Regulacja prędkości obrotowej silników elektrycznych
Tadeusz Minksztym (Danfoss Poland Sp. z o.o.) drukuj
Firma Danfoss specjalizuje się w produkcji wysokiej jakości napędów elektrycznych, stosowanych w przemyśle. Ich zastosowanie oraz regulacja prędkości obrotowej napędów maszyn przynosi często korzyści energetyczne, które można bardzo szybko zauważyć bezpośrednio na rachunku za prąd. W artykule opisujemy zabiegi, które warto zastosować, by zoptymalizować pracę napędzanych maszyn.
Nazwa Danfoss od lat jest synonimem przetwornic częstotliwości i softstartów o najlepszych parametrach technicznych, najwyższej niezawodności i funkcjonalności. Marka VLT to także gwarancja prawidłowego doboru komponentów napędu elektrycznego i redukcja kosztów eksploatacji.
Istnieje kilka podstawowych czynników, na które warto zwrócić uwagę w trakcie planowania wdrożenia lub modernizacji systemów napędowych. Odnoszą się one zarówno do sposobu działania silnika, jak i układu nim sterującego.
Oszczędność energii
W trakcie eksploatacji napędu elektrycznego, w zależności od charakterystyki momentu obrotowego obciążenia, mamy rożne poziomy możliwych do uzyskania oszczędności. W zastosowaniach z charakterystyką stałomomentową, oszczędność zużycia energii jest tylko wprost proporcjonalna do redukcji momentu i prędkości obrotowej na wale, podczas gdy w zastosowaniach ze zmiennym momentem o kwadratowej charakterystyce obciążenia, oszczędności te rosną w trzeciej potędze do zakresu zmniejszenia prędkości obrotowej.
Dostosowanie cos φ i obciążenia częściowe
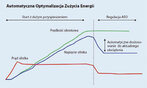
Rys. 1. Dopasowane strategie regulacji umożliwiają energetycznie optymalną pracę. W przetwornicach Danfoss wprowadzono sprawdzoną regulację AEO
Wiele przetwornic częstotliwości koryguje cos φ niemal do wartości 1 i redukuje w ten sposób indukcyjny pobór mocy biernej. Tym samym zmniejszają się straty w kablach zasilającym napęd. Warto też zauważyć, że współczynniki sprawności dla silników indukcyjnych trójfazowych podane są zazwyczaj tylko dla punktu nominalnego. Jeżeli silnik pracuje zasilany bezpośrednio z sieci z obciążeniem poniżej nominalnego, znacznie pogarsza się jego sprawność z powodu stałych strat mechanicznych i elektromagnetycznych. Praca z przetwornicą częstotliwości, w zależności od jakości metody regulacji, zapewnia zawsze optymalne namagnesowanie silnika. Z tego względu, przy zastosowaniu przetwornicy, współczynnik sprawności całego układu napędowego nie spada tak bardzo przy pracy z niedociążonym silnikiem. Wyczuwalną poprawę można zauważyć zwykle przy silnikach o mocy powyżej 11 kW.
Automatyczna Optymalizacja Zużycia Energii
W zastosowaniach, w których nie występują szybkie zmiany obciążenia, użytkownik może zastosować Automatyczną Optymalizację Zużycia Energii (AEO). Przetwornica obniża wówczas namagnesowanie silnika do optymalnego minimum. Efektem jest dodatkowa oszczędność zużycia energii, w stosunku do tej wynikającej ze zmniejszenia obrotów. Funkcja ta sprawdza się przy wszystkich powolnych regulacjach, jakie zwykle spotyka się w układach automatyki pomp i wentylatorów.
Zmniejszenie liczby cykli rozruchu
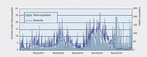
Rys. 2. Przykład praktyczny: po wprowadzeniu napędów z regulacją prędkości obrotowej w czwartym kwartale doszło do znacznej redukcji rozruchów, a tym samym mechanicznego obciążenia układu
Regulacja prędkości obrotowej może w wielu zastosowaniach zredukować liczbę uruchomień. Każdy nieregulowany rozruch silnika elektrycznego wymaga dodatkowej energii. W przypadku pomp zużycie energii na uruchomienie wynosi zazwyczaj 5–10 proc. całkowitego zużycia energii, ale istnieją przykłady na to, że na rozruch konieczne jest do 40 proc. energii. Ponadto zmniejszają się prądy szczytowe i obciążenia udaru mechanicznego przy rozruchu.
Inne korzyści z zastosowania regulacji prędkości obrotowej to dłuższy czas życia urządzeń z uwagi na zmniejszenie mechanicznego obciążenia jego komponentów. Wszystkie te możliwości dostępne są dzięki zintegrowanym funkcjom oprogramowania, zastosowanym w nowoczesnych przetwornicach częstotliwości.
Układy napędowe i stałomomentowa charakterystyka obciążenia
Do zastosowań z charakterystyką stałego momentu obciążenia należą takie, w których obciążenie nieznacznie zmienia się przy zmianie prędkości obrotowej w szerszym zakresie. Zaliczają się do tego m.in. podajniki linii produkcyjnych, taśmociągi, podnośniki, mieszadła i młyny.
Rozważając przykład aplikacji podajnika, gdzie korpus montowanego do samochodu silnika stoi na taśmie produkcyjnej, oczywiste jest, że ciężar korpusu jest zawsze taki sam, niezależnie od tego, czy taśma przesuwa się szybko czy wolno. Tym samym moment, potrzebny do poruszania tego bloku, jest zawsze taki sam. Oczywiście zmieniają się momenty tarcia i przyspieszenia, zależnie od stanu pracy, jednak zapotrzebowanie na moment obciążenia jest stałe. Moc, jakiej wymaga taki system, jest proporcjonalna do potrzebnego momentu obrotowego i prędkości obrotowej silnika. Jeżeli możliwe jest zmniejszenie prędkości obrotowej przy stałym obciążeniu, pojawią się bezpośrednio także oszczędności energetyczne.
Często ilość towaru transportowana na taśmie nie jest stała. Jeżeli prędkość taśmy dopasowana jest do transportowanej ilości materiału, umożliwia to nie tylko płynność i ciągłość transportu, lecz także oszczędność energii. Jeżeli jednak dopasowanie prędkości jest niemożliwe lub niepożądane, to i tak w przypadku większości przetwornic częstotliwości możliwe jest uzyskanie oszczędności.
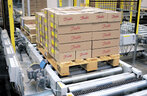
Rys. 3. Poprzez optymalizację momentu obrotowego i prędkości obrotowej można zwiększyć energooszczędność w wielu zastosowaniach ze stałym momentem obrotowym
Przetwornice regulują napięcie wyjściowe silnika, zależnie od obciążenia. Przetwornica częstotliwości zasila np. silnik 400 V w trybie jałowym, przy częstotliwości wyjściowej 50 Hz, często tylko napięciem 380 V. Przy wzroście obciążenia zaś podnosi wartość napięcia. Jakość takiej regulacji określana jest jakością przetwornicy. Same oszczędności energetyczne, jakie można uzyskać dzięki tej funkcji, nie wystarczają jednak do uzasadnienia inwestycji w przetwornicę częstotliwości.
Napędy z momentem obciążenia o charakterystyce kwadratowej
Układy regulacji obrotów pomp i wentylatorów to najczęstsze zastosowania napędów ze zmiennym momentem obciążenia o charakterystyce kwadratowej. W przypadku pomp należy jednak odróżnić szeroko rozpowszechnione pompy wirowe, mające zmienną charakterystykę momentu, od pomp mimośrodowych, próżniowych, bądź wyporowych, które mają moment obciążenia o stałym przebiegu.
Udział zastosowań pomp i wentylatorów jest ogromny. Około 70 proc. prądu używanego do celów przemysłowych w całej UE zużywają silniki elektryczne. Pompy i wentylatory mają w tym spory udział (37 proc.). W handlu, drobnej wytwórczości i sektorze usług, udział ten wynosi w całej UE nawet około 40 proc.
Prostą, ale bardzo efektywną metodą oszczędzania energii w maszynach przepływowych ze zmiennym momentem obciążenia jest regulacja prędkości obrotowej. Przy zmniejszeniu prędkości obrotowej, zapotrzebowanie na energię maleje aż w trzeciej potędze.
Ten wysoki potencjał oszczędności czyni wszystkie aplikacje z momentem o kwadratowym przebiegu idealnymi obiektami do rozpoczęcia działań, zmierzających do analizy energooszczędności. Dla uniknięcia niespodzianek przy regulacji prędkości obrotowej pomp i wentylatorów, użytkownik powinien w fazie projektowania pamiętać, że wraz ze zmianą prędkości obrotowej, zmienia się także punkt roboczy i tym samym współczynnik sprawności maszyny przepływowej.
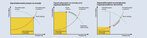
Rys. 4. Przy zmniejszeniu prędkości obrotowej następuje zmniejszenie zapotrzebowania na energię w funkcji trzeciej potęgi. Zastosowanie przetwornic częstotliwości do regulacji wentylatorów i pomp wirowych amortyzuje się tym samym w wielu zastosowaniach, już w ciągu niespełna dwóch lat
Zespół złożony z maszyny przepływowej i przetwornicy ze zmiennym zakresem prędkości obrotowej, to system, który oszczędza energię. Jeżeli różnica między maksymalną potrzebną mocą a przeciętną pracą z niedociążonym silnikiem jest zbyt duża, dobrym rozwiązaniem jest zastosowanie układu kaskadowego. Także przy przebudowie istniejącego już systemu takie inwestycje zwracają się po krótkim czasie.
W układzie kaskadowym pompa z regulacją prędkości obrotowej pokrywa zapotrzebowanie podstawowe. Z chwilą wzrostu zapotrzebowania przetwornica częstotliwości załącza kolejne pompy. W ten sposób pompy pracują przy swoim optymalnym współczynniku sprawności. Regulacja pompy zapewnia zawsze najlepsze pod względem energetycznym wykorzystanie układu. Taki sam układ może być analogicznie zastosowany do zespołu wentylatorów. W zależności od producenta i wersji, odpowiednie regulatory kaskady są już wbudowane w przetwornicy lub są dostępne jako moduły zewnętrzne.
Szczególne cechy maszyn przepływowych
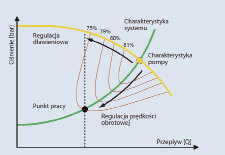
Rys. 5. Na wykresie charakterystyk, obok charakterystyki pompy i systemu, pokazano także kilka krzywych granicznych współczynnika sprawności. Zarówno przy regulacji dławieniem, jak i przy regulacji zmianą prędkości obrotowej, punkt roboczy wychodzi poza optimum współczynnika sprawności
W przypadku większości układów pompowych lub wentylatorowych zastosowanie znajdują klapy, żaluzje, zawory dławiące bądź zawory trójdrogowe, które służą do regulacji ciśnienia lub wielkości przepływu. Jeżeli regulacja pompy wirowej odbywa się za pomocą zaworu, poprzez dławienie, punkt roboczy przesuwa się wzdłuż krzywej charakterystyki pracy pompy. Dochodzi jedynie do minimalnej redukcji potrzebnej energii, w porównaniu z zapotrzebowaniem dla znamionowego punktu pracy pompy. W przypadku regulacji wydajności pompy za pomocą zmiany prędkości obrotowej, punkt roboczy przesuwa się wzdłuż krzywej charakterystyki systemu. Przy takim sposobie regulacji zapotrzebowanie na energię spada w trzeciej potędze, w porównaniu z regulacją dławieniem. Przykładowo przy połowie prędkości obrotowej pompa potrzebuje tylko jednej ósmej mocy.
Przez analogię odnosi się to także do wentylatorów i wszystkich innych typów pomp ze zmiennym, kwadratowym przebiegiem charakterystyki momentu obciążenia. Na rysunku 5., obok krzywej charakterystyki pompy i systemu, narysowano także krzywe graniczne współczynnika sprawności. Można dzięki temu zauważyć, że zarówno przy regulacji dławieniowej, jak i regulacji zmianą prędkości obrotowej, punkt roboczy wychodzi z optimum współczynnika sprawności. Z przedstawionej specyficznej krzywej zużycia energii (rys. 6. – dotyczy tylko wybranej pompy) można odczytać wpływ regulacji na zmianę współczynnika sprawności pompy. Od 32 Hz w dół dodatkowe straty pompy zaczynają przewyższać oszczędności zużycia energii w stosunku do pracy z nominalnymi parametrami (zasilanie bezpośrednie 50 Hz). W rozpatrywanym urządzeniu energetycznie optymalna częstotliwość wynosi zatem 38 Hz.
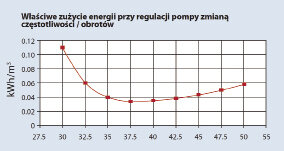
Rys. 6. Krzywa przedstawia zużycie energii wybranej pompy, przy regulacji prędkości obrotowej. Przy częstotliwości poniżej 32 Hz dodatkowe straty pompy przewyższają oszczędności. W przedstawionym urządzeniu optymalna energetycznie częstotliwość wynosi więc 38 Hz. Gdyby pompa nie miała regulacji prędkości obrotowej, bilans energetyczny byłby znacznie gorszy
Gdyby pompa nie umożliwiała regulacji prędkości obrotowej, bilans energetyczny byłby znacznie gorszy. W praktyce okazuje się, że właśnie maszyny przepływowe często nie zawsze pracują (nie mogą pracować) w optymalnym punkcie roboczym. Przykładowo, urządzenia klimatyzacyjne muszą latem wykonać większą pracę niż zimą. Ponieważ jednak system musi być zaprojektowany dla maksymalnego zapotrzebowania mocy, skutkuje to nieuchronnie wysokim udziałem czasu pracy układu poniżej parametrów nominalnych.
Fakt ten uwzględniają tylko niektórzy producenci układów pompowo–wentylatorowych. Projektują oni system tak, aby zachować rezerwę dla krótkich okresów zapotrzebowania maksymalnej wydajności, ale jednocześnie ustalając optimum sprawności tak, by odpowiadało około 70 % wydajności pompowania.
Podsumowanie
Aby osiągnąć sukces przy realizacji projektów oszczędzania energii, warto zasięgnąć porady specjalistów w tej dziedzinie. Mają oni niezbędne doświadczenie, które pozwala na ominięcie niebezpieczeństw na drodze do zwiększenia efektywności energetycznej i obliczenia maksymalnych oszczędności dla użytkownika. Danfoss oferuje zarówno doradztwo na etapie przygotowania projektu, jak i na etapie wdrożenia i oddania do ruchu.
Tadeusz Minksztym
źródło: Danfoss
Komentarze
blog comments powered by Disqus