Jak wybrać sterownik PLC na bazie specyfikacji technicznej?
Z tego artykułu dowiesz się:
- jakie są rodzaje sterowników PLC,
- do jakich zastosowań wybrać konkretny sterownik PLC,
- jak dobrać sterownik na podstawie specyfikacji technicznej.
Analizując potrzeby polskich automatyków w zakresie systemów sterowania, można stwierdzić, że około 50% wszystkich systemów sterowania stanowią układy obsługujące do 256 sygnałów obiektowych. W nomenklaturze producentów systemów sterowania oznacza to systemy średniej wielkości. Dobór właściwego rozwiązania do takich układów nie zawsze jest oczywisty.
Instalacje obsługujące takie ilości sygnałów znajdujemy w każdej branży. Najczęściej sterują prostymi układami autonomicznymi (takimi jak maszyny), ale spotkać też je można przy obsłudze linii i ciągów technologicznych.
Każda instalacja ma swoje wymagania techniczne, dlatego należy przeanalizować dobierane rozwiązanie pod wieloma względami.
Podstawowe wymagania – konstrukcja sterownika
W przypadku małych i prostych układów, obsługujących minimalne ilości sygnałów IO, najlepszym rozwiązaniem będą kontrolery o budowie kompaktowej. Jedna zwarta konstrukcja upraszcza montaż urządzenia i zajmuje niewiele miejsca, jednak taka budowa ma też kilka ograniczeń.
Po pierwsze – konfiguracja wbudowanych sygnałów IO. Nie zawsze się okazuje, że ilość i typ wbudowanych sygnałów odpowiadają dokładnie potrzebom konkretnej instalacji. Oczywiście PLC o konstrukcji kompaktowej można rozbudować, ale bardzo często dochodzi do przewymiarowania układu. Dołożenie dodatkowego pomiaru analogowego może oznaczać dołożenie jednego modułu rozszerzeń, który w standardzie obsługuje 4 kanały.
Oczywiście od przybytku głowa nie boli i lepiej mieć kilka kanałów zapasowych, ale taka rozbudowa pociąga za sobą dodatkowe koszty. Sprawa komplikuje się jeszcze bardziej, gdy musimy obsługiwać sygnały obiektowe różnego typu: prądowe, napięciowe o różnych dokładnościach, temperaturowe przekaźnikowe, tranzystorowe… w takim przypadku dobór sterownika kompaktowego oraz modułów rozszerzeń będzie bardzo skomplikowany.
W takim modelu idealnie sprawdzą się sterowniki PLC o budowie modułowej. Ich konstrukcja pozwala bowiem na dokładanie takich rozszerzeń, jakie są niezbędne w systemie, unikając zbędnego przewymiarowania układu. Zaletą urządzeń o budowie modułowej jest bardzo duży wybór modułów rozszerzeń i możliwość korzystania z różnych modułów w ramach tego samego układu sterowania.
Dzięki temu możemy konfigurować każdy układ indywidualnie pod kątem potrzeb. Taki układ, w zależności od konfiguracji sygnałów IO, wychodzi często taniej niż konfiguracja alternatywna na kompaktowych modułach rozszerzeń i kompaktowych sterownikach PLC. Z tego powodu wielu klientów decyduje się na systemy sterowania o budowie modułowej. Dają większą elastyczność i łatwość na etapie doboru właściwego rozwiązania, jak i późniejszej rozbudowy, jeśli pojawi się taka konieczność.
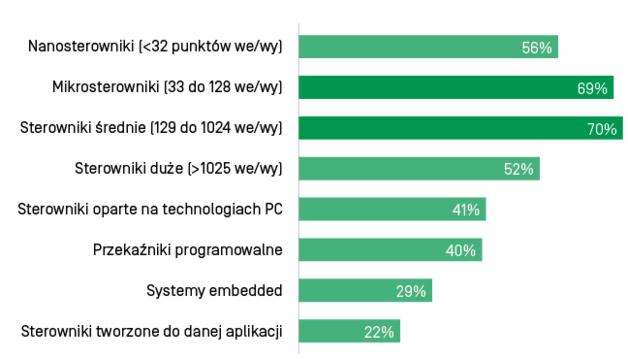
Dane z raportu Sterowniki programowalne – raport z polskiego rynku dystrybucji. Źródło: www.automatykab2b.pl
Architektura obiektu
To również bardzo ważny element podczas doboru właściwego systemu sterowania. O ile w małych maszynach, gdzie nie pojawia się konieczność układania długich kabli sygnałowych, sterownik kompaktowy może okazać się lepszym wyborem, o tyle w systemach rozproszonych obsługujących długie ciągi technologiczne – już nie do końca. Powody są dwa: koszty oraz zakłócenia.
Dobrej jakości kable sygnałowe do pomiarów analogowych są drogie. Im dalej pomiar od sterownika, tym koszt wyższy. Dodatkowo wymagają właściwego układania – tak, aby nie wpływały na nie zakłócenia (często konieczne jest stosowanie osobnych koryt kablowych), co również podnosi koszty.
Oczywiście długość kabla sygnałowego i sposób jego ułożenia w sposób bezpośredni przekładają się na jakość samego pomiaru. Często okazuje się, że zbyt długie kable oraz podatność na zakłócenia sprawiają, że pomiar „pływa”. Wpływa to niekorzystnie na algorytm sterujący.
Można sobie z tym oczywiście poradzić software’owo, włączając filtrowanie szumów i zakłóceń (jeśli PLC posiada taką funkcję), ale nie uchroni Cię to przed wyższymi kosztami. W przypadku, gdy system sterowania jest rozproszony, wygodniej zastosować sterowniki o budowie modułowej z możliwością podłączania oddalonych układów wejść-wyjść.
Taki układ może być zainstalowany blisko pomiarów – stosujemy krótsze kable sygnałowe i eliminujemy wpływ zewnętrznych zakłóceń na jakość pomiaru. Węzeł oddalony może zbierać wiele różnych sygnałów i przesyłać je do sterownika PLC przemysłową siecią komunikacyjną.
Komunikacja przemysłowa pomiędzy PLC a oddalonym układem wejść-wyjść jest bardzo odporna na zakłócenia, wymaga ułożenia tylko jednego kabla pomiędzy układem IO a PLC i pozwala na oddalenie układu na znaczną odległość od sterownika.
Możliwości komunikacyjne
To kolejny bardzo ważny element przy właściwym doborze systemu sterowania. Komunikacja w systemach sterowania jest podstawą do integracji całego układu, zarówno pod kątem obsługi urządzeń obiektowych jak i komunikacji między sterownikowej oraz z systemami nadrzędnymi.
Lokalnie – Modbus RTU
Jeśli poszukujesz sterowania do autonomicznego układu, wówczas należy się skupić na możliwościach komunikacyjnych PLC, które pozwolą podłączyć do niego inne urządzenia obiektowe, takie jak panele HMI, falowniki, serwonapędy, czytniki kodów kreskowych, wag, modemów, konwerterów i innych.
W tym celu PLC powinien być wyposażony w minimum port szeregowy RS232/RS485 z obsługą przemysłowych standardów komunikacyjnych takich jak Modbus RTU. To w dalszym ciągu najpopularniejszy protokół przemysłowy do szeregowej wymiany danych w systemie. Ma swoje zalety (popularność, łatwość implementacji), ale też i wady (ilość obsługiwanych urządzeń, maksymalna prędkość komunikacji).
Do układów wejść-wyjść w systemach rozproszonych: Profinet
Często okazuje się, że w przypadku systemów wymagających większych możliwości komunikacyjnych szeregowa wymiana danych jest niewystarczająca i należy przejść na Ethernet. Ta sieć jest obecnie najpopularniejszym medium wymiany danych w systemach automatyki. Sieć ta daje bardzo duże możliwości w zakresie ilości urządzeń, które można ze sobą połączyć, rozproszenia architektury oraz szybkości komunikacji.
Przyjęło się, że w aplikacjach o charakterze procesowym, natywną siecią do wymiany danych jest Profinet (następca bardzo popularnego Profibusa DP). Sieć Profinetowa wykorzystywana jest do łączenia systemu sterowania z oddalonymi układami wejść-wyjść oraz do komunikacji z urządzeniami polowymi. Gwarantuje czasy komunikacji na poziomie 1 ms, pozwala przesyłać dużo danych i – co bardzo ważne – może pracować w architekturze redundantnej, zabezpieczając układ przed awariami segmentów sieci, jak i całych węzłów oddalonych.
Profinet jest też bardzo wydajną siecią jeśli chodzi o architekturę, w jakiej można podłączać urządzenia – poczynając od tradycyjnej magistrali, przez gwiazdę, na ringu skończywszy. Profinet daje jeszcze jedną bardzo ważną funkcjonalność, a mianowicie możliwość zarządzania, programowania i konfigurowania wszystkich urządzeń na sieci z jednego miejsca, co ułatwia i przyspiesza prace serwisowe.
Kolejnym ważnym protokołem komunikacji na sieci Ethernet jest Modbus TCP, bardzo popularny standard u wszystkich dostawców automatyki, który pozwala integrować w jeden system różne urządzenia.
W systemach wieloprocesorowych: komunikacja EGD
W przypadku łączenia kilku sterowników ze sobą i tworzenia systemów wieloprocesorowych w ramach jednego układu, konieczne staje się stosowanie dedykowanych protokołów, które zapewnią szybką i niezależną wymianę danych pomiędzy PLC.
Jest to o tyle istotne, że w przypadku niezależnej komunikacji nie ma urządzenia, które zarządza całą komunikacją, a co za tym idzie – wyłączenie dowolnego urządzenia z sieci nie spowoduje utraty komunikacji pomiędzy urządzeniami pracującymi. W takich architekturach najlepiej sprawdzają się połączenia bazujące na UDP i wymianie danych typu peer-to-peer. Przykładem może być tutaj wymiana danych EGD (Ethernet Global Data), w której każde urządzenie generuje dane do wszystkich urządzeń i może odebrać dane od wszystkich urządzeń, które je generują. Daje to bardzo duże możliwości w zakresie budowania aplikacji rozproszonych z gwarancją pracy pomimo wyłączenia pojedynczych urządzeń.
Do warstwy SCADA: protokół OPC-UA
Jeszcze inny rodzaj komunikacji należy rozpatrzeć w chwili łączenia PLC do systemów nadrzędnych (np. SCADA). Tutaj przemysłowe protokoły wymiany danych, o których wspominaliśmy wcześniej, ustępują miejsca standardom OPC Unified Architecture (OPC-UA).
Jest to otwarty standard komunikacyjny, stosowany w automatyce przemysłowej i informatycznych systemach wyższych warstw (biznesowej i zarządzania, przedsiębiorstw przemysłowych). Wymiana danych w tym standardzie pozwala łączyć ze sobą różne platformy sprzętowe i systemy operacyjne, zapewniając wydajną wymianę danych oraz bezpieczeństwo komunikacji.
Bezpieczeństwo w kontekście łączenia systemów ze sobą i coraz częściej pojawiających się cyberataków staje się kluczowym aspektem w systemach sterowania w każdej branży. Wbudowane mechanizmy zabezpieczeń w OPC-UA wymagają w celu dostępu do danych – oprócz znajomości podstawowych parametrów komunikacyjnych, takich jak adres IP – podania także loginu oraz hasła, a przy najwyższym poziomie zabezpieczeń – również certyfikatów autoryzacyjnych.
W zdalnych dostępach: WebServer
Coraz częściej w aplikacjach sterujących pojawia się potrzeba dostępów zdalnych w celach serwisowych do oddalonych urządzeń. Dostępy takie realizowane są na 2 sposoby.
Pierwszy – to wbudowany w urządzenie webserver, który pozwala na dostęp do urządzenia, tablicy błędów oraz tablicy zmiennych. Dzięki temu masz dostęp na podstawowym poziomie do urządzenia w celu podglądnięcia podstawowych parametrów jego pracy.
Drugi model zakłada zdalne połączenie oprogramowaniem narzędziowym z oddalonym sterownikiem. Taki dostęp daje inżynierowi dokładnie takie same możliwości, jak przy bezpośrednim połączeniu PLC do programatora. Tutaj należy zwrócić szczególną uważną na kwestie bezpiecznego połączenia. Zdalny dostęp do urządzenia może generować ryzyko nieautoryzowanych dostępów i ingerencji w aplikację sterującą. Dlatego w takiej komunikacji stosujemy dedykowane routery, które mogą zestawiać połączenie VPN, gwarantując nam zabezpieczony kanał komunikacyjny.
Zobacz ofertę sterowników w naszym sklepie internetowym https://www.astor.com.pl/sklep/sterowanie/sterowniki-plc.html
Sprawdź bezpłatne kursy programowania sterowników na https://www.astor.com.pl/poradnikautomatyka/kursy/
źródło: Astor
Słowa kluczowe
ASTOR, automatyka, plc, Poradnik Automatyka, sterowanie, sterownik