Robotyka i sztuczna inteligencja w przemyśle
Marcin Bieńkowski drukuj
Sztuczna inteligencja (SI, z ang. Artifical Inteligence, AI) to ostatnio bardzo głośny temat. Media głównego nurtu budują wokół niego skrajne emocje – począwszy od zachwytu nad Chat GPT, po apokaliptyczną wizję katastrofy ludzkości, tak jak to miało miejsce z początkiem czerwca, gdy jeden z amerykańskich generałów ujawnił wyniki symulacji, w której dron „zabił” swojego operatora, gdyż ten przeszkadzał mu w wykonywaniu misji. Jednak SI, tak jak każda technologia, może zarówno nam zaszkodzić, jak i pomóc w codziennym życiu i pracy. Przyjrzyjmy się zatem do czego może przydać się SI w produkcji przemysłowej.
Podobnie, jak wcześniej automatyzacja i robotyzacja, sztuczna inteligencja ma za zadanie poprawić konkurencyjność przedsiębiorstwa dzięki poprawie procesów wytwarzania, ich dopasowaniu do spływających zamówień i optymalizacji zasobów, w tym eliminacji nieplanowanych przestojów. Sztuczna inteligencja pozwala też na wprowadzenie nowych usług i produktów, które będą w dużo większym stopniu dopasowane do zmieniających się potrzeb klientów. Odpowiednie algorytmy można też wykorzystać do analizy preferencji i zachowań użytkowników, co pozwoli w krótszym czasie na lepsze zrozumienie ich potrzeb i oczekiwań. Dzięki temu można wytwarzać dużo bardziej spersonalizowane produkty i oferować usługi, które w jeszcze większym stopniu trafią w gusta klientów, przez co wygenerują znacznie większe przychody.
Sztuczna inteligencja pozwala też na wdrażanie adaptacyjnych, elastycznych, dostosowujących się do potrzeb, i co najważniejsze, autonomicznych systemów technologicznych, które działają w środowisku Przemysłu 4.0 i Przemysłowego Internetu Rzeczy, rozwiązań opartych na cyfrowych danych. Do działania sterowanych sztuczną inteligencją systemów Przemysłu 4.0 niepotrzebny jest ciągły nadzór ze strony człowieka. Dzięki temu możliwa staje się zaawansowana automatyzacja sterowana sztuczną inteligencją.
Jednocześnie zarządzanie przez algorytmy SI zbieranymi w „w locie” danymi pozwala na dużo bardziej sprawne podejmowanie decyzji w czasie rzeczywistym. Mogą one dotyczyć zarówno procesów produkcyjnych, działania maszyn, jak i przewidywania zdarzeń i zapobiegania awariom. Z kolei przetwarzanie danych na temat stanu surowców i produktów pozwala na lepsze zarządzanie łańcuchami dostaw i gospodarką magazynową. Możliwe jest też dokładne modelowanie kosztów wytwarzania i logistyki z nią związanych.
Jak wykorzystać sztuczną inteligencję w produkcji?
Wykorzystanie sztucznej inteligencji w przemyśle ma ogromny, jeszcze często niedoceniany i nieuświadamiany potencjał. Wiele możliwych zastosowań nie zostało jeszcze w ogóle skonkretyzowanych i zależy wręcz od pomysłowości i inwencji wdrażających dane rozwiązanie inżynierów. Obecnie wyróżnić można pięć głównych obszarów zastosowań sztucznej inteligencji w przemyśle:
- sterowanie i automatyzacja procesów produkcyjnych,
- prognozowania jakości i wydajności, czyli analiza predykcyjna produkcji,
- konserwacja predykcyjna,
- zarządzanie zapasami,
- optymalizacja łańcucha dostaw.
Zacznijmy od sterowania i automatyzacji procesów produkcyjnych. Pod pojęciem sztucznej inteligencji „na produkcji” kryją się wszelkiego rodzaju inteligentne maszyny i inteligentne systemy automatyki przemysłowej, które pozwalają na automatyczne i autonomiczne wykonywanie zadań związanych ze sterowaniem, kontrolą i nadzorem, w taki sposób, jakby robiłby to w mający ogromne doświadczenie pracownik. Innymi słowy, obrabiarki czy linie technologiczne samodzielnie reagują, bez udziału operatora, na wszelkie planowane i nieplanowane zdarzenia produkcyjne, rozwiązują pojawiające się problemy, a także mogą wykrywać z wyprzedzeniem nadchodzące nieprawidłowości i zareagować na nie. Potrafią też samodzielnie, bez udziału człowieka, obsłużyć wszelkiego rodzaju sytuacje awaryjne.
