Oprogramowanie przemysłowe i cyfryzacja
Marcin Bieńkowski drukuj
Cyfryzacja ogarnęła praktycznie każdą dziedzinę życia. Trudno wyobrazić sobie obecnie życie bez smartfona, braku nawigacji satelitarnej, czy nieobecności systemów infotainment w samochodach lub w domu. Bez komputerów i laptopów również nie istniałoby współczesne społeczeństwo. Nic dziwnego, że cyfryzacja obejmuje też przemysł, logistykę, łańcuchy dostaw i systemy sterowania procesami produkcyjnymi.
Na początku należy wyjaśnić kilka dość istotnych kwestii. Zacznijmy od tego, co kryje się pod pojęciem cyfryzacja (digitalization) oraz nagminnie z nim mylonym słowem digitalizacja (digitization). Digitalizacja to po prostu proces tworzenia cyfrowej wersji analogowej informacji. Najprostszym przykładem jest tu skanowanie papierowych dokumentów. Dzięki temu, informacja, która pierwotnie miała postać analogową (fizyczną) może być przetwarzana, przechowywana, wykorzystywana i udostępniana przez systemy komputerowe. Przykładem digitalizacji może być też zastąpienie analogowych rysunków technicznych ich cyfrowymi odpowiednikami w oprogramowaniu CAD. Innymi słowy digitalizacja to proces „przeróbki” zasobu analogowego na cyfrowy, wraz z przygotowaniem, formatowaniem, przypisywaniem tagów czy meta danych oraz udostępnieniem tego zasobu w postaci cyfrowej.
Pojęcie cyfryzacji jest pojęciem dużo szerszym. Obejmuje ono przede wszystkim zastąpienie procesów, podkreślmy jeszcze raz, PROCESÓW analogowych ich cyfrowymi odpowiednikami. W odniesieniu do naszego przykładu, zastąpienie deski kreślarskiej oprogramowaniem CAD i przygotowywanie na komputerze rysunków technicznych, planów czy dokumentacji technologicznej jest cyfryzacją procesu projektowania. Podobnie cyfrowy obieg dokumentów jest cyfryzacją analogowego obiegu papierowych dokumentów, a wymieniony wyżej proces skanowania będzie tu jego częścią. Oznacza to, że digitalizacja, jako proces mający na celu stworzenie cyfrowych kopii analogowych źródeł, jest elementem cyfryzacji.
Kolejnym określeniem, które należy wyjaśnić, to technologie cyfrowe. Pod pojęciem tym kryją się wszelkie techniki cyfrowe i systemy informatyczne, w tym sprzęt i oprogramowanie, które pozwalają w cyfrowy sposób przetwarzać i składować różnego rodzaju dane. Mogą to być dane o naturze technicznej, ekonomicznej czy organizacyjnej. Na ich podstawie można następnie podejmować decyzje dotyczące sterowania produkcją, procesami czy zamówieniami. Szeroko pojętą technologią cyfrową jest zarówno fotografia cyfrowa, tworzenie stron WWW i dokumentów w Wordzie, poczta elektroniczna, cyfrowy przepływ dokumentów , Internet, tomografia komputerowa, a także systemy Business Inteligence, ERP, sterowniki PLC czy systemy SCADA.
Skoro powiedzieliśmy już sobie, czym jest digitalizacja i cyfryzacja oraz to czym są technologie cyfrowe, odpowiedzmy również na pytanie, czym jest w takim razie cyfrowa transformacja. Otóż cyfrową transformację definiuje się jako integrację technologii cyfrowej ze wszystkimi obszarami funkcjonowania przedsiębiorstwa. Dzięki niej możliwe jest wykorzystanie gromadzonych przez firmę danych do tworzenia innowacyjnych usług i produktów oraz poszerzenia dotychczasowej oferty i zmiany technologii produkcji wpływających na jakość i zadowolenie klienta.
W zakres cyfrowej transformacji wchodzą działania związane z modyfikacją procesów biznesowych i organizacyjnych oraz procesów produkcyjno-logistycznych, w tym cyfryzacja produkcji, czyli wprowadzanie cyfrowych technologii do procesów produkcyjnych. Celem cyfrowej transformacji jest pełne wykorzystanie możliwości, jakie niosą ze sobą nowoczesne, cyfrowe rozwiązania technologiczne. Z definicji cyfrowa transformacja, zwłaszcza cyfrowa transformacja produkcji zakłada zastosowanie rozwiązań z zakresu Przemysłu 4.0, Internetu Rzeczy i sztucznej inteligencji. Cyfrowa transformacja może przebiegać zupełnie inaczej w każdej firmie.
Firmy w obliczu cyfrowej rewolucji
Proces cyfrowej transformacji zmienił wiele branż. Jedną z najbardziej imponujących była cyfryzacja bankowości, gdzie banki z instytucji zatrudniających tysiące ludzi i mających setki oddziałów, przekształciły się w firmy, w których o sukcesie decydują cyfrowe usługi i aplikacje i funkcjonalność aplikacji na smartfony. Wysiłek transformacji podjęła też szeroko rozumiana branża przemysłowa. Jeszcze przed pandemią, która przyspieszyła procesy cyfryzacji, w 2017 r. według badania IDC European DX Practice Survey, aż 67 % podmiotów podjęło formalne kroki w kierunku transformacji cyfrowej.
Według tego badania widać, że w dalszym ciągu transformacja cyfrowa jest czymś stosunkowo nowym dla firm produkcyjnych w Europie Zachodniej. Aż 31 % z nich przyznało, że traktuje transformację cyfrową jako biznesowy priorytet dopiero od niedawna. Z drugiej strony 22 % respondentów przyznało, że ten temat jest ważny dla ich biznesu już od dłuższego czasu. W tej drugiej grupie znalazły się wielkie, międzynarodowe koncerny, od lat wykorzystujące technologie IT w produkcji i oferujące mocno ucyfrowione produkty.
Firmy, do adaptacji coraz nowocześniejszych cyfrowych technologii i do wkroczenia na drogę cyfrowej transformacji są zwykle przymuszane przez zewnętrze warunki biznesowe. Chodzi tu przede wszystkim o utrzymanie lub poprawienie swojej rynkowej pozycji względem konkurencyjnych firm i zdobycie nowych klientów. Dla wielu producentów jest to wręcz kwestia przetrwania. Co więcej, transformacja cyfrowa jest kierunkiem, który może istotnie zwiększyć potencjał przedsiębiorstwa. Nie jest zaś, i co należy podkreślić, nie powinna być celem samym w sobie, ale obecnie najlepszym sposobem na budowanie konkurencyjnej przewagi. Głównym czynnikiem, który skłania firmy do przeprowadzenia cyfrowej transformacji są rosnące oczekiwania klientów odnośnie ceny i jakości produktów lub usług oraz jakości obsługi sprzedaży i serwisu posprzedażowego.
Cyfrowa transformacja jest procesem, który zakłada stałą gotowość do zmian. Dzięki niej firma nie musi zatrzymywać się w miejscu, tracąc klientów, ale poradzi sobie z każdym problemem czy nową sytuacją na rynku. Moment, w którym dany rynek, producent lub biznes będzie gotowy na wdrożenie cyfrowych innowacji zależy od jego specyfiki i aktualnego zaawansowania technologicznego, zarówno firmy, jak i rynku – np. tablety były obecne na rynku od początku lat 90. XX wieku, ale dopiero od chwili pojawienia się iPada w 2010 r., rynek był w stanie masowo wchłonąć nową technologię. Podobnie w przypadku obszaru działań, który obejmie transformację cyfrowę – jest on zależny od potrzeb organizacji i czasu, kiedy do niej dojrzeje. Cyfrowa transformacja może więc objąć zarówno wprowadzenie mało skomplikowanych systemów IT, jak i wdrożenie rozwiązań z obszaru chmury, sztucznej inteligencji, wideokonferencji, pracy zdalnej czy uczenia maszynowego.
Jakie są największe korzyści z digitalizacji procesów przemysłowych, co firmy mogą dzięki nim zyskać? Digitalizacja jest jednym z filarów Przemysłu 4.0. Coraz więcej przedsiębiorstw decyduje się na wdrożenie w swoich zakładach rozwiązań cyfrowych z uwagi na szereg korzyści. Analizując różne gałęzie przemysłu, możemy zaobserwować podobne tendencje rynkowe niezależnie od branży. Firmy stawiają duży nacisk na poprawę jakości, optymalizację procesów, zarządzanie zapasami oraz możliwość szybszej reakcji na zmiany rynkowe. Cyfryzacja jest odpowiedzią na takie zapotrzebowanie. Nowoczesne systemy do zarządzania produkcją umożliwiają obserwację procesów w czasie rzeczywistym, co z kolei daje możliwość natychmiastowej reakcji na wszelkie nieprawidłowości. Użytkownik na bieżąco ma dostęp do informacji o kondycji urządzeń, różnych parametrach jakościowych oraz stanach magazynowych niezbędnych surowców, co pozwala zoptymalizować pewne operacje, a także w szybki sposób dostosować się do zmian. W wielu wypadkach zdalny dostęp pozwala do minimum ograniczyć potrzebę wizyty bezpośrednio na instalacji lub przygotować się do operacji konserwacyjnych z wyprzedzeniem, a zatem wdrożyć zarządzanie predykcyjne. Tym, co buduje aktualnie przewagę konkurencyjną firm, są elastyczność oraz szybkość reagowania oraz adaptowania się w zmiennych warunkach. Zakłady przemysłowe dysponujące zdalnym dostępem i wykorzystujące technologie cyfrowe są zdecydowanie bardziej konkurencyjne. |
Oblicza cyfryzacji
Jak wynika z raportu firmy Autodesk „Digitalizacja polskich firm przemysłowych w dobie pandemii” (źródło), w porównaniu z 2019 r., aż o 42 % wzrosła świadomość dotycząca rozwiązań Przemysłu 4.0, a 56 % firm utrzymało lub zwiększyło swoje inwestycje w cyfryzację. Jeśli chodzi o największe korzyści wynikające z cyfrowej transformacji, to większość ankietowanych zwróciła uwagę na poprawę ogólnej efektywności procesów (90,3 %) oraz optymalizację działania fabryki (88 %). Wprowadzenie rozwiązań Przemysłu 4.0 przełożyło się również na poprawę wydajności pracy (83,4 %), jakości (81,7 %), a także na poprawę wydajności łańcucha dostaw (81,1 %) oraz czasu wprowadzania produktu na rynek (81,1 %).
Wdrażanie cyfrowych rozwiązań w przemyśle jest naturalną konsekwencją zmiany zachowań społecznych. Jak wynika z raportu firm We Are Social i Hootsuite „Digital 2021” (źródło), aż 66,6 % światowej populacji korzysta obecnie z telefonów komórkowych. Z Internetu korzysta zaś 59,5 % ludności świata. Internauta spędza zaś w Internecie średnio 2,5 godziny. W Polsce z dostępu do sieci korzysta 84,5 % populacji, a ludzie spędzają tam średnio cztery godziny dziennie. Warto podkreślić, że w styczniu 2021 r. w Polsce było 25,90 mln użytkowników mediów społecznościowych, co stanowi 68,5 % ogółu populacji. Jeśli chodzi o aktywność komercyjną, to wyszukiwanie produktów lub usług on-line dotyczyło 81,5 % internautów. Jakąkolwiek firmową stronę WWW odwiedziło 90,4 % osób, a zakupów on-line dokonało 76,8 % respondentów badań.
Uwaga na pułapki
Niestety transformacja cyfrowa dla większości firm produkcyjnych pozostaje hasłem bez treści. Owszem wdrażają pojedyncze, cyfrowe technologie, automatyzują produkcję, ale tylko niewielka część przedsiębiorstw czerpie zyski z potencjału, jaki daje efektywne wykorzystanie danych, począwszy od zamówienia, przez poszczególne etapy produkcji, dystrybucję, sprzedaży i serwis posprzedażowy. Co gorsza, obecny, pandemiczny kryzys sprawia, że nowe technologie nie hamują wcale spadku wydajności. Tylko w Stanach Zjednoczonych wydajność spadła z 2,8 % do 1,3 %, a realne przychody uległy stagnacji.
Mimo to świadomość konieczności wprowadzenia cyfrowych zmian rośnie. Wzrost poziomu cyfryzacji w polskich firmach jest już namacalnym skutkiem ograniczeń, które zostały nałożone na gospodarkę ze względu na pandemię COVID-19. Wiele polskich przedsiębiorstw stanęło przed wyborem, albo dokona przyspieszonej cyfryzacji procesów albo musi się liczyć z koniecznością zawieszenia niektórych operacji biznesowo-produkcyjnych. Kluczowymi obszarami, które trzeba wziąć pod uwagę, rozważając plan cyfrowej transformacji przedsiębiorstwa, są; klienci, konkurencja, dane, innowacyjność oraz kreowana wartość. Przeanalizowanie aktualnego stanu i nakreślenie własnej przewagi w wymienionych zakresach to podstawa sukcesu.
W cyfrowym świecie należy bezwzględnie pamiętać o tym, że klienci tworzą sieci wpływu oraz mają możliwość dynamicznego reagowania i komunikacji z marką. Klient nie jest już tylko interesariuszem, któremu oferowana jest wartość, ale jest także partnerem. Cyfrowe technologie pozwalają mu uczestniczyć w tworzeniu produktu już na etapie prac badawczo-rozwojowych, a w fazie użytkowania czynnie może wpływać na opinie innych klientów, na przykład za pomocą mediów społecznościowych. Może on zatem udoskonalać produkt, ale też aktywnie wpływać na reputację marki i budować lub niszczyć ją.
Kluczem do cyfrowej transformacji są dane. Dzięki odpowiedniej analizie i ich wykorzystaniu można podejmować odpowiednie działania na wszystkich szczeblach i we wszystkich procesach w firmie. Cyfryzacja generuje coraz większe ilości danych, dlatego istotne jest, aby efektywnie z nich korzystać. W dobie cyfryzacji dane napędzają i inicjują procesy w różnych działach firmy. W tym aspekcie konieczne jest odpowiednie oprogramowanie scalające źródła danych w przedsiębiorstwie. W wypadku produkcji są to narzędzia klasy SCADA, PLM czy CMMS, o których za chwilę.
Z pomocą przychodzą również algorytmy sztucznej inteligencji oraz analiza Big Data. Pozwalają one przewidywać pewne trendy rynkowe z wyprzedzeniem, a także znacznie lepiej kontrolować produkcję i łańcuchy dostaw. Ważne jest też zapewnienie danym odpowiedniej ochrony i bezpieczeństwa. Brak bezpieczeństwa, jest jednym z najważniejszych zagrożeń dotyczących cyfrowej transformacji, dlatego musi być jednym z priorytetów realizowanych zmian.
Jak widać, proces cyfrowej transformacji przedsiębiorstwa nie powinien obejmować jedynie warstwy produkcyjno-produktowe, ale wszystkie procesy biznesowe. W celu pełnego wykorzystania cyfrowego potencjału, firmy muszą przeanalizować swoją strategię i na tej podstawie podjąć decyzję, jak ma wyglądać ich nowy model operacyjny oraz w jaki sposób przeorganizować swoje struktury i procesy. Oznacza to, że strategia cyfrowego rozwoju musi wynikać ze strategii biznesu oraz z koncepcji realizacji procesów wewnętrznych przedsiębiorstwa i interakcji z rynkiem. I tu dochodzimy do koncepcji Przemysłu 4.0. W tym miejscu warto podkreślić, że koncepcja Przemysłu 4.0 pozwala wykorzystać zachodzące od lat w przemyśle procesy cyfrowej transformacji, a w szczególności procesy cyfrowej automatyzacji, które pozwalają na przekształcenie fabryk w samosterujące i, co ważne, samoadaptujące i samoorganizujące systemy nazywane często inteligentnymi, bądź cyfrowymi fabrykami (smart factories, digital factories).
W przemyśle cyfryzacja procesów produkcyjnych dotyczy przede wszystkim pionowych i poziomych procesów wytwórczych, które odpowiadają za tworzenie finalnego produktu. Chodzi tu o tak zwane pionowe i poziome łańcuchy wartości. Warto jednak podkreślić, że doświadczenia wielu firm pokazują, iż cyfrowa transformacja i ściślejsza integracja procesów postępuje znacznie wolniej w przypadku pionowych (procesy, cele), niż poziomych łańcuchów wartości (współpraca z dostawcami, klientami oraz innymi partnerami).
Przemysł 4.0 i Internet Rzeczy
Koncepcja Przemysłu 4.0 (Industrie 4.0) narodziła się w Niemczech w 2001 r., kiedy to decyzją rządu niemieckiego stała się kluczowym elementem strategii innowacyjnego rozwoju naszego zachodniego sąsiada. Utworzona w wyniku tej decyzji grupa robocza „Industrie 4.0 Working Group” sformułowała pierwsze rekomendacje dotyczące implementacji koncepcji „Przemysł 4.0”, które zostały opublikowane w kwietniu 2013 r.
Przemysł 4.0 nierozerwalnie związany jest z kilkoma zaawansowanymi technologiami, z którymi mamy już do czynienia w ostatnich latach. Na pierwszym miejscu wymienić należy Internet Rzeczy (Internet of Things - IoT) lub, zawężając to pojęcie, Przemysłowy Internet Rzeczy (Industrial Internet of Things – IIoT), który charakteryzować się będzie przesyłaniem ogromnych ilości danych, zbieranych przez rozproszone w sieci urządzenia, np. czujniki sczytujące dane z procesu technologicznego. To właśnie w tym celu, aby umożliwić przesyłanie i wymianę informacji między urządzeniami bez udziału człowieka, tak duży nacisk kładzie się telefonię piątej generacji 5G, która pozwala na komunikację nawet do miliona urządzeń rozmieszczonych na kilometrze kwadratowym. W praktyce, taka liczba komunikujących się ze sobą urządzeń z naddatkiem zaspokaja potrzeby większości, nawet najbardziej skomplikowanych linii technologicznych i zakładów przemysłowych.
Z Przemysłem 4.0 nierozerwalnie związane są nowoczesne technologie umożliwiające uelastycznienie produkcji umożliwiające produkowanie niewielkich serii wyrobów i ich dopasowanie pod ścisłe potrzeby klienta. Do technologii, które umożliwiają już dziś personalizację produkcji, zalicza się druk 3D, zaawansowane symulacje, rzeczywistość wirtualną i rozszerzoną. Dopełnieniem wszystkich powyższych technologii będzie znacznie większa niż obecnie integracja przemysłowych systemów informatycznych i systemów automatyki, zarówno w obrębie samego przedsiębiorstwa, jak i obsługi klienta – począwszy od produkcji po dystrybucję wyrobów i serwis posprzedażowy.
Cyfrowy bliźniak i datafikacja
Z Przemysłem 4.0 bardzo silnie związane są również dwa pojęcia, a mianowicie datyfikacja i cyfrowy bliźniak. Datafikacja to proces pozyskiwania informacji przez tworzenie cyfrowych reprezentacji świata rzeczywistego, np. w wyniku omówionej wcześniej digityzacji czy przesyłanych w postaci cyfrowej informacji sczytywanych przez sieć czujników i urządzeń Przemysłowego Internetu Rzeczy. Do procesu tego zalicza się również przetwarzanie i łączenie zbiorów danych oraz ich analizę z wykorzystaniem na przykład algorytmów sztuczne inteligencji, analizę Big Data czy przetwarzanie w systemach klasy Business Inteligence. Wszystkie technologie wykorzystywane do gromadzenia, integracji i analizy danych określa się zbiorczym mianem technologii datafikacji.
Z kolei cyfrowy bliźniak (digital twin) odnosi się do cyfrowej reprezentacji, można wręcz rzec, cyfrowej repliki fizycznych obiektów, procesów i systemów. Innymi słowy model digital twin to połączenie fizycznego obiektu oraz jego cyfrowego odwzorowania w przestrzeni wirtualnej. Na tej podstawie można sterować cyfrową fabryką, przeprowadzać symulacje dotyczące wydajności produkcji, optymalizować rozmieszczenie linii i urządzeń na nich, analizować procesy logistyczne itp.
Co rozumiemy pod pojęciem sztucznej inteligencji (AI)? W ostatnich latach wdraża się coraz bardziej skomplikowane algorytmy realizacji procesów przemysłowych, reagujące na stan obiektu niedający się przewidzieć pierwotnie ze 100 % pewnością. Są to algorytmy samouczące się, bazujące na zdobywaniu i gromadzeniu danych przez maszyny oraz na podejmowaniu działań w oparciu o analizę danych archiwalnych o zdarzeniach. Takie pojmowanie AI ma sens w zastosowaniach przemysłowych – przestrzeń zdarzeń w procesie produkcyjnym jest skończona lub mieści się w pewnych ramach. Pozostaje mały odsetek przypadków „wystających” poza ramy, na początku wymagających wsparcia człowieka, ale później również wbudowywanych w wiedzę systemu AI. Dzięki temu następuje stałe zawężanie „wystającego poza ramy” obszaru doświadczeń AI. Inaczej mówimy o AI w kontekście ogólnym, w znaczeniu, które jest ukształtowane przez literaturę i filmy S-F. Na razie jest to przyszłość. Mówimy tu o takiej drodze ewolucji tej inteligencji, jaką przebył ludzki umysł na drodze od małpy człekokształtnej do homo sapiens. To inny proces, w wyniku którego pojawiają się uczucia, abstrakcyjne myślenie – czy dziś możemy znaleźć je w systemach AI? Nie można jednak wykluczyć, że ze scenariusza, który piszemy dla siebie i maszyn zrealizuje się pomysł maszyny myślącej, czującej, działającej w oparciu o odruchy. Jeśli nasz mózg przeszedł taką drogę, to dlaczego samouczące się i samomodyfikujące się oprogramowanie nie może? Ale to już nie działka przemysłowej AI. |
Coś więcej niż tylko cyfrowa inżynieria
Kolejną grypą trendów związanych z cyfryzacją przemysłu i produkcji jest cyfrowa inżynieria i idąca za nią zwinna, elastyczna produkcja oraz biorący swój początek w usługach informatycznych model wykorzystania czasu pracy maszyn jako usługi Machine-as-a-Service (MaaS). Cyfrowa inżynieria bezpośrednio związana jest z cyfrowym bliźniakiem. Inżyniera cyfrowa nie rewolucjonizuje projektowania, ale je unowocześnia. Można pozostać przy znanych narzędziach i procesach. Zanim powstanie fizyczny projekt, można przetestować go w świecie wirtualnym – i tu przydaje się wirtualny bliżniak.
Stworzenie – za pomocą oprogramowania CAD – cyfrowego bliźniaka maszyny, linii produkcyjnej czy systemu automatyki przemysłowej w postaci modelu 3D, umożliwia zaaplikowanie parametrów fizyczne, z którymi przyjdzie pracować w rzeczywistym środowisku. Nie chodzi tu jednak o zwykła analizę wytrzymałościową, ale możliwość sprawdzenia, jak maszyna, czy system będzie pracować jako oddzielna jednostka oraz w połączeniu z innymi urządzeniami, a także, co ważne, podczas obsługi przez operatorów. Dzięki cyfrowej reprezentacji danych opisujących nowy produkt lub tworzoną linię produkcyjną czy halę, można założyć gogle VR i sprawdzić na własne oczy działanie urządzenia, tak jakby stało tuż przed nami. Można rozwiązywać wszelkie problemy, zoptymalizować miejsce pracy operatora czy przygotować różne udoskonalenia jednym kliknięciem, jeszcze przed wykonaniem fizycznego prototypu.
Cyfrowego bliźniaka produktu lub urządzenia można też przekazać do przetestowania klientowi, aby mógł zoptymalizować swoją maszynę już w trakcie wirtualnej eksploatacji. Wyniki można wykorzystać do tworzenia kolejnych, podobnych produktów dla innych klientów, bez konieczności rozpoczynania prac projektowych od podstaw. Co więcej, możliwy jest też trening pracowników i szkolenia operatorów maszyn jeszcze przed ich fizycznym wyprodukowaniem i ustawieniem na linii produkcyjnej.
Co więcej, gdy maszyna jest łączona z układem sterowania dopiero u klienta, istnieje zawsze ryzyko, że nie będą one ze sobą współpracować. Jednak dzięki wirtualnemu „przekazaniu do eksploatacji” testy układu sterowania można przeprowadzić jeszcze przed dostarczeniem urządzenia do docelowego zakładu. Pozwala to na wykrycie i rozwiązanie problemów z integracją systemów sterowania lub sekwencjonowaniem linii technologicznej przed montażem maszyny u klienta.
Przykładem oprogramowania, które realizuje tego typu zadania cyfrowej inżynierii jest m.in. konfigurator produktów smartDESIGNER firmy WAGO. Umożliwia on projektowanie on-line za pomocą przeglądarki internetowej układów do elektrotechniki i automatyki przy zastosowaniu komponentów WAGO w środowisku 3D. Projektowanie w trybie on-line w przeglądarce internetowej, pozwala uniknąć instalacji oprogramowania i zapewnia użytkownikowi stały dostęp do projektu, niezależnie od tego, gdzie się znajduje oraz do aktualnych danych WAGO.
Po stworzeniu schematu połączeń elektrycznych w oprogramowaniu CAE lub projektu w zintegrowanym, dostarczanym również przez WAGO środowisku programistycznym e!COCKPIT. Wspiera ono wszystkie działania związane z automatyzacją: od konfiguracji sprzętu, przez programowanie, symulację i wizualizację, aż po rozruch gotowego produktu. W aplikacji smartDESIGNER można wyeksportować dane dotyczące wszystkich lub wybranych listew zaciskowych i nadać im własne numery zamówień. Listwa zaciskowa zostaje automatycznie zaprojektowana i zweryfikowana. Co więcej istnieje też możliwość importu plików z opisami z CAE oraz druku opisów złączek.
Projekty złączek listwowych opracowane w smartDESIGNER w formacie natywnym lub neutralnym można przesłać do działu konstrukcji w postaci modeli CAS 2D i 3D przez portal WAGO-PARTcommunity. Do docelowego systemu CAD (a dodatkowo także do oprogramowania PLM/ERP) przesyłane są, oprócz wymiarów geometrycznych, także dane techniczne i handlowe produktu.
W ten sposób tworzony jest cyfrowy ślad lub ścieżka (digital trail, digital thread) danych, które przypisane są do konkretnego produktu, opracowanego w ramach cyfrowego bliźniaka. Co więcej, są one dostępne w całym jego cyklu życia – od projektu do chwili wycofania z rynku i zaprzestania wsparcia. Dane te mogą być przekształcone w łatwy do zrozumienia model, tak jak w przykładowym systemie WAGO, który informuje jak dany produkt lub usługa działa lub jak będzie działał, zarówno w fabryce, jeśli chodzi o proces lub technologię, lub zachowywał się na miejscu u klienta.
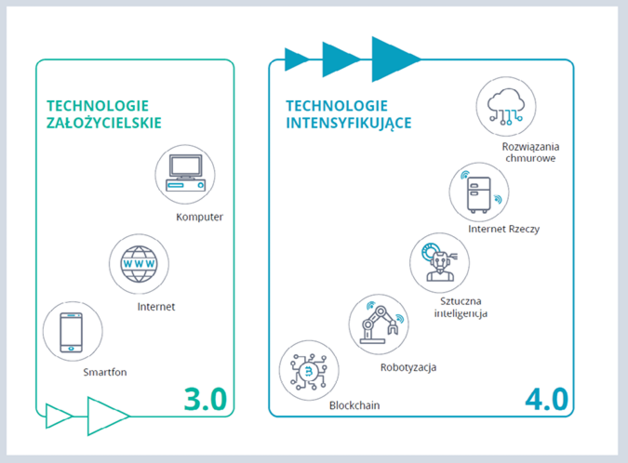
Rys. 1. Technologie założycielskie i intensyfikujące czwartej rewolucji technologicznej, źródło: K. Śledzińska, R. Włoch, Gospodarka cyfrowa, Jak Nowe Technologie zmieniają świat, WUW, Warszawa 2020
Elastyczna, zwinna produkcja
Bezpośrednio z cyfryzacją związana jest też bardzo modna ostatnio koncepcja zwinnego wytwarzania (agile manufacturing). Koncepcja ta ma w swoim założeniu zapewnić przewagę konkurencyjną przez ciągłe doskonalenie, szybką reakcję, systematyczne podnoszenie jakości i koncentrację na potrzebach klienta. Podstawowymi elementami zwinnego wytwarzania są:
- włączenie klienta do procesu projektowania i wytwarzania, czyli cyfrowa inżynieria,
- szybka odpowiedź na potrzeby klienta, związana z monitoringiem rynku, między innymi w mediach społecznościowych,
- indywidualne produkty zgodne z wymaganiami klienta, a więc cyfrowe wytwarzanie na indywidualne zamówienia,
- gotowość do zmian, w tym rekonfiguracji systemów produkcyjnych, czyli wręcz gotowość do przejścia w tryb wynajmowania maszyn, czy całych linii produkcyjnych we wspomnianym modelu MaaS .
Celem zwinnej produkcji jest stworzenie mechanizmów umożliwiających elastyczne i efektywne gospodarowanie zasobami. Zwinna produkcja zakłada więc takie zorganizowanie, które gwarantuje zdolność do szybkiego i efektywnego reagowania na aktualny popyt rynkowy oraz zdolność do aktywnego rozwijania przyszłych możliwości rynkowych. Na poziomie strategicznym wymaga podejścia skierowanego na zewnątrz przedsiębiorstwa. Na poziomie operacyjnym jest związana z elastycznymi zmianami zachodzącymi wewnątrz systemu, szczególnie w procesach innowacji, projektowania, a przede wszystkim − wytwarzania.
Zwinna produkcja wykorzystuje nadmiarową elastyczność (wbudowaną w przedsiębiorstwo lub nie) do szybkiej odpowiedzi na nieprzewidywane zmiany zarówno potrzeb klientów, jak i popytu rynkowego. Zwinna produkcja może być zatem definiowana jako zdolność przedsiębiorstwa do utrzymywania niskokosztowej elastyczności polegającej na równoważeniu poziomów: szczupłości i elastyczności oraz związanej z nią szybkości reakcji i zdolności dostosowywania się do zmieniającego się otoczenia. Poziom szczupłości jest uzależniony od ilości i kosztu generowanych strat, natomiast poziom elastyczności od ilości i kosztu utrzymywania jej nadmiarów [1].
Machine-as-a-Service
W kontekście inteligentnej fabryki, maszyny i urządzenia na hali produkcyjnej powinny być wyposażone w szereg czujników zbierających i przesyłających w czasie rzeczywistym dane w ramach Przemysłowego Internetu Rzeczy, a więc muszą być podłączone do fabrycznych platform IIoT, interfejsów HMI i systemu SCADA. Jak widać, cyfrowa, inteligentna fabryka ułatwia możliwość zastosowania i wdrożenia usługi MaaS, czyli zdalnego udostępniania mocy produkcyjnych poszczególnych linii i maszyn. Jedyną przeszkodą jest to, że dane produktowe i operacyjne generowane przez maszyny muszą być zintegrowane nie tylko z wewnętrznymi procesami produkcyjnymi i systemem IT przedsiębiorstwa, ale również z zewnętrznymi procesami klienta, co dobrze komponuje się z cyfrową inżynierią.
Rodzi się tu zapotrzebowanie na solidną, bezpieczną i niezawodną platformę chmury przemysłowej, która dostarczałaby jednocześnie, w czasie rzeczywistym, dane z maszyny zarówno do systemu IT przedsiębiorstwa, jak i do klienta odnajmującego czas pracy maszyny. Dzięki takiemu podejściu, maszyny na naszej hali produkcyjnej mogą być udostępniane on-line klientom zewnętrznym, którzy chcą używać konkretnej maszyny jako części swoich zasobów produkcyjnych. Dzięki temu, przychód dla właściciela fabryki jest generowany nie tylko ze względu na funkcję, jaką maszyny te pełnią w wewnętrznych procesach fabrycznych, a także na rolę, jaką te same maszyny odgrywają w procesach produkcyjnych zewnętrznych klientów.
Z drugiej strony, klienci, którzy sami nie kupili maszyn lub nie wyposażyli swoich fabryk we wszystkie niezbędne im linie produkcyjne, zlecając produkcję w modelu MaaS, czerpią korzyści z niższych nakładów inwestycyjnych, zamieniając je w koszty operacyjne. Mogą też skorzystać z maszyn, których tak naprawdę potrzebują jedynie sporadycznie, zwiększając w ten sposób elastyczność swojej oferty, zarówno produktowej jak i ilościowej, gdzie zwiększenie mocy produkcyjnych możliwe jest wyłącznie na czas realizacji zamówienia. Dzięki modelowi MaaS można również dość szybko i niższym kosztem, otworzyć fabrykę, ponieważ koszt wynajmu wielu potrzebnych maszyn jest znacznie niższy niż ich fizyczny zakup.
Wirtualna i rozszerzona rzeczywistość
Przejdźmy teraz do wirtualnej rzeczywistości VR (Virtual Reality) i zastanówmy w jakich okolicznościach wirtualny świat może sprawdzić się w przemyśle, w kontekście jego cyfryzacji. Po pierwsze wirtualna rzeczywistość może służyć do planowania hal fabrycznych i linii produkcyjnych, a także kontroli działania robotów. Korzystając z wirtualnych gogli i danych z systemu CAD czy innego oprogramowania związanego z cyfrową inżynierią, można przetestować wirtualnie produkty czy sprawdzić rozmieszczenie maszyn na linii zanim zostanie ona fizycznie wybudowana. W ten sposób łatwo wychwycić wszystkie błędy, a klient ma szansę zapoznać się z produktem zanim fizycznie zostanie on przygotowany i dostarczony.
Technologia wirtualnej rzeczywistości wykorzystywana jest także do monitorowania linii produkcyjnych i całych istniejących fabryk. Wirtualnego bliźniaka wykorzystuje się do monitorowania danych w czasie rzeczywistym i na ich podstawie do optymalizowania procesów. Jest to już obecnie jedna ze standardowych technologii wykorzystywanych przez duże przedsiębiorstwa produkcyjne i firmy z branży motoryzacyjnej i lotniczej.
Obecnie VR w przemyśle wykorzystuje się również podczas prowadzenia szkoleń. Oczywiście dominują tu szkolenia techniczne związane z symulacją różnych procesów. W ten sposób przeszkolić można pracowników, którzy muszą przetrenować jakieś ręcznie wykonywane czynności lub opanować procesy produkcyjne. Podstawową zaletą systemów VR jest to, że można zasymulować warunki niebezpieczne, a z drugiej strony podczas szkolenia nie blokujemy w fabryce linii produkcyjnej.
Z kolei rozszerzona rzeczywistość AR (Augmented Reality) już dzisiaj odgrywa ważną rolę w kontroli jakości wyprodukowanych lub zmontowanych wyrobów. Obecnie przemysł motoryzacyjny i lotniczy wykorzystuje oprogramowanie rozszerzonej rzeczywistości do kontroli jakości części dostarczanych przez firmy zewnętrzne. Rozszerzoną rzeczywistość stosuje się też do kontroli poprawności montażu i rozmieszczenia różnych podzespołów. Firmy z branży motoryzacyjnej, które zastosowały tablety z systemami AR w miejsce tradycyjnych instrukcji roboczych, informują, że dzięki temu liczba błędów zmalała o 90 %, a czas cyklu montażowego skrócił się o 40–50 %.
Digitalizacja odbywa się na wielu poziomach zarządzania produkcją Nasza platforma Asix znajduje się na poziomie systemów SCADA. Od lat zauważamy zwiększającą się obecność oprogramowania, z którym wymieniamy dane. Chodzi tu o oprogramowanie MOM i ERP. Te systemy, które jeszcze kilka lat temu były wyjątkami, stają się normą. Naszym zdaniem możemy tu mówić o trwałym trendzie. Pojawiają się wymagania dotyczące współpracy z oprogramowaniem klasy APS i CMMS. To pierwsze, to przedłużenie systemu MOM w celu optymalizacji procesu wytwarzania, CMMS jest pewną nowością. To poszukiwanie przez przedsiębiorców nowych narzędzi do sprawnego zarządzania maszynami i zasobami ludzkimi w celu zapewnienia wielopoziomowej optymalizacji procesu produkcji, obejmującej koszty bezpośrednie i te związane z optymalną alokacją zadań oraz z utrzymaniem w stanie sprawności parku maszynowego przy ograniczonych zasobach. ASKOM przewidział ten trend i oferuje narzędzia do monitoringu maszyn, jako gotowe do użycia elementy naszego systemu „out of the box”. Opisane powyżej trendy pokazują, że coraz częściej odchodzi się od zarządzania i planowania produkcji za pomocą wspomaganego dokumentacją papierową Excel-a. To dobry trend. |
Rola oprogramowania w cyfrowej transformacji
Najistotniejszą rolę w cyfrowej transformacji odgrywa jednak oprogramowanie. To dzięki niemu możliwe jest przetworzenie zebranych danych, dostarczanie informacji w ramach raportów, czy sterowanie procesami i programowanie maszyn wykonujących określone zadania. Zastosowane oprogramowanie inteligentnej fabryki musi wspierać realizację następujących aspektów zarządzania inteligentną produkcją [2]:
- Gromadzenie danych: bezpieczne gromadzenie i przechowanie, niezależnie od sprzętu, danych ze wszystkich procesów, urządzeń i wprowadzonych/wygenerowanych przez ludzi. Szeroka gama protokołów komunikacyjnych pozwala na komunikację ze wszystkimi wykorzystywanymi urządzeniami, sterownikami PLC i systemami zarządzania przedsiębiorstwem oraz aplikacjami w chmurze.
- Wizualizacja i kontrola: wyświetlanie danych operacyjnych w czasie rzeczywistym na indywidualnie dopasowanym interfejsie, zapewniające większą świadomość i wydajniejsze sterowanie procesami, zarówno lokalnie, jak i zdalnie.
- Zarządzanie danymi: kontekstualizacja danych pozwalająca na podejmowanie lepiej uzasadnionych i wiarygodnych decyzji.
- Analityka i raportowanie: analiza, np. przy wykorzystaniu sztucznej inteligencji, danych historycznych i danych zbieranych w czasie rzeczywistym w celu wypracowania jak najdokładniejszych wniosków.
- Inżynieria i konserwacja: narzędzia pozwalające na tworzenie projektów, utrzymanie ruchu i zarządzanie fabryką.
Co ważne, oprogramowanie inteligentnej fabryki pozwala na poziomą integrację maszyn i pionową integrację systemów całego przedsiębiorstwa, komunikację maszyn, systemów i zasobów, jak również udostępnia dane z czujników systemom planowania zasobów przedsiębiorstwa. Dzięki temu aplikacje zarządzające inteligentną fabryką eliminują natłok informacji w firmie i ułatwiają komunikację między maszynami, obiektami, ludźmi, systemami IT przedsiębiorstwa i systemami klienta.
Czy chmura w środowisku przemysłowym ma sens? Czy rzeczywiście przeniesienie danych przemysłowych do chmury jest w stanie zwiększyć produktywność i usprawnić przepływ procesów? Istotną zaletą rozwiązań chmurowych jest brak konieczności przygotowania specjalistycznej infrastruktury IT, niezbędnej do przechowywania i przeliczania danych. Nie ma już potrzeby inwestowania w kosztowne serwery i najnowsze oprogramowanie czy utrzymywania serwerowni, ponieważ w ramach usługi użytkownik uzyskuje dostęp do zasobów i możliwości obliczeniowych dostawcy rozwiązania chmurowego. To jedna strona medalu. Mając do dyspozycji nowoczesne narzędzia cyfrowe, działające w oparciu o rozwiązanie chmurowe, organizacja biznesowa staje się dużo bardziej elastyczna, procesy mogą być realizowane i nadzorowane nie tylko zdalnie, z uwzględnieniem dodatkowych informacji z urządzeń inteligentnych, co zwiększa ich niezawodność oraz stwarza nowe możliwość gruntownej analizy na podstawie większej liczby zmiennych. Bezpośrednie zaangażowanie ludzi w diagnostykę i nadzór nad pracą maszyn może zostać ograniczone do minimum, przy jednoczesnym wdrożeniu predykcyjnego modelu zarządzania. Kolejnym aspektem jest zwiększenie bezpieczeństwa – zarówno przez ograniczenie ryzyka narażenia pracowników na szkodliwe warunki otoczenia przemysłowego, jak i bezpieczeństwo procesowe, osiągnięte dzięki mniejszej liczbie awarii oraz możliwości reagowania na wszelkie nieprawidłowości, zanim doprowadzą one do postoju linii produkcyjnej czy jakiegoś procesu. |
Sztuczna Inteligencja, czyli przyszłość cyfrowej transformacji
Na koniec warto kilka słów poświęcić przyszłości cyfrowej transformacji. Transformacja cyfrowa nie jest jednak zjawiskiem nowym i tak naprawdę trwa już od ponad 20 lat. Jak pokazaliśmy, dobrze przygotowana cyfryzacja wymaga zintegrowania inteligentnych technologii z istniejącymi procesami biznesowymi. Jedną z nich jest sztuczna inteligencja. Umiejętne wykorzystane możliwości sztucznej inteligencji, uczenia maszynowego i analityki danych może stać się fundamentem innowacyjności i źródłem przewagi konkurencyjnej.
Sztuczna inteligencja coraz częściej staje się również katalizatorem cyfrowej transformacji. Wspiera firmy w stawaniu się bardziej elastycznymi i innowacyjnymi. Przedsiębiorstwa wdrażające rozwiązania wykorzystujące algorytmy sztucznej inteligencji efektywniej pozyskują nowych klientów, ograniczają ryzyko i usprawniają obsługę klienta. Możliwości oferowane przez technologie sztucznej inteligencji i uczenia maszynowego są też niezbędne do przetwarzania i analizowania zbiorów danych Big Data, pozyskiwanych m.in. z Przemysłowego Internetu Rzeczy i systemów automatyki przemysłowej. Z kolei sztuczna inteligencja i uczenie maszynowe muszą również dysponować odpowiednio dużymi zbiorami danych, by oferować dokładne i rzetelne wyniki oraz efektywnie się uczyć i przeprowadzać biznesowo-produkcyjne analizy. Współdziałanie technologii Big Data, sztucznej inteligencji i narzędzi analitycznych jest obecnie podstawą cyfrowej transformacji.
W przyszłości znaczenie sztucznej inteligencji będzie jeszcze większe. Przewiduje się, że już za pięć lat szybko rosnący globalny rynek oprogramowania sztucznej inteligencji AI (Artifical Intelligence), osiągnie wartość około 126 miliardów dolarów. O utrzymaniu konkurencyjności zadecyduje przemyślane wykorzystanie dostępnych danych i wdrożenie cyfrowych narzędzi, które pozwolą ujednolicić informacje spoczywające w bazach, hurtowniach danych i tzw. jeziorach danych (data lakes), gdzie przechowywane są wielkie zbiory nieustrukturyzowanych danych. Przedsiębiorstwa, będą musiały analizować tak zgromadzone informacje, właśnie za pomocą rozwiązań wspieranych przez algorytmy sztucznej inteligencji. Inaczej nie da się nie tylko osiągać lepszych wyników finansowych, ale zrozumieć bieżących, zmieniających się potrzeb kleientów i sterować dopasowaną do nich produkcją. Co więcej, potrafiąc przewidywać przyszłe zachowania klientów, wykorzystując uczenie głębokie do rozpoznawania wzorców, można znacznie szybciej przygotować odpowiednie, zindywidualizowane produkty i dostosować do ich wytwarzania linie produkcyjne.
Klasy oprogramowania stosowanego najczęściej w przemyśle SCADA (Supervisory Control And Data Acquisition) – system informatyczny nadzorujący przebieg procesu technologicznego lub produkcyjnego. Jego główne funkcje obejmują zbieranie aktualnych danych (pomiarów), ich wizualizację, sterowanie procesem, alarmowanie oraz archiwizację danych. CAD/CAM, oznacza wspomagane komputerowo projektowanie (Computer Aided Design) i wytwarzanie (Computer Aided Manufacturing). W systemach CAD, możemy kreślić geometrię 2D projektowanych częci i wyrobów, modelować je w 3D, przygotować dokumentację techniczną, wykonywać obliczenia wytrzymałościowe, czy przeprowadzać symulację działania konstrukcji pod wpływem określonych warunków fizycznych. Zaletą systemów CAD jest cyfrowy zapis geometrii obiektów umożliwiający szybkie i łatwe tworzenie skomplikowanych modeli, możliwość wprowadzania licznych poprawek, wirtualnego testowania, archiwizację przygotowanych projektów w postaci cyfrowej oraz wymiany cyfrowych danych z innymi systemami. Systemy CAM to z kolei oprogramowanie, którego zadaniem jest integracja systemów projektowania i wytwarzania. System CAM, w oparciu o stworzone modele CAD, odpowiada za wygenerowane kody, które po przesłaniu do maszyn wykonawczych, np. obrabiarek sterowanych numerycznie, pozwalają wyprodukować zaprojektowaną część. PLM (Product Lifecycle Management) to oprogramowanie do zarządzania cyklem życia produktu. Wspiera proces tworzenia i rozwoju produktów od momentu koncepcji, przez projekt i produkcję, kończąc na serwisie gwarancyjnym, wsparciu posprzedażowym, serwisowym, aż po utylizację. Dzięki temu następuje konwergencja systemów projektowania wspomaganego komputerowo CAD, wytwarzania wspomaganego komputerowo CAM, inżynierii wspomaganej komputerowo CEA (Computer Aided Engineering), zarządzania danymi produktów PDM (Product Data Management) oraz cyfrowej produkcji realizowanej m.in. w cyfrowych fabrykach. PLM odróżnia się jednak od innych rozwiązań dla przedsiębiorstw, ponieważ koncentruje się na pozyskiwaniu maksymalnych przychodów z powtarzających się procesów, w tym procesów produkcyjno-projektowych. MES (Manufacturing Execution System) to systemy realizacji produkcji. Systemy klasy MES współpracują z elementami systemów automatyki, służą do ciągłego monitorowania procesów produkcyjnych oraz pozyskiwania odpowiednich informacji z przebiegu produkcji i przekładaniu ich na płaszczyznę biznesową. Wszystko po to, by w czasie rzeczywistym otrzymywać realne informacje na temat produkcji i móc sprawnie reagować na zaistniałe sytuacje lub modyfikować produkcję tak, by była jak najbardziej efektywna. Co ważne, dane o realizowanej produkcji są zbierane i dostarczane użytkownikowi w czasie rzeczywistym, dzięki czemu możliwa staje się natychmiastowa reakcja na wszelkie niepożądane zjawiska zarówno związane z produkcją, jak i idącymi za tym czynnikami biznesowymi. Co więcej, system MES informuje też osoby odpowiedzialne za produkcję o jej faktycznym stanie. Narzędzia tego typu umożliwiają m.in.:
|
[1] M. Dudek, Równoważenie poziomów elastyczności wewnętrznej i szczupłości w kontekście zwinnej produkcji, Zeszyty Naukowe Uniwersytetu Ekonomicznego w Katowicach Nr 351, s. 164, 2018
[2] Materiały firmy COPA-DATA
źródło: Automatyka 12/2021
Słowa kluczowe
automatyka, cyfryzacja, cyfryzacja przemysłu, oprogramowanie, oprogramowanie przemysłowe
Komentarze
blog comments powered by Disqus