Robotyzacja spawania z wykorzystaniem technologii hybrydowej Plazma-MIG/MAG
Zbigniew Pilat, Marek Pachuta (Łukasiewicz – PIAP) drukuj
Producenci działający na rynku konstrukcji stalowych poszukują rozwiązań, które umożliwią poprawę produktywności realizowanych procesów spawalniczych. W odpowiedzi na te potrzeby dostawcy sprzętu spawalniczego wprowadzają coraz nowocześniejsze technologie. Należy do nich spawanie hybrydowe. Najbardziej rozpowszechnionej obecnie hybrydowej technologii spawania Laser-MIG/MAG przybył mocny konkurent: Plazma-MIG/MAG.
Gospodarczy wymiar globalizacji oznacza m.in. osłabienie lub wręcz likwidację barier i ograniczeń w handlu międzynarodowym. Procesom tym bardzo dobrze służy rozwój środków i metod transportu, co ułatwia przemieszczanie surowców i wyrobów. Bardzo istotny jest też rozwój ICT, który spowodował niewyobrażalne wręcz przyspieszenie i wzrost przepustowości przesyłu informacji. Dla rodzimych producentów konstrukcji stalowych, podobnie jak w innych branżach, sytuacja ta rodzi zarówno szanse, jak i zagrożenia. Z jednej strony mogą oni pozyskiwać rozwinięte, wysokowydajne technologie wytwarzania. Mają także możliwości dostępu do odległych rynków zbytu. Z drugiej strony na rynku krajowym, gdzie mieli do niedawna pewną pozycję, a także na atrakcyjnych rynkach krajów UE i regionu, muszą zmierzyć się z konkurencją dostawców z obszarów, gdzie siła robocza jest znacznie tańsza. W efekcie nasi producenci są pod stałą presją obniżania kosztów przy utrzymaniu, a nawet podnoszeniu jakości oferowanych wyrobów.
W produkcji konstrukcji stalowych, szczególnie jeśli występują w nich podzespoły wykonane z blach grubych, na całkowite koszty wytworzenia w istotny sposób wpływają operacje spawania. Dlatego producenci działający na tym wymagającym rynku wciąż poszukują rozwiązań, które w ich firmach podniosą produktywność realizowanych procesów spawalniczych, określaną jako stosunek efektów do nakładów, obejmujących zarówno pracę żywą, jak też wykorzystanie infrastruktury i środków technicznych (maszyny, narzędzia). Odpowiadając na te potrzeby, dostawcy sprzętu spawalniczego oferują udoskonalone, a także zupełnie nowe technologie. Jedną z takich propozycji jest spawanie hybrydowe. Jego idea zasadza się na połączeniu dwóch różnych źródeł ciepła w jednym procesie spawania. Kompozycja metod ukierunkowana jest na wykorzystanie ich pozytywnych indywidualnych cech, z jednoczesnym eliminowaniem ich ograniczeń w hybrydzie.
Najbardziej rozpowszechnioną obecnie hybrydową technologią spawalniczą jest proces Laser-MIG/MAG. Jego cechą charakterystyczną jest głęboka penetracja, niski dopływ ciepła do materiałów łączonych i duża szybkość spawania. Jest to jednak bardzo kosztowna technologia. Drogie są same urządzenia, głowice hybrydowe i zestawy laserowe. Ze względów bezpieczeństwa stosowanie tej technologii wymaga budowy stanowisk w pełni zautomatyzowanych, z zapewnieniem odpowiedniej ochrony pracujących w pobliżu ludzi, co powoduje dalszy wzrost kosztów inwestycji. Stosowanie tej technologii wymaga także bardzo dokładnego, a więc kosztownego przygotowania krawędzi łączonych detali.
W tej sytuacji korzystną alternatywą może być technologia hybrydowa Plazma-MIG/MAG. Wykorzystuje ona dwa standardowe procesy: spawanie plazmowe (PAW) oraz spawanie łukowe elektrodą topliwą w osłonie gazowej (MIG/MAG). Jest to metoda szczególnie wydajna w przypadku łączenia elementów o dużej grubości (8–10 mm i powyżej). Cechuje ją mniejsza wymagana dokładność przygotowania powierzchni łączonych elementów niż przy spawaniu z wykorzystaniem techniki laserowej. Jest też znacznie od niej tańsza, zarówno na etapie samej inwestycji, jak też podczas eksploatacji. Stosowanie tej technologii wymaga również budowy stanowisk w pełni zautomatyzowanych, w szczególności zrobotyzowanych.