Klasyczna automatyzacja produkcji niskoseryjnej często może być nieopłacalna ze względu na krótkie cykle produkcyjne i wysokie koszty przezbrojeń i każdorazowego przeprogramowania maszyn. Inteligentne maszyny czy zrobotyzowane gniazda produkcyjne oparte na SI mogą wyeliminować konieczność ich przeprogramowania, skracając czas i redukując koszty rekonfiguracji linii produkcyjnej. Wykorzystując techniki uczenia maszynowego, które zasilane danymi z rzeczywistego procesu produkcyjnego, np. pochodzące z systemu widzenia maszynowego, nieustannie uczą się reagować na zmienne parametry produkcji, w tym na przezbrojenia. Dzięki temu zaangażowanie pracowników w sterowanie procesem produkcyjnym zostaje ograniczone do minimum, a działanie linii produkcyjnej oraz całego procesu produkcyjnego jest zachowane w sposób płynny.
Co więcej, wykorzystanie głębokiego uczenia pozwala na stworzenie zrobotyzowanych systemów, które, podobnie jak człowiek, mają możliwość wspomnianego widzenia, a także czucia, dotyku czy orientacji w przestrzeni. Dzięki temu system taki potrafi rozróżniać obiekty i autonomicznie podejmować nawet dość skomplikowane decyzje. Zdolność dotyku pozwala zaś na łatwe manipulowanie rzeczami delikatnymi lub kruchymi bez obawy o ich uszkodzenie.
Nowoczesne rozwiązania produkcyjne bazujące na sztucznej inteligencji lub wyposażone w jej elementy są w stanie znacząco wesprzeć obsługę konkretnych procesów wytwórczych oraz zredukować liczbę potencjalnych błędów. Czujniki, dające sztucznej inteligencji wgląd w przepływy materiałowe i procesy technologiczne, pozwalają na podejmowanie dobrych decyzji w czasie rzeczywistym i gwarantują płynność działania linii technologicznej czy maszyny w nagłych sytuacjach awaryjnych.
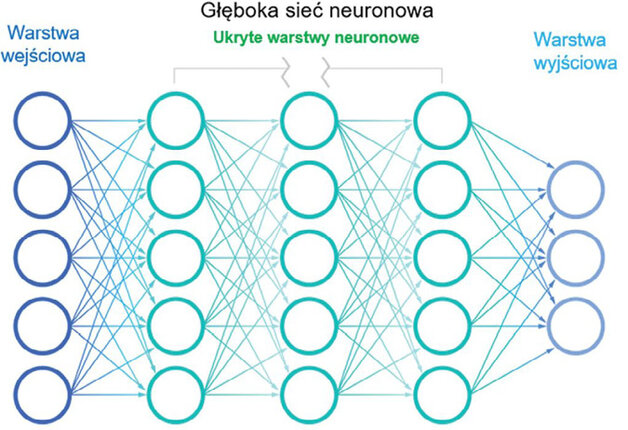
Architektura sieci neuronowej głębokiego uczenia, będącego podobszarem uczenia maszynowego – Andrzej Klimpel, Politechnika Śląska, Stal 2–4 2023
Predykcja i prognozowanie
Jeśli chodzi o prognozowanie jakości i predykcję produkcji, to sztuczna inteligencja może odgrywać istotną rolę przy kontrolowaniu przebiegu całego procesu technologicznego, który, przy współpracy z czujnikami Przemysłowego Internetu Rzeczy generuje ogromne ilości danych. Co więcej, współczesne oprogramowanie sterujące produkcją, takie jak np. systemy SCADA wspiera wykrywanie i analizę i przyczyn strat. Zastosowanie w nim algorytmów SI analizujących poszczególne procesy jest w stanie zaalarmować nas o zbliżających się problemach.
