Bezpieczeństwo maszyn i urządzeń
Marcin Bieńkowski drukuj
Prawodawstwo poszczególnych krajów, nie tylko Unii Europejskiej, coraz większy nacisk kładzie na bezpieczeństwo funkcjonowania maszyn i urządzeń. Wiąże się to z coraz większą automatyzacją środków produkcji oraz szerszym wprowadzaniem na hale produkcyjne systemów autonomicznych posiłkujących się algorytmami sztucznej inteligencji. Pozostawienie działania maszyn, linii i urządzeń „samym sobie”, wymusza opracowanie odpowiednich środków bezpieczeństwa, tak aby nie stanowiły zagrożenia dla pracowników.
Eliminacja potencjalnych zagrożeń, które związane są z funkcjonowaniem linii produkcyjnych, maszyn czy urządzeń jest w bezpośrednim interesie ekonomicznym funkcjonowania przedsiębiorstwa. Oprócz wyeliminowania wszelkich konsekwencji związanych z wypłatą odszkodowań osobom, które uległy wypadkowi, konieczności zapewnienia im opieki medycznej oraz szeregu strat związanych z powypadkowymi przestojami, które często są uzależnione od zewnętrznej decyzji prokuratora (ciężki uszczerbek na zdrowiu, zdarzenie śmiertelne), podniesiona zostaje odporność linii produkcyjnej na ludzkie błędy. Zmniejsza się też w istotny sposób czas nieplanowanych przestojów i wyraźnie wydłuża okres bezawaryjnej pracy maszyn, urządzeń, a nawet całych linii technologicznych.
W tym miejscu należy podkreślić, że z bezpieczeństwem systemów przemysłowych, w tym maszyn i urządzeń, związane jest też bezpieczeństwo funkcjonalne. Termin ten odnosi się do systemu sterowania, którego jakość działania zależy od prawidłowego funkcjonowania elementów realizujących zdefiniowane funkcje bezpieczeństwa oraz od zewnętrznych rozwiązań i czujników zmniejszających ryzyko wystąpienia zagrożeń. Dobrym przykładem tego typu zewnętrznych systemów bezpieczeństwa, są różnego rodzaju czujniki elektromechaniczne, kurtyny świetlne, czy maty bezpieczeństwa.
Klasyfikacja zagrożeń
Zagrożenia, z jakimi możemy mieć do czynienia w przemyśle, klasyfikowane są ze względu na stopień ich uciążliwości oraz ze względu na ich rodzaj i charakter. Co prawda praca w warunkach uciążliwych nie stwarza bezpośredniego zagrożenia, ale zwykle utrudnia wykonywanie powierzonych zadań i męczy pracownika. Jeśli chodzi zaś o czynniki szkodliwe, na które narażeni są ludzie podczas pracy, to mogą one wywoływać u nich szereg chorób zawodowych lub osłabiać reakcje pracowników na niebezpieczne bodźce.
Z punktu widzenia bezpieczeństwa przemysłowego przyjmuje się, że najgroźniejsze są jednak warunki niebezpieczne, które zwykle działają w sposób nagły i mogą spowodować poważne urazy czy zatrucia u pracownika, a w skrajnych wypadkach doprowadzić do jego śmierci. To dlatego przy wdrażaniu aplikacji automatyzujących produkcję i związanych z tym systemów bezpieczeństwa, najistotniejsze są właśnie te, niespodziewanie pojawiające się, warunki niebezpieczne. Również i przepisy nakładają w tej kwestii wymóg bezwzględnego zabezpieczenia pracowników przed warunkami niebezpiecznymi, które mogą pojawić się niespodziewanie.
Wróćmy jednak do klasyfikacji. Ze względu na swój charakter, zagrożenia szkodliwe oraz uciążliwe dzieli się na cztery główne grupy:
- czynniki fizyczne, np. mechaniczne, związane z odpryskami czy opiłkami metalu powstającymi podczas obróbki skrawaniem;
- psychofizyczne związane z kondycją i koncentracją człowieka, np. zmęczeniem czy hałasem;
- zagrożenia chemiczne związane z kontaktem pracownika z niebezpiecznymi materiałami chemicznymi. Materiały te mogą być zarówno surowcem, produktem, jak i odpadem bądź produktem ubocznym prowadzonego procesu technologicznego;
- zagrożenia biologiczne, do których zalicza się mikroorganizmy, tj. grzyby, wirusy czy bakterie, mogą być związane z przebiegiem mikrobiologicznego procesu technologicznego.
