Robotyka przemysłowa dziś i jutro
mgr inż. Monika Różańska-Walczuk, dr inż. Krzysztof Kukiełka drukuj
Pierwszy robot przemysłowy został wyprodukowany przez firmę Unimation. Znalazł zastosowanie w fabryce General Motors w Trenton, przy obsłudze wysokociśnieniowej maszyny odlewniczej. W ciągu kilku lat roboty Unimate zostały przystosowane do pracy w innych gałęziach przemysłu. Od tego czasu upłynęło już ponad pół wieku – robotyka przemysłowa przeszła dużo zmian, rozwinęła się i zagościła w różnych dziedzinach przemysłu.
Dane z rynku potwierdzają, że robotyka przemysłowa ma się dobrze, a nawet bardzo dobrze. Ostatni rok przyniósł kolejny rekord sprzedaży robotów na świecie. Na targach Automatica w Monachium Arturo Baroncelli, prezydent IFR (International Federation of Robotics) mówił: – Liczba zleceń w ciągu pierwszych czterech miesięcy 2014 roku wzrosła znacząco, a zapytania ze strony klientów ze wszystkich branż przemysłowych, również osiągają wyższy poziom. Spodziewamy się więc, że w 2014 roku wzrost sprzedaży będzie kontynuowany w takim samym tempie, jak w roku 2013. Może to sugerować osiągnięcie kolejnego rekordu sprzedaży robotów przemysłowych, również w tym roku.
Statystyki
Dane dotyczące globalnej sprzedaży robotów w ostatnich latach potwierdzają wspomniany trend.
Kolejny wykres pokazuje udział poszczególnych sektorów przemysłu w globalnej sprzedaży robotów. Już od kilku lat widać w przemyśle motoryzacyjnym zwiększone inwestycje w robotykę. Daje to motoryzacji miano najważniejszego klienta dostawców robotów. Można zaobserwować zależność między tym rynkiem a robotyką przemysłową: gdy przemysł motoryzacyjny przeżywa kryzys, zauważalny staje się ogólny spadek sprzedaży robotów przemysłowych. Również w pozostałych branżach obserwowana jest tendencja wzrostowa.
Branża spożywcza, farmaceutyczna i kosmetyczna
Patrząc na dane szczegółowe niektórych branż, można zauważyć utrzymującą się wysoką sprzedaż w przemyśle spożywczym. Coraz więcej mniejszych wytwórni decyduje się na zakup robota, aby być konkurencyjnym. W Polsce sprzedaż robotów dla tego segmentu rynku zaskoczyła w 2012 r. Wzrost w porównaniu z rokiem 2011 wynosił aż 139 proc. (dane ze strony internetowej ogólnopolskiego programu edukacyjnego, upowszechniającego wiedzę na temat robotyzacji – nieznanamocrobotow.pl).
Także dziś branża wykazuje dalsze zainteresowanie robotyzacją produkcji. – Branża spożywcza otwiera się na roboty i nawet małe piekarnie, ze względu na współpracę z dyskontami, myślą o manipulatorach – zauważa Patryk Dąbrowa, specjalista ds. zrobotyzowanych linii produkcyjnych z firmy ASTOR. W artykule „Co robią roboty w branży spożywczej? Trendy, wyzwania, skala oszczędności”, opublikowanym na stronie firmy ASTOR, zostały przedstawione kluczowe trendy związane z automatyzacją i robotyzacją branży spożywczej w 2014 r.
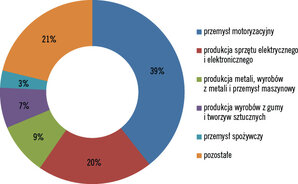
Światowa sprzedaż robotów w 2011 r. według sektorów przemysłu – szacunki Międzynarodowej Federacji Robotyki
Kolejnymi branżami, które zaskoczyły wynikami sprzedaży w 2013 r., są przemysł farmaceutyczny i kosmetyczny. Choć ogólna liczba sprzedanych robotów nie jest w tym przypadku wielka, to przyrost w 2013 r., sięgający 69 proc., jest już znaczny. Tę tendencję widać też w zmianie w ofertach dostawców robotów. Firma Kawasaki wprowadziła do sprzedaży roboty przeznaczone do farmacji. – Coraz więcej takich urządzeń pojawia się w zakładach na zachodzie. Stopniowo dąży się do pełnego zamknięcia produkcji leków i odsunięcia od niej człowieka – mówi Patryk Dąbrowa.
