „elastycznych biznesowo”, którym łatwiej jest dostosować się do bieżących potrzeb rynku i wykorzystać tę rewolucyjną zmianę. Z badania Smart Industry 2017, które Siemens przeprowadził wspólnie z Ministerstwem Rozwoju na grupie MŚP wynika, że polskie przedsiębiorstwa są wciąż jeszcze zbyt zamknięte na informacje z zewnątrz i kooperację. Braki widać szczególnie we współpracy z ośrodkami naukowymi, a częstą barierą jest niedobór funduszy na zakup technologii i patentów. Istotnymi utrudnieniami we wprowadzaniu nowych technologii w firmach produkcyjnych, dostrzeganymi przez samych przedsiębiorców MŚP, są przeszkody natury formalnej, w tym punkcie respondenci badania wymieniają biurokrację, brak wsparcia czy zachęt ze strony organów publicznych. Do barier w rozwoju technologii cyfrowych zaliczyć też trzeba ograniczone możliwości finansowania, brak dostępu do wykwalifikowanych kadr oraz obawy przed ryzykiem braku zwrotu z inwestycji. To się jednak zmienia, bo do wdrażania nowych technologii zachęca coraz częściej państwo. Przykładem jest tzw. ustawa o robotyzacji, która została w lipcu podpisana przez prezydenta i weszła w życie z datą wsteczną – pierwszego stycznia 2017 r. |
Co można zyskać?
Promotorzy idei Przemysłu 4.0 obiecują dosyć dużo korzyści z implementacji nowoczesnych rozwiązań. Opracowany w ubiegłym roku, raport PwC na temat Industry 4.0 i bazujący na odpowiedziach ponad 2000 firm zcałego świata, które wypełniły ankiety wskazuje, że nowoczesne rozwiązania przemysłowe powinny pozwalać zmniejszać koszty działania zakładów przemysłowych w tempie 3,6 proc. rocznie, przynajmniej do 2020 r. Co ważne, oszczędności te mają pochodzić zarówno z usprawnień wewnątrz firm, jak i wynikających z współpracy firm między sobą. W tym drugim aspekcie chodzi przede wszystkim o łańcuchy dostaw, które powinny lepiej funkcjonować dzięki rozwiązaniom Przemysłu 4.0.
Jednocześnie mówi się o wzroście przychodów na poziomie 2,9 proc. rocznie (w tym samym okresie), wynikającym z możliwości oferowania nowych produktów i usług oraz poprawianiem jakości dotychczas wytwarzanych. Usprawnienia mają koncentrować się na digitalizacji działań firm, a więc w dużej mierze na dostarczaniu informacji w postaci cyfrowej, nie tylko obejmującej więcej danych, ale i pozwalającej na łatwe, komputerowe przetwarzanie.
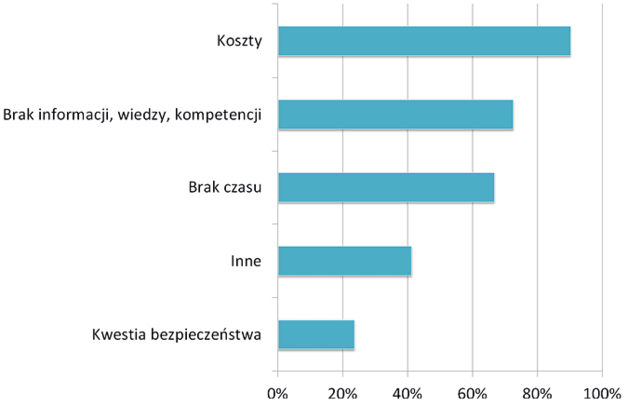
Co stanowi w Państwa firmie istotną przeszkodę we wdrażaniu idei Przemysłu 4.0? Źródło: własne badania ankietowe
To wszystko ma się odbyć kosztem ponad 900 mld USD, ponoszonym na modernizację zakładów w każdym roku w tym okresie. Co ciekawe, suma ta jest tylko nieznacznie niższa niż suma oszczędności i dodatkowych zysków, jakie mają być spowodowane przez wprowadzone zmiany w latach objętych prognozą, ale nie oznacza to, że nie warto ponosić tych wydatków. Trzeba pamiętać, że korzyści z inwestycji przemysłowych czerpie się przez bardzo wiele lat i dlatego wdrażanie idei Przemysłu 4.0 jest sumarycznie opłacalne. Ponad połowa firm ankietowanych przez PwC uważa, że w ich przypadku koszty inwestycji zwrócą się już w przeciągu dwóch lat, a więc bardzo szybko. Dzięki temu zmodernizowane linie produkcyjne oraz procesy będą w kolejnych latach przynosić już same korzyści, bez dodatkowych
kosztów.
