Aparatura kontrolno-pomiarowa
dr inż. Marcin Bieńkowski drukuj
Bez różnego rodzaju czujników, mierników, sensorów, rejestratorów, przetworników czy analizatorów, które podłączone są do systemów sterowania i systemów automatyki, trudno wyobrazić sobie współczesny przemysł. Co więcej, jak pokazują badania, można zapobiec od 80 % do 90 % awarii monitorując stan techniczny związany z funkcjonowaniem podzespołów urządzeń, sprawdzając parametry robocze maszyny i właściwości fizyko-chemiczne czynników czy cieczy roboczych. Dzięki temu można nie tylko zwiększyć jakość, ale również, w istotny sposób, zmniejszyć koszty produkcji i utrzymania ruchu.
Każda fabryka, każda linia technologiczna, każda maszyna i urządzenie, czy wreszcie każdy system sterowania wymaga odpowiedniej aparatury dostosowanej do prowadzenia pomiarów właściwych dla danej technologii oraz charakterystyki użytkowej wykorzystanego na linii produkcyjnej sprzętu i podzespołów.
Pomiar parametrów maszyn niezbędnych do prawidłowego ich działania
Za prowadzenie wszelkiego typu pomiarów w przemyśle odpowiedzialne są nie tylko czujniki pomiarowe, ale również aparatura kontrolno-pomiarowa i współpracujące z nimi systemy automatyki. Tego typu kompleksowe rozwiązania pomiarowe bardzo często w literaturze określane są skrótem AKPiA, czyli Aparatura Kontrolno--Pomiarowa i Automatyka.
Systemy sterowników AKPiA gwarantują kontrolę nad każdym pojedynczym procesem produkcyjnym, zapewniają poprawę bezpieczeństwa pracy i eliminują przyczyny powstawania błędów produkcyjnych. Dzięki systemom aparatury kontrolno-pomiarowej i automatyki można przewidywać z wyprzedzeniem awarię maszyn i maksymalnie eliminować błędy związane z czynnikiem ludzkim przy produkcji. Sterowniki AKPiA znajdują zastosowanie w firmach produkcyjnych, magazynach i centrach logistycznych. Najczęściej stosowane są w przemyśle: motoryzacyjnym, spożywczym, chemicznym, meblarskim, podczas produkcji elementów budowlanych, a także w branży FMCG.
Mierniki, rejestratory, detektory i charakterografy
Niezależnie od tego, czy daną wielkość fizyczną mierzymy w sposób bezpośredni czy pośredni, czy mierzona wielkość jest wielkością elektryczną, mechaniczną czy optyczną, przyrządy pomiarowe służące do ich pomiaru podzielić można na trzy podstawowe grupy – mierniki, rejestratory i detektory, a ze względu na funkcję metrologiczną, na przyrządy pomiarowe, kontrolne i użytkowe.
Zacznijmy od tego, czym jest miernik. Miernik to po prostu przyrząd pozwalający określić mierzoną wielkość fizyczną. Wielkość ta może być przedstawiona za pomocą podziałki, tak jak w przyrządach analogowych, bądź też za pomocą cyfr przedstawiających bezpośrednio jej wartość. W tym wypadku mamy do czynienia z miernikami cyfrowymi. Chyba najprostszym możliwym miernikiem jest zwykła szkolna linijka z milimetrową podziałką. Prostym, analogowym miernikiem jest też termometr rtęciowy do mierzenia temperatury za naszym oknem. Jak można się domyślić, nieco szerszym pojęciem jest przyrząd pomiarowy. Termin ten obejmuje bowiem nie tylko nieco bardziej skomplikowane urządzenia pomiarowe, pozwalające na rejestrację mierzonych wartości, ale również różnego rodzaju generatory pomiarowe, analizatory czy wzorce.
Jeśli chodzi o rejestratory, a więc przyrządy umożliwiające rejestrację mierzonych wartości, to obecnie w przemyśle wykorzystuje się wyłącznie urządzenia cyfrowe. Pozwalają one na zapis mierzonych w czasie rzeczywistym wartości na wbudowanej pamięci flash lub na zewnętrznych, cyf-
rowych nośnikach, w tym nośnikach znajdujących się w sieci lub w chmurze. To właśnie dlatego nowoczesne, cyfrowe rejestratory wyposażane są niemal zawsze w różne interfejsy komunikacyjne, w tym karty sieciowe, pozwalające na swobodne przesyłanie i składowanie mierzonych wartości do systemów bezpośrednio sterujących procesem technologicznym, takich jak sterowniki PLC czy systemy SCADA. Warto nadmienić, że spotykane w przemyśle rejestratory oferują zwykle proste funkcje skalowania mierzonego sygnału i jego rejestrację w jednostkach fizycznych. Ponadto często są one wyposażane w wyjścia alarmowe pozwalające sygnalizować przekroczenia dopuszczalnych dla danego procesu wartości granicznych.
Ostatnią grupą urządzeń pomiarowych systemów automatyki są detektory stosowane w chwili, gdy badany sygnał nie możne być zarejestrowany bezpośrednio i musi być zamieniony na inną formę możliwą do obserwacji lub rejestracji. Detektory można podzielić na detektory cząstek, np. detektory cząstek elementarnych, detektory promieniowania elektromagnetycznego, np. fototranzystory, detektory zmiany składu chemicznego, np. spektrometry, tlenomierze, jonometry, detektory stężeniowe oraz na detektory zmian parametrów fizycznych.
Mimo że tego typu urządzenia nie są standardowo wykorzystywane w przemyśle jako takim, to warto jeszcze wspomnieć o ostatniej grupie urządzeń pomiarowych, a mianowicie charakterografach. Jest to sprzęt służący do przeprowadzenia pomiarów pozwalających określić charakterystykę mierzonego elementu. Z charakterografem spotkać się można przede wszystkim tam, gdzie wyznacza się charakterystyki prądowo-napięciowe elementów półprzewodnikowych, takich jak tranzystory, diody czy analogowe układy scalone.