Regiony i czynniki
Szacowana średnia sprzedaż robotów zakłada 12-proc. wzrost w latach 2015–2017. W obu Amerykach i w Europie ma się on kształtować na poziomie 6 proc., natomiast w Azji i Australii ma wynieść 16 proc. Ogólna tendencja do automatyzacji produkcji będzie nadal zwiększać liczbę zainstalowanych robotów. Można stwierdzić, że przed robotyką przemysłową rysuje się bardzo dobra przyszłość. Główne czynniki wpływające na rozwój robotyzacji, wymienione w tegorocznym raporcie IFR, to m.in.:
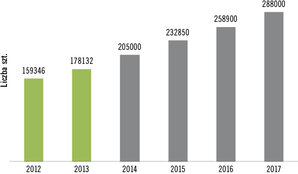
Prognozowana sprzedaż robotów w ciągu najbliższych lat – szacunki Międzynarodowej Federacji Robotyki
1. globalna presja konkurencyjna, wymagająca zwiększonej wydajności i lepszej jakości,
2. energooszczędność oraz nowe materiały, wymagające zmian w procesie produkcji,
3. współpraca człowiek–maszyna, która otwiera robotykę na nowe aplikacje i znajduje nowych klientów,
4. rosnące rynki konsumenckie, wymagające rozbudowy mocy produkcyjnych,
5. zmniejszenie cyklu życia produktów oraz zwiększenie gamy produktów, wymagające elastycznej automatyzacji,
6. poprawienie jakości pracy przez przejmowanie niebezpiecznych i uciążliwych zadań, które są niemożliwe do wykonania przez ludzi, zagrażają ich życiu i zdrowiu bądź są powtarzalne.
Dział przemysłowy | Liczba robotów [szt.] | Przyrost [szt.] |
Tempo wzrostu (%) | ||
2012 r. | 2013 r. | ||||
1. | Produkcja pojazdów samochodowych | 66 500 | 69 400 | 2900 | 4 |
2. | Produkcja metalowych wyrobów gotowych | 15 100 | 16 500 | 1400 | 9 |
3. | Produkcja wyrobów z gumy i tworzyw sztucznych | 11 400 | 12 200 | 800 | 7 |
4. | Produkcja artykułów spożywczych | 4850 | 6200 | 1350 | 28 |
5. | Produkcja farmaceutyczna i kosmetyczna | 1180 | 2000 | 820 | 69 |
Przemysł ogółem | 159 000 | 178 200 | 19 200 | 12 |
Tab.1. Przyrost liczby robotów przemysłowych w niektórych działach przemysłu w 2013 r. – szacunki Międzynarodowej Federacji Robotyki
Aktualne trendy
Już obecnie można zauważyć wiele zmian, jakie w ostatnich latach wpłynęły na kształt polskiego rynku robotyki. Wśród nich można wyróżnić aktualne trendy, które zdominowały ten sektor przemysłu.
Kierunek rozwoju firm integrujących
Na polskim rynku jest wiele firm zajmujących się integracją urządzeń automatyki z przemysłowymi liniami produkcyjnymi. Jedne specjalizują się w projektowaniu aplikacji typu pick & place, inne ograniczają się do procesów spawalniczych, a jeszcze inne ukierunkowują na malowanie czy obsługę maszyn. Takie podejście można uznać za pewnego rodzaju ograniczenie, ale umożliwia to integratorom zdobywanie większego doświadczenia w wybranym sektorze przemysłowym.
Tendencję tę dobrze widać na przykładzie firmy ABB, w odniesieniu do jej globalnego sposobu działania. W dziale robotyki przemysłowej wydzielono centra kompetencji, które rozwijają działalność badawczo-rozwojową w określonej dziedzinie – w obsłudze danego typu procesu produkcyjnego. Pozwala to inżynierom ABB na opracowanie specjalizowanych rozwiązań dla procesu, poczynając od przypisywanych konkretnej aplikacji narzędzi, przez szczegóły związane z instalacją stanowiska
(np. wykaz dodatkowych urządzeń, schematy elektryczne), po oprogramowanie przeznaczone i specjalizowane do sterowania pracą robota i innych urządzeń danego stanowiska.
Przykładem może być ABB Picking & Packaging Engineering Center powstałe w polskim oddziale, które specjalizuje się w aplikacjach związanych z pakowaniem i układaniem elementów, stosowanych m.in. w przemyśle spożywczym, farmaceutycznym, chemicznym i kosmetycznym. Centrum tworzy gotowe rozwiązania dla klientów, służy wsparciem technicznym, szkoli, prowadzi też testy produkcyjne zaprojektowanych aplikacji. Jednym z założeń jest wejście na rynek z propozycjami standardowych pakietów funkcjonalnych, gotowych do zastosowania w poszczególnych branżach przemysłu. Przykładem może być pakiet związany z paletyzowaniem elementów. W ramach opracowanych rozwiązań oferowane są roboty i chwytaki, przeznaczone do przenoszenia różnych przedmiotów (worków, pudełek kartonowych itp.), dodatek do systemu robota, ułatwiający programowanie operacji paletyzowania (PalletWare) oraz niezbędne informacje o integracji robota z pozostałymi elementami stanowiska.
Inne centra kompetencji ABB zajmują się m.in. kontrolowaniem siły oddziaływania robota (Force Control w Austrii), spawaniem i cięciem (Czechy), obsługą pras (Hiszpania).
