Komputery panelowe i panele operatorskie HMI w przemyśle
Marcin Bieńkowski drukuj
Trudno wyobrazić sobie współczesny system automatyki bez rozwiązań cyfrowych. Najczęściej spotykamy się tu ze sterownikami PLC, jednak coraz częściej popularnością dorównują im przemysłowe systemy IT, w tym komputery przemysłowe. Jednym z rodzajów komputerów przemysłowych są komputery panelowe i przypominające je, ale charakteryzujące się dużo mniejszą funkcjonalnością panele operatorskie.
Komputery przemysłowe, nazywane też komputerami IPC (od Industrial PC) wykorzystywane są do sterowania działaniem maszyn, linii produkcyjnych, zrobotyzowanych gniazd, sterowania liniami produkcyjnymi, gromadzenia danych, przewidywania na podstawie zebranych danych z czujników możliwych awarii, analizy wąskich gardeł i oferowania różnych funkcjonalności dostosowanych (zaprogramowanych) stosownie do aplikacji. Co więcej, wszystkie zebrane i przetworzone przez komputery IPC dane są na bieżąco wysyłane do firmowego systemu IT, w tym aplikacji ERP czy PLM.
Komputery przemysłowe wykorzystuje się też w zastosowaniach biznesowych. Znajdziemy je w kasach fiskalnych, bankomatach, w terminalach POS (Point Of Sales), systemach inteligentnego transportu, w aparaturze medycznej, na lotniskach i dworcach kolejowych, gdzie odpowiadają za wyświetlanie informacji dla podróżnych (tzw. systemy Digital signage) itp. Z drugiej strony rozwój systemów Przemysłu 4.0, Przemysłowy Internet Rzeczy (IIoT) oraz szeroko pojęta cyfryzacja fabryk (tzw. Smart Factories) sprawił, że komputer IPC jest już nieodzownym elementem systemu sterowania procesami produkcyjnymi, logistycznymi i technologicznymi w większości firm. Na początek przyjrzyjmy się, czym różnią się komputery klasy Industrial PC od typowych maszyn, z których korzystamy na co dzień.
Jakie są główne zastosowania HMI? Pomimo dynamicznego rozwoju informatyzacji w przemyśle i coraz częściej pojawiających się komputerów przemysłowych w obszarach produkcyjnych, nadal głównym interfejsem łączącym maszynę z operatorem są panele HMI. Za ich pomocą operatorzy mogą nadzorować produkcję oraz na bieżąco śledzić parametry maszyn. Prosta i wytrzymała budowa paneli HMI oraz możliwość ich szybkiej wymiany w przypadku uszkodzenia sprawiają, że wciąż są to rozwiązania często wykorzystywane, szczególnie w trudnych warunkach przemysłowych. Rosnąca popularność i zapotrzebowanie na analizę parametrów produkcyjnych sprawiają, że interfejsy graficzne wypierają proste rozwiązania z przyciskami i sygnalizatorami. Panele HMI coraz częściej pełnią także funkcje pomocnicze, takie jak rejestracja danych czy obsługa urządzeń peryferyjnych typu drukarki oraz czytniki kodów kreskowych. Na znaczeniu zyskują również takie funkcje, jak zdalne łączenie się z panelem za pomocą serwerów WWW czy VNC, co umożliwia serwisowanie i podgląd stanu maszyny z dowolnego miejsca na ziemi. |
Przemysłowe warunki pracy
Podstawową różnicą między komputerem przemysłowym klasy IPC, a zwykłym pecetem jest odporność na wymagające, spotykane na co dzień warunki pracy w przemyśle. W komputerze przemysłowym nie wystarczy zastosować podzespoły klasy serwerowej czy zadbać o to, aby użyte do jego budowy elektroniczne części spełniały wymagania wojskowej, amerykańskiej normy MIL-STD-810. Maszyna tego typu musi sprostać trudnym, panującym w fabryce lub na linii technologicznej warunkom. Często musi też pracować na dworze pod gołym niebemalbo w środowisku zagrożonym wybuchem (wówczas wymagana jest zgodność z europejską dyrektywą ATEX).
