Przemysł 4.0 w praktyce
Marcin Bieńkowski drukuj
O Przemyśle 4.0 na łamach Automatyki pisaliśmy wielokrotnie. Koncepcja cyfrowej transformacji produkcji zdążyła już przez lata okrzepnąć, nie budzi już też kontrowersji wśród kadry kierowniczej i inżynierskiej przedsiębiorstw. Rozwiązania będące częścią cyfrowych założeń Industry 4.0, nie tylko są coraz częściej wdrażane w praktyce, ale zaczynają przynosić również wymierne korzyści. Przyjrzyjmy się zatem, jak czwarta rewolucja przemysłowa wygląda dzisiaj i w jaki sposób zaczyna oddziaływać na codzienne funkcjonowanie firm produkcyjnych.
Zachodzące gwałtownie na przełomie XX i XXI wieku procesy związane z cyfryzacją produkcji, logistyki, zbierania danych i przede wszystkim rozwój Internetu oraz mobilnej komunikacji zapoczątkowały próby usystematyzowania zachodzących zjawisk społeczno-technologicznych, nadania im kierunku, który pozwoliłby w przemyślany sposób dokonać cyfryzacji gospodarki. Jedną z takich prób sklasyfikowania i uregulowania cyfrowej transformacji przemysłu była zaproponowana przez niemieckich naukowców i inżynierów koncepcja Przemysłu 4.0. W 2011 r., decyzją niemieckiego rządu, stała się ona kluczowym elementem strategii innowacyjnego rozwoju naszego sąsiada zza Odry, która ma zapewnić gospodarce niemieckiej przewagę w zakresie nowoczesnych technologii.
Utworzona w wyniku tej decyzji grupa robocza „Industrie 4.0 Working Group” sformułowała pierwsze rekomendacje dotyczące implementacji koncepcji Przemysł 4.0 w praktyce. Dokumenty te ujrzały światło dzienne w kwietniu 2013 r., a opracowany dokument, zawierający ogólną wizję rozwoju przemysłu, stał się podstawą do opracowania przez „Plattform Industrie 4.0” ostatecznych zaleceń dotyczących urzeczywistnienia czwartej rewolucji przemysłowej. Zalecenia dotyczące ewolucji niemieckiej gospodarki przedstawiały śmiałą perspektywę rozwoju przedsiębiorstw funkcjonujących w cyfrowych sieciach obejmujących całe fabryki, maszyny, systemy magazynowe i urządzenia produkcyjne [1].
W ślad za Niemcami pojęcie Przemysłu 4.0 upowszechniło się w Europie, do czego w niemałym stopniu przyczyniły się, odbywające się co roku, targi przemysłowe w Hanowerze, gdzie koncepcja ta była szeroko propagowana. Warto w tym miejscu zaznaczyć, że w Stanach Zjednoczonych częściej mówi się o „inteligentnej produkcji” (Smart Manufacturing), a w Azji – o „inteligentnej fabryce” (smart factory). Wszędzie jednak chodzi o to samo zjawisko – przejściu od dominującej obecnie produkcji zautomatyzowanej do cyfrowej, inteligentnej produkcji umożliwiającej swobodne dostosowanie nawet jednostkowych wyrobów, pod konkretne potrzeby klienta.
Przejście między trzecią a czwartą rewolucją przemysłową ma charakter w dużej mierze inkrementalny (narastający – zachodzi stosunkowo powoli w wybranych obszarach) i jakościowy. Większość rozwiązań technologicznych niezbędnych dla Industry 4.0 funkcjonuje w obecnym modelu produkcji, który wyłonił się pod koniec lat 70. przy okazji ustępowania systemów analogowych na rzecz mikroelektroniki, półprzewodników, rozwiązań informatycznych i sieci. Ethernet, sensory, programy typu SCADA (Supervisory Control And Data Acquisition) w połączeniu z zaawansowaną analityką umożliwiały coraz szerszą automatyzację procesów wytwórczych, a także automatyzacje logistyki i projektowania [2].
Warto podkreślić, że Przemysł 4.0 wyróżnia sposób korzystania z danych, ich efektywne pozyskiwanie, przetwarzanie, wykorzystywanie w celu zoptymalizowania produkcji, sprzedaży i logistyki. To nie byłoby możliwe bez Internetu Rzeczy, chmury, sztucznej inteligencji, sensorów, kolejnych generacji robotów i rozwoju bezprzewodowej transmisji danych, w tym sieci komórkowych 5G. W efekcie dochodzi do zmiany paradygmatu produkcji, którego istotą nie są już linia produkcyjna czy nawet łańcuch wartości dodanej, ale o całościowe przetwarzanie nazywane coraz częściej datafikacją. Datyfikacja, będąca swego rodzaju integracją danych z urządzeń, czujników, systemów informatycznych i operacyjnych, pozwala na rozwój nowych rozwiązań w całym cyklu życia produktu – od jego zaprojektowania, produkcję, sprzedaż, używanie u klienta, serwisowanie, na utylizacji kończąc, a nie jak to miało miejsce w Przemyśle 3.0, skoncentrowaniu się wyłącznie na jego projektowaniu i produkcji [2].