Zrobotyzowane magazynowanie
Jednym z najbardziej popularnych zastosowań robotyki przemysłowej, wykorzystującym systemy zautomatyzowane, jest magazynowanie. Zrobotyzowane systemy magazynowania wpływają na zwiększenie produkcji, na jakość, spójność, a także elastyczność procesu. Przyczyniają się do obniżenia liczby wypadków z udziałem pracowników, zmniejszenia ilości odpadów (związanych z nieefektywnością pracy) oraz lepszego wykorzystania przestrzeni roboczej. Roboty wspierają aplikacje dotyczące transportowania i przenoszenia różnego rodzaju materiałów – od dużych pojazdów do małych próbek.
Postęp obejmujący rozwój robotów, systemów wizyjnych oraz narzędzi manipulacyjnych, umożliwia ścisłą współpracę robotów w przemyśle spożywczym. Wspiera również precyzyjne monitorowanie efektów produkcji, np. zliczanie zjeżdżających z linii produkcyjnej produktów końcowych. Umożliwia śledzenie pełnego przebiegu procesu wytwarzania produktu, od początku, aż do jego umieszczenia na półce.
W przemyśle farmaceutycznym robot może składać opakowania, pakować lekarstwa i wspierać proces pakowania lub paletyzacji opakowań zbiorczych. Natomiast branża lotnicza wykorzystuje roboty poczynając od procesu produkcji elementów lotniczych, kończąc na bezpośredniej konserwacji samolotów.
Centra dystrybucyjne również zyskują na popularności. Ich zadaniem jest wsparcie techniczne oraz obsługa większej liczby komponentów (niezbędnych w procesie produkcji), które muszą być dostarczane szybko i precyzyjnie. Muszą również wspierać zarządzanie informacjami o zapotrzebowaniu, ze względu na ewentualne braki lub dokonane zmiany, związane z zapasami elementów produkcyjnych, oraz dodatkowe usługi serwisowe. Zorganizowana dystrybucja wpływa na zwiększenie realizacji zamówień, przy jednoczesnym zwiększeniu dokładności i optymalizacji procesu.
Oczujnikowanie
Zrobotyzowane aplikacje do magazynowania, stosowane do przenoszenia, załadunku/rozładunku, pakowania czy pobierania elementów z pojemnika, realizują swoje zadania z coraz większą dokładnością i zdecydowanie większą prędkością niż kilka lat temu. Aby wymienione aplikacje spełniały swoje funkcje, a przy tym były wydajne, muszą być wyposażone w sensory, które są odpowiednikiem ludzkich zmysłów. Wysoka precyzja jest osiągana właśnie dzięki nim.
Roboty mogą być wyposażone w czujniki siły (np. FANUC Force Sensor i ABB Force Control), które umożliwiają dokonanie korekcji dojazdu ramieniem robota do elementu, w taki sposób, aby obiekt ten był odpowiednio podniesiony lub poddany obróbce z odpowiednią precyzją.
Systemy wizyjne
Obecnie standardem są oferowane klientom przez producentów robotów rozwiązania pozwalające na identyfikowanie detali w przestrzeni pracy robota, realizowane za pomocą systemu wizyjnego. Jest to kolejny ze zmysłów robota, czyniący go bardziej inteligentnym.
Systemy wizyjne są coraz częściej stosowane w zrobotyzowanych liniach produkcyjnych. Dlatego też, aby uprościć proces ich konfiguracji i integracji ze stanowiskiem, producenci robotów integrują je z kontrolerami robotów. Przykładem jest system iRVision (Intgrated Robot Vision) firmy FANUC oraz Integrated Vision firmy ABB. Rozwiązaniem najczęściej spotykanym w aplikacjach zrobotyzowanych jest system z kamerą 2D, wykorzystujący wizję do przetwarzania informacji z otoczenia.
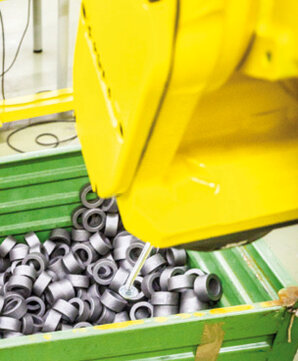
Robot pobierający elementy z pojemnika przy wykorzystaniu systemu iRVision 3D Area Sensor firmy FANUC
Jednak współczesne zadania aplikacyjne sprawiają, że takie systemy nie zawsze są wystarczające. Firma FANUC oferuje narzędzie wizyjne, umożliwiające detekcję obiektów w przestrzeni trójwymiarowej.3D Area Sensor składa się z projektora rzucającego wiązki światła na detale oraz dwóch kamer, skierowanych na nie pod kątem. Na zasadzie triangulacji z dwóch obrazów 2D obliczana jest mapa punktów w trzech wymiarach, a następnie określane jest położenie całego detalu w tej przestrzeni. W zależności od rodzaju obiektu do wyboru jest wiele możliwości (szukanie powierzchni, najwyższych punktów pozyskanej mapy 3D, płaszczyzn czy też otworów). Narzędziem przeznaczonym do współpracy z czujnikiem 3DAS jest chwytak produkcji FANUC (FANUC gripper). Jego budowa jest uniwersalna, dzięki czemu można go stosować do aplikacji wymagających chwytania obiektów o zróżnicowanych kształtach.