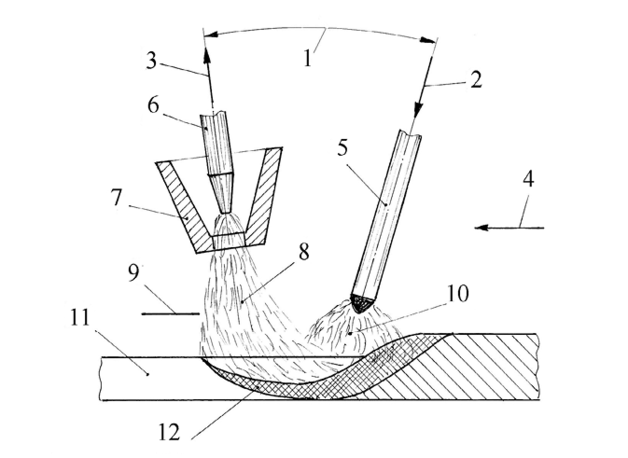
Rys. 1. Idea spawania hybrydowego Plazma-MIG/MAG: 1 – kąt między osiami elektrody topliwej (poz. 5) oraz elektrody nietopliwej (poz. 6), 2 – kierunek przepływu prądu spawania łukowego, 3 – kierunek przepływu prądu strumienia plazmy, 4 – kierunek spawania, 5 – elektroda topliwa (drut spawalniczy), 6 – elektroda nietopliwa – dysza plazmowa, 7 – osłona dyszy plazmowej, 8 – strumień plazmy, 9 – pole magnetyczne oddziałujące na strumień plazmy, 10 – łuk spawania MIG/MAG, 11 – spawany materiał, 12 – stopiony metal
Spawanie hybrydowe Plazma-MIG/MAG
Idea spawania hybrydowego Plazma-MIG/MAG, przedstawiona na rys. 1, znana jest od lat 70. ubiegłego wieku. Technologia ta była przedmiotem wielu prac badawczych prowadzonych w ośrodkach na całym świecie. Jednak dopiero na początku XXI w. izraelska firma PLT opanowała tę metodę na tyle, że zdecydowała się na wprowadzenie jej na rynek komercyjny. Od 2008 r. firma PLT oferuje linię urządzeń o nazwie Super-MIG. W tym rozwiązaniu palnik MIG/MAG oraz palnik plazmowy są zintegrowane w jednej głowicy technologicznej. Podczas procesu spawania głowica musi być tak prowadzona, aby łuk plazmowy wyprzedzał łuk MIG/MAG. Łuk plazmowy powoduje powstanie w trakcie spawania kanału parowego (ang. keyhole). Parametry procesu są tak dobrane, aby głębokość kanału była porównywalna z grubością spawanego materiału, a jego średnica z szerokością szczeliny między spawanymi elementami. Dzięki temu uzyskuje się głęboki przetop spawanego materiału. Za łukiem plazmowym podąża łuk MIG/MAG w takiej odległości, aby oddziaływał na jeziorko spawalnicze zanim nastąpi skrystalizowanie cieczy powstałej na skutek działania plazmy (fot. 2). W ten sposób topione spoiwo elektrody MIG/MAG łączy się z płynnym materiałem rodzimym, wypełniając spoinę i tworząc jej lico. Synergia dwóch procesów spawania plazmowego i MIG/MAG daje konkretne korzyści. Do najważniejszych należą:
- większa prędkość spawania w porównaniu z typowymi metodami MIG/MAG,
- większa dopuszczalna tolerancja zmieniających się parametrów geometrycznych szczelin spawalniczych (mniejsze wymagania w zakresie jakości przygotowania detali),
- większa głębokość wtopienia, szczególnie istotna dla złącz doczołowych, zakładkowych i pachwinowych,
- zmniejszona ilość wprowadzanego ciepła – mniejsza strefa wpływu ciepła i wynikające z tego zmniejszenie odkształceń spawalniczych.