Integracja danych i ich analiza w chmurze to przyszłość przemysłu Z Przemysłem 4.0 powiązanych jest wiele ciekawych rozwiązań. Ostatnie trendy wskazują na znaczny wzrost zainteresowania możliwościami podglądu oraz analizy kluczowych danych z dowolnego miejsca. Rozwiązaniem tego zagadnienia są systemy chmurowe, które oprócz gromadzenia danych zawierają narzędzia do łatwego tworzenia analiz, raportów, wizualizacji, pozwalające na ustawienie powiadomień o konkretnych zdarzeniach dla wybranych użytkowników. Systemy chmurowe mogą operować danymi pochodzącymi z systemów opartych np. na technologii RFID czy IO-Link, które pozwalają w wyraźny sposób optymalizować proces, jak i zwiększyć jego dokładność. Warto także wykorzystać możliwości oferowane przez systemy chmurowe w koncepcji predykcyjnego utrzymania ruchu. Dzięki dostępności odpowiednio przeanalizowanych danych użytkownik może reagować z wyprzedzeniem na wystąpienie potencjalnych zagrożeń, związanych z zakłóceniem ciągłości produkcji i łańcucha dostaw. Kolejnym tematem, na który warto zwrócić uwagę, jest integracja danych pochodzących z urządzeń znajdujących się na maszynie, z systemami nadrzędnymi. Idealnym rozwiązaniem jest wykorzystanie protokołu OPC UA, wspieranego przez coraz większą liczbę urządzeń, które nie zawsze są sterownikami PLC. Wdrażanie koncepcji Przemysłu 4.0 polega między innymi na integracji systemów działających bezpośrednio na obiekcie z oprogramowaniem skojarzonym z obsługą aplikacji biznesowych. Takie rozwiązania stają się coraz bardziej popularne. |
Datyfikacja i cyfrowy bliźniak
Z Przemysłem 4.0 związane są bardzo silnie dwa coraz częściej stosowane w opracowaniach pojęcia – wspomniana datyfikacja i cyfrowy bliźniak, zacznijmy jednak od cyfryzacji, nazywanej też digitalizacją i często mylonej z dygityzacją. Ta ostatnia to po prostu proces zamiany analogowych danych na ich cyfrowy odpowiednik, digitalizacja to zaś proces polegający na stosowaniu cyfrowych technologii do przetwarzania i obróbki danych. Innymi słowy dygityzujemy informacje, a digitalizujemy procesy, zarówno gospodarcze, społeczne jak i produkcyjne.
Warto w tym miejscu zauważyć, że często pojęcia digitalizacji i dygityzacji są mylone. Digitalizacją nazywa się błędnie, przekształcanie analogowego formatu danych na ich cyfrowy odpowiednik. Na szczęście w polskiej literaturze digitalizację procesów określa się zwykle terminem cyfryzacja, dzięki czemu szybko można się zorientować co jest pod tym terminem rozumie. Niestety, zamieszanie pojęciowe pogłębia fakt, że Komisja Europejska konsekwentnie używa pojęcia dygityzacji w rozumieniu cyfryzacji.
Wróćmy jednak do datyfikacji. Datyfikacja to po prostu proces pozyskiwania informacji poprzez tworzenie cyfrowych reprezentacji świata rzeczywistego (np. w wyniku digityzacji), przetwarzanie i łączenie (integrację) zbiorów danych oraz przez ich analizę z wykorzystaniem np. algorytmów sztucznej inteligencji. Technologie stosowane do gromadzenia, integracji i analizy danych określa się mianem technologii datafikacji.
Z kolei, cyfrowy bliźniak (digital twin) odnosi się do cyfrowej repliki fizycznych obiektów, procesów i systemów. Model digital twin to połączenie fizycznego obiektu oraz jego cyfrowego odwzorowania w przestrzeni wirtualnej, który realizowany jest dzięki możliwości przetwarzanie danych w czasie rzeczywistym i stałej aktualizacji stanu obiektów i procesów. Tyle teorii.
Zmiana ideologii procesów wytwarzania
Istotnym czynnikiem warunkującym przyspieszenie cyfryzacji procesów produkcyjno-biznesowych jest wzrost liczby dostępnych na rynku inteligentnych produktów, które wyposażone będą w czujniki zbierające dane na temat sposobu ich użytkowania w całym cyklu ich życia. Drugim elementem, na którym nie będziemy się szczegółowo skupiać, jest rozwój usług określanych mianem „Wszystko jako serwis” (Everything as a Service), dotyczacych subskrybowania lub krótkoterminowego wynajmu rzeczy, na przykład telewizji (Netflix), serwisów streamingowych z muzyką, dostępu do oprogramowania i baz danych a także samochodów, rowerów miejskich czy hulajnóg, które pozwalają śledzić globalne trendy dotyczące zachowań konsumenckich.
Zebrane w ten sposób dane pozwalają już dziś firmom ulepszać usługi i tworzyć bardziej atrakcyjną ofertę, która spełni oczekiwania klienta, a tym samym zbudować przewagę konkurencyjną na rynku. Pozyskiwanie i przetwarzanie danych z każdego etapu użytkowania produktu przez klienta w czasie rzeczywistym daje np. możliwość tworzenia cyfrowego bliźniaka – cyfrowej reprezentacji produktu, którą klient może w dowolny sposób rekonfigurować lub, jeszcze przed wyprodukowaniem, dostosować do swoich potrzeb już na etapie zamówienia.