Generalnie celem predykcji jest przewidywanie, na postawie nadchodzących danych, awarii i alarmowanie o nich pracowników. Wykorzystywanie sztucznej inteligencji w produkcji może też zapobiec wtórnym uszkodzeniom linii technologicznej, a cały proces może działać bez niepotrzebnych przerw konserwacyjnych. Jednym z ważniejszych zagadnień jest oszacowanie czasu maksymalnej wydajności maszyn, czasu bezawaryjnego działania oraz dobór takiej częstotliwości prac konserwacyjnych, aby uniknąć nieoczekiwanych awarii sprzętu.
Możliwość przewidywania pozostałego okresu użytkowania części lub zasobu na podstawie danych w czasie rzeczywistym pozwala na optymalizację zasobów serwisowych. Na podstawie pomiarów SI może oszacować, kiedy dany podzespół może ulec awarii i zaplanować tak prace konserwacyjne, aby można było je wykonać tuż przed wystąpieniem zdarzenia. Wiedząc, kiedy dana część ulegnie awarii, można zaplanować prace konserwacyjne tylko wtedy, gdy jest to rzeczywiście potrzebne, jednocześnie unikając nadmiernej konserwacji i zapobiegając nieoczekiwanej awarii sprzętu. W predykcji wyróżnia się trzy główne elementy systemu automatyki, które pozwalają na śledzenie stanu zasobów w czasie rzeczywistym oraz umożliwiają przewidzenie awarii sprzętu z wyprzedzeniem [1]:
1. Zainstalowane czujniki monitorujące wysyłają w czasie rzeczywistym dane dotyczące wydajności i stanu maszyny. Czujniki te mogą mierzyć wielkości elektryczne, wibracje, temperaturę, ciśnienie, poziom oleju, hałas, poziom korozji oraz wiele innych parametrów. Dodatkową zaletą stosowania czujników monitorujących stan jest możliwość dokładnego odwzorowania tego, co dzieje się wewnątrz danego elementu lub samej maszyny, bez jakichkolwiek zakłóceń procesu produkcyjnego.
2. Internet Rzeczy, który umożliwia komunikację między maszynami i ich elementami, pomaga w gromadzeniu i analizowaniu ogromnych ilości danych. Ważnym czynnikiem jest tu połączenie komponentów i zasobów z centralnym systemem, który przechowuje i przetwarza napływające informacje. Dzięki temu elementy systemu automatyki sterowanego sztuczną inteligencją mogą się komunikować, współpracować, analizować dane, zalecać działania naprawcze lub bezpośrednio podejmować odpowiednie działania bez udziału operatora.
3. Algorytmy predykcyjno-prognostyczne. Sposób ich działania musi uwzględniać wiele różnych zmiennych oraz ich wzajemne powiązania, tak aby można było przewidzieć nadchodzącą awarię. Im więcej zmiennych zostanie użytych, tym dokładniejsze będzie działanie systemu, dlatego budowanie modeli predykcyjnych jest procesem iteracyjnym. W uproszczeniu opracowane modele:
- przestrzegają zestawu z góry określonych reguł, które porównują obecne zachowanie systemu z jego oczekiwanym zachowaniem,
- informują o każdej anomalii, która wskazuje na stopniowe zużywanie się elementu, co w konsekwencji może doprowadzić do jego uszkodzenia,
- na podstawie nieprawidłowości, bieżących warunków pracy, danych dotyczących wcześniejszych awarii i wszystkich innych zmiennych wbudowanych w model danych, algorytmy próbują przewidzieć punkty awarii.
Efektem końcowym jest autonomiczny system, który monitoruje warunki pracy za pomocą zainstalowanych czujników, rozumie i przewiduje wzorce tworzone przez anomalie danych, tworzy ostrzeżenia w przypadku odchylenia od ustalonych progów poprawnej pracy [1].