Mniejsze, ale silniejsze
Utrzymującą się tendencją jest zmniejszanie wymiarów kontrolerów. Podobnie jak inne urządzenia elektroniczne, sterowniki robotów będą mieć mniej elementów dyskretnych wewnątrz obudowy, dzięki ich integracji. Kompaktowe sterowniki robotów są bardzo popularne w przemyśle elektronicznym. Wpływa to również na wzrost bezpieczeństwa, gdyż pozwala na uporządkowanie kontrolera i znajdującego się w nim okablowania. Małe sterowniki są również niezbędne do robotyzacji aplikacji w laboratoriach badawczych i na stanowiskach naukowych. Wpłynęło to pozytywnie na wzrost odnotowany w przemyśle farmaceutycznym, o czym wspominał Patryk Dąbrowa z firmy ASTOR, wypowiadając się o zmianach i robotyzacji tzw. małego przemysłu. – Miniaturyzacja zwiększa bezpieczeństwo w przypadku robotyki dla aplikacji nieprzemysłowych. Zintegrowane kontrolery sprawiają, że roboty są bezpieczniejsze bez stosowania dodatkowych elementów zabezpieczających, to znaczy kurtyn bezpieczeństwa itd. Takie kontrolery są łatwiejsze w obsłudze przez niewykwalifikowaną kadrę, techników montażowych lub naukowców, którzy chcą obsługiwać roboty w ramach trendu wprowadzania współpracy człowieka z robotem – dodaje przedstawiciel ASTOR. Zauważa również, iż część małych, przydomowych zakładów szuka zestawu robota ze spawarką i samodzielnie, po przeszkoleniu, integruje stanowisko. Rośnie wiedza wśród inwestorów, co w połączeniu z młodszą kadrą ułatwia takie wdrożenia.
Można przypuszczać, że miniaturyzacja sterowników robota będzie kontynuowana do czasu, gdy nie zostanie on zintegrowany z ramieniem robota, a jego obsługa nie stanie się intuicyjna. Zintegrowanie kontrolera robota z jego ramieniem jest wymogiem, który stawiają robotykom inżynierowie i naukowcy zajmujący się robotami humanoidalnymi. Wystarczająco zminiaturyzowane kontrolery będą stosowane w zaawansowanych robotach mobilnych.
Nadchodzące trendy
Oprócz trendów oddziałujących na rynek już teraz, można zaobserwować też zmiany, które w przyszłości będą kształtowały robotykę.
Współpraca robotów i ludzi
Nowy typ robotów – współpracujących z ludźmi – utorował sobie drogę w branży, zmieniając nieufne nastawienie względem robotyki. Ich główną cechą jest zdolność do bezpiecznego wykonywania pracy u boku ludzi. Dlatego współpraca człowiek–robot jest nowym wyzwaniem stawianym w dziedzinie robotyki.
Do tej pory roboty były zawsze uważane za duże, mocne i solidne urządzenia, realizujące zadania przeznaczone specjalnie dla nich. W celu zapewnienia bezpieczeństwa odgradzano je barierą i systemami zabezpieczającymi. Pomalowane na jasny kolor, miały ostrzegać pracowników o zagrożeniach, jakie mogą powstać w związku z ich obecnością. Dodatkowo konieczne były umiejętności programistyczne, aby właściwie skonfigurować i zaprogramować robota.
Roboty współpracujące z ludźmi są przeciwieństwem robotów przemysłowych – są kompaktowe, lekkie i zręczne. Wykorzystanie nowych technologii do ich budowy daje możliwość tworzenia robotów o siedmiu stopniach swobody – jest to o jeden stopień więcej niż jest to konieczne. Niemniej pozwala to uzyskać większe możliwości konfiguracyjne ramienia robota.
Co więcej, roboty te mają zintegrowane czujniki, związane z funkcjami bezpieczeństwa. Służą one do wykrywania zewnętrznych sił, aby robot mógł odpowiednio zareagować. Jeśli siła jest zbyt duża, robot powinien zatrzymać swój ruch. W przypadku wykrycia kolizji, będzie przemieszczał swoją oś w przeciwnym kierunku, aby uniknąć zderzenia i uszkodzenia.
Niektóre współpracujące roboty można programować, stosując metodę programowania przez demonstrację, polegającą na obwiedzeniu efektorem robota trajektorii, jaką ten ma wykonywać. Nie jest wówczas potrzebna szeroka wiedza na temat programowania robota. Większość oferowanych współcześnie robotów współpracujących można w łatwy sposób przemieszczać między różnymi fragmentami linii produkcyjnej. Wszystko to sprawia, że taki robot może być w prosty sposób przeniesiony w nowe miejsce i szybko dostosowany do wykonywania nowego zadania.