W jakim kierunku zmierza rozwój aparatury kontrolno-pomiarowej? Pierwszy kierunek rozwoju jest zbieżny z tym, którego doświadczamy w zasadzie w każdej dziedzinie naszego życia. Jest nim cyfryzacja. Ponad 80 % urządzeń pomiarowych dostarczanych do przemysłu przez Endress+Hauser to sprzęt inteligentny. Co to oznacza? Urządzenia te potrafią dostarczać dokładne dane pomiarowe i diagnostyczne zarówno do systemu sterowania, jak i do przemysłowej chmury obliczeniowej, z której są dostępne w trybie 24/7/365, w tym również przez urządzenia mobilne, dla kadry zakładu, systemu zarządzania produkcją oraz dla podmiotów z jego ekosystemu (poddostawców surowców, odbiorców produktów gotowych, zewnętrznych służb technicznych itd.). W efekcie, skuteczne prewencja i predykcja w zakresie zaopatrzenia, sprzedaży i utrzymania ruchu stają się dziś czymś zupełnie naturalnym. Przemysłowy Internet Rzeczy to zagadnienie zdefiniowane ponad 10 lat temu. Dziś jego rolą w pomiarach przemysłowych jest dostarczać możliwie dużą ilość danych pomiarowych i diagnostycznych do przemysłowej chmury obliczeniowej. Dzięki temu możliwe staje się szybkie i celne wnioskowanie w oparciu o archiwizowane zbiory Big Data. Kadry zakładów przemysłowych wykorzystują tę technologię do podejmowania właściwych decyzji we właściwym czasie w zakresie m.in. optymalizacji zużycia energii i surowców do produkcji, planowania zaopatrzenia i sprzedaży oraz utrzymania ciągłości ruchu. Każdy zakład, inwestujący w Przemysłowy Internet Rzeczy, zyskuje przewagę konkurencyjną na rynku. Drugi kierunek to galopująca miniaturyzacja i masowe rozpowszechnianie się sond i przetworników pomiarowych o podstawowej funkcjonalności, głównie wśród producentów maszyn i linii technologicznych. Niezwykle cenna jest bezobsługowość i w wielu przypadkach umiejętność szybkiej adaptacji do systemu sterowania (plug & play), którymi to cechami ta grupa urządzeń się wyróżnia. W Endress+Hauser wdrażamy rocznie kilkanaście nowych produktów z tej grupy, w tym z komunikacją IO-Link, Ethernet-APL i Modbus TCP. |
Przyrządy pomiarowe i aparatura kontrolno-pomiarowa
Najprościej definiując, przyrząd pomiarowy to proste urządzenie będące pojedynczym miernikiem, do którego może być podłączony jeden lub kilka czujników. Typowym miernikiem jest multimetr cyfrowy, pozwalający na ręczny pomiar napięcia, natężenia prądu, rezystancji, czasami mocy – nic więcej. Służy po prostu do odczytu mierzonej wartości. Innym przykładem może być suwmiarka, śruba mikrometryczna czy termometr.
Aparatura pomiarowa to dużo bardziej złożone urządzenie, o dużo większych możliwościach technicznych. Może zwykle pracować samodzielnie bez udziału człowieka, rejestrować wartości pomiarów, wykonywać je w ściśle określonych odstępach czasu itp. Co więcej, często aparaturą pomiarową może być system automatycznego pomiaru mierzonych wartości, składający się z kilku pojedynczych mierników podłączonych np. do sterownika PLC lub komputera przemysłowego. Dobrym przykładem aparatury pomiarowej może być automatyczny oscyloskop cyfrowy, za pomocą którego można przeprowadzić zarówno proste pomiary, jak i sprawdzić charakterystyki sygnałów i je zapisać, oraz wysłać dane za pośrednictwem sieci Ethernet na firmowy serwer do dalszej analizy.
Służby Utrzymania Ruchu
Zanim przejdziemy do omówienia urządzeń stosowanych na liniach produkcyjnych, zatrzymajmy się na chwilę przy aparaturze kontrolno-pomiarowej i miernikach wykorzystywanych przez Służby Utrzymania Ruchu. Ze względu na swoją specyfikę, pracownicy SUR stosują sprzęt mobilny czyli tak zwaną aparaturę przenośną. Ze względu na charakterystykę i zastosowania aparaturę tę można podzielić na dwie grupy:
- sprzęt do kompleksowej diagnostyki urządzeń elektrycznych i pomiarów wielkości mechanicznych,
- sprzęt kontrolny, pozwalający sprawdzić i wywzorcować czujniki oraz urządzenia pomiarowe na stałe zamontowane w maszynach czy na linii produkcyjnej.
W skład pierwszej grupy wchodzą urządzenia do szeroko rozumianych pomiarów elektrycznych, aparatura do pomiaru wibracji, akcelerometry, analizatory ultradźwiękowe i rentgenowskie, wszelkiego rodzaju przenośne wagi, kamery termowizyjne lub czujniki do pomiarów temperatury, a także zwykłe suwmiarki, śruby mikrometryczne, a niekiedy czujniki zegarowe do pomiaru wielkości mechanicznych.
Do tej grupy zalicza się wszelkiego typu kalibratory pozwalające na weryfikację, czy urządzenia pomiarowe nadal oferują wyniki pomiarów mieszczące się w założonej klasie dokładności, przenośne czujniki gazów czy kamery termowizyjne wykorzystywane do sprawdzania poprawności działania zamontowanych w maszynach pirometrów.
Warto zauważyć, że niezależnie od tego, do której grupy urządzeń przenośnych należy dany przyrząd, widać wyraźną tendencję do maksymalnego uproszczania ich obsługi. Duży nacisk kładzie się też na integrację przenośnych urządzeń pomiarowych z oprogramowaniem, a także wyposaża się je w szereg interfejsów komunikacyjnych, w tym pozwalające na łączność bezprzewodową. Kolejnym trendem konstrukcyjnym, jest budowanie urządzeń łączących w sobie kilka funkcji pomiarowych, tak aby pracownicy SUR nie musieli nosić ze sobą „po całym zakładzie”, kilku lub kilkunastu przyrządów pomiarowych.
