Końcówka prądowa a ciągłość i stabilność spawania
Marcin Niemiec drukuj
Końcówka prądowa jest jedną z najmniejszych i relatywnie najtańszych części uchwytu spawalniczego, jednak jej wady lub zużycie mogą być przyczyną awarii prowadzących do przestojów produkcyjnych generujących duże koszty. W większości przypadków straty ekonomiczne spowodowane zużyciem końcówki prądowej wielokrotnie przewyższają wartość nowej części.
Podstawowym zadaniem każdej końcówki prądowej jest przekazanie prądu elektrycznego do podawanego drutu spawalniczego. Kontakt elektryczny występuje między podawanym drutem a ścianką otworu końcówki. Wady końcówki prądowej, występujące zarówno w procesie spawania zrobotyzowanego, jak i ręcznego, możemy podzielić na:
- powodujące zatrzymanie procesu,
- powodujące brak zajarzenia (przyklejenie drutu, zły start, niestabilność łuku),
- wpływające na jakość kładzionej spoiny.
W procesie spawania ręcznego zazwyczaj o wymianie końcówki na nową decyduje spawacz, a ewentualne problemy są na bieżąco monitorowane. W aplikacjach zrobotyzowanych użytkownicy dążą do zachowania maksymalnej ciągłości procesu oraz zminimalizowania przestojów, toteż końcówki prądowe wymieniane są według narzuconego harmonogramu – najczęściej co jedną lub kilka zmian produkcyjnych. Jednocześnie końcówkom stawiane są bardzo wysokie wymagania jakościowe, ponieważ konieczność nieplanowanego zatrzymania procesu skutkuje poważnymi stratami.
Powtarzalność punktu roboczego uchwytu robota, tzw. TCP (ewentualna jego automatyczna kalibracja), jest niezbędna, aby uniknąć kosztownej korekty programowej trajektorii robota. Jednym z istotniejszych problemów związanych z dokładnością pozycji TCP jest wytarcie eliptyczne końcowej części otworu wylotowego końcówki (fot. 1) spowodowane tarciem drutu spawalniczego o ścianki kanału wewnętrznego. Tego typu uszkodzenia w spawaniu na stacji zrobotyzowanej mogą być przyczyną braku przetopu lub przepaleń/nadpaleń.
W wyniku przeprowadzonych badań okazało się, że końcówka prądowa najczęściej ulega uszkodzeniu w strefie wylotu. W tym obszarze natężenie prądu oraz temperatura są na tyle duże, że dochodzi do tzw. erozji elektrycznej oraz ścierania i utleniania – zjawisk znacznie przyspieszających zużycie. W rezultacie prąd przekazywany do drutu jest zbyt niski lub niestabilny. Przepływ prądu zależy w dużym stopniu od rezystancji na styku pomiędzy drutem i kanałem końcówki, a przewodność elektryczna odgrywa zasadniczą rolę w długości pracy końcówek prądowych. Zastosowanie stopu o jak najwyższej przewodności elektrycznej spowoduje więc wzrost żywotności końcówek prądowych.
Dobór końcówki prądowej
Od wielu dekad materiałem wybieranym do produkcji końcówek prądowych była miedź, głównie z powodu drugiej po srebrze najlepszej przewodności elektrycznej. Jednakże jej uporządkowana regularno-ścienna struktura krystaliczna powoduje naturalną ciągliwość materiału, co w połączeniu z małą twardością miedzi ogranicza jej zastosowanie.
Miedź może być ulepszana w procesach gniecenia na zimno, utwardzania wydzielinowego i dyspersyjnego. Najpopularniejszy i najtańszy stop miedzi, stosowany od lat do produkcji końcówek prądowych, to miedź odtleniana fosforem DIN 2.0090 Cu – DHP.
Stopy utwardzane poprzez domieszkowanie innych pierwiastków, takie jak FTC DIN 2.1293 (CuCrZr) i DIN 2.1291 (CuCr) są powszechnie stosowane do produkcji końcówek prądowych o podwyższonej jakości – tzw. utwardzanych. Niestety procesy umacniania miedzi powodują pogorszenie jej przewodności elektrycznej. W efekcie optymalny dobór końcówki prądowej zależy od rodzaju spawania oraz wielu czynników zewnętrznych.
Porównanie możliwości, jakie dają różne materiały, z których wykonane są końcówki prądowe przedstawia się następująco:
- DHP – Cu99,9% – miedź odtleniana fosforem, standardowy materiał, bardzo dobre właściwości.
- FTC – CuCrZr – stop o podwyższonej twardości stosowany do spawania ręcznego i zrobotyzowanego. Znakomicie sprawdza się w przypadku sztywnych i abrazyjnych drutów stopowych i rdzeniowych. Jest bardzo szeroko stosowany jako uniwersalny materiał dla wymagających aplikacji.