W takich miejscach często występuje zwiększone zapylenie, wilgoć, drgania czy wibracje, które są zabójcze dla standardowych, biurowych komputerów, a nawet serwerów. W nieogrzewanej hali może pojawić się ujemna temperatura, a obok pieca hutniczego czy na walcowni często temperatura otoczenia przekracza +60 °C. Komputer przemysłowy musi być też odporny na zakłócenia elektromagnetyczne oraz skoki napięcia wywołane włączaniem i wyłączaniem obrabiarek czy linii technologicznych. To dlatego komputery IPC są projektowane w zupełnie inny sposób.
Podzespoły
Po pierwsze, do budowy maszyn typu IPC stosuje się znacznie trwalsze podzespoły elektroniczne. Standardem są części, które mogą pracować w temperaturze +110 °C (np. wewnątrz obrabiarki, czy systemu sterującego wielkim piecem), a tam gdzie to wymagane, również takie, które mogą pracować w ujemnej temperaturze sięgającyej –20 °C lub niższej – jest to wymagane np. w kopalniach odkrywkowych czy systemach sterujących przesyłem prądu w energetyce.
Do lutowania komponentów na płytce drukowanej wykorzystuje się też dużo trwalsze luty. Mało tego, aby zwiększyć niezawodność konstruktorzy w maksymalny sposób starają się wyeliminować ruchome części. To dlatego w komputerach przemysłowych nie spotkamy praktycznie wentylatorów – wszędzie, gdzie to możliwe, stosuje się chłodzenie pasywne, jedynie za pomocą radiatorów. Co ciekawe w maszynach IPC często obudowa pełni właśnie funkcję zewnętrznego radiatora, stąd często spotykane jej użebrowanie.
Skoro jesteśmy przy obudowach, to istotnym problemem dla komputera przemysłowego mogą być pył i wilgoć, które po dostaniu się do jego wnętrza mogłyby spowodować zwarcie lub korozję elementów elektronicznych i ich styków na płytce drukowanej. Dlatego na rynku bardzo często spotyka się komputery przemysłowe ze specjalnie wykonanymi gniazdami, a ich obudowa jest wykonana zgodnie ze specyfikacją IP67 lub IP68. W tym miejscu warto też wspomnieć, że w komputerach IPC niemal wcale nie stosuje się tradycyjnych twardych dysków. Zastąpiono je całkowicie odpornymi na wstrząsy napędami SSD, najczęściej w postaci modułów M.2
HMI umożliwia operatorowi ustalanie parametrów pracy obiektów i urządzeń Głównym zadaniem HMI jest komunikowanie się z innymi urządzeniami lub obiektami w celu wizualizowania ich pracy. Jak sama nazwa wskazuje, HMI pośredniczy między człowiekiem a maszyną. Dzięki interfejsowi HMI osoba odpowiedzialna za realizację zadań produkcyjnych może nie tylko obserwować proces, ale też wpływać na jego przebieg i go kontrolować. W uproszczeniu można powiedzieć, że zadaniem HMI jest wizualizacja procesu oraz umożliwienie operatorowi zadawania parametrów pracy obiektów i urządzeń. HMI wykorzystuje się często do obsługi nie tylko jednej maszyny, ale nawet całej linii produkcyjnej, sterowania systemem HVAC lub do kontekstowej wizualizacji drobnych procesów produkcyjnych. Wielu osobom najczęściej z pojęciem HMI kojarzą się w przemyśle panele operatorskie, które dzięki łatwości programowania, wygodzie instalacji i stosunkowo niskich cenach zyskały swoją popularność. W bardzo prostych procesach, często stosuje się urządzenia integrujące sterowniki PLC z interfejsem operatorskim HMI. |
Wibracje – istotny problem
Oddzielną kwestią są wspomniane przed chwilą przy okazji dysków twardych są drgania i wibracje. Mimo że we współczesnych maszynach IPC nie wykorzystuje się praktycznie w ogóle ruchomych elementów, to wstrząsy mogą, mimo wszystko, uszkodzić konstrukcję komputera. Jeśli maszyna IPC zamontowana jest bezpośrednio na obrabiarce lub na linii produkcyjnej, gdzie występują drgania, wykorzystuje się specjalne, beznaprężeniowe luty. Zabezpieczają one elektroniczne podzespoły zamontowane na płytce drukowanej komputera przed możliwością przerwania elektrycznych kontaktów między komponentami a płytką.