Głowica systemu Super-MIG jest przystosowana do współpracy z powszechnie oferowanym sprzętem spawalniczym. W głowicy umieszczone są: palnik do spawania łukowego elektrodą topliwą (MIG/MAG) oraz palnik do spawania plazmowego. W obudowie głowicy zainstalowany jest zespół elektromagnesów, zlokalizowany w pobliżu palnika plazmowego. Ich pracę nadzoruje sterownik zestawu hybrydowego, który – regulując prądy przepływające przez cewki elektromagnesów – zmienia pole elektromagnetyczne oddziałujące na strumień plazmy. Sterownik ten zarządza także dopływem gazów technicznych (argon i mieszanka argon + CO2 jako gaz osłonowy). Sterownik jest zamontowany w osobnej szafie sterowniczej, razem ze źródłami plazmowymi. Na ścianie szafy jest zainstalowany pulpit operatora w postaci wyświetlacza z przyciskami, który umożliwia wprowadzanie i edycję parametrów procesu spawania hybrydowego. Wyświetlane są również na nim informacje o pracy systemu, w tym komunikaty o wykrytych błędach.
Zrobotyzowane stanowisko spawania hybrydowego Plazma-MIG/MAG
Możliwości i efekty wykorzystania technologii Plazma-MIG/MAG w stanowisku zrobotyzowanym były tematem projektu E!IIPL-IL/05/02/2013 „RobWeld Super-MIG Robotized Welding With Use of New Generation of Hybrid System Based on Super Heavy Duty Super MIG Concept”, realizowanego w ramach Inicjatywy EUREKA i dofinansowanego przez Narodowe Centrum Badań i Rozwoju. Liderem konsorcjum była firma PLT (Izrael), dostawca technologii spawania hybrydowego Plazma-MIG/MAG. Wspomagali ją wykonawcy z Polski: Przemysłowy Instytut Automatyki i Pomiarów PIAP (w zakresie robotyzacji) i Supra Elco Jacek Szulc (integracja systemów spawalniczych i technologia spawania).
W ramach realizacji projektu opracowano modelowe zrobotyzowane stanowisko spawania, które zostało zainstalowane w laboratorium PIAP. Rozwiązanie integruje technologię spawania hybrydowego Super-MIG z laserowym systemem śledzenia spoiny oraz nowoczesnym układem sterowania robota przemysłowego. W stanowisku modelowym wykorzystano robota KR16-2F (KUKA) i system sensoryczny TH6D (Scansonic). Głowica sensoryczna umieszczona jest na ramieniu robota, w pobliżu hybrydowej głowicy spawalniczej (fot. 1), a komputer sterujący pracą czujnika – w szafie sterowniczej stanowiska. Komputer komunikuje się za pośrednictwem szybkiej sieci Ethernet bezpośrednio z układem sterowania robota. W modelowym stanowisku zastosowano najnowszej generacji układ sterowania robotów przemysłowych firmy KUKA, model KRC4. Ma on wewnętrzną architekturę PC z wykorzystaniem technologii wieloprocesowej z pamięcią wewnętrzną 2 GB RAM i dyskiem twardym 30 GB. Funkcjonalność układu sterowania może być rozszerzona m.in. o zaawansowane funkcje współpracy z systemami sensorycznymi, w tym do poszukiwania spoiny (KUKA.SeamTech Finding) oraz śledzenia i korekcji on-line trajektorii ruchu robota podczas spawania (KUKA.SeamTech Tracking). Implementacja funkcji dodatkowych odbywa się za pomocą tzw. pakietów technologicznych.
Szafa sterownicza stanowiska zawiera sterownik nadrzędy z komputerem panelowym typu PC – którego ekran dotykowy pełni rolę pulpitu operatorskiego, a więc interfejsu człowiek-maszyna całego stanowiska (HMI, Human Machine Interface) – oraz systemem bezpieczeństwa (sterownik bezpieczeństwa PILZ integrujący elementy i urządzenia bezpieczeństwa). Zastosowane komponenty umożliwiają nadrzędne sterowanie całym stanowiskiem z poziomu komputera PC, który może również zapewniać zdalny monitoring całej instalacji (wpięcie
w zakładową LAN).