Jakie korzyści przynosi, a jakie zagrożenia powoduje robotyzacja? Argumentami przemawiającymi za robotyzacją są przede wszystkim korzyści ekonomiczne. Poprawa kluczowych parametrów, takich jak: wydajność, jakość i powtarzalność, decyduje o możliwości ograniczenia liczby reklamacji, redukcji jednostkowych kosztów produkcji, a także o wzroście produktywności i poziomie zysków z produkcji. Producenci, którzy zdecydowali się na inwestycję w tę technologię doceniają fakt, że roboty poza niezawodnością działania gwarantują oszczędności kosztów energii, przestrzeni w halach produkcyjnych oraz środków produkcji, a także znacznie przyczyniają się do ustabilizowania i zwiększania przewidywalności produkcji. W obecnych czasach, gdy przemysł zmaga się z problemem niedoboru kadr, firmy zaczynają postrzegać roboty jako jedno z najlepszych i stosunkowo łatwo dostępnych rozwiązań umożliwiających realizację planów produkcyjnych. Producenci zwracają uwagę także na elastyczność stanowisk zrobotyzowanych, co zapewnia możliwość szybkiego przezbrajania linii produkcyjnej, dostosowując ją do wytwarzanego asortymentu, odpowiadającego bieżącym zamówieniom. Warto wspomnieć również o tym, że roboty przyczyniają się do podniesienia kultury technicznej zakładów i rozwoju kompetencji personelu fabryk. Roboty otwierają przed producentami nowe możliwości rozwoju produkcji, zarówno w obszarze poszerzania asortymentu o nowe lub ulepszone produkty, jak i zwiększania mocy przez rozbudowę linii produkcyjnych. Zagrożenia wiążą się głównie z niewłaściwym lub pominiętym etapem przygotowań do wdrożenia stanowiska zrobotyzowanego. W celu zagwarantowania wysokiego poziomu efektywności, a także oczekiwanych korzyści konieczne jest precyzyjne zdefiniowanie zadań stawianych przed robotem, określenie oczekiwań co do efektów jego pracy (w postaci konkretnych liczb), a także podjęcie odpowiednich kroków projektowych i testowych przed wyborem docelowego typu i modelu robota, aby mieć pewność, że technicznie spełni on swoje zadanie. |
Zarządzanie zapasami
Systemy zarządzania produkcją wspomagane algorytmami SI zaprząc można również do procesu obniżania kosztów utrzymania zapasów. Dzięki kontrolowaniu stanu magazynów, AI może przewidywać braki zasobów, zanim te się pojawią. Co więcej, sztuczna inteligencja może nie tylko kontrolować stan zapasów, ale również zużycie energii i surowców stosowanych w produkcji. Dzięki ciągłemu zbieraniu informacji i analizie danych, algorytmy SI mogą wspierać podejmowanie decyzji optymalizujących wszystkie procesy logistyczne. Do najważniejszych korzyści płynących z zastosowania sztucznej inteligencji w łańcuchach dostaw zaliczyć można [2]:
Dokładne zarządzanie zapasami – precyzyjne zarządzanie zapasami może zapewnić właściwy przepływ towarów do i z magazynu. Ogólnie rzecz biorąc, istnieje wiele zmiennych związanych z zapasami, takich jak przetwarzanie zamówień, kompletacja i pakowanie, co może być bardzo czasochłonne i obarczone dużą skłonnością do błędów.
Wydajność magazynu – sprawnie działający magazyn jest integralną częścią łańcucha dostaw, a automatyzacja może pomóc w terminowym pobraniu towaru z magazynu i zapewnić jego bezproblemową drogę do klienta. Systemy sztucznej inteligencji mogą również rozwiązać wiele problemów związanych z magazynem szybciej i dokładniej niż człowiek, a także uprościć złożone procedury i przyspieszyć pracę. Oprócz oszczędności cennego czasu, automatyzacja oparta na sztucznej inteligencji może znacznie zmniejszyć zapotrzebowanie na pracowników magazynu.
Większe bezpieczeństwo – zautomatyzowane narzędzia oparte na SI mogą zapewnić inteligentniejsze planowanie i efektywne zarządzanie magazynem, co może zwiększyć bezpieczeństwo pracowników i materiałów. Sztuczna inteligencja może analizować dane dotyczące bezpieczeństwa w miejscu pracy i informować producentów o wszelkich możliwych zagrożeniach. Może rejestrować parametry magazynowe i aktualizować operacje wraz z niezbędnymi pętlami informacji zwrotnej i proaktywną konserwacją. Pomaga to producentom reagować szybko i zdecydowanie w celu utrzymania bezpieczeństwa w magazynach i zgodności z normami bezpieczeństwa.