Wypadki i ochrona
Do wypadków w przemyśle, jak wskazują statystyki, dochodzi najczęściej na skutek nieprawidłowych i nieprzemyślanych zachowań pracowników. Tego typu zachowania wynikają z wielu powodów. Najczęstszą przyczyną niebezpiecznych zachowań w miejscu pracy jest brak wystarczającej wiedzy na temat prawidłowego i bezpiecznego sposobu wykonywania pracy i obsługi maszyn (niewystarczające szkolenia), złej oceny poziomu ryzyka dla określonego zachowania, złej organizacji pracy, wiedzy o konsekwencji niebezpiecznych zachowań oraz braku świadomości dotyczącego bezpieczeństwa pracy. Najlepszą i najskuteczniejszą metodą eliminowania zagrożeń są szkolenia BHP i doskonalenie umiejętności związanych z wykonywaną pracą i obsługą maszyn. Tego typu szkolenia muszą być też prowadzone dla doświadczonych pracowników z długim stażem, by zapobiec rutynie, która również jest praprzyczyną wielu wypadków.
Kolejnym, istotnym elementem bezpieczeństwa przemysłowego są odpowiednie stroje robocze oraz środki ochrony osobistej. Do tej grupy zalicza się wszelkie urządzenia, stroje oraz wyposażenie, które noszone są lub trzymane przez pracownika w charakterze ochrony przed zagrożeniami. Jak można się domyślić, w tej grupie „sprzętu” znajdziemy m.in. rękawice ochronne, fartuchy, stroje robocze ze wzmocnieniami, specjalne buty chroniące stopę przed upadkiem na nią ciężkich przedmiotów, kaski, przyłbice, maski, aparaty tlenowe czy okulary ochronne itp.
Obecnie bezpośredni wpływ na bezpieczeństwo przemysłowe mają też różnego rodzaju automatyczne systemy zabezpieczeń. Ich zadaniem jest nie dopuścić do wystąpienia zagrażającej życiu i zdrowiu ludzi sytuacji. Najczęściej są to, wspomniane już kurtyny świetlne, które po przekroczeniu przez człowieka lub autonomiczny system transportu wewnętrznego granic obszaru roboczego maszyny lub robota, natychmiast wyłączają urządzenie, a nawet całą linię, nie dopuszczając tym samym do wystąpienia groźnej sytuacji.
Oczywiście rodzaj tego typu zabezpieczeń zależy zwykle od maszyny, ustawienia linii, strefy pracy robota czy wielu innych czynników, często specyficznych dl dla rodzaju produkcji i branży. Największym odbiorcą automatycznych systemów zabezpieczeń jest branża maszynowa i drzewna, do których zalicza się wszelkich wytwórców obrabiarek, maszyn, środków transportu oraz producentów niewielkich urządzeń mechanicznych, takich jak piły, szlifierki kątowe czy wiertarki. Jeśli chodzi o branżę drzewną, zabezpieczone są nie tylko maszyny ale i wydzielone obszary i gniazda robocze, co wynika ze specyfiki procesu technologicznego, gdzie wykorzystywane są otwarte, wirujące ostrza (strugi, pilarki, piły tarczowe itp.) niezbędne do prawidłowej obróbki drewna.
Warto tu podkreślić, że konieczność stosowania odpowiednich, zautomatyzowanych zabezpieczeń dotyczy tych maszyn, w których występuje częsta interakcja z człowiekiem, który może podawać komponenty czy surowce i odbiera gotowe produkty, a dodatkowo występują w tym procesie duże siły (np. prasy czy walcownie) oraz/lub duże prędkości ruchu elementów roboczych, tak jak ma to miejsce w przypadku frezarek, szlifierek, tokarek czy różnego typu zautomatyzowanych centrów obróbczych i obrabiarek CNC. Jak już kilkukrotnie wspomniano, odpowiedniego zabezpieczenia wymagają też gniazda produkcyjne, w tym gniazda zrobotyzowane i zautomatyzowane oraz linie i instalacje przemysłowe, a nawet całe ciągi technologiczne. To ostatnie dotyczy przede wszystkim przemysłu przetwórstwa drzewnego, papierniczego, systemów kopalnianych, produkcji cementu, instalacji chemicznych i petrochemicznych.
Co ważne, systemy zabezpieczające różnego rodzaju ciągi produkcyjne, instalacje i linie technologiczne oprócz pełnienia funkcji związanych stricte z bezpieczeństwem nadzorują również, pod względem dostępu pracę inteligentnej fabryki, wykorzystującej rozwiązania Internetu Rzeczy. Raportowane są tu wszelkie zdarzenia związane ze stanem linii produkcyjnych, otwarciem osłon, zatrzymaniem maszyn, dostępem uprawnionych osób do określonych, wydzielonych stref czy innych obszarów i zadań związanych bezpośrednio lub pośrednio z zapewnianiem bezpieczeństwa pracownikom. Oddzielną kwestią jest transport i logistyka wewnętrzna, gdzie systemy automatycznego bezpieczeństwa pełnią kluczową rolę w zapobieganiu wypadkom.