Nieco inne wyniki otrzymaliśmy z ankiety, którą samodzielnie przeprowadziliśmy wśród kilkudziesięciu polskich przedsiębiorstw. Najczęściej pojawiającą się odpowiedzią odnośnie pytań na temat czasu zwrotu zplanowanych inwestycji w rozwiązania Przemysłu 4.0 było 5 lat, przy czym trzeba zaznaczyć, że wiele firm nie miało opracowanych, kompletnych planów inwestycyjnych. Dużym problemem w porównywaniu działań firm jest różny poziom wiedzy osób, które zajmują się inwestycjami, jak również różny szczegółowy zakres ich kompetencji. Tak jak to zostało wcześniej wspomniane, spojrzenie na ideę Industry 4.0 silnie zależy od tego, skąd wywodzi się dany pracownik, czym zajmował się wcześniej i jakie ma wykształcenie. Można powiedzieć, że w polskich przedsiębiorstwach jest niestety względnie niewiele osób, które są w stanie potraktować omawiany temat całościowo.
Duże rozbieżności w szacunkach odnośnie korzyści płynących z implementacji rozwiązań klasy Przemysł 4.0 widać również w raporcie PwC, ale jednocześnie są one dosyć równomiernie rozmieszczone na obszarze całego świata. Oznacza to mniej więcej tyle, że dzięki globalizacji niezależnie od regionu, zakłady przemysłowe borykają się z podobnymi problemami i czwarta rewolucja przemysłowa jest na podobnym etapiezaawansowania.
Przemysł 4.0 to wyzwanie dla przemysłu i szkolnictwa Idea Przemysłu 4.0 coraz śmielej wkracza w rzeczywistość produkcji przemysłowej na całym świecie. W związku z tym atuty w postaci niskich kosztów pracy czy atrakcyjnej lokalizacji – w przypadku krajów takich jak Polska – powoli przestają mieć znaczenie. Dziś liczy się nowoczesna technologia, a także umiejętne wykorzystanie możliwości, które ona ze sobą niesie, bo te są praktycznie nieograniczone. Przemysł 4.0 to ogromne wyzwanie dla producentów technologii takich jak FANUC. Nasi konstruktorzy muszą nieustannie wyprzedzać rynek i szukać rozwiązań spełniających coraz bardziej wyśrubowane potrzeby użytkowników – zarówno obecne, jak i te, które dopiero pojawią się w przyszłości. Jednak przed jeszcze większym wyzwaniem stoją firmy inżynierskie wdrażające te rozwiązania. Kreatywność inżynierów w bezpośredni sposób decyduje o efektach wykorzystania technologii w produkcji. Jest to szczególnie ważne ponieważ dziś już wiadomo, że problemem nie jest dostęp do najnowszej technologii czy możliwości sfinansowania jej zakupu. Największym ograniczeniem rozwoju, a zarazem wyzwaniem, z którym sektor przemysłu będzie mierzył się w nadchodzących latach jest brak wykształconej i kreatywnej kadry, potrafiącej wykorzystać choć część potencjału tkwiącego w technologii. Inteligentne maszyny mogą wesprzeć wszystkie obszary produkcji, dlatego właśnie dziś warto otwierać się na współpracę z maszynami i aktywnie poszukiwać nowych zastosowań dla robotów czy obrabiarek. By móc skutecznie rozwiązać problem braku kadry technicznej potrzebne są przemyślane działania na wielu etapach i szczeblach rynku. Niestety, firmy nie są w stanie dokonać tego bez pomocy państwa. Nie da się ukryć, że najważniejsza jest edukacja. To już na etapie edukacji szkolnej, młodzież w szkołach zawodowych – których obecnie praktycznie nie ma – powinna mieć możliwość bezpośredniego kontaktu z najnowszą technologią. Dobrze wyjaśniona teoria uwzględniająca trendy i osiągnięcia liderów automatyzacji powinna być uzupełniona jak największą liczbą praktcznych zajęć z użyciem inteligentnych maszyn. Tylko wspólne i spójne działania sektora przemysłu i państwa są w stanie wykształcić ludzi, którzy będą umieli nie tylko z technologii korzystać, ale również ją dalej rozwijać. |
Problemy
Wdrożenie idei Industry 4.0 w firmie nie jest jednak wcale takie łatwe. Problem całościowego postrzegania przedsiębiorstwa to jedno, ale są też inne trudności. Pierwszą z nich są finanse. Naturalnie ponoszenie nowych inwestycji kapitałowych często nie jest tym, czego pragną udziałowcy. Wynika to w dużej mierze z niepewności prowadzenia biznesu, szczególnie w rejonach, w których występują różnego rodzaju zagrożenia. A te obecnie pojawiają się niemal na całym świecie i są spowodowane albo zmianami politycznymi, lokalnymi konfliktami zbrojnymi czy niestabilnością walut i rosnącym zadłużeniem państw. Dlatego wnioskowanie o nowe inwestycje nie jest łatwe.