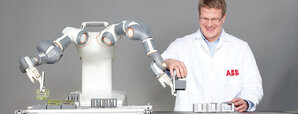
Robot dwuramienny YuMi firmy ABB, współpracujący z człowiekiem; przykład rozdzielania zadań oraz współdzielenia przestrzeni
Nowe możliwości
Współpraca robota z ludźmi pozwala na ingerencję operatora w trakcie pracy stanowiska zrobotyzowanego, przy zachowaniu bezpieczeństwa. Podczas wspólnych operacji robot działa w trybie automatycznym. Zatrzymuje się wtedy, gdy konieczna jest współpraca. Sterownik oprogramowania rozpoznaje, kiedy np. cela paletyzująca wymaga uzupełnia o elementy wykorzystywane w produkcji, a także może zapobiegać naruszaniu i wjeżdżaniu przez robota w obszar zajmowany przez operatora, znajdujący się w jego przestrzeni roboczej. Roboty współpracujące mogą również wspierać operatora i asystować w uciążliwych pracach, np. przy podnoszeniu ciężkich elementów, tak aby operator mógł się skupić wyłącznie na procesach myślowych.
Współpraca robotów z ludźmi to zdecydowana droga ku przyszłości, ponieważ robot i operator mogliby pracować w harmonii, zwiększając produkcję. Kwestia bezpieczeństwa powinna być realizowana niezawodnie, dzięki kontrolerowi bezpieczeństwa, w trakcie wykonywanej pracy, montażu i fazy uruchomieniowej komórki.
Normy i postępy
Aktualna faza to dopiero początek ścisłej współpracy między człowiekiem a robotem. Największym wyzwaniem jest zapewnienie bezpieczeństwa w odniesieniu do bliskiej współpracy robota z człowiekiem, bez stosowania ogrodzeń ochronnych. Kwestie bezpieczeństwa dotyczące robotyki przemysłowej są zawarte m.in. w normie ISO 10218. Znajdziemy w niej wytyczne dotyczące współpracy robota z człowiekiem. Obecnie trwają prace nad normą
ISO/TS 15066, która w całości będzie poświęcona zagadnieniom bezpieczeństwa robotów współpracujących.
Roboty współpracujące mogą pracować samodzielnie, gdy nie ma nikogo w ich chronionym obszarze roboczym i muszą przejść w stan „protective stop”, kiedy człowiek wejdzie w ich chronioną przestrzeń roboczą. Następnie mogą wznowić pracę automatyczną, gdy człowiek jest poza tą przestrzenią. Ludzie mogą wchodzić w interakcję z robotem, a ponadto ludzie i roboty mogą poruszać się jednocześnie wokół wspólnego obszaru roboczego. Zastosowanie wymagań normy gwarantuje, że wspólny obszar roboczy jest zwykle szerszy niż chronione miejsce. W normach omawiane są cztery kryteria bezpieczeństwa dla pracy grupowej. Odnoszą się one do:
- monitorowanych zatrzymań,
- kontrolowania prędkości,
- odległości separacji,
- ograniczenia mocy i siły.
Podczas pracy robota w cyklu automatycznym wymagana jest sygnalizacja świetlna, gdy wybrana i aktywna jest praca w trybie współpracy. Jeżeli robot może wykonać monitorowane zatrzymanie, oznacza to, że układ napędowy robota ma wbudowany system bezpieczeństwa, gwarantujący ograniczenie prędkości lub momentu obrotowego do bezpiecznej wartości. Dzięki tej funkcji kontroler robota ma zdolność do bezpiecznego ograniczenia zakresu ruchów robota. Twarde zatrzymanie nie jest już obowiązkowe w nowych kontrolerach robotów, które mają tę funkcję.
Producenci robotów przeznaczonych do bliskiej współpracy z ludźmi twierdzą, że ich roboty są bezpieczne, zgodnie z wymaganiami bezpieczeństwa dla robotów przemysłowych, określonymi przez wymagania normy ISO 10218. Nawet przy takim założeniu ocena ryzyka jest jednak konieczna, aby upewnić się, że otoczenie robota jest w pełni zabezpieczone.
Pilz SafetyEYE
Rozwiązaniem wspierającym bezpieczne współdzielenie przestrzeni przy współpracy ludzi i robotów jest system SafetyEYE firmy Pilz. Jest to system kamer bezpieczeństwa, bazujący na optoelektronicznych urządzeniach ochronnych. Całość tworzy kombinację inteligentnych sensorów oraz efektywnego sterowania. Wyjątkowość systemu SafetyEYE jest związana z jego trójwymiarowym sposobem monitorowania stref ostrzegawczych i ochronnych.
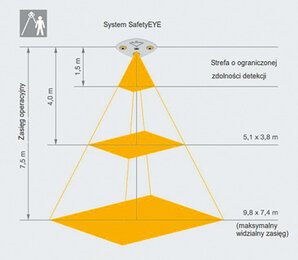
SafetyEYE umożliwia monitorowanie obszaru o wymiarach 9,8 m × 7,4 m, z wykorzystaniem tylko jednego systemu kamer
Dzięki wysokiemu bezpieczeństwu, jakie zapewnia system firmy Pilz, możliwa jest bliska i bezpieczna współpraca między człowiekiem a maszyną. To bardzo istotna kwestia, gdyż szczególnie w procesach produkcyjnych, w których człowiek aktywnie współpracuje z robotem, bezpieczeństwo musi być na bardzo wysokim poziomie. Dzięki stałemu monitoringowi stref ostrzegawczych oraz ochronnych możliwe jest uniknięcie nadmiernego zbliżenia się operatora lub pracownika do miejsca potencjalnie niebezpiecznego w czasie pracy robota.