Obniżenie kosztów operacyjnych – od obsługi klienta po magazyn, zautomatyzowane inteligentne operacje mogą działać bezbłędnie przez dłuższy czas, zmniejszając liczbę błędów i incydentów w miejscu pracy. Roboty magazynowe zapewniają większą szybkość i dokładność, osiągając wyższy poziom wydajności.
Dostawy na czas – systemy sztucznej inteligencji mogą pomóc w zmniejszeniu zależności od czynności wykonywanych ręcznie, dzięki czemu cały proces jest szybszy, bezpieczniejszy i bardziej inteligentny. Ułatwia to terminową dostawę do klienta zgodnie z podjętym zobowiązaniem. Zautomatyzowane systemy przyspieszają tradycyjne procedury magazynowe, usuwając w ten sposób wąskie gardła operacyjne w całym łańcuchu dostaw przy minimalnym wysiłku w celu osiągnięcia celów związanych z dostawą.
Cyfrowy bliźniak, sieci neuronowe, machine learning i deep learning
Od strony technicznej, zagadnienia związane ze sztuczną inteligencją wykorzystywaną w przemyśle obejmują sieci neuronowe (neural networks), modelowanie działań w strukturze cyfrowego bliźniaka (digital twin, digital twins framework), uczenie maszynowe (machine learning), głębokie uczenie (deep learning) oraz wnioskowanie (gathering), czyli elementy zbieżne ze standardowymi systemami sztucznej inteligencji, takimi jak popularny Chat GPT.
Cyfrowy bliźniak jest cyfrową reprezentacją, czyli cyfrowym modelem rzeczywistego obiektu, np. maszyny, linii produkcyjnej, zrobotyzowanego gniazda lub szerzej procesu produkcyjnego, który charakteryzuje się nie tylko tymi samymi elementami czy podzespołami, ale również takim samym zachowaniem i odpowiedzią na warunki zewnętrzne, jak jego fizyczny odpowiednik. Innymi słowy, zawiera w sobie wszystkie niezbędne informacje oraz dane pozwalające na scharakteryzowanie w sposób dynamiczny fizycznych cech systemu automatyki, maszyny, gniazda produkcyjnego czy linii technologicznej. Informacje te obejmują kombinację metadanych (klasyfikacja, skład, struktura itp.), warunków lub stanów (lokalizacja, temperatura), danych zdarzeń (szeregi czasowe) i informacji analityczno-modelowych, niezbędnych do analizy zdarzeń i ich symulacji (algorytmy i reguły, zasady postępowania itp.).
Cyfrowe bliźniaki mogą w czasie rzeczywistym zapewnić kompleksowe monitorowanie i digitalizację fizycznych elementów infrastruktury produkcyjnej oraz przenieść ich reprezentację do wirtualnej symulacji, na której można realizować w czasie rzeczywistym różnorodnych eksperymentów i analiz. Co więcej, analizy te mogą być prowadzone na podstawie napływających na bieżąco danych z rzeczywistego systemu produkcyjnego czy maszyny, a więc mogą być wykorzystane do emulacji sterowania procesem technologicznym. Modele cyfrowego bliźniaka są stosowane w celu lepszego poznania stanu obiektu lub systemu, przyspieszenia jego reakcji na zmiany, poprawy działań i wzrostu wydajności. Wpływają na usprawnienie systemu podejmowania decyzji, umożliwiają rozwój nowych procesów biznesowych sterowanych zdarzeniami oraz modeli biznesowych i ekosystemów z cyfrowym dostępem [3].
Mając do dyspozycji cyfrowego bliźniaka, który z dostateczną dokładnością odzwierciedla zachowania rzeczywistego systemu produkcyjnego, można przejść do analizy jego zachowań i nauczenia sztucznej inteligencji, w jaki sposób ma reagować na zachodzące w rzeczywistym środowisku produkcyjnym zdarzenia. Aby to osiągnąć, stosuje się algorytmy uczenia maszynowego i głębokiego uczenia. Na tej podstawie sztuczna inteligencja może już dokonać oceny sytuacji (wnioskowania) i automatycznie wysłać odpowiednie sygnały sterujące do systemu automatyki wymuszając odpowiednią reakcję maszyny czy linii technologicznej na zaistniałą sytuację – a wszystko to bez jakiegokolwiek udziału operatora.