Pewnym sposobem na ominięcie tego problemu jest stopniowa modernizacja urządzeń i systemów, finansowana z budżetu operacyjnego. Jest to możliwe ponieważ komponenty automatyki stosowane we wdrożeniach Industry 4.0 z powodzeniem mogą realizować pracę wielu starszych urządzeń. Co prawda są droższe niż bezpośrednie zamienniki dotychczas stosowanych podzespołów, ale zazwyczaj też cechują się lepszą dokładnością, szybkością czy energooszczędnością. Można więc stopniowo modernizować zakład przemysłowy, nie zmieniając jego sposobu funkcjonowania, aż do momentu, gdy nakłady inwestycyjne potrzebne na zakończenie modernizacji spadną do niewysokiego poziomu. Wtedy wystarczy zainwestować w nowe oprogramowanie, uzupełnić sprzęt o niezbędne komponenty i opracować nowe zasady działania, wpisujące się w idee czwartej rewolucji przemysłowej.
Inną trudnością związaną z nowymi pomysłami na działania przemysłowe jest przekonanie do nich ludzi – w tym przede wszystkim pracowników. Aby w pełni korzystać z możliwości, jakie dają nowoczesne systemy automatyki, pracownicy muszę zmienić swoje zwyczaje. Wiele osób woli bowiem wykonywać niektóre operacje ręcznie lub współpracujące z innymi ludźmi, mimo że jest to metoda bardziej czasochłonna. Wykorzystanie maszyn i systemów informatycznych pozwala skrócić czas oczekiwania na informacje i wnioskowania na temat stanu procesów. Zmniejsza też zapotrzebowanie na kontakt między ludźmi i ogranicza liczbę osób niezbędnych do zdobycia kompletnych informacji i podjęcia decyzji. Takie zmiany nie są jednak mile widziane przez część personelu, który woli trzymać się dawnych przyzwyczajeń. W związku z tym powstaje ryzyko, że nawet po zainwestowaniu dużych środków we wdrożenie, pracownicy będą stosować dotychczasowe metody działania i inwestycja nie przyniesie oczekiwanych korzyści.
Oczywiście potrzebne są także dodatkowe szkolenia techniczne, dzięki którym personel nie tylko będzie chciał, ale przede wszystkim umiał posługiwać się nowoczesnymi narzędziami informatycznymi. Co prawda wiele zsystemów automatyki, prezentowanych jako sposoby na wdrożenie Przemysłu 4.0 w firmie jest reklamowanych jako bardzo przejrzyste i łatwe w użyciu, ale trzeba pamiętać o ogromnym wzroście dostępnych informacji wpostaci tzw. Big Analog Data, co jest częstą konsekwencją implementacji systemów IoT. To prawda – nowe systemy są bardzo wygodne w obsłudze i pozwalają intuicyjnie grupować dane, ale większość pracowników jest przyzwyczajona do pracy ze znacznie mniejszą ilością informacji. Dotyczy to szczególnie osób w starszym wieku, a więc i z większym doświadczeniem. Istnieje obawa, że ich dotychczasowa, cenna wiedza przestanie być użyteczna, gdy pojawią się nowoczesne systemy. W rzeczywistości jest to tylko częściowo prawdą.
Wiedzę ekspercką można zaimplementować do wdrażanego systemu automatyki. Można wręcz powiedzieć, że bez tego aplikacja nie będzie dobrze spełniała swojej roli. Co więcej, nowa instalacja jest zazwyczaj jej pozbawiona i w praktyce trzeba ją następnie stopniowo implementować w postaci algorytmów. Jest to czasochłonny proces, który może przebiegać latami.