Dyrektywa maszynowa
Aby zapobiec sytuacji, że każdy producent systemów bezpieczeństwa będzie je rozumiał po swojemu, a każdy użytkownik stosuje je w dowolny, wygodny dla siebie sposób, ale nie koniecznie zgodny z zasadami bezpieczeństwa, wprowadzono szereg regulacji, zarówno krajowych, jak i międzynarodowych. Z naszego punktu widzenia najważniejszą z tych regulacji, na poziomie Unii Europejskiej, jest tzw. Dyrektywa Maszynowa. Oficjalny tytuł to: Dyrektywa 2006/42/WE Parlamentu Europejskiego i Rady z dnia 17 maja 2006 r. w sprawie maszyn, zmieniająca dyrektywę 95/16/WE. Weszła ona w życie 29.12.2009 r., co oznacza, że niezależnie od miejsca i daty wyprodukowania, wszystkie maszyny użyte po raz pierwszy na terenie UE po 1 stycznia 1995 r. podlegają wymaganiom Dyrektywy Maszynowej oraz muszą być oznaczone znakiem CE. Polskie rozporządzenie wdrażające Dyrektywę maszynową 2006/42/WE należy czytać łącznie z ustawą o systemie oceny zgodności (Dz.U. z 2019 r. poz. 155, z póżn. zm.). Przepisy unijne wynikające z Dyrektywy maszynowej określają tzw. wymagania zasadnicze dla maszyn. Niemniej konkretny produkt może podlegać przepisom nawet kilku aktów prawnych dotyczących bezpieczeństwa wyrobów. W tym miejscu trzeba jeszcze dodać, że 26 lipca 2019 r. weszło w życie rozporządzenie 2019/1243, którego przepisy umożliwiają Komisji Europejskiej w ramach tzw. procedury regulacyjnej, wydawanie w zakresie dyrektywy maszynowej aktów delegowanych.
Co w praktyce reguluje dyrektywa
W skrócie, dyrektywa maszynowa to jeden z najważniejszych aktów prawnych harmonizujących zasadnicze wymogi w zakresie bezpieczeństwa maszyn w Unii Europejskiej. Określa ona znormalizowane wymagania w zakresie bezpieczeństwa i higieny pracy. Dyrektywa wspiera swobodny przepływ maszyn w ramach jednolitego rynku i gwarantuje wysoki poziom ochrony pracowników i obywateli UE. Istotne jest to, aby producent maszyny lub jego upoważniony przedstawiciel przeprowadził ocenę ryzyka w celu określenia, mających zastosowanie do tej maszyny, zasadniczych wymagań w zakresie bezpieczeństwa i ochrony zdrowia.
Co to oznacza w praktyce? Przede wszystkim to, że każda maszyna powinna być zaprojektowana i wykonana z uwzględnieniem wyników wspomnianej przed chwilą oceny. Układy sterowania muszą być zaprojektowane i wykonane tak, aby zapewniały maksymalne bezpieczeństwo oraz zapobiegały powstawaniu sytuacji, w których może wystąpić zagrożenie. Ponadto jakiekolwiek defekty sprzętu komputerowego i oprogramowania układów sterowania nie mogą prowadzić do powstawania sytuacji niebezpiecznych. Co więcej, systemy sterowania muszą również być odporne na wszelkiego typu obciążenia wynikające z ich zastosowania oraz na wpływ czynników zewnętrznych. Również i tu błędy w układach logicznych nie mogą prowadzić do powstawania sytuacji niebezpiecznych. Jeśli to możliwe, to sterowanie powinno uwzględniać czynnik ludzki, czyli być odporne na wszystkie możliwe do przewidzenia błędy, jakie pracownicy mogą popełnić w trakcie obsługi maszyny czy urządzenia, tak aby te nieodpowiedzialne czynności nie prowadziły do powstawania sytuacji niebezpiecznych.
Przy projektowaniu jakichkolwiek maszyn czy urządzeń, a także linii technologicznych lub infrastruktury przemysłowej należy zwrócić szczególną uwagę na to, aby maszyny nie mogły się samoistnie i nieoczekiwanie uruchomić, a parametry ich pracy nie mogą się zmieniać w sposób niekontrolowany, jeżeli tego typu zmiany mogą prowadzić do nieoczekiwanych, niebezpiecznych sytuacji. Co więcej, po wydaniu przez operatora polecenia dotyczącego zatrzymania, a zwłaszcza zatrzymania awaryjnego, wszelkie wchodzące w skład systemu urządzenia lub cała linia technologiczna muszą się zatrzymać. Mało tego, żadna ruchoma część ani zamocowany element nie może też odpaść lub zostać wyrzucony w trakcie procesu zatrzymania.