![Rys. 2. Cyfrowy bliźniak, czyli odtworzony w zdigitalizowanym środowisku model rzeczywistego, systemu produkcyjnego, na którym można emulować zachowanie lini produkcyjnych, procesów wytwórczo-logistycznych czy przeprowadzać analizę zmian przed wdrożeniem ich do rzeczywistego środowiska [2] Rys. 2. Cyfrowy bliźniak, czyli odtworzony w zdigitalizowanym środowisku model rzeczywistego, systemu produkcyjnego, na którym można emulować zachowanie lini produkcyjnych, procesów wytwórczo-logistycznych czy przeprowadzać analizę zmian przed wdrożeniem ich do rzeczywistego środowiska [2]](/var/aol/storage/images/media/images/przemys__4_0_w_praktyce-2/883717-1-pol-PL/Przemys__4_0_w_praktyce-2_large.jpg)
Rys. 2. Cyfrowy bliźniak, czyli odtworzony w zdigitalizowanym środowisku model rzeczywistego, systemu produkcyjnego, na którym można emulować zachowanie lini produkcyjnych, procesów wytwórczo-logistycznych czy przeprowadzać analizę zmian przed wdrożeniem ich do rzeczywistego środowiska [2]
Inteligentne produkty pozwalają na tworzenie oferty komplementarnych produktów usług, prowadząc tym samym do wzmocnienia trendu serwicyzacji, definiowanego klasycznie jako „decyzja producenta o połączeniu produktów z usługami w celu zwiększenia zysków i poszerzenia pozycji w łańcuchu wartości”, a bardziej współcześnie – jako „innowacyjna zmiana potencjału i procesów w organizacji służąca wytwarzaniu wartości w wyniku przejścia od sprzedaży produktów do sprzedaży Systemów Produktowo-Usługowych (Product Service Systems, PSS). Serwicyzacja może też odnosić się do modeli biznesowych, które zakładają, wspomniany przed chwilą trend subskrybowania lub wynajmu produktu, bez przenoszenia prawa własności na użytkownika. Umiejętność czerpania wartości z danych w coraz większym stopniu decyduje o pozycji konkurencyjnej na rynku, zmieniając w rezultacie funkcjonowanie firm i całej gospodarki [2].
Transformacja cyfrowa przedsiębiorstw jest kluczowym, a zarazem problematycznym składnikiem całościowej transformacji cyfrowej gospodarki. Badania przeprowadzone w 2018 r. przez firmę McKinsey na próbie 1793 przedstawicieli firm z całego świata pokazują, że „udana transformacja cyfrowa jest trudniejsza niż jakikolwiek znany dotychczas rodzaj zmiany organizacyjnej”. Tylko 16 % respondentów uznało, że transformacja cyfrowa w ich firmach zwiększyła efektywność działania, a zmiany utrzymają się w dłuższej perspektywie. Dotyczyło to nawet firm działających w sektorach o wysokim poziomie ucyfrowienia (firmy technologiczne, medialne i telekomy), wśród których tylko co czwarta uznała, że transformacja była udana. W sektorach tradycyjnych (motoryzacyjnym, wydobywczym, budowlanym i farmaceutycznym) stopa sukcesu była jeszcze niższa i wahała się od 4 % do 11 %. Znacznie większą szansę na udaną transformację miały natomiast firmy mniejsze, zatrudniające do 100 pracowników. Kluczowymi determinantami sukcesu okazywały się: poziom adaptacji technologii cyfrowych, cyfrowe przywództwo (digital-savvy leaders), rozwijanie potencjału pracowników w zakresie kompetencji przyszłości i zachęcanie ich do pracy w nowy sposób, cyfryzacja podstawowych narzędzi i mechanizmów pracy oraz częsta komunikacja w obrębie firmy za pośrednictwem kanałów tradycyjnych i cyfrowych [2].
W które rozwiązania Przemysłu 4.0 warto zainwestować? Wśród rozwiązań promowanych w kontekście hasła Przemysł 4.0 znajdziemy autonomiczne wózki AGV, Przemysłowy Internet Rzeczy, szeroko rozumianą digitalizację oraz Sztuczną Inteligencję czy Uczenie Maszynowe. W które z tych rozwiązań inwestować? Oczywiście odpowiedź na to pytanie brzmi: „To zależy”. Wszelkie nowe trendy technologiczne pojawiające się w przemyśle mają na celu zwiększenie efektywności lub dostępności maszyn, zapewnienie łatwiejszego i tańszego ich serwisu lub poprawę jakości produktu. Pierwszym krokiem w planowaniu, powinna być wewnętrzna analiza rzeczywistych potrzeb zakładu, a następnie wybór tych rozwiązań, które mogą przynieść wymierne korzyści. Zdaniem Festo, jednym z ważniejszych rozwiązań jest Sztuczna Inteligencja. Jest to narzędzie, które udowodniło już swoją przydatność w naszym codziennym życiu – w postaci haseł podpowiadanych przez wyszukiwarki czy inteligentnych asystentów głosowych. Coraz śmielej wchodzi ono na hale produkcyjne, a Festo stara się być częścią tej rewolucji i rozwija Przemysłową Sztuczną Inteligencję w postaci systemu Festo AX. Bazując na analizie danych możliwe jest zarówno predykcyjne wykrycie awarii, nadzór nad zużyciem energii czy przyśpieszenie kontroli jakościowej produktu. Trzeba mieć jednak świadomość, że jest to narzędzie, które każdorazowo wymaga dostrojenia, a czasem dodatkowych inwestycji (niestety bez odpowiedniej ilości i jakości danych może nie udać się osiągnąć zamierzonego efektu). Zastosowane w odpowiedni sposób może jednak uchronić nas przed znacznie droższymi serwisami, nieprzewidzianym zatrzymaniem produkcji, czy potencjalnymi reklamacjami w przyszłości.Jeśli jednak wąskim gardłem produkcji jest np. logistyka zakładowa, wtedy zapewne inne rozwiązania z zakresu Przemysłu 4.0 mogą okazać się tymi bardziej odpowiednimi. |
Gdzie jesteśmy z przemysłem 4.0?