Stanowisko modelowe jest otoczone ogrodzeniem ochronnym. Zastosowano rozwiązanie modułowe, z możliwością zmiany kształtu/wymiarów (demontaż modułów lub całej ściany). Ściana przednia jest otwarta. Wejście przez nią jest chronione kurtyną świetlną oraz zasłaniane półprzezroczystymi lamelami spawalniczymi, zabezpieczającymi wzrok przed rozbłyskami.
Detale do spawania umieszczane są na stole spawalniczym o blacie 50 mm × 800 mm × 1200 mm i wysokości 850–900 mm. Blat jest przystosowany do montażu zacisków spawalniczych (otwory robocze). Nogi stołu są odejmowane, dzięki czemu możliwe jest ułożenie blatu w innej pozycji niż pozioma. Blat stołu może być także zainstalowany na obrotniku. Dwuosiowy stół pozycjonujący DKP-400 (KUKA) stanowi opcjonalne wyposażenie stanowiska. Po dołączeniu stołu konfiguracja robota KR16 jest zmieniana tak, że osie stołu są traktowane jako dodatkowe osie robota. Pozwala to na prowadzenie prób spawania w różnych pozycjach, zgodnie z wymaganiami technologicznymi procesu oraz programem prowadzonych badań. Umożliwia też pracę współbieżną robota i stołu – prowadzenie palnika przez robota przy jednoczesnym ruchu blatu stołu (pochylanie i obrót).
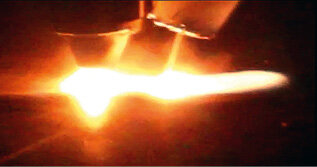
Fot. 2. Głowica spawania hybrydowego Plazma-MIG/MAG wraz z czujnikiem śledzenia spoiny zamontowane na ramieniu robota
Próby wykonane na stanowisku modelowym
W ramach realizacji projektu RobWeld przeprowadzono szereg prób i badań na stanowisku modelowym. Dotyczyły one zarówno zrobotyzowanego spawania z wykorzystaniem technologii hybrydowej Plazma-MIG/MAG, jak też systemu śledzenia trajektorii robota podczas spawania. Część prób wykonano w laboratorium Instytutu PIAP. Na początku przeprowadzono testy spawania na przygotowanych próbkach blach o różnej grubości i różnych typach złącz, dzięki którym ustalono najlepszy sposób prowadzenia zintegrowanej głowicy hybrydowej oraz określono sposób doboru parametrów (prądy spawania, prędkość podawania drutu, prędkość prowadzenia procesu, przepływy gazów osłonowych). Następnie wykonano próby spawania w pozycjach innych niż podolna. W badaniach wzięli udział przedstawiciele firm produkcyjnych. Do części testów wykorzystano próbki przygotowane przez partnerów przemysłowych. Przeprowadzono także serię badań we współpracy z Zakładem Spajania Politechniki Warszawskiej. Obejmowały one m.in. spawanie stali o wysokiej granicy plastyczności (S700MC) i stali nierdzewnej oraz próby napawania. W laboratorium PW przeprowadzono badania metalograficzne wykonanych złącz. Umożliwiły one ujawnienie i ocenę mikrostruktury złącz (fot. 3) oraz wielkości strefy wpływu ciepła (SWC). Wykonano także pomiary twardości obszarów charakterystycznych złącz.
Stanowisko modelowe przetestowano także w warunkach przemysłowych, we współpracy z wybranymi partnerami – zakładami produkcyjnymi. Przeprowadzono dwie takie serie prób. W pierwszym przypadku zainstalowano zestaw Super-MIG na portalu do spawania wzdłużnego. Łączone były blachy 4–8 mm, złącze doczołowe, bez ukosowania, w pozycji PA. Wyniki uzyskane podczas spawania płyt próbnych były pozytywne. Dla grubości materiału 4, 5 i 7 mm uzyskano prędkości spawania odpowiednio: 0,80, 0,70 i 0,65 m/min. W stosunku do procesu produkcyjnego realizowanego obecnie w tej firmie (technologia plazmowa Key Hole z podawaniem zimnego drutu) oznacza to procentowy wzrost prędkości spawania w zakresie 150–300 proc.