Inżynierowie projektujący maszynę, muszą też położyć nacisk na to, aby automatyczne lub ręczne zatrzymywanie części ruchomych nie mogło być zakłócone, czyli np. nie może nastąpić ponowny, nieoczekiwany rozruch lub niekontrolowane zwiększenie prędkości obrotowej. Oprócz tego wszystkie elementy układu sterowania związane z bezpieczeństwem muszą działać w sposób spójny w całym zespole maszyn lub na linii technologicznej, nawet jeśli system lub maszyna nie są w całości oddane do użytku, co ma na celu przede wszystkim ochronę osób odpowiedzialnych za montaż i rozruch. Tak przygotowana maszyna powinna charakteryzować się tak zwaną „Deklaracją zgodności”. Pod tym pojęciem kryje się oświadczenie producenta, stwierdzające, na jego wyłączną odpowiedzialność, że wyrób, proces wytwórczy lub usługa są zgodne z określoną normą lub innym dokumentem normatywnym.
Zmiany dotyczące dyrektywy
Dyrektywa nie może być aktem skończonym i zamkniętym. Na jej kształt musi bowiem wpływać rozwój technologiczny dotyczący konstrukcji maszyn i systemów automatyki, zwłaszcza tych działających autonomicznie w ramach rozwiązań cyfrowej fabryki i Przemysłu 4.0, a także zmiany zachodzące w systemach produkcyjnych, jako całości – od zarządzania po produkcję. Tak więc dyrektywa maszynowa wymaga cyklicznych aktualizacji w celu zwiększania poziomów bezpieczeństwa, w tym w większym stopniu uwzględnienia kwestii bezpieczeństwa oraz nadążania za rozwojem technologicznym zgodnie z założeniami Przemysłu 4.0. Obecnie Komisja Europejska zakończyła etap zgłaszania uwag w sprawie rewizji Dyrektywy Maszynowej. Proponowane nowelizacje mają objąć [3]:
- dostosowanie dyrektywy do zharmonizowanego prawodawstwa UE w zakresie zdrowia i bezpieczeństwa produktów;
- usunięcia braków przejrzystości prawnej co do zakresu i definicji, w szczególności definicji „maszyny nieukończonej” powodującej niepewność prawną i dodatkowe koszty dla podmiotów gospodarczych i organów krajowych oraz wyraźnego rozgraniczenia wyłączeń mających zastosowanie w innych przepisach, m.in. Dyrektywy niskonapięciowej;
- dostosowania przepisów do wyzwań związanych z postępem technicznym w cyfryzacji (Sztuczna Inteligencja i Internet Rzeczy).
Niektóre z planowanych zmian w nowym unijnym rozporządzeniu w sprawie maszyn dotyczyć mają [3]:
- Maszyn podlegająch kontroli. Rozszerzono listę maszyn podlegających kontroli. Co więcej, w momencie stosowania norm zharmonizowanych, w przypadku maszyn podlegających kontroli nie będzie już możliwe, aby procedura oceny zgodności była przeprowadzana przez producentów całkowicie samodzielnie.
- Definicji istotnej modyfikacji maszyny oraz o związanych z nią konsekwencji prawnych. W kontekście bezpieczeństwa maszyn procedura oceny zgodności jest wymagana, jeżeli maszyna zostanie poddana istotnym modyfikacjom lub jeżeli zostaną przeprowadzone modyfikacje, które mają wpływ na zgodność maszyny z przepisami dotyczącymi oznakowania CE.
- Podzespołów związanych z bezpieczeństwem. Definicja podzespołów związanych z bezpieczeństwem obejmować ma również oprogramowanie, które pełni funkcję zabezpieczającą.
- Instrukcji w formie cyfrowej. Producenci będą mogli dostarczać instrukcje w formie cyfrowej. Na życzenie klienta producent musi dostarczyć instrukcje w formie papierowej.
- Specyfikacji technicznych. Domniemanie zgodności jest również możliwe w przypadku zgodności ze specyfikacjami technicznymi lub ich częściami.
Jeśli chodzi o Sztuczną Inteligencję (SI), to zagadnienia te porusza odrębny projekt rozporządzenia UE. Ma on obejmować wszystkie produkty wykorzystujące sztuczną inteligencję i jej zastosowania. Przewiduje się, że nie powinny być tu wymagane żadne dodatkowe środki bezpieczeństwa, zostanie jedynie wprowadzona bardziej precyzyjna ich definicja. Przemawia za tym fakt, że skutki działania sztucznej inteligencji są już uwzględnione w istniejących procedurach oceny zgodności i definicji przeznaczenia.
