Druk 3D w przemyśle. Najnowsze trendy i sposoby wykorzystania
dr inż. Maciej Cader (Łukasiewicz – PIAP) drukuj
W nomenklaturze dotyczącej wytwarzania przyrostowego coraz częściej i naprzemiennie pojawiają się dwa pojęcia: druk 3D (3D Printing) i wytwarzanie addytywne (Additive Manufacturing). To jednak nie to samo. Zgodnie z wytycznymi Amerykańskiego Narodowego Instytutu Normalizacyjnego pojęcie druku 3D (drukowanie 3D) odnosi się tylko i wyłącznie do technologii i maszyn powiązanych z produkcją przez nakładanie materiału na stół modelowy maszyny. Natomiast technologie przyrostowe (wytwarzanie przyrostowe/addytywne) to pojęcie związane ze wszystkimi technikami, dzięki którym budowanie odbywa się przez łączenie lub obróbkę materiału rozprowadzanego na stole modelowym maszyny. A zatem o każdej technologii związanej z budowaniem produktów warstwa po warstwie można powiedzieć technologia addytywnego wytwarzania, ale już nie każda technologia może być nazwana drukiem 3D.
Bez względu na to czy mówimy o druku 3D, czy o technologiach wytwarzania przyrostowego obecnie obserwuje się dynamiczny rozwój tego obszaru nauki i technologii. Można zidentyfikować kilka kluczowych trendów – łączenie technik wytwarzania i procesów, coraz większą modułowość maszyn, wytwarzanie wielkoseryjne i adaptację technik addytywnych na potrzeby wykorzystania w wybranych branżach przemysłu. Co roku we Frankfurcie na Menem odbywa się najważniejsza w Europie impreza targowa połączona z konferencją – FORMNEXT, w ramach których prezentowane są przemysłowe rozwiązania z zakresu technologii przyrostowych i druku 3D – maszyny, systemy, studia przypadków, materiały. Przez ostatnie trzy lata FORMNEXT zdominowały technologie przetwórstwa metali – SLS, DMLS, SLM, EBM, LENS. Światło dzienne ujrzało kilka ciekawych nowości, w tym nowatorskich prototypów maszyn. W branży rysuje się wyraźna tendencja tworzenia maszyn i systemów szytych na miarę potrzeb konkretnych branż przemysłu, np. lotniczego czy samochodowego, a także produkcji form wtryskowych. Rozwój maszyn zmierza do poprawy jakości powierzchni zewnętrznych wytwarzanych części, jednorodności struktur wewnętrznych (dążenie do izotropii) oraz skrócenia czasu i zachowania ciągłości wytwarzania. Można wysnuć tezę, że obecnie żadna z dostępnych technologii addytywnych nie spełnia w pełni wszystkich tych wymogów równocześnie. Dlatego branża coraz śmielej patrzy w kierunku rozwiązań hybrydowych, które zamykają w jednej maszynie kilka procesów lub technologii. Jednym z reprezentatywnych przykładów jest maszyna hybrydowa LASERTEC 65 3D (fot. 1).
LASERTEC 65 3D, której szczegółowe parametry można znaleźć na stronie producenta DMG Mori jest maszyną łączącą w sobie dwie technologie – napawania sproszkowanego metalu oraz obróbki skrawaniem. Maszyna bazuje na budowaniu modeli 3D przez napawanie proszków metali na zamocowany uprzednio detal. Następnie naddatek jest obrabiany za pomocą odpowiednich mikrofrezów. Jak podkreśla producent maszyna została wyprodukowana z myślą o regeneracji zużytych/uszkodzonych podzespołów maszyn, np. łopatek turbin energetycznych, ślimacznic itp.
Kolejnym przykładem wytwórczego centrum hybrydowego jest maszyna MetalFAB1 (fot. 3). Producent przyjął strategię budowy modułowej, rozszerzając ją zgodnie z wymogami kompletnego ciągu produkcyjnego. Pomysł na MetalFAB1 powstał w związku z rozpoczęciem wygasania w 2014 r. patentów na technologię spiekania proszku laserem, co umożliwiło firmie Additive Industries komercyjne wykorzystanie podstaw tej technologii w systemie MetalFab1. Oprócz zintegrowanego komputera pozwalającego na akwizycję i obróbkę modeli CAD prezentowana wersja maszyny ma dwie komory do selektywnego, wielolaserowego spiekania proszku metali, komorę do relaksacji modeli oraz komorę do piaskowania modeli. Dzięki temu MetalFAB1 zapewnia kompleksową realizację pełnego cyklu produkcyjnego – od załadowania referencyjnego modelu CAD 3D części przeznaczonej do produkcji, aż po proces obróbki uszlachetniającej powierzchnię zewnętrzną w pełni gotowego izotropowego modelu.
Przykładem innej bardzo ciekawej hybrydy jest przedstawiciel japońskiej firmy Matsuura – urządzenie Lumex Avance-25 (fot. 4). To maszyna reprezentatywna pod względem łączenia dwóch technik produkcji: obróbki skrawaniem oraz selektywnego spiekania proszków metali.
W przypadku maszyny LUMEX proces budowania modelu (jeden cykl) składa się z czterech etapów. W pierwszym etapie zgarniacz maszyny rozprowadza metalowy proszek na stole modelowym, na wysokość jednej warstwy (tj. ok. 0,05 mm). Następnie – w drugim etapie – maszyna uruchamia laser sterowany układem zwierciadeł i kontrolowany przez system wizyjny bazujący na kamerze CCD, który jest ogniskowany na rozprowadzonym proszku. W trzecim etapie dochodzi do selektywnego spieczenia proszku i połączenia go, także z warstwą poprzednią. Po 10 powtórzeniach – po zbudowaniu 10 warstw – następuje uruchomienie etapu czwartego: obróbki skrawaniem powierzchni zewnętrznych zbudowanego modelu za pomocą mikrofrezu.
Technologia, choć umożliwia budowanie dowolnych modeli, została wymyślona przede wszystkim jako narzędzie do produkcji form wtryskowych z kanałami chłodzącymi idealnie dopasowanymi do geometrii ścian formy. Lumex Avance-25 to przykład maszyny wskazującej kolejny trend, tj. produkcję narzędzi – w tym wkładek do form lub kompletnych form wtryskowych – głównie w obszarze tzw. chłodzenia konformalnego wyprasek.
Od niedawna coraz więcej mówi się w branży technologii addytywnych o wytwarzaniu gotowych narzędzi produkcyjnych, w tym form wtryskowych z optymalnie ułożonymi kanałami chłodzącymi.
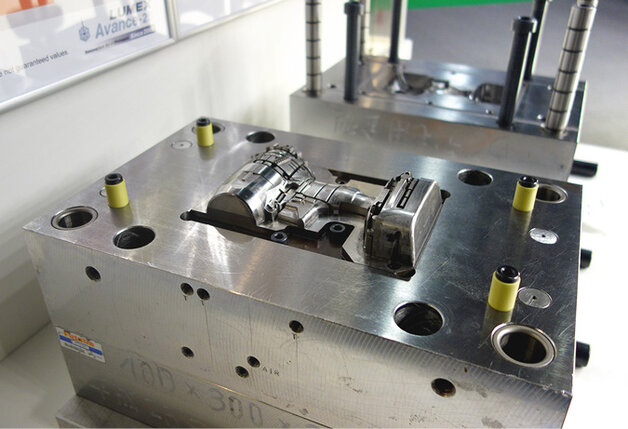
Fot. 6. Forma wtryskowa w całości wytworzona na hybrydowym centrum do addytywnego wytwarzania i obróbki skrawaniem – LUMEX Avance-25
Jedną z firm, w której docelowo stosuje się drukowane narzędzia wytwórcze (formy) jest niemiecka spółka Robert Seuffer, produkująca podzespoły elektroniczne, m.in. czujniki i sterowniki. Firma wzbogaciła proces kontroli jakości o badania wyprasek testowych w celu sprawdzenia poprawności dopasowania i funkcjonalności potencjalnego nowego produktu, który będzie wytwarzany docelowo metodą wtrysku z form metalowych. Wprowadzając rozszerzenie kontroli jakości, zarząd spółki był szczególnie zainteresowany znalezieniem alternatywnej metody do standardowej (produkcja niskowytrzymałych form z aluminium), która pozwoliłaby przyspieszyć proces i zmniejszyć liczbę iteracji projektowych. W tym celu wykorzystano właśnie technologię addytywną PolyJET jako technologię Rapid Tooling – bezpośredniego wytwarzania narzędzi, czyli form wtryskowych. Firma bardzo szybko dokonała zestawienia korzyści wynikających z wykorzystania metody PolyJET w stosunku do metody tradycyjnej. Czas produkcji gotowej formy, od momentu zaprojektowania do momentu wykonania pierwszego wtrysku, wynosił średnio 56 dni i kosztował firmę 52 725 dolarów. Ta sama forma wytworzona przy wykorzystaniu technologii PolyJET była gotowa do procesu wtryskiwania po dwóch dobach, a koszt wytworzenia wyniósł 1318 dolarów. To najlepiej pokazuje pole do wykorzystania technologii addytywnej i drukowanych w 3D form niskoseryjnych.
Nie bez znaczenia jest kolejna zaleta wynikająca z zastosowania technik addytywnych – optymalne chłodzenie wyprasek. Chłodzenie konformalne, bo o nim mowa, to takie, w którym kanały chłodzące mają taki sam kształt jak gniazdo formy, co przedstawiono na fot. 8. Powołując się na dane udostępnione przez firmę FADO, która stosuje technologię addytywną DMLS (technologia bezpośredniego spiekania proszków metali) do produkcji form, chłodzenie formy zajmuje 70% czasu cyklu wytwórczego (fot. 9), a więc jest etapem najbardziej czasochłonnym w całym procesie, wymagającym optymalizacji.
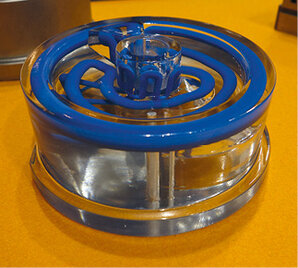
Fot. 8. Elementy form z chłodzeniem konformalnym wytworzone w technologiach addytywnych: DMLS (po prawej – gotowe produkty) oraz PolyJET Matrix (po lewej – prototypy do weryfikacji); źródło: zasoby własne (targi Formnext 2016)
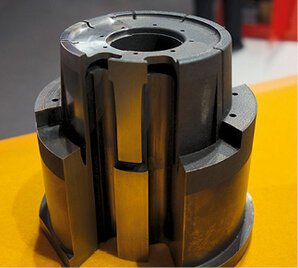
Fot. 8. Elementy form z chłodzeniem konformalnym wytworzone w technologiach addytywnych: DMLS (po prawej – gotowe produkty) oraz PolyJET Matrix (po lewej – prototypy do weryfikacji); źródło: zasoby własne (targi Formnext 2016)
Niestety wytwarzanie form z chłodzeniem konformalnym nie jest tak prostym i intuicyjnym procesem, jak mogłoby się wydawać. Obecnie projektanci borykają się z czterema istotnymi problemami, których rozwiązanie jest istotne dla rozwoju technik addytywnych do produkcji tego typu narzędzi:
- stosunkowo wysoka chropowatość ścian kanałów chłodzących, która powoduje zmniejszenie czasu korodowania ścian, co przekłada się na spadek efektywności chłodzenia,
- niepewność w zakresie stałości wymiarów średnicy kanału chłodzącego na całej jego długości,
- konieczność wyeliminowania struktur wspierających ściany kanału
- i/lub eliminacji niespieczonego proszku metalicznego,
- efektywne czyszczenie kanałów.
Obecnie optymalne wydaje się produkowanie form przy użyciu metod addytywnych oraz obróbki skrawaniem jednocześnie. Studium takiego przypadku udostępnione przez firmę Fado zaprezentowano na fot. 10.
Mówiąc o przyszłości i trendach w branży technik addytywnych i druku 3D, nie można nie wspomnieć o fabrykach przyszłości.
Nowa, zintegrowana koncepcja maszyny pod hasłem „fabryka jutra” zapowiada nowy poziom technik addytywnych pod względem jakości, elastyczności i zwiększenia wydajności. Trendy zmian dotyczących rozwiązań dla maszyn i technologii widać przede wszystkim w obszarze spiekania proszków metali, a bazują one na takich założeniach jak „więcej źródeł laserowych”, „więcej mocy lasera”, „szybsze budowanie” i „rozszerzenie wymiarów przestrzeni roboczych”. W ten sposób jeden z pionierów idei „fabryki przyszłości bazującej na technikach addytywnych” – firma Concept Laser, obecnie stanowiąca część koncernu GE (GE Additive) – likwiduje przestoje, synchronizuje maszyny, a także optymalizuje ich ułożenie w celu poprawy efektywności produkcji i wykorzystania przestrzeni fabryki związanej bezpośrednio z procesami towarzyszącymi technologiom addytywnym.
Firma opracowuje techniki mające na celu optymalne przygotowanie procesu addytywnego – optymalizacja rozkładu struktur wspierających, postprocesing polegający na usuwaniu struktur wspierających, relaksacja po wytwarzaniu, uszlachetnianie powierzchni, ale także zautomatyzowany przepływ materiałów wsadowych do maszyn, co wyraźnie zmniejsza obciążenie operatorów oraz integracji z systemami standardowymi (obróbka skrawaniem). Głównym założeniem jest znaczne zwiększenie stopnia sprawności i dostępności systemu produkcyjnego przy jednoczesnym wyraźnym zmniejszeniu ilości wymaganej przestrzeni w hali produkcyjnej. Symulowane scenariusze produkcyjne pokazują, że przestrzeń może być zmniejszona nawet o 85% w stosunku do obecnej. Ponadto firma pracuje nad zwiększeniem mocy laserów. Na razie została ona zwiększona siedmiokrotnie (na m2) przy jednoczesnej możliwości multiplikacji. Maszyny umożliwiają opcjonalne podłączanie dwóch lub czterech laserów o mocy 400–1000 W.
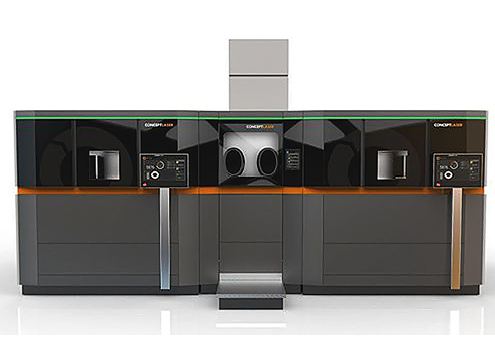
Fot. 12. Zintegrowane centrum wytwarzania (dwie komory po prawej i lewej stornie) połączonego z komorą postprocesingu według założeń firmy Concept Laser
Firma Concept Laser proponuje również, aby maszyny nie miały na stałe wbudowanych stołów modelowych i zasobników na materiały modelowe. Stoły modelowe i zasobniki umieszczone są na specjalnych modułach umożliwiających ich transport w samojezdnych, autonomicznych wózkach. Po zrealizowanym procesie wydruku maszyna wysyła sygnał do wózka, a wózek po odebraniu sygnału dokuje się w maszynie w celu podjęcia modułu ze stołem modelowym (i wytworzoną częścią) oraz zamocowaniu nowego stołu modelowego. Analogicznie sprawa wygląda w sytuacji, kiedy kończy się materiał (proszek) modelowy. Koncepcja służy utrzymaniu ciągłości procesów produkcyjnych w fabryce, bez konieczności obsługi przez człowieka – wymiana materiałów, przygotowanie stołu modelowego, uruchomienie procesu. Pobrany stół modelowy wraz z detalem może być przewieziony do innej maszyny (np. piaskarki) lub przetransportowany w inne, wyznaczone miejsce fabryki (np. spawalnia, magazyn).
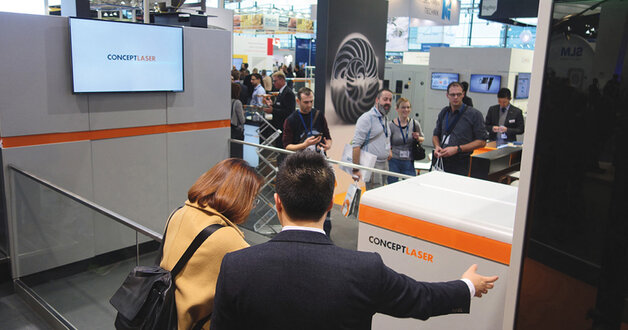
Fot. 14. Stoisko Concept Laser obrazujące ideę modułowej fabryki przyszłości według założeń Concept Laser
Wizje fabryki przyszłości bazującej na technikach addytywnych przekładają się na wielkość i szacowany przebieg maszyn. Amerykański potentat w świecie wytwarzania przyrostowego z uplastycznionych polimerów przemysłowych – firma Stratasys – już kilka lat temu zademonstrowała dużą maszynę produkcyjną FORTUS 900mc (fot. 14) – centrum produkcyjne dla „fabryki przyszłości”. Maszyna została zaprojektowana z myślą o użyteczności w małoseryjnej produkcji, a ze szczegółowymi danymi można zapoznać się na stronie producenta.
Do zalet maszyny należą: komora o wymiarach 914 mm × 610 mm × 914 mm, układy napędowe oparte na śrubach kulowych (a nie paskach, jak to ma miejsce standardowo) oraz możliwość ładowania powiększonych kaset materiałowych pozwalających na 400 godzin pracy bez nadzoru człowieka.
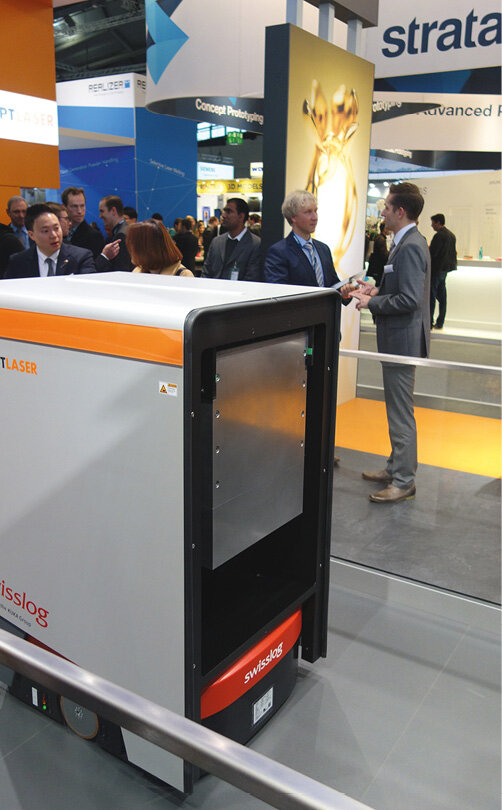
Fot. 15. Stoisko Concept Laser – modułowa fabryka przyszłości; po lewej: samojezdny wózek pobierający moduł stołu modelowego z maszyny addytywnej; po prawej: wózek podczas przejazdu z widocznym portalem modułowym
Kilka lat później, po mariażu Stratasys z izraelską firmą Objet na rynku pojawiła się kolejna maszyna – Objet1000 (fot. 15), największa na świecie maszyna pracująca w technologii PolyJET z komorą 1000 mm × 800 mm × 500 mm, która bazuje na produkcji wielkogabarytowych modeli z żywic światłoutwardzalnych. Szczegóły dotyczące tej maszyny można znaleźć na stronie internetowej producenta.
Do tej pory potentaci druku 3D przedstawiali wizję fabryki jako pomieszczenie, w którym znajduje się duża liczba pracujących maszyn produkcyjnych. Dziś ten trend zaczyna ewoluować – powstają rozwiązania systemowe, czyli hybrydy, w ujęciu oprogramowania i sprzętu. Takimi przykładami dużych, niezależnych maszyn są właśnie wspomniane FORTUS 900mc oraz Objet1000.
Najnowsze źródła pokazują, że dynamiczny rozwój technologii wytwarzania przyrostowego i druku 3D sprawia, iż stają się one coraz poważniejszą alternatywą dla konwencjonalnych technologii wytwarzania. Technologie te są coraz powszechniej stosowane do coraz bardziej wymagających zadań, takich jak produkcja funkcjonalnych części (33,8%) czy produkcja narzędzi i wzorców, w tym wkładek i form wtryskowych (23,1%). Nie bez znaczenia jest także rosnące użycie technologii addytywnych i druku 3D w procesach montażu (16%). Na podstawie analizy trendów rozwoju technik addytywnych oraz druku 3D, należy się spodziewać, że dynamika wzrostu ich stosowania do coraz bardziej wymagających zadań i w coraz większym wolumenie produkcji będzie gwałtownie rosnąć.
Jak obniżyć koszty prototypowania i produkcji dzięki drukowi 3D?
Monika Gawryś, menedżer produktu igubal, igus Polska
Druk 3D to technologia, która rozwija się i będzie mocno się rozwijać w najbliższych latach. Co ważne Polska jest bardzo ważnym punktem na mapie tej technologii, ponieważ z jednej strony mamy światowej klasy producentów drukarek 3D, a z drugiej dynamicznie rosnące – również nowe – obszary, w których znajduje ona zastosowanie. Jako producent filamentów możemy podać jeden z najnowszych przykładów, który rewolucjonizuje branżę prototypowania i próbnych serii. W ostatnich latach wprowadziliśmy na rynek nowoczesną metodę prototypowania części wykonanych z naszych materiałów ślizgowych iglidurów, pozwalającą na znaczne obniżenie kosztów uruchomienia produkcji mało- i średnioseryjnej. Polega ona na wtryskiwaniu polimerów do form wtryskowych, wykonanych technologią druku 3D, metodą SLS. Dzięki temu mogą powstawać niskokosztowe elementy końcowe dla producentów wielu branż – od spożywczej, przez meblarską czy tekstylną, po urządzenia medyczne, maszyny rolnicze, samochody, samoloty lub urządzenia do pracy pod wodą, które muszą być wyposażone w niekorodujące ruchome elementy z tworzyw.
Drukowane formy wtryskowe nie są oczywiście aż tak trwałe, jak tradycyjne stalowe, ale umożliwiają produkcję krótkich serii (od kilku do kilkuset sztuk elementów) z tych samych, trwałych tworzyw, z jakich wytwarza się je w tradycyjnej technologii. Stosując tę metodę można tworzyć elementy prototypowe, które wyglądają, zachowują się i są równie trwałe, jak docelowe. Co istotne zastosowanie takich form powoduje, że proces prototypowania staje się nawet do 80% tańszy od tego z użyciem form tradycyjnych. To otwiera przed producentami nowe możliwości. Nie muszą już inwestować dużych kwot w uruchomienie produkcji z użyciem, tradycyjnych stalowych form wtryskowych, które kosztują co najmniej kilka tysięcy euro. Mogą więc znacznie obniżyć koszt etapu prototypowania i sprawdzania czy dane urządzenie działa i czy przyjmie się na rynku. Taki system świetnie wpisuje się w wymagania coraz bardziej zindywidualizowanego współczesnego rynku.
Polska wytycza kierunki rozwoju w branży druku 3D
Michał Melon, Chief Operating Officer, UBOT 3D
Obecnie na rynku można wybierać spośród co najmniej kilkunastu technologii druku 3D. Różnice między nimi polegają przede wszystkim na doborze materiałów, z których otrzymuje się wydruki. Największy udział rynkowy zajmuje technologia
FDM/FFF czyli druk z termoplastów o różnych właściwościach. W technologii FDM/FFF można drukować z termoplastów odpornych na temperaturę 125 °C – nylon(PA), o właściwościach elastycznych – guma(TPU), odporny na warunki atmosferyczne – ASA, oraz z popularnego ABS-u i wielu innych. Rozwój tej technologii zmierza w trzech głównych kierunkach. Pierwszym jest poszerzenie gamy materiałów, wykorzystywanych w druku 3D, o nowe termoplasty o innych właściwościach chemicznych i mechanicznych. Drugi kierunek polega na zwiększaniu jakości i optymalizowaniu czasu współpracy użytkownika z drukarką, a trzeci na skracaniu czasu wydruku. Dzięki temu drukarki 3D coraz częściej zastępują tradycyjne metody wytwarzania prototypów oraz umożliwiają wydruk detali spersonalizowanych bez zwiększania kosztów produkcji.
W ostatnim czasie pojawia się na rynku coraz więcej udogodnień związanych raczej z procesem druku 3D niż z samą maszyną. Powstają np. urządzenia, które pomagają w obróbce detalu – w tzw. post-processingu. Niektóre z nich są już na tyle zautomatyzowane, że za pomocą jednego kliknięcia jesteśmy w stanie obrobić detal. Kolejnym przykładem rozwoju w tym kierunku są zmiany w oprogramowaniu drukarek, które ułatwiają operatorowi pracę, tak aby obsługa odbywała się w możliwie najprostszy i najbardziej efektywny sposób. Dzięki temu w tym samym momencie może on sterować z jednego komputera wieloma maszynami.
Polska niewątpliwie należy do krajów o największej liczbie producentów drukarek 3D. Coraz częściej jesteśmy autorami innowacyjnych rozwiązań na skale globalną. Druk 3D w naszym kraju cały czas prężnie się rozwija i kształtuje rynek w coraz większym stopniu samodzielnie, ograniczając wpływy z zagranicy, a polskie drukarki 3D są rozpoznawalne na całym świecie.
Wytwarzanie przyrostowe redukuje ograniczenia w produkcji
Bogdan Dąbrowski, specjalista ds. systemów wytwarzania przyrostowego Renishaw
Od kilku lat obserwuje się wzmożone zainteresowanie wykorzystaniem technologii wytwarzania przyrostowego w produkcji części metalowych w różnych gałęziach przemysłu. Widoczne jest to zwłaszcza w przypadku takich aplikacji, jak narzędziowe (formy wtryskowe oraz wkładki z konformalnymi kanałami chłodzącymi), motoryzacyjne czy lotnicze. Coraz częściej mamy również do czynienia z drukowaniem medycznych wyrobów stomatologicznych i implantów ortopedycznych.
Technologia wytwarzania przyrostowego znacznie redukuje ograniczenia dotyczące produkcji elementów trójwymiarowych. Swoboda projektowania i wytwarzania w druku 3D umożliwia wykonanie w pełni funkcjonalnych części o zoptymalizowanej strukturze i kształtach, które w przypadku klasycznych technologii obróbki metalu byłyby trudne lub niemożliwe do osiągnięcia. Wykorzystując druk 3D w wytwarzaniu części z proszku metalu, znacząco zmniejsza się straty materiałowe, a także wyklucza konieczność stosowania dodatkowych narzędzi, ich mocowania i pozycjonowania. Nie bez znaczenia pozostaje również aspekt nakładów finansowych ponoszonych przy wdrażaniu nowych produktów.
Techniki druku 3D umożliwiają szybką walidację iteracyjnych zmian (dokonanych za pomocą komputerowej optymalizacji topologicznej) konstrukcji części, co znacząco skraca proces wdrożenia nowych wyrobów do produkcji. Źródłem korzyści jest możliwość ewolucji, jak również optymalizacji modelu biznesowego, przez wykorzystanie szerokiego spektrum zalet wytwarzania przyrostowego celem dostosowania wyrobu do indywidualnych potrzeb klienta.
źródło: Automatyka 11/2018
Komentarze
blog comments powered by Disqus