Podstawowym elementem, tworzącym wszelkiego typu systemy, które można określić mianem Industry 4.0 jest Przemysłowy Internet Rzeczy (Industrial Internet of Things, IIoT). Składa się on z różnego rodzaju elementów automatyki przemysłowej, tj. czujniki, systemy sterowania, sterowniki PLC, komputery przemysłowe, interfejsy HMI (Human-Machine Interface), a także centra obróbcze, roboty przemysłowe i szeroko pojęte systemy logistyki, wyposażone są w sensory zbierające dane, czy w elektronikę pozwalająca na wzajemną komunikację. Innymi słowy elementy te mogą zbierać i dzielić się zebranymi przez siebie elementami z otoczeniem, a także wykonywać napływające z sieci, adresowane do nich, rozkazy i polecenia, tzn.wchodzić we wzajemne interakcje.
Linearny, punktowy proces pozyskiwania i przetwarzania informacji, a następnie podejmowania na ich podstawie decyzji odnośnie procesów fizycznych, który był charakterystyczny dla Przemysłu 3.0, zostaje zastąpiony przez nieprzerwany, cykliczny proces zbierania, analizy i wykorzystania danych, który odbywa się w czasie rzeczywistym. Dane są gromadzone w obszarze całego łańcucha wartości, obejmującego środki produkcji, systemy magazynowe i sieci dostawców, i efektywne ich wykorzystanie. Przemysłowy Internet Rzeczy zastosowany w fabryce umożliwia stałe monitorowanie procesów produkcyjnych oraz dostosowanie planu konserwacji i serwisowania, a tym samym zapobiega awariom i związanym z nimi przestojom. Dzięki zintegrowaniu z systemami ERP, CRM, SCADA, systemami inżyniersko-projektowymi CAD oraz oprogramowaniem PLM możliwe jest stworzenie środowiska do zarządzania wszystkimi zasobami przedsiębiorstwa, a także do optymalizacji procesów produkcyjnych, projektowych, sprzedażowych, logistycznych i serwisowych, dzięki czemu możliwa jest optymalizacja wytwarzania w czasie rzeczywistym pod kątem maksymalnego wykorzystania mocy produkcyjnych, przestawiania linii technologicznych, a nawet wprowadzenia zindywidualizowanej produkcji pod konkretne zamówienie i oczekiwania klienta [1, 2].
![Rys. 3. Schemat działania systemuu FuelPrime, wykorzystującego Przemysłowy Internet Rzeczy, który wdrożony został w sieci stacji Shell na terenie Polski [5] Rys. 3. Schemat działania systemuu FuelPrime, wykorzystującego Przemysłowy Internet Rzeczy, który wdrożony został w sieci stacji Shell na terenie Polski [5]](/var/aol/storage/images/media/images/przemys__4_0_w_praktyce-3/883720-1-pol-PL/Przemys__4_0_w_praktyce-3_large.jpg)
Rys. 3. Schemat działania systemuu FuelPrime, wykorzystującego Przemysłowy Internet Rzeczy, który wdrożony został w sieci stacji Shell na terenie Polski [5]
Do najbardziej zaawansowanych systemów cyberfizycznych należą wspomniane cyfrowe bliźniaki, czyli cyfrowe repliki fizycznych obiektów lub produktów, a także procesów produkcyjnych, utworzone w oparciu o dane, które są na bieżąco dostarczane z wielu sensorów i systemów IT, w tym inżyniersko projektowych, czy systemów SCADA. Dane te są następnie przetwarzane w czasie rzeczywistym. Można tu posłużyć się środowiskiem chmurowym, jak i wydzielonymi serwerami, w tym serwerami brzegowymi, obsługującymi bezpośrednio proces produkcyjny. Do przetwarzania zebranych informacji stosuje się zarówno środowiska analitycze, w tym systemy klasy Business Inteligence, algorytmy sztucznej inteligencji, jak i analizę Big Data. Dzięki temu można bez problemu odwzorować każdy fizyczny i związany z zarządzaniem produkcją proces zachodzący w fabryce, a także modelować na bieżąco produkty dostosowywane do potrzeb klienta.