Bezpieczeństwo funkcjonalne – sterowanie
Niezależnie od konstrukcji maszyny czy urządzenia, zawsze nadrzędnym elementem dla systemu bezpieczeństwa jest układ sterowania. Tego typu systemy, pod względem zastosowanej architektury i ich budowy, podzielić można na cztery grupy:
- Maszyny bądź urządzenia z lokalnym systemem sterowania realizującym funkcje bezpieczeństwa w oparciu o przekaźniki bezpieczeństwa.
- Maszyna lub urządzenia z lokalnym lub globalnym systemem sterowania wykorzystującym programowalne przekaźniki bezpieczeństwa.
- Maszyna oraz systemy z rozproszonymi czujnikami bezpieczeństwa i elementami wykonawczymi wykorzystującymi przemysłowe systemy transmisji danych.
- Maszyny, urządzenia bądź linie sterowane globalnie z rozbudowanymi funkcjami bezpieczeństwa.
Najczęściej w systemach przemysłowych w zupełności wystarczają podstawowe, zaimplementowane lokalnie funkcje bezpieczeństwa. Chodzi tu o takie funkcje, jak: awaryjny stop, osłony uniemożliwiające uruchomienie maszyny, jeśli nie są zamknięte oraz różnego rodzaju bariery świetlne. Do takich zastosowań wykorzystać można stosunkowo proste przekaźniki bezpieczeństwa, jak np. Siemens SIRIUS 3Z1R, Schneider Preventa XPSA czy Phoenix Contact PSRSCP 24U. Są to urządzenia realizujące podstawowe funkcje bezpieczeństwa, niewymagające programowania.
Systemy, zarówno z lokalnym, jak i z globalnym programowalnym przekaźnikiem bezpieczeństwa, pozwalają na realizację bardziej złożonych zadań. Tego typu przekaźnik, np. SIRIUS 3SK2, pozwala na swobodne zdefiniowanie zadań i sterujących nimi algorytmów. Do typowych zadań realizowanych przez te urządzenia należą kontrola zatrzymania awaryjnego, kontrola przesunięcia/wychylenia/obrotu, kontrola mat czujnikowych i kurtyn świetlnych oraz kontrola łączników lub rygli blokujących działanie maszyny, jeśli nie są zamknięte osłony lub operator odpowiednio nie ustawił elementów urządzenia.
Zaawansowane przekaźniki bezpieczeństwa, oferują rozbudowaną diagnostykę, sporą liczbę wejść, nawet do 32, parametryzację oraz możliwość przyłączenia ich do nadrzędnego systemu automatyki. Dzięki temu możliwa jest realizacja rozbudowanych aplikacji wykorzystujących wiele funkcji bezpieczeństwa, m.in. muting dla kurtyn świetlnych, monitorowanie wielu osłon i ustawień przełączników nastawczych, w tym z funkcją ryglowania, jak również realizacja funkcji awaryjnego zatrzymania maszyny. Z kolei globalne systemy sterowania, pozwalają z jednego miejsca zarządzać całą rozbudowaną infrastrukturą linii produkcyjnych. Charakteryzują się bardzo dużą liczbą wejść i wyjść oraz znacznie rozbudowanymi funkcjami bezpieczeństwa.
W tym miejscu warto zaznaczyć, że żaden moduł bezpieczeństwa nie jest w stanie prawidłowo funkcjonować bez przekaźników bezpieczeństwa. W układzie bez tego rodzaju przekaźnika nie monitoruje się bowiem zwarć w sytuacji, gdy wyłączniki awaryjne lub styczniki działają prawidłowo, a tego typu awaria może doprowadzić do sytuacji niebezpiecznej. Dlatego rolą przekaźników bezpieczeństwa jest monitorowanie wszystkich połączeń kablowych, stanu wyłączników blokujących, przycisków stopu awaryjnego, wyłączników awaryjnych oraz styczników.
Warto jednak pamiętać, że w prostych aplikacjach, gdzie nie ma uzasadnienia stosowania modułów bezpieczeństwa, gdyż brak jest bezpośredniego niebezpieczeństwa dla ludzi lub istnieje tylko niewielkie zagrożenie, przekaźniki przejmują na siebie takie funkcje jak awaryjny stop, kontrolę drzwi ochronnych, kontrolę barier i kurtyn świetlnych, kontrolę mat naciskowych, prędkości, stanu zatrzymania, a więc wszystkich elementów bezpieczeństwa.