W tym miejscu należy kilka słów poświęcić uczeniu maszynowemu i uczeniu głębokiemu. Otóż uczenie maszynowe to technika stosowana w systemach SI pozwalająca wykorzystać napływające dane do stopniowego poprawiania dokładności działania systemu, a więc do „zdobywania doświadczenia”. Algorytmy uczenia maszynowego budują model matematyczny na podstawie przykładowych danych zwanych zbiorem uczącym. Na tej podstawie algorytmy SI uczą się prognozowania lub podejmowania decyzji, i co ważne bez wcześniejszego zaprogramowanym explicite tych algorytmów przez człowieka.
Głębokie uczenie jest podkategorią uczenia maszynowego, która polega na tworzeniu w trakcie procesu uczenia głębokich sieci neuronowych czyli sieci z wieloma poziomami neuronów. Dzięki temu możliwe jest stworzenie generatywnej sztucznej inteligencji, która może automatycznie przetwarzać polecenia, obrazy, a nawet rozumieć język naturalny. Proste sieci neuronowe można zaprojektować „ręcznie”, by konkretna warstwa wykrywała konkretne cechy w strukturze danych, a uczenie się polega na ustaleniu odpowiednich wag dla danych, na podstawie których podejmowane mają być konkretne decyzje.
W dużych sieciach neuronowych proces głębokiego uczenia jest do pewnego stopnia samodzielny. To znaczy sieć nie jest projektowana pod wykrywanie konkretnych cech, leczy wykrywa je na podstawie przetwarzana odpowiednio oznaczonych zbiorów danych. Zarówno takie zbiory jak i sam sposób działania sieci muszą być odpowiednio przygotowane, na przykład na podstawie rzeczywistych danych z systemu produkcyjnego, ale cechy, np. anomalie wykrywa już sam program. Dzięki temu możliwe jest przetworzenie wielkiej ilości danych, a sieć może automatycznie nauczyć się reprezentacji cech wyższego poziomu, co oznacza, że mogą one wykryć skomplikowane wzorce w danych wejściowych. W ten sposób system sterowania procesem produkcyjnym może uczyć się na podstawie własnego przetwarzania danych [4].
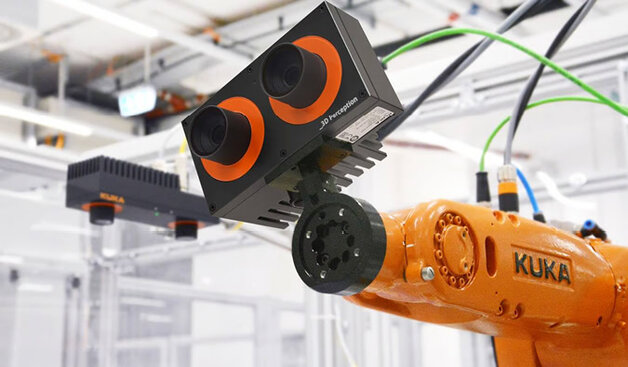
Za pomocą systemu kamer oprogramowanie umożliwia robotowi postrzeganie otoczenia, a także niezależne podnoszenie i pozycjonowanie obiektów
Sztuczna inteligencja w przemyśle
Pierwszym przychodzącym na myśl zastosowaniem SI w przemyśle jest robotyka. Roboty, zwłaszcza współpracujące, zwane kobotami, mogą gromadzić dane na temat wykonywanych przez siebie operacji, oceniać swoje działania za pomocą algorytmów SI, a nawet mogą doradzić operatorowi, jakie powinny być dalsze kroki postępowania np. przy każdym przezbrojeniu linii. Co więcej, sztuczna inteligencja umożliwia kobotom reagowanie na mowę i gesty ludzkie oraz uczenie się z nich bez angażowania pracowników do ich szkolenia czy programowania.