Większe części mocowane są dodatkowo z użyciem elastycznych wypełnień tłumiących drgania, a sama płytka drukowana zabezpieczana jest dodatkowo elastyczną pianką. W komputerach przemysłowych standardowo stosuje się różnego rodzaju podkładki pozwalające w elastyczny i trwały sposób przymocować płytkę drukowaną do obudowy, tak aby nie pękła podczas większych wstrząsów.
Zakłócenia elektromagnetyczne i trwałość
Istotnym zadaniem obudowy jest zapewnieniu komputerowi IPC ochrony przed zewnętrznymi zakłóceniami elektromagnetycznymi. Zakłócenia te są najczęściej generowane przez indukcyjne silniki elektryczne, które stosowane są do napędzania obrabiarek. Aby zwiększyć ochronę, stosuje się też ekranowane przewody i gniazda. Standardowo stosowane są zabezpieczenia przeciwzwarciowe, nadprądowe, przepięciowe, przeciw temperaturowe i zabezpieczenia związane z nadmiernym poborem mocy przez urządzenie.
Komputery przemysłowe muszą cechować się też dużą żywotnością, przez co rozumie się, że muszą wytrzymywać co najmniej kilka lat nieprzerwanej pracy. Wynika to z paru powodów, przy czym najważniejszą jest to, że wszelkie zmiany w instalacji przemysłowej wymagają wstrzymania jej pracy, co jest bardzo kosztowne. Ponadto instalacja po zmianach musi ponownie przejść próby rozruchowe, co dodatkowo wydłuża czas przestoju.
Co gorsza, wymiana komputera IPC na nowocześniejszy jego model, o ile nie jest modernizowana cała linia produkcyjna, ze względu na kompatybilność sprzętowo-programową może być problematyczna i zazwyczaj jest nieopłacalna, gdyż nie wnosi niczego istotnego do działania linii czy maszyny. To dlatego producenci komputerów przemysłowych projektują je tak, aby zapewnić im sprawny serwis przez 10–15 lat po ich wprowadzeniu do sprzedaży. Co ciekawe, wciąż dostępne są na rynku starsze rozwiązania, które swoją premierę miały nawet 20 lat temu.
Dobór panelu determinuje jego przeznaczenie Przy doborze panelu należy wziąć pod uwagę kilka kwestii. Są to czynniki takie jak: możliwości integracji, miejsce, w którym panel będzie używany – a więc stopień ochrony obudowy, to czy panel ma być mobilny czy może będzie zamontowany na stałe przy maszynie oraz oczywiście kwestie takie jak cena, a szczególnie w dzisiejszych czasach – dostępność i wsparcie. W zależności od tego, jak i gdzie panel będzie stosowany, firma Beckhoff oferuje przekrój urządzeń od stopnia ochrony IP20 do IP65 oraz serię CPX dla stref zagrożonych wybuchem (strefa 2/22). Niektóre narzędzia do tworzenia wizualizacji – jak na przykład TwinCAT HMI – umożliwiają wyświetlanie jej w przeglądarce internetowej, a co za tym idzie, można wtedy wykorzystać urządzenia przenośne, które są nam doskonale znane z użytku codziennego. Warto również korzystać z urządzeń i oprogramowania, które mają możliwość ewentualnej rozbudowy w przyszłości, bo wymagania dotyczące aplikacji mogą się zmieniać w czasie i nie musi się to wtedy wiązać z zakupem nowego urządzenia. Zyskujące na popularności panele mobilne mogą być stosowane np. w przypadku rozbudowanych linii produkcyjnych, gdzie zastępują kilka paneli. Także w autonomicznych systemach transportu, jak np. wózki AGV, które do komunikacji wykorzystują bezprzewodowe technologie wymiany informacji. Są producenci, którzy oferują panele mobilne przeznaczone ściśle do aplikacji i warunków przemysłowych, ale takim mobilnym panelem, przy doborze odpowiedniej technologii wizualizacji i komunikacji, może być również zwykły tablet czy telefon komórkowy. To rozwiązanie jest coraz bardziej popularne zarówno w przemyśle – w aplikacjach monitorujących wydajność produkcji, jak i w budownictwie – do sterowania automatyką pomieszczeń. Zupełnie inną formą komunikacji człowieka z maszyną mogą być gogle rozszerzonej rzeczywistości, które na przykład wspomagałyby operatora w poszukiwaniu i usuwaniu usterek, pozwalając zobaczyć maszynę w zupełnie innym wymiarze niż obecna, klasyczna dokumentacja. |
Komputery przemysłowe – podział
Zanim przejdziemy do komputerów panelowych, przyjrzyjmy się teraz klasyfikacji maszyn IPC. Najczęściej stosowanym jest podział na komputery kompaktowe, panelowe, jednopłytkowe oraz maszyny IPC Box, określane też mianem Box PC. W systemach automatyki przemysłowej najczęściej wykorzystuje się tzw. komputery jednopłytkowe znane również pod nazwą komputerów SBC (Single Board Computer).