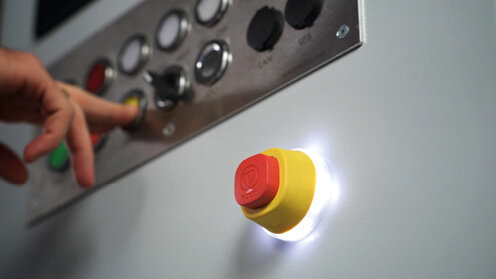
Ponowny rozruch maszyny z funkcją startu monitorowanego – przycisk bezpieczeństwa i przekaźnik Schneider Electric Preventa XPS
Osłony i kontrola krańcowego położenia
Jeśli chodzi o kontrolę położenia osłon stosowanych w maszynach i na liniach produkcyjnych oraz do monitorowania pozycji przesuwnych, uchylnych i zdejmowanych osłon ochronnych, to sensory wykorzystywane w tego typu zadaniach muszą być zgodne z wymaganiami normy PN-EN 60947-5-3. Do tego typu zadań stosuje się przede wszystkim elektromagnetyczne, bezdotykowe czujniki bezpieczeństwa, gdzie występują zjawiska magnetyzmu i indukcji magnetycznej. Co ważne, tego typu czujniki można bez problemu wykorzystać również do monitorowania położenia, w tym kontroli położenia krańcowego.
W wypadku aplikacji związanych z bezpieczeństwem są to zwykle te same czujniki magnetyczne lub indukcyjne, które znaleźć można w standardowych systemach automatyki, ale charakteryzują się tylko nieco inną, bardziej odporną na czynniki zewnętrzne budową korpusu, tak aby mogły pracować w warunkach, w których nie za bardzo się o nie dba. Zazwyczaj czujniki tego typu charakteryzują się odległości przełączania wynoszącą 2–10 mm i stopniem ochrony IP65 lub IP67. Istnieją modele zarówno z komunikacją przewodową, jak i bezprzewodową.
Czym jest maszyna? Na potrzeby dyrektywy maszynowej, maszynę definiuje się jako zespół składający się ze sprzężonych części lub elementów, połączonych w całość mającą konkretne zastosowanie, z których przynajmniej jedna wykonuje ruch. Na potrzeby dyrektywy maszynowej jako maszynę rozumie się ponadto:
Oprócz maszyn wymienionych powyżej dostępna jest również lista wyjątków, tj. maszyn, które – zgodnie z efinicją – objęte są zakresem obowiązywania Dyrektywy, ale ustawowo podlegają odrębnym przepisom. Źródło: Pilz |
Bariery i kurtyny świetlne
Aktualnie najczęściej wykorzystywanym rozwiązaniem dotyczącym bezpieczeństwa maszyn, urządzeń, linii i gniazd produkcyjnych są kurtyny oraz bariery świetlne. Pozwalają zabezpieczyć potencjalnie niebezpieczne strefy, takie jak zrobotyzowane gniazdo obróbcze, czy obszar roboczy prasy hydraulicznej. Wyłączają maszynę w chwili, gdy do takiej strefy wtargnie człowiek lub automatyczny system transportu, a także chronią pracowników przed przypadkowym włożeniem palców czy rąk w niebezpieczną przestrzeń obszaru roboczego obrabiarki. Podstawową różnicą między barierami i kurtynami świetlnymi jest to, że bariery świetlne emitują tylko kilka, do kilkunastu promieni, zaś kurtyny od kilkunastu do kilkudziesięciu, a nawet kilkuset wiązek światła. Wymagania dotyczące barier i kurtyn świetlnych zawiera norma PN-EN 61496-1:2014-02 – Elektroczułe wyposażenie ochronne; Część 2: Wymagania szczegółowe dotyczące wyposażenia wykorzystującego aktywne optoelektroniczne urządzenia ochronne (AOPD).
Najprościej rzecz ujmując, bariery świetlne wykorzystywane są w charakterze niewidocznego ogrodzenia strefy ryzyka i zazwyczaj używa się ich do nadzorowania niebezpiecznych stref w otoczeniu maszyn, gniazd, czy linii produkcyjnych. Bardzo często montuje się je w pobliżu wejść do zautomatyzowanych przestrzeni magazynowych czy strefy zagrożonych wybuchem. Bardzo dobrze sprawdzają się w miejscach załadunku towarów. W takim przypadku instalowane są bariery z tzw. funkcją mutingu. Funkcja ta pozwala odróżnić przemieszczający się towar od osób, które wtargnęły do strefy ochronnej. Bariery świetlne chroniące daną strefę mają od jednego do kilku promieni. Ich liczba dobierana jest na podstawie potrzeb określonych w ramach analizy ryzyka.