Roboty wykorzystujące sztuczną inteligencję są często wyposażone w różne czujniki (np. urządzenia wizyjne, takie jak kamery 2D/3D, czujniki wibracyjne, czujniki zbliżeniowe, przyspieszeniomierze i inne czujniki środowiskowe), które dostarczają dane do analizy i działania w czasie rzeczywistym. Dzięki sztucznej inteligencji roboty przemysłowe mogą wykonywać swoje zadania szybciej i dokładniej. Technologie sztucznej inteligencji wykorzystują informacje z czujników wizji, np. kamery 2D/3D (widzenie maszynowe), aby kategoryzować i rozumieć otoczenie oraz wykrywać i klasyfikować przedmioty pojawiające się w ich zasięgu.
W wypadku autonomicznych mobilnych robotów AMR sztuczna inteligencja pozwala im na pozyskiwanie informacji z kamer 3D i czujników LiDAR, a następnie na analizowanie zebranych informacji. Na tej podstawie, oraz na podstawie programu misji transportowej, system sterowania może dokonać wnioskowania i podjąć decyzję o poruszaniu się daną trasą, ominięciu przeszkód lub modyfikacji działanie w celu osiągnięcia jak najlepszych wyników.
Zadania i działania realizowane przez urządzenia AMR ze sztuczną inteligencją znacząco się różnią w zależności od branży. Na przykład, podczas przenoszenia zapasów z jednego miejsca w magazynie w inne, urządzenia AMR unikają kolizji przez omijanie pracowników lub opakowań, które spadły na trasę, jednocześnie określając najlepszą drogę do ukończenia zadania.
Oddzielną grupą zastosowań sztucznej inteligencji są przemysłowe systemy Edge AI, a więc systemy przetwarzające dane produkcyjne na brzegu sieci (a w miejscu ich powstawania) z zaimplementowanymi algorytmami sztucznej inteligencji. Uczenie maszynowe czy uczenie głębokie zastosować można do znacznie szybszej i pewniejszej analizy napływających w czasie rzeczywistym do węzła brzegowego danych.
Ponadto brzegowa, sztuczna inteligencja pozwala w znacznie lepszym stopniu zarządzać nie tylko procesami produkcyjnymi, ale również zasobami – w tym prądem, wodą czy innymi surowcami wykorzystywanymi podczas wytwarzania. Kontrola kluczowych parametrów procesu może też pomóc w przewidywaniu awarii. Zaburzenia świadczące o nadchodzącej awarii maszyn często widoczne są zanim ona nastąpi i na tej podstawie algorytmy sztucznej inteligencji mogą przewidzieć, kiedy będzie ona miała miejsce. Dzięki takiej predykcji można z dużym wyprzedzeniem podjąć środki zaradcze.
Co ciekawe, według raportu Gartnera „Emerging Technologies: Tech Innovators in Edge AI”, w ciągu najbliższych czterech lat uczenie maszynowe będzie zastosowane w ponad 65 % przypadków użycia na węzłach brzegowych narzędzi typu Edge AI. W 2021 roku z tego typu praktykami spotkać się można było jedynie w 10 % przypadków. Jednak ten sam raport podaje, że do 2025 roku, Edge AI pozostanie „w stadium embrionalnym” ze względu na brak wiedzy i doświadczenia związanego z nadawaniem odpowiednich uprawnień „krawędziom”, np. komputerom przemysłowym klasy embedded, urządzeniom sieciowym i lokalnym serwerom sterującym produkcją.
Literatura:
[1] T. Kycia, Metody sztucznej inteligencji w predykcyjnym utrzymaniu ruchu, Monografia „Predykcja w układach mechanicznych i automatycznych 2021 – metody statystyczne i sztuczna inteligencja”, Politechnika Rzeszowska 2021.
[2] Materiały start-up’u Dature – https://dature.cloud/
[3] M.Maternowska, Nowe technologie i ich wpływ na łańcuchy dostaw. Sztuczna inteligencja, Zeszyty Naukowe Uniwersytetu Ekonomicznego w Katowicach, Nr 388, 2019.
[4] https://pl.wikipedia.org/wiki/Sie%C4%87_neuronowa
źródło: Automatyka 6/2023
Słowa kluczowe
AI, automatyka, cyfryzacja, Przemysł 4.0, robotyka, robotyzacja, sztuczna inteligencja
Komentarze
blog comments powered by Disqus