Pierwsze krajowe centrum wytwórcze technologii addytywnych
Maciej Cader (Łukasiewicz – PIAP) drukuj
Od 2014 r. w Przemysłowym Instytucie Automatyki i Pomiarów PIAP trwały prace nad stworzeniem pierwszego polskiego centrum wytwórczego do technologii addytywnych (druku 3D) spełniającego standardy przemysłowe. W czasie dwóch lat został opracowany model, a na jego podstawie gotowa maszyna (fot. 1) pracująca w technologii FDM – produkcja na bazie nakładania cienkich włókien termoplastycznego polimeru. Aktualnie FORIND 500 przechodzi procedurę nadawania znaku CE.
Maszyna FORIND 500 swoją nazwę zawdzięcza zlepkowi angielskich słów: for industry (dla przemysłu), for industrial needs (dla potrzeb przemysłu) oraz for individual needs (w rozumieniu realizacji indywidualnej, nie tylko małoseryjnej produkcji).
Funkcjonalna konstrukcja
Najważniejszą cechą maszyny FORIND 500 jest to, że ma zamkniętą, dużą komorę roboczą (fot. 2) umożliwiającą budowanie modeli o wymiarach 450 × 450 × 500 mm w stałych i stabilnych warunkach. To pozwala na wytwarzanie wielkogabarytowych modeli z ABS-u i poliwęglanu bez obaw o ich uszkodzenie wynikające ze zbyt niskiej lub niestabilnej temperatury oraz wilgotności. Komora jest odizolowana od komponentów maszyny, dzięki czemu można wytwarzać wielogodzinnie duże modele bez obawy, że komponenty nadmiernie się przegrzeją. W komorze znajduje się stół modelowy. Budowanie modelu odbywa się na specjalnej polimerowej podstawie modelowej przytwierdzanej do stołu za pomocą generowanego podciśnienia (fot. 2). Są to podstawy modelowe o bardzo silnej adhezji, dzięki czemu zapobiegają odklejaniu się modelu od stołu podczas procesu wytwarzania. Mata przylega do stołu dzięki podciśnieniu wygenerowanemu przez zintegrowaną z maszyną pompę podciśnienia, co zapewnia jej idealne przyleganie do stołu modelowego i eliminuje niepożądane przesunięcia. Płyta stołu modelowego ma wyfrezowane kanały, dzięki którym generowane pomiędzy podstawą modelową i stołem modelowym podciśnienie jest równomierne dla całej powierzchni. Zapewnia to odpowiednią dokładność nakładania polimeru i w następstwie odpowiednią jakość modeli.
Maszyna ma system podwójnej ekstruzji – łatwo wymienialne dwie dysze produkcji Stratasys, które dają możliwość wytwarzania dowolnych kształtów z wykorzystaniem dwóch materiałów, m.in. wypłukiwalnego materiału podporowego. FORIND 500 ma system automatycznej kalibracji wysokości dysz oraz możliwość wytwarzania dyszami o różnej średnicy przetłaczania – z różną dokładnością i prędkością.
W celu zapewnienia najwyższej jakości powierzchni budowanych modeli maszyna jest wyposażona w czyścik dysz. Zadaniem czyścika jest oczyszczenie dysz z materiału, który odłożył się na ich powierzchniach lub wycieka, co jest naturalne w technologii FDM.
Zasobnik materiału
Nie bez znaczenia jest fakt, że FORIND 500 został wyposażony w komorę zasobnikową, znajdującą się w dolnej części maszyny, która umożliwia przechowywanie do czterech kaset materiału w stabilnych warunkach środowiskowych. Ponadto ma system automatycznego ładowania materiału – wystarczy wprowadzić włókno materiału do stożkowego otworu, a następnie maszyna sama go załaduje do głowicy i usunie resztki poprzedniego tworzywa z dyszy.
Mózg i interfejs maszyny
Mózgiem maszyny FORIND 500 jest wbudowany komputer klasy PC, który umożliwia przygotowanie modelu do wydruku bez konieczności podłączania dodatkowego komputera. Moc komputera pozwala na zainstalowanie również oprogramowania do projektowania, obróbki graficznej oraz skanowania 3D. Dzięki temu FORIND 500 jest niezależnym centrum technologii 3D. Wyprowadzone porty umożliwiają również podłączenie skanera 3D lub innych rządzeń peryferyjnych, np. drukarki 2D (do drukowania dokumentacji) bądź innych urządzeń działających w standardzie USB 3.0. Interfejsem komunikacyjnym jest ruchomy, dotykowy, pojemnościowy ekran 22”, który pozwala optymalnie sterować procesem przygotowania geometrii do wytwarzania oraz oprogramowaniem zainstalowanym w komputerze pokładowym drukarki 3D. Ruchome posadowienie monitora pozwala dostosować kąt pochylenia odpowiedni dla wygody użytkownika.
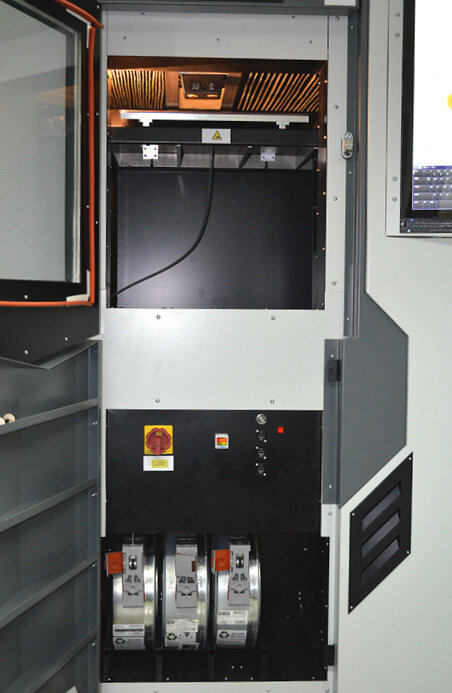
Fot. 3. Front maszyny FORIND 500 po otwarciu drzwi komory roboczej (u góry) i komory zasobnikowej (u dołu)
źródło: Automatyka 5/2016
Komentarze
blog comments powered by Disqus