Komputery SBC przeznaczone są przede wszystkim do montażu w większych systemach automatyki przemysłowej, które są projektowane bezpośrednio przez nabywcę lub przez integratora systemu. Komputer taki to po prostu niewielka, nieobudowana płytka drukowana z zainstalowanymi na niej wszystkimi niezbędnymi do pracy elementami. Znajdziemy tam wlutowany procesor, kartę graficzną i pamięć oraz wszystkie komponenty, które są niezbędne dla danej aplikacji.
Istotne jest to, że wszystkie złącza mogą być albo wlutowane przy krawędziach płytki, albo sygnały wyprowadzane są przez specjalne piny. Do tego typu pinowych złączy podłącza się odpowiednie wtyczki, co ułatwia montaż w docelowym urządzeniu. Dzięki temu, że komputery SBC są sprzedawane w postaci płytki drukowanej, obudowę oraz sposób montażu nabywca lub integrator dobiera sobie sam we własnym zakresie, w zależności od wymagań aplikacji. Na rynku istnieje kilka standardów formatu komputerów SBC, z których najpopularniejszymi są m.in. PC-104, EBX, EPIC, Nano-ITX, Pico-ITX oraz Femto-ITX. Komputery SBC sprzedawane są również w wersjach fabrycznie zamontowanych w obudowach. Najczęściej spotkać się można z komputerami przystosowanymi do montażu na szynie DIN, która wykorzystywana jest w wielu rozwiązaniach systemów automatyki przemysłowej.
Komputery Box PC i komputery kompaktowe
Druga grupa komputerów przemysłowych to komputery klasy Box PC. Są to w pełni funkcjonalne komputery klasy PC o niewielkich wymiarach i, co najważniejsze, dostosowane do pracy w warunkach przemysłowych. Najczęściej tego typu maszyny spotyka się w aluminiowych obudowach z użebrowaniem, które służy jako zewnętrzny radiator odprowadzający ciepło, o czym już wspomniano. Oczywiście systemy Box PC sprzedawane są też w obudowach dostosowanych do montażu na szynie DIN, a nawet w standardowych serwerowych 19-calowych obudowach typu rack. W tych ostatnich montowane są również pojawiające się ostatnio na rynku systemy klasy Edge Computing. Dzięki obudowie typu rack, komputer przemysłowy może być bez problemu zamontowany w zwykłej szafie serwerowej, co pozwala znacząco obniżyć koszty infrastruktury systemu automatyki.
Ostatnią grupą są komputery kompaktowe. Ujmując w skrócie, jest to w pełni funkcjonalny, niewielki pod względem wymiarów sprzęt przeznaczony do montażu tam, gdzie występuje bardzo mocno ograniczona przestrzeń – np. w systemie zrobotyzowanym, czy wewnątrz obrabiarki. Cechą charakterystyczną komputerów kompaktowych jest całkowicie pasywne chłodzenie, aluminiowa , zawsze użebrowana obudowa oraz bardzo wysoka odporność na wibracje. Komputery te korzystają najczęściej z energooszczędnych procesorów ARM. Bardzo rzadko można w nich znaleźć układy z rodziny Intel Core.
Komputery panelowe i panele operatorskie HMI
Przejdźmy do komputerów panelowych (panel PC) i systemów HMI (Human-Machine Interface). Ich cechą charakterystyczną jest zintegrowany, najczęściej dotykowy ekran. Dzięki temu, podobnie jak znane z biur komputery All-in-One, łączą one w sobie funkcjonalność komputera i monitora. Systemy tego typu wykorzystywane są przede wszystkim jako terminale operatorskie lub stanowiskowe stacje robocze. Komputery panelowe oraz panele operatorskie HMI przymocowuje się najczęściej do maszyn i obrabiarek, wbudowuje w pulpity bądź szafy sterownicze, mocuje na ścianie lub, w zależności od wersji, nad- lub podtynkowo, np. w salach konferencyjnych i systemach inteligentnych budynków.