Niemal każdy, stosowany profesjonalnie mobilny przyrząd pomiarowy i przenośny miernik, jest w stanie gromadzić dane pomiarowe w pamięci, z której można je przegrać do obsługującej je aplikacji. Coraz częściej dane te można wysłać bezpośrednio, np. za pomocą interfejsu Bluetooth lub przez Wi-Fi wprost do oprogramowania zainstalowanego na telefonie komórkowym. Zauważalną tendencją w ich budowie jest również to, że aparaturę przenośną wyposaża się w duże wyświetlacze graficzne pozwalające na łatwe jednoczesne zobrazowanie kilku parametrów pomiarowych oraz na tworzenie w czasie rzeczywistym czytelnych wykresów. Mobilny sprzęt jest też coraz częściej dużo bardziej kompaktowy i znacznie bardziej wygodny w użyciu niż jeszcze kilka lat temu. Mierniki o największych możliwościach pomiarowych charakteryzują się również coraz większą dokładnością i rozdzielczością, zbliżoną do sprzętu typowo laboratoryjnego, wykorzystywanego na przykład do wzorcowania.
Urządzenia instalowane na maszynach i na liniach produkcyjnych
Do tej grupy aparatury kontrolno-pomiarowej i automatyki zalicza się przede wszystkim systemy pomiarów wielkości elektrycznych, termometry, ultradźwiękowe czujniki napełnienia zbiorników i silosów, różnego rodzaju wagi tensometryczne, manometry i przepływomierze mierzące w sposób ciągły ciśnienie i przepływ medium procesowego w fazie ciekłej lub gazowej, a także czujniki położenia, czujniki ruchu i aparaturę optyczną oraz wizyjną, w tym kamery, mierzące wielkość i parametry części wytwarzanych na linii produkcyjnej.
W wypadku mierników elektrycznych, jest to sprzęt dostosowany zwykle do montażu na standardowej szynie DIN. Najczęściej spotykamy się z takimi miernikami jak woltomierze, amperomierze, analizatory sieci 1-fazowych i 3-fazowych, które pozwalają na ciągłe pomiary w czasie rzeczywistym głównych parametrów elektrycznych sieci takich jak: napięcia, prąd, częstotliwości, współczynnik mocy, moc czynną i bierną oraz energię aktywną i bierną, a także sprawdzają jakość dostarczanej do urządzeń produkcyjnych energii dzięki możliwości pomiarów THD.
Kolejną grupą urządzeń montowanych w systemach automatyki przemysłowej, które dostosowano do montażu w szafach sterowniczych są różnego rodzaju urządzenia pomiarowe wykorzystywane do monitoringu i regulacji temperatury. Korzystają one z szeregu czujników zewnętrznych i są wyposażone w całą gamę różnorodnych wejść sygnałowych, w tym wejść uniwersalnych, wejść termoparowych, złączy PT oraz analogowych wejść prądowo-napięciowych. Dzięki temu mogą one nie tylko mierzyć temperaturę w różnych punktach, ale również w pewnym zakresie sterować procesem technologicznym.
Internet Rzeczy, jego rola w pomiarach
Coraz częściej rolę aparatury kontrolno-pomiarowej w systemach automatyki przemysłowej przejmują urządzenia Przemysłowego Internetu Rzeczy (IIot) współpracujące bezpośrednio ze sterownikami PLC i komputerami przemysłowymi. Tego typu sensory wyposażone są standardowo w moduły komunikacyjne, najczęściej zgodne z przewodowym standardem Ethernet lub bezprzewodowym Wi-Fi, rzadziej Bluetooth. Dzięki temu mogą aktywnie wysyłać rejestrowane wartości pomiarów bezpośrednio do urządzeń nadrzędnych, takich jak specjalizowane sterowniki PLC czy komputery przemysłowe, które pełnią wówczas funkcję miernika realizującego pomiary w czasie rzeczywistym. Dzięki możliwości dwustronnej komunikacji sensor IIoT może wykonywać pomiar tylko na wyraźne żądanie odczytu wysłane przez element nadrzędny, co zmniejsza obciążenie sieci, a dodatkowo wydłuża czas pracy urządzenia, zwłaszcza jeśli zasilane jest z własnych akumulatorów lub baterii.
Dzięki wykorzystaniu czujników i urządzeń zgodnych z założeniami Przemysłowego Internetu Rzeczy można zbierać i rejestrować dane i informacje w czasie rzeczywistym na temat realizowanych procesów, operacji technologicznych i całej produkcji eliminując nie tylko braki, ale również sterując inteligentną fabryką. Zebrane w ten sposób dane pozwalają usprawnić działania, zoptymalizować dostawy i logistykę wewnątrzzakładową, dostosować produkcję do potrzeb konkretnego zamówienia, a także lepiej wykorzystać zasoby i poprawić jakość obsługi klienta. Co więcej, wykorzystanie elementów Internetu Rzeczy i funkcjonalności Inteligentnej Fabryki pozwala zminimalizować ryzyko wystąpienia awarii, co przyczynia się do zwiększenia kontroli nad całym procesem technologicznym i zmniejsza obciążenie Służb Utrzymania Ruchu.
Jeśli chodzi o koncepcję wykorzystania urządzeń pomiarowych zgodnych z założeniami Przemysłowego Internetu Rzeczy, to tak naprawdę idea sprowadza się do zastąpienia klasycznych czujników pomiarowych ich inteligentnymi odpowiednikami wyposażonymi w interfejsy komunikacyjne i systemy umożliwiające przechowywanie zarejestrowanych danych, a więc w pamięć własną, która nie musi być zbyt duża, jeśli informacje pomiarowe są wysyłane do urządzeń nadrzędnych w czasie zbliżonym do czasu rzeczywistego. Innymi słowy, inteligencja czujnika sprowadza się tu do wstępnego przetworzenia mierzonej wartości na sygnał cyfrowy, bądź liczbę odpowiadającą jego wartości, zarejestrowanie pomiaru w pamięci podręcznej i wysłaniu wartości pomiaru do urządzenia nadrzędnego za pomocą interfejsu komunikacyjnego.