Warto przy tym wspomnieć o innej obawie, która często pojawia się, gdy rozważane są próby rewolucjonizowania sposobu pracy zakładu przemysłowego. Pracownicy nierzadko obawiają się utraty swoich stanowisk pracy i bycia zastąpionymi przez maszyny. To fakt – celem automatyzacji bardzo często jest wyręczenie człowieka z wielu obowiązków, ale trzeba przy tym zauważyć, że zazwyczaj chodzi o obowiązki najbardziej żmudne, nudne, czy wręcz niebezpieczne. Tyle że przykładowa rozbudowa parku maszyn choć z jednej strony zmniejsza zapotrzebowanie na pracowników stojących przy linii produkcyjnej, to z drugiej strony zwiększa zapotrzebowanie na operatorów i serwisantów tych maszyn. A to często oznacza, że osoby, które dotąd wykonywały meczącą i niekorzystną dla zdrowia pracę mogą wciąż zajmować się podobną produkcją, ale w inny sposób, w bardziej komfortowych warunkach. W podobny sposób, doświadczeni inżynierowie utrzymania ruchu, zamiast ręcznie monitorować pracę maszyn mogą nauczyć się korzystać z nowych systemów i stopniowo przenosić do nich swoją wiedzę, co może poskutkować jej lepszym wykorzystaniem. I o ile inwestorzy chętnie jak najszybciej zastąpiliby zbędny personel tańszymi w utrzymaniu systemami komputerowymi, to w rzeczywistości kompletne wdrożenia Przemysłu 4.0 są bardzo czasochłonne, właśnie ze względu na długotrwałe dostosowywanie instalacji do specyfiki procesów prowadzonych w danym zakładzie oraz na przenoszenie wiedzy pracowników do systemów komputerowych.
Wdrażanie Przemysłu 4.0 wymaga zmiany organizacji łańcucha wartości przedsiębiorstwa Obecnie coraz więcej firm zapoznaje się z tematyką Przemysłu 4.0 lub już planuje szacowanie możliwości, jakie niosą ze sobą inicjatywy Czwartej Rewolucji Przemysłowej. Zainteresowanie wzmagają rosnące oczekiwania klientów dotyczące większej elastyczności w zakresie indywidualizacji zamówień, podniesienia jakości wytwarzanych produktów oraz skrócenia czasu realizacji zleceń. Firmy, które zastanawiają się nad rozwiązaniami Przemysłu 4.0, powinny rozpocząć proces od autorefleksji dotyczącej gotowości do wdrożenia nowoczesnych technologii i oceny realnych korzyści związanych z wdrożeniem. W pierwszej kolejności należy odpowiedzieć sobie na pytanie – czy moja fabryka jest już Fabryką 3.0, czyli fabryką zautomatyzowaną (lub zrobotyzowaną) w zakresie realizacji produkcji i gromadzenia danych produkcyjnych? Jeżeli krok związany z automatyzacją został już wykonany wtedy droga do osiągnięcia korzyści z transformacji do Fabryki 4.0 z całą pewnością będzie mniej wyboista, a osiągnięcie zakładanych celów realne. Wdrażanie rozwiązań Przemysłu 4.0 wiąże się nie tylko z wyborem i implementacją nowych technologii, ale także z równoległą zmianą koncepcji organizacji łańcucha wartości przedsiębiorstwa. Wyzwaniem stojącym przed firmami wdrażającymi jest także odpowiednie przygotowanie kadry (managerów, inżynierów i operatorów) do zmian, ponieważ tylko dzięki takim połączonym działaniom transformacja może zakończyć się powodzeniem. |
Bezpieczeństwo informatyczne
Spośród wszystkich problemów, jakie pojawiają się w trakcie omawiania tematu Przemysłu 4.0, zdecydowanie najpoważniejszym, a być może nawet wciąż niedocenianym, jest zagrożenie bezpieczeństwa systemów przemysłowych. Już sam Internet Rzeczy polega na podłączeniu wszelkich urządzeń elektronicznych do sieci, a więc i jego przemysłowy odpowiednik bazuje na tym samym. Konwergencja technologii informatycznych zprzemysłowymi prowadzi do nowych zagrożeń.