Tu ważna uwaga, w większości dostępnych katalogów nie rozróżnia się paneli operatorskich HMI i komputerów panelowych. Tymczasem obie klasy urządzeń dość mocno się różnią od siebie. Panel operatorski HMI to stosunkowo prosty sterownik przemysłowy, wyposażony w wyświetlacz i przyciski. Jego zadaniem jest wizualizacja pracy maszyn, linii produkcyjnej czy obiektów przemysłowych i systemów automatyki budynków, do których jest bezpośrednio podłączony.
Co więcej, podobnie jak sterowniki PLC, panele operatorskie mają wbudowany szereg, często specjalizowanych wejść i wyjść – cyfrowych i analogowych. Do panelu HMI wgrywane jest specjalne dedykowane dla danego modelu i aplikacji oprogramowanie wizualizacyjne. Innymi słowy, panel operatorski służy do wizualizacji oraz do zadawania parametrów pracy podłączonych do niego urządzeń, linii czy systemów automatyki budynkowej. Niekiedy dodatkową funkcją jest możliwość udostępnia przez panel informacji procesowe do nadrzędnych systemów IT. Innymi słowy, panel operatorski to sterownik PLC z ekranem.
Komputer panelowy to pełnoprawny komputer klasy Box PC zintegrowany z ekranem. Bez problemu poradzą sobie z uruchamianiem dowolnego oprogramowania, w tym stosowanych do sterowania produkcją aplikacji SCADA. Mogą też posłużyć do wizualizacji procesu, alarmowania i wysyłania komunikatów o stanie procesu, gromadzenia danych z linii produkcyjnej i ich archiwizowania. Bez problemu można na nich wykonywać różnorodne analizy, w tym analizy z wykorzystaniem algorytmów sztucznej inteligencji i Big Data. Tego typu komputery panelowe nazywa się systemami Edge Computing. Mają one wystarczająco dużą moc obliczeniową, często wyposażone są też w akceleratory grafiki. Wykorzystuje się je do analizy danych bezpośrednio na linii produkcyjnej, w tym przy wykorzystaniu wspomnianej sztucznej inteligencji i uczenia maszynowego.
Oczywiście komputery panelowe, podobnie jak wszystkie systemy IPC, stosowane są też do uruchamiania dedykowanych aplikacji wspierających proces produkcji i jej wizualizacji. Komputer panelowy wyposażony w odpowiednią kartę graficzną, umożliwia nie tylko podgląd działania procesu i sterowanie nim, ale również jego wizualizację w 3D. Komputer panelowy bez problemu może też gromadzić dane z całego procesu produkcyjnego, komunikuje się ze sterownikami PLC, panelami operatorskimi HMI, wbudowanymi w obrabiarki a także czujnikami, w tym z systemami Przemysłowego Internetu Rzeczy IIoT.
Nowe technologie a rozwój rynku paneli Klienci przyzwyczajeni do atrakcyjnych stron internetowych i aplikacji w smartfonie chcieliby, aby ich wizualizacje przemysłowe wyglądały równie nowocześnie i i były tak samo funkcjonalne. Stąd duże zainteresowanie technologiami webowymi i szklanymi panelami z technologią multitouch. Zauważam również większe zainteresowanie zabudowanymi panelami do montażu na ramieniu takimi jak np. B&R AP5000, wyposażonymi w dodatkowe przyciski czy czytnik RFID. Rosnące koszty pracowników sprawiają, że coraz częściej opłaca się kupić gotowy, zabudowany panel niż konstruować szafkę elektryczną ręcznie montując wyświetlacz, przyciski i inne oprzyrządowanie. Jako urządzenia dodatkowe sprawdzają się panele mobilne. Smartfony są coraz częściej używane do zdalnego monitorowania linii produkcyjnych. Większe tablety pomagają natomiast podczas prac nastawczych i serwisowych, dzięki czemu operatorzy i serwisanci nie są przywiązani do jednego punktu linii produkcyjnej, ale mogą sprawdzać funkcjonalność poruszając się z tabletem wzdłuż kolejnych stacji procesowych. Wszystkie nowe rozwiązania stały się możliwe dzięki zastosowaniu technologii webowych takich jak B&R mapp View, które pozwalają na uruchomienie wizualizacji przemysłowej na dowolnym urządzeniu z przeglądarką internetową. Zakup powinny rozważyć firmy, w których występują częste przezbrojenia linii produkcyjnych, ponieważ panele mobilne pomagają sprawniej przeprowadzać i monitorować zmiany. |
Konstrukcja panelu dotykowego
Jak można się domyślić, podstawowym interfejsem użytkownika, zarówno w komputerach panelowych, jak i panelach operatorskich HMI jest ekran dotykowy. Spotkać się tu można z czterema rozwiązaniami, spośród których można wybrać taki typ panelu dotykowego, który najlepiej dopasowany jest do potrzeb aplikacji lub specyfiki obsługi urządzenia. Dwa podstawowe bardzo dobrze znane są z urządzeń mobilnych – są to ekrany dotykowe rezystancyjne i pojemnościowe.