Technologia cyfrowego bliźniaka daje wgląd w specyfikę działania złożonych elementów maszyn i umożliwia testowanie ich funkcjonowania w zróżnicowanych warunkach. Pozwala też zoptymalizować plan napraw i konserwacji na podstawie bieżącej diagnozy zużycia części maszyn. Symulowane układy fabryczne pozwalają na lepsze zorganizowanie produkcji, a następnie wprowadzenie fizycznych zmian za pośrednictwem modułów i urządzeń wykonawczych. To wszystko sprzyja tworzeniu spersonalizowanego produktu i ułatwia konstruowanie prototypów, obniżając ich koszt za sprawą wirtualnych, szybkich i skalowanych testów. W konsekwencji zapewnia też optymalizację procesów decyzyjnych w produkcji, logistyce, sprzedaży i w usługach powiązanych [3].
W 2025 r. wartość rynku cyfrowych bliźniaków ma wynieść blisko 36 mld dolarów. W niedalekiej perspektywie model cyfrowego bliźniaka może zostać zastosowany w skali całego przedsiębiorstwa, a nie tylko maszyny, produktu czy wydzielonej linii produkcyjnej. Dzięki temu będzie można odwzorować cały proces funkcjonowania inteligentnej fabryki, i co najważniejsze, wraz z jej łańcuchem dostaw. Szacowano, że w 2020 r. aż 1/3 firm z listy Global 2000 będzie wykorzystywać dane pochodzące z cyfrowych bliźniaków oraz Przemysłowego Internetu Rzeczy [4].
Czy pandemia będzie miała wpływ na rozwój Przemysłu 4.0? Czas pandemii to okres niełatwych wyzwań niemal dla wszystkich uczestników rynku. W szczególności niepewność dotyka tych producentów, którzy wyroby swoje lokują jako dobra, niekoniecznie pierwszej potrzeby. Dla tej gałęzi przemysłu obecnie to moment wyzwań i podejmowania strategicznych decyzji biznesowych o kierunkach rozwoju i inwestycji. Nie wszystkie branże, mimo przewidywanego spowolnienia, zostały przymusowymi beneficjentami aktualnej sytuacji pandemicznej. Dla firm branży spożywczej czy farmaceutycznej to moment wzmożonego ruchu na produkcji. Na tym tle, odpowiedzią na obecne wyzwania może być niewątpliwie rozwój przedsiębiorstw w kierunku Przemysłu 4.0. Wydaje się, że czas pandemii, czyli dla niektórych firm pewnego spowolnienia, to dobry moment na inwestycje i rozwój, przy nietraceniu na przestojach linii spowodowanych ich modernizacjami czy inwestycjami w nowe węzły produkcji. Z drugiej strony, dla firm dobrze prosperujących, jest to czas wysokich przychodów, pozwalających na alokacje nadwyżek, także na inwestycje w moce produkcyjne, już w kierunku Przemysłu 4.0. W podsumowaniu odpowiedzi na pytanie, można zaryzykować tezę, że jednym z wygranych tego niełatwego czasu, będzie Przemysł 4.0, jako kierunek rozwoju firm produkcyjnych. Automatyzacja, robotyzacja coraz szerzej wchodząca do firm, staje się już i w naszym kraju pewnym standardem. Istnieje obiektywna potrzeba rozsądnie prowadzonych inwestycji w dobra produkcji, które przyniosą realne korzyści i pozwolą na wyróżnienie się na bardzo konkurencyjnych rynkach. Przemysł 4.0 jest właściwym kierunkiem, łączącym w sobie cechy samej warstwy wykonawczej automatyki i robotyki, wznosi je na wyższy poziom użyteczności, opartej w warstwie programowej na zaawansowanych rozwiązaniach komunikacji, archiwizacji, decyzyjności i wsparcia procesów elementami sztucznej inteligencji i operowania na wielkiej liczbie danych (big data). |
Systemy Przemysłowego Internetu Rzeczy
Nowoczesne firmy produkcyjne, które chcą wdrożyć koncepcję Industry 4.0, sięgają najczęściej właśnie po IIoT, przede wszystkim w celu uzyskania dokładnej analizy danych z urządzeń, które komunikują się ze sobą w czasie rzeczywistym (Online IIoT). Zasoby firmy, wytwarzane towary, dane, rynek i klienci stanowią ekosystem, który wymaga wydajnych środków dostępu i wymiany informacji [5]. Obecnie w większości nowoczesnych fabryk działają co najmniej elementy Przemysłowego Internetu Rzeczy. Czujniki przesyłają bowiem dane do nadzorujących ich kontrolerów, a te bardzo często, w ramach maszyny, gniazda produkcyjnego, czy linii wytwórczej, wchodzą ze sobą w interakcje. Dalej jest już różnie i nie zawsze zebrane informacje są gromadzone, czy przesyłane do systemów nadzorujących procesy biznesowe, zamówienia, logistykę czy sterujące fabryką jako całością.
