Robotyzacja spawania hybrydowego - Plazma-MIG/MAG do elementów o grubości powyżej 20 mm
mgr inż. Jacek Szulc, mgr inż. Zbigniew Pilat, mgr inż. Łukasz Wojtczak (Łukasiewicz – PIAP) drukuj
W połowie lat 90. naukowcy i inżynierowie z Instytutu Spawalnictwa im. Patona w Kijowie (Ukraina) założyli w Izraelu firmę Plasma Laser Technologies (PLT). Jej działalność od początku koncentrowała się na pracach badawczo-rozwojowych oraz wdrożeniach zaawansowanych technologii spawalniczych, przeznaczonych również do robotyzacji procesu spawania.
Jednym z interesujących rezultatów prac grupy jest system Weldone – linia urządzeń wykorzystujących łuk plazmowy i promieniowanie laserowe, generowane w jednej, zintegrowanej głowicy spawalniczej.Od 2008 r. firma PLT oferuje także nową, innowacyjną technologię hybrydową Super-MIG, łączącą dwa procesy: spawanie łukiem plazmowym i technologię MIG/MAG. Dotychczasowe doświadczenia pokazują, że sprawdza się ona przy zrobotyzowanym spawaniu większości metali i stopów, przy różnych typach złączy, a jest szczególnie wydajna w przypadku łączenia elementów o grubości powyżej 20 mm. Główne korzyści, jakie daje hybrydowa technologia plazma-MIG/MAG, są związane z możliwościami wykorzystania dużych prędkości spawania oraz z głębokim przetopem, pojedynczego przejścia. Pełna powtarzalność procesu jest zapewniona przez utrzymanie stałych parametrów ruchu i kąta prowadzenia głowicy przez robota.
Projekt RobWeld Super-MIG
Celem projektu RobWeld Super-MIG jest opracowanie zrobotyzowanego gniazda spawania, wykorzystującego technologię Super-MIG jako produktu gotowego do praktycznego zastosowania. O potencjale rynkowym rozwiązania, będącego wynikiem projektu, będą decydować liczne czynniki. Należą do nich: innowacyjność technologii spawania opracowanej przez partnera izraelskiego PLT, wiedza, kompetencje i doświadczenia zespołu partnera polskiego, Przemysłowego Instytutu Automatyki i Pomiarów PIAP w zakresie robotyzacji procesów przemysłowych, w tym spawania, oraz zespołu partnera polskiego Supra Elco, w zakresie nowoczesnych technologii spawalniczych, a także znajomość rynku europejskiego. Ten komplementarny wkład partnerów będzie źródłem wartości dodanej projektu i innowacyjności jego
rezultatów.
Rozwój zaawansowanych technologii spawalniczych
Obecnie w zautomatyzowanych instalacjach produkcyjnych dominuje zastosowanie technologii spawania łukowego elektrodą topliwą, w osłonie gazowej GMA. W zależności od zastosowanego gazu, mówimy o spawaniu MIG (gaz obojętny) lub MAG (gaz aktywny). Odbiorcy wciąż jednak oczekują nowych, bardziej wydajnych metod spawania.
W praktyce producenci oferują dzisiaj dwa rozwiązania: spawanie laserowe albo technologie hybrydowe. Metody laserowe są bardzo drogie na etapie inwestycji i w eksploatacji. Zakup samej instalacji laserowej do spawania to wydatek rzędu kilkuset tysięcy euro. Dodatkowo technologia spawania laserowego wymaga bardzo dokładnego, a więc i kosztownego przygotowania elementów. Dlatego użytkownicy, którzy spawają elementy z blach grubych, coraz chętniej sięgają po wydajne rozwiązania hybrydowe. Obecnie praktyczne zastosowanie przemysłowe znalazły następujące technologie spawania hybrydowego:
1) laser + MIG/MAG,
2) laser + źródło światła,
3) laser + łuk kryty,
4) laser + plazma.