Wiążące się z tym ryzyko jest bardzo duże. W przeciągu ostatnich kilku lat każdego roku powstawały nowe zagrożenia wirusami i atakami, które powodowały wielomilionowe straty w firmach na całym świecie. W 2017 r. byliśmy świadkami sytuacji, gdzie jednego dnia niemal wszystkie komputery w firmie padały ofiarą ataku za sprawą wirusa Petya, który żądał okupu. Wykorzystywał on względnie niedawno odkrytą lukę w systemie operacyjnym Windows, po cichu instalował się na komputerach w otoczeniu sieciowym, by po pewnym czasie uśpienia i namnażania – zaatakować. Co ciekawe, wirus ten nawet nie był nastawiony na zarobek, gdyż szybko można było odkryć, że jego twórcy nie są w stanie zweryfikować, kto okup opłacił, a kto nie, a więc wpłacanie jakichkolwiek środków na ich konto nic nie da. Wirusy takie jak ten mogą być więc tworzone nie tyle po to, by bezpośrednio na nich zarobić, ale by spowodować problemy w firmie i uniemożliwić jej funkcjonowanie. W momencie gdy Przemysłowy Internet Rzeczy się upowszechni, liczba firm zagrożonych atakiem znacznie wzrośnie, a co więcej, będą to różne zakłady przemysłowe, których nawet krótki przestój kosztuje krocie.
Niestety, ratunkiem nie jest zastosowanie systemu operacyjnego, innego niż Microsoft Windows. Luki pojawiają się także w innym oprogramowaniu, czego dobrym przykładem jest błąd Heartbleed ujawniony w 2014 r. I o ile w przypadku systemów konsumenckich, można przyjąć, że częste aktualizacje oprogramowania są najlepszym sposobem na uniknięcie problemów, w rzeczywistości przemysłowej będzie to trudne w realizacji. Oprogramowanie przemysłowe zazwyczaj nie zmienia się tak szybko, a inżynierowie utrzymania ruchu starają się unikać aktualizacji, o ile nie są one konieczne. Wynika to z obaw przed różnicami w działaniu starszej inowszej wersji systemu. Aktualizacje często trudno cofnąć, a nowy system może błędnie realizować specyficzne zadanie, które składa się na proces przeprowadzany w zakładzie. Oznacza to, że sama aktualizacja może stanowić zagrożenie, gdyż jest w stanie niekiedy doprowadzić do wstrzymania produkcji.
Postęp techniczny wymaga zmiany systemu kształcenia Przygotowanie kadr technicznych na progu zbliżającego się Przemysłu 4.0, to proces, któremu towarzyszy obecnie szereg zmian systemu edukacji w Polsce. Złożoność problemu tkwi w tym, że podczas dynamicznie zachodzących zmian w przemyśle, trzeba się jak najszybciej uporać z reformą szkolnictwa zawodowego oraz wyższego technicznego. Szansą natomiast jest to, że aby nadążyć za nowoczesnym przemysłem, potrzebne są właśnie zasadnicze zmiany w kształceniu technicznym i nowe podejście do współczesnych procesów wytwarzania. Pojawia się coraz częściej zapotrzebowanie na specjalistów o innych niż dotychczas umiejętnościach zawodowych, którzy w dobie Internetu Rzeczy, z niespotykaną dotąd ilością danych w procesach przemysłowych, będą zdolni obsługiwać elastyczne systemy produkcyjne, reagujące w tzw. czasie rzeczywistym. Postęp techniczny zaczyna generować nowe środowisko, które można nazywać początkami istnienia przestrzeni cyber-fizycznej, a to wymaga większych niż do tej pory umiejętności od przyszłej kadry. Producenci poszukują obecnie specjalistów z zakresu informatyki, automatyki czy mechatroniki, których wiedza teoretyczna dorównuje praktycznej. Sprawdzone wzorce kształcenia dualnego to natomiast kierunek, w którym podąża współczesna edukacja techniczna w wielu krajach Europy. Warto więc zdać sobie sprawę z faktu, że sama szkoła czy uczelnia ze swoimi zasobami często już nie wystarcza. Kadry muszą być szkolone również bezpośrednio tam, gdzie najszybciej zachodzą zmiany i najpilniej potrzebne są nowe umiejętności, czyli w przemyśle. Istotą dobrego przygotowania przyszłych kadr technicznych, do nadchodzącej czwartej rewolucji przemysłowej, jest więc bezpośrednia i ścisła współpraca szkół zawodowych oraz uczelni z przemysłem. |
Jak wdrożyć Przemysł 4.0?
