Monitoring i zdalne sterowanie w systemach automatyki przemysłowej
Marcin Bieńkowski drukuj
Współczesne systemy sterowania w rozwiązaniach automatyki przemysłowej rzadko są projektowane w postaci autonomicznych układów sterujących pojedynczym elementem linii czy jednym podzespołem maszyny. Zazwyczaj są one połączone ze sobą wzajemnie, jak i, w zależności od rozwiązania, ze sterującym elementem nadrzędnym, odpowiednio dobraną do potrzeb magistralą danych. W ten sposób tworzą one jednolity, scentralizowany lub rozproszony system sterowania linią produkcyjną, fabryką, gniazdem bądź całym urządzeniem.
Linie produkcyjne, obrabiarki numeryczne czy zrobotyzowane gniazda, z punktu widzenia monitoringu i sterowania, mają w pewnym sensie charakter modułowy. Moduły odpowiadają tu różnym etapom procesu technologicznego – np. stanowisko zaopatrzenia materiałowego, stanowisko montażowe, system zasilania, system podawania narzędzi, stanowisko odbioru gotowych wyrobów, system sterowania, urządzenia pomiarowe itp. Tak zorganizowany układ można zautomatyzować posługując się modelem sterowania rozproszonego lub scentralizowanego. Zacznijmy od systemu rozproszonego.
Sterowanie rozproszone
Sięgając do literatury, rozproszony system sterowania DCS (Distributed Control System) zdefiniowany jest jako system odpowiadający za sterowanie i wizualizację procesu przemysłowego, który, w przeciwieństwie do scentralizowanych systemów SCADA i PLC, o czym za chwilę, wykorzystuje wspólną bazę oznaczonych specjalnymi znacznikami urządzeń (np. unikatowym numerem lub symbolem), a także danych wykorzystywanych do sterowania i wizualizacji. Dzięki temu poszczególne elementy mogą jednoznacznie i wzajemnie określić w systemie DCS realizowane aktualnie zadania „nie wchodząc sobie w drogę”, a system wizualizacji oraz oprogramowanie aplikacyjne dokładnie zidentyfikują dany element urządzenia wysyłając odpowiednie rozkazy sterujące.
W systemach DCS urządzenia wykonawcze, np. zawory, czujniki czy falowniki podłączone są do tzw. stacji procesowych. Stacje te sterują automatyką w obrębie swoich modułów i z reguły pozbawione są funkcji wizualizacyjnych i operatorskich. Ze względu na wąski zakres zadań wykonywanych w obrębie pojedynczego modułu, zastosowane w stacjach procesowych sterowniki charakteryzują się względnie niską wydajnością, a dzięki temu niższą ceną. Aby zachować właściwą synchronizację w momencie włączenia/wyłączenia linii, sterownik modułowy musi komunikować się z centralnym sterownikiem poprzez szybką magistralę. Dlatego stacje procesowe wyposażone są nie tylko w kontrolery i karty wejść i wyjść komunikujące się z urządzeniami wykonawczymi, ale również w kontroler magistrali współpracujący z magistralą systemową, którą przesyłane są informację do stacji operatorskich. Wymiana danych dokonuje się przez cykliczną wymianę zmiennych w sieci lub acykliczne moduły komunikacyjne.
W przypadku małych i średnich aplikacji (do 3000 we/wy) korzysta się zazwyczaj z systemów z architekturą bezserwerową, w przypadku większych systemów i linii produkcyjno-procesowych korzysta się z serwera. Funkcją serwera jest zarówno przekazywanie danych, jak i ich archiwizacja w postaci plików historycznych. Ze względu na modułowy charakter systemów DCS, za konfigurację systemu i nadzór oprogramowania wewnątrz kontrolerów odpowiada tzw. stacja inżynierska, a diagnostyka może być prowadzona przez stację diagnostyczną.
Proces podejmowania decyzji wewnątrz modułu, a także współpraca między modułami musi uwzględniać typowe dla danego systemu automatyki czy maszyny produkcyjnej ograniczenia dotyczące ustalonego następstwa wykonywanych w procesie wytwórczym czynności. Są to tak zwane ograniczenia kolejnościowe związane z faktem, iż dany zasób może wykonywać jednocześnie najczęściej tylko jedną czynność. Należy również uwzględnić ograniczenia decyzyjne, aby podejmowane przez system automatyki decyzje nie doprowadziły do powstania blokady, a więc zablokowania kolejnych czynności. W systemach DCS, podstawowym problemem przy podejmowaniu zautomatyzowanych decyzji jest problem wyboru kolejności i momentu rozpoczęcia realizacji poszczególnych czynności na przyporządkowanych zasobach. Problemem jest też kwestia wyboru wariantu procesu w przypadku procesów wielowariantowych lub też wybór zasobu w przypadku systemów charakteryzujących się redundancją zasobów.
Technologia lokalnego, rozproszonego sterowania odznacza się bardzo dobrze ustrukturyzowaną architekturą. Prosta jest też wymiana danych i testowanie poszczególnych modułów. Ze względu na prostą topologię można bez problemów stosować np. standardowe systemy fieldbus. Jednak komunikacja między modułami, z uwzględnieniem sterownika nadrzędnego, a także synchronizacja sterowników podczas procedury rozruchu/zatrzymania linii, jest już stosunkowo skomplikowana.
Systemy scentralizowane
W wypadku bardziej złożonych systemów, urządzeń czy linii produkcyjnych, znacznie lepszą funkcjonalnością i elastycznością cechują się systemy scentralizowane. Podstawową zaletą technologii sterowania scentralizowanego jest „zebranie” w jednym punkcie procedur diagnozy, rozruchu, konserwacji, kolejności wykonywania operacji oraz algorytmów zapobiegania blokadom związanym z kolejnością czynności, jak i dostępem do zasobów – np. podzespołów czy narzędzi. Łatwiejsza jest także procedura rozruchu lub zatrzymania linii lub jej fragmentu oraz łatwe zarządzanie operatorskie za pomocą jednego programu SCADA.
W modelu scentralizowanym wykorzystywane są najczęściej komputery przemysłowe sterujące całą linią lub kontrolery PLC odpowiedzialne za sterowanie systemem w obrębie jednego lub kilku modułów. Dzięki zastosowaniu sterowników samodzielnie realizujących obliczenia związane z przebiegiem procesu, np. pozycjonowaniem, urządzenia sterujące elementami wykonawczymi nie muszą niczego same liczyć – są stale sterowane zdalnie. W takim układzie reagowanie zsynchronizowanych napędów następuje bardzo szybko, co eliminuje potrzebę stosowania kłopotliwego sprzęgania napędów, co upraszcza konstrukcję systemu wykonawczego. Co więcej, im lepsze są parametry komputera, tym bardziej złożone zadania może on realizować. Standardowy komputer przemysłowy może obecnie z łatwością sterować pozycjonowaniem nawet w kilkuset osiach.
Jak widać, pod względem funkcjonalnym współczesne scentralizowane systemy automatyki przemysłowej oraz systemy rozproszone są do siebie zbliżone. Pracą systemu, bądź jego części steruje sterownik PLC lub innego rodzaju urządzenie sterujące. To właśnie ten moduł podejmuje decyzje sterujące czyli fizycznie kieruje urządzeniami, np. silnikiem, na podstawie zebranych danych o stanie maszyny bądź obiektu. Jak już wspomniano, informacje te pochodzą z podłączonych do jego wejść czujników, np. temperatury oraz różnego typu przetworników, które są najczęściej sprzężone z elementami wykonawczych maszyny lub instalacji automatyki przemysłowej. Urządzenie sterujące na podstawie wszystkich otrzymanych danych automatycznie realizuje zaprogramowane wcześniej czynności związane z procesami sterowania i regulacji, reagując tym samym w czasie rzeczywistym, na wszelkiego typu zdarzenia związane z wykonywaną pracą.
W tym miejscu warto wspomnieć, że identyczny schemat działania występuje również w przypadku sterowania i monitoringu obiektów rozproszonych – np. elektrowni wiatrowych, przy czym sterowanie jest tu rozdzielone między moduły sterowania obiektowego i system centralny, który odpowiedzialny jest za nadzór i sterowanie całością rozproszonej infrastruktury. Jak już wspomniano, nie jest tu istotne, z jakim obiektem, urządzeniem, czy linią mamy do czynienia. Wszystko bowiem jest opisane za pomocą funkcjonalnych modułów, gdzie elementy podrzędne we własnym zakresie dokonują regulacji i reagują na polecenia elementu nadrzędnego, który nadzoruje pracę kilku obiektów podrzędnych, sam wysyłając informacje i odbierając polecenia z modułu sterującego znajdującego się ewentualnie „nad nim”. W ten sposób tworzony jest hierarchiczny łańcuch urządzeń sterowania pozwalający sprawować kontrolę nad infrastrukturą rozproszoną – niezależnie czy jest to typowy system scentralizowany czy bliżej mu do infrastruktury DCS.
Industry 4.0 i Smart Maintenece
Bez względu na to, czy mamy do czynienie ze zdalnym monitoringiem systemu rozproszonego czy scentralizowanego, istotne stają się kwestie zdalnej transmisji danych pomiarowych i sterujących. Takie podejście do problemu sterowania pozwala bowiem połączyć rozproszone obiekty w jeden spójny system centralnego monitoringu i zdalnej kontroli, co jest zgodne z ideą Przemysłu 4.0, a szczególności w zakresie wywodzącej się z niego tzw. koncepcji Smart Maintenance, rozumianej jako zwiększenie autonomiczności obiektów, mocniejszą integrację urządzeń oraz, co najważniejsze, znaczącemu usprawnieniu zarządzania utrzymaniem ruchu i serwisowania.
Jak wspomniano, podstawowym celem przyświecającym powstaniu systemów zdalnego sterowania i monitoringu jest obniżenie kosztów produkcji i eksploatacji. Pozwalają one również zautomatyzować procesy technologiczne i usprawniają dostęp do danych o stanie procesu, niezależnie od tego, jak bardzo jest on rozproszony i w ilu obiektach i miejscach realizowany. W rezultacie skraca się również czas reakcji nadzoru na stany awaryjne.
Tradycyjne metody nadzoru w wyjątkowo rozproszonych obiektach infrastruktury, na przykład w energetyce czy w branży wodno-kanalizacyjnej obejmują objazd obiektów przez służby techniczne w celach kontrolnych i pomiarowych. Nie jest to efektywne działanie i może powodować problemy w lokalizowaniu miejsc wystąpienia awarii. Dzięki zastosowaniu scentralizowanego systemu zdalnego monitoringu można precyzyjnie diagnozować miejsca wystąpienia awarii i skrócić czas obsługi oraz ewentualnych napraw. Ponadto dostęp do bieżących i historycznych danych pomaga w przewidywaniu awarii, śledzeniu poprawności procesu i pozwala też na precyzyjne planowanie zmian.
Włączenie zautomatyzowanego systemu monitoringu i sterowania w infrastrukturę IT przedsiębiorstwa pozwala też wyposażyć kadrę kierowniczą w narzędzia wspomagające procesy decyzyjne związane z bieżącą działalnością firmy. Odpowiednie oprogramowanie może bowiem pomóc w analizach techniczno-ekonomicznych, na podstawie których można podejmować decyzje dotyczące produkcji, zamówień, a także, w połączeniu z mechanizmami sprzedaży ocenić zadowolenie klienta.
Co więcej, zautomatyzowany system sterowania i monitoringu linii, maszyn i obiektów technologicznych można w dowolnym momencie elastycznie dopasować do aktualnie stawianych wymagań. Łatwość integracji z powszechnie dostępnymi systemami sterowania oraz otwartość na wymianę danych z innymi systemami automatyki stosowanymi w przemyśle, pozwala na zbudowanie jednego, spójnego rozwiązania nadzorującego działanie przedsiębiorstwa, dostarczającego w dowolnej chwili zawsze wiarygodnych i aktualnych informacji.
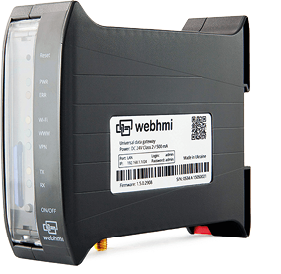
WebHMI to urządzenie z wbudowanym systemem SCADA dla małych i średnich aplikacji zarządzanym za pośrednictwem przeglądarki WWW
Trzy warstwy
Strukturę zautomatyzowanego systemu monitoringu i zdalnego sterowania najczęściej przedstawia się w oparciu o trzy warstwy funkcjonalne – warstwę aplikacyjną, warstwę sterowania i warstwę komunikacji. Warstwa aplikacyjna budowana jest w oparciu o sprzęt komputerowy lub panele operatorskie HMI z oprogramowaniem odpowiedzialnym za gromadzenie, wizualizację i przetwarzanie spływających w czasie rzeczywistym z rozproszonego systemu danych. Dodatkową funkcją jest archiwizowanie zebranych informacji.
Najczęściej wykorzystuje się tu oprogramowanie klasy SCADA (Supervisory Control And Data Acquisition) oraz wspomniane panele operatorskie HMI (Human Machine Interface) wspomagane przez moduły raportowania i analizy danych. Dodatkowo wykorzystywane są tu programowe interfejsy pozwalające na płynną integrację z systemami ERP przedsiębiorstwa, a także narzędziami klasy Business Inteligence.
Przyjmuje się, że dobrze zaprojektowana i wdrożona warstwa aplikacyjna pozwala korzystać z jednej wspólnej bazy danych dla wszystkich serwerów i rozproszonych stacji monitoringu oraz z jednej bazy użytkowników. Zwykle stosuje się tu bazy korzystające z rozwiązań klasy SQL.
Dzięki jednej scentralizowanej bazie możliwe jest też modyfikowanie działania i zarządzanie aplikacją z poziomu oprogramowaniem SCADA z jednego centralnego punktu czyli pokoju lub centrali operatorskiej. Jedna baza daje też możliwość grupowania zmiennych, skryptów, konfiguracji alarmów, zdarzeń i logowania historycznego związanych z konkretnymi fizycznymi urządzeniami, a także możliwość wielokrotnego wykorzystania przygotowanych szablonów sterowania przez ich proste powielanie i ewentualne modyfikowanie. Łatwiej też zabezpieczyć kluczowe elementy systemu przed problemami z dostępnością i awariami. Wystarczy zastosować w infrastrukturze IT odpowiednio dobrane mechanizmy redundancji serwerów i stacji operatorskich oraz backup danych.
Komunikacja i sterowanie
Obecnie trzon warstwy komunikacyjnej stanowi przemysłowy, przewodowy Ethernet oraz wszędzie, gdzie to niezbędne, bezprzewodowa transmisja danych. Ta ostatnia przydaje się zwłaszcza tam, gdzie mamy do czynienia z rozproszonymi obiektami, gdzie trudno doprowadzić okablowanie. Jeśli chodzi o rozwiązania bezprzewodowe, najczęściej stosuje się radiomodemy (systemy wodno-kanalizacyjne, energetyka, kopalnie odkrywkowe), modemy LTE, a w obrębie hal produkcyjnych rozwiązania bazujące na komunikacji Wi-Fi, coraz częściej działające w paśmie 5 GHz, w tym zgodne z najnowszym standardem Wi-Fi 6E. Uzupełnieniem systemu są oczywiście switche i routery przemysłowe, a także różnego rodzaju konwertery komunikacyjne. Dobierając system transmisji warto zwrócić uwagę na [1]:
- możliwość przesyłania danych online bez ograniczeń przy zachowaniu stałych opłat transmisyjnych (niezależnie od ilości przesyłanych danych i liczby obiektów);
- możliwość łatwego dodawania kolejnych obiektów, najlepiej za pomocą graficznego edytora do projektowania tras komunikacyjnych;
- możliwość serwisowania infrastruktury sieciowej w dowolnie zaplanowanym momencie;
- możliwość zabezpieczenia przed zakłóceniami z innych sieci;
- możliwość zabezpieczenia przed przerwami w dostępności sieci;
- możliwość zarządzania siecią i prowadzenia diagnostyki wszystkich urządzeń transmisyjnych w sposób zdalny;
- możliwość prowadzenia redundantnej transmisji danych (ważne dla infrastruktury krytycznej).
Warstwa sterowania, to przede wszystkim sterowniki PLC, układy wejść/wyjść, panele operatorskie, a także przemienniki częstotliwości. Elementy te odpowiadają za wydajną pracę linii technologicznych, maszyn czy gniazd produkcyjnych. Urządzenia te odpowiadają też za zbieranie za pomocą podłączonych do nich czujników informacji i gromadzenie kluczowych dla procesu sterowania i produkcji danych. Dobierając system sterowania należy zwrócić uwagę na funkcje i parametry, np. dla sterowników PLC mogą to być [1]:
- możliwość wymiany danych w najbardziej popularnych sieciach, np. Modbus RTU/Modbus TCP, Profibus/Profinet;
- możliwość łatwego rozbudowania o dodatkowe moduły sygnałowe dyskretne i analgowe oraz o moduły specjalistyczne i komunikacyjne;
- możliwość szybkiego sterowania sygnałami dyskretnymi i analogowymi;
- możliwość programowania sterownika i wymiany modułów na ruchu;
- możliwość budowania programów sterujących w wielu językach, np.: LD, ST, FBD, C;
- możliwość obsługi zaawansowanych funkcji w programie sterującym (funkcje matematyczne, regulacja PID, przerwania sprzętowe itd.);
- możliwość prowadzenia lokalnej diagnostyki w oparciu o zestaw diod LED;
- możliwość pracy w układzie redundancji (ważne dla infrastruktury krytycznej).
Decydując się na budowę systemu zdalnego monitoringu i sterowania należy przede wszystkim zwrócić uwagę na możliwość współpracy nowego systemu z istniejącą infrastrukturą – chyba, że projektujemy proces technologiczny zupełnie od podstaw (nowa fabryka), co daje znacznie lepsze możliwości dobrania wszystkich jego elementów do obecnych oraz przyszłych potrzeb. Należy też opracować podstawowe założenia systemu i pod ich kątem poszukać dostawców sprzętu i rozwiązań programowych. Dopiero w tym momencie można zbudować koncepcję techniczną, która spełni założone cele i zmieści się w planowanych kosztach wdrożenia. Przejdźmy teraz do analizy kluczowych elementów systemu sterowania i monitoringu, czyli paneli operatorskich HMI i systemów SCADA.
Panel operatorski HMI
Panel operatorski, czyli panel HMI to urządzenie, które pozwala sprawować kontrolę nad innymi urządzeniami systemu realizującymi swoje zadania związane z procesem wykonawczym, technologicznym lub produkcyjnym i umożliwia prezentację danych i zadawanie parametrów pracy. Do głównych funkcji panelu operatorskiego należy pośredniczenie w komunikacji człowieka z maszyną, stąd nazwa HMI, a więc właśnie wspomniane odbieranie i przekazywane sygnałów, zbieranie aktualnych danych pomiarowych z kontrolowanych procesów i ich wizualizacja, sterowanie tymi procesami oraz alarmowanie. Obecnie panel operatorski ma postać wyświetlacza LCD z dotykowym ekranem, na którym oprogramowanie do wizualizacji prezentuje w czytelnej formie parametry pracy maszyny lub linii produkcyjnej.
Współczesne panele HMI ułatwiają nie tylko integrację wszystkich urządzeń pracujących w instalacji lub maszynie w jeden spójny system, ale oferują również zaawansowane funkcje, związane z logowaniem danych i zdarzeń, wizualizacją, ciągłym monitoringiem kluczowych parametrów, alarmowaniem, obsługą skryptów, receptur i systemów zabezpieczeń raportowanie, generowanie trendów, rejestracja danych do systemów MES czy komunikacja z innymi urządzeniami. Oczywiście, możliwe jest także podłączenie do nich różnych innych urządzeń systemu automatyki, w tym sterowników PLC, dlatego dla małych aplikacji o ograniczonych wymaganiach lub w przypadku sterowania pojedynczą maszyną, w tym obrabiarką numeryczną, panel HMI jest wystarczającym rozwiązaniem.
Panele HMI montowane są zazwyczaj bezpośrednio w maszynie lub przy obiekcie automatyki przemysłowej i służą do sterowania, zadawania parametrów, a także do informowania operatorów o bieżącym stanie maszyny lub systemu automatyki. Oczywiście mogą to być systemy rozproszone, niemniej rola paneli operatorskich kończy się na lokalnym sterowaniu i wyświetlaniu informacji zbieranych w pobliżu obiektu automatyki przemysłowej bądź z maszyny. W przypadku bardziej zaawansowanych aplikacji korzysta się z systemów SCADA.
Systemy SCADA
Podstawowym zadaniem systemu jest nadzór nad procesem i pozyskiwanie związanych z nim danych. Innymi słowy systemy SCADA samodzielne realizują postawione im zadania związane z szeroko rozumianymi procesami przemysłowego sterowania – oczywiście z udziałem człowieka, który nadzoruje całokształt funkcjonowania procesu technologicznego lub produkcyjnego. W tym miejscu warto podkreślić, że systemy SCADA stosowane są głównie w różnego typu instalacjach procesowych lub technologicznych, które są fizycznie rozproszone na znacznym obszarze. Dobrze sprawdzają się też w przemyśle farmaceutycznym, petrochemicznym i chemicznym, w tym przy produkcji nawozów sztucznych, w których trzeba sterować wyjątkowo złożonymi etapami technologiczno-procesowymi związanymi z syntezą chemiczną.
Podkreślmy, że każde z urządzeń wchodzących w skład infrastruktury technologiczno-procesowej jest z reguły sterowane lokalnie, za pomocą systemu automatyki, najczęściej bazującego na sterowniku PLC i podłączonych do niego elementów wykonawczych i pomiarowych. Brak tu natomiast nadzoru nad całością infrastruktury i taką role odgrywa tu właśnie system SCADA – realizuje on nadzór nad całością infrastruktury i zachodzących w niej procesów.
Dzięki temu, w sytuacjach, które tego wymagają, z poziomu stacji operatorskich sytemu SCADA można oddziaływać nie tylko na parametry sterowania lokalnych systemów automatyki, ale również podejmować nadrzędne decyzje wpływające na działanie całej linii technologicznej – np. możemy podjąć decyzję o odcięciu stacji transformatorów, co wpłynie na całą sieć energetyczną.
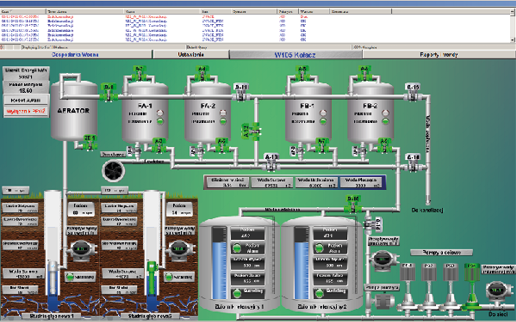
Przykładowy ekran wizualizacyjny z systemu SCADA wykorzystywanego w procesach monitoringu i zdalnego sterowania
Zadania
Jednym z głównych zadań systemów SCADA jest wizualizacja danych procesowych, które muszą być przedstawiane w czytelnej, przejrzystej oraz przyjaznej dla człowieka formie. W tym punkcie system SCADA przypomina w swojej formie działania interfejsy HMI, ale w wypadku SCADA zakres graficznej formy obrazowania obejmuje znacznie szerszy zestaw rozproszonych urządzeń, a nie tylko ograniczony jest do lokalnego systemu automatyki czy pojedynczej maszyny. Co więcej, w systemach SCADA graficzna reprezentacja danych musi być intuicyjna i jednoznaczna, a dostarczane użytkownikowi informacje muszą być w prostej, analitycznej formie. Dzięki temu możliwa jest szybka reakcja pracowników obsługi na zmieniającą się dynamicznie sytuację procesową.
Kolejnym zadaniem systemów SCADA, które notabene jest bardzo rzadko realizowane przez panele HMI, to tworzenie okresowych raportów, zawierających zestawienie odpowiednich danych procesowych. Raporty takie są tworzone co ściśle określony czas, który może być indywidualnie ustalany w zależności od charakteru monitorowanego procesu. Systemy SCADA pozwalają nie tylko na pełną wizualizację bieżących procesów, ale również mogą korzystać z danych archiwalnych i porównywać je ze stanem aktualnym, co pomaga m.in. w przewidywaniu awarii.
Oprogramowanie SCADA musi być też na tyle elastyczne i skalowalne, nie tylko pod względem możliwości podłączania do niego kolejnych elementów systemu automatyki, ale przede wszystkim prezentacji przekazywanych informacji, co w praktyce oznacza, że system SCADA musi mieć możliwość prezentowania tych samych danych na różne sposoby, a także możliwość definiowania własnych skryptów użytkownika związanych z prezentacją wykresów z danymi.
Bezpieczeństwo i ciągłość produkcji
Kolejnym aspektem wykorzystania systemów SCADA są kwestie zapewnienia bezpieczeństwa i ciągłości produkcji. To dlatego jest tak ważne generowanie informacji o stanach alarmowych i awaryjnych. Przydatny może się tu okazać moduł analityczny, który pozwala użytkownikom podejmować prawidłowe decyzje w sytuacjach wyjątkowych i krytycznych. Oczywiście, z pomocą przychodzą tu również zgromadzone dane historyczne. Na ich podstawie można bowiem podejmować decyzje, kierując się rozwiązaniami problemów, które pojawiały się już w przeszłości. Archiwizacja danych, niosących informacje o przebiegu procesu technologicznego umożliwia zatem długoterminową analizę pracy obiektu. Historyczne dane są również cennym źródłem wiedzy w przypadku wystąpienia sytuacji awaryjnych.
W wypadku awarii lub przekroczenia parametrów krytycznych monitorowanego procesu wszczęty alarm musi być przede wszystkim skuteczny. Musi on zwrócić uwagę operatora na kryzysową sytuację i wymusić jego reakcję. Wystąpieniu alarmu towarzyszy zawsze sygnał graficzny, taki jak migający monitor, wyskakujące okienko z powiadomieniem alarmowym oraz sygnał dźwiękowy. Dodatkowo system wysyła alarmowe e-maile i SMS-y do odpowiedzialnych za działanie systemu osób. Co ważne, zamknięcie okna lub komunikatu alarmu wymaga potwierdzenia. Można więc przyjąć, że użytkownik został poinformowany o wszczętym alarmie.
Z punktu widzenia bezpieczeństwa danych, istotnym elementem systemu SCADA musi być zaawansowana ochrona dostępu, która pozwala na przypisanie użytkownikom indywidualnych uprawnień. Systemy SCADA charakteryzują się również zaawansowanymi możliwościami sieciowymi oraz funkcją pozwalającą na przeprowadzenie zdalnej konfiguracji przez Internet. Dzięki temu operator może zmienić parametry pracy systemu bez konieczności przerywania jego pracy i zatrzymywania produkcji, nawet w środku nocy z domu.
Otwarta architektura
Założenia Przemysłu 4.0 wymagają też elastycznej, otwartej architektury wdrażanych systemów przemysłowych. Taką otwartością cechują się też praktycznie wszystkie dostępne na rynku systemy SCADA, które utożsamiane są bardziej z infrastrukturą informatyczną przedsiębiorstwa a nie z systemami automatyki przemysłowej.
System SCADA pełni funkcję nadrzędną w stosunku do urządzeń sterujących automatyki przemysłowej, dzięki czemu łatwo do niego podłączyć kolejne elementy rozproszonej architektury. Nie ma też problemu z przekonfigurowaniem działającego w firmie rozwiązania. Zazwyczaj bezpośrednio do systemu SCADA podłączane są sterowniki PLC, a te z kolei są połączone z urządzeniami wykonawczymi, np. napędami i zaworami czy urządzeniami pomiarowymi. Dzięki takiemu modułowemu, a jednocześnie hierarchicznemu podejściu nie ma najmniejszych problemów z przekonfigurowaniem systemu i dostosowaniem go do zmieniających się potrzeb. Z drugiej strony, dzięki odpowiednim interfejsom programowym, system SCADA bez problemu może współpracować z dowolnym elementem infrastruktury programowej przedsiębiorstwa, w tym systemami ERP czy CRM.
Cechą charakterystyczną systemu SCADA jest to, że układy regulacji występujące w danym procesie technologicznym mogą działać niezależnie od niego. System SCADA stanowi tu wyłącznie warstwę nadrzędną, która realizuje swoje podstawowe zadania w procesie sterowania kontrolując pracę sterowników. Otwartość i uniwersalność tych systemów związana z możliwością pracy w sieci, w tym w sieci przemysłowego Ethernetu, lub na poziomie Przemysłowego Internetu Rzeczy i współpracy z elementami Przemysłu 4.0.
Co ważne, systemy SCADA bez problemu mogą współpracować z inteligentnymi urządzeniami automatyki takimi jak sterowniki PLC, regulatory, rejestratory, czujniki, elementy wykonawcze, przetworniki, które pochodzą od najróżniejszych producentów. Dodatkowo pod system SCADA podłączyć można system automatyki budynkowej, dzięki czemu SCADA może zagwarantować odpowiednie warunki środowiskowe (m.in. sterowanie klimatyzacją, oświetleniem, ogrzewaniem), które niezbędne są do zapewnienia komfortowej pracy ludzi, a jednocześnie spełnione będą wymaganie (jeśli są określone i konieczne) do prowadzenia procesu technologicznego.
W mniej skomplikowanych procesach system SCADA może pracować na specjalizowanym komputerze przemysłowym. Większa aplikacja, na przykład sterująca pracą rafinerii wymaga znacznie większej infrastruktury od strony systemów IT, łącznie z wieloma serwerami, środowiskiem chmurowym i systemami storage’owymi. Jak widać jest to bardzo elastyczne rozwiązanie.
Licencje
Warto pamiętać, że używanie gotowego oprogramowania SCADA, nawet jeśli sami je konfigurujemy i wdrażamy, wiąże się zazwyczaj z zakupem licencji, które nierzadko muszą być cyklicznie odnawiane. Wiele tradycyjnych systemów w ramach standardowych licencji ma ograniczoną ilość danych, które serwer może wymieniać ze sterownikami. Ten wolumen można oczywiście zwiększyć, płacąc za droższą licencję. Dodatkowo wizualizacja na większej liczbie stacji roboczych, czy urządzeniach mobilnych, wymaga wykupienia kolejnych licencji stanowiskowych, co też trzeba brać pod uwagę planując wdrożenie systemu SCADA.
Istotnym elementem otwartego i uniwersalnego systemu SCADA, a także ważnym z punktu widzenia licencji, jest możliwość instalacji aplikacji zarządzających na platformach wieloserwerowych, w tym w środowisku zwirtualizowanym oraz w skalowalnym środowisku chmurowym. Często w skomplikowanych środowiskach technologiczno-produkcyjnych może się bowiem okazać, że komputer, na którym zainstalowana jest centralna aplikacja systemu SCADA jest tak obciążony, że nie jest w stanie poprawnie pracować w czasie rzeczywistym. Dlatego warto skorzystać z platformy przystosowanej do pracy w środowisku wieloserwerowym, w tym zwirtualizowanym, lub wersji przystosowanej do pracy w chmurze, najlepiej hybrydowej.
Co ważne, platformy chmurowe pozwalają również zdecentralizować system SCADA, co zwiększa bezpieczeństwo produkcji, a w razie większego obciążenia, przeskalować środowisko, tworząc nowe wirtualne serwery lub dodając „w locie” brakujące zasoby. Jak widać, przeniesienie aplikacji do środowiska chmurowego daje niemal stuprocentowe bezpieczeństwo związane z działanie centralnego elementu systemu SCADA.
Istotnym elementem każdego systemu SCADA jest zbieranie danych i sposób komunikacji z elementami nadzorującymi pracę poszczególnych elementów systemu automatyki, czyli w praktyce ze sterownikami PLC, które już bezpośrednio odpowiadają za realizację procesów automatyzacji produkcji czy sterowanie maszyną. Dlatego należy tu unikać oprogramowania SCADA, które ma bardzo ograniczone możliwości komunikacyjne ze sterownikami PLC pochodzącymi od różnych producentów. Koniecznie należy sprawdzić, jakie sterowniki PLC i jakich producentów będziemy stosować i czy wybrany system SCADA ma wbudowane drivery komunikacyjne do tych wszystkich typów sterowników, z których będą odczytywane informacje.
Zamiast zakończenia
Jak widać systemy SCADA pozwalają osiągnąć wzrost skuteczności działania firmy, nie tylko za sprawą integracji rozproszonego sterowania i scaleniu go w jeden spójny, elastyczny i otwarty system automatyki, ale również dzięki połączeniu procesów produkcyjnych z systemami analityczno-biznesowymi klasy ERP. Sam system SCADA oferuje też wyższy komfort pracy personelu odpowiedzialnego za obsługę procesów produkcyjnych, a więc mniejszą ilość popełnianych błędów. Kolejną korzyścią jest możliwość przewidywania awarii i nietypowych zdarzeń. Istotnemu skróceniu ulega również czas podejmowania decyzji oraz ich realizacji.
Co więcej, systemy SCADA, a w mniejszym zakresie również panele operatorskie HMI, zdejmują z osób odpowiedzialnych za nadzór procesu technologicznego potrzebę analizowania części informacji, pozwalając na skuteczną selekcję i oddzielenie ważnych informacji od tych mniej, w danym momencie istotnych. Dzieje się tak właśnie dzięki automatyzacji przetwarzania danych oraz przyjaznej i czytelnej dla użytkowników formie prezentacji informacji. SCADA i panele operatorskie pozwalają również na lepszą kontrolę rzeczywistego stanu technicznego elementów linii technologicznej czy maszyny, przyczyniając się bezpośrednio do optymalizacji zadań związanych z utrzymaniem ruchu.
źródło: Automatyka 11/2021
Komentarze
blog comments powered by Disqus