- CuAg – opracowany we współpracy z japońskimi producentami OEM sprzętu spawalniczego. Przewodność elektryczna materiału miedź-srebro (CuAg) wynosi 98% IACS. Nie jest zaskoczeniem, że przewodność elektryczna jest parametrem wyróżniającym końcówkę prądową ze stopu CuAg. Materiał ten znalazł zastosowanie przy produkcji końcówek o podwyższonych właściwościach ograniczających występowanie zjawiska erozji elektrycznej. Cechy te są bezpośrednio związane z niższą temperaturą pracy, lepszą przewodnością oraz zdolnościami przenoszenia łuku elektrycznego przez końcówki. Charakteryzuje się płynnym zajarzeniem łuku w spawaniu zrobotyzowanym i automatycznym. Doskonale sprawdza się przy pracy z drutem stalowym, aluminiowym oraz niektórymi rodzajami drutów rdzeniowych.
- CEP – wynalezienie innowacyjnego procesu wyciskania hydrostatycznego umożliwiło produkcję kompozytowych rurek grubościennych przeznaczonych do produkcji końcówek prądowych, które łączą cechy dwóch materiałów. Materiałem zewnętrznym jest czysta miedź E-Cu (najlepsza przewodność elektryczna i relatywnie niska cena), a kanał prowadzący wykonany jest z miedzi dyspersyjnie utwardzanej (bardzo dobra twardość w wysokiej temperaturze pracy – około 160 HB przy temperaturze do 800 °C, podwyższona odporność na ścieranie abrazyjne). Wewnętrzny kanał prowadzący drut jest idealnie okrągły. Możemy również dostarczyć końcówki z kanałem wewnętrznym o przekroju w kształcie gwiazdy pięcioramiennej, charakteryzujące się lepszym przyleganiem drutu do ścianek oraz o około 30% większą zdolnością odprowadzania zanieczyszczeń i złuszczeń drutu.
Przyczyny zużycia końcówek prądowych
Erozja elektryczna jest zjawiskiem bardzo podobnym do pracy szczotek w silniku elektrycznym lub do zjawiska iskry w świecy zapłonowej. Drut spawalniczy jest podawany poprzez końcówkę z szybkością około 8 m/min, a prąd elektryczny musi zostać przekazany z końcówki prądowej do drutu, stąd potoczna nazwa „końcówka kontaktowa”. Na styku między drutem a wewnętrznym otworem końcówki występuje zjawisko ciągłego łuku elektrycznego. W efekcie erozji elektrycznej powierzchnia kontaktowa otworu stopniowo się powiększa/wytapia. Gdy kluczowe dla użytkownika jest płynne zajarzenie łuku, należy stosować stop miedzi o najlepszych parametrach elektrycznych. Jeśli przewodność końcówki prądowej będzie wyższa, przekazanie przez nią prądu elektrycznego do drutu będzie płynniejsze.
Kolejnym czynnikiem wpływającym na pracę końcówki oraz jej zużycie jest temperatura pracy. Podczas nagrzewania się końcówki w procesie spawania materiał mięknie i staje się mniej odporny na ścieranie. Zdolność końcówki do rozpraszania ciepła (przewodność cieplna) odgrywa ważną rolę w utrzymaniu właściwej temperatury pracy, natomiast niższa temperatura pracy końcówki wpływa korzystnie na stabilność kontaktu elektrycznego pomiędzy końcówką a drutem.
Przyczyny szybkiego zużycia końcówki prądowej mogą być różne – często decydujący wpływ mają również czynniki zewnętrzne.
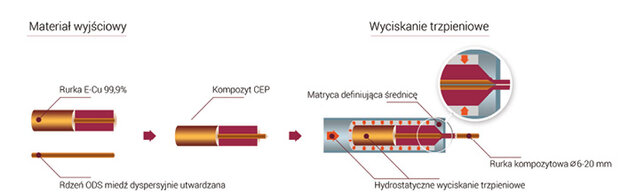
Rys. 1. Schemat hydrostatycznego wyciskania trzpieniowego rurek kompozytowych CEP – Compound Extrusion Products GmbH
Oporność elektryczna materiału jest odwrotnie proporcjonalna do jego przewodności elektrycznej i wpływa bezpośrednio na wytwarzane ciepło. Wyższa przewodność elektryczna poprawia przekazanie prądu elektrycznego do końcówki, co ułatwia zajarzenie łuku oraz redukuje zjawisko przyklejania się drutu i występowanie odprysków. W przypadku maszyn pracujących w trybie pulsacyjnym PULSE, gdzie prąd szczytowy osiąga bardzo wysoką wartość, najlepiej będą pracowały końcówki prądowe z materiałów FTC i CEP. Proponujemy również sprawdzić końcówki ze stopu CuAg dla spawania ręcznego. Podczas spawania zabrudzonym lub łuszczącym się drutem zanieczyszczenia zbierają się na „wejściu” końcówki. Zalecana jest wówczas częstsza wymiana prowadników drutu lub wprowadzenie dodatkowego czyszczenia drutu przez oczka/szczotki. Najlepszym wyborem będzie jednak zakup drutu dobrej jakości od innego producenta.