Z punktu widzenia systemu AKPiA, wykorzystywane są tu dokładnie te same czujniki, które stosuje się w tradycyjnych systemach kontrolno-pomiarowych automatyki. Różnica tkwi w dodatkowym, inteligentnym interfejsie komunikacyjnym, który pozwala oddalić czujnik od miernika nawet o setki metrów. Miernikiem może być tu dowolny sterownik PLC lub komputer przemysłowy, który odbiera sygnały i wysterowywuje urządzenia wykonawcze. Dodatkowo odpowiada za przesyłanie informacji o wykonanych przez inteligentne sensory pomiarach do systemu nadzorującego pracę linii produkcyjnej, czy systemy sterowania maszyny bądź zrobotyzowanego gniazda. Informacje te mogą trafiać dalej do systemu SCADA odpowiedzialnego za realizację i monitoring całego procesu technologicznego, a stąd (po przetworzeniu) do systemu ERP lub BI przedsiębiorstwa.
Zaawansowane urządzenia muszą być proste i uniwersalne Obecnie rozwój aparatury kontrolno-pomiarowej zmierza w kierunku uniwersalności, prostej i szybkiej konfiguracji bez skomplikowanych modułów. Odchodzi się już od scenariusza, w którym klient otwierając katalog produktów miał do wyboru dziesięć różnych sond radarowych do pomiaru poziomu pracujących na trzech różnych częstotliwościach. Wybór konkretnego rozwiązania nie był prosty, a klient nie miał pewności, czy wybrał odpowiednią częstotliwość. Obecnie producenci starają się maksymalnie uprościć zarówno dobór urządzenia, jak i sam proces parametryzacji, a następnie uruchomienia. Dobrym przykładem jest nowa sonda radarowa VEGAPULS 6X, która nadaje się do wszystkich zastosowań, niezależnie od tego, czy mierzone medium jest ciekłe czy stałe, gorące, zimne lub o właściwościach agresywnych. Dzięki temu nie trzeba już wybierać spośród wielu różnych modeli sond. Uproszczenie zaczyna się już na etapie konfiguracji urządzenia. Na podstawie podanych parametrów i warunków procesowych konfigurator sam proponuje urządzenie pomiarowe dopasowane do konkretnych potrzeb. VEGAPULS 6X to pierwsza sonda na świecie, która w zależności od wymagań może zostać wyposażona w różne moduły i pracować na jednej z trzech częstotliwości – 80 GHz, 26 GHz lub 6 GHz. Prostsze jest także uruchomienie urządzenia na miejscu. Dotychczas musieliśmy ustawić aż piętnaście parametrów sondy radarowej, teraz jest ich tylko siedem. Nie potrzeba już też specjalnych modułów do ustawienia sondy. W przypadku czujnika z komunikacją Bluetooth wystarczy telefon, tablet lub laptop – wykorzystanie darmowego oprogramowania VEGA Tools lub PACTware pozwala sprawnie sparametryzować sondę. |
Pomiary elektryczne, magnetyczne, optyczne i inne
W przemyśle najczęściej dokonywanymi pomiarami są pomiary elektryczne i pomiary wielkości mechanicznych. Jeśli chodzi o te pierwsze, to oprócz standardowo wykonywanych pomiarów napięcia, natężenia prądu, rezystancji czy mocy w kluczowych dla procesu sterowania punktach związanych z zasilaniem urządzeń, wykonywany jest cały szereg pomiarów diagnostycznych. Mają one wykryć możliwość wystąpienia awarii, zanim ona rzeczywiście nastąpi.
Do tego typu pomiarów najczęściej stosuje się multimetry cyfrowe, które pozwalają na pomiar kilku fizycznych wielkości elektrycznych. Są to przede wszystkim pomiary prądów, napięć, rezystancji. W droższych, bardziej zaawansowanych modelach możliwy jest również pomiar częstotliwości, pojemności, mocy czynnej, biernej, pozornej i innych często nieelektrycznych wielkości takich jak temperatura czy wilgotność.
Nowoczesne, cyfrowe multimetry charakteryzują się możliwością automatycznej zmiany zakresów pomiarowych, dzięki czemu pracownik Służb Utrzymania Ruchu nie musi przewidywać, jaka może być wartość mierzonego parametru, tak aby nie uszkodzić urządzenia. Co więcej, automatyczna zmiana zakresów pomiarowych umożliwia na swobodne pomiary parametrów zarówno dla urządzeń elektronicznych, jak i energetycznych.
Uniwersalne multimetry pozwalają na wykonywanie pomiarów wartości rzeczywistych i skutecznych, a także wyposażone są we własną pamięć, co ułatwia gromadzenie danych pomiarowych i generowanie, w wypadku wyposażenia urządzenia w graficzny wyświetlacz, różnego rodzaju wykresów w czasie rzeczywistym dla mierzonych wielkości. Warto zauważyć, że niektóre zaawansowane multimetry z graficznym wyświetlaczem łączą w sobie również funkcję oscyloskopu. Tego typu sprzęt wykorzystywany jest najczęściej przez techników odpowiedzialnych za uruchomienie linii produkcyjnej i Służby Utrzymania Ruchu. Oczywiście, w zaawansowane modele w multimetrów wyposaża się również serwisantów uruchomiających linie produkcyjne czy dokonujących napraw maszyn i systemów automatyki na miejscu u klienta.
Wybór dostępnych na rynku multimetrów jest ogromy – od prostych urządzeń za kilkadziesiąt złotych, po bardzo precyzyjne urządzenia laboratoryjne czy sprzęt dopuszczony do pracy w atmosferze wybuchowej, czyli zgodny z wymaganiami ATEX. Ten ostatni wykorzystywany jest najczęściej w kopalniach i wszędzie tam gdzie mamy do czynienia z pyłem, a więc w młynach, elewatorach czy w elektrowniach opalanych węglem bądź miałem węglowym.