Mówimy o stworzeniu ekosystemu IIoT dla rozwiązań, które charakteryzują się szerokim zakresem możliwości rozwoju (skalowania) zarówno sprzętowego, jak i programowego. Głównym składnikiem tego ekosystemu może być platforma IIoT. Łącząc platformę IIoT za pomocą komponentów sieciowych, takich jak koncentratory IoT (przekaźniki), sygnalizatory i znaczniki RFID (nadajniki), możliwe jest zapewnienie komunikacji w czasie rzeczywistym i zbieranie danych z maszyn oraz czujników. W ten sposób zapewniana jest kontrola i ciągłość dostępu do danych w całym łańcuchu produkcyjnym, od komunikacji między urządzeniami, przez linię montażową, aż po procesy zarządzania i dystrybucję produktów do klienta [5]
Jak wspomniano, systemy IIoT pozwalają na śledzenie procesów produkcyjnych i logistycznych oraz na reagowanie na zdarzenia produkcyjne, w tym na sytuacje krytyczne. Z punktu widzenia produkcji, zwłaszcza w wypadku kopalń, istotna jest kontrola wszelkiego rodzaju parametrów środowiskowych (np. temperatura, ciśnienie, wilgotność, zapylenie) i na tej podstawie zarządzanie brygadami górniczymi, maszynami i urządzeniami.
Przykładem może być e-kopalnia oferowana przez grupę Famur. System ten odpowiada za sterowanie i monitoring maszyn dołowych i jest to szereg współdziałających ze sobą rozwiązań informatycznych oraz sprzętowych, które odpowiadają m.in. za zdalne i lokalne sterowanie maszyn, agregację i transmisję danych, wizualizację, archiwizację, analizę danych wraz z generowaniem szczegółowych raportów oraz integrację z układami innych producentów. Głównym narzędziem dozoru jest oprogramowanie SCADA, łączące wiele maszyn i autonomicznych układów w spójny, wysokowydajny i niezawodny system wydobywczy. Dla przykładu operator kombajnu chodnikowego obserwuje z oddalonego stanowiska sterowania wirtualny model maszyny, dzięki któremu zna jej dokładne położenie, widzi aktualną pozycję głowicy urabiającej oraz ma do dyspozycji obraz z kamer wizyjnych. System ma również za zadanie odpowiednio wcześnie informować o zbliżającej się kolizji z elementami obudowy chodnikowej [6].
Przykładem może być też wdrożenie systemu IIoT, FuelPrime w sieci stacji benzynowych Shell w Polsce. System ten kontroluje paliwa płynne na każdym etapie dystrybucji, porównując różnice pojawiające się w procesach przelewania oraz monitoruje proces poboru paliw przez klientów z dystrybutorów na stacjach. Wysoką skuteczność uzyskano dzięki dokładnym czujnikom zaprojektowanym specjalnie do pomiarów paliw oraz dzięki metodzie opartej na analizie dużych zbiorów danych, tzw. Business Intelligence (BI). Serwer FuelPrime, umożliwia zarówno analizę bieżących danych jak też dostęp do danych historycznych oraz przesyła powiadomienia e-mail lub SMS o sytuacjach krytycznych, do których zalicza się próby ingerencji w urządzenia lub pojawienie się nieprzewidywalnego wypływu paliwa. W ten sposób uzyskano pełną kontrolę nad poziomem paliwa. System pozwala przewidywać konieczność zamówienia dostawy, wyeliminowano straty paliw płynnych oraz niepotrzebne transporty [5].
Dlaczego warto wdrażać rozwiązania Przemysłu 4.0 w firmach z sektora MŚP? Przypatrzmy się europejskim systemom płatności kartami. W Niemczech wciąż dominują płatności gotówkowe i stary system finansowy. Wszelkie badania wskazują na to, że w Polsce odrobiliśmy zadanie domowe i możemy dzisiaj powiedzieć, że jesteśmy zdecydowanie cyfrowi, jeśli chodzi o płatności. Kupiliśmy dobrą technologię, skutecznie edukowaliśmy społeczeństwo i efektywnie wykorzystaliśmy transformację cyfrową. Transakcje bezgotówkowe pomagają nam bezpiecznie i komfortowo żyć. Przed podobnym wyzwaniem stoi nasz przemysł. Analogicznie do cyfrowych systemów płatności, rozwiązania związane z czwartą rewolucją przemysłową dają nam szansę na skok technologiczny. Wiele zakładów w Polsce działa jeszcze w oparciu o manufakturę. Nie zdają sobie sprawy, że mogą nawet dziesięciokrotnie przyspieszyć proces produkcyjny. I to niewielkim kosztem. W APA Group już mamy doświadczenie i wiedzę jak tego dokonać. Chcemy się nią podzielić z polskimi zakładami produkcyjnymi m.in. zapraszając do uczestnictwa w projekcie NAZCA 4.0. To jest ten czas, aby podjąć decyzję o zmianie. Nowa droga nie jest tak kosztowna, jak mogłoby się wydawać, a inwestycja zwraca się w ekspresowym tempie. Istnieje wiele źródeł finansowania innowacyjnych projektów: Program Operacyjny Inteligentny Rozwój (POIR), Program Operacyjny Polska Wschodnia, Program Operacyjny Wiedza Edukacja Rozwój, czy Bony Innowacyjności. |
Robotyka
Trudno wyobrazić sobie funkcjonowanie fabryk zgodnych z założeniami Przemysłu 4.0 bez systemów zrobotyzowanych. Według danych International Federation of Robotics, liczba robotów pracujących w różnego rodzaju fabrykach i zakładach produkcyjnych wzrosła z 1,8 mln w 2016 r. do ponad 3 mln w 2020 r. Najwięcej z nich pracuje w przemyśle motoryzacyjnym, obecnie jest tam 923 tys. jednostek. Na drugim miejscu są firmy z sektora elektroniki i elektryki (627 tys.), podium zamyka przemysł mechaniczny – 281 tys. robotów.