Są one doskonałymi narzędziami do zwiększenia produktywności. Zapewniają poprawę jakości produktów, minimalizację zniekształceń oraz zmniejszenie kosztów pracy w całkowitych kosztach procesu wytwórczego. Jednak wdrożenie technologii hybrydowych wymaga dobrego planowania, przy czym zwykle pożądana jest inwestycja w poprawę procesu przygotowania detali. Z uwagi na zastosowanie systemu laserowego całkowity koszt samej instalacji, jak też później jej eksploatacji, są wciąż bardzo wysokie.
W praktyce stosuje się również tzw. łukowe technologie wysokowydajne:
1) spawanie spoiwem o dużym przekroju poprzecznym (drutem płaskim lub okrągłym),
2) spawanie wielodrutowe łukiem krytym,
3) spawanie dwuelektrodowe MIG/MAG Tandem.
Są one tańsze niż technologie hybrydowe z laserem, a w niektórych zastosowaniach sprawdzają się nawet lepiej. Są jednak mniej wydajne.
Na tym tle technologia spawania hybrydowego Heavy Duty Super-MIG, z zastosowaniem wiązki plazmy, opracowana przez firmę PLT, jawi się jako oferta wypełniająca lukę między wydajnymi i drogimi metodami, wykorzystującymi technikę laserową, a mniej wydajnymi, ale tańszymi metodami wysokowydajnymi, pracującymi bez wsparcia lasera.
Charakterystyka technologii hybrydowej Super-MIG
Technologia Super-MIG wykorzystuje dwa standardowe procesy: spawanie plazmowe (PAW) oraz spawanie łukowe elektrodą topliwą w osłonie gazowej (MIG/MAG), tak jak to zostało pokazane na rys. 1.
W opisywanej technologii łuk plazmowy wyprzedza łuk MIG/MAG, tworząc tzw. „oczko” (ang. Key Hole) do wprowadzania materiału spoiwa. Oba palniki są zintegrowane w jednej głowicy spawania hybrydowego, umieszczonej na ramieniu robota. Jest w niej zamontowany również zespół elektromagnesów, które wytwarzają pole magnetyczne, oddziałujące na strumień plazmy, powodując jego odchylenie. Konstrukcja oraz zasada pracy głowicy są opatentowane przez firmę PLT.
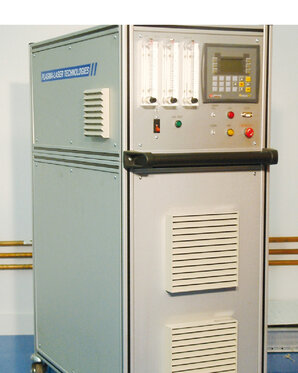
Fot. 2. System spawania hybrydowego Super-MIG firmy PLT. Plazmotron z wbudowanym systemem interfejsu obsługi i sterowania
Korzyści
Główne zalety stosowania zrobotyzowanej technologii Super-MIG to:
- możliwość uzyskiwania większych prędkości spawania niż w konwencjonalnym spawaniu MIG/MAG,
- mniejsza wrażliwość na zmienność szczelin spawalniczych,
- możliwość uzyskiwania większych głębokości wtopienia,
- zmniejszona ilość wprowadzanego ciepła,
- mniejsza uciążliwość procesu dla środowiska i zmniejszenie zużycia energii,
- wysoka i stabilna jakość spoin oraz możliwość wykonywania złączy spawanych w każdej pozycji.
Zwarta, kompaktowa budowa głowicy hybrydowej (rys. 2) jest bardzo podatna na robotyzację procesu spawania technologią Super-MIG. Głowica ta jest przystosowana do współpracy ze sprzętem spawalniczym MIG/MAG, oferowanym przez czołowych, międzynarodowych producentów, takich jak Fronius, Lincoln, Esab i Miller.
Problem wyposażenia stanowiska
W niektórych przypadkach efektywne wykorzystanie technologii hybrydowych z zastosowaniem lasera wymaga stosowania robotów o podwyższonym udźwigu. Dzieje się tak np. wówczas, gdy masa głowic systemów laser–łuk kryty SAW, laser–tandem przekracza 20 kg. Wraz ze wzrostem gabarytów robota i jego udźwigu najczęściej zmniejsza się jego dokładność, a tym samym spada jakość prowadzenia głowicy hybrydowej po rowku spoiny. Przy dużych robotach mogą pojawić się również problemy ze sztywnością. Trudniej jest w nich realizować ruchy z nałożonymi, dynamicznymi oscylacjami o niewielkiej amplitudzie. Duże roboty są także droższe niż roboty małe. Pewnym rozwiązaniem może być stosowanie manipulatorów o podwyższonej dokładności, to jednak wymaga również zwiększonych nakładów na robota.