Największymi zaletami systemu SafetyEYE, które potwierdzają jego wyjątkowość, są wysoka produktywność, uzyskana przez ergonomię zrobotyzowanych stanowisk oraz zoptymalizowanie przebiegu roboczego, a także wysoki poziom zabezpieczenia przed manipulacją. Szybkość instalacji oraz łatwe uruchomienie systemu SafetyEYE,
bez potrzeby korzystania z wielu komponentów, a także załączone, proste oprogramowanie konfiguracyjne i komfortowa diagnostyka, są również cechami sprzyjającymi użytkownikom. Oprogramowanie jest intuicyjne, a konfigurację obszarów SafetyEYE, przez definiowanie stref, łączenie ich w grupy ostrzeżeń, bądź ochrony, można zrealizować za pomocą komputera PC.
System firmy Pilz może wykrywać, a także informować o przedostaniu się niepożądanych obiektów do zdefiniowanych (dowolnie przez użytkownika) stref ostrzegawczych i ochronnych. SafetyEYE może określić, czy osoby przebywają w strefie zagrożonej przez niebezpieczne ruchy (kwestie bezpieczeństwa), czy też znalazły się w strefie o podwyższonym stopniu ochrony (kwestia zabezpieczeń).
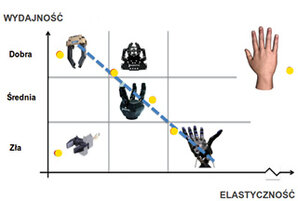
Zależność poprawności i jakości wykonania zadania przez robota przemysłowego, względem liczby zadań, które może wykonać w odniesieniu do rodzaju zastosowanego chwytaka
Chwytanie adaptacyjne
Stosowanie specjalizowanych, ograniczonych funkcjonalnie oraz mechanicznie narzędzi jest bardzo niepraktyczne w dzisiejszym procesie produkcji. Obecnie zmiany muszą dokonywać się dynamicznie, z optymalnym dostosowaniem do całego cyklu produkcyjnego. Nowe chwytaki adaptacyjne mogą chwycić niemal wszystko w zakresie ich możliwości mechaniczno-konstrukcyjnych. Największą zaletą takich chwytaków jest to, że dostosowują się niemal automatycznie do każdego kształtu.
Ręka Robotiq
Zaprojektowane do różnego typu aplikacji chwytaki adaptacyjne radzą sobie z manipulacją różnymi obiektami. Takie rozwiązanie ma na celu poprawienie elastyczności procesu i jego spójności. Robotyczna ręka firmy Robotiq umożliwia chwytanie w skomplikowanych aplikacjach, np. w zrobotyzowanym spawaniu, maszynowym załadunku/rozładunku itp. Jej główna cecha to elastyczność – może chwycić przedmioty o różnych kształtach i wymiarach, a dokładny panel sterowania umożliwia prostą kontrolę położenia, prędkości i siły palców. Ręka jest również wytrzymała i niezawodna, ponieważ zaprojektowana jest dla środowiska przemysłowego. Jest też kompatybilna z robotami wszystkich wiodących producentów. Komunikuje się przez kontroler robota za pomocą interfejsów EtherNet/IP, TCP/IP, DeviceNet, CANopen, EtherCAT czy Modbus RTU.
Bioniczne Festo
DHDG firmy Festo, składający się z napędu pneumatycznego i trzech palców korzystających z efektu Fin Ray, to kolejny przykład innowacyjnego chwytaka adaptacyjnego. Chwytak ten charakteryzuje się bionicznym sposobem chwytania. Przy uwzględnieniu jego minimalnej wagi cechuje go stosunkowo duża dynamika pracy. Umożliwia bezpieczne i nieniszczące, a zarazem silne i elastyczne (względem elementów o nieregularnych kształtach) chwytanie części roboczych.
Chwytak jest wyposażony w system delikatnego chwytania (ang. SoftGrip) z funkcją blokowania. Jego wszechstronne palce dostosowują się do różnych kształtów i konturów, a przy tym jest o 80 proc. lżejszy w porównaniu do podobnych, seryjnie produkowanych chwytaków. Optymalizacja, tzn. kompaktowa konstrukcja, siłownik dwustronnego działania oraz wymienne palce chwytaka, jest jego dużą zaletą. Ze względu na wytrzymałość może być stosowany przez wiele lat. Innowacyjność polega również na połączeniu chwytaka adaptacyjnego oraz palców chwytaka równoległego. Przedstawiciele Festo podkreślają, że sprawdza się on idealnie przy manipulacji zarówno produktami delikatnymi, podatnymi na uszkodzenia, czy kruchymi, jak i obiektami o nieregularnych kształtach. Podając minimalne ciśnienie na powierzchnię chwytającą, dobrze współpracuje z komponentami wrażliwymi na wysokie ciśnienie.