Najczęściej wykonywanymi przez roboty przemysłowe pracami jest przenoszenie materiałów i załadunek, w tym, paletyzacja (ponad 1,2 mln robotów), spawanie (640 tys.) i montaż (287 tys.). Obok zrobotyzowanych gniazd produkcyjnych, charakterystycznych dla klasycznego przemysłu, w fabrykach zgodnych z założeniami Przemysłu 4.0, pojawiają się autonomiczne roboty mobilne (Autonomic Mobile Robots, AMR), wykorzystywane głównie w logistyce wewnętrznej, oraz roboty współpracujące (koboty, collaborative robots), stworzone w celu bezpośredniej współpracy z człowiekiem. Pierwszego kobota na rynek wprowadziła w 2008 r. firma Universal Robots. Obecnie koboty mogą wyręczyć robotników przy niebezpiecznych i nużących zadaniach, współpracując bezpośrednio z ludźmi na liniach produkcyjnych.
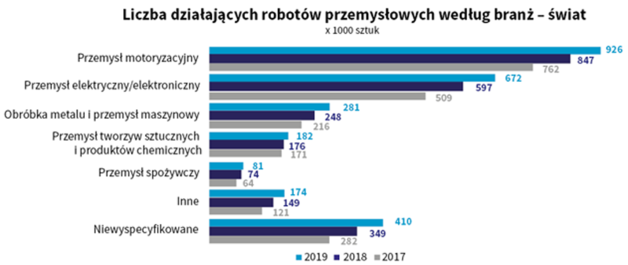
Rys. 4. Liczba robotów pracujących w poszczególnych sektorach przemysłu w latach 2017–2019. Źródło: International Federation of Robotics
Upowszechnianie kobotów jest przejawem rozwoju rekonfigurowalnych systemów produkcyjnych (Reconfigurable Manufacturing Systems) pozwalających na dopasowanie potencjału, funkcjonalności i wydajności infrastruktury produkcyjnej. Składają się one z modułów, które dzięki mechanicznej i informatycznej integracji można łatwo ze sobą łączyć, rozdzielać lub dodawać nowe, podczas gdy zintegrowany układ pomiarowy ocenia kondycję całego systemu. Mobilne i elastyczne roboty, uczące szybkiej i taniej rekonfiguracji linii produkcyjnych w celu wytwarzania krótkich serii odpowiadających na zmieniające się preferencje klientów. Długofalowo procesy technologiczne charakteryzujące Przemysł 4.0 umożliwią zaawansowaną personalizację produktu końcowego, dzięki wykorzystaniu sztucznej inteligencji, zwiększają możliwość szybkiej i taniej rekonfiguracji linii produkcyjnych w celu wytwarzania krótkich serii odpowiadających na zmieniające się preferencje odbiorców. Długofalowo procesy technologiczne charakteryzujące Przemysł 4.0 umożliwią zaawansowaną personalizację produktu końcowego [2].
Na jakie nowe rozwiązania Przemysłu 4.0 należy zwrócić uwagę? Rynek wymaga od producentów zdolności do szybkiego reagowania, m.in. elastycznego wprowadzania zmian w asortymencie lub skali produkcji, realizowania planów produkcyjnych w obliczu niedoborów kadr lub konieczności wprowadzania różnego rodzaju obostrzeń. Wiele firm w obliczu pandemii zostało zmuszonych do poszukiwania nowych metod produkcji zapewniających większą odporność na czynniki zewnętrzne, jak i gwarantujących większą efektywność kosztową. Poszukując rozwiązań najlepiej odpowiadających dzisiejszym potrzebom producentów przemysłowych warto zwrócić uwagę na innowacyjne rozwiązania techniczne, umożliwiające optymalizowanie parametrów produkcji w oparciu o dane. Przykładem mogą być systemy FANUC FIELD oraz ZDT, umożliwiające bieżące analizowania wskaźników obrazujących pracę maszyn i stanowisk produkcyjnych, prowadzenie diagnostyki predykcyjnej (minimalizowanie przestojów i kosztów eksploatacji) oraz wprowadzanie zmian do procesu produkcji w celu obniżania kosztów. Coraz popularniejsze stają się także koboty. Wyposażone w nowoczesne funkcje i systemy bezpieczeństwa umożliwiają bezpośrednią współpracę robotów z ludźmi. Takie jednostki są łatwe do wdrożenia (kompaktowe konstrukcje, zróżnicowane możliwości montażu, możliwość współpracy z platformami jezdnymi AGV) i obsługi (nowoczesne, intuicyjne interfejsy, funkcje ułatwiające obsługę i programowanie, np. funkcja ręcznego prowadzenia), są w stanie szybko dostosować się do zmieniającego się środowiska produkcyjnego i istotnie wspierać pracę ludzi na newralgicznych odcinkach linii. |
Podsumowanie
Koncepcja Przemysłu 4.0 już dziś budzi obawy o miejsce człowieka w przemysłowym wytwarzaniu produktów, a co za tym idzie o przełożeniu zmian społecznych na funkcjonowanie gospodarki. Do negatywnych skutków cyfryzacji produkcji zaliczyć można niepewność zatrudnienia, degradację zawodową wielu grup pracowników, rozwój nowych, niezależnych od człowieka mechanizmów kontroli, ograniczenie decyzyjności pracowników oraz nadmierne oczekiwania dotyczące produktywności siły roboczej – co gorsza, wszystkie te negatywne zjawiska zaczęły silnie narastać wraz z pojawieniem się pandemii COVID-19. Stąd też, coraz częściej w kręgach politycznych mówi się m.in. o gwarantowanym dochodzie podstawowym, który wyeliminuje problemy związane z brakiem możliwości zatrudnienia mniej wykwalifikowanych pracowników.