Innymi słowy, na rynku dostępne są modele gorsze i lepsze, bardzo dokładne i takie, których wskazania są obarczone sporym błędem. Bez problemu kupimy też model bardzo funkcjonalny, rozbudowany z graficznym wyświetlaczem i funkcją oscyloskopu czy charakterografu, jak i wyjątkowo proste i tanie modele. W sprzedaży są też wyjątkowo trwałe i odporne na przeciążenia modele oraz takie, które zabezpieczone są w podstawowy sposób, za to są bardzo tanie.
Producenci, dostępne na rynku multimetry dzielą na kilka segmentów. Pierwszy, to sprzęt o podstawowej funkcjonalności. Są to tanie modele o umiarkowanej dokładności i rozdzielczości. Dla użytkownika najważniejszy jest tutaj jednak stosunek jakości do ceny, tak aby sprzęt cechował się wystarczającą trwałością i odpornością na typowe przeciążenia.
Drugą grupę stanowią urządzenia bardziej zaawansowane. Są to typowe przemysłowe mierniki o większej dokładności pomiarowej i rozdzielczości, które realizują też więcej funkcji. Sprzęt ten zapewnia dokładny pomiar do 3, 4 miejsc po przecinku. Charakteryzuje się też szerszym zakresem pomiarowym, umożliwiającym mierzenie wielkości o niewielkich wartościach, a jednocześnie pozwala na prowadzenie pomiarów wielkości „energetycznych” związanych z trójfazowym napięciem zasilającym doprowadzonym do maszyn i urządzeń. Co ważne urządzenia przemysłowe spełniają też wyższe normy w zakresie bezpieczeństwa użytkowania i mają odporne na uszkodzenia mechaniczne obudowy, co jest niezbędne przy noszeniu ich w miejsce pomiaru przez SUR.
Do trzeciej kategorii zalicza się sprzęt laboratoryjny o największych możliwościach pomiarowych, bardzo wysokiej dokładności i rozdzielczości wynoszącej 6–8 cyfr lub więcej. Urządzenia te charakteryzują się dużymi możliwościami pomiarowymi i funkcjonalnością. Obecnie standardem jest wyposażenie miernika w wyświetlacz graficzny, często w moduł oscyloskopu i w gniazdo do podłączenia czujnika temperatury czy wilgotności, które służą np. do kompensacji prowadzonych pomiarów.
Mierniki cęgowe, pomiary rezystancji i uziemienia
W praktyce przemysłowej bardzo często stosuje się mierniki cęgowe, które są swego rodzaju rozwinięciem grupy multimetrów. Najważniejszą zaletą jest możliwość pomiaru wartości prądów w przewodach bez konieczności przerywania ciągłości obwodu elektrycznego. Nowoczesna aparatura tego typu umożliwia wykonywanie pomiarów nie tylko prądu mierzonego cęgami, ale też różnych wielkości elektrycznych, w tym częstotliwości, oraz wartości magnetycznych, jak natężenie pola czy strumienia magnetycznego. Co ważne, dobre mierniki cęgowe mogą mierzyć z dużą dokładnością prądy o niewielkiej, mikroamperowej wartości, zarówno dla prądu stałego, przemiennego, jak i przemiennego ze składową stałą. Bardziej zaawansowane modele poradzą sobie też z pomiarami wirowania faz.
Oddzielną grupę urządzeń pomiarowych stanowią mierniki rezystancji izolacji i uziemienia. Wykorzystywane w przemyśle mierniki izolacji pozwalają na pomiar rezystancji bardzo małym prądem, dzięki czemu mierniki te oferują zakres pomiarowy przekraczający nawet 100 GΩ. Wartość napięcia pomiarowego można wybrać z zakresu 50, 100, 250, 500 oraz 1000 V lub, w zależności od budowy miernika, w sposób płynny od 50 V do 1000 V, zwykle z dokładnością do 10 V. Pomiar prowadzony jest metodą dwu- lub trójprzewodową za pomocą specjalnego adaptera wpinanego do gniazda sieciowego.
Z kolei proste mierniki, które pozwalają na pomiar uziemień, przystosowane są do prowadzenia pomiarów metodą techniczną czyli metodą niskoczęstotliwościową. Pozwalają one na wykonanie pomiaru ciągłości połączeń ochronnych i wyrównawczych. Pomiar rezystancji przeprowadzany jest metodą dwuprzewodową (2p). W bardziej zawansowanych modelach przewidziano również możliwość pomiaru ciągłości połączeń wyrównawczych i ochronnych prądem 200 mA z funkcją autozerowania, zgodnie z normą PN-EN 61557-4.
Droższe, bardziej zaawansowane modele mierników uziemienia pozwalają na pomiar metodą techniczną trój- i czteroprzewodową (3p, 4p). W niektórych modelach pomiar jest przeprowadzany przy użyciu prądu o częstotliwości 125 Hz. W ten sposób uzyskano wysoki poziom odporności na zakłócenia pochodzące z sieci energetycznej. Urządzenia te standardowo oferują opcję związaną z możliwością pomiaru rezystywności gruntu i niskich rezystancji. W sklepach dostępne są też przyrządy przeznaczone do pomiarów uziemień w energetyce, gdzie zakres pomiarowy, zgodnie z normą PN-EN 61557, zaczyna się od 0,30 Ω.
Pomiary wielkości nieelektrycznych – temperatura
Aby maszyna lub linia produkcyjna prawidłowo działały, niezbędny jest też monitoring różnego rodzaju fizycznych wielkości nieelektrycznych. Nie chodzi tu jednak o same pomiary mechaniczne, ale pomiary takich wielkości fizycznych jak ciśnienie, temperatura czy szybkość przepływu. Na tej podstawie można już odpowiednio sterować elementami wykonawczymi maszyny, podzespołu linii produkcyjnej. W tej grupie wielkości fizycznych najczęściej monitoruje się temperaturę, ciśnienie, wilgotność, szybkość przepływu i poziom napełnienia zbiorników lub silosów.