Kurtyny świetlne stosowane są najczęściej do nadzorowania strefy, która bezpośrednio przylega do obszaru roboczego obrabiarki lub zrobotyzowanego gniazda produkcyjnego. Ich zadanie polega na kontroli przekroczenia tej strefy w stosunkowo niewielkim obszarze. W ten sposób wykryć można np. palce bądź dłoń operatora w strefie działania narzędzi – najczęściej tego typu rozwiązania znajdziemy w prasach. Istotną zaletą kurtyn jest to, że można je montować zarówno w pionie, jak i w poziomie. W pierwszym wypadku wykrywają pojawienie się obiektów (np. ręki operatora) w strefie zagrożenia, w drugim zapewniają detekcję w obszarze, gdzie mogą występować stwarzające zagrożenie ruchy maszyny.
Bariery wykonane są w postaci dwóch głównych elementów – nadajnika i odbiornika światła. Najczęściej wykorzystuje się tu równoległe wiązki promieniowania podczerwonego. Wiązki te modulowane są określoną częstotliwością, a odbiornik czuły jest tylko na wiązki wysyłane przez nadajnik, które charakteryzują się ściśle zdefiniowanymi parametrami. Dzięki temu inne źródła podczerwieni, np. fotodetektory IR, nie zakłócają działania bariery.
Dostępne na rynku bariery i kurtyny świetlne różnią się zestawem funkcji i zastosowanymi w nich technologiami. Najważniejszą z nich jest banking. Opcja ta pozwala na wyłączenie żądanych wiązek promieni. Z kolei multiscanning daje możliwość wielokrotnej detekcji wiązki w ściśle określonej jednostce czasu. To również funkcja pozwalająca na wyeliminowanie wpływu zewnętrznych źródeł światła na działanie bariery. Istotnym parametrem jest czas reakcji. Określa on czas od chwili przerwania wiązki do momentu reakcji polegającej np. na zatrzymaniu maszyny. Typowo jest to ok. 2 ms.
Warto też wymienić wspomniany wyżej muting. Funkcja ta pozwala na przejście zdefiniowanego obiektu o znanych wymiarach przez strefę ochronną bez uruchomienia alarmu. Wykrywane są tutaj kolejno: położenie i kierunek ruchu od chwili pojawienia się obiektu w strefie ochronnej, aż do chwili opuszczenia tej strefy. W przypadku kurtyn czy barier wielowiązkowych, istotnym parametrem jest również rozdzielczość, czyli odległość między promieniami świetlnymi. Zwykle jest to 14 mm.
Innym często stosowanym zabezpieczeniem są laserowe skanery bezpieczeństwa. Są to urządzenia optyczne przypominające nieco swoim działaniem kurtynę świetlną, nie wymagają jednak oddzielnej listwy z odbiornikami. Są one bowiem zintegrowane z nadajnikiem. Wiązka laserowa wysłana z emitera przez system lusterek, trafia na wirujące zwierciadło, które rozprowadza ją w określonej strefie. Promienie laserowe odbite od obiektu wracają do odbiornika. Lokalizacja wykrywanego obiektu odbywa się na zasadzie pomiaru czasu powrotu promieni oraz kąta padania wiązki względem odbiornika.
Do podstawowych zadań laserowych skanerów bezpieczeństwa należą: kontrola wejścia w strefę niebezpieczną, kontrola przestrzeni wokół automatycznych wózków transportowych, a także kontrola obecności przedmiotów w określonej strefie. Istotną cechą laserowych skanerów bezpieczeństwa, jest to, że mogą wykryć obecność osoby zbliżającej się do chronionego obszaru. Dzięki temu można w sposób kontrolowany zatrzymać maszynę, a nie wyłączyć ją awaryjnie. Oprócz tego, gdy utrudniona jest obserwacja strefy niebezpiecznej, lasery bezpieczeństwa wykrywają aktualną lokalizację danej osoby i nie dopuszczają do ponownego zainicjowania niebezpiecznego ruchu obrabiarki czy robota przemysłowego – właśnie dlatego laserowe skanery bezpieczeństwa stosuje się do zapewnienia bezpieczeństwa w obszarze zrobotyzowanych gniazd produkcyjnych.
Typowo skanery laserowe pozwalają na obserwację obszaru w szerokim kącie widzenia, dochodzącym do 190–275° i chronią strefę w promieniu 2–6 m. Co ważne w promieniu 10–20 m od skanera można dodatkowo zdefiniować strefę ostrzegawczą. W zależności od urządzenia możliwy jest jednoczesny monitoring kilku, zwykle do 5–7 zdefiniowanych, oddzielnych stref, a także możliwe jest łączenie szeregowe kilku skanerów, co pozwala objąć monitoringiem całą linię produkcyjną a nawet halę fabryczną. Istotną funkcją jest możliwość wyboru rozdzielczości ochronnej dla rąk, nóg lub ciała – są to wartości 30, 50 lub 70 mm.