Versaball
Nowością w dziedzinie chwytaków przemysłowych jest wielozadaniowy chwytak Versaball, zaprezentowany w połowie 2014 r. przez firmę Empire Robotics. Ma on formę chwytającej piłki. Versaball można zamontować na końcu ramienia robota, aby mógł chwytać i przenosić przedmioty z odpowiednią precyzją. Kluczowym atutem tego chwytaka jest jego zdolność do bezpiecznego chwytania szerokiej gamy obiektów i szybkiego manipulowania nimi. Jest to istotna zaleta dla odbiorców, ponieważ umożliwia zautomatyzowanie większej liczby zadań w procesach produkcyjnych, przy zastosowaniu jednej końcówki roboczej. Versaball jest mały i szybki. Mniejsza wersja chwytaka ma niespełna 90 mm i może chwycić obiekt w czasie około 0,1 s oraz upuścić go w mniej niż 0,2 s. Większy chwytak, o wymiarze 165 mm, może chwycić przedmiot w czasie około 0,7 s, a upuścić go w mniej niż około 1 s.
Największym atutem tego miękkiego, gąbczastego chwytaka przemysłowego jest jego prostota. Wykonany jest z miękkiej mieszanki polimerowej i ma trwałą warstwę wierzchnią, wyposażoną w odpowiednią ilość elastycznej gąbki, niezbędnej do dopasowania się do chwytanego obiektu. Zasada pracy tego chwytaka polega na usunięciu odpowiedniej ilości powietrza, którym jest wypełniona piłka.
Producent chwytaków wskazuje na jego użytkową wszechstronność, podając przykłady zastosowania Versaball do przenoszenia cegieł, żarówek czy odłamków szkła.
Cechami opisującymi Versaball są elastyczność, delikatność w trakcie procesu manipulacji elementami, powtarzalność wykonywanych ruchów i chwytania (odkładanie obiektów w to samo miejsce za każdym razem, przyjmując tolerancję względem manipulowanego elementu), niezawodność (żadnego upuszczenia elementu manipulowanego po 8000 cykli), a przede wszystkim trwałość, nawet przy manipulacji elementami metalowymi, takimi jak przekładnie, lub ostrymi i ściernymi, jak cegły.
„Robotyfikacja”, czyli nowe obszary robotyzacji
Postęp i dokonane zmiany, związane z budową i wyglądem kontrolerów robotów, pomagają zrobotyzować nowe typy procesów i wykorzystać roboty w nowych, niestandardowych zastosowaniach. Otwierają się obszary, które nie były tradycyjnie eksplorowane przez branżę robotyki. Obecnie proces ten dotyka obszarów, w których normalnie pracują ludzie lub specjalizowane urządzenia i maszyny, np. przy wykańczaniu i obróbce powierzchniowej obiektów, przy ważeniu oraz w montażu precyzyjnym.
Tradycyjne aplikacje nadal będą rozwijane z wykorzystaniem nowych technologii, związanych ze sposobem chwytania elementów. Integracja sensorów (np. sonarów, laserów skanujących, trójwymiarowych systemów wizyjnych) z kontrolerem robota pozwala na rozwój aplikacji oraz sprawia, że roboty są bardziej elastyczne i mogą działać w dynamicznym środowisku.
Gdy kontrolery staną się wydajniejsze, będą również zarządzać innymi urządzeniami oraz funkcjonowaniem całej komórki roboczej, w której pracują. Użytkownicy końcowi chcą ścisłej integracji z platformami logicznymi i wbudowaną kinematyką.
Inteligentne kontrolery, gwarantujące zwiększone bezpieczeństwo, pozwalają na zmniejszenie dystansu w obszarze roboczym między człowiekiem a robotem. W przyszłości roboty będą przystosowane do pracy na zewnątrz zakładów produkcyjnych, np. będą mogły konserwować statki czy być wsparciem przy naprawie elementów okrętowych, bezpośrednio na pokładzie. Mogą być odpornymi na zmienne warunki pogodowe „pracownikami” na platformach wiertniczych. Obecnie firma KUKA oferuje już robot KR QUANTEC PA Arctic, który może pracować w niskich temperaturach oraz wodoodporny robot KR AGILUS Waterproof.
Oprogramowanie ROS-I w przemyśle
Architektura oprogramowania robotów przemysłowych wydaje się być zastrzeżona i przystosowana jedynie do konkretnej marki robota. Ostatnio pojawił się nowy trend, zmierzający do promowania systemów operacyjnych, bazujących na otwartych źródłach kodu. Impulsem dla przemysłu było opracowanie ROS-I, czyli systemu operacyjnego dla robotów przemysłowych (ang. Robot Operating System Industrial). Ze względu na otwartość licencji, jaką oferują twórcy z Willow Garage, ROS-I
może być wdrożony do zastosowań komercyjnych i aplikacji z prawem własności. ROS-I jest rozszerzeniem popularnego wśród inżynierów zajmujących się robotyką mobilną systemu ROS – rozszerza otwarty model źródłowy do sfery przemysłowej i jest skierowany do użytkowników z branży przemysłowej, przeznaczony do sterowników dla manipulatorów przemysłowych, sensorów lub magistral komunikacyjnych.