Patrząc na aspekt ekonomiczny rozwiązania, przeciętny koszt instalacji kompletnego systemu Super-MIG oraz Heavy Duty Super-MIG, przystosowanego do współpracy z robotem (fot. 2 i 3) jest kilkukrotnie mniejszy w porównaniu z systemami hybrydowymi z wykorzystaniem lasera. Do praktycznego zastosowania technologii Super-MIG lub Heavy Duty Super-MIG wystarczy robot o udźwigu 6 kg. Do tej klasy należą typowe, oferowane przez dostawców w dobrych cenach, roboty spawalnicze. Dla tych modeli ich producenci opracowali również szereg specjalnych rozwiązań do zastosowań spawalniczych, które bardzo dobrze sprawdzają się także w aplikacjach z plazmą.
Ekonomiczne rozwiązanie
Dotychczasowe badania porównawcze metody Super-MIG ze spawaniem łukiem krytym SAW wskazują na istotnie niższe koszty wytwarzania w przypadku stosowania technologii hybrydowej plazma-MIG/MAG. Spowodowane jest to m.in. zwiększeniem uzyskiwanych prędkości spawania, możliwością spawania w każdej pozycji, zmniejszeniem nakładów na przygotowanie detali (mniejsze fazy przy ukosowaniu krawędzi) oraz krótszym czasem obróbki przed i po spawaniu.
Czynniki ekonomiczne (zakup instalacji, koszt robota) oraz eksploatacyjne (koszty użytkowania) na obecnym etapie rozwoju technologii stanowią istotną przesłankę do prowadzenia prac badawczych oraz rozwoju, przy równoczesnym stosowaniu technologii spawania hybrydowego plazma-MIG/MAG na skalę przemysłową.
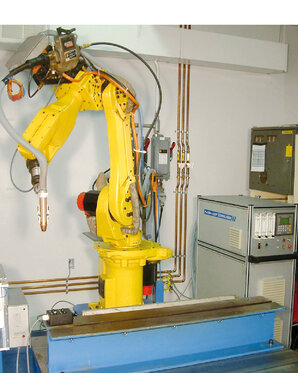
Fot. 3. System spawania hybrydowego Super-MIG firmy PLT. Hybrydowa głowica plazma-MIG/MAG, zainstalowana na ramieniu robota
Koncepcja modelowego zrobotyzowanego stanowiska spawania hybrydowego
Najlepszym, a często jedynym sposobem przekonania użytkownika o przewadze jednej technologii spawania nad inną, jest pokazanie efektów działania obu metod na konkretnym przykładzie. Wynika stąd bezpośrednia potrzeba prezentacji działającego rozwiązania, jak i możliwości realizacji na tym samym stanowisku spawania, przy wykorzystaniu różnych technologii. Dlatego w ramach realizacji projektu RobWeld Super-MIG przewidziano opracowanie modelowego, zrobotyzowanego gniazda spawalniczego (RWC, ang. Robotic Welding Cell), przystosowanego do pracy z technologią hybrydową Super-MIG oraz z klasyczną technologią MIG/MAG. W skład stanowiska wchodzą:
- robot KR 16-2F firmy KUKA – wersja przystosowana do pracy w warunkach podwyższonej temperatury, a jej nowy układ sterowania KRC4 umożliwia współpracę z dwoma zestawami spawalniczymi jednocześnie,
- zestaw spawalniczy Super Heavy Duty Super-MIG,
- zestaw spawalniczy MIG/MAG o wydatku nie mniejszym niż 400 A, z możliwością rozbudowy do 800 A,
- skaner laserowy TH6D (Scansonic), który umożliwia określenie położenia złącza spawanego przed spawaniem oraz śledzenie spoiny i korekcję trajektorii ruchu robota podczas spawania,
- stół spawalniczy,
- urządzenie wentylacyjno-odciągowe, lokalne, z możliwością przestawienia według aktualnych potrzeb,
- ogrodzenie w postaci ścian bocznych z szybami i lamelami spawalniczymi (dostęp do stanowiska od frontu jest zabezpieczony kurtyną świetlną),
- system bezpieczeństwa – sterownik bezpieczeństwa integrujący elementy i urządzenia bezpieczeństwa, zamontowany w szafie sterownika nadrzędnego stanowiska,
- akcesoria: sprzęgło kolizyjne, stacja czyszczenia palnika i obcinania drutu oraz elementy sygnalizacyjne.
Zestawione stanowisko było prezentowane podczas tegorocznych targów Expowelding w Sosnowcu. Po targach zostało ponownie uruchomione w laboratorium PIAP. W ramach projektu RobWeld planowane są próby spawania, które umożliwią porównanie efektywności technologii hybrydowej z klasyczną MIG/MAG.
Przykłady zastosowania hybrydowej technologii plazma-MIG/MAG
Głównymi obszarami potencjalnego zastosowania technologii spawania hybrydowego plazma-MIG/MAG), dającego najlepsze efekty dla grubych blach, są:
- przemysł stoczniowy, przemysł maszyn i urządzeń górniczych oraz maszyn budowlanych,
- produkcja elementów konstrukcyjnych dla budownictwa, produkcja elementów konstrukcyjnych i podzespołów dla energetyki oraz taboru kolejowego,
- motoryzacja – samochody osobowe i ciężarowe, autobusy itp.
Podsumowanie
Warto podkreślić, iż technologia hybrydowa plazma-MIG/MAG, w szczególności zastosowana na stanowisku zrobotyzowanym, jest rozwiązaniem stosunkowo nowym i na polskim rynku praktycznie nieznanym. Jej upowszechnienie jest jednym z celów projektu RobWeld Super-MIG. Został on ustanowiony w wyniku drugiego polsko-izraelskiego konkursu na projekty badawczo-rozwojowe, ogłoszonego przez Narodowe Centrum Badań i Rozwoju (NCBR) oraz Israel Industry Center for R&D (MATIMOP), w ramach Inicjatywy EUREKA. Koordynatorem projektu jest firma PLT, dostawca technologii. Partnerami są: Przemysłowy Instytut Automatyki i Pomiarów PIAP, dysponujący wiedzą, kompetencjami i wieloletnim doświadczeniem w zakresie robotyzacji procesów przemysłowych, w tym spawania, oraz firma SUPRA ELCO Jacek Szulc, wieloletni dystrybutor i dostawca zaawansowanych systemów spawalniczych, znający bardzo dobrze rynek krajowy i europejski. W ramach projektu opracowano rozwiązanie zrobotyzowanego gniazda spawania nowej generacji, wykorzystującego technologię Super Heavy Duty („SHD”) Super-MIG jako produktu gotowego do praktycznego zastosowania. Więcej informacji o samym projekcie i jego przebiegu można znaleźć na stronie
www.robweld.eu.
Artykuł powstał w toku realizacji projektu E!II/PL-IL/05/02/2013 „RobWeld Super-MIG Robotized Welding With Use of New Generation of Hybrid System Based on Super Heavy Duty Super MIG Concept”, w ramach Inicjatywy EUREKA przy dofinansowaniu przez Narodowe Centrum Badań i Rozwoju. Publikacja odzwierciedla jedynie stanowisko autorów. Komisja Europejska ani NCBR nie ponoszą odpowiedzialności za umieszczoną w niej treść merytoryczną, ani za sposób wykorzystania zawartych w niej informacji.
mgr inż. Jacek Szulc
SUPRA ELCO
mgr inż. Zbigniew Pilat
mgr inż. Łukasz Wojtczak
Przemysłowy Instytut Automatyki i Pomiarów PIAP
źródło: Przemysłowy Instytut Automatyki i Pomiarów PIAP
Komentarze
blog comments powered by Disqus