Dywaniki i maty bezpieczeństwa
Ostatnim elementem dotyczącym bezpieczeństwa maszyn są maty i dywaniki bezpieczeństwa. Tego typu akcesoria wykorzystuje się bezpośrednio przy stanowiskach roboczych, a także w miejscach kontrolnych i przejściach. Ich podstawową zaletą jest prosta konstrukcja, łatwość instalacji oraz możliwość wyraźnego wydzielenia strefy ochronnej. Urządzenia te charakteryzują się praktycznie brakiem jakiejkolwiek reakcji na fałszywe sygnały wywoływane, np. upadkiem drobnych przedmiotów. Mat i dywaników nie należy natomiast stosować tam, gdzie spadać mogą przedmioty większe i ostre.
Zasada działania maty bezpieczeństwa jest wyjątkowo prosta. W macie znajdują się dwie warstwy przewodzące, które oddzielono od siebie separatorami. Wejście pracownika na matę sprawia, że pod jego ciężarem separatory zostają ściśnięte i dwie warstwy przewodzące stykają się ze sobą powodując alarm i zatrzymanie maszyny. Jak można się domyślić, maty i dywaniki różnią się od siebie wielkością obszaru detekcji – dywaniki są dużo mniejsze, jednak w katalogach wszystkie tego typu urządzenia umieszczane są w kategorii mat bez podziału ze względu na ich wielkość.
Istotną zaletą mat jest to, że charakteryzują się pełną zdolnością detekcji na całej swojej powierzchni. Użyte do jej produkcji tworzywo musi charakteryzować się wytrzymałą konstrukcją mechaniczną i odpornością na oleje – zwłaszcza gdy mata chroni obszar roboczy maszyn do obróbki skrawaniem. Najważniejszymi parametrami maty są obszar detekcji oraz ciężar, jaki powoduje ściśnięcie separatorów. Istotna jest też minimalna powierzchnia nacisku, wywołująca zadziałanie maty.
Maty wykorzystuje się jako główny lub dodatkowy system zabezpieczający do natychmiastowego zatrzymania maszyny. Zadaniem mat stosowanych jako wtórne zabezpieczenie jest uniemożliwienie ponownego uruchomienie maszyny, gdy ktoś znajduje się w strefie ryzyka. Bardzo często maty współpracują z kurtynami świetlnymi, które są wówczas głównym zabezpieczeniem, a mata zabezpiecza przed ponownym uruchomieniem urządzenia w sytuacji, gdy pracownik jest wciąż w strefie ryzyka.
Rozwój systemów bezpieczeństwa
Jeśli chodzi o wymagania względem systemów bezpieczeństwa maszyn to produkty z tej kategorii muszą cechować się wysoką jakością i spełniać wymogi aplikacji. Istotnym czynnikiem może być cena, zwłaszcza jeśli ochrony wymaga stosunkowo proste lub tanie urządzenie. Obecnie producenci maszyn i integratorzy systemów automatyki poszukują również nowatorskich rozwiązań z obszaru bezpieczeństwa funkcjonalnego. Dużą uwagę przywiązuje się do technologii sieciowych umożliwiających tworzenie systemów bezpieczeństwa z wykorzystaniem specjalizowanych sieci komunikacyjnych. Chodzi tu przede wszystkim o takie rozwiązania jak Safety over IO-Link, Safety over EtherCAT. Coraz większą popularnością cieszą się też urządzenia bezpieczeństwa RFID.
Te trendy komunikacyjne związane są z popularyzacją rozwiązań Przemysłu 4.0 i Internetu Rzeczy. Chętnie wykorzystuje się do celów diagnostycznych i do celów bezpieczeństwa interfejs IO-Link, ze wspomnianym wariantem protokołu komunikacyjnego Safety over IO-Link. Warto jednak wspomnieć, że tego typu rozwiązania dostępne są obecnie tylko w najbardziej zaawansowanych urządzeniach, takich jak laserowe skanery bezpieczeństwa i programowalne sterowniki bezpieczeństwa. Proste urządzenia bezpieczeństwa, takie jak czujniki, maty, kurtyny i wyłączniki krańcowe, przez kilka najbliższych lat sprzedawane będą raczej w tradycyjnej formie.
Literatura
[1] Dyrektywa 2006/42/WE Parlamentu Europejskiego i Rady z dnia 17 maja 2006 r. w sprawie maszyn, zmieniająca dyrektywę 95/16/WE (przekształcenie) (Dz.U. L 157 z 9.6.2006, str. 24)
[2] Rozporządzenie Ministra Gospodarki z dnia 21 października 2008 r. w sprawie zasadniczych wymagań dla maszyn (Dz.U. 2008 nr 199 poz. 1228)
[3] Materiały firmy Pilz (www.pilz.com)
źródło: Automatyka 1-2/2023
Komentarze
blog comments powered by Disqus