Pomiar temperatury w warunkach przemysłowych może być prowadzony na dwa sposoby. Pierwszym z nich to prostsza i tańsza metoda kontaktowa, drugą są wszelkiego rodzaju metody bezkontaktowe. W pierwszym wypadku wykorzystuje się przede wszystkim wszelkiego rodzaju czujniki rezystancyjne nazywane termistorami oraz termopary. Zaletą pierwszej grupy czujników kontaktowych jest ich szeroka oferta obejmująca różnego rodzaju obudowy, sposoby montażu i podłączenia. Z kolei termopary sprawdzają się miejscach trudno dostępnych. Stosuje się je tam, gdzie panuje wysokie ciśnienie, np. wewnątrz elementów wykonawczych maszyn hydraulicznych lub w aplikacjach związanych z przetwórstwem tworzyw sztucznych przy pomiarach temperatury wtrysku.
Istotnym elementem biorącym udział w procesie pomiaru temperatury jest przetwornik. Jego zadaniem jest przetworzenie sygnału otrzymywanego z czujnika na sygnał elektryczny. Przetworniki produkowane są w najróżniejszych formach, począwszy od modułu montowanego fabrycznie w sterowniku, poprzez niezależne moduły przystosowane do montażu na szynie DIN, na tzw. modelach głowicowych skończywszy.
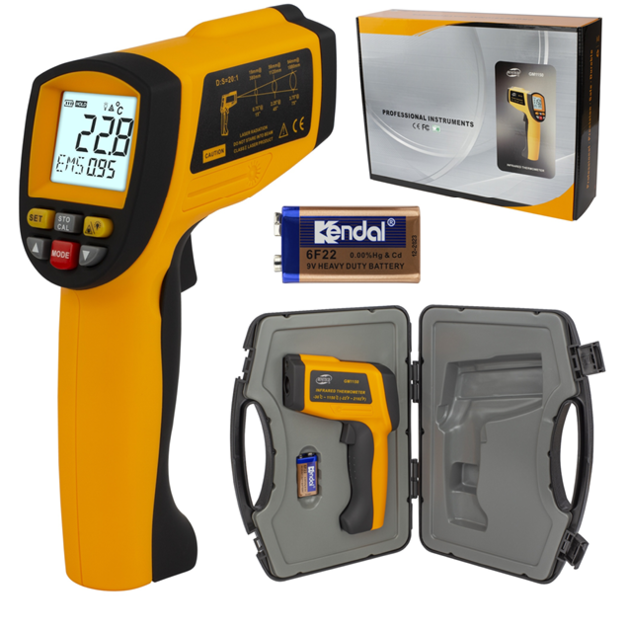
Ręczny laserowy pirometr Benetech GM1150 o zakresie pomiaru temperatury od –50 °C do +1150 °C z regulacją emisyjności
Pirometry i termowizja
Bezkontaktowe pomiary temperatury są realizowane za pomocą pirometrów lub kamer termowizyjnych. Ich zaletą, oprócz braku fizycznego kontaktu z mierzonym obiektem, jest możliwość kontroli temperatury w trudno dostępnych miejscach. Pomiary bezkontaktowe pozwalają też na bezproblemowy pomiar bardzo wysokiej temperatury panującej np. w wielkim piecu czy na walcowni, bądź wszędzie tam, gdzie temperatura może dochodzić do kilku tysięcy stopni.
Zazwyczaj za pomocą pirometrów mierzy się temperaturę w granicach od –65 °C do 1250 °C. Obudowa czujnika zapewnić może wysoki stopień ochrony IP, nawet do IP68, i pracę w atmosferze wybuchowej ATEX. Niektóre czujniki dostosowane są do wykrywania gorących obiektów w ruchu. Pirometry mogą występować jako oddzielne czujniki montowane na stałe na linii produkcyjnej, jak i w postaci przenośnego miernika z ekranem graficznym, gdzie pomiar wykonuje bezpośrednio człowiek.
Z kamer termowizyjnych korzysta się do prowadzenia pomiarów temperatury obiektów w ruchu lub do kontroli temperatury różnych, często wielkogabarytowych obiektów, w tym silników, transformatorów linii energetycznych, taśmociągów itp. Jak można się domyślić, kamery termowizyjne są bardzo chętnie stosowane przez Służby Utrzymania Ruchu. Zakres pomiarowy zależy od czujnika. Najlepsze modele pozwalają na pomiar temperatury od –120 °C do kilku tysięcy stopni, niemniej wykorzystuje się tu typowy zestaw kilku detektorów o różnym zakresie czułości temperaturowej – niestety, na jednym czujniku nie da się zapewnić tak szerokiej rozpiętości pomiaru temperatury.
Większość nowoczesnych kamer pozwala na automatyczne wyszukiwanie zimnych i gorących przedmiotów, rejestruje datę i czas pomiaru oraz korzysta z aplikacji do analizy zdjęć i tworzenia protokołów kontroli niezbędnych dla SUR. Coraz częściej standardem jest tu łączność bezprzewodowa umożliwiająca wysyłanie zdjęć wprost do smartfona lub firmowej infrastruktury IT.
Pomiary wizyjne
Pomiary wizyjne, w warunkach przemysłowych, wykorzystywane są najczęściej do pomiaru wielkości geometrycznychi kontroli jakości wykonania obiektów przemieszczających się pod obiektywem kamery wyposażonej w przetwornik CMOS. Jeśli chodzi o pomiary, to systemy wizyjne pozwalają na bezkontaktowy pomiar wielkości elementów o nietypowych kształtach, pomiary średnic otworów, pomiary szczelin, rowków czy kanalików w elementach formowanych maszynowo. Jednak o takie pomiary, jak wysokość wytłoczonego profilu, ilość produktów w trakcie wytwarzania, pozycjonowania i prowadzenie robota jest dziś ciągle bardzo trudne. Ograniczenia te nie są jednak związane z jakością metody, ponieważ kamery wizyjne mogą mieć wysoką rozdzielczość, ale możliwością zastosowania odpowiednich algorytmów przetwarzania obrazu i wynalezienia metody pomiarowej, która tak naprawdę nie została stworzona do zadań metrologicznych.