Omówione zagrożenia oraz poziom wiedzy i rozumienia zagadnień związanych z czwartą rewolucją przemysłową wskazują, że za wdrażanie rozwiązań Przemysłu 4.0 najlepiej nie zabierać się samemu. Większość firm, z którymi rozmawialiśmy w trakcie powstawania tego artykułu albo nie miało żadnego konkretnego, kompleksowego planu implementacji nowych rozwiązań, albo starało się oprzeć na pomysłach zewnętrznych konsultantów. Można powiedzieć, że ta druga grupa była w lepszej sytuacji, bo wyprzedza swoją konkurencję. Trzeba jednak uważać, by nie wpaść w pułapkę w postaci odgórnego ograniczenia się do rozwiązań tworzonych przez jedną firmę. Praktycznie wszyscy znaczący producenci automatyki i systemów przemysłowych widzą w Przemyśle 4.0 nie tylko duży potencjał ale i szansę na zarobek. Firmy te tworząc własne rozwiązania, starają się jak najszybciej je spopularyzować, co pozwoliłoby następnie oferować swoje i powiązane ze swoimi produkty właśnie opierając się na ich popularności. Przewagę w tym zakresie mają firmy, którym udało się wcześniej spopularyzować autorskie rozwiązania przemysłowego Ethernetu.
Dostawcy też dosyć dobrze zdają sobie sprawę z ograniczeń wiedzy na temat Przemysłu 4.0 i starają się prezentować tę koncepcję tak, by najbardziej pasowała do tego, co sami oferują. Jest to oczywiście naturalne i szczęśliwie oferowane rozwiązania są zazwyczaj dobrze przemyślane, a ich całościowe zastosowanie pozwala uzyskać bardzo dobre rezultaty. Producenci automatyki zatrudniają też specjalistów od wdrożeń, którzy pomagają planować strategię klientów, biorąc pod uwagę zarówno czynniki ekonomiczne, konkurencję, sytuację rynkową, techniczną, jak i dotychczas stosowane narzędzia. Wydaje się, że skorzystanie z takich usług i zlecenie modernizacji, a raczej ułożenia planu modernizacji zakładu przemysłowego jest najlepszym wyjściem dla zdecydowanej większości polskich przedsiębiorców z branży przemysłowej. Oddanie tego zadania w ręce specjalistów, którzy dobrze znają temat pozwoli uniknąć błędów, a jednocześnie umożliwi ocenę zakładu z obiektywnego, zewnętrznego punktu widzenia, a więc dostrzeżenie zjawisk, szans i problemów, które z wewnątrz firmy mogą być niewidoczne. Wtedy jedyną trudnością jest wybór dostawcy, który najlepiej przeprowadzi ten proces i będzie mógł zaoferować komponenty i systemy optymalnie pasujące do specyfiki modernizowanego zakładu.
Inżynierowie 4.0 korzystają na współpracy uczelni z przemysłem W wiedzę przyszli inżynierowie wyposażani są na uczelniach – powstaje coraz więcej kierunków studiów, będących odpowiedzią na zapotrzebowanie ciągle zmieniającego się przemysłu. Inżynierowi 4.0 pozostaje jeszcze zdobycie doświadczenia przez kontakt z nowoczesnymi technologiami w „naturze”. Ten aspekt kształcenia uczelnie realizują coraz bardziej popularyzując współpracę z przemysłem. Studenci coraz częściej wysyłani są na kursy lub warsztaty „do źródeł”, czyli do przedsiębiorstw, które w konkretnych branżach dostarczają innowacyjne produkty i rozwiązania. Współpraca miedzy szkołami a firmami prywatnymi to świetna okazja, by pokazać młodym ludziom, jakie są najnowsze tendencje na rynku technologicznym i przygotować ich do zadań, jakie będą wykonywać w przyszłym miejscu pracy. Nie możemy zapominać też o funkcjonującej na rynku pracy kadrze technicznej, która ma już wiedzę i niezbędne doświadczenie. To na czym należałoby się skupić, to kompetencje miękkie. Do tego oczywiście potrzebna jest otwartość na zmianę ze strony samego inżyniera oraz wsparcie organizacji, w której pracuje. Dlatego kluczowym elementem składającym się na sukces transformacji przedsiębiorstwa do standardów Fabryki 4.0 jest zaangażowanie kierownictwa oraz działów HR w budowanie odpowiedniej polityki kadrowej w zakresie wsparcia rozwoju pracowników. Stworzenie kompleksowych programów rozwojowych wymaga dużej pracy na kilku etapach. A to co powinno być istotą tych programów to nacisk na promowanie interdyscyplinarności, która powinna być ich fundamentem. |
Kiedy dołączyć do rewolucji?