Do pozytywnych skutków Przemysłu 4.0 z pewnością zliczyć można wyeliminowanie pracy fizycznej, atrakcyjne warunki zatrudnienia dla specjalistów, możliwość rozwoju kompetencji jednostkowych poszczególnych pracowników, zwiększenie autonomii działania oraz rozwój samoorganizujących się i autonomicznych sieci współpracy.
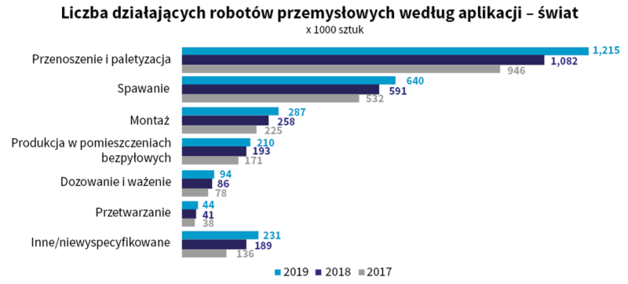
Rys. 5. Liczba robotów wykonujących najczęstsze rodzaje prac w latach 2017–2019. Źródło: International Federation of Robotics
Jak można się domyślić, humanizacyjną odpowiedzią na zagrożenie, jakie stanowi ograniczanie roli człowieka w Przemyśle 4.0 jest koncepcja Przemysłu 5.0, którą wprowadził w 2015 r. Michael Rada – prezes International Business Center of Sustainable Development. W koncepcji Industry 5.0 człowiek oraz maszyna tworzyć mają funkcjonalną całość, co ma też miejsce w przypadku Przemysłu 4.0 – choćby w przypadku wspomnianych przed chwilą kobotów.
Siłą napędową Przemysłu 5.0 mają być tzw. technologie kognitywne czyli umożliwiające rozpoznawanie przez maszyny otoczenia. W ten sposób maszyny i systemy automatyki, a nawet obrabiarki numeryczne, zyskają możliwość wykonywania zadań, które dotychczas zarezerwowane były wyłącznie dla ludzi. Przygotowanie maszyn do wykonywania nowych zadań, a także do działania w różnorodnych, zmieniających się środowiskach ma być możliwe dzięki sztucznej inteligencji i zaawansowanym algorytmom uczenia maszynowego. Kiedy to się stanie? Trudno powiedzieć, na razie wdrożyć trzeba założenia cyfrowej transformacji nie tylko w największych firmach, będących liderami Przemysłu 4.0, ale również w małych kilkuosobowych przedsiębiorstwach – a to może potrwać jeszcze nawet kilkanaście lat.
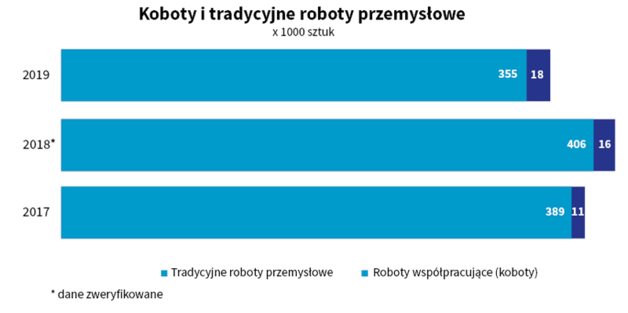
Rys. 6. Wzrost liczby sprzedanych kobotów w latach 2017–2019. Źródło: International Federation of Robotics
Literatura
[1] Jacek Bendkowski, Zmiany w pracy produkcyjnej w perspektywie koncepcji „Przemysł 4.0”, Zeszyty
Naukowe Politechniki Śląskiej 2017, Seria: Organizacja i Zarządzanie z. 112 Nr kol. 1990, s. 21–33
[2] Katarzyna Śledziewska, Renata Włoch, Gospodarka cyfrowa. Jak nowe technologie zmieniają świat, Wydawnictwo Uniwersytetu Warszawskiego, Warszawa 2020.
[3] Prezentacja firmy General Electric ”The Digital Twin, Compressing time-to-value for digital industrial companies”
[4] Raport IDC FutureScape: Worldwide IoT 2018 Predictions
[5] IoT w polskiej gospodarce – Raport grupy roboczej do spraw Internetu Rzeczy przy Ministerstwie Cyfryzacji
[6] Jerzy Dudała, Przemysł 4.0 na dobre się rozgościł, Biuletyn Górniczy nr 11–12 (267–268) Listopad–Grudzień 2017 r.
źródło: Automatyka 3/2021
Komentarze
blog comments powered by Disqus