Pomiarowe systemy wizyjne wykonywane są na indywidualne zamówienia i jakość ich pracy oraz dokładność pomiarów zależy od zastosowanych algorytmów i mocy obliczeniowej, jaką można użyć do danego zadania. Często wykorzystuje się metodę triangulacyjną, która wymaga użycia kilku, przynajmniej trzech kamer CMOS o dużej rozdzielczości, co podnosi koszty stanowiska pomiarowego. Istotne jest też zapewnienie odpowiedniego oświetlenia.
Wysokiej jakości obiektyw, dobry element CMOS do tworzenia obrazu oraz zastosowanie mocnych procesorów sygnałowych DSP pozwala na bardzo szybki pomiar obrazu bez zniekształceń. Zastosowanie metody triangulacyjnej sprawia, że pomiarowe systemy wizyjne mogą być z powodzeniem wykorzystywane w zadaniach metrologicznych. Niestety, w warunkach przemysłowych wizyjne systemy pomiarowe wymagają co jakiś czas precyzyjnej kalibracji, co podnosi i tak niemałe koszty ich instalacji i późniejszej eksploatacji. Najważniejszą zaletą tego typu systemów jest szybkość działania i możliwość montażu bezpośrednio na stanowiskach obróbczo-transportowych.
Pomiary ciśnienia
Oprócz pomiarów ciśnienia dokonywanych za pomocą tradycyjnych czujników mechanicznych czyli różnego rodzaju manometrów, coraz częściej pomiary ciśnienia realizuje się przy użyciu czujników elektronicznych takich jak tensometry, czujniki piezorezystancyjne i pojemnościowe. Ich zaletą jest możliwość bezpośredniego wykorzystywania sygnału pomiarowego w układach rejestrujących i regulacyjnych, co dość mocno utrudnione jest w wypadku tradycyjnych manometrów, wymagających stosowania przetwornika.
Zasada działania tensometrycznych czujników ciśnienia bazuje na wykorzystaniu zjawiska zmiany rezystancji drutu oporowego na skutek przyłożonej do niego siły. W wypadku manometrów, tensometry montowane są na membranie, a jej odkształcanie pod wpływem ciśnienia wywieranego przez mierzone medium na membranę sprawia, że zmienia się również siła nacisku na czujnik. Prowadzi to do zmiany rezystancji drutu oporowego. Największą wadą tensometrycznych sensorów ciśnienia, jest duża zależność czułości i dokładności pomiaru od sposobu umieszczenia czujnika na powierzchni czynnej membrany, zaletą – wysoka odporność na wibracje i uderzenia.
W czujnikach piezorezystancyjnych siła przykładana jest wprost do krzemowej powierzchni sensora. W ten sposób uzyskano znaczną czułość oraz wysoką dokładność pomiaru ciśnienia. Ponadto właściwości fizykochemiczne krzemu pozwalają na pomiar bardzo małych ciśnień, rzędu pojedynczych milibarów. Wykonaną z krzemu membranę z naniesionym na niej za pomocą technik litograficzno-epitaksjalnych zestawem sensorów piezorezystancyjnych umieszcza się w hermetycznej obudowie. Przestrzeń między czujnikiem a zewnętrzną membraną wypełnia się cieczą manometryczną, którą najczęściej jest olej syntetyczny. Zewnętrzna membrana uginając się, napiera na olej, a ten na membranę czujnika. Wadą tego typu rozwiązań jest wpływ rozszerzalności temperaturowej cieczy na pomiary, dlatego minimalizuje się przestrzeń między zewnętrzną membraną a krzemową membraną czujnika.
Jak można się domyślić, zasada działania czujników pojemnościowych polega na zmianie pojemności. Cienka, krzemowa membrana umieszczana jest między okładzinami, tworząc w ten sposób kondensator. Ciśnienie medium, uginając membranę wpływa na pojemność tak zbudowanego kondensatora, która to pojemność przetwarzana jest na sygnał wyjściowy. Czujniki pojemnościowe są umieszczane w szczelnej obudowie wypełnionej olejem i wyposażonej w membranę wykonaną najczęściej ze stali nierdzewnej.
W tym miejscu warto podkreślić fakt, że standardowe przetworniki ciśnienia na wyjściu podają analogowy sygnał prądowy lub napięciowy, zaś programowalne, sygnał cyfrowy. Jak można się domyślić, wyposażone są one w przetwornik analogowo-cyfrowy oraz mikroprocesor, który też odpowiada za ewentualną kompensację pomiarową oraz wstępną obróbkę sygnału, tak aby bez problemu mógł być wysyłany do nadrzędnych elementów systemu automatyki.
Pomiary przepływu
Pomiary przepływu dotyczą przepływu gazów, cieczy oraz materiałów sypkich takich jak mąka, piasek, ziarno czy cement. Pomiary przepływu niezbędne są przede wszystkim we wszelkiego typu systemach dozujących oraz w gazociągach i rurociągach. Pozwalają one też kontrolować prawidłowość przebiegu procesu technologicznego i wykryć nieszczelności instalacji.
Istnieje kilka rodzajów przepływomierzy, które podzielić można na mechaniczne i elektryczne. Przepływomierze mechaniczne dzieli się na konstrukcje objętościowe, manometryczne, zmiennoprzekrojowe oraz przepływomierze z otwartym kanałem. W drugiej grupie wyróżnia się przepływomierze magnetyczne, impulsowe, ultradźwiękowe, Coriolisa i przepływomierze typu Vortex.
Objętościowe przepływomierze mechaniczne działają na zasadzie pomiaru szybkości napełniania i opróżniania określonej objętości. Najczęściej do odmierzanie gazów i paliw ciekłych stosuje się przepływomierze łopatkowe. W wypadku przepływomierzy manometrycznych w pomiarach wykorzystuje się zjawisko różnicy ciśnień między wejściem i wyjściem układu pomiarowego. Ich zaletą jest stosunkowo niska cena.