Projekt ROS-I tworzy standardy kodu oraz rozwija oprogramowanie w celu zapewnienia wysokiej niezawodności. Nie ma służyć do projektowania podstawowych aplikacji typu pick&place ale umożliwi użytkownikom robotów mobilnych wdrażanie ich do niestrukturalnych aplikacji (niezorganizowanych), kładących nacisk na możliwość współpracy. ROS-I nie zapewnia jeszcze krytycznych funkcji zabezpieczających człowieka. Obowiązują w nim te same standardy bezpieczeństwa, co w istniejących systemach specjalizowanych. System ROS daje użytkowi końcowemu możliwość wykorzystania np. nowo opracowanego kodu, który został rozwinięty w ośrodku naukowo-badawczym, obchodząc problem dotyczący ograniczeń związanych z własnościami specjalizowanych sterowników. System ROS-I zapewnia wspólny interfejs dla robotów przemysłowych różnych firm, co oznacza, że użytkownicy końcowi mogą wdrożyć jedną aplikację dla różnych typów robotów, przy jednoczesnej minimalnej zmianie kodu. ROS osiągnął już taki punkt rozwoju i dystrybucji wśród programistów, naukowców i inżynierów, że użytkownicy na całym świecie mogą ściśle współpracować ze sobą. Ponadto jest łatwo przenośny.
Jak zatem ROS wpłynął na robotykę przemysłową? Naukowcy wykorzystują tanie technologie, dołączając je do robota i piszą w systemie ROS fragmenty kodu w celu osiągnięcia odpowiednich funkcji. Producenci robotów, aby uczestniczyć w tym rozwoju, muszą dostosowywać swoje oprogramowanie i kontrolery, by umożliwiały one zastosowanie innego darmowego kodu źródłowego, w przeciwnym razie zamkną się na nowe technologie. Przemysł coraz poważniej traktuje strategię rozwoju w kierunku rozwiązań z otwartym kodem źródłowym.
System operacyjny ROS-I stanie się znaczącym elementem robotyki przemysłowej, kiedy tylko będzie wystarczająco stabilny, kompatybilny z robotami głównych producentów z branży, a także znajdzie akceptację wśród największych odbiorców robotyki.
Podsumowanie
Robotyka przemysłowa jest działem dynamicznym, który rozwija się i zmienia, aby sprostać nowym wyzwaniom. Biorąc pod uwagę ogólny wzrost gospodarczy oraz coraz nowsze rozwiązania oferowane przez producentów robotów, można stwierdzić, że szacowany wzrost sprzedaży robotów w najbliższych latach nie jest bezzasadny. Ważne są też pojawiające się ostatnio w prasie informacje, że utrzymanie dotychczasowego poziomu rozwoju w skali globalnej może być niemożliwe ze względu na brak wystarczającej liczby rąk do pracy. Wydaje się, że to właśnie robotyzacja może stanowić rozwiązanie tego problemu.
Kontrolery robotów wyposażone są we wszelkie narzędzia, umożliwiające ich zastosowanie w niemal każdej nowej aplikacji, również niestandardowej. Jak to zwykle bywa, jedynym ograniczeniem jest wyobraźnia inżynierów, programujących i projektujących aplikacje, oraz złożoność postawionego zadania czy problemu. Roboty mają bardzo duży wpływ na zmianę procesów produkcyjnych, w których biorą udział, np. mają bezpośredni wpływ na aplikację pakowania, przemieszania produktu i pracę centrów dystrybucji.
Kiedy architektura robotów przemysłowych pozwoli na ich pełną współpracę z ludźmi, bez konieczności stosowania ogrodzeń lub kurtyn świetlnych? Roboty mogą współpracować z ludźmi, ale z niską wydajnością. Wszystko jednak wskazuje na to, że w ciągu kilku lat to się zmieni. Już teraz można spotkać roboty o architekturze Cobots, np. PR2 (Willow Garage’s)
lub robot Rethink Robotics Baxter. Roboty pracujące obok pracowników, na linii produkcyjnej, uwolniły swoje ramiona z „klatek”, a ludzie są coraz bardziej skłonni akceptować je w swoim środowisku pracy.
mgr inż. Monika Różańska-Walczuk
dr inż. Krzysztof Kukiełka
Instytut Automatyki i Robotyki Politechnika Warszawska
Słowa kluczowe
ABB, B&R, bezpieczeństwo, chwytak, czujnik, fanuc, festo, oprogramowanie, PIAP, pilz, robotyka przemysłowa, systemy wizyjne
Komentarze
blog comments powered by Disqus