Zanieczyszczenia są przyczyną wypaleń w końcówce spowodowanych przez cofanie się łuku. Jeśli zanieczyszczenia są suche i działają tylko abrazyjnie, zastosowanie końcówek utwardzonych FTC wydłuży czas eksploatacji. W przypadku smarów i innych zanieczyszczeń oleistych sugerujemy stosowanie końcówek standardowych DHP, ponieważ końcówki bardzo szybko zapychają się i wypalają, co powoduje konieczność częstej ich wymiany, a użytkownik zwraca zwykle uwagę na najniższą cenę.
Druty rdzeniowe są w procesie produkcyjnym ciągnione na zimno lub na gorąco. Miękki drut rdzeniowy można wyginać, zaś twardy zazwyczaj pęknie przy próbie przegięcia. Miękkie druty rdzeniowe, podawane przez podajnik z kołami prowadzącymi o części roboczej w kształcie litery U, będą doskonale pracowały z końcówkami CuAg. Rolki podajnika o powierzchni roboczej w kształcie litery V, płaskie lub radełkowane, deformują drut stalowy oraz powodują łuszczenie się drutu powlekanego. Zastosowanie utwardzonych końcówek prądowych FTC będzie najlepszym wyborem.
Końcówki standardowe Cu-DHP są proponowane tylko klientom kupującym duże ilości części do manualnego spawania zwykłym drutem, gdzie najważniejszym kryterium wyboru jest cena. Przyklejanie się drutu, brak zajarzenia czy też słaby zapłon łuku mogą być spowodowane wieloma czynnikami, np. zabrudzonym prowadnikiem i/lub końcówką prądową, zwiniętym, przegiętym czy skręconym przewodem uchwytu spawalniczego lub przewodu między podajnikiem a uchwytem spawalniczym na robocie. Istotny wpływ ma również zbyt duża lub zbyt mała odległość końcówki od spoiny podczas spawania, stan przewodów masowych i podających drut, występujący olej, brud oraz zgorzelina na powierzchni konstrukcji spawanej, duża liczba odprysków przy ocynkowanych blachach czy słabo dokręcona końcówka lub dyfuzor. Stosowanie końcówek prądowych ze stopów CuAg, FTC i CEP pomoże zminimalizować powyższe problemy, ale ich nie wyeliminuje.
Zużycie części wylotowej końcówki prądowej wynika zarówno z twardości i parametrów samej końcówki, jak i ze zbyt długiego czasu, jaki upływa między jedną a drugą jej wymianą. Jeśli przerwy związane ze zużyciem końcówki występują rzadko i po jej wymianie proces przebiega prawidłowo, można przyjąć taki stan jako punkt odniesienia dla testów końcówek z naszych materiałów. Wyniki testów zwykle przekładają się wprost na oszczędności.
Firma Plasma Point Polska specjalizuje się w oferowaniu części zużywających się do procesu cięcia i spawania. Współpraca z firmą umożliwia zoptymalizowanie zużycia części eksploatacyjnych i obniżenie kosztów ich zakupu. Dodatkowym, a często kluczowym aspektem jest poprawa jakości wyrobów, zmniejszenie przestojów produkcyjnych i liczby re-worków oraz stabilność punktu roboczego TCP przy spawaniu zrobotyzowanym.
Końcówki oferowane przez firmę wytwarzane są w cyklu automatycznym na zadaniowych maszynach produkcyjnych. Stosowane są wciskane rurki grubościenne najwyższej jakości, bez domieszek miedzi z recyklingu, renomowanych europejskich producentów stopów miedzi przeznaczonych dla procesów spawania. Głównymi klientami firmy Plasma Point Polska są firmy z sektora Automotive wykorzystujące części w zrobotyzowanych kabinach spawalniczych, co potwierdza najwyższą jakość wyrobów. Firma dostarcza części eksploatacyjne do urządzeń spawalniczych takich producentów jak Fronius, Binzel, OTC, SKS, Dinse, Lincoln, Keempi, Esab i Bernard oraz do spawania łukiem krytym według standardu Esab, Miller i Lincoln.
Plasma Point Polska nie jest w jakikolwiek sposób związana z producentami wyszczególnionymi powyżej. Oferowane komponenty nie są oryginalnymi częściami, lecz zostały wyprodukowane przez Plasma Point na podstawie własnej dokumentacji konstrukcyjnej. Nawiązanie do nazw maszyn, palników i numerów referencyjnych tych firm zostało użyte jedynie w celu ułatwienia i wygody kupującego.
PLASMA POINT POLSKA
ul. Jedności 27, 43-100 Tychy
tel. 32 780 18 91, fax 32 780 18 93
e-mail: biuro@plasmapoint.pl
www.plasmapoint.pl
źródło: Automatyka 6/2016
Komentarze
blog comments powered by Disqus