Przepływomierze zmiennoprzekrojowe, nazywane też rotametrami charakteryzują się stożkową budową i obecnością pływaka, którego położenia wyznacza aktualny przepływ. Stosuje się je zarówno do pomiaru przepływu cieczy, jak i gazów. Ostatnią grupę przepływomierzy mechanicznych stanowią przepływomierze z otwartym kanałem. Tutaj prędkość przepływu określa się na podstawie poziomu cieczy w pionowej rurce.
Przepływomierze elektryczne
Działanie przepływomierzy elektromagnetycznych opiera się na zjawisku indukcji elektromagnetycznej Faradaya. Przewodzące medium porusza się w rurociągu przez powierzchnię prostopadłą do kierunku pola magnetycznego generowanego przez cewki. Elektrody mierzą różnicę potencjałów proporcjonalną do prędkości przepływu.
Przepływomierze ultradźwiękowe dokonują pomiaru prędkości przepływu na podstawie pomiaru różnicy czasów przejścia fali ultradźwiękowej. Fala emitowana jest naprzemiennie między dwoma czujnikami pomiarowymi zamontowanymi na rurociągu. Mierzona różnica czasów przejścia jest proporcjonalna do prędkości cieczy w rurociągu.
Zaletą obu metod jest bezkontaktowy pomiar, brak spadku ciśnienia oraz możliwość ich wykorzystania do pomiaru przepływu materiałów sypkich. W tym ostatnim przypadku ultradźwięki można zastąpić promieniowaniem rentgenowskim.
Przepływomierze masowe, zwane też przepływomierzami Coriolisa wykorzystują siłę bezwładności czyli siłę Coriolisa, której kierunek wyznaczony jest przez iloczyn wektorowy prędkości liniowej i obrotowej. Wartość siły jest proporcjonalna do masy poruszającego się ciała oraz iloczynu wektorowego składowych prędkości. W przepływomierzu Coriolisa ruch obrotowy zastąpiono oscylacyjnym (drganiami) rury pomiarowej. Występujące w układzie bezwładności powodują opóźnienie fazy drgań rury w części dolotowej oraz jej przyspieszenie na odcinku wylotowym. Układ elektroniczny dokonuje pomiaru przesunięcia fazowego, i na tej podstawie określa wartość strumienia masy.
Zasada działania przepływomierzy typu Vortex, zwanych też przepływomierzami wirowymi wykorzystuje teorię ścieżki Karmana. Zgodnie z nią, po umieszczeniu w strudze płynu elementu o nieopływowym kształcie powstają naprzemienne wiry. Wiry te są proporcjonalne do natężenia przepływu medium. Częstotliwość występowania wirów jest powiązana bezpośrednio z prędkością mierzonego medium i średnicą czujnika.
Pomiary poziomu
Ostatnią, często wykorzystywaną grupą aparatury kontrolno-pomiarowej w przemyśle jest sprzęt do pomiaru poziomu. Pozwala on monitorować zarówno poziomu cieczy, jak i materiałów sypkich w różnego rodzaju zbiornikach i silosach, jak również bezpośrednio w systemach podawczych i transportowych. W pomiarach poziomu wykorzystuje się dwa typy czujników: kontaktowe i bezkontaktowe. Najprostszą metodą jest tu kontaktowa metoda mechaniczna realizowana za pomocą pływaka i ciężarka na lince. Jednak ze względu na dużą niedokładność, metoda ta stosowana jest coraz rzadziej i zastąpiły ją metody hydrostatyczne, ultradźwiękowe i laserowe, a także metody elektryczne.
Hydrostatyczne pomiary poziomu bazują na sprawdzaniu ciśnienia wytwarzanego przez słup cieczy, którą napełniany jest zbiornik. Dokładność pomiaru zależy wprost od dokładności wykorzystanego manometru. W wypadku pomiarów poziomu za pomocą lasera lub ultradźwięków, odpowiednie czujniki umieszcza się nad mierzonym medium, a ich kontakt z medium jest możliwy tylko w przypadkach awaryjnych. Pomiar odległości odbywa się na zasadzie znalezienia różnicy faz fali dźwiękowej lub świetlnej i na tej podstawie wyznaczana jest wysokość.
W wypadku pomiarów elektrycznych wykorzystuje się przede wszystkim metodę rezystancyjną i pojemnościową. Pierwsza z nich bazuje na wskazaniach sondy w postaci metalowego pręta. Przez pręt ten płynie prąd, o jego wielkość zależy od miejsca, do którego odsłonięty jest pręt, czyli od wysokości, do jakiej dochodzi medium w zbiorniku. Druga metoda polega na badaniu zmiany pojemności między sondą pomiarową a ścianką zbiornika.
Automatyczna analiza danych
Niezależnie od pomiaru i metody pomiarowej, dane przekazane przez systemy AKPiA muszą być w jakiś sposób przetworzone i opracowane. Najbardziej wygodną metodą opracowania i wizualizacji wyników pomiarowych są systemy SCADA. Pozwalają na bieżąco wizualizować parametry instalacji procesowej lub ilustrują działanie linii technologicznej i przekazują te dane do systemów IT przedsiębiorstwa – na przykład do systemu klasy ERP.
Obecnie do przetworzenia ogromnych ilości danych zbieranych przez czujniki IIoT pracujące w Inteligentnej Fabryce coraz częściej wykorzystuje się systemy uczenia maszynowego i algorytmy sztucznej inteligencji. Umożliwiają przetworzenie ogromnych ilości napływających w czasie rzeczywistym danych i analizę ich pod kątem możliwych zaburzeń procesu. Dzięki temu możliwe jest nie tylko elastyczne sterowanie produkcją, tak aby nie tworzyły się wąskie gardła, ale również przewidywanie nadchodzących awarii, tylko na podstawie zmian w aktualnych danych. Co więcej, systemy sztucznej inteligencji potrafią zaproponować rozwiązania zanim pojawią się kłopoty oraz podpowiedzieć, jak takie problemy rozwiązano w przeszłości i co można było zrobić lepiej. Ale to już temat na zupełnie inny artykuł.
źródło: Automatyka 9/2023
Komentarze
blog comments powered by Disqus