Drugi partner, producent dużych konstrukcji stalowych, w celu przeprowadzenia prób, zorganizował specjalne stanowisko w hali produkcyjnej. Został na nim zainstalowany robot ze stanowiska modelowego wraz z wyposażeniem technologicznym. Próby wykonano na różnych materiałach podstawowych (m.in. S960QL; S1300QL; Alform 960) i grubości 5–9,5 mm. Zakres prób obejmował wykonanie spawania na złączach doczołowych typu I (złącza bez ukosowania) i V (złącza z pełnym ukosowaniem, bez progu). Spawanie wykonywano w pozycjach PA i PC. W tym przypadku wyniki prób były na tyle pozytywne, że firma zdecydowała się na zakup zestawu technologicznego Super-MIG oraz systemu sensorycznego Scansonic. Jest to pierwsza w Polsce instalacja przemysłowa zrobotyzowanego spawania hybrydowego Plazma-MIG/MAG.
W kontaktach z firmami przemysłowymi pojawił sie aspekt uznania technologii. Certyfikat „Qualification of a Welding Procedure (WPQR)” jest traktowany jako gwarancja wysokich walorów jakościowych i wydajnościowych oferowanej technologii, szczególnie w przypadku technologów, specjalistów z działów głównego spawalnika, szefa produkcji lub utrzymania jakości. Z tego powodu wykonawcy projektu zdecydowali się na przeprowadzenie uznania technologii spawania hybrydowego Plazma-MIG/MAG. Jako wykonawcę procedury wytypowano uznaną międzynarodową firmę TÜV. Do badań wybrano materiał S355, o grubości 8 mm i złącza doczołowe, bez ukosowania. Założono spawanie jednościegowe w pozycji podolnej (PA). Badania wykonanych próbek, przeprowadzone przez specjalizowane laboratoria, potwierdziły, że złącza spełniają wymagania stosownych norm. Uzyskano przy tym bardzo dobrą wydajność – prędkość spawania wynosiła 80 cm/min. Wykonawcy projektu – RobWeld, PIAP i Supra Elco – udostępniają na życzenie skan certyfikatu wraz z WPS.
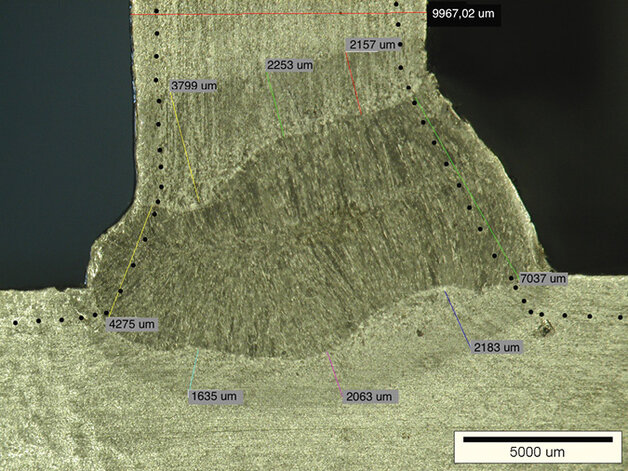
Fot. 3. Mikrostruktura złącza wykonanego metodą Plazma-MIG/MAG z pomiarami wielkości obszarów charakterystycznych spoiny czołowej: stal niestopowa S235JR, grubość 10 mm, złącze teowe
Podsumowanie
Zrobotyzowane stanowisko spawania hybrydowego Plazma-MIG/MAG jest gotowe do wdrożenia. Połączone zespoły Instytutu PIAP i Supra Elco mogą zaadaptować rozwiązania będące wynikiem projektu RobWeld do specyfiki konkretnego procesu produkcyjnego i wdrożyć zarówno kompletne stanowisko zrobotyzowane, jak też poszczególne jego elementy.
Przeprowadzone badania i zebrane dotychczas doświadczenia pokazują rozliczne korzyści wynikające z zastosowania zrobotyzowanego spawania z wykorzystaniem technologii hybrydowej Plazma-MIG/MAG. Można je zebrać w następujących punktach:
- możliwość uzyskiwania większych prędkości spawania niż w konwencjonalnym spawaniu MIG/MAG lub SAW,
- mniejsza wrażliwość na zmienność szczelin spawalniczych w porównaniu do spawania plazmowego lub z wykorzystaniem lasera,
- możliwość uzyskiwania większych niż w konwencjonalnym spawaniu MIG/MAG głębokości wtopienia przy wykonywaniu złączy doczołowych, zakładkowych, pachwinowych,
- zmniejszona ilość wprowadzanego ciepła dzięki węższej strefie wpływu ciepła (SWC), a w efekcie – zmniejszenie odkształceń spawalniczych (termicznych) i czystsze spoiny,
- mniejsza uciążliwość procesu dla środowiska (spawanie bez użycia topników, jak przy łuku krytym SAW) oraz zmniejszenie zużycia energii,
- lepsza i bardziej stabilna jakość spoin dla tych samych zakresów materiałów spawanych,
- w porównaniu do spawania z udziałem technologii laserowej, hybryda Plazma-MIG/MAG jest mniej wymagająca pod względem jakości przygotowania powierzchni spawanych,
- technologia ta jest znacznie tańsza, zarówno na etapie inwestycji, jak też podczas eksploatacji, od innych wysokowydajnych metod, np. spawania hybrydowego Laser-MIG/MAG.
Zaawansowany system sensoryczny, wykorzystujący specjalizowany skaner laserowy, umożliwia korekcję trajektorii głowicy hybrydowej on-line (podczas spawania). Pozwala to kompensować odkształcenia detali spawanych – termiczne (będące skutkiem ciepła pochodzącego z procesu spawania) i mechaniczne (ugięcia długich konstrukcji). Zastosowanie śledzenia on-line spoiny umożliwia spawanie za pomocą robotów przemysłowych detali, które do tej pory mogły być łączone tylko spawaniem ręcznym, ze względu na niepowtarzalność wymiarową detali, jak i odkształcenia występujące w czasie procesu.
Potwierdzeniem wysokiego poziomu technicznego zrobotyzowanego spawania hybrydowego Plazma-MIG/MAG oraz jego potencjału aplikacyjnego są liczne nagrody i wyróżnienia uzyskane podczas krajowych i międzynarodowych pokazów oraz imprez wystawienniczych. Do ostatnio otrzymanych należą Medal Targów Expo Silesia, który jest najważniejszą nagrodą prestiżowego konkursu na najlepszy produkt/technologię prezentowaną na Międzynarodowych Targach Spawalniczych ExpoWELDING 2016 oraz wyróżnienie w kategorii „produkt przyszłości konsorcjum: jednostka naukowa – przedsiębiorca” w konkursie Polski Produkt Przyszłości 2016, organizowanym przez PARP.
Kontakt
Modelowe zrobotyzowane stanowisko spawania, po zakończeniu projektu RobWeld, pozostało w Instytucie PIAP z przeznaczeniem do wykorzystania w przyszłych pracach badawczych i rozwojowych. Zainteresowanych zachęcamy do kontaktu z Instytutem PIAP (dane poniżej w ramce). Odpowiemy na pytania oraz prześlemy dalsze informacje (ulotka, certyfikat, artykuły). Możliwe jest umówienie się na prezentację stanowiska. Możemy również przygotować i przeprowadzić próby na dostarczonych próbkach i elementach. PIAP kontynuuje współpracę zarówno z firmą SupraElco, jak też z firmą Weldobot (Izrael), która wykupiła PLT i jest obecnie dostawcą zestawów hybrydowych Plazma-MIG/MAG. Możemy więc zaoferować kompletną ocenę i konsultacje przedstawionego problemu od strony technologii i automatyzacji/robotyzacji procesu.
PRZEMYSŁOWY INSTYTUT AUTOMATYKI I POMIARÓW PIAP
Al. Jerozolimskie 202, 02-486 Warszawa
tel. 22 874 01 94, 22 874 04 42, fax 22 874 02 16
e-mail: mechatronika@piap.pl
www.piap.pl
źródło: Automatyka 6/2017
Słowa kluczowe
PIAP, Plazma-MIG/MAG, roboty przemysłowe, Robotyzacja spawania, spawanie, spawanie zrobotyzowane
Komentarze
blog comments powered by Disqus