W ekranach rezystancyjnych nałożona na wyświetlacz powierzchnia czuła na dotyk, zbudowana jest z dwóch plastikowych płytek. Płytka wierzchnia wykonana jest z cienkiego i odpornego na zadrapania polimeru i pokryta umieszczoną „od spodu” cienką warstwą materiału przewodzącego prąd elektryczny (tlenek cyny i tlenek indu). Pod górną płytką, poniżej materiału przewodzącego, znajduje się druga plastikowa płytka. Obydwie płytki nie mają ze sobą kontaktu aż do momentu, gdy użytkownik nie wciśnie ekranu palcem lub rysikiem. Następuje wówczas kontakt pomiędzy oddalonymi od siebie nieznacznie powierzchniami. W wyniku ich zetknięcia powstaje zwarcie, które dzięki zmierzeniu oporów pionowego i poziomego zamieniane jest na dane wskazujące procesorowi odpowiedzialnemu za obsługę ekranu miejsce styku.
Ekran rezystancyjny zapewnia punktową, precyzyjną czułość miejsca wskazania i dobrą widoczność, która spada jednak mocnym słońcu. Można go obsługiwać za pomocą każdego materiału, nie tylko palcem. Charakteryzuje się krótkim czasem reakcji i niskimi kosztami produkcji. Co ważne, problemów nie sprawia nawet obsługa lekko zmoczonego czy zabrudzonego wyświetlacza. Podstawową wadą jest tu brak wielodotyku. Ekrany te wymagają też dość mocnego wciśnięcia danego punktu w celu wykrycia dotyku.
Ekran pojemnościowy składa się najczęściej ze szklanej szybki pokrytej specjalną warstwą przewodzącą. W tej roli wykorzystywany jest zazwyczaj tlenek indowo-cynowy, który charakteryzuje się dużą przepuszczalnością światła i bardzo dobrym przewodnictwem. Dotknięcie powierzchni płytki palcem lub wskaźnikiem przewodzącym prąd powoduje zmiany pojemności elektrostatycznej znajdujących się w danym miejscu elektrod. Dzięki temu punkt styku palca z wyświetlaczem może być bardzo dokładnie określony. Zresztą nie tylko jeden. Urządzenie potrafi bowiem określić ich kilka lub nawet kilkanaście, dzięki czemu można skorzystać z zalet wielodotyku. Ekran taki znakomicie wykrywa nawet drobne muśnięcia czy przesunięcia palcem po wyświetlaczu. Co ważne, przepuszcza dużo światła i można go pokryć warstwą ochronną, co zwiększa jego żywotność i pozwala korzystać z niego w pełnym słońcu, Wadą jest dużo wyższy koszt produkcji, utrudniona obsługa w przypadku zabrudzeń i to, że obsługiwać go można palcem lub specjalnym materiałem.
Innymi typami ekranów stosowanych w przemysłowych komputerach panelowych i panelach operatorskich HMI są wyświetlacze z ekranami dotykowymi na podczerwień (nazywanymi też czasem, niezbyt poprawnie, optycznymi) i ultradźwiękowymi, nazywanymi też ekranami dotykowymi typu SAW (Surface Acoustic Wave). Co ciekawe, oba pozwalają na swobodne sterowanie urządzeniem, nawet w sytuacji kiedy pracownik ma ubrane grube rękawice ochronne. Tego typu ekrany działają również w zupełnie inny sposób. Nie wymagają pokrywania wyświetlacza żadną specjalną warstwą.
Na dwóch krawędziach takiego ekranu zamontowane są listwy z diodami LED emitujące podczerwone światło, a na przeciwnych listwy z detektorami czułymi na podczerwień. W przypadku ekranów SAW montuje się emitery i odbiorniki ultradźwięków. W wypadku ekranów IR emitowane wiązki tworzą siatkę świetlną, która jest wykrywana przez czujniki umieszczone na przeciwległych krawędziach. Przytknięcie jakiegoś materiału, np. palca, do wyświetlacza zaburza przesyłanie promieni podczerwonych w danym miejscu, co pozwala na dokładne określenie punktu dotyku. Ekrany optyczne obsługują wielodotyk i umożliwiają obsługę praktycznie dowolnym przedmiotem. Ich podstawowa wada to podatność na zakłócenia wynikające z bardzo silnego światła czy zapylenia pomieszczenia. Poza tym czujniki umieszczone są w ramce okalającej wyświetlacz, co wpływa na zwiększenie gabarytów wyświetlacza.
Podobnie działają ekrany SAW, jednak muszą być dodatkowo zaopatrzone w szybę, po powierzchni której rozpraszane będą fale ultradźwiękowe. Podobnie jak w przypadku ekranów dotykowych IR, fale te tworzą siatkę. Miękkie przedmioty takie jak palec czy gumka ołówkowa w momencie dotknięcia ekranu pochłaniają część fal tworząc tzw. „cień ultradźwiękowy”. Cień wykrywany jest przez receptory na brzegach ekranu, a następnie przetwarzany przez kontroler ekranu na współrzędne miejsca dotyku.
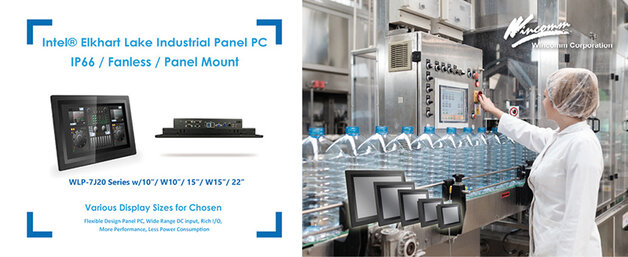
Komputery panelowe są również dostępne w obudowach zabezpieczających je przed wilgocią. Na zdjęciu komputer WLP-7J20 firmy Wincomm Corporation w obudowie IP66
Budowa komputerów panelowych
Jak już wspomniano, pod względem funkcjonalności komputery panelowe przypominają zwykłe komputery typu All-in-One. Asortyment przekątnych ekranu jest tu bardzo szeroki. Znaleźć można m.in. niewielkie dotykowe ekrany LCD o przekątnej 4,5–5,5 cala, jak również wyświetlacze, których przekątna osiąga nawet 64 i więcej cali. Jednak typowy ekran w komputerze panelowym ma wielkość od 5,5 do 13–15 cali. Jeśli chodzi o rozdzielczość to jest to zwykle 720 px lub 1080 px. Coraz częściej w komputerach z większymi panelami, rzędu 28–32 cali pojawiają się ekrany o większych rozdzielczości, gdzie spotkać się można nawet z rozwiązaniami 4K, a nawet w tych największych 8K. Co ciekawe, dość trudno spotkać komputery panelowe z ekranem panoramicznym o proporcjach ekranu 16:9 – jeśli już to najczęściej są to maszyny z grupy Digital Signage wykorzystywane do prezentacji treści multimedialnych, np. na lotniskach.
Zależnie od wymagań aplikacji, nośnikiem danych w komputerze panelowym jest karta Flash z systemem operacyjnym albo wbudowany napęd SSD M.2 (czasami kilka). W maszynach tych bez problemu zamontować można karty rozszerzeń za pomocą wykorzystania złączy PCI Express x1 lub x4, a niekiedy nawet x16 (karta graficzna). Obecnie komputery panelowe wyposażone są najczęściej w energooszczędne wersje procesorów Intel Core i3, i5 oraz i7 i AMD Ryzen. Często można spotkać procesory ARM. Typowo montuje się w nich 8–64 GB pamięci RAM, choć zdarzają się również modele wyposażone nawet w 512 GB pamięci operacyjnej. Bywają też maszyny wykorzystujące w niezwykle silne karty graficzne pozwalającą na rendering grafiki 3D w czasie rzeczywistym. We wszystkich tego typu komputerach panelowych można bez problemu rozbudować pamięć RAM, zwykle za pomocą modułów SO-DIMM. Zapowiadane są też maszyny wykorzystujące najnowsze pamięci DDR5, póki co, nie ma ich jeszcze w polskich sklepach.
Jeśli chodzi o sygnał wideo, to standardem są wyjścia HDMI i mini DisplayPort. Obowiązkowe są też porty COM (ze względu na kompatybilność ze starszymi systemami automatyki przemysłowej), złącza USB, w tym USB 3.2 Gen 2x2, Thunderbolt 3 i 4 oraz dwa, trzy porty LAN, a także moduł Wi-Fi, w tym w najnowszym standardzie Wi-Fi 6E. Wiele modeli komputerów panelowych może być zasilanych w trybie AT, czyli komputer uruchamia się natychmiast po włączeniu zasilania. Typowo komputery te pozwalają na pracę w temperaturach od –20 °C do +75 °C. Dzięki temu mogą być stosowane na otwartym powietrzu, np. w energetyce, górnictwie odkrywkowym, cukrowniach, elewatorach czy w przemyśle cementowym.
Jakimi czynnikami kierują się klienci w wyborze paneli operatorskich? Rynek automatyki wymusza stały rozwój w zakresie rozwiązań nowoczesnych systemów sterowania, kontroli procesów produkcyjnych i wizualizacji. Jednym z podstawowych czynników, którymi kierują się klienci w wyborze paneli HMI, jest możliwość obsłużenia tych elementów przez panel operatorski. Im większa liczba dostępnych gotowych sterowników do urządzeń automatyki, tym większa jest uniwersalność panelu HMI. Innym ważnym czynnikiem jest funkcjonalność panelu HMI. Klienci wymagają od panelu operatorskiego tworzenia trendów, receptur, skryptów, poziomów dostępów dla poszczególnych użytkowników oraz możliwości kompilacji i zapisu danych historycznych na zewnętrznych nośnikach pamięci. Do tego dochodzą rozwiązania, które zwiększają wygodę użytkownika. Możemy do nich zaliczyć rozwój możliwości sprzętowych panelu HMI (rozdzielczości, liczby kolorów, prędkości procesora), jak również możliwość obsługi przez urządzenia peryferyjne, takie jak smartfon, tablet czy komputer PC, a także usługę zdalnego dostępu. Ostatnim ważnym czynnikiem przy doborze panelu HMI jest cena urządzenia. Ciekawym produktem wydają się także panele “w chmurze” (są to urządzenia HMI, które nie mają własnego wyświetlacza, a urządzeniem wyświetlającym może stać się dowolne urządzenie mobilne). Wśród coraz częściej wymienianych funkcjonalności są także możliwości obsługi, różnego rodzaju baz danych, jak również integracji wyświetlacza z zaimplementowanymi już systemami automatyki (np. typu SCADA). |
Tablet zamiast panelu
Coraz więcej maszyn i urządzeń wyposażonych jest w moduły łączności bezprzewodowej Wi-Fi. Dzięki temu producenci zaczęli myśleć nad dość nowatorskim rozwiązaniem, jakim jest zastosowanie tabletu klasy przemysłowej zamiast panelu operatorskiego. Co to daje? Oszczędności. Jeden tablet można bowiem wykorzystać do zarządzania kilkoma maszynami.
Przykładowo taki tablet może być standardowo doczepiony i przypisany do jednej obrabiarki. Maszyna, która nie wymaga zaś częstych interwencji obsługi może być pozbawiona własnego wyświetlacza i doraźnie można posłużyć się tym samym, jednym tabletem. Czy takie rozwiązanie ma sens? Raczej tak, oprócz obniżenia kosztów zmniejsza się też liczba elementów, które trzeba serwisować w ramach obowiązków służb utrzymania ruchu.
źródło: Automatyka 11/2022
Komentarze
blog comments powered by Disqus