Skoro wiadomo już, jakie korzyści niesie Przemysł 4.0, jakie się z nim wiążą zagrożenia i jak zabrać się do przeprowadzenia nowych wdrożeń, pozostaje pytanie - kiedy to zrobić? Odpowiedź na nie nie powinna być zaskakująca – jest taka sama, jak w przypadku chyba większości planowanych procesów, tj. „jak najszybciej”. Wynika to z dwóch czynników. Po pierwsze, jak już zostało wspomniane, korzyści płynące z zastosowania nowoczesnych procedur i digitalizacji procesów można czerpać przez długi czas po wdrożeniu. W odróżnieniu od planów rozbudowy parku maszynowego, które należałoby dostosowywać do koniunktury na rynku, modernizacje w stylu Przemysłu 4.0 nie będą podnosiły kosztów utrzymania, co mogłoby się przełożyć na dodatkowe straty w gorszych latach. Nowoczesne systemy informatyczne oraz oczujnikowanie procesów wogólności prowadzi do zmniejszenia kosztów operacyjnych. Co więcej, nie należy się też spodziewać, że systemy te nagle znacznie stanieją. To fakt, że stanowią jeszcze pewnego rodzaju nowość, ale wcale nie bazują na wykorzystaniu niezwykle drogich, nowoczesnych rozwiązań technologicznych. Przemysł 4.0 tak naprawdę polega na sprytnym, kompleksowym wykorzystaniu zasobów i technik dostępnych od lat, które zdążyły już stanieć, np. komunikacja cyfrowa, inteligentne czujniki oraz przetwarzanie danych w chmurze.
Po drugie, zwlekanie z modernizacją sprawia, że zakład przestaje być konkurencyjny. Mamy 2017 rok, a więc Przemysł 4.0 jest z nami już 6 lat i jest mocno promowany przez rządy uprzemysłowionych państw na całym świecie. Nowe, elektroniczne usługi, na jakie pozwala czwarta rewolucja przemysłowa są stopniowo wdrażane w kolejnych firmach i jeśli nie dołączy się do tego ruchu, zostanie się w tyle. Dlatego zignorowanie tematu zdecydowanie nie jest dobrym rozwiązaniem.
Jakie wyzwania stoją przed wdrażającymi idee Przemysłu 4.0? Przedsiębiorstwa mające w planach transformację i wdrożenie rozwiązań z zakresu Przemysłu 4.0 staną przed trzema głównymi wyzwaniami. Pierwszym będzie sfinansowanie całej operacji. Zakład powinien być wyposażony w silną infrastrukturę, która pozwoli na automatyzację i informatyzację produkcji. Jeszcze większym wydatkiem będzie inwestycja w zaawansowane technologie oraz we wspierające ich oprogramowanie. Co za tym idzie konieczne będzie stworzenie przez firmy długookresowego planu inwestycji. Drugim wyzwaniem będzie cyberbezpieczeństwo. Podłączenie całego zakładu do Internetu wiąże się z ryzykiem ataku hakerskiego. Takie ataki powodują nie tylko straty finansowe, lecz mogą się wiązać z zagrożeniem życia ludzkiego. Z tego powodu ważne jest stworzenie odpowiedniej polityki bezpieczeństwa oraz inwestowanie w produkty o bezpiecznej architekturze. Trzecim ważnym wyzwaniem, przed którym staną firmy są niedobory kadrowe. Na rynku pracy brakuje wyspecjalizowanych inżynierów, potrafiących połączyć różne specjalizacje, np. automatykę z informatyką. Przedsiębiorcy powinni zacieśnić współpracę z uczelniami, tak aby ich zapotrzebowanie na wyszkolone kadry miało odwzorowanie w programach nauczania.Jeśli firmy sprostają wspomnianym wyzwaniom czeka je duży wzrost wydajności operacyjnej i produktywności. |
źródło: Automatyka 10/2017
Komentarze
blog comments powered by Disqus