Zwiększanie konkurencyjności z firmą LUMEL dzięki kalkulacji OEE
Andrzej Barciński (LUMEL S.A. ) drukuj
Przy stale rosnących cenach mediów i surowców, potrzebnych do produkcji, tzw. koszty stałe mają coraz większy udział w ogólnych kosztach firmy. Ich ograniczenie jest jedną z bardziej efektywnych metod zwiększenia konkurencyjności przedsiębiorstwa.
Jednym z parametrów obrazujących wydajność produkcji i pozwalających ograniczyć straty jest tzw. Wskaźnik Efektywności Parku Maszynowego – OEE (ang. Overall Equipment Effectiveness).
Obliczanie OEE
Istnieje wiele publikacji na temat OEE. W uproszczeniu można powiedzieć, że współczynnik ten wylicza się na podstawie trzech parametrów:
OEE = dostępność × wydajność × jakość,
gdzie:
dostępność – przedstawia stosunek czasu przeznaczonego na realizację zadania do czasu, jaki można realnie na to zadanie poświęcić, uwzględniając awarie i przezbrojenia maszyn,
wydajność – przedstawia rzeczywiste wykorzystanie maszyny, odniesione do jej nominalnych możliwości określonych przez producenta,
jakość – to stosunek dobrych do złych wyrobów.
Jak i czym zmierzyć OEE?
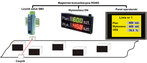
Rys. 1. Przykład systemu zliczającego i monitorującego liczbę wyprodukowanych elementów (jedna linia produkcyjna)
Lumel ma w ofercie odpowiednie narzędzia, pozwalające dokonywać pomiaru i wyliczenia współczynnika OEE. Do narzędzi tych zalicza się:
- liczniki pozwalające zmierzyć liczbę wytworzonych sztuk produktu, czas pracy maszyn i czas przestojów,
- panele operatorskie, pozwalające na lokalne (bezpośrednio na linii produkcyjnej) wprowadzanie wartości zadanych i bieżący podgląd mierzonych parametrów,
- wyświetlacze diodowe prezentujące mierzone wskaźniki (np. dla załogi),
- konwertery pozwalające na przesyłanie zebranych informacji za pomocą magistrali komunikacyjnych przewodowych (Modbus, Ethernet) i bezprzewodowych (moduły radiowe oraz Wi-Fi),
- oprogramowanie pozwalające na gromadzenie danych i wyliczanie odpowiednich wskaźników.
Lumel, oprócz dostawy poszczególnych wyrobów, oferuje oczywiści możliwość wykonania całego systemu „pod klucz”, wraz z konfiguracją i uruchomieniem na terenie zakładu.
Przykładowe wdrożenia
Firma Lumel wykonała już niejedno wdrożenie, związane z pomiarem wskaźnika OEE. Poniżej przedstawiono dwa wybrane wdrożenia w w/w zakresie.
Opomiarowanie 12 linii produkcyjnych
Pierwsza z realizacji dotyczyła opomiarowania wydajności produkcji i parametrów sieci zasilającej na 12 liniach produkcyjnych, w zakładzie produkującym komponenty dla przemysłu samochodowego (rys. 1).
Funkcje wymagane przez klienta:
- pomiar liczby wyprodukowanych komponentów na każdej z maszyn produkcyjnych,
- pomiar liczby nieplanowanych przestojów,
- zliczanie czasu nieplanowanych przestojów,
- pomiar zużytej energii elektrycznej i innych parametrów sieci zasilającej,
- alarmowanie obsługi w przypadku wystąpienia przestojów,
- obliczenie współczynnika OEE na podstawie monitorowanych parametrów,
- prezentacja kluczowych danych (plan, wykonanie itp.) na wyświetlaczach diodowych, widocznych ze znacznych odległości, w halach produkcyjnych,
- archiwizacja i prezentacja zebranych danych dla osób zarządzających produkcją.
Po uzgodnieniu wszystkich szczegółowych wymagań klienta wdrożono rozwiązanie oparte na systemie rozproszonym. Przy każdej maszynie na linii produkcyjnej zabudowano małą szafkę pomiarową, wyposażoną w następującą aparaturę:
- licznik liczby wyprodukowanych sztuk,
- licznik liczby i czasu nieplanowanych przestojów,
- miernik parametrów sieci, pozwalający na pomiar zużytej energii, mocy, harmonicznych i wielu innych parametrów.
Wszystkie szafki w obrębie danej linii produkcyjnej zostały połączone magistralą komunikacyjną i podłączone do głównej szafki sterowniczej, wyposażonej w sterownik i panel operatorski. Na panelu operatorskim obsługa wprowadza niezbędne parametry do wyliczania współczynnika OEE, takie jak dostępny czas produkcji, czas jednego cyklu produkcyjnego i czas planowanych przestojów.
Aplikacja wykonana na panelu operatorskim dostarcza obsłudze informacji o bieżącym wykonaniu planu, wskaźniku wykorzystania parku maszynowego (OEE), wystąpieniu przestoju każdej z maszyn, liczbie przestojów i łącznego czasu ich trwania na poszczególnych maszynach, raportach z przestojów (liczba i czas przestojów oraz średni czas przestoju każdej z maszyn na zmianie) oraz raportów z wykorzystania parku maszynowego (wskaźnik OEE) i realizacji planu produkcji.
Dodatkowo nad każdą linią produkcyjną zamontowany został widoczny ze znacznej odległości wyświetlacz diodowy, informujący o planie i bieżącej realizacji produkcji. Szafki sterownicze zostały podłączone do lokalnej sieci komputerowej klienta. Na serwerze zainstalowano aplikację, odczytującą mierzone parametry dotyczące wskaźnika OEE oraz parametrów sieci zasilającej. Zainstalowany program pozwala na przeglądanie mierzonych parametrów i wyliczonych wskaźników oraz tworzenie odpowiednich raportów z realizacji produkcji i zużytej energii elektrycznej.
Wdrożenie systemu przyniosło wiele korzyści. Informacja o bieżącym wykorzystaniu parku maszynowego dla operatorów i nadzoru stała się dostępna lokalnie na panelach operatorskich, lokalnie na wielkogabarytowych wyświetlaczach diodowych oraz na komputerach wpiętych do sieci zakładowej. Ponadto zyskano krótsze czasy przestojów, w związku z monitorowaniem stanów alarmowych. Udostępniona też została informacja o ilości zużytej energii na proces produkcyjny oraz poprawiono jakość i zmniejszono koszty produkcji.
Opomiarowanie 80 linii produkcyjnych
Kolejna realizacja została przeprowadzona również w zakładzie z branży motoryzacyjnej, a dotyczyła opomiarowania wydajności około 80 linii produkcyjnych, zlokalizowanych w kilku halach (rys. 2). Funkcje wymagane przez klienta to: lokalna informacja dla obsługi o bieżącej realizacji planów produkcyjnych, możliwość automatycznego rozsyłania planów dla operatorów na produkcji za pomocą odpowiedniej aplikacji, logowanie danych z realizacji planów produkcyjnych w bazie SQL klienta i umożliwienie łatwego tworzenia raportów z realizacji zadań produkcyjnych.
W celu lokalnego informowania obsługi o bieżących planach produkcyjnych zainstalowano na terenie zakładu około 80 odpornych na trudne warunki środowiskowe wyświetlaczy diodowych, prezentujących plan, realizację i procent wykonania zadań produkcyjnych. Informacja o stopniu realizacji pobierana jest przez wyświetlacze z zainstalowanych na liniach liczników. Plany zapisywane są w sposób automatyczny z zainstalowanej na serwerze firmowym aplikacji, a realizacje są wyliczane przez sterowniki tablic.
Wyświetlacze zostały wyposażone w moduły komunikacyjne Wi-Fi, co znacznie zmniejszyło koszty podłączenia ich do sieci komputerowej klienta.
Aby sprostać wszystkim wymaganiom klienta, zdecydowano się na stworzenie „pod klucz” nowego programu do monitorowania wykonania produkcji. Program został zainstalowany na serwerze firmowym. Stworzony program umożliwia: odczyt (z wyświetlaczy) wykonania produkcji za pomocą sieci Wi-Fi,
zadawanie planów dla poszczególnych wyświetlaczy przez zalogowanych użytkowników, za pomocą przeglądarki internetowej, wysyłanie planów do wyświetlaczy w sposób automatyczny, z krokiem co 15 minut, zapis danych archiwalnych do bazy SQL, zainstalowanej w firmie i tworzenie raportów z zapisanych danych archiwalnych.
Na rys. 3. pokazano przykładowy raport z realizacji zadań produkcyjnych. Uzgodniona z klientem forma raportów pozwala przeanalizować, czy plan został zrealizowany oraz jak przebiegała jego realizacja w ciągu dnia roboczego. Wdrożenie pozwoliło osiągnąć następujące korzyści:
- klient otrzymał narzędzie do automatycznego informowania obsługi, rozproszonej na terenie dużego zakładu produkcyjnego, o bieżących planach produkcyjnych,
- załoga może na bieżąco kontrolować postęp wykonania założonego planu (dzięki zamontowanym wyświetlaczom),
- osoby odpowiedzialne za nadzór produkcji mają bieżące informacje o postępie w realizacji zadań produkcyjnych, zarówno w lokalnej sieci komputerowej, jak i na zewnątrz zakładu,
- archiwizowane w bazie SQL dane mogą być pobierane i wykorzystywane przez inne aplikacje klienta,
- zwiększono wydajność produkcji dzięki stałemu monitorowaniu wszystkich kluczowych linii produkcyjnych.
Oba opisane wdrożenia zostały przeprowadzone za pomocą odmiennej aparatury, lecz ich wynikiem jest osiągnięcie tego samego celu, w postaci kontroli i poprawy realizacji zadanych planów produkcyjnych. Wielkogabarytowe wyświetlacze diodowe spełniają funkcję kontrolną dla służb nadzoru i funkcję motywacyjną dla załogi. Służby nadzoru mają stały dostęp do zebranych danych. Analiza danych pozwala wykryć wiele nieplanowanych przestojów, wynikających np. ze źle zaplanowanego przezbrojenia maszyn, awarii, braków materiałowych lub czynnika ludzkiego. Dodatkowo, jak w przypadku pierwszej realizacji, system można rozszerzyć o kontrolę parametrów sieci zasilającej, co pozwala uzyskać informację o ilości zużytej energii i jej jakości oraz w dużym stopniu uniknąć niepotrzebnej pracy urządzeń bez obciążenia. Opisane systemy mogą być wdrażane jednoetapowo, ale można też zdecydować się na ich wdrażanie etapami, z podziałem na pojedyncze linie lub hale produkcyjne, poczynając od najbardziej newralgicznych punktów.
Działając od ponad 60 lat na rynku, Lumel dysponuje ogromnym doświadczeniem i odpowiednimi kadrami, by szybko i efektywnie wdrażać podobne systemy w różnych gałęziach przemysłu.
Marcin Ponoś, Kamil Macias
źródło: LUMEL
Słowa kluczowe
koszty produkcji, lumel, obliczanie OEE, oee, oprogramowanie, optymalizacja, polecane
Komentarze
